appelés couramment polyesters insaturés. INRS Matières plastiques
La réticulation du polyester insaturé par le solvant monomère, lui aussi insaturé, s’effectue après addition des adjuvants de durcissement, à chaud ou à température ambiante et forme un polyester réticulé thermorigide.
Il existe de nombreuses variétés de résines polyesters dont les caractéristiques physico-chimiques, et surtout les propriétés mécaniques, varient en fonction de la nature des diacides et des polyols qui ont servi à les fabriquer [3].
Les différents constituants de ces résines sont :
1.
–
Monomères.
Le plus utilisé est le styrène. On emploie également le méthacrylate de méthyle et pour certains polyesters spéciaux utilisés comme poudres
à mouler le phtalate de diallyle ou le cyanurate de triallyle. Des recherches sont en cours pour trouver des monomères moins volatils que le styrène ou le méthacrylate de méthyle et moins chers que le phtalate de diallyle.
2.
–
Catalyseurs.
Ce sont généralement des peroxydes organiques ajoutés à la résine à raison de 0,5 à 3 %.
Pour la mise en œuvre à la température ambiante, citons les peroxydes de méthyléthylcétone, de cyclohexanone, de benzoyle, l’hydroperoxyde de cumène, etc.
Pour la mise en œuvre à chaud, citons les peroxydes de benzoyle, de méthylisobutylcétone, le perbenzoate de butyle tertiaire, etc.
Les catalyseurs sont des produits très actifs, habituellement livrés sous forme de pâtes, poudres ou liquides ou bien incorporés dans un plastifi ant « fl egmatisant » (phosphate de tricrésyle, par exemple).
Sous l’action de la chaleur et de la lumière, ou à froid sous l’action d’un accélérateur, ils se scindent en radicaux libres qui provoquent l’ouverture des doubles liaisons du monomère, pour conduire au réseau tridimensionnel du polyester réticulé [36].
3. – Accélérateurs.
Ce sont des initiateurs de décompositions des peroxydes à des températures inférieures à leurs températures normales de décomposition.
On utilise habituellement :
— des sels métalliques (naphténate et octoate de cobalt, sels de manganèse et de vanadium) en solution dans du toluène à des concentrations de 1 à
6 % exprimées en métal ;
— des amines tertiaires (diméthylaniline, diéthylaniline, diméthylparatoluidine).
154
Citons aussi les sels d’ammonium quaternaire utilisés comme promoteurs associés au système catalyseur accélérateur.
4. – Charges et renforts.
Des charges de natures variées peuvent être ajoutées aux résines polyesters : poudres minérales (craie, ardoise, mica, talc, kaolin, silice, baryte, graphite, trioxyde d’antimoine) ou charges fi breuses (verre, carbone, polyamides, éventuellement amiante et sisal).
L’adjonction de ces fi bres (celles de verre sont les plus utilisées) donne les polyesters renforcés. Si les renforts sont orientés préférentiellement dans l’espace (feutres ou mâts de verre, tissus…), on obtient des polyesters stratifi és par empilement de couches enrobées de résine. La teneur d’un stratifi é en renfort peut varier de 25 à 75 % du poids total.
5. – Pigments et colorants.
Ces produits doivent pouvoir résister en milieu fortement oxydant, à des températures pouvant atteindre 200 °C. On utilise des pigments organiques et minéraux pour les polyesters opaques et des colorants organiques solubles pour les polyesters transparents.
Les principaux pigments matériaux employés sont des sels de cadmium, de chrome, de cobalt, de manganèse, de plomb, ainsi que des oxydes de fer anhydres et l’oxyde de titane.
6. – Agents anti-UV.
Les qualités de résines destinées à la fabrication de stratifi és translucides contiennent des adjuvants dont le rôle est d’empêcher le jaunissement sous l’action des rayons ultraviolets, tels que benzotriazoles, benzophénones ou salicylate de phényle.
7. – Solvants.
L’acétone et l’acétate d’éthyle sont utilisés pour faire varier la viscosité des polyesters notamment sous forme de gel-coat.
Les hydrocarbures chlorés sont utilisés comme solvants de nettoyage.
8. – Stabilisants.
L’hydroquinone ou certains phénols sont utilisés.
II. – MISE EN ŒUVRE
Les résines polyesters renforcées sont utilisées principalement pour la fabrication d’objets moulés et de stratifi és. Les résines non renforcées servent
à faire des revêtements, des laques et vