Telwin SUPERIOR PLASMA 60 HF Manuel utilisateur
Cod.988407
SUPERIOR PLASMA 60 HF inver ter
SOMMAIRE
PAG
FONCTIONNEMENT ET SCHEMAS ELECTRIQUES…...2
- Schéma bloc
- Analyse schéma bloc
- Illustrations
- Schémas électriques
2
3
5
7
GUIDE POUR LA REPARATION.................................... 12
- Equipement nécessaire 12
- Prescriptions générales pour les réparations 13
- Détection des pannes et interventions sur machine 13
- Essai de fonctionnement final machine
- Illustrations
17
20
LISTE PIECES DETACHEES...........................................24
FICHE RÉPARATION.......................................................27
“ r e p a r a t i o n n o - p r o b l e m ”
SUPERIOR PLASMA 60 HF
SCHEMA BLOC
+ -
2
SUPERIOR PLASMA 60 HF
ANALYSE SCHÉMA BLOC
REMARQUE: en l'absence d'indications, les composants sont montés sur la carte primaire ou sur la machine.
Bloc 1
Filtre EMC
Composé de: C1, C2, C3, C4, C5, C6, C7, L1, L2, L3 (carte filtre d'entrée)
Évite la propagation de perturbations provenant de la machine vers la ligne d'alimentation et vice versa.
Bloc 2
Varistor
Composé de: RV1, RV2, RV3 (carte filtre d'entrée)
Évite l'entrée de perturbations (spike) provenant de la ligne d'une ampleur supérieure à 400V dans la machine.
Bloc 3
Pont redresseur
Composé de: D19, D10
Convertit la tension alternative secteur en tension continue pulsatoire.
Bloc 4
Précharge
Composé de: K1, K2, R3, R9
Évite la formation de courants transitoires élevés risquant d'endommager l'interrupteur secteur, le pont redresseur et les condensateurs électrolytiques.
Lors de la mise en fonction du générateur, les relais K1 et K2 sont désexcités, les condensateurs C6, C17, C22, C38, C45 et C47 sont alors chargés au moyen de R3 et R9. Lorsque les condensateurs sont chargés, les relais sont excités.
Bloc 5
Filtre
Composé de: C6, C17, C22, C38, C45, C47
Convertit la tension pulsatoire provenant du pont redresseur en tension continue.
Bloc 6
Hacheur
Composé de : Q3, Q4, Q5, Q12, Q13, Q14
Convertit la tension continue provenant du filtre en une onde carrée à haute fréquence (environ 32,5 KHz) en mesure de piloter le transformateur de puissance.
Régule la puissance en fonction du courant/tension de soudage requis.
Bloc 7
Transformateur de courant
Composé de: T1
Le T.A. permet de mesurer le courant circulant sur le primaire du transformateur de puissance et de transmettre l'information au bloc15 (détecteur et régulateur de courant primaire).
Bloc 8
Transformateur de puissance
Composé de: T1
Réduit la tension convertie par le bloc 6 (hacheur) et adapte tension et courant aux valeurs nécessaires au processus de soudage.
Sépare en outre galvaniquement le primaire du secondaire (circuit de soudage de la ligne d'alimentation).
Bloc 9
Diodes secondaire
Composé de: D1, D2, D3, D4, D5 (carte secondaire)
N.B. Certaines versions peuvent présenter 4 diodes de puissance
(D1, D2, D3, D4).
D1 et D2 éliminent la partie négative de la tension du secondaire.
D3, D4 et D5 font recirculer le courant de l'inductance en sortie durant la période de non conduction des IGBT.
Bloc 10
Inductance et shunt
Composé de: L1, R1 et R2
L’inductance nivelle le courant de sortie des diodes de la carte secondaire en le rendant pratiquement continu. Le shunt R1 lit le courant de l'arc pilote, le shunt R2 lit le courant circulant dans l’inductance et le transmet au bloc 20 (amplificateurs shunt) pour l'élaboration des données.
Bloc 11
Filtre EMC secondaire
Composé de: C1, C2
Évite la propagation des perturbations provenant du générateur vers les câbles de soudage et vice-versa.
Bloc 12
Transformateur HF
Composé de: T2
Le transformateur HF élève le signal provenant du bloc 40
(générateur hf) en élevant l'impulsion de tension dans le secondaire lors de l'amorçage de l'arc.
Procède en outre à isoler le circuit de soudage du circuit primaire.
Bloc 13
Alimentation flyback
Composé de: U4, Q6, T3, U1,U2, U3
Utilise une technique de commutation pour transformer et stabiliser la tension obtenue du bloc 5 (filtre) et fournit 2 valeurs de tension de 27V permettant une alimentation correcte du bloc 14
(driver). Fournit en outre trois autres tensions stabilisées (U1, U2,
U3) de -12V, +5V et +12V principalement utilisées pour alimenter la carte de contrôle.
Bloc 14
Driver
Composé de: U1(carte isolateurs optiques), Q7, Q8 et U2 (carte isolateurs optiques), Q9, Q10.
Détecte le signal provenant du bloc 13 (alimentation flyback) et, sous la commande du bloc 16 (formateur durée de cycle), l'adapte au pilotage du bloc 6 (hacheur).
Bloc 15
Détecteur et limiteur de courant primaire
Composé de: D3, R1, R2, R3, et R9 et R16 (carte contrôle)
Détecte et limite le signal provenant du bloc 7 (transformateur de courant) et définit le courant maximum primaire admissible, avant de redimensionner le signal de façon à pouvoir l'élaborer et le comparer dans le bloc 16 (formation durée de cycle).
Bloc 17
Additionneur
Composé de: U4A, U4B (carte contrôle)
Rassemble toutes les informations provenant du bloc 21
(régulateur courant maximal) et du bloc 19 (micro-contrôleur) avant de les transmettre au bloc 16 (formateur durée de cycle).
Bloc 18
Bloc alarmes
Composé de: Q3, D12, D15 (carte contrôle)
Lors de la détection d'une alarme, limite radicalement le courant de sortie de la machine en agissant et en altérant directement le signal de référence obtenu du bloc 16 (formateur durée de cycle) dans les cas suivants:
1) Intervention capsule thermostatique sur dissipateur diodes de la carte secondaire.
2) Intervention capsule thermostatique sur transformateur de puissance.
3) Intervention en cas de sous-tension.
4) Intervention en cas de surtension.
5) Court-circuit en sortie (pince por te-électrode et câble de masse connectés entre eux ou électrode collée sur la pièce à souder).
3
SUPERIOR PLASMA 60 HF
Bloc 19
Microcontrôleur
Composé de: U7 (carte contrôle)
La fonction principale de ce bloc est d'élaborer et de gérer les informations provenant des blocs voisins.
Bloc 20
Amplificateurs Shunt
Composé de: U3A, U3C, U4C, U4D et U5 (carte contrôle)
Les deux shunts (R1 et R2) amplifient les signaux provenant du bloc 10 (inductance shunt) et fournissent deux types de signaux en sortie:
1) Signal analogique: permet d'obtenir un arc pilote et un arc de coupe à courants contrôlés (signal provenant du shunt R1).
2) Signal numérique: au moyen de deux comparateurs installés en aval des amplificateurs shunt, permet d'obtenir deux signaux (présence arc pilote et présence arc de coupe) lesquels sont transmis au microcontrôleur (signal provenant du shunt R2).
Bloc 21
Régulation du courant maximal
Composé de: R55 (carte contrôle)
Élabore les informations provenant du bloc 20 (amplificateurs shunt) et, au moyen de R55, permet l'étalonnage du courant maximal de soudage pouvant être distribué par le générateur.
Bloc 22
Protection surtension
Composé de: U5A, R38, R40
Si la tension secteur dépasse la valeur maximale, la protection intervient (tolérance admise d'environ 15% autour de la valeur de la tension d'alimentation; la protection intervient à l'extérieur de cette gamme).
Bloc 23
Protection sous-tension
Composé de: U5B, R30, R32
Si la valeur de la tension secteur est inférieure au minimum autorisé, la protection intervient (tolérance admise d'environ
±15% autour de la valeur de la tension d'alimentation; la protection intervient à l'extérieur de cette gamme).
