▼
Scroll to page 2
of
34
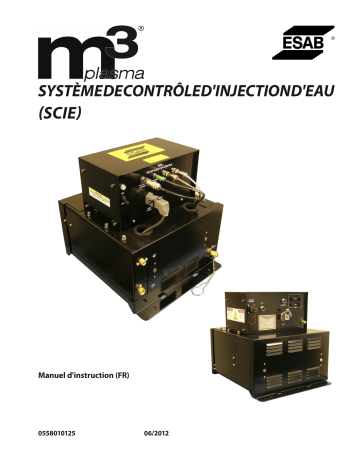
Systèmedecontrôled'injectiond'eau (SCIE) Manuel d'instruction (FR) 0558010125 06/2012 ASSUREZ-VOUS QUE CETTE INFORMATION EST DISTRIBUÉE À L'OPÉRATEUR. VOUS POUVEZ OBTENIR DES COPIES SUPPLÉMENTAIRES CHEZ VOTRE FOURNISSEUR. aTTENTION Les INSTRUCTIONS suivantes sont destinées aux opérateurs qualifiés seulement. Si vous n’avez pas une connaissance approfondie des principes de fonctionnement et des règles de sécurité pour le soudage à l’arc et l’équipement de coupage, nous vous suggérons de lire notre brochure « Precautions and Safe Practices for Arc Welding, Cutting and Gouging, » Formulaire 52-529. Ne permettez PAS aux personnes non qualifiées d’installer, d’opérer ou de faire l’entretien de cet équipement. Ne tentez PAS d’installer ou d’opérer cet équipement avant de lire et de bien comprendre ces instructions. Si vous ne comprenez pas bien les instructions, communiquez avec votre fournisseur pour plus de renseignements. Assurez-vous de lire les Règles de Sécurité avant d’installer ou d’opérer cet équipement. RESPONSABILITÉS DE L'UTILISATEUR Cet équipement opérera conformément à la description contenue dans ce manuel, les étiquettes d’accompagnement et/ou les feuillets d’information si l’équipement est installé, opéré, entretenu et réparé selon les instructions fournies. Vous devez faire une vérification périodique de l’équipement. Ne jamais utiliser un équipement qui ne fonctionne pas bien ou n’est pas bien entretenu. Les pièces qui sont brisées, usées, déformées ou contaminées doivent être remplacées immédiatement. Dans le cas où une réparation ou un remplacement est nécessaire, il est recommandé par le fabricant de faire une demande de conseil de service écrite ou par téléphone chez le Distributeur Autorisé de votre équipement. Cet équipement ou ses pièces ne doivent pas être modifiés sans permission préalable écrite par le fabricant. L’utilisateur de l’équipement sera le seul responsable de toute défaillance résultant d’une utilisation incorrecte, un entretien fautif, des dommages, une réparation incorrecte ou une modification par une personne autre que le fabricant ou un centre de service désigné par le fabricant. ASSUREZ-VOUS DE LIRE ET DE COMPRENDRE LE MANUEL D'UTILISATION AVANT D'INSTALLER OU D'OPÉRER L'UNITÉ. PROTÉGEZ-VOUS ET LES AUTRES ! 2 Table des matières Section/Titre Page 1.0 Précautions de sécurité . . . . . . . . . . . . . . . . . . . . . . . . . . . . . . . . . . . . . . . . . . . . . . . . . . . . . . . . . . . . . . . . . . . . . . . . . . . . . . . 5 Classe de boîtier . . . . . . . . . . . . . . . . . . . . . . . . . . . . . . . . . . . . . . . . . . . . . . . . . . . . . . . . . . . . . . . . . . . . . . . . . . . . . . . . . . . . . . 5 2.0 Description . . . . . . . . . . . . . . . . . . . . . . . . . . . . . . . . . . . . . . . . . . . . . . . . . . . . . . . . . . . . . . . . . . . . . . . . . . . . . . . . . . . . . . . . . . . 9 2.1 Fonctions et caractéristiques . . . . . . . . . . . . . . . . . . . . . . . . . . . . . . . . . . . . . . . . . . . . . . . . . . . . . . . . . . . . . . . . . . . . 9 2.2 Fonctions et caractéristiques (module de la pompe) . . . . . . . . . . . . . . . . . . . . . . . . . . . . . . . . . . . . . . . . . . . . 10 2.3 Spécifications techniques . . . . . . . . . . . . . . . . . . . . . . . . . . . . . . . . . . . . . . . . . . . . . . . . . . . . . . . . . . . . . . . . . . . . . . 11 2.4 Connexions, commandes et indicateurs . . . . . . . . . . . . . . . . . . . . . . . . . . . . . . . . . . . . . . . . . . . . . . . . . . . . . . . . 12 3.0 Installation . . . . . . . . . . . . . . . . . . . . . . . . . . . . . . . . . . . . . . . . . . . . . . . . . . . . . . . . . . . . . . . . . . . . . . . . . . . . . . . . . . . . . . . . . . 13 3.1 Emplacements des trous de montage . . . . . . . . . . . . . . . . . . . . . . . . . . . . . . . . . . . . . . . . . . . . . . . . . . . . . . . . . . 13 3.2 Besoins en eau de découpe . . . . . . . . . . . . . . . . . . . . . . . . . . . . . . . . . . . . . . . . . . . . . . . . . . . . . . . . . . . . . . . . . . . . 13 4.0 Fonctionnement . . . . . . . . . . . . . . . . . . . . . . . . . . . . . . . . . . . . . . . . . . . . . . . . . . . . . . . . . . . . . . . . . . . . . . . . . . . . . . . . . . . . 15 4.1 Fonctionnement en mode de communication CAN . . . . . . . . . . . . . . . . . . . . . . . . . . . . . . . . . . . . . . . . . . . . . 15 4.2 Fonctionnement en mode de commande optionnelle . . . . . . . . . . . . . . . . . . . . . . . . . . . . . . . . . . . . . . . . . . 17 4.3 Précautions concernant le moteur . . . . . . . . . . . . . . . . . . . . . . . . . . . . . . . . . . . . . . . . . . . . . . . . . . . . . . . . . . . . . 17 4.4 Fonction antigel . . . . . . . . . . . . . . . . . . . . . . . . . . . . . . . . . . . . . . . . . . . . . . . . . . . . . . . . . . . . . . . . . . . . . . . . . . . . . . 18 4.4.1 Procédure antigel . . . . . . . . . . . . . . . . . . . . . . . . . . . . . . . . . . . . . . . . . . . . . . . . . . . . . . . . . . . . . . . . . . . . . . . . . . . . . 18 4.5 Manifold du régulateur de contre-pression (RCP) . . . . . . . . . . . . . . . . . . . . . . . . . . . . . . . . . . . . . . . . . . . . . . . 20 5.0 Entretien . . . . . . . . . . . . . . . . . . . . . . . . . . . . . . . . . . . . . . . . . . . . . . . . . . . . . . . . . . . . . . . . . . . . . . . . . . . . . . . . . . . . . . . . . . . . 21 6.0 Pièces de rechange . . . . . . . . . . . . . . . . . . . . . . . . . . . . . . . . . . . . . . . . . . . . . . . . . . . . . . . . . . . . . . . . . . . . . . . . . . . . . . . . . . 