Polybutyral et polyformal de vinyle. INRS Matières plastiques
POLYVINYLIQUES
POLYBUTYRAL ET POLYFORMAL VINYLIQUES
POLYBUTYRAL VINYLIQUE Abréviation normalisée : PVB
MOWITAL B
POLYFORMAL VINYLIQUE
PIOLOFORM F
Noms commerciaux
RHOVINAL B
Abréviation normalisée : PVFM
REVYL F
I. – CARACTÉRISTIQUES
La formule générale approximative du polyformal et du polybutyral vinyliques peut être à titre d’exemple :
Le radical R est H dans le cas du polyformal vinylique et C
3
H
7
dans le cas du polybutyral vinylique. Les groupements « hydroxyle » OH et « acétyle »
OCOCH
3
proviennent du polyalcool et/ou du polyacétate vinylique servant à la préparation du polyformal et du polybutyral. Le nombre de ces groupements dépend du degré de polymérisation des produits de départ et des conditions de leur réaction avec les aldéhydes formique et butyrique.
Le polybutyral vinylique, poudre jaune crème, inodore ou à très faible odeur butyrique est livré sous forme de poudres, d’émulsions ou de feuilles.
Différents adjuvants peuvent être ajoutés à la résine pure :
74
1. – Plastifi ants.
Phtalates, phosphates, huile de ricin.
2. – Solvants.
Hydrocarbure chlorés, méthyléthylcétone, méthylcyclohexanone, dioxanne, alcool méthylique.
Le polyformal vinylique, poudre incolore ou jaunâtre et inodore, est livré sous forme de poudres ou d’émulsions.
La résine peut être modifi ée par l’adjonction des produits suivants :
1. – Plastifi ants.
Phtalate de méthyle, tartrate de butyle, salicylates, triacétine.
2. – Solvants.
Alcool méthylique, chlorure de méthylène, chlorure d’éthylène, dioxanne, phénol et crésols.
3. – Charges.
Farine de bois, stéarate de calcium.
II. – MISE EN ŒUVRE
La transformation du polybutyral vinylique s’effectue le plus souvent à partir de solutions ou d’émulsions [11].
1. – Enduction-vernis.
En raison de la bonne adhérence de cette résine en solution sur l’acier et l’aluminium, on l’utilise pour les couches de fond sur métaux, dans les peintures marines et industrielles anticorrosion (Wash Primer, Shop Primer) et pour vernir l’intérieur des boîtes de conserves.
2. – Imprégnation.
— soit à partir de solutions de résines à 50 % dans le méthanol ;
— soit à partir d’émulsions aqueuses de résines.
3. – Extrusion-calandrage.
À partir d’un polybutyral vinylique spécial, correctement plastifi é, on réalise des feuilles qui servent d’armatures d’assemblage de deux plaques de verre pour la confection de verre feuilleté pour pare-brise automobile de sécurité.
75
Le polyformal vinylique est principalement utilisé dans la fabrication de vernis, pour l’émaillage de fi ls électriques ainsi que dans la préparation de colles pour métaux.
1. – Vernis.
En association avec le phénol ou les crésols, le polyformal vinylique permet de fabriquer des vernis d’émaillage pour fi ls électriques en cuivre ou en aluminium. Après cuisson, l’émail au formal présente une adhérence excellente au métal, une grande souplesse, une résistance à l’abrasion et des propriétés diélectriques remarquables, mais la tenue thermique d’un tel émail reste limitée.
2. – Colles.
L’utilisation de colles pour métaux à base de polyformal vinylique et de phénoplaste prend actuellement de l’importance.
On enduit la surface à coller avec la solution phénolique. Après un séchage partiel, on projette la poudre de polyformal. Le séchage s’effectue sous pression vers 150 °C.
III. – RISQUES*
1. – Résines et adjuvants.
Le polyformal et le polybutyral vinyliques sont des résines moyennement infl ammables [12], [16]. Ils ne présentent pas de risque toxicologique particulier à température ordinaire à l’exception du danger habituel dû aux poussières inertes lorsque la résine est manipulée sous forme pulvérulente.
Les risques dus aux adjuvants se manifestent surtout au moment de la préparation des mélanges et de la mise en solution des poudres.
— Plastifi ants.
Pour les risques dus aux phosphates, aux phtalates, se reporter au tableau en fi n de volume.
— Solvants.
L’alcool méthylique est toxique en particulier par inhalation. Les hydrocarbures chlorés et le dioxanne sont nocifs également par inhalation.
Le phénol et les crésols utilisés pour les vernis de polyformal vinylique sont généralement caustiques et toxiques par contact cutané.
76
également le tableau en fi n de volume.
2. – Dégradation thermique. a) Aux températures de mise en œuvre.
Dès 150 °C, il peut y avoir un début de décomposition des résines avec dégagement d’aldéhydes formique et butyrique irritants pour les muqueuses oculaires et respiratoires.
Ce début de décomposition a lieu surtout en cas de surchauffe accidentelle ou non de la matière (défaut de régulation, durée prolongée de chauffe…).
De l’anhydride phtalique, irritant des muqueuses et voies respiratoires et allergène, peut se former si les phtalates fi gurent parmi les plastifi ants.
b) En cas de pyrolyse ou de combustion.
Les produits de décomposition sont toujours les aldéhydes formique et butyrique en quantité plus importante que précédemment.
Il se forme également de l’aldéhyde acétique, irritant puissant des voies respiratoires, des hydrocarbures aliphatiques (méthane et hydrocarbures insaturés légers), de l’anhydride carbonique et de l’oxyde de carbone, toxique.
77
POLYSTYRÉNIQUES
POLYSTYRÈNE Abréviation normalisée : PS
Polystyrène standard et polystyrène choc
Noms commerciaux
Polystyrène expansé
BUTOFAN ROBEX BALIPOR
DISTRÈNE STERNITE HOSTAPOR
ESTYPRÈNE STYRAFIL POLISOL
HOSTYREN STYRANIL ROOFMATE
LACQRENE STYRAVER STYROCELL
LORKALÈNE STYRON STYROMAT
PLASTRYL TROLITUL VESTYPOR
POLYFLEX VESTYRON
I. – CARACTÉRISTIQUES
La formule générale du polystyrène peut s’écrire :
Il faut distinguer :
— le polystyrène standard communément appelé polystyrène cristal à cause de sa transparence qui résulte de la polymérisation du styrène sous l’action de catalyseurs. Il est caractérisé par sa rigidité et sa fragilité ;
78
— le polystyrène choc, produit translucide ou opaque résultant d’une copolymérisation par greffage avec un élastomère ; polybutadiène ou poly(butadiène/styrène) qui lui confère une rigidité atténuée et une bonne tenue aux chocs (3 à 10 % de butadiène) ;
— le polystyrène chaleur résultant d’une copolymérisation avec de l’
α− méthylstyrène qui lui confère une meilleure résistance à la chaleur.
Les polystyrènes sont des résines de faible densité ayant une bonne résistance aux acides faibles, aux bases et aux huiles. Ils sont solubles dans la plupart des solvants organiques.
Le polystyrène commence à se déformer sous l’effet de la chaleur entre 70 et 90 °C. Il se présente sous la forme d’un fl uide visqueux vers 140-
180 °C.
Il est livré sous des formes commerciales diverses : poudres, granulés, billes, pâtes, solutions et émulsions, demi-produits (feuilles, plaques, tubes, profi lés…).
Divers adjuvants peuvent lui être ajoutés :
1. – Plastifi ants.
Ce sont généralement des huiles de paraffi ne, certains esters d’acides gras ou des phtalates, notamment le phtalate de dibutyle. Ils sont employés en faible quantité.
2.
–
Solvants.
— le monomère styrène ;
— les hydrocarbures tels que toluène, xylènes, cyclohexane, méthylcyclohexane, solvant naphta ;
— les hydrocarbures chlorés : 1,1,1-trichloréthane ; cyclohexanone ;
— les acétates de méthyle, d’éthyle, de butyle ;
— le tétrahydrofuranne.
3.
–
Charges.
Le polystyrène est le plus souvent sans charge pour respecter sa transparence naturelle.
On peut néanmoins le renforcer avec des fi bres de verre ou lui ajouter des charges telles que carbonate de calcium, noir de carbone, mica.
4.
–
Colorants et pigments.
Toute la gamme des pigments et colorants habituels est utilisable pourvu qu’ils soient solides aux températures de mise en œuvre
(160-250 °C).
79
On utilise aussi l’oxyde de titane comme opacifi ant et, pour des effets décoratifs spéciaux, de la poudre d’aluminium et de bronze.
5. – Stabilisants et anti-oxydants.
En ce qui concerne le polystyrène standard, les stabilisants sont très peu utilisés, si ce n’est pour améliorer la résistance à la lumière. Dans ce but, on lui ajoute des absorbeurs UV, tels que benzophénones et benzotriazoles,
à raison de 0,1 à 0,2 %.
Dans le polystyrène-choc, la protection contre la dégradation thermique est réalisée par adjonction d’anti-oxydants phénoliques seuls ou mélangés à des phosphites à raison de 0,1 à 0,2 % environ.
6. – Antistatiques.
Pour faciliter l’écoulement des charges électrostatiques, on peut ajouter
à la résine de base 1 à 2 % d’amines ou d’alcools et des sels d’ammonium quaternaire.
7. – Lubrifi ants.
Ils sont ajoutés en très faible quantité (inférieurs à 1 %) pour faciliter la mise en œuvre et améliorer la résistance à l’abrasion. Ce sont généralement des stéarates de zinc ou de magnésium, des stéaramides, des cires naturelles ou synthétiques.
II. – MISE EN ŒUVRE
1. – Moulage.
On opère généralement un préchauffage des granulés dans une étuve à
70-80 °C pendant quelques heures pour en éliminer l’humidité.
— Injection : les températures sont de l’ordre de 160-320 °C.
— Extrusion : les températures sont de l’ordre de 180-300 °C.
Thermoformage.
Les feuilles extrudées de polystyrène choc sont formées sous vide à partir de rouleaux de feuilles ou directement à la sortie de l’extrudeuse.
Les feuilles biorientées de polystyrène standard sont formées sous pression.
Extrusion-souffl age.
Cette technique est très peu utilisée. Elle permet néanmoins de fabriquer des fl acons à usage alimentaire et pour la parfumerie.
80
2. – Revêtements et enduction.
On part de résines en solution dans le monomère ou dans un mélange de solvants. On peut également utiliser le polymère en émulsion aqueuse.
Solutions.
Les solvants utilisés dans les peintures et vernis pour imperméabilisation des matériaux de construction sont des hydrocarbures benzéniques, des esters, des cétones ou leurs mélanges.
Émulsions.
Ce sont des suspensions aqueuses de fi nes particules de polystyrène plastifi é ou non, en milieu neutre ou peu alcalin. Elles sont utilisées dans l’industrie du papier et pour l’apprêtage du tissu.
3. – Usinage et fi nition.
Le polystyrène standard, cassant et rigide, s’usine mal. Par contre, l’usinage du polystyrène choc ne pose pas de problème particulier, si ce n’est d’éviter les surchauffes locales de la matière par un refroidissement approprié.
4. – Collage.
Le polystyrène est collé à lui-même par dissolution dans un solvant ou un mélange de solvants. Les solvants les plus employés sont le toluène, la méthyléthylcétone, l’acétate de butyle et le tétrahydrofuranne. Le collage peut s’effectuer à froid ou à chaud (environ 60 °C).
Une autre technique de plus en plus utilisée est le soudage par ultrasons.
5. – Produits allégés et expansés.
On distingue généralement :
— les polystyrènes allégés [71], de densité comprise entre 0,7 et 1, obtenus :
• soit par procédé chimique : un agent porogène (azodicarbonamide, bicarbonate de sodium…) libère par action de la chaleur un gaz inerte
(anhydride carbonique, azote…) dans la matière fondue ;
• soit par procédé physique : de l’azote est envoyé sous pression dans le polystyrène fondu ;
— les polystyrènes expansés de très faible densité : la polymérisation est effectuée avec incorporation de n-pentane à raison d’environ 6 % dans le mélange. Les perles obtenues subissent une expansion en deux
étapes : préexpansion des perles de polystyrène à la vapeur d’eau et expansion à plus haute température [91], [94].
6. – Découpe de blocs de P.S. expansé au fi l chaud.
Température : environ 400 °C.
81
III. – RISQUES*
1. – Résine et adjuvants.
Le polystyrène est infl ammable.
La résine ne présente pas de risque toxicologique particulier à température ordinaire à l’exception du danger habituel dû aux poussières inertes lorsqu’elle est manipulée sous forme pulvérulente.
Les adjuvants sont ajoutés en faible quantité ce qui n’exclut pas les risques au moment de leur incorporation [25].
— Plastifi ants.
Parmi les plastifi ants, les phtalates sont légèrement irritants pour la peau et les muqueuses.
— Solvants.
À côté des solvants tels que cétones et esters, les opérations de collage et d’imprégnation utilisent les monomères et les hydrocarbures benzéniques beaucoup plus dangereux :
•
Le styrène a d’abord une action irritante sur les yeux et les voies respiratoires. À plus forte concentration, il peut exercer une action dépressive sur le système nerveux central.
•
Les hydrocarbures benzéniques : toluène et xylènes sont nocifs par inhalation (action ébrio-narcotique) et irritants pour la peau et les muqueuses.
•
Les hydrocarbures chlorés sont nocifs par contact cutané et par inhalation.
— Stabilisants.
La benzophénone est légèrement irritante [95].
— Charges.
Les fi bres de verre sont irritantes pour les voies respiratoires et la peau.
— Antistatiques.
Les amines et sels d’ammonium quaternaires sont irritants pour la peau et certains sont allergisants.
2. – Dégradation thermique. a) Aux températures de mise en œuvre (160-320 °C) [5], [6], [7], [54].
82
également le tableau en fi n de volume.
La décomposition thermique du polystyrène commence généralement vers 250 °C en présence d’air avec dégagement de différents produits gazeux :
— Styrène : le pourcentage de monomère dans les produits de dégradation augmente en fonction de la température. Il y a également formation d’oligomères (dimère, trimère…).
— Hydrocarbures benzéniques notamment le benzène, l’éthylbenzène et le cumène.
— Aldéhydes, notamment le benzaldéhyde.
deux facteurs, température et temps de chauffe, interviennent sur la décomposition : ainsi dès 230 °C, un séjour de plusieurs heures dans une machine en chauffe peut provoquer un début de décomposition.
Parmi les adjuvants, les antioxydants phénoliques notamment se libèrent au cours de la dégradation.
b) En cas de pyrolyse ou de combustion [33], [92].
Les gaz formés sont essentiellement l’anhydride carbonique, l’oxyde de carbone, le styrène, l’éthylbenzène, le benzène, le toluène et des hydrocarbures lourds.
Le polystyrène brûle facilement. Son pouvoir calorifi que est d’environ
9 500 kcal/kg [16] ; l’incendie se propage rapidement à cause des gaz formés dont certains sont eux-mêmes combustibles.