Bloc 24
Thermostat diodes secondaire
Composé de: capsule thermostatique ST1
Si la température du dissipateur de la carte secondaire atteint
70°C (valeur approximative), la protection intervient. Le rétablissement s'effectue automatiquement avec la disparition de la condition d'alarme.
Bloc 25
Thermostat inductance
Composé de: capsule thermostatique ST2
Si la température de l'inductance atteint une température trop
élevée, la protection intervient. Le rétablissement s'effectue automatiquement avec la disparition de la condition d'alarme.
Bloc 26
DEL rouge d'alarme générale
Composé de: D37 (carte contrôle)
S'allume en cas d'intervention de surtension ou de sous-tension secteur, ou en cas d'intervention des capsules thermostatiques.
Bloc 27
DEL jaune manque air
Composé de: D36 (carte contrôle)
S'allume simultanément avec la diode del rouge D37 en cas de
.
pression d'air insuffisante ou nulle.
Bloc 28
DEL jaune tension torche
Composé de: D38 (carte contrôle)
S'allume sur pression du poussoir torche et indique que le circuit de coupe est activé
Bloc 29
Del verte d'alimentation
Composé de : D40 (carte contrôle)
S'allume si la machine est alimentée et prête au fonctionnement.
Bloc 30
DEL jaune absence phase
Composé de: D51 (carte contrôle)
S'allume simultanément avec la diode del rouge D37 en cas d'absence de phase d'alimentation
Bloc 31
Potentiomètre courant
Composé de: R95 (carte contrôle)
Permet de créer la référence de tension nécessaire à la régulation du courant en sortie: varie le courant de la valeur minimale à la valeur maximale.
Bloc 32
Poussoir air
Composé de: S3 (carte contrôle)
La pression du poussoir entraîne la sortie d'air continue de la torche pendant 30 secondes environ. Utilisation type: refroidissement de la torche et régulation de la pression sur le manomètre.
.
Bloc 33
Absence phase
Composé de: ISO2, ISO3 (carte isolateurs optiques), UT (car te contrôle)
La protection intervient en cas d'absence de l'une des trois phases de la tension secteur.
Bloc 34
Transformateur auxiliaire
Composé de: T3
Fournit à la machine deux tensions alternatives de valeur différente:
- 230 Vac pour l'alimentation des blocs 39 (activation
électrovanne et hf) et 37 (activation arc pilote);
- 9 Vac pour l'alimentation du bloc 35 (protection hf).
Bloc 35
Protection HF
Composé de: P01, RL01, C09, C08, R01, R02 (carte filtre hf)
La protection HF est alimentée par le bloc 34 (transformateur auxiliaire) lorsque le bloc 36 (poussoir torche) est enfoncé; le relais RL01 transmet le signal au bloc 19 (microcontrôleur) pour son élaboration. La protection hf isole également la carte de contrôle de la haute fréquence pour éviter que le signal résiduel provenant des câbles du poussoir torche n'entre dans la carte.
Bloc 36
Poussoir torche
Composé de: torche plasma
L'actionnement du poussoir torche déclenche l'amorçage de l'arc pilote.
Le signal est redimensionné pour son élaboration et sa comparaison dans le bloc 17 (additionneur).
Bloc 37
Activation arc pilote
Composé de: Q8, K1 (carte contrôle) et K3 (carte filtre hf).
Sur actionnement du poussoir torche, le bloc 19 (microcontrôleur) transmet un signal au bloc 37; à l'aide du bloc 38 (filtre hf), ce dernier génère l'arc pilote.
4
SUPERIOR PLASMA 60 HF
Bloc 38
Filtre HF
Composé de: R1, R2, C2, C2A, C3, C4 et C5 (carte filtre hf)
Le signal provenant du bloc 10 (inductance shunt) est filtré et transmis au bloc 37 (activation arc pilote).
Bloc 39
Validation électrovanne 1, électrovanne 2 et HF
Composé de : Q8, Q7, Q6 (carte contrôle) et K1, K2, K3 (carte contrôle auxiliaire)
Sur actionnement du poussoir torche, le bloc 19
(microcontrôleur) transmet trois signaux au bloc 39; ce dernier adapte les signaux au pilotage des blocs 40 (générateur hf), 41
(électrovanne 1) et 42 (électrovanne 2).
Bloc 40
Générateur HF
Composé de: carte hf
Au moyen du signal transmis par le bloc 39 (validation
électrovanne hf), produit un signal haute fréquence et le transmet au bloc 12 (transformateur hf).
Bloc 41
Électrovanne 1
Composé de: Y1
L'enfoncement du poussoir torche entraîne l'excitation de l'électrovanne Y1 et la sortie de l'air pour l'amorçage de l'arc pilote.
Bloc 42
Électrovanne 2
Composé de: Y2
L'amorçage de l'arc entraîne l'excitation de l'électrovanne Y2
(l'électrovanne Y2 reste excitée) et permet l'augmentation du débit d'air dans la torche.
Bloc 43
Ventilateur
Composé de: V1 et V2
Permet le refroidissement des composants de puissance et est alimenté par le bloc 13 (à 12 Vdc).
ILLUSTRATIONS
Carte filtre d’entrée
(1) FILTRE EMC
(2)
VARISTORE
(5)
FILTRE
(3)
PONT REDRESSEUR
(1) FILTRE EMC
(6)
CHOPPER
(13)
DRIVER
Carte primaire
OPTO
ISOLATEUR
(U1,U2, ISO2, ISO3)
(4) PRÉCHARGE
(6) CHOPPER
5
(7) TRANSFORMATEUR
DE COURANT
(12) ALIMENTATEUR
FLY-BACK
SUPERIOR PLASMA 60 HF
Carte secondaire
(24)
THERMOSTAT
DIODES SECONDAIRE
(9) DIODES
SECONDAIRE
(21)
RÉGULATION
DU COURANT MAXIMAL
Carte contrôle
(15) DÉTECTEUR ET
LIMITEUR DE COURANT PRIMAIRE
(16) FORMATEUR
DUTY CYCLE
(19)
MICROCONTRÔLEUR
(16)
SOMMATEUR
(26)
DEL ROUGE
D’ALARME GÉNÉRALE
(27)
DEL JAUNE
MANQUE AIR
(28)
DEL JAUNE
TENSION TORCHE
(29)
DEL VERTE
D'ALIMENTATION
(31)
POTENTIOMETRE
COURANT
(30)
DEL JAUNE
ABSENCE PHASE
6
(32)
POUSSOIR AIR
SUPERIOR PLASMA 60 HF
SCHÉMAS ÉLECTRIQUES
Schéma électrique général
Schéma électrique de la carte filtre d’entrée
7
SUPERIOR PLASMA 60 HF
Schéma électrique de la carte du primaire – puissance
Schéma électrique de la carte du primaire – driver
8
SUPERIOR PLASMA 60 HF
Schéma électrique de la carte du primaire alimentateur
Schéma électrique carte contrôle
9
SUPERIOR PLASMA 60 HF
Schéma électrique carte contrôle
Schéma électrique carte contrôle
10
SUPERIOR PLASMA 60 HF
Schéma électrique de la carte du secondaire
Schéma électrique de la carte filtre HF
Schéma contrôle auxiliaire
Schéma électrique de la carte filtre HF
11
SUPERIOR PLASMA 60 HF
EQUIPEMENT NÉCESSAIRE
6
5
4
1
3
2
7
9 8
INSTRUMENTS INDISPENSABLES
1 Oscilloscope à double trace code 802401 (*)
2 Charge statique code 802111 (*)
3 Variac
0 - 500v 4500VA code 802440
(*)
4 Multimètre digital
5 Sonde de Hall
6 Alimention HV code 802406
code 802403 (*)
INSTRUMENTS UTILES
7 Poste de dessoudure
DIVERS
8 Pince à becs plats
9 Pince coupante
(*) Les instruments ayant un code peuvent être fournis par la maison Telwin. Leur prix de vente est communiqué sur demande!
12
SUPERIOR PLASMA 60 HF
ATTENTION:
AVANT DE PROCÉDER À TOUTE RÉPARATION DE
LA MACHINE, LIRE ATTENTIVEMENT LE MANUEL
D'INSTRUCTIONS
ATTENTION:
LES OPÉRATIONS D'ENTRETIEN CORRECTIF
DOIVENT EXCLUSIVEMENT ÊTRE EFFECTUÉES
PAR UN PERSONNEL QUALIFIÉ DANS LE
SECTEUR ÉLECTRIQUE ET MÉCANIQUE.