27 3 Table des matières 4 section 1précautions de sécurité 1.0 Précautions de sécurité Les utilisateurs du matériel de soudage et de coupage plasma ESAB ont la responsabilité ultime d'assurer que toute personne qui opère ou qui se trouve dans l'aire de travail observe les précautions de sécurité pertinentes. Les précautions de sécurité doivent répondre aux exigences applicables à ce type de matériel de soudage ou de coupage plasma. Les recommandations suivantes doivent être observées en plus des règles standard qui s'appliquent au lieu de travail. Tous les travaux doivent être effectués par un personnel qualifié possédant de bonnes connaissances par rapport au fonctionnement du matériel de soudage et de coupage plasma. Un fontionnement incorrect du matériel peut produire des situations dangereuses qui peuvent causer des blessures à l'opérateur ou des dommages au matériel. 1. Toute personne travaillant avec le matériel de soudage ou de coupage plasma doit connaître : - son fonctionnement; - l'emplacement des interrupteurs d'arrêt d'urgence; - sa fonction; - les précautions de sécurité pertinentes; - les procédures de soudage et/ou de coupage plasma. 2. L'opérateur doit assurer que : - seules les personnes autorisées à travailler sur l'équipement se trouvent dans l'aire de travail lors de la mise en marche de l'équipement; - toutes les personnes dans l'aire de travail sont protégées lorsque l'arc est amorcé. 3. Le lieu de travail doit être : - aménagé convenablement pour acquérir le matériel en toute sécurité; - libre de courants d'air. 4. Équipement de sécurité personnelle - Vous devez toujours utiliser un équipement de sécurité convenable tels que les lunettes de protection, les vêtement ininflammables et des gants de protection. - Vous ne devez jamais porter de vêtements amples, tels que foulards, bracelets, bagues, etc., qui pourraient se prendre dans l'appareil ou causer des brûlures. 5. Précautions générales : - Assurez-vous que le câble de retour est bien branché. - La réparation d'un équipement de haute tension doit être effectuée par un électricien qualifié seulement. - Un équipement d'extinction d'incendie approprié doit être à proximité de l'appareil et l'emplacement doit être clairement indiqué. - Vous ne devez jamais procéder à la lubrification ou l'entretien du matériel lorsque l'appareil est en marche. Classe de boîtier Le code IP indique la classe du boîtier, à savoir le niveau de protection offert contre toute pénétration par des objets solides ou de l’eau. La protection est fournie contre le contact d’un doigt, la pénétration d’objets solides d’une taille supérieure à 12 mm et contre l’eau pulvérisée jusqu’à 60 degrés de la verticale. L’équipement marqué IP23S peut être stocké mais ne doit pas être utilisé à l’extérieur quand il pleut à moins d’être sous abri. ATTENTION Inclinaison maximum autorisée Si l’équipement est placé sur une surface inclinée de plus de 15°, il y a danger de basculement et en conséquence, des blessures personnelles et/ou des dommages importants à l’équipement. 15° 5 section 1 PRÉCAUTIONS DE SÉCURITÉ AVERTISSEMENT LE SOUDAGE ET LE COUPAGE À L'ARC PEUVENT CAUSER DES BLESSURES À L'OPÉRATEUR OU LES AUTRES PERSONNES SE TROUVANT DANS L'AIRE DE TRAVAIL. ASSUREZ-VOUS DE PRENDRE TOUTES LES PRÉCAUTIONS NÉCESSAIRES LORS D'UNE OPÉRATION DE SOUDAGE OU DE COUPAGE. DEMANDEZ À VOTRE EMPLOYEUR UNE COPIE DES MESURES DE SÉCURITÉ QUI DOIVENT ÊTRE ÉLABORÉES À PARTIR DES DONNÉES DES RISQUE DU FABRICANT. CHOC ÉLECTRIQUE - peut être mortel. - Assurez-vous que l'unité de soudage ou de coupage plasma est installée et mise à la terre conformément aux normes applicables. - Ne touchez pas aux pièces électriques sous tension ou les électrodes si vos mains ne sont pas bien protégées ou si vos gants ou vos vêtements sont humides. - Assurez-vous que votre corps est bien isolé de la mise à la terre et de la pièce à traiter. - Assurez-vous que votre position de travail est sécure. VAPEURS ET GAZ - peuvent être danereux pour la santé. - Gardez votre tête éloignée des vapeurs. - Utilisez un système de ventilation et/ou d'extraction à l'arc pour évacuer les vapeurs et les gaz de votre zone respiratoire. RAYONS DE L'ARC - peuvent endommager la vue ou brûler la peau. - Protégez vos yeux et votre corps. Utilisez un écran de soudage/coupage plasma convenable équipé de lentilles teintées et portez des vêtements de protection. - Protégez les personnes se trouvant dans l'aire de travail à l'aide d'un écran ou d'un rideau protecteur convenable. RISQUE D'INCENDIE - Les étincelles (projections) peuvent causer un incendie. Assurez-vous qu'il n'y a pas de matériel inflammable à proximité de l'appareil. BRUIT - un bruit excessif peut endommager la capacité auditive. - Protégez vos oreilles. Utilisez des protecteurs d'oreilles ou un autre type de protection auditive. - Avertissez les personnes se trouvant dans l'aire de travail de ce risque. FONCTIONNEMENT DÉFECTUEUX - Dans le cas d'un fonctionnement défectueux demandez l'aide d'une personne qualifiée. ASSUREZ-VOUS DE LIRE ET DE COMPRENDRE LE MANUEL D'UTILISATION AVANT D'INSTALLER OU D'OPÉRER L'UNITÉ. PROTÉGEZ-VOUS ET LES AUTRES ! ATTENTION Ce produit est uniquement destiné à la découpe du plasma. Toute autre utilisation peut entraîner des blessures ou endommager l’équipement. ATTENTION Pour éviter toute blessure personnelle et/ ou endommagement à l’équipement, soulever à l’aide de la méthode et des points d’attache indiqués ici. 6 PS PS PS-PSC 7 CC-TC IN Manual 0558008526 Ext. 115/230V (doit être de 230V avec AHC) IFH-IC IFH-TDF MMI (Vision 50P) MMI-IC IFH-IC (Station centrale d’interface) IFH Digital I/O CC-TC OUT Remote -TDF Customer CNC Ext. E-Stop GFA (Filtre à gaz) GFA-H35 H35 ALIMENTATION DONNÉES Ar LIQUIDE GAZ Manual 0558008527 Optionnel SGC-CH4 GFA-CH4 CH4 GFA-Ar SGC-N2 SGC-O2 GFA-N2 N2 GFA-O2 SGC-Air WIC SGC-PG2 SGC-PG1 IFH-PGC CAN Manual 0558008527 (Système de contrôle de gaz plasma) PGC Manual 0558008527 0558009782-OU Manual 0558006404 Rideau d’eau Tuyau du rideau d’eau Torche pt-36 Tuyau du gaz plasma Tuyau du gaz de protection Manual 0560946014 (A6) or 0560946015 (B4) AHC Téléphone 1-843-664-5550 Courrier électronique: oemplasma@esab.com PGC-CAN PGC-Ar PGC-H35 PGC-PG2 PGC-PG1 SGC-PWR PGC-PWR SGC-A/C OUT Manual 0558009491 BPR (régulateur de contre-pression) WIC-H2O OUT AHC-CAN AHC- AC IN RAS -VDR Alimentation, arc pilote, liquide de refroidissement (Système de contrôle d’injection d’eau) (Système de contrôle de gaz de protection) SGC-SG SGC WIC-Air IN (optional) WIC-H2O IN 230V AC WIC-AC IN Manual 0558008527 RAS (démarreur à distance de l’arc) WIC-CAN O2 GFA-Air SGC-A/C IN IFH-WIC CAN IFH-AC1 IFH-SGC CAN SGC-CAN IFH-AHC CAN RAS-CAN SGC-AC IN Air RAS-TC OUT RAS-E-Stop IFH-AC2 IFH-RAS CAN Coolant Return Hose (Tuyau de retour du liquide de refroidissement) RAS-TC IN Pilot Arc Cable (Câble de l’arc pilote) Coolant Supply Hose (Tuyau d’alimentation du liquide de refroidissement) RAS-PA Power Cable (Câble d’alimentation) IFH-AC IN Manual 0558008526 Manual 0558007823 PN 0558007515 (Circulateur du liquide de refroidissement) CC CC-IC PS-IC PS-PA RAS-PSC RAS-E(-) PS & CC Control Cable (Câble de commande) Schéma de connexion du système d’injection d’eau (Alimentation électrique) PS-E(-) R AHC-VDR 8 Section 2 2.0 Description Description Système de contrôle d'injection d'eau ......................................................................................................................................0558009370 2.1 Fonctions et caractéristiques Le système de contrôle d'injection d'eau (SCIE) régule le débit d'eau de découpe fournie à la torche à plasma. Cette eau est utilisée comme protection lors du processus de découpe. Cette protection assiste la formation de l'arc plasma et refroidit également la surface de découpe. La sélection et la sortie d'eau de découpe sont effectuées et contrôlées par le CNC. Le SCIE se compose d'un régulateur d'eau, d'une pompe et d'une boucle d'asservissement fermée entre la vanne proportionnelle et le capteur de débit. Il est contrôlé par une unité locale de contrôle du processus (UCP). Lorsqu'il est utilisé avec une machine à découper équipée d'un CNC ESAB Vision 5X, il envoie des signaux de commande à l'UCP à travers le bus CAN. Si d'autres CNC sont utilisés, le SCIE est utilisé en mode de commande optionnelle (se référer à la section Mode de Commande Optionnelle). Cela contrôle les vannes proportionnelles et électrovannes. Similairement au système de contrôle de gaz de protection m3 (SCGPR), le SCIE est contrôlé est envoie des signaux d'asservissement au CNC à travers le bus CAN pour effectuer un diagnostic en utilisant des différents fichiers sdp. Le SCIE peut également être utilisé conjointement avec le SCGPR pour sélectionner une découpe humide (eau de découpe comme protection) ou une découpe sèche (gaz comme protection). Option 1 : Découpe humide en utilisant le SCIE et le système de contrôle du gaz plasma (SCGPL). Le SCIE fournit une alimentation de 24 V CC et 24 V CA au SCGPL. Option 2 : Découpe humide ou sèche (SCGPR + SCGPL ou SCIE + SCGPL). Le SCGPR fournit une alimentation de V CC et 24 V CA au SCGPL. 12,1” (307 mm) 6,4” (163 mm) 6,4” (163 mm) 8,6” (218 mm) 15,0” (381 mm) 18,3” (465 mm) 18,3” (465 mm) 9 Section 2 2.2 Description Fonctions et caractéristiques (module de la pompe) Le module de la pompe du SCIE se compose d'un régulateur de pression (REG), d'une pompe, d'un capteur de pression (CP), d'une vanne proportionnelle (VP) et d'un capteur de débit (CD) connectés en série tel qu'illustré ci-dessous. Le filtre et les vannes sont optionnels et sont fournis par le client. L'eau de découpe filtrée et adoucie est fournie à la connexion H2O IN à plus de 20 psi (1,4 bar). Le régulateur de pression réduit la pression de l'eau à 20 psi (1,4 bar) (réglage d'usine) et l'envoie à la pompe. La pompe peut augmenter la pression de l'eau de découpe de 150 psi (10,4 bar) (réglage d'usine) au-delà de la pression d'entrée ; l'eau située après la pompe devra donc avoir une pression d'environ 170 psi (11,7 bar). L'UCP du SCIE peut réguler le débit d'eau à une valeur donnée en contrôlant le débit. Éléments fournis par le client SOUPAPE D'ÉVACUATION (Vanne ouverte pendant la purge) H2O ROBINET D'EAU PRI ENTRÉE P1/ M1 FILTRE CV1 (ALIMENTATION EN AIR optionnelle) AIR PT1 CV2 PV1/ PWM ENTRÉE SOL1 VERS LA TORCHE H2O SORTIE FS1 RCP Schéma de circulation des fluides du système de contrôle d'injection d'eau 10 Section 2 2.3 Description Spécifications techniques Dimensions (module électrique) 163 mm x 307 mm x 163 mm (6,4 in x 12,1 in x 6,4 in) Dimensions (module de la pompe) 465 mm x 465 mm x 218 mm (18,3 in x 18,3 in x 8,6 in) Poids (module électrique) 15 livres à sec (6,8 kg) Poids (module de la pompe) 60 livres à sec (27,2 kg) Besoins en eau L’eau du robinet avec une dureté de l’eau admissible de <2 ppm de CaCO3 et de la conductivité: résistivité doit être d’au moins 200.000 ohms • cm, la conductivité peut être pas plus de (5 μ S / cm), filtré à 5 microns. 