Il existe cependant des qualités de polystyrène comportant des retardateurs de combustion en particulier pour les produits allégés et expansés particulièrement infl ammables [18], [43], [93]. Lors de la fabrication et du stockage du polystyrène expansé, il faut attirer l’attention sur les risques présentés par la présence de pentane utilisé comme agent d’expansion.
83
POLYSTYRÉNIQUES
COPOLYMÈRES STYRÉNIQUES SAN - ABS - MBS - SBS - SIS
Noms commerciaux
ABSACON TERLURAN
ABSON TRONAL
AÉTERNACRYL UGIKRAL
AFCORYL URTAL
ALTUCHOC
AMPAGLAS
SAN
BLENDEX DIKARYL
BUTAVER ESTYSAN
CYCOLAC KOSTIL
CYCOLON LASTIL
DOW ABS LURAN
KAPRONET (matière de purge) RESTIL
KLÉGISAB STARASAN
KRALASTIC STYRABIL
LASTILAC STYVACRYL
LORKARIL TYRIL
LUSTRAN I VERSAN
NABUTÈNE VESTORAN
NÉOKARIL
NORSORAU
MBS
RONFALIN
ROYALEX
SABEX
SICOFLEX ABS
Élastomères thermoplastiques SIS et SBS
CARIFLEX TR
STARABS KRATON
STRATO SOLPRÈNE
STYLAC
I. – CARACTÉRISTIQUES
Pour améliorer les propriétés chimiques et physiques du polystyrène, des copolymères ont été réalisés en associant le styrène de formule
84
à d’autres monomères :
— l’acrylonitrile : formule du monomère CH
2
= CH – CN ;
— le butadiène : formule du monomère CH
2
= CH – CH = CH
2
;
— le méthacrylate de méthyle formule du monomère
CH
2
= CH – COOCH
|
CH
3
3
— l’isoprène : formule du monomère
CH
2
= CH – C = CH
|
CH
3
2
Les copolymères ainsi obtenus sont les suivants :
— SAN poly(styrène/acrylonitrile) :
— ABS poly(styrène/acrylonitrile/butadiène) ;
— MBS poly(styrène/méthacrylate de méthyle/butadiène) ;
— SIS poly(styrène/isoprène/styrène) ;
— SBS poly(styrène/butadiène/styrène).
Les deux derniers sont des copolymères triséquencés qui ont des propriétés d’élastomères thermoplastiques. Se reporter, à ce sujet, au chapitre II des généralités, [11], [45], [158].
Les SAN sont des copolymères statistiques simples, obtenus par copolymérisation en émulsion.
Les MBS sont obtenus par greffage en masse d’un mélange de méthacrylate de méthyle et de styrène sur un élastomère styrène/butadiène.
Le produit fi ni est une dispersion transparente de MBS dans une matrice méthacrylate de méthyle-styrène.
Les ABS sont obtenus :
— soit par greffage en émulsion d’acrylonitrile et de styrène sur polybutadiène (on obtient une dispersion d’élastomère ABS dans une matrice nitrile-styrène) ;
— soit par des dispersions d’un élastomère nitrile-butadiène dans une matrice nitrile-styrène (obtenus tous les deux en émulsion).
Suivant les proportions des monomères de départ, on obtient toute une gamme de produits aux propriétés modulées.
Les copolymères styréniques sont des résines incolores, inodores.
Les MBS et SAN sont transparents, tandis que les ABS, les SBS et les
SIS sont opaques. Leurs températures de ramollissement sont de l’ordre de
90-100 °C et ils deviennent fl uides et visqueux entre 180 °C et 200 °C.
Divers produits peuvent leur être adjoints.
85
1. – Stabilisants, lubrifi ants.
— les SAN peuvent contenir :
• des lubrifi ants : stéarate de butyle, stéarates métalliques, stéaramides ;
• des absorbeurs de rayons ultra-violet : benzophénone et benzotriazoles
(0,1 à 0,2 %) ;
• des anti-oxydants thermiques organiques, thioesters notamment le thiopropionate de lauryle ;
— les ABS peuvent contenir :
• des lubrifi ants : huile de paraffi ne, phtalates, stéaramides ;
• des agents antistatiques : amines et alcools ;
• des stabilisants ;
— les MBS contiennent très peu d’additifs :
• lubrifi ants : stéarates métalliques, stéaramides (0,1 %) ;
— les adjuvants des SBS et des SIS sont identiques à ceux des ABS, mais ces copolymères en contiennent généralement très peu.
2. – Charges.
Les copolymères styréniques sont habituellement peu chargés. Certaines qualités spéciales sont renforcées aux fi bres de verre.
3. – Colorants et pigments.
Pratiquement tous les ABS sont colorés (utilisation esthétique, mobilier, etc.).
Les MBS sont utilisés le plus souvent sans colorant pour préserver leurs bonnes propriétés optiques.
4. – Solvants.
Les principaux solvants des copolymères styréniques sont le styrène, la méthyléthylcétone, la méthylisobutylcétone. Ils sont utilisés en particulier dans les opérations de fi nition et de collage.
II. – MISE EN ŒUVRE
La transformation des copolymères styréniques ne présente pas de diffi culté particulière. Toutefois, il est souvent nécessaire de sécher au préalable les granulés, dans une étuve à circulation d’air, pendant plusieurs heures à 80 °C, [2], [11].
86
1. – Injection.
C’est la technique la plus utilisée pour les SAN. Les températures sont de l’ordre de 170 à 260 °C.
Les conditions d’injection sont pratiquement les mêmes pour les
ABS et les MBS. Les températures sont alors de 190-250 °C.
2. – Extrusion.
Cette technique, très utilisée pour les ABS, permet de réaliser des plaques et des feuilles. Par contre, les SAN sont peu souvent extrudés, sinon pour la fabrication de mono-fi laments.
Les températures sont de l’ordre de 170-240 °C.
Il est également possible d’obtenir des feuilles d’épaisseurs allant de quelques dizaines de microns à plusieurs millimètres.
3. – Extrusion-souffl age.
Elle permet de fabriquer des corps creux en ABS, SAN et MBS à des températures de 190-240 °C.
4. – Fabrication d’allégés.
Le transformateur ajoute habituellement un porophore en mélange à sec avec les poudres et granulés de SAN et ABS. Ce porophore, sous l’action de la chaleur, dégage un gaz qui expanse la matière au cours du moulage et conduit à une structure macromoléculaire moins dense.
5. – Thermoformage.
Les feuilles extrudées d’ABS et de MBS peuvent être thermoformées, à partir de rouleaux de feuilles, ou directement à la sortie de l’extrudeuse
à des températures de 140-180 °C.
Les feuilles bi-orientées de SAN sont formées sous pression.
6. – Usinage et fi nition.
L’usinage des ABS est très facile, tandis que celui des MBS et des SAN présente quelques diffi cultés en raison de leur rigidité et leur fragilité.
L’assemblage des pièces peut s’effectuer :
— par soudage au chalumeau à air chaud ;
— par soudage aux ultrasons ;
— par collage : dissolution superfi cielle dans la méthyléthylcétone ou de préférence dans une solution d’ABS ou de SAN (à 10-20 %) dans ce solvant.
87
7. – Galvanoplastie.
Le chromage et le nickelage peuvent être effectués sur l’ABS, la fi xation étant réalisée par les sels de Palladium, après une dissolution sélective superfi cielle pour permettre l’accrochage et une métallisation chimique pour rendre la surface conductrice.
III. – RISQUES*
1. – Résines et adjuvants.
Les copolymères styréniques sont généralement infl ammables.