ATTENTION:
TOUT CONTRÔLE EFFECTUÉ SOUS TENSION À
L'INTÉRIEUR DE LA MACHINE COMPORTE DES
RISQUES DE CHOC ÉLECTRIQUE GRAVE EN
CAS DE CONTACT DIRECT AVEC LES PARTIES
SOUS TENSION ET/OU DES RISQUES DE
LÉSIONS EN CAS DE CONTACT DIRECT AVEC
LES ORGANES EN MOUVEMENT.
Le câblage de la figure 1B est fourni en même temps que l'alimentation HV (KIT câblage cod. 902760); comme solution alternative, les câblages de la figure 1B et 2B peuvent également
être construits sans difficulté en se reportant aux schémas
électriques suivants:
FIGURE 1B
0.20 mm
2
Connecteur carte controle
5
6
7
8
1
2
3
4
9
10
11
12
JC
AMP MODUII
5
6
7
8
1
2
3
4
Connecteur carte primaire
9
10
11
12
JP
AMP MODUII
FIGURE 2B
S1
Poussoir torche
Connecteur carte controle
5
6
7
3
4
1
2
10
11
8
9
12
JP2
AMP MODUII
MODULE ALIMENTATION HT
L'ALIMENTATION HT est utilisée pour garantir le fonctionnement de l'alimentation à commutation (circuit sur carte primaire fournissant les tensions auxiliaires), même en cas de fonctionnement de la machine à basse tension.
Le module peut être construit sans difficulté en se reportant aux schémas électriques de la figure A, et avec les composants suivants:
T1 = transformateur d'isolation 230-230V 50VA(*)
D1 = pont redresseur 36MB 80 (code 112357)
C1 = condensateur électrolytique 470uF 400V ALL
(code112514)
R1 = résistance 10 ohms 5W 5%
R2 = résistance 100K ohms 2W 5%
F1 = fusible retardé 1,5 A Porte-fusible 5X20mm
Faston femelle rouge et noir Boîtier en plastique.
FIGURE A
F1
R1
T1
D1
C1
R2
REMARQUE: Pour procéder aux essais machine à basse tension, il est également nécessaire d'utiliser deux câblages d'essai adéquats (Fig. 1B 2B) permettant de forcer plusieurs signaux d'alarme entre la carte primaire, la carte de contrôle et la carte filtre hf.
PRESCRIPTIONS GÉNÉRALES POUR LA
RÉPARATION
On trouvera ci-dessous les règles pratiques auxquelles se conformer pour une réparation correcte.
A) Manipuler les composants électroniques actifs, en particulier
IGBT et DIODES de puissance, en respectant les règles
élémentaires de protection antistatique (utilisation de chaussures ou de brassards antistatiques, plans de travail antistatiques, etc.)
B) Pour garantir le flux thermique entre composants
électroniques et dissipateur, toujours prévoir une légère couche de pâte thermo conductrice (ex. COMPOUND
GREASIL MS12) sur les zones de contact.
C) Les résistances de puissance (en cas de nécessité de remplacement) doivent toujours être soudées en les soulevant
à 3 mm min. de la carte.
D) En cas de retrait du silicone appliqué sur certains points des cartes, il est nécessaire d'en rajouter ensuite. NB. Utiliser uniquement des silicones à réticulation oximique ou neutre non conducteurs (ex. DOW CORNING 7093). Dans le cas contraire, laisser le silicone réticuler avec des points de potentiel différents (Conducteurs électriques IGBT, etc.) avant de procéder à l'essai de la machine.
E) L'étamage des dispositifs avec semi-conducteur doit être effectué en respectant les limites maximales de température
(généralement 300°C pendant 10 secondes max.).
Accorder une extrême attention aux phases de démontage et de montage des différents éléments de la machine. Conserver les petits composants et les éléments démontés de la machine pour les remonter ensuite de façon identique lors du procédé inverse de montage (les éléments endommagés ne doivent jamais être éliminés, mais remplacés en se reportant à la liste des pièces de rechange à la fin de ce manuel).
H) Ne jamais modifier les car tes (éventuellement réparées) ou câblages sans l'autorisation préalable de Telwin.
I) Pour toute information supplémentaire concernant caractéristiques et fonctionnement de la machine, se reporter
ATTENTION! L'intérieur de la machine en fonctionnement présente des valeurs de tension dangereuses: éviter tout contact avec les cartes la composant quand la machine se trouve sous tension.
13
SUPERIOR PLASMA 60 HF
D É T E C T I O N D E S P A N N E S E T
INTERVENTIONS SUR MACHINE
1.0 Démontage de la machine
Toutes les interventions doivent être effectuées en conditions de sécurité, avec le câble d'alimentation débranché de la prise secteur.
dévisser les 8 vis fixant les 2 boîtiers en plastique (4 par boîtier) à l'avant et à l'arrière (figure 1A);
dévisser les 8 vis fixant le capot à la structure (figure 1B);
retirer le capot (figures 1B) en exerçant une légère traction vers l'extérieur;
dévisser les 4 vis fixant le fond à la structure (figure 2A et 2B);
séparer la structure métallique supérieure du fond et la poser sur le banc de travail (figure 2A et 2B).
REMARQUE: le fond fait partie intégrante de la structure de support et doit être retiré en cas de nécessité d'accéder aux cartes internes.
La réparation terminée, procéder en sens inverse pour le montage du capot et des boîtiers.
2.0 Nettoyage interne de la machine
Nettoyer soigneusement les composants du générateur pour soudage avec un jet d'air comprimé: la saleté représente un risque potentiel pour les parties à haute tension, et compromet la séparation galvanique entre les cartes primaire et secondaire.
Accorder une attention particulière au nettoyage des pièces suivantes:
Ventilateur d'extraction air fixé sur la partie frontale (figure
2A)
Contrôler que la saleté ne compromet pas la rotation des pales; si le problème persiste après le nettoyage, remplacer le ventilateur.
Ventilateur d'introduction air fixé sur la partie arrière (figure
2B)
Contrôler que la saleté ne compromet pas la rotation des pales; si le problème persiste après le nettoyage, remplacer le ventilateur.
Carte primaire (figure 5)
- conducteurs électriques IGBT Q3,Q4,Q5, Q12, Q13, Q14;
- conducteurs électriques diodes de recirculation D7, D24;
- conducteur électrique diodes sur réseaux "snubber" D4, D27;
- zones de connexion avec boîte noire (contient la carte où sont appliqués les isolateurs optiques du circuit de commande).
Carte secondaire (figure 4)
- diodes de puissance D2, D4, D5;
- capsule thermostatique sur dissipateur (figure 3);
- shunt SH1 et SH2.
Groupe transformateur de puissance et inductance
En cas de nécessité d'extraction de la carte primaire; il est
également possible d'accéder aux éléments sur le côté de la carte secondaire pour effectuer un nettoyage rapide).
Composants fixés sur le fond (figure 4)
En cas de retrait de la carte primaire et de la carte secondaire
(avec le diaphragme), nettoyer soigneusement les composants installés sur le fond:
unité groupe air;
carte filtre d'entrée;
carte HF;
carte filtre HF;
transformateur HF;
carte contrôle auxiliaire.
3.0 Examen visuel de la machine
C o n t r ô l e r l ' a b s e n c e d e d é f o r m a t i o n s m é c a n i q u e s , bossellements, connecteurs endommagés et/ou déconnectés.
Vérifier que le câble d'alimentation n'est pas endommagé ni débranché intérieurement et que les ventilateurs fonctionnent lorsque la machine est en fonction. Contrôler que les composants
énumérés ci-dessous ne présente aucun signe de brûlure ou de rupture:
14
Interrupteur d'alimentation (figure 2B)
Au moyen du multimètre, contrôler si les contacts sont collés ou ouverts. Cause probable:
choc mécanique ou électrique (ex. pont redresseur ou IGBT en court-circuit, manœuvre sous charge).
Potentiomètre de courant carte de contrôle R95(figure 2A)
Cause probable:
choc mécanique.
Commutateur sélection mode de soudage carte de contrôle
S3 (Figure 2A)
Cause probable:
choc mécanique.