1 gpm (3,8 l / min) débit minimum à 20 psi @ (1,4 bar). Approvisionnement en air (fonction 250 CFH à 80 psi (7,1 cmh à 5,5 bar) antigel) Pompe Déplacement positif, palette rotative avec vanne de dérivation réglable (250 psi /17,2 bar maximum), rotation dans le sens des aiguilles d'une montre, capacité : 1,33 gpm à 150 psi (5,04 l/min à 10,3 bar). Vitesse nominale : 1725 tr/min, température nominale : 150o F (66o C) Moteur 1/2 HP, 230 VAC monophasé, 50/60 Hz, 1725/1425 RPM, 3.6A, Cote de température: 150 ° F (66o C) Régulateur de pression Pression d'entrée de l'eau : 100 psi (6,9 bar) maximum Pression de sortie de l'eau : 20 psi (1,4 bar) (réglage d'usine) Capteur de pression Plage de pression maximum : 0 - 200 psi (0 - 13,8 bar) Plage de température : -40 - 257o F (-40 - 125o C) Tension d'alimentation : 24 V CC Sortie du signal de pression : 4 mA pour 0 psi, 20 mA pour 200 psi (13,8 bar). Réglé de 1 à 5 V CC avec une résistance de 250 ohms. Vanne proportionnelle Tension d'alimentation : 24 V CC Courant de pleine charge : 500 mA, signal de commande d'entrée : 0-10 V CC. Bobine : tension standard de 24 V CC, courant de fonctionnement : 100-500 mA, Vanne : taille de l'orifice de 3/32”, Cv : 0,14 (complètement ouverte) Pression différentielle de fonctionnement : 115 psi (8,0 bar) ; Débit max.1,5 gpm Température maximum du fluide : 150o F (66o C) Capteur de débit Pression de fonctionnement maximum : 200 psi (13,8 bar), Température de fonctionnement : -4 - 212o F (-20 - 100o C), puissance d'entrée : 5 - 24 V CC à 50 mA maximum, signal de sortie : 58 - 575 Hz, zone d'écoulement : 0,13 - 1,3 gpm Vanne électromagnétique d'air Tension d'alimentation : 24 V CC, pression de fonctionnement maximum : 140 psi (9,7 bar), température de fonctionnement : 32 - 77o F (0 - 25o C) 11 Section 2 2.4 Description Connexions, commandes et indicateurs Les descriptions suivantes des connexions, commandes et indicateurs seront utiles lors du fonctionnement. Interrupteur marche/arrêt – Cet interrupteur contrôle la mise en marche/arrêt de la puissance d'entrée. B. Voyant d'alimentation - Ce voyant s'allume A lorsque l'unité est sous tension. C. Capteur de pression - Entrée du signal du capteur de pression et alimentation de 24 V CC. D. Vanne proportionnelle – Signal de commande de la vanne proportionnelle et alimentation de 24 V CC. K E. Vanne électromagnétique d'air Alimentation de 24 V CC de la vanne électromagnétique pour purger l'eau des tuyaux pour éviter le gel. F. Capteur de débit – Entrée du signal du J capteur de débit et alimentation de 24 V CC. G. Puissance de pompage – 230 V CA de sortie au moteur. L'alimentation est mise en marche/ arrêt par le programme de commande. H. *Air – Entrée d'air à des fins antigel uniquement. J. *Sortie de l'eau – Sortie de l'eau de découpe vers la torche. K. * ENTRÉE de l'eau – Entrée de l'eau de découpe depuis l'alimentation. L. **Commande optionnelle – Il s'agit d'une L commande auxiliaire utilisée uniquement pour le mode de commande optionnelle si le CAN n'est pas disponible. M. *CAN - Connexion CAN. N. **24 V CA/CC - Sortie d'alimentation de 24 V CA pour le système de contrôle du gaz plasma, si le système de contrôle du gaz de protection n'est pas disponible. Ce port est utilisé lorsque le client souhaite effectuer une découpe avec de l'eau comme protection tout le temps ; dans ce cas-là, le système de contrôle du gaz de protection (SCGPR) n'est pas nécessaire. Dans ce cas, le SCIE devra fournir une puissance de 24 V CC/ CA au système de contrôle de gaz plasma (SCGPL). O. Fusibles – Fusible de 10A à action retardée pour une protection complète de l'unité. Le fusible de 1A à action retardée est destiné à la sortie de 24 V CA uniquement. P. *Entrée CA- Alimentation électrique (230 V CA) de toute l'unité. Q. Goujon de mise à la terre – Connecter le châssis de la machine à ce goujon. B A. C D E F SCIE SYSTÈME DE CONTRÔLE D'INJECTION D'EAU MARCHE CAPTEUR DE PRESSION VANNE VANNE ÉLECTRO- CAPTEUR PROPORTION- MAGNÉTIQUE DE DÉBIT NELLE D'AIR ARRÊT PUISSANCE DE POMPAGE G H AIR PROTECTION ANTIGEL N M O 10A COMMANDE OPTIONNELLE CAN 24 V CA/CC 1A P FUSIBLE Q ENTRÉE CA * Connexions requises ** Connexions optionnelles Remarque : Le châssis doit être connecté à la masse de la machine. 12 Section 3 Installation 3.0 Installation 3.1 Emplacements des trous de montage Installer le SCIE dans un site convenable pour maintenir un débit d'air adéquat et sans restrictions à l'intérieur et à l'extérieur de l'armoire. Pour un montage permanent, se référer à la figure ci-dessous pour les dimensions des trous de montage. 0,281” 7,137 mm 0,50” 12,7 mm 10,28” 261,11 mm 16,75” 425,45 mm 3.2 Besoins en eau de découpe Le client doit fournir une source d'eau propre à la WIC de maximiser la vie des consommables. L'eau doit être filtré à un niveau bas de carbonate de calcium (mesurée dans la dureté de l'eau). Cela est essentiel pour la bonne exécution de la buse de la torche. La formation excessive de carbonate de calcium sur la buse modifie le flux d'eau et de produire un arc instable. La dureté de l'eau à la torche doit être inférieure à 2 ppm. Si vous utilisez un conductimètre pour mesurer la pureté de l'eau, le niveau recommandé est le suivant: Résistivité doit être d'au moins 200.000 ohms • cm, la conductivité peut être pas plus de (ou 5 microns S cm). L'eau de source peut exiger un adoucisseur d'eau, système d'osmose inverse ou autre de l'équipement-ionisants pour obtenir ce faible niveau de dureté. Consulter un spécialiste de l'eau pour obtenir des conseils détaillés dans ce domaine. 13 Section 3 Installation 14 Section 4 Fonctionnement 4.0 Fonctionnement 4.1 Fonctionnement en mode de communication CAN En mode de communication CAN, le client doit sélectionner un fichier d'injection d'eau (SDP) tel qu'illustré dans la figure 4.1. S'assurer de sélectionner le type correct de gaz avec l'eau comme protection. Le tableau 4.1 montre la totalité des différents types de gaz utilisés dans le système au plasma m3 G2. Les types de gaz 13 et 14 sont utilisés pour l'injection d'eau. Si la sélection est confirmée dans l'écran des paramètres, le débit d'eau recommandé sera affiché (voir figure 4.2). Après la sélection du fichier, réaliser « l'essai de protection » et l'eau circulera à travers la torche. Si tout est correct, sélectionner « cycle start » (« démarrer cycle ») pour mettre en marche le plasma. Remarque : En mode de communication CAN uniquement, la commande du débit d'eau augmentera automatiquement de 25% pendant l'essai de protection et la marche