Les résines ne présentent pas de risque toxicologique particulier à température ordinaire sauf si elles renferment des monomères résiduels
(acrylonitrile, styrène…) [52] :
— l’acrylonitrile est toxique par inhalation et contact cutané. C’est un poison du système nerveux et il est suspecté d’être cancérogène [40] ;
— le styrène et le méthacrylate de méthyle sont irritants pour les yeux et les voies respiratoires.
Les adjuvants sont ajoutés en quantité assez faible ce qui n’exclut pas les risques au moment de leur incorporation ou lors de l’usinage.
— Lubrifi ants et agents antistatiques.
Les phtalates peuvent être légèrement irritants.
Les amines exercent une action irritante ou même corrosive sur la peau.
Certaines sont sensibilisantes.
— Charges.
Les fi bres de verre présentent un danger d’irritation de la peau et des voies respiratoires notamment au moment de leur incorporation dans les résines.
— Solvants.
La méthyléthylcétone est irritante pour les muqueuses oculaires et respiratoires.
Le styrène a également une action irritante sur les yeux et les voies respiratoires. À plus forte concentration, il peut exercer une action dépressive sur le système nerveux central.
— Stabilisants.
La benzophénone est légèrement irritante [95].
2. – Dégradation thermique. a) Aux températures de mise en œuvre (170-260 °C) [51], [52].
Les copolymères styréniques commencent généralement à se décomposer avant 260 °C (l’ABS notamment commence vers 200 °C mais sa
88
également le tableau en fi n de volume.
décomposition n’est pas encore très marquée à 250 °C). Au cours de cette décomposition, il y a dégagement des produits de départ : les monomères en particulier, le styrène, l’acrylonitrile, le méthacrylate de méthyle.
Ces dégagements peuvent découler de la présence de monomères résiduels mais proviennent surtout d’un début de dépolymérisation. Ils sont favorisés par le temps passé par la matière dans la machine en chauffe. Les monomères sont dangereux et infl ammables (voir paragraphe précédent).
Il y a également formation d’hydrocarbures benzéniques, de nitriles et d’aldéhydes, notamment l’acroléine.
D’autre part, les anti-oxydants phénoliques présents parfois dans les
SAN se dégagent facilement.
b) En cas de pyrolyse ou de combustion.
Outre les monomères cités ci-dessus, il se forme également de l’oxyde de carbone, de l’anhydride carbonique, des hydrocarbures aliphatiques.
Des nitriles, de l’ammoniac, de l’acide cyanhydrique, toxique par inhalation, peuvent se former dans le cas de l’ABS et du SAN.
Se reporter également aux différents chapitres correspondant à chacun des produits de base des copolymères.
Les copolymères styréniques brûlent facilement [21], [24]. Pour certaines applications, ils peuvent être ignifugés au moyen d’adjuvants spéciaux ou bien de petites quantités de PVC leur sont ajoutées pour améliorer leur réaction au feu. Dans ce cas, un dégagement d’acide chlorhydrique est à prévoir en cas de combustion.
89
POLYACRYLIQUES ET POLYMÉTHACRYLIQUES
POLYMÉTHACRYLATE DE MÉTHYLE
Abréviation normalisée : PMMA
Noms commerciaux de résines polyacryliques et polyméthacryliques
I. – CARACTÉRISTIQUES
Le polyméthacrylate de méthyle a pour formule générale :
Il est obtenu par polymérisation du méthacrylate de méthyle :
— en masse (plaques coulées et poudres à mouler) ou en sirop (colles polymérisables à froid) ;
— en suspension (poudres à mouler et poudres pour peintures et vernis) ;
— en émulsion (peintures, vernis et revêtements).
Le PMMA est caractérisé par sa transparence, ses facilités de mise en
œuvre, ses propriétés diélectriques et sa résistance au vieillissement.
Il est livré sous différentes formes : plaques coulées, joncs, disques, bâtons, poudres à mouler par injection et extrusion, poudres pour peintures et vernis, granulés, émulsions, sirops, demi-produits extrudés.
90
Certains adjuvants peuvent être ajoutés à la résine :
1. – Catalyseurs de polymérisation.
Ce sont des peroxydes organiques ajoutés en très faible quantité.
2. – Colorants et pigments.
Ce sont en général des complexes minéraux, que l’on incorpore dans la masse du sirop avant polymérisation dans le cas des plaques coulées ou bien que l’on mélange intimement à la poudre de PMMA avant sa mise en
œuvre.
3. – Plastifi ants.
Le polyméthacrylate n’en contient qu’exceptionnellement, pour des applications bien spécifi ques. On utilise alors des phtalates.
Habituellement, la plastifi cation du PMMA est obtenue par copolymérisation avec l’acrylate d’éthyle ou de méthyle, par exemple.
4. – Charges.
Le polyméthacrylate de méthyle n’en contient généralement pas.
Seules certaines résines de coulée peuvent être chargées de silice ou d’autres produits, pour des applications routières particulières.
5. – Solvants.
Le monomère méthacrylate de méthyle, qui se présente sous forme d’un liquide visqueux, d’odeur piquante, est le solvant employé généralement dans les colles polymérisables ainsi que dans les mélanges polymèremonomère utilisés en dentisterie.
Les autres solvants les plus actifs sont : des hydrocarbures chlorés
(chlorure de méthylène, monochlorhydrine de glycol, trichloréthylène, chloroforme, etc.), des cétones, des hydrocarbures benzéniques.
Ces solvants sont utilisés dans les opérations d’assemblage des plaques coulées et dans la préparation de peintures, vernis, adhésifs et revêtements.
II. – MISE EN ŒUVRE
Le polyméthacrylate de méthyle se prête à la plupart des méthodes habituelles de mise en œuvre des résines. Suivant la nature et la forme du produit de départ, les techniques sont différentes.
91
1. – Plaques coulées.
Dans cette méthode, le polyméthacrylate de méthyle est une résine de haut poids moléculaire, obtenue par polymérisation lente en masse sous forme de plaques, blocs, feuilles, joncs ou bâtons. Il possède alors une bonne mémoire élastique dans une large zone de température, ce qui rend possible certaines techniques de transformation :
— Thermoformage sous pression d’air.
Le chauffage à 130-160 °C s’effectue dans des étuves à air chaud ou à rayonnement infrarouge.
— Plage à froid avec chauffage local le long de la génératrice de pliage à l’aide d’une résistance chauffante à des températures de l’ordre de
130-160 °C.
— Usinage (sciage, découpage, perçage, tournage, fraisage, polissage…).
Il est particulièrement aisé, puisque les machines habituelles de mécanique et de travail du bois sont utilisables.
Il convient d’éviter un échauffement de la matière en cours d’usinage par une lubrifi cation et un refroidissement localisé à l’aide d’eau pure.
— Assemblage.
Le collage du polyméthacrylate de méthyle sur lui-même peut s’effectuer :
— par dissolution (ramollissement) des surfaces de contact au moyen d’un solvant (acétone, hydrocarbures chlorés) ;
— ou bien à l’aide de colles-solvant qui sont des dissolutions dans un solvant, de faibles quantités de polyméthacrylate de bas poids moléculaire ;
— ou bien à l’aide de colles polymérisables à base de PMMA à bas poids moléculaire en solution dans le monomère. L’addition au moment de l’emploi du catalyseur de polymérisation permet d’obtenir un joint de PMMA.
2. – Plaques extrudées.
Il s’agit de polyméthacrylate transformé par extrusion, à partir de poudres à mouler de bas poids moléculaire.
Ces plaques ont une excellente transparence. On ne retrouve la mémoire
élastique que dans une très faible partie de la plage de transformation précédente.