Relais K1 et K2 carte primaire (figure 5)
Cause probable:
voir interrupteur d'alimentation. N.B. Si les contacts du relais sont collés ou sales, ne pas tenter de les détacher ni de les nettoyer, mais remplacer le relais.
Condensateurs électrolytiques C6, C17, C38, C45 carte
primaire (figure 5)
Cause probable:
choc mécanique;
machine connectée à une tension de ligne bien supérieure à
400Vac;
conducteurs électriques d'un ou plusieurs condensateurs rompus: les éléments restants sont soumis à des sollicitations excessives et s'endommagent lors du réchauffage;
vieillissement après un nombre important d'heures de fonctionnement;
surchauffe provoquée par la panne des capsules thermostatiques.
IGBT Q3, Q4, Q5, Q12, Q13, Q14 (figure 5)
Cause probable:
réseau snubber interrompu;
panne du circuit de commande (driver);
mauvais contact thermique entre l'IGBT et le dissipateur (ex. vis de fixation desserrée: contrôler);
surchauffe excessive due à une anomalie de fonctionnement.
Diodes primaire D4, D7, D24, D27 (figure 5)
Cause probable:
surchauffe excessive due à une anomalie de fonctionnement.
Diodes secondaire D2,D4, D5 (figure 4)
Cause probable:
réseau snubber interrompu;
mauvais contact thermique diodes-dissipateur (ex. vis de fixation desserrées: contrôler);
anomalie connexion sortie de la machine.
Shunt SH1 et SH2 carte secondaire (figure 4)
Contrôler l'éventuel changement de coloris. Cause probable :
surchauffe due au relâchement des vis connectant les dérivations aux circuits du secondaire.
Transformateur de puissance et inductance filtre (figure 3)
Après accès aux composants sur le fond:
Varistors carte filtre d'entrée RV1,RV2,RV3 (figure 3)
Cause probable:
tension d'alimentation bien supérieure à 400Vac.
Relais K1, K2 et K3 carte contrôle auxiliaire (figure 4)
Cause probable:
choc mécanique ou électrique. N.B. Si les contacts du relais sont collés ou sales, ne pas tenter de les détacher ni de les nettoyer, mais remplacer le relais. Contrôler également que les connecteurs sont solidement branchés à la carte.
Relais K3 et K4 carte filtre HF (figure 3)
Cause probable:
choc mécanique ou électrique. N.B. Si les contacts du relais sont collés ou sales, ne pas tenter de les détacher ni de les nettoyer, mais remplacer le relais.
Fusible F1 câblage fusible (figure 4)
Cause probable:
- absorption excessive de courant par le réseau.
SUPERIOR PLASMA 60 HF
Transformateur HF (figure 4)
Unité groupe air (figure 4)
Contrôle visuel et contrôle de fonctionnement des composants suivants:
manomètre;
pressostat;
-
électrovannes;
raccord torche;
tuyaux et raccords variés de connexion.
Torche (Figure 1A)
État d'entretien conforme aux indications du manuel d'instructions. Conditions des parties non sujettes à usure du câble de branchement entre torche et machine (isolement).
4.0 Contrôle câblages de puissance et de signal
Il est important de contrôler que tous les branchements sont en bon état et que les connecteurs sont introduits et/ou fixés correctement.
Pour s'en assurer, saisir les câbles entre le pouce et l'index (le plus près possible des Faston ou des connecteurs) et exercer une légère traction vers l'extérieur: les câbles ne doivent pas sortir des
Faston ou des connecteurs.
A) Contrôler en particulier sur la carte de contrôle (figure 6):
câblage (JP3) vers carte primaire (J1);
câblage (CN2) vers carte contrôle auxiliaire (CN2);
câblage (JP2) vers capsules thermostatiques, shunt et carte filtre HF.
B) Contrôler en particulier sur la carte primaire (figure 3):
connexions R,S,T (J3, J4, J5) des 3 phases au commutateur général et en amont de ce dernier: carte filtre d'entrée et câble d'alimentation;
2 connexions entre carte primaire et transformateur de puissance (broche1 TRAFO et broche2 TRAFO);
connexions d'alimentation des 2 ventilateurs sur J9, J10, J11,
J12).
C) Contrôler en particulier sur la carte secondaire (figure 6):
connexions entre le transformateur de puissance et les 2 douilles de la carte secondaire;
connexion correcte de l'inductance de niveau de sortie (entre douille carte secondaire et sortie OUT- de la machine);
connexions sur la dérivation (dissipateur secondaire, lecture dérivation et sortie positive de la machine OUT+);
câblages des capsules thermostatiques dissipateur secondaire et transformateur de puissance (connecter les thermostats en série).
Autres contrôles:
connexion correcte du transformateur HF (entre extrémité de l'inductance et prise dinse OUT- de la machine);
connexion correcte du transformateur HF (J3-A, J8-B) à la carte HF;
- branchements corrects au pressostat et électrovannes.
5.0 Mesures électriques avec la machine hors fonction
A) Au moyen du multimètre numérique réglé sur essai diodes, contrôler les composants suivants (tensions raccords non inférieures à 0,2V):
ponts redresseurs D10, D19 (figure 5);
IGBT Q3, Q4, Q5, Q12, Q13, Q14 (absence de court-circuit entre collecteur-gate et collecteur-émetteur figure 5);
Diodes D1, D2, D3, D4, D5 carte secondaire entre anode et cathode (figure 3).
B) Au moyen du multimètre numérique réglé sur ohms, contrôler les composants suivants:
résistances R3, R9: 47 ohms ±5% 7W (précharge figure 5);
résistances R1, R2, R69, R71: 10 ohms ±10% 11W (snubber primaire figure 5).
15
résistance R1: 10 ohms ±10% 5W (snubber secondaire figure
3).
- essai de continuité de la capsule thermostatique sur transformateur de puissance et dissipateur secondaire: débrancher les Faston (de façon à connecter les thermostats en série) et mesurer la résistance aux extrémités; cette dernière doit être d'environ 0 ohm (figure 3).
6.0 Mesures électriques avec la machine en fonction
ATTENTION
!
Avant de procéder à la détection des pannes, ne pas oublier que le générateur de courant est ici alimenté, et que l'opérateur est donc soumis au risque de choc électrique. Les essais ci-dessous permettent de contrôler le fonctionnement des parties actives et de contrôle de la machine.
6.1
Préparation des essais
A) Déconnecter de la carte primaire les Faston broche1 TRAFO
(J8) et broche2 TRAFO (J2) du transformateur de puissance
(figure 3).
B) Préparer l'oscilloscope avec sonde de tension x100 connectée entre collecteur Q6 (sonde) et condensateur C47 sur le côté de Q3 (masse) sur la carte primaire (figure 5).
C) Déconnecter le cavalier JP2 sur la carte primaire.
D) Connecter la sortie HT de l'alimentation HT sur carte primaire de la façon suivante (figure 5):
(+) Positif (pince) sur la broche du connecteur JP2 sur le côté de la résistance R75;
(-) Négatif (Faston) sur le Faston négatif du pont à diodes D19.
E) Déconnecter les câblages de la carte de contrôle et retirer la carte contrôle (selon les indications reportées ci-dessous).
F) Connecter le câble d'alimentation de la machine à un variac triphasé avec sortie variable 0-500 Vac.
6.2
Essais prévus
A) Allumer l'alimentation HT (sortie HT) et vérifier que les relais de précharge K1 et K2 sur la carte primaire se ferment après un bref délai (figure 5).
B) Au moyen de l'oscilloscope, contrôler que la forme d'onde de la tension entre le collecteur de Q6 (sonde) et le conducteur
électrique de C47 du côté de Q3 (masse), est analogue à celle de la figure C.
FIGURE C
Tolérance ampleur: ±10%
Fréquence: 32,5KHz ±10%
C) Vérifier sur la carte primaire les valeurs des tensions d'alimentation suivantes:
entre cathode de D20 et anode de D21 égale à +28Vdc ±5%;
entre cathode de D12 et anode de D13 égale à +28Vdc ±5%;
entre anode de D11 et bac de U3 égale à +12Vdc ±5%;
entre anode de D6 et bac de U3 égale à +5Vdc ±5%;
entre cathode de D5 et bac de U3 égale à -12Vdc ±5%.