à sec. Le débit réel sera donc plus élevé de 25% que le débit de commande du CNC pendant l'essai de protection et la marche à sec. Figure 4.1 Figure 4.2 15 Section 4 Fonctionnement Tableau 4.1 Type de gaz, plasma m3 G2 GS 1 2 3 4 5 6 7 8 9 10 11 12 13 14 TYPE DE GAZ GPRGPR1 GPRGPR2 GPR-GPL1 GPRGPL2 GS_N2_O2_N2O2 1 2 2 1 3 1 (DÉBUT GPL1, DÉCOUPE GPL2) N2 O2 N2 O2 N2/O2/AIR O2 GS_AIR_O2_AIRO2 2 2 3 1 3 1 (DÉBUT GPL1, DÉCOUPE GPL2) AIR O2 AIR O2 N2/O2/AIR O2 GS_N2_N2_N2CH4 1 1 2 2 3 2 (DÉBUT N2-GPL2, DÉCOUPE N2GPL2) N2 CH4 N2 N2 N2/O2/AIR N2 GS_N2_H35_AIR 2 - 2 2 2 2 (DÉBUT GPL2, DÉCOUPE GPL1) AIR N2 N2 H35 N2 GS_N2_H35_N2CH4 1 1 2 2 2 2 (DÉBUT GPL2, DÉCOUPE GPL1) N2 CH4 N2 N2 H35 N2 GS_ARG_ARG_AIR 2 - 2 1 1 1 (DÉBUT GPL1, DÉCOUPE GPL1) AIR N2 O2 ARG O2 GS_ARG_ARG_N2 1 2 1 1 1 (DÉBUT GPL1, DÉCOUPE GPL1) N2 N2 O2 ARG O2 GS_AIR_AIR_AIR 2 3 3 3 3 (DÉBUT GPL2, DÉCOUPE GPL2) N2 N2 O2 N2/O2/AIR O2 GS_N2_O2_AIR 1 2 1 3 1 (DÉBUT GPL1, DÉCOUPE GPL2) AIR N2 O2 N2/O2/AIR O2 GS_N2_N2_AIR 2 2 2 3 2 (DÉBUT GPL2, DÉCOUPE GPL2) AIR N2 N2 N2/O2/AIR N2 GS_ARG_O2_N2O2 1 2 2 1 1 1 (DÉBUT GPL1, DÉCOUPE GPL2) N2 O2 N2 O2 ARG O2 GS_ARG_O2_AIRO2 2 - 2 1 1 1 (DÉBUT GPL1, DÉCOUPE GPL2) AIR N2 O2 ARG O2 GS_ARG_ARG_H2O 1 1 (DÉBUT GPL1, DÉCOUPE GPL2) ARG ARG - GPL-GPL1 GPL-GPL2 GS_N2_N2_H2O 2 2 3 2 (DÉBUT GPL1, DÉCOUPE GPL2) N2 N2 N2 N2 16 Section 4 4.2 Fonctionnement commande optionnelle Fonctionnement en mode de Lorsque les communications CAN ne sont pas disponibles, le SCIE peut fonctionner en mode de commande optionnelle. Cela se produit lorsqu'un système plus ancien est mis à niveau avec une torche PT-36. Dans ce mode, toutes les commandes proviennent du connecteur à 10 broches étiqueté « commande optionnelle » sur le panneau arrière du SCIE. Les signaux de ce connecteur à 10 broches sont répertoriés ci-dessous : COMMANDE OPTIONNELLE SCHÉMA DE LA BROCHE (vue externe) A C G F B E D H J K La broche A (+24 V CC) est une sortie pour le client. Le client doit envoyer +24 V CC à travers la broche B pour activer la fonction antigel. La broche D est le signal de défaillance, lequel est normalement élevé ; le niveau du signal provient de la broche C. En cas de défaillance, la broche D se réinitialisera à un niveau bas. Le client doit surveiller la broche D pour détecter d'éventuelles défaillances. Le débit d'eau est fourni au système à travers les broches E et F. Chaque volt donne 0,2 gpm ; par exemple : 5V = >1,0 gpm ou 1V = >0,2 gpm. Le système peut également retourner le débit et la pression d'eau au client. Pour ces deux signaux, les relations de mise en correspondance sont : 5V = >1 gpm pour le débit, 5V = >100 psi (6,9 bar) pour la pression. Les sorties de la broche D (défaillance), la broche G (sortie du débit d'eau) et de la broche H (sortie de la pression d'eau) sont disponibles aussi bien en mode de communication CAN qu'en mode de commande optionnelle. Pour le mode de commande optionnelle, les broches A et J doivent être unies au moyen d'un cavalier pour fournir une alimentation de 24 V CC au PCUA. BROCHE Fonction A B C D E +24 V CC (SORTIE) Antigel externe CNC COM Défaillance COM de référence externe Référence de débit externe Sortie du débit d'eau Sortie de la pression d'eau +24 V CC (depuis la broche A) Châssis F G H J K Une commande de débit d'eau est nécessaire pour démarrer la pompe. Le débit minimum est de 0,15 gpm. Pour le mode de commande optionnelle, chaque volt commandera un débit d'eau de 0,2 gpm. Toutefois, la commande de débit doit respecter les exigences minimum. Si une commande de débit d'eau du CAN est disponible et supérieure aux exigences de débit minimum, le SCIE ignorera la commande de débit d'eau du connecteur à 10 broches. Lorsque la pompe fonctionne, la pression et le débit réel de l'eau sont toujours disponibles depuis le connecteur à 10 broches. Le client peut les utiliser pour régler d'éventuels pannes. 4.3 Précautions concernant le moteur La pompe utilisée dans cette application est équipée d'un dispositif de dérivation réglable pour maintenir la pression à un certain niveau. Avec ses réglages d'usine, la pompe peut augmenter la pression jusqu'à 150 psi (10,4 bar) au-delà de la pression d'entrée. Si l'on permet à la pompe de fonctionner en continue et que le débit est bloqué, la chaleur du moteur peut élever considérablement la température de l'eau. Si de telles chaleurs excessives se produisent, elles peuvent provoquer des pannes du moteur. 17 Section 4 4.4 Fonctionnement Fonction antigel SCIE SYSTÈME DE CONTRÔLE D'INJECTION D'EAU MARCHE Pour les clients résidant dans des régions où les conditions atmosphériques sont rigoureuses, il est recommandé de purger l'eau du SCIE s'il n'est pas prévu d'utiliser l'unité pendant des périodes prolongées. Pour éviter que la torche, les tuyaux et le SCIE ne gèlent, le SCIE est équipé d'un mécanisme antigel en option. De l'air comprimé à 80 psi (5,5 bar) est introduit à travers l'entrée pour chasser l'eau piégée à l'intérieur des composants, des tuyaux et de la torche du SCIE. Pendant la purge, l'eau sortira de la torche et de la soupape d'évacuation. CAPTEUR CAPTEUR VANNE VANNE DE PRESSION PROPORTION-ÉLECTROMAG- DE DÉBIT NÉTIQUE NELLE D'AIR ARRÊT PUISSANCE DE POMPAGE Entrée d'air antigel AIR PROTECTION ANTIGEL Remarque : Pendant le processus de purge, le réglage du régulateur de contre-pression ne doit pas être modifié car la vanne proportionnelle est très sensible à la pression différentielle (115 psi /8,0 bar). Si la valeur du régulateur de contre-pression est modifiée, il est possible que la vanne proportionnelle fonctionne bruyamment car la pression différentielle peut être supérieure à 115 psi (8,0 bar). Cela peut se produire initialement après le démarrage de la pompe, ce qui peut causer un à-coup élevé de pression à travers la vanne proportionnelle. 