— Thermoformage sous vide.
Les températures sont de l’ordre de 130-160 °C.
— Pliage à froid.
— Usinage.
— Assemblage.
92
Ces trois opérations présentent les mêmes caractéristiques que dans le cas des plaques coulées.
3. – Poudres à mouler.
Ce sont des poudres de polyméthacrylate de méthyle de bas poids moléculaire, obtenues par polymérisation lente en suspension dans l’eau puis séchage.
La poudre, après adjonction des adjuvants, est dans la plupart des cas, transformée en granulés ou en lentilles pour la mise en œuvre par :
— Injection.
C’est le procédé le plus employé, mais il demande quelques précautions particulières : une bonne régulation thermique des zones de chauffage, des précautions pour éviter les phénomènes d’électricité statique, une grande propreté des locaux et de l’appareillage et une matière à mouler parfaitement sèche. Les températures sont de :
•
170-240 °C pour les résines dures ;
•
180 °C pour les résines molles.
— Extrusion : températures de l’ordre de 160-220 °C.
Une très bonne régulation des températures, pression et vitesse est nécessaire.
Le refroidissement de l’objet extrudé en PMMA est assuré par de l’air froid et non pas de l’eau, pour éviter tout choc thermique à la matière.
— Dissolution pour fabrication des peintures, vernis et encres d’imprimerie.
— Moulage utilisé en dentisterie du mélange polymère-monomère en présence d’adjuvants [30].
4. – Émulsions.
Elles sont obtenues par polymérisation dans l’eau avec des agents
émulsifi ants.
méthacrylate d’éthyle ou de n-butyle notamment.
Les applications sont les vernis, peintures, revêtements, apprêts pour tissus et papiers, protections murales.
5. – Sirops.
Ce sont des résines de coulée pouvant être polymérisées par addition de catalyseurs, agissant soit à froid, soit à chaud, soit sous rayonnement
UV,
β
ou
γ
. Leurs applications sont les colles polymérisables, permettant de souder deux pièces de PMMA.
93
III. – RISQUES*
1. – Résine et adjuvants.
Le polyméthacrylate de méthyle est une résine infl ammable.
À l’état polymérisé, elle ne présente pas de risque toxicologique particulier à température ordinaire.
Toutefois, sous forme pulvérulente, au cours de la préparation de mélanges, solutions ou émulsions et lors de l’usinage, la résine peut entraîner des irritations de la peau et du système respiratoire pouvant être dues à la présence de monomère résiduel [30].
Les risques dus aux adjuvants se manifestent au cours de leur incorporation et lors de la transformation notamment lors des travaux d’assemblage et de collage pour les solvants [98].
— Solvants.
Le méthacrylate de méthyle monomère est un composé infl ammable qui peut former des mélanges explosifs avec l’air.
Ses vapeurs, irritantes pour les yeux et les voies respiratoires peuvent avoir un effet narcotique à forte concentration. Le liquide est irritant pour la peau et peut être sensibilisant lors de son utilisation dans les pâtes et colles autopolymérisantes notamment [96], [97].
Parmi les autres solvants, les hydrocarbures chlorés et aromatiques sont nocifs en particulier par inhalation.
— Catalyseurs.
Les peroxydes, instables, peuvent donner lieu à des décompositions explosives. D’autre part, ils sont irritants et particulièrement dangereux pour les yeux. Se reporter au chapitre III.5 des généralités.
— Plastifi ants.
Les phtalates peuvent être légèrement irritants pour la peau.
Les acrylates de méthyle ou d’éthyle, habituellement employés en copolymérisation pour plastifi er le polyméthacrylate de méthyle, sont nocifs par inhalation et ingestion et irritants pour la peau, les yeux et les voies respiratoires.
Les résines plastifi ées avec les acrylates peuvent entraîner des réactions d’irritation et de sensibilisation lors de leur utilisation.
— Charges.
Silice : se reporter au tableau en fi n de volume.
94
également le tableau en fi n de volume.
2. – Dégradation thermique. a) Aux températures de mise en œuvre (100-24 °C) [48].
Dès 180 °C, le polyméthacrylate de méthyle commence généralement
à se décomposer en libérant le monomère d’abord en faible quantité puis en quantité plus importante quand la température s’élève.
Ces dégagements peuvent avoir lieu lors du moulage, lors de l’usinage si le refroidissement des pièces usinées n’est pas suffi sant et chaque fois qu’une surchauffe se produit.
b) En cas de pyrolyse ou de combustion.
Le polyméthacrylate de méthyle est généralement infl ammable. Il brûle facilement. Son pouvoir calorifi que est d’environ 6 000 kcal/kg, [16]. La matière une fois enfl ammée, la combustion continue d’elle-même en dégageant principalement des vapeurs de méthacrylate de méthyle monomère, de l’anhydride carbonique et de l’oxyde de carbone, toxique, et en quantité moins importante, des hydrocarbures aliphatiques et des aldéhydes [33].
Il existe certaines variétés de polyméthacrylate coulé, classées diffi cilement infl ammables [21] qui brûlent lorsqu’elles sont placées dans une fl amme mais s’éloignent d’elles-mêmes lorsque le foyer est éloigné.
95
POLYACRYLIQUES ET POLYMÉTHACRYLIQUES
POLYACRYLONITRILE ET COPOLYMÈRES
Abréviation normalisée : PAN
Noms commerciaux
COURTELLE LOPAC ZÉFRAN
CRESLAN NOMELLE
I. – CARACTÉRISTIQUES
La formule générale du polyacrylonitrile peut s’écrire :
1. – Fibres synthétiques.
Sous forme d’homopolymère ou copolymérisé avec de faibles proportions d’autres polymères vinyliques (au moins 85 % d’acrylonitrile), le polyacrylonitrile est utilisé comme fi bre synthétique dans l’industrie textile : les fi bres « acryliques ». La résine ne peut fondre sans se décomposer mais sa solubilité dans quelques solvants permet le fi lage [3].
Copolymérisé avec des monomères chlorés (chlorure de vinyle ou de vinylidène), l’acrylonitrile donne des fi bres appelées « modacryliques » si elles contiennent une proportion suffi sante d’acrylonitrile (de 35 % à 85 %).
Peu d’adjuvants sont ajoutés en général au polyacrylonitrile :
— catalyseurs de polymérisation : peroxydes organiques ;
— solvants : diméthylformamide, diméthylsulfoxyde, diméthylacétamide.
96
2. –
Résines thermoplastiques.
a) En copolymérisation par greffage avec les acrylates, les méthacrylates, le butadiène ou le styrène, l’acrylonitrile, à des teneurs supérieures à 60 %, conduit à un groupe de résines thermoplastiques, servant essentiellement à la fabrication de corps creux [11], [99]. Ce copolymère rigide transparent est pratiquement imperméable aux gaz et imprimable.
Solvants : diméthylformamide, acétonitrile.
b) En copolymérisation avec le styrène et le butadiène, l’acrylonitrile copolymère styrène/acrylonitrile (SAN). Pour ces polymères, se reporter au chapitre « Polystyréniques ».
3.
–
Caoutchoucs « nitriles ».
Copolymérisé avec du butadiène, l’acrylonitrile conduit à des caoutchoucs « nitriles » qui ne sont pas traités dans le cadre de cette brochure.
II. – MISE EN ŒUVRE
1. – Fibres.
Le polymère est dissout à chaud dans un solvant approprié. Les fi bres sont obtenues à partir de cette solution de viscosité défi nie et constante par extrusion et coagulation ultérieure.
2. – Résines.