SUPERIOR PLASMA 60 HF
D) Éteindre l'alimentation HV, réinstaller la carte de contrôle et reconnecter les câblages, à l'exception de celui entre primaire (sur
J1) et contrôle (sur J3). Ce dernier doit être remplacé par le câblage d'essai spécifique de la figure 1B (à positionner avec attention), et celui entre la carte de contrôle (sur JP2) et la carte filtre hf (sur J5). Ce dernier doit être remplacé par le câblage d'essai spécifique de la figure 2B.
E) Régler le commutateur S1-8 (commutateur S1 n°8) sur ON pour désactiver la HF et l'alarme de manque d'air (figure 6).
ATTENTION: la tension haute fréquence endommagera irrémédiablement tout instrument connecté à la machine. Avant de poursuivre, contrôler avec attention que le commutateur S1-
8 est désactivé.
F) Rallumer la HV et contrôler les points suivants:
del verte D40 d'alimentation;
extinction du DEL rouge d'alarme machine après 2 secondes environ.
G) Préparer l'oscilloscope avec une sonde x10 connectée entre gate (sonde) et émetteur (masse) de l'IGBT Q3 sur la carte primaire (figure 5). Enfoncer le poussoir torche (poussoir figure
2B) et contrôler les points suivants:
extinction de la DEL D38 tension torche après environ 2 secondes;
forme d'onde affichée analogue à celle de la figure D.
- répéter cet essai sur Q4, Q5, Q12, Q13, Q14 de la carte primaire.
N.B. pour obtenir la forme d'onde, enfoncer le simulateur du poussoir torche à plusieurs reprises, la machine restant en fonction pour une durée maximale d'environ 2 secondes.
FIGURE D
FIGURE E
Tolérance ampleur: ±10%
Fréquence: 32,5KHz ± 10%
Tolérance ampleur: ±10%
Fréquence: 32,5KHz ± 10%
N.B. en cas d'absence de signal et/ou d'alarme machine (DEL jaune allumée), possibilité d'anomalie de la carte de contrôle (la remplacer le cas échéant) ou du circuit pilote des IGBT (figure 5).
H) Éteindre la HV et rétablir les 2 Faston de connexion entre carte primaire et transformateur de puissance (J2 et J8). Allumer la HV et le variac (programmé initialement sur la valeur 0V), fermer l'interrupteur général d'alimentation de la machine et augmenter progressivement la tension du variac jusqu'à la valeur
24Vac.
I) Préparer l'oscilloscope avec sonde x10 branchée entre collecteur (embout) et émetteur (masse) de l'IGBT Q3 sur la carte primaire (figure 5).
Enfoncer le poussoir torche et contrôler les points suivants:
extinction DEL jaune D38 tension torche après environ 2 secondes;
forme d'onde affichée analogue à celle de la figure E;
répéter l'essai sur Q12 carte primaire.
16
J) Éteindre la machine et l'alimentation HV et procéder aux opérations suivantes:
débrancher la HV de la machine;
déconnecter l'oscilloscope;
rétablir le cavalier JP2 sur la carte primaire;
remplacer le câblage d'essai entre carte primaire et carte de contrôle par l'original;
remplacer le câblage du simulateur poussoir torche par l'original.
K) Rallumer la machine et le variac (initialement défini à la valeur de 0V), fermer l'interrupteur général d'alimentation de la machine et augmenter graduellement la tension du variac jusqu'à fermeture des relais K1 et K2 de la carte primaire.
Contrôler que la DEL verte D40 d'alimentation, la DEL rouge D37 d'alarme générale machine et la DEL jaune D51 d'absence de phase sont allumées.
Augmenter la tension sur le variac jusqu'à la valeur 240 Vac
(valeur approximative) et contrôler que les conditions de la machine sont celles indiquées plus haut, à l'exception de la DEL jaune D51 absence de phase qui doit être éteinte.
Augmenter à nouveau la tension sur le variac et contrôler que, entre 330 Vac et 460 Vac (valeur approximative), la machine ne se trouve pas en conditions d'alarme (DEL jaune D35 du panneau
éteinte).
Augmenter enfin la tension sur le variac jusqu'à la valeur de 470
Vac, et contrôler que la machine se replace en conditions d'alarme
(DEL rouge D37 allumée).
N.B. le valeur du variac ne doit jamais dépasser 475 Vac.
Replacer immédiatement le variac à 400 Vac et éteindre la machine.
7.0 Réparation et remplacement des cartes
Si la réparation des cartes se révèle difficile ou impossible, procéder au remplacement complet de ces dernières. Chaque carte est identifiée par un code à 6 chiffres (en sérigraphie blanche sur le côté des composants après le sigle TW). Ce code constitue la référence nécessaire en cas de remplacement: Telwin se réserve la possibilité de fournir des cartes compatibles ayant un code différent.
Attention: avant d'introduire une nouvelle carte, contrôler attentivement qu'elle n'a subi aucun dommage durant le transport.
Les cartes fournies sont soumises à essai préalable et, par conséquent, si le problème persiste après le remplacement, contrôler les autres éléments de la machine. Sauf nécessité pressante, ne jamais intervenir sur les potentiomètres des cartes.
SUPERIOR PLASMA 60 HF
A) Retrait carte primaire (figure 3)
Retirer tous les câblages connectés à la carte et les câbles reliant la carte aux ventilateurs et au transformateur de puissance. N.B. Les connexions entre carte primaire et transformateur de puissance ne doivent en aucun cas être inversés lors du montage de la nouvelle carte
Retirer la carte de contrôle, après avoir ôté les manettes des potentiomètres du panneau frontal, en retirant les câblages et en libérant la carte des 4 colonnes en plastique la fixant à la carte primaire.
Desserrer les 4 vis fixant la carte primaire à la structure métallique.
Retirer la carte en la tournant légèrement vers le haut et le panneau frontal (cette manœuvre peut être facilitée en exerçant une légère traction vers l'extérieur sur la tôle du panneau frontal).
N.B. Pour le montage, procéder en sens contraire.
Remarques importantes sur les opérations de remplacement des IGBT et/ou des ponts redresseurs:
Même si un seul IGBT est endommagé, il est nécessaire de les remplacer tous les 6.
- Sur la carte retirée de la machine, desserrer les 4 écrous de fixation des dissipateurs et les 8 vis de fixation des IGBT et des ponts à diodes (figure 5).
- Débrancher le câblage thermostatique du connecteur JP1.
- Avant de procéder au remplacement, contrôler que les composants pilotant les IGBT ne sont pas également endommagés:
avec un multimètre en ohms, contrôler sur le circuit imprimé l'absence de court-circuit entre le 1° et le 3° plot
(entre gate et émetteur) à hauteur de chaque composant;
les résistances R17, R19, R24, R45, R46 et R47 risquent
également d'être endommagées et/ou les diodes D9, D14,
D22 et D23 de ne pas être en mesure de fonctionner à une tension de Zener correcte (phénomène détecté lors des essais préalables).
- Dessouder les composants, dégager les plots de l'étain et séparer les composants de la carte.
- Nettoyer les dissipateurs des éventuelles aspérités ou saletés.
En cas d'endommagement des IGBT, les dissipateurs peuvent
être eux aussi endommagés de façon irrémédiable: le cas
échéant, remplacer ces derniers.
- Appliquer la pâte thermo conductrice selon les prescriptions générales.
Préparer les composants à remplacer. Dans le cas des IGBT, plier à 90° les conducteurs électriques (ne jamais plier et/ou de tendre la partie de ces derniers proche du bac).
- Installer les composants sur le dissipateur avec les vis de maintien, sans bloquer définitivement ces dernières.
Relier l'unité dissipateurs/composants au circuit en introduisant tous les conducteurs électriques dans les plots et les entretoises filetées sur les 4 orifices de fixation
Fixer les dissipateurs au moyen des écrous et procéder au serrage définitif de la façon suivante:
écrous fixation dissipateurs au circuit avec couple de serrage de 2 Nm ±20%;
- vis de fixation redresseurs à dissipateurs avec couple de serrage de 2 Nm ±20%;
vis de fixation IGBT à dissipateurs avec couple de serrage de 1 Nm ±20%.
Souder les terminaux en évitant que l'étain coule le long de ces derniers.
- Couper du côté composants la partie en saillie des conducteurs électriques et vérifier que ces derniers ne sont pas en court-circuit (en particulier entre gate et émetteur).