4.4.1 Procédure antigel 1. Fermer le robinet d'eau. 2. Ouvrir la soupape d'évacuation. (se référer au schéma de circulation des fluides du système de contrôle d'injection d'eau à la page suivante) 3. Sur le CNC, appuyer sur le bouton antigel illustré ci-dessous. 4. Le SCIE ouvrira la vanne électromagnétique d'air. 5. La vanne proportionnelle s'ouvrira lentement jusqu'à atteindre un orifice fixé. (voir la configuration dans la constante de station.) 6. La purge durera au moins 3 minutes pendant que l'eau provient de la torche et de la soupape d'évacuation. 7. Lorsque le temporisateur arrive au bout de son délai ou lorsque le bouton antigel est de nouveau pressé, la vanne électromagnétique d'air et la vanne proportionnelle seront fermées. 8. La purge est terminée. Retour au fonctionnement normal. 1. Fermer la vanne d'évacuation. 2. Ouvrir le robinet d'eau. 3. Sur le CNC, appuyer sur « Shield Gas Test » (« Essai du gaz de protection ») et ensuite « Cut Gas Test » (« Essai du gaz de découpe »). 4. Attendre que l'eau sorte de la torche. 5. Sur le CNC, appuyer sur « Cut Gas Test » et ensuite « Shield Gas Test ». Cela arrêtera l'eau de la torche. 6. Prêt pour un fonctionnement normal. 18 Section 4 Fonctionnement Éléments fournis par le client SOUPAPE D'ÉVACUATION (Vanne ouverte pendant la purge) ROBINET D'EAU TP REG H2O ENTRÉE POMPE FILTRE CLAPET DE NON-RETOUR (ALIMENTATION EN AIR optionnelle) AIR VERS LA TORCHE H2O CLAPET DE NON-RETOUR ENTRÉE VP VANNE ÉLECTROMAGNÉTIQUE D'AIR SORTIE CD RCP Schéma de circulation des fluides du système de contrôle d'injection d'eau En mode de commande optionnelle, le client devra régler la broche B (antigel externe) sur « HIGH » (élevé) pendant au moins 3 minutes pour purger l'eau du SCIE, des tuyaux et de la torche. Une fois que ce signal disparaît, la purge s'arrêtera. La purge s'arrêtera toutefois automatiquement après 3 minutes même si l'antigel externe est encore élevé. Pendant la purge, le CNC du client ignorera toute erreur de débit ou de pression. Lorsqu'il est prêt à effectuer une nouvelle découpe, le CNC du client devra émettre une commande de 0,35 gpm au SCIE pour que la torche/les tuyaux se remplissent d'eau à nouveau. Le CNC du client devra également ignorer les erreurs de débit/pression à ce moment-là. Essai de protection de découpe Fonction antigel 19 Section 4 4.5 Fonctionnement Manifold du régulateur de contre-pression (RCP) Le collecteur du régulateur de contre-pression (réglé en usine à 2,8 bar) est constitué d'un régulateur de contre-pression et de deux clapets anti-retour. L'ensemble est monté sur le régulateur de gaz plasma ou à proximité, aussi près que possible du chalumeau. La fonction du régulateur de contre-pression est de maintenir la pression de l'eau vers le chalumeau et d'assurer une réponse rapide du débit d'eau de coupe vers le chalumeau. En outre, le régulateur de contre-pression permet d'éviter le débit de gaz inverse dans le contrôleur d'injection d'eau dans l'alimentation en gaz de protection. Ceci se fait par l'intermédiaire des deux clapets anti-retour dans le collecteur. Il y a trois entrées vers le régulateur de contre-pression : eau de coupe du contrôleur d'injection d'eau, gaz de protection et rideau d'air du régulateur de gaz de protection ou du régulateur de gaz combiné. Si le système est muni d'un régulateur de gaz de protection, les tuyaux de gaz se protection et de rideau d'air doivent être directement connectés à l'entrée du régulateur de contre-pression. Si le système ne contient pas de régulateur de gaz de protection mais utilise un régulateur de gaz combiné, la sortie du gaz de protection du régulateur de gaz combiné doit être connectée à l'entrée du régulateur de contre-pression à l'aide du tuyau d'arrivée inclus avec le régulateur de contre-pression. Les deux sorties du régulateur de contre-pression sont le gaz de protection ou l'eau, et le rideau d'air vers le chalumeau. En fonction de l'entrée, la sortie peut être soit de l'eau (H2O), soit du gaz de protection. H2O SG Vis de réglage CV1 A/C CV2 REG SG/H2O A/C Figure 4.3 Schéma du régulateur de contre-pression Si la configuration du RCP est altérée ou modifiée pour une raison quelconque, le client devra suivre la procédure ci-dessous pour régler la pression à 40 psi (2,8 bar) : (1) Effectuer « l'essai de protection » pendant 5-10 secondes puis l'arrêter ; (2) Lire la pression d'eau sur Vision 50P. (3) Si la pression d'eau sans débit d'eau n'est pas égale à 40 psi (2,8 bar), ajuster lentement la vis sur le manifold du RCP. Répéter les étapes (1) à (3) jusqu'à ce que la pression soit égale à 40 psi (2,8 bar). Pour le mode de commande optionnelle, envoyer une commande de débit de 0,5 gpm au lieu d'effectuer « l'essai de protection » ; la pression de l'eau pourra être lue depuis le connecteur à 10 broches. 20 section 5maintenance 5.0 Maintenance 5.1 Troubleshooting with ESAB Vision 5x CNC With the ESAB Vision 5x CNC, details of analog outputs, analog inputs, digital outputs and digital inputs can be checked for diagnosis. Below are two screen shots for analog inputs and outputs. For some important measures, the Vision 5x CNC will be monitored and will signal if an error has ocurred. 