Les copolymères polyacrylonitrile à haute teneur en acrylonitrile sont surtout moulés par souffl age pour obtenir des bouteilles et des fl acons. Les températures sont de l’ordre de 200-215 °C.
Le calandrage et le formage sous vide sont aussi applicables [11].
III. – RISQUES*
1. – Résines et adjuvants.
Les résines polyacrylonitrile et les copolymères ne présentent pas de risque particulier à température ordinaire. Toutefois, l’éventuelle présence dans ces résines d’acrylonitrile monomère, toxique et cancérogène suspecté
[40], a conduit aux États-Unis à l’interdiction des résines à base d’acrylonitrile pour la fabrication des bouteilles à usage alimentaire.
également le tableau en fi n de volume.
97
Les risques dus aux adjuvants proviennent essentiellement des
solvants :
— le diméthylformamide est nocif par inhalation et irritant pour la peau et les muqueuses ;
— le diméthylsulfoxyde, peu toxique, traverse rapidement le peau et peut favoriser la pénétration d’autres substances. Il peut être irritant ;
— le diméthylacétamide est moyennement nocif par inhalation et contact cutané.
Les peroxydes instables peuvent donner lieu à des décompositions explosives. D’autre part, ils sont irritants et particulièrement dangereux pour les yeux (se reporter au chapitre III.5 des généralités).
2. – Dégradation thermique. a) Aux températures de mise en œuvre (jusqu’à environ 250 °C) [6], [51],
[52].
Les copolymères polyacrylonitrile commencent généralement à se décomposer vers 200 °C, avant de fondre en libérant :
— des aldéhydes (notamment l’acroléine) irritant pour les voies respiratoires ;
— de l’acrylonitrile, et d’autres nitriles.
On note aussi la présence d’hydrocarbures aliphatiques et d’acrylates.
b) En cas de pyrolyse ou de combustion [3], [7], [33],
les principaux gaz de décomposition sont :
— l’oxyde de carbone, toxique et l’anhydride carbonique ;
— l’acrylonitrile toxique par inhalation et voie cutanée, cancérogène suspecté
[40] ;
— l’ammoniac, gaz toxique et très irritant pour les muqueuses oculaires et respiratoires ;
— l’acide cyanhydrique, gaz très toxique qui est libéré en quantités croissantes en fonction de la température.
Les fi bres de polyacrylonitrile sont infl ammables [26]. L’introduction dans un tissu acrylique de fi bres « modacryliques » diminue son infl ammabilité
[7], [21].
98
POLYAMIDES
Abréviation normalisée : PA
Noms commerciaux
AETERNAMID
AKULON (PA 6 – PA 6-6)
CAPRAN (PA 6)
CAPROLAN (PA 6)
PERLON N (PA 6-10)
POLYANYL
PRODILAN
RÉNYL (PA 6)
CELON (PA 6)
CIPONYL
RHODIALON (PA 6)
RILFORM (PA ou complexe)
DURÉTHAN B, A, C (PA 6 – PA 6-6 – RILSAN A (PA 12)
PA 12) RILSAN B (PA 11)
ENKALON (PA 6)
ERTALON (PA 6)
FABELNYL (PA 6 - PA 6-6)
SNIAMID (PA 6 – PA 6-6)
SNIAVITRID (PA 6 – PA 6-6)
STARAMIDE (PA 6 – PA 6-6, 11, 12
GRILAMID (PA 12)
GRILON (PA 6)
LATAMID
LURON
TECHNYL (PA 6, 6-6, 6-10)
ULTRAMID A (PA 6-6)
ALTRAMID B (PA 6)
ULTRAMID S (PA 6-10)
MARANYL VÉRAMIDE
MINLON (PA 6-6) VERSAMID
MONOCAST
NYLATRON (PA 6 – PA 6-6)
VESTAMID (PA 6-12 – PA 12)
WALOMID (fi lm)
NYLFRANCE (PA 6-6)
NYLON (PA 6)
NYLSÈNE (PA 6 – PA 6-6)
NYLTEST (PA 6-6)
OBTEL (PA 6-6)
ORGAMIDE R (PA 6)
ORGASSAN (PA 11)
PERLON L (PA 6)
ZYTEL (PA 6-6)
NOMEX (polym, phénylène, isophtalamide)
TROGAMID T (à partir d’acide téréphtalique et d’isomères 2,2,4 et 4,4,2triméthylhexaméthylène diamine)
I. – CARACTÉRISTIQUES
Les polyamides sont caractérisés du point de vue chimique par le groupement amide : qui se répète à intervalles réguliers dans la molécule.
99
Les polyamides peuvent être obtenus selon les procédés classiques suivants :
— polycondensation d’un diacide avec une diamine, exemples :
PA 6-6 : polyhexaméthylène adipamide :
PA 6-10 : polyhexaméthylène sébacamide : qui mettent en réaction pour : le PA 6-6 : l’hexaméthylènediamine et l’acier adipique, le PA 6-10 : l’hexaméthylènediamine et l’acide sébacique ;
— polycondensation d’un amino-acide sur lui-même, exemple : PA 11 : polyundécanamide : qui met en réaction l’acide amino-undécanoïque ;
— polymérisation d’un lactame, exemple : PA 6 : polycaprolactame
PA 12 : polyaurolactame : qui mettent en réaction pour :
PA 6 : le caprolactame,
PA 12 : le dodécalactame ;
— polycondensation ne faisant pas intervenir la fusion des monomères. Dans ce cas, les techniques de polycondensation mettent en cause des solutions de monomère ; il existe des procédés qui utilisent des monomères plus réactifs, comme des chlorures d’acides.
D’une manière générale, ces polyamides spéciaux à zone de fusion
élevée, sont préparés selon une technologie particulière adaptée aux fi bres.
Par convention, les polyamides obtenus à partir d’aminoacides ou de lactames sont désignés par un seul chiffre indiquant le nombre de carbones des monomères (PA 6, PA 11, PA 12, etc.). Pour les polyamides désignés par deux chiffres : le 1 er chiffre désigne le nombre de carbones de la diamine et
100
le second celui du diacide (PA 6-6, PA 6-10). Dans certains cas de copolyamides, la désignation peut être PA 6/PA 6-6/PA 6-10.
Les polyamides sont livrés sous forme de poudres, granulés, solutions, demi-produits, fi bres. Par élévation de température, ils ne se ramollissent pas progressivement comme la plupart des autres thermoplastiques, mais passent brusquement de l’état solide à l’état liquide (fusion entre 150 et
270 °C suivant le type de polyamides).
Ce sont des polymères fi lables. Une grande partie de la production mondiale est transformée en fi bres textiles.
Ils sont aussi utilisés comme plastiques techniques qui sont transformés comme les autres polymères.
Les caractéristiques des polyamides peuvent être modifi ées par l’adjonction de différents produits :
1. – Plastifi ants. phtalates, les benzoates ou encore les dérivés des acides benzènesulfonique, permettent d’obtenir des polyamides souples.
2. – Solvants.
Les solvants les plus employés sont des mélanges d’alcools
(méthylique, éthylique, isopropylique), de chloroforme et de trichloréthylène ou des mélanges d’alcools et d’eau.
Des acides forts comme l’acide formique, des phénols comme le métacrésol et des solvants chlorés sont également utilisés pour certains polyamides.
3. – Charges.
Les polyamides « renforcés » nécessaires pour des applications dont le coeffi cient de frottement entre deux pièces doit être le plus bas possible peuvent contenir de 15 à 40 % de charges.