N.B. Les 6 IGBT doivent appartenir au même Kit de sélection fourni par Telwin.
B) Retrait carte secondaire (figure 4)
La carte secondaire n'est généralement pas retirée, à moins d'un endommagement du dissipateur dû à une explosion des diodes, et les diodes peuvent être directement remplacées sur la carte montée sur la machine. S'il était néanmoins nécessaire de retirer la carte pour procéder à son remplacement, dévisser les 4 vis la fixant à la structure de la machine, ôter les 3 vis à tête hexagonale fixant la dérivation et reliant le transformateur de puissance, puis débrancher les câblages de la capsule thermostatique. Procéder ensuite au remplacement.
Remarques importantes sur les opérations de remplacement des diodes secondaire (figure 5):
- après avoir renversé la machine, dévisser les vis fixant les composants endommagés au dissipateur et dessouder la languette métallique,
- retirer les composants et nettoyer le dissipateur d'aspérités et saleté,
- appliquer la pâte thermo conductrice selon les prescriptions générales,
poser les composants sur le dissipateur à hauteur des zones de soudage et les fixer au moyen des vis (couple de serrage vis 1,4 Nm ±20%).
- Souder les languettes en ayant soin que l'étain ne provoque pas de court-circuit.
N.B. Vérifier que R1, C1 et C2 (snubber secondaire) sont correctement soudés sur le circuit.
C) Carte de contrôle
Si la panne intéresse la carte de contrôle, il est vivement conseillé de remplacer cette dernière sans procéder à aucune intervention.
ESSAI DE FONCTIONNEMENT FINAL DE
LA MACHINE
L'essai de fonctionnement doit être effectué sur la machine assemblée avant la fermeture de sa chemise. Durant les essais, ne jamais commuter les sélecteurs ni actionner le contacteur de la charge ohmique avec la machine en fonction.
ATTENTION! avant de procéder à l'essai de fonctionnement, ne pas oublier que le générateur de courant est ici alimenté, et que l'opérateur est donc soumis au risque de choc électrique. Les essais ci-dessous permettent de contrôler le fonctionnement du générateur de courant sous charge.
1.1 Préparation des essais
A) Maintenir le commutateur S1-8 (commutateur S1 n°8) sur ON afin de désactiver la HF et l'alarme de manque d'air (figure 6).
ATTENTION: la tension haute fréquence endommagera irrémédiablement tout instrument connecté à la machine. Avant toute intervention, contrôler avec attention que le commutateur
S1-8 est désactivé.
B) Connecter la machine à la charge statique à l'aide des câbles
équipés de prises dinse. N.B. Pour connecter le négatif de la charge statique au raccord torche, utiliser l'adaptateur avec simulateur poussoir torche. Si nécessaire, un adaptateur peut être demandé à Telwin.
C) Brancher une sonde de tension x100 entre collecteur (sonde) et émetteur (masse) de Q5 .
D) Passer la sonde de courant du transducteur à effet Hall sur le câble reliant le transformateur de puissance au Faston broche2
TRAFO (J2) avec flèche de référence entrant dans J2.
E) Connecter ensuite le Hall Probe et la sonde de courant à l'oscilloscope.
F) Déconnecter le cavalier JP2 la carte primaire.
17
SUPERIOR PLASMA 60 HF
G) Connecter la sortie HT de l'alimentateur HT sur la carte primaire de la façon suivante (figure 5) :
- (+) Positif (pince) sur la broche du connecteur JP2 du côté résistance R75;
- (-) Négatif (Faston) sur le Faston négatif du pont à diodes
D19.
H) Déconnecter le câblage de connexion entre carte de contrôle
(J3) et carte primaire (J1) et le remplacer par le câblage d'essai spécifique de la figure 1B (comme précédemment); déconnecter le câblage entre carte de contrôle (sur JP2) et carte filtre HF (sur
J5), et le remplacer par le câblage d'essai spécifique de la figure
2B.
I) Positionner le potentiomètre du courant au minimum (R95) sur la carte contrôle.
J) Brancher le câble d'alimentation de la machine à un variac triphasé avec sortie variable de 0-500 Vac.
1.2 Essais prévus
A) Essai à vide:
Avec la charge débranchée, allumer tout d'abord l'alimentation HV, et vérifier qu'après un bref transitoire (DEL vert allumée) les relais de précharge K1 et K2 (figure 5) commutent et que les ventilateurs entrent en fonction.
-
Allumer la machine et le variac et placer ce dernier sur la valeur de 400 Vac.
- Enfoncer le poussoir torche (poussoir figure 2B) et vérifier que les formes d'onde de tension et de courant affichées au moyen de l'oscilloscope sont analogues à celles de la figure F.
FIGURE F
FIGURE G
Tolérance ampleur: ±10%
Échelle courant: 500mV=5A
0 0 0 0
Numéro du commutateur
Position du commutateur
Tensions aux extrémités de la charge: 86Vdc ±3%
Courant sur charge 15Adc ±5%
C) Essai avec charge nominale:
- Préparer la charge statique avec commutateurs réglés comme au tableau de la figure H; sur le panneau frontal, placer le potentiomètre du courant de soudage à 60A, et mettre la machine sous tension. N.B. si le courant en sortie de charge n'est pas de 60A, étalonner le courant au moyen de R14 de la carte de contrôle (figure 7).
-
Avec la charge introduite, enfoncer le poussoir torche
(poussoir figure 2B), et contrôler que les formes d'onde de tension et courant sont analogues à celles de la figure H.
FIGURE H
Tolérance ampleur: ±10%
Fréquence: 32 KHz ± 10%
Échelle courant: 200mV=2A
Éteindre la machine, le variac et l'alimentateur HV.
-
Déconnecter la machine du variac et de l'alimentation HV.
-
Rétablir le cavalier JP2, le câblage original entre primaire (J1) et contrôle (J3), et le câblage original entre carte contrôle (JP2) et carte filtre HF (J5).
B) Essai avec charge minimale:
- Préparer la charge statique avec commutateurs réglés comme au tableau de la figure G; sur le panneau frontal, placer le potentiomètre du courant de soudage à 12A, connecter la machine à la ligne triphasée 400 Vac et la mettre sous tension.
-
Avec la charge introduite, enfoncer le simulateur poussoir torche placé sur le raccord torche et vérifier que les formes d'onde de tension et de courant sont analogues à celles de la
figure G.
18
Tolérance ampleur:
±10%
Échelle courant: 2V=20A
Numéro du commutateur
Position du commutateur
Tensions aux extrémités de la charge: 104Vdc ±3%
Courant sur charge 60Adc ±2%
N.B. Pour ne pas soumettre la charge statique à une surchauffe excessive, éviter de laisser la machine en fonction durant une période prolongée dans cette condition.
D) Contrôle tension des diodes carte secondaire:
Connecter 2 sondes de tension x100 entre les 2 sorties du transformateur de puissance de la carte secondaire (embouts) et la dérivation vers le dissipateur (masses).
SUPERIOR PLASMA 60 HF
Allumer la machine et placer le potentiomètre du courant au maximum, après avoir connecté les 2 sondes à l'oscilloscope dans les conditions de charge prévues sur le tableau de la
figure H.
-
Avec la charge introduite, enfoncer le poussoir torche
(poussoir figure 2B), et contrôler que les formes d'onde de tension et courant sont analogues à celles de la figure I.
FIGURE I
FIGURE J
Électrode
Buse
Diffuseur isolant
Porte-buse
Tolérance ampleur: 10%
La pointe de tension inverse ne doit pas dépasser 900V
-
Éteindre l'interrupteur général de la machine, retirer la sonde à effet Hall et débrancher l'oscilloscope.
E) Essai de durée
Dans les conditions de charge correspondant au tableau de la
figure H et avec le potentiomètre du courant de coupe au maximum, allumer la machine et maintenir enfoncé le poussoir torche jusqu'à intervention des capsules thermostatiques
(machine en conditions d'alarme).
F) Contrôles du fonctionnement
-
Avec la machine sous tension et en mode veille, enfoncer le poussoir air S3 sur la carte contrôle et vérifier que l'électrovanne reste excitée durant une période de 30 secondes environ (durée du cycle de refroidissement).
-
Contrôler le positionnement correct des câblages et des cartes, repositionner le commutateur S1-8 en position OFF
(Attention! présence de HF sur la torche), et déconnecter la charge statique.