21 section 5maintenance 5.2 Troubleshooting of CAN Communication Inside the WIC, there is a process control unit (PCU). The PCU regulates the flow and control the valves. This PCU has two LEDs: one green and one yellow. These LEDs indicate status about the PCU’s power, CAN communication, and station selection. When power is on, the green LED must be on. Otherwise, check the power connection. On the CAN bus network, each CAN node has an address. The address for the WIC is 0x15 (S1=1, S2=5). If the station is selected, the yellow LED must be on. In Optional Control Mode, the yellow LED is always on. process control unit leds off Power down 10% on - 90% off Bootloader active 50% on - 50% offApplication active (green) 90% on - 10% offApplication active + Connection to CNC offStation deselected onStation selected (yellow) 22 Unit Select Switc section 5maintenance ACON units are designa switches. These will be a unit needs to be repla rotary switches and set station(s), using chart b 5.3 S1 and S2 Address m3 G2 Plasma System S1 S2 Device 1 - 12 1 - 12 1 - 12 1 - 12 1 - 12 1 - 12 0 1 2 3 4 5 B4 / A6 Lift Shield Gas Control (SGC) Plasma Gas Control (PGC) Remote Arc Starter (RAS) Interface Hub (IFH) Water Injection Control (WIC) Switch Function Station 1...15 1. Station 16...30 1. Each device contains two address switches: S1 and S2. The combination of these switches identify the station and substations on the CAN Bus. Switch 1 designates the station number. Switch 2 designates the substations. Central Station 1...15 23 section 5maintenance 5.4 Faults and Errors In CAN Communication Mode, faults and errors are sensed and displayed on Vision CNC control as a part of the self-diagnostics procedure. Some typical errors are listed below. In Optional Control Mode, if there is a fault, the fault output (pin D, normal high) will reset to 0. Customer CNC needs to monitor this signal, water pressure output (pin H), water flow (pin G), etc. to make a decision. If there is a flow problem, ensure hoses are not blocked, water is turned on, back pressure regulator and proportional valve are working properly, and verify the pump inlet filter is clean. ID Description Possible Solutions Proportional Valve Power Fault 1. Proportional valve (water injection only) has no power. 2. Check 24VDC power inside the water injection box. 11075 Cut Water Flow Is Blocked. 1. 2. 3. 4. 11080 Cut Water Pressure Is Too Low Check water pump. Clean pump filter. 11081 Cut Water Pressure Is Too High Check proportional valve. 11082 Cut Water Flow Is Too Low Check water valve. 11083 Cut Water Flow Is Too High Check proportional valve. 11092 Cut Water Pressure out of range Please check the cut water pressure. 11073 Cut water hose is blocked. Cut water valve is not ON. Smaller nozzle. Proportional valve does not work. 24 section 5maintenance caution The WIC cut water pump motor is set at a default of 230 VAC input power. Proper voltage selection is required. Failure to do so may result in damage to the motor. 5.5 Power Requirement The WIC is powered by 230 VAC, which will be used to operate the motor. The motor has been factory set to 230 VAC, as shown in the diagram below. The working current for this motor is 3.6 amp @ 230 VAC. When turning on/ off this motor, inrush current can be higher. Thus, a 10 amp slow-blow fuse is used to protect the circuit. #1 #2 230 VAC Wiring Diagram caution The customer needs to check the jumper to ensure the correct configuration of 230 vaC. to pump power on front of electrical module 25 section 5maintenance 5.6 Flow Sensor Replacement The Flow Sensor is located at back left side of Pump Module. For replacement part number see replacement parts section of this manual. 1. Remove covers/electrical unit. 2. Unscrew two phillips head screws from rear panel. 3. Unscrew hose using a 3/4” and 5/8” wrench. Flow Sensor assembly can now be removed. Unscrew hose using a 3/4” and 5/8” wrench Unscrew two phillips head screws 4. Replace Flow Sensor assembly. 5. Assemble in reverse fashion. Flow Sensor assembly (for part number see replacement parts section) 26 section 5maintenance 5.7 Pump Filter Replacement The Pump Filter is located at the rear of Pump Module above the pump. For replacement part number see replacement parts section of this manual. 1. 2. 3. 4. 5. 6. 7. Disconnect power and disconnect cables to top electrical unit. Remove electrical unit by removing 4 allen-head screws. Remove covers of Pump Module to expose pump and connections. Unscrew hose using a 3/4” and 5/8” wrench. Disassemble filter assembly using a 7/8” and 1 1/8” wrench. Pump Filter can now be removed and replaced or cleaned. Ensure O-ring is not lost or damaged. Reassemble in reverse fashion. Disconnect cables to top electrical unit. Remove electrical unit and rear cover. Unscrew hose using a 3/4” and 5/8” wrench. Replace or clean filter. Disassemble filter assembly using a 7/8” and 1 1/8” wrench. 27 section 5maintenance 28 section 6 replacement parts 6.0 Replacement Parts 6.1 General Always provide the serial number of the unit on which the parts will be used. The serial number is stamped on the unit nameplate. 6.2 Ordering To ensure proper operation, it is recommended that only genuine ESAB parts and products be used with this equipment. The use of non-ESAB parts may void your warranty. Replacement parts may be ordered from your ESAB Distributor. Be sure to indicate any special shipping instructions when ordering replacement parts. Refer to the Communications Guide located on the back page of this manual for a list of customer service phone numbers. 6.3 WIC Parts Inside the WIC most of the parts can be replaced at the site by a qualified service engineer or by the customer. These parts are listed on the following pages. It is recommended that customers contact technical support before attempting any repairs on these units. Note Bill of material items that have blank part numbers are provided for reference only. These items should be available through local sources. Note Replacement Parts, Schematics and Wiring Diagrams are printed on 279.4mm x 431.8mm (11” x 17”) paper and are included inside the back cover of this manual. 