Ces charges qui servent aussi à augmenter la résistance mécanique sont généralement des fi bres de verre, des billes de verre, certains graphites, du bisulfure de molybdène, des silicates et parfois du polytétrafl uoroéthylène en poudre.
4. – Colorants et pigments.
Il existe une grande variété de colorants et de pigments ; ils peuvent
être organiques ou minéraux. Leur teneur dans les polyamides est faible en général (5 à 10 ‰) ; mais dans certains cas (polyamides utilisés en câblerie) les charges de pigments peuvent atteindre 15 %. D’une manière générale, le choix de ces colorants et pigments est tel qu’ils doivent résister aux températures élevées de mise en œuvre.
5. – Stabilisants.
Les sels métalliques (halogénures de cuivre) et les polyphénols
(hydroquinone et pyrocatéchine) sont utilisés dans les applications particulières pour éviter la dégradation thermique ou solaire.
101
6. – Retardateurs de combustion.
Bien que brûlant mal, certains polyamides coulent à la fusion et s’ils sont enfl ammés, peuvent propager la fl amme. Pour remédier à ce risque, on incorpore aux polyamides des additifs spéciaux ; ils sont généralement à base d’halogènes, de phosphore, de bore, de bismuth, d’aluminium…
7. – Lubrifi ants.
Ce sont des charges spéciales qui permettent d’étendre le domaine d’application de certains polyamides : stéarates de calcium et de zinc à faible concentration.
II. – MISE EN ŒUVRE
À la livraison, les polyamides en poudres à mouler ou en granulés sont généralement prêts à l’emploi, avec une teneur en humidité maximale de
0,2 %.
Si ce n’est pas le cas, il est indispensable de prévoir un séchage préalable pour prévenir tout risque de dégradation lors de la transformation.
1. – Moulage.
Moulage par injection.
Températures de l’ordre de : 270-290 °C pour le PA 6-6,
230-260 °C pour le PA 6,
220-260 °C pour le PA 11.
Moulage par coulée.
Il est utilisé pour fabriquer des pièces massives, avec des résines polyamides polymérisées en masse, dans le moule, notamment directement
à partir du monomère caprolactame pour le PA 6.
2. – Extrusion.
Cette technique est applicable aux polyamides dont les zones de fusion ne sont pas très élevées et qui possèdent une bonne plage thermoplastique.
L’extrusion du polyamide 6-6 est diffi cile car la latitude de mise en œuvre d’un tel polymère est restreinte, beaucoup plus que celle des PA 6 et PA 11, par exemple.
Températures de l’ordre de : 255-265 °C pour le PA 6-6,
220-260 °C pour le PA 6,
205-260 °C pour le PA 11.
102
L’extrusion est toujours réalisée en vue de l’usinage ultérieur des pièces.
3. – Frittage.
Compression de poudres très fi nes en présence d’un pourcentage important de charges métalliques.
4. – Revêtement couramment appelé « rilsanisation ».
Au préalable, les surfaces métalliques à revêtir doivent subir une préparation pour enlever les graisses, la rouille, les écailles de laminage, etc.
On procède :
— par décapage par projection de sable, de corindon ou de grenaille d’acier ;
— par traitement chimique, à l’aide de différents produits, tels que : trichloréthylène, acide sulfurique à 10 %, etc. ;
— parfois, les surfaces métalliques à recouvrir sont revêtues d’une souscouche avant le trempage ; celle-ci peut contenir des solvants aromatiques ou chlorés.
Le revêtement des pièces métalliques peut être obtenu par différents procédés, à des températures pouvant atteindre 380-400 °C :
— le trempage qui consiste à plonger les pièces préalablement chauffées dans une cuve qui contient la poudre en suspension dans l’air ou dans un gaz inerte ;
— la projection au pistolet-chalumeau de la poudre de polyamide à travers une fl amme sur la surface métallique préchauffée ;
— la projection au pistolet électrostatique.
5. – Enduction.
Elle s’effectue au moyen de polyamides dits « solubles », soit dans des solvants aqueux (alcools + eau), soit dans des mélanges de solvants anhydres
(alcools + chloroforme + trichloréthylène).
Les concentrations en résine sont relativement faibles.
On peut utiliser jusqu’à 50 % de plastifi ants ; on peut également ajouter des charges, des colorants, des diluants, etc.
6. – Usinage : fraisage, perçage, taraudage, tournage.
Il ne présente pas de diffi culté particulière.
7. – Assemblage.
Collage.
On a recours à des produits spécifi ques dont les principaux sont : phénol, m-crésol, alcools lourds, acide formique, solvants chlorés.
Certaines colles sont à base de résine phénol-formol, de résorcineformol, précondensées et polymérisées à chaud ; il existe également des colles époxydiques et des colles de polyuréthanne.
103
Soudage.
Possible par friction, par vibrations, par impulsions thermiques et à haute fréquence plus rarement ou par ultrasons.
III. – RISQUES*
1. – Résines et adjuvants.
Les polyamides, une fois polymérisés, ne présentent pas de risque particulier à température ordinaire à l’exception du danger habituel dû aux poussières inertes lorsque les résines sont manipulées à l’état pulvérulent
(au cours de la « rilsanisation » notamment).
Il n’en est pas de même au cours de la polycondensation qui peut intervenir en même temps que la mise en œuvre dans certains cas comme le moulage de pièces massives.
a) Certains monomères sont dangereux.
D’une manière générale, les diamines aliphatiques ou aromatiques sont des produits toxiques.
L’hexaméthylène diamine, en particulier, est un produit corrosif, irritant pour la peau, les yeux et le système respiratoire. On a également noté des anémies du type hémolytique et des dermites eczématiformes.
Le
ε
-caprolactame, qui intervient directement lorsqu’il est polymérisé en masse dans le moule, peut entraîner, à des concentrations assez importantes, des signes nerveux (irritabilité, nervosité…). Ses vapeurs sont irritantes pour les muqueuses oculaires et respiratoires [103]. L’expérimentation animale a permis d’observer des troubles sanguins et hépato-rénaux [25].
Des chlorures d’acide sont parfois employés comme monomères à la place des acides correspondants. Ce sont en général des produits plus nocifs et corrosifs que les acides.
b) Les risques dus aux adjuvants se manifestent au cours de leur incorporation mais aussi lors de la transformation ou des travaux de fi nition :
— l’acide formique fortement corrosif et le crésol toxique et corrosif peuvent provoquer des brûlures ;
— les phosphates organiques sont nocifs et irritants pour la peau et les muqueuses ;
— les hydrocarbures chlorés nocifs par inhalation et contact cutané exercent une action narcotique ;
— les fi bres de verre sont irritantes pour la peau et les voies respiratoires.
également le tableau en fi n de volume.
104
Pour les autres adjuvants dangereux cités, se reporter au tableau en fi n de volume.
c) Certains risques sont particulièrement dus aux méthodes de mise en
œuvre :
— au cours de l’injection et de l’extrusion, il existe des risques importants de brûlures par suite de projections dues à des décompositions accidentelles, brûlures particulièrement graves car le polyamide chaud adhère à la peau. L’appareillage doit comporter une régulation parfaitement contrôlée pour éviter des décompositions qui comportent, en plus des risques de brûlures, des dangers d’intoxication par les produits de dégradation (voir plus loin dans le chapitre « Dégradation thermique ») ; exposent à l’inhalation des produits de décomposition du polyamide vers 400 °C (voir chapitre « Dégradation »). Elles comportent également des risques dus aux poussières (inhalation et explosion) ; de plus la préparation des surfaces fait intervenir des produits irritants), l’acide sulfurique (liquide corrosif pour la peau et les yeux, aux vapeurs irritantes pour les voies respiratoires) ; le décapage au jet de sable peut entraîner des risques de silicose ;
— les opérations d’usinage peuvent provoquer des surchauffes locales entraînant une décomposition.