-
Rallumer la machine et contrôler l'allumage des DELs suivantes sur le panneau frontal (figure 7):
-
Del verte D40 (alimentation).
-
Del jaune D36 (pression air insuffisante).
-
Del rouge D37 (alarme générale).
-
Éteindre la machine.
G) Contrôles du fonctionnement torche (figure J)
Si l'essai avec charge statique a été positif mais que l'amorçage de l'arc pilote se révèle difficile ou même impossible, la panne peut être localisée sur la torche. Au moyen du multimètre numérique réglé sur Ohms et la torche installée sur la machine, contrôler la continuité électrique de cette dernière.
a) OUT:
entre la partie centrale de la torche (porte-buse dévissé pour pouvoir accéder à l'intérieur de l'appareil) et la sortie du transformateur HF (OUT-);
b) OUT AP:
entre la partie filetée externe de la torche (porte-buse dévissé pour pouvoir accéder à l'intérieur de l'appareil) et la sortie
Faston OUT AP connecté sur J4 carte filtre HF.
H) Contrôles fonctionnement HF:
-
Pour l'essai suivant, déconnecter tous les instruments ainsi que les Faston J2 et J5 sur la carte HF (figure 4).
-
Avant de continuer, contrôler avec attention que tous les instruments sont déconnectés. Éviter également tout contact corporel avec les sorties ou les parties internes du générateur.
Allumer la machine et, au moyen d'un multimètre numérique réglé sur Volts, contrôler que sur pression du poussoir torche la tension des Faston J2 et J5 (déconnectés) est égale à 230
Vac.
-
Si l'essai précédent s'est révélé positif, la panne peut être localisée dans la carte HF ou dans la carte filtre HF (poussoir torche). Dans ce cas, contrôler les câblages des cartes; si le problème se représente, remplacer la carte intéressée.
-
Éteindre la machine et procéder à son assemblage définitif.
I) Essai de coupe
Avec la machine préparée conformément aux indications du manuel d'instructions, procéder à un essai de coupe sur une pièce de tôle de fer (épaisseur inférieure à 20 mm). Pour cet essai de coupe, il est nécessaire de prévoir le branchement de l'air comprimé (pression 4,5 bars). Contrôler le comportement dynamique de la machine.
19
SUPERIOR PLASMA 60 HF
ILLUSTRATIONS
VIS
VIS
VIS
VIS
VIS CAPOT
VIS CAPOT
VIS CAPOT
20
SUPERIOR PLASMA 60 HF
DEL JAUNE
TENSION TORCHE
DEL JAUNE
MANQUE AIR
DEL ROUGE
D’ALARME
GÉNÉRALE
VIS
FIXATION
VENTILATEUR
VIS CAPOT
VIS
FIXATION
FOND
DEL VERTE
ALIMENTATION
DEL JAUNE
ABSENCE PHASE
POTENTIOMÈTRE
COURANT
POST-AIR
VIS
FIXATION
VENTILATEUR
VENTILATEUR
AVANT
VIS CAPOT
VIS
FIXATION
FOND
MANOMETRE
SORTIE FIXE
DE LA TORCHE
DE DECUPAGE PRISE DINSE CABLE DE MASSE
ATTACHE DE
L’AIR COMPRIME
VENTILATEUR
ARRIERE
VIS
FIXATION
VENTILATEUR
VIS CAPOT
VIS
FIXATION
FOND
CABLE
D'ALIMENTATION
VIS
FIXATION
VENTILATEUR
VIS CAPOT
VIS
FIXATION
FOND
COMMUTATEUR
ALIMENTATION
GÉNÉRALE
21
SUPERIOR PLASMA 60 HF
CARTE
CONTRÔLE
PIN 1 TRASFO
PIN 2 TRASFO
VIS FIXATION
CARTE PRIMAIRE
VIS FIXATION
TRANSFORMATEUR
DE PUISSANCE
CARTE PRIMAIRE
VIS FIXATION
CARTE
SECONDAIRE
THERMOSTAT
SECONDAIRE
STRUCTURE
METALLIQUE
CARTE
FILTRE
FOND
CARTE
FILTRE
D'ENTRÉE
VARISTOR
D’ENTREE
ÉLECTROVANNE
CARTE
SECONDAIRE
SHUNT1
E SHUNT 2
TRANSFORMATEUR
DE PUISSANCE
PRESSOSTAT
DIODES
DE CIRCULATION
SNUBBER
SECONDAIRE
ÉLECTROVANNE
FUSIBLE
CARTE CONTRÔLE
AUXILIAIRE
TRANSFORMATEUR
AUXILIAIRE
22
CARTE
HF
TRANSFORMATEUR
HF
SUPERIOR PLASMA 60 HF
U2
U3
U1
Q6
IGBT Q3,Q4,Q5
R1 D4
R2
D7
D24
R9
RELE’
K1,K2
R3
C6
C17
C47
CART
JP2
OPTO-ISOLATEURS
R71
DISSIPATEUR
IGBT - DIODES
D27
IGBT
Q12,Q13,Q14
JP3
R69
THERMOSTAT
PRIMAIRE
C45
C38
JP2
S1
CN2
S2
D37 D36 D38 D40 D51 R95
23
S3
SUPERIOR PLASMA 60 HF
ELENCO PEZZI DI RICAMBIO - LISTE PIECES DETACHEES
SPARE PARTS LIST - ERSATZTEILLISTE - PIEZAS DE REPUESTO
Esploso macchina, Dessin appareil, Machine drawing, Explosions Zeichnung des Geräts, Diseño seccionado maquina.
12
37
34
38
32
35
30
31
2 3 5 41 27 46 1 28 44 24 20 4 11
33
39
14
42
21
17
23
7 29 15 19 10 26 23 36 25 8 43 16 18 45 9 6 40
13
22
Per richiedere i pezzi di ricambio senza codice precisare: codice del modello; il numero di matricola; numero di riferimento del particolare sull'elenco ricambi.
Pour avoir les pieces detachees, dont manque la reference, il faudra preciser: modele, logo et tension de I'appareil; denomination de la piece; numero de matricule
When requesting spare parts without any reference, pls specify: model-brand and voltage of machine; list reference number of the item; registration number
Wenn Sie einen Ersatzteil, der ohne Artikel Nummer ist, benoetigen, bestimmen Sie bitte Folgendes: Modell-zeichen und Spannung des Geraetes; Teilliste Nuemmer; Registriernummer
Por pedir una pieza de repuesto sin referencia precisar: modelo-marca e tension de la maquina; numero di riferimento de lista; numero di matricula
24
REF.
1
2
3
4
5
6
7
8
9
10
11
12
13
14
ELENCO PEZZI DI RICAMBIO
PIECES DETACHEES
SPARE PARTS LIST
ERSATZTEILLISTE
PIEZAS DE REPUESTO
Potenziometro
Potentiometre
Potentiometer
Potentiometer
Potenciometro
Resistenza
Resistance
Resistor
Widerstand
Resistencia
Rele'
Relais
Relais
Relais
Relais
Condensatore
Condensateur
Capacitor
Kondensator
Condensador
Raddrizzatore
Redresseur
Rectifier
Gleichrichter
Rectificador
Scheda Filtro
Platine Filtre
Filter Card
Filterkarte
Tarjeta Filtro
Scheda Ausiliario Di Controllo
Platine De Reglage Auxiliare
Auxiliary Control Pcb
Hilfsteuerungskarte
Circuito Ausiliario De Control
Scheda Filtro
Platine Filtre
Filter Card
Filterkarte
Tarjeta Filtro
Scheda Secondario
Fiche Secondaire
Secundary Pcb
SekundÄrtrafokarte
Tarjeta Secundario
Scheda H.f.
Platine H.f.
H.f. Card
H.f. Karte
Tarjeta H.f.
Assieme Riduttore
Reducteur
Gas Regulator
Druckminderer
Reductor De Presion
Cavo
Cable
Cable
Kabel
Cable
Manopola Per Commutatore
Poignee Pour Commutateur
Switch Knob
Schaltergriff
Manija Por Conmutador
Switch Aria
Commutateur Air
Air Switch
Luftschalter
Conmutador Aria
SUPERIOR PLASMA 60 HF
REF.
15
16
17
18
19
20
21
22
23
24
25
26
27
28
ELENCO PEZZI DI RICAMBIO
PIECES DETACHEES
SPARE PARTS LIST
ERSATZTEILLISTE
PIEZAS DE REPUESTO
Elettrovalvola
Electrovanne
Electro Valve
Elektroventil
Electrovalvula
Elettrovalvola
Electrovanne
Electro Valve
Elektroventil
Electrovalvula
Fusibile 1A
Fusible 1A
Fuse 1A
Sicherung 1A
Fusible 1A
Termostato 10,0A
Thermostat 10,0A
Thermal Switch 10,0A
Thermostat 10,0A
Termostato 10,0A
Pressostato
Pressostat
Pressure Switch
Druckanzeige
Presostato
Termostato 10,0A
Thermostat 10,0A
Thermal Switch 10,0A
Thermostat 10,0A
Termostato 10,0A
Commutatore
Commutateur
Switch
Schalter
Conmutador
Cavo Alimentazione
Cable D'alimentation
Mains Cable
Netzkabel
Cable Alimentacion
Ventilatore
Ventilateur
Fan
Ventilator
Ventilador
Trasformatore Di Corrente Ta
Transformateur De Courant Ta
Current Transformer Ta
Stromwandler Ta
Transformador De Corriente Ta
Trasformatore Impulsi
Trasformateur Pulsee
Pulse Transformer
Pulse Transformator
Transformador Pulsado
Trasformatore Hf
Transformateur Hf
Hf Transformer
Hf Trafo
Transformador Hf
Trasformatore Potenza
Trasformateur Puissance
Power Transformer
Leistungstransformator
Transformador De Potencia
Induttanza
Inductance
Inductance
Drossel
Induccion
REF.
29
30
31
32
33
34
35
36
37
38
39
40
41
42
ELENCO PEZZI DI RICAMBIO
PIECES DETACHEES
SPARE PARTS LIST
ERSATZTEILLISTE
PIEZAS DE REPUESTO
Trasformatore Ausiliario
Transformateur Auxiliaire
Auxiliary Transformer
Hilfstransformator
Transformador Auxiliar
Fibbia
Boucle
Buckle
Schnalle
Hebilla
Cinghia
Courroie
Belt
Gurt
Correa
Frontale
Partie Frontal
Front Panel
Geraetesfront
Frontal
Manometro
Manometre
Manometer
Manometer
Manometro
Fondalino
Chassis
Bottom
Bodenteil
Base
Mantello
Capot
Cover
GehÄusedeckel
Panel De Cobertura
Presa Dinse
Prise Dix
Dinse Socket
Dinse Steckdose
Enchufe Dinse
Pinza Di Massa
Pince De Masse
Work Clamp
Masseklemme
Pinza De Masa
Attacco Torcia
Attelage Torche
Torch Connection
Brenneranschluss
Enganche Soplete
Torcia Plasma 6 M
Torche Plasma 6 M
Plasma Torch 6 M
Plasma Brenner 6 M
Antorcha Plasma 6 M
Kit Pressacavo + Ghiera
Kit Presse Cable + Embout
Kit Cable Bushing + Ring Nut
Kit Kabelhalter + Nutmutter
Kit Prensa Cable + Virola
Kit Scheda Primario
Kit Fiche Primaire
Kit Primary Pcb
Kit Primaertrafokarte
Kit Tarjeta Primario
Kit Manopola
Kit Poignee
Knob Kit
Griff Kit
Kit Manija
REF.
43
44
45
46
ELENCO PEZZI DI RICAMBIO
PIECES DETACHEES
SPARE PARTS LIST
ERSATZTEILLISTE
PIEZAS DE REPUESTO
Kit Igbt
Kit Igbt
Kit Igbt
Kit Igbt
Kit Scheda Controllo
Kit Platine De Control
Kit Control Pcb
Kit Steurungskarte
Kit Tarjeta De Controlo
Kit Diodi
Kit Diodes
Kit Diodes
Kit Diodes
Kit Diodos
Kit Microcontrollore
Kit Microcontroller
Kit Microcontroller
Kit Microcontroller
Kit Microcontroller
25
SUPERIOR PLASMA 60 HF
Esploso torcia, Dessin torche, Torch drawing, Schlauchpaket - Explosionszeichnung, Diseño seccionado antorcha.
REF.
1
2
3
4
5
6
7
8
ELENCO PEZZI RICAMBIO TORCIA
LISTE PIECES DETACHEES TORCHE
SPARE PARTS LIST TORCH
ERSATZTEILLISTE SCLAUCHPAKET
PIEZAS DE REPUESTO ANTORCHA
Corpo Torcia
Corpus Torche
Torch Body
Schlauchpaketkopf
Cabezera Antorcha
Impugnatura Torcia
Poignee Torche
Torche Handle
Schlauchpaketgriff
Empunadura Antorcha
Pulsante Torcia
Poussoir Torche
Torch Pushbutton
Brennerdruckknopf
Pulsador Antorcha
Kit 5 Elettrodi
Kit 5 Electrodes
Kit 5 Electrodes
Kit 5 Elektroden
Kit 5 Electrodos
Kit 5 Ugelli
Kit 5 Buses
Kit 5 Nozzles
Kit 5 DÜsen
Kit 5 Inyectores
Kit 5 Elettrodi Prolungati
Kit 5 Electrodes Prolongees
Kit 5 Long Electrodes
Kit 5 VerlÄngerte Elektroden
Kit 5 Electrodos Prolongados
Kit 5 Ugelli Prolungati
Kit 5 Buses Prolongees
Kit 5 Long Nozzles
Kit 5 VerlÄngerte DÜsen
Kit 5 Inyectores Prolungados
Kit 2 Diffusori Isolanti
Kit 2 Diffuseurs Isolants
Kit 2 Insulating Diffusers
Kit 2 Diffusor Isolierteil
Kit 2 Diffusor Aislador
CODE
CODICE
KODE
722476
722605
722711
802076
802077
802078
802079
802080
REF.
9
10
-
ELENCO PEZZI RICAMBIO TORCIA
LISTE PIECES DETACHEES TORCHE
SPARE PARTS LIST TORCH
ERSATZTEILLISTE SCLAUCHPAKET
PIEZAS DE REPUESTO ANTORCHA
Kit 2 Portaugelli
Kit 2 Embouts
Kit 2 Nozzle-holders
Kit 2 DÜsenhalter
Kit 2 Puntales
Kit 5 Distanziali
Kit 5 Entretoises
Kit 5 Spacers
Kit 5 AbstandstÜck
Kit 5 Espaciadores
Torcia 6m
Torche 6m
Torch 6m
Schlauchpaket 6m
Antorcha 6m
CODE
CODICE
KODE
802081
802128
742040
REF.
ELENCO PEZZI RICAMBIO TORCIA
LISTE PIECES DETACHEES TORCHE
SPARE PARTS LIST TORCH
ERSATZTEILLISTE SCLAUCHPAKET
PIEZAS DE REPUESTO ANTORCHA
CODE
CODICE
KODE
26
SUPERIOR PLASMA 60 HF
Centres de service après-vente agréés
Fiche de réparation
Date:
Modèle convertisseur:
N° de fabrication:
Société:
Technicien:
Dans quel environnement a travaillé le convertisseur:
Chantier:
Atelier:
Autre:
Alimentation:
Groupe électrogène
Du secteur sans rallonge
Du secteur avec rallonge m:
Stress mécaniques subis par la machine
Description:
Degré de saleté
Répartition de la saleté dans la machine
Description:
Type de panne
Ponts redresseurs
Condensateurs électrolytiques
Relais
Résistance précharge
IGBT
Circuits snubber
Diodes secondaires
Potentiomètre
Autre
Sigle composant
Remplacement carte primaire: oui non carte controle: non
Problèmes rencontrés durant la réparation:
27
TELWIN S.p.A. - Via della Tecnica, 3
36030 VILLAVERLA (Vicenza) Italy
Tel. +39 - 0445 - 858811
Fax +39 - 0445 - 858800 / 858801
E-mail: telwin@telwin.com http://www.telwin.com
ISO
9001
CERTIFIED QUALITY SYSTEM
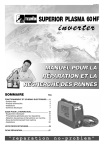
Öffentlicher Link aktualisiert
Der öffentliche Link zu Ihrem Chat wurde aktualisiert.