29 section 6 replacement parts 6.4 Hoses and Cables Description Available lengths m. (ft) ESAB P/N 4m (13’) 0558009751 5m (16.4’) 0558009752 6m (19.7’) 0558009753 7m (23’) 0558009754 Water Hose CAN Cable * Input Power Cable ** Optional Control Cable *** (10 Pin Female-open) 8m (26’) 0558009755 9m (29.5’) 0558009756 10m (32.8’) 0558009757 1m (3.3') 0558008464 2m (6.5') 0558008465 3m (10') 0558008466 4m (13') 0558008467 5m (16') 0558008468 6m (19') 0558008469 7m (23') 0558008470 8m (26') 0558008471 9m (30') 0558008472 10m (33') 0558008473 5m (16') 0558008261 10m (33') 0558008262 15m (49') 0558008810 20m (66') 0558008811 25m (82') 0558008812 4.5m (15’) 0558009526 7.6m (25’) 0558009527 15.2m (50’) 0558009528 22.8m (75’) 0558009529 25.0m (82’) 0558009530 * Connects between the Water Injection Control and the Interface Hub. ** One end has a plug that connects to the Water Injection Control, the other end is unterminated and will connect to the customer's 230V single phase supply. *** This cable is optional and is needed only when CAN communication is not available. One end has a 10-pin female connector and the other end is open for customer CNC connection. 30 section 6 replacement parts Description Available lengths m. (ft) ESAB P/N 1m (3.3’) 0558008464 2m (6.5’) 0558008465 3m (10’) 0558008466 4m (13’) 0558008467 5m (16’) 0558008468 CAN Bus Cable Power Cable* (Plasma Gas Control) 6m (19’) 0558008469 7m (23’) 0558008470 8m (26’) 0558008471 9m (30’) 0558008472 10m (33’) 0558008473 11m (36’) 0558008474 12m (39’) 0558008475 13m (43’) 0558008476 14m (46’) 0558008477 15m (49’) 0558008478 20m (66’) 0558008479 25m (82') 0558008809 36m (118') 0558008480 1.5m (5’) 0560947079 3m (10’) 0560947080 4m (13’) 0560947061 5m (16’) 0560947081 6m (19’) 0560947062 7m (23’) 0560947063 8m (26’) 0560947064 9m (30’) 0560947065 10m (33’) 0560947082 12.8m (42') 0560946780 15m (49’) 0560947066 20m (66’) 0560947083 * This cable is used to provide power to plasma gas control if a shield gas control (SGC) is not to be used. 31 section 6 replacement parts 6.5 Recommended Wall Mounted Filter Assembly Description ESAB P/N Filter, FLUFLO Single Shell 2211684 Cartridge Water Filter 2211683 6.6 Back Pressure Regulator (BPR) Assembly Description ESAB P/N BPR mounted to PGC 0558009371 BPR mounted to CGC 0558010158 revision history 1. original release - 09/2010 2. revision 11/2010 - Removed note and added section 6.5. 3. Revision 05/2011 - updated section 4.5 with additional information per D. Wiersema and added p/n’s to replacement parts section. 4. revision 08/2011 - added section 5.7, pump filter replacement. 5. revision 11/2011 - minor updates from K. Li and J. Magee (BOM). 6. revision 06/2012 - minor updates per K. Li. ESAB subsidiaries and representative offices Europe AUSTRIA ESAB Ges.m.b.H Vienna--Liesing Tel: +43 1 888 25 11 Fax: +43 1 888 25 11 85 BELGIUM S.A. ESAB N.V. Brussels Tel: +32 2 745 11 00 Fax: +32 2 745 11 28 THE CZECH REPUBLIC ESAB VAMBERK s.r.o. Prague Tel: +420 2 819 40 885 Fax: +420 2 819 40 120 DENMARK Aktieselskabet ESAB Copenhagen--Valby Tel: +45 36 30 01 11 Fax: +45 36 30 40 03 FINLAND ESAB Oy Helsinki Tel: +358 9 547 761 Fax: +358 9 547 77 71 FRANCE ESAB France S.A. Cergy Pontoise Tel: +33 1 30 75 55 00 Fax: +33 1 30 75 55 24 GERMANY ESAB GmbH Solingen Tel: +49 212 298 0 Fax: +49 212 298 218 GREAT BRITAIN ESAB Group (UK) Ltd Waltham Cross Tel: +44 1992 76 85 15 Fax: +44 1992 71 58 03 ESAB Automation Ltd Andover Tel: +44 1264 33 22 33 Fax: +44 1264 33 20 74 HUNGARY ESAB Kft Budapest Tel: +36 1 20 44 182 Fax: +36 1 20 44 186 ITALY ESAB Saldatura S.p.A. Mesero (Mi) Tel: +39 02 97 96 81 Fax: +39 02 97 28 91 81 THE NETHERLANDS ESAB Nederland B.V. Utrecht Tel: +31 30 2485 377 Fax: +31 30 2485 260 NORWAY AS ESAB Larvik Tel: +47 33 12 10 00 Fax: +47 33 11 52 03 POLAND ESAB Sp.zo.o. Katowice Tel: +48 32 351 11 00 Fax: +48 32 351 11 20 PORTUGAL ESAB Lda Lisbon Tel: +351 8 310 960 Fax: +351 1 859 1277 SLOVAKIA ESAB Slovakia s.r.o. Bratislava Tel: +421 7 44 88 24 26 Fax: +421 7 44 88 87 41 SPAIN ESAB Ibérica S.A. Alcalá de Henares (MADRID) Tel: +34 91 878 3600 Fax: +34 91 802 3461 SWEDEN ESAB Sverige AB Gothenburg Tel: +46 31 50 95 00 Fax: +46 31 50 92 22 ESAB International AB Gothenburg Tel: +46 31 50 90 00 Fax: +46 31 50 93 60 SWITZERLAND ESAB AG Dietikon Tel: +41 1 741 25 25 Fax: +41 1 740 30 55 North and South America ARGENTINA CONARCO Buenos Aires Tel: +54 11 4 753 4039 Fax: +54 11 4 753 6313 Asia/Pacific CHINA Shanghai ESAB A/P Shanghai Tel: +86 21 5308 9922 Fax: +86 21 6566 6622 INDIA ESAB India Ltd Calcutta Tel: +91 33 478 45 17 Fax: +91 33 468 18 80 INDONESIA P.T. ESABindo Pratama Jakarta Tel: +62 21 460 0188 Fax: +62 21 461 2929 JAPAN ESAB Japan Tokyo Tel: +81 3 5296 7371 Fax: +81 3 5296 8080 MALAYSIA ESAB (Malaysia) Snd Bhd Shah Alam Selangor Tel: +60 3 5511 3615 Fax: +60 3 5512 3552 SINGAPORE ESAB Asia/Pacific Pte Ltd Singapore Tel: +65 6861 43 22 Fax: +65 6861 31 95 Representative offices BULGARIA ESAB Representative Office Sofia Tel/Fax: +359 2 974 42 88 EGYPT ESAB Egypt Dokki--Cairo Tel: +20 2 390 96 69 Fax: +20 2 393 32 13 ROMANIA ESAB Representative Office Bucharest Tel/Fax: +40 1 322 36 74 RUSSIA-- CIS ESAB Representative Office Moscow Tel: +7 095 937 98 20 Fax: +7 095 937 95 80 ESAB Representative Office St Petersburg Tel: +7 812 325 43 62 Fax: +7 812 325 66 85 Distributors For addresses and phone numbers to our distributors in other countries, please visit our home page www.esab.com SOUTH KOREA ESAB SeAH Corporation Kyungnam Tel: +82 55 269 8170 Fax: +82 55 289 8864 UNITED ARAB EMIRATES ESAB Middle East FZE Dubai Tel: +971 4 887 21 11 Fax: +971 4 887 22 63 BRAZIL ESAB S.A. Contagem--MG Tel: +55 31 2191 4333 Fax: +55 31 2191 4440 CANADA ESAB Group Canada Inc. Missisauga, Ontario Tel: +1 905 670 02 20 Fax: +1 905 670 48 79 MEXICO ESAB Mexico S.A. Monterrey Tel: +52 8 350 5959 Fax: +52 8 350 7554 USA ESAB Welding & Cutting Products Florence, SC Tel: +1 843 669 44 11 Fax: +1 843 664 57 48 ESAB AB SE-- 695 81 LAXÅ SWEDEN Phone +46 584 81 000 www.esab.com 041227