2. – Dégradation thermique. a) Aux températures de mise en œuvre (200-400 °C) [6], [7].
Les polyamides commencent généralement à se décomposer avant
250 °C.
Jusqu’à 290-300 °C (température maximale de moulage), la décomposition est encore faible ; il se forme des hydrocarbures aliphatiques, des aldéhydes (acétaldéhyde, acroléine, crotonaldéhyde…) irritants, des nitriles (acrylonitrile, acétonitrile…) et des cétones (acétone…) [50].
Vers 400 °C, température pouvant être atteinte lors de la rilsanisation, la décomposition devient très nette. Les gaz dégagés sont, en plus de ceux précédemment cités [48], [104] :
— de l’ammoniac et des nitriles toxiques et irritants pour les muqueuses oculaires et respiratoires ;
— de l’oxyde de carbone toxique ;
— de l’anhydride carbonique.
b) En cas de pyrolyse ou de combustion.
Les polyamides sont le plus souvent peu ou moyennement infl ammables. Leur pouvoir calorifi que est d’environ 7 500 à 9 000 kcal/kg
[16]. Leur comportement au feu varie suivant la nature chimique du polyamide, sa température de fusion et la forme des objets, réalisés avec ce matériau [102].
La présence de certains adjuvants (plastifi ants) modifi e ce comportement au feu dans le sens d’une plus grande combustibilité [21].
105
L’adjonction de certains apprêts et colorants en particulier à base de chrome peuvent rendre les polyamides très infl ammables [100].
Les gaz se dégageant lors de la pyrolyse ou de la combustion sont principalement [33], [101], [104] :
— l’anhydride carbonique ;
— l’oxyde de carbone ;
— l’ammoniac ;
— l’acide cyanhydrique, très toxique par inhalation, et des nitriles toxiques
(acétonitrile, acrylonitrile…).
106
POLYCARBONATES
Abréviation normalisée : PC
Noms commerciaux
ALTULEX PC MERLON
AETERNABON ORGALAN
CARBAVER PANLITE
GERPALON POKALON
LATILON POLYCARBAFIL
LEXAN SINVET
MAKRISOL STARBONATE
MAKROLON ULTRAPHAN
I. – CARACTÉRISTIQUES
Les polycarbonates sont des composés macromoléculaires obtenus principalement à partir du diphénylolpropane ou bis-phénone A, par polycondensation. Leur formule générale peut s’écrire :
Ils sont livrés sous des formes commerciales diverses : granulés ou demi-produits (plaques, feuilles, fi lms…).
Ce sont des matériaux à usage technique, durs et rigides, diffi cilement combustibles, dont les propriétés principales sont :
— stabilité mécanique et dimensionnelle et résistance aux chocs ;
— solidité et résistance à l’abrasion ;
— bonne stabilité aux très basses températures jusqu’à – 150°C et aux températures élevées jusqu’à 140°C environ ;
— transparence ;
— bonnes propriétés électriques et diélectriques ;
— résistance vis-à-vis des produits chimiques et de certains solvants.
Les polycarbonates sont assez sensibles à l’humidité et sont perméables
à certains gaz.
107
Certains adjuvants peuvent lui être incorporés :
1. – Charges - plastifi ants.
Les polycarbonates n’en contiennent généralement pas. Cependant, pour des opérations particulières, certains sont renforcés aux fi bres de verre.
2. – Stabilisants.
Pour stabiliser ces produits au rayonnement ultraviolet, de petites quantités de noir de carbone peuvent être ajoutées s’il n’est pas nécessaire que le polymère soit transparent.
3. – Colorants et pigments.
La gamme des colorants et pigments pouvant être incorporés aux résines brutes est limitée, car ils doivent rester solides aux températures élevées de mise en œuvre (225-300 °C).
4. – Solvants.
Le meilleur solvant des polycarbonates est le dichlorométhane. Le
1,2-dichloroéthane, le dioxanne, le monochlorobenzène et les mélanges de ces solvants sont également utilisés, principalement dans les opérations de collage des polycarbonates sur eux-mêmes.
II. – MISE EN ŒUVRE
La transformation des polycarbonates exige l’utilisation d’un produit absolument sec sous peine de dégradation immédiate du matériau.
Le séchage des granulés sera effectué pendant plusieurs heures dans une étuve à 120°C au minimum.
1. – Moulage par injection.
Les polycarbonates se prêtent sans inconvénient à cette technique de mise en œuvre à des températures de l’ordre de 250-330 °C.
L’utilisation d’une buse chauffante est recommandée et la trémie d’alimentation doit être maintenue fermée pour éviter le passage de poussières et d’humidité.
2. – Moulage par extrusion.
Les températures sont de l’ordre de 240-300 °C.
Cette technique permet de fabriquer tubes, barres, tuyaux, feuilles.
Les semi-produits sont ensuite transformés par thermoformage, souffl age, emboutissage sous vide.
108
3. – Usinage et fi nition.
Les polycarbonates peuvent être aisément usinés. Le polissage est réalisé avec des pâtes à polir exemptes de produits alcalins pour éviter toute corrosion.
L’assemblage de polycarbonates peut se faire par dissolution superfi cielle à l’aide de solvants ou par soudage aux ultrasons.
III. – RISQUES*
1. – Résines et adjuvants.
Les polycarbonates sont combustibles mais diffi cilement infl ammables.
Les résines ne présentent pas de risque toxicologique particulier à température ordinaire à l’exception du danger habituel dû aux poussières inertes lorsqu’elles sont manipulées à l’état pulvérulent.
Les risques dus aux adjuvants peuvent se manifester au moment de leur incorporation et/ou lors des travaux de fi nition :
— les fi bres de verre sont irritantes pour les voies respiratoires et la peau ;
— parmi les solvants, le dichlorométhane [105] très employé et le 1,2dichloroéthane sont très volatils ; ce sont de puissants narcotiques qui sont aussi dangereux pour les yeux et la peau. Le dioxanne et le monochlorobenzène sont également nocifs par inhalation.
2. – Dégradation thermique. a) Aux températures de mise en œuvre : 220-320 °C [2], [50].
Les polycarbonates commencent à fondre à partir de 220 °C.
Entre 250 °C et 280 °C, la dégradation est peu marquée ; il se dégage seulement des traces d’hydrocarbures aliphatiques insaturés et benzéniques
(benzène, toluène…) et des traces d’aldéhydes divers. Il peut y avoir
également émission des solvants chlorés utilisés parfois dans la fabrication
(dichlorométhane, monochlorobenzène) [50].
Mais vers 320 °C-340 °C, la décomposition débute réellement en entraînant un changement de couleur par modifi cation de structure et un dégagement des mêmes gaz en quantité plus importante.
b) Aux températures supérieures à 330 °C.
Vers 380 °C [7], la décomposition, importante, entraîne la formation d’anhydride carbonique, d’oxyde de carbone toxique, d’hydrocarbures, notamment le méthane, et de bisphénol A ou diphénylolpropane.
Les polycarbonates sont combustibles. Leur pouvoir calorifi que est d’environ 7 000 kcal/kg. Ils sont ordinairement diffi cilement infl ammables mais peuvent être infl ammables sous forme de feuilles, plaques ou tubes [8].
également le tableau en fi n de volume.
109
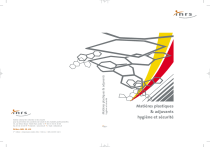
Lien public mis à jour
Le lien public vers votre chat a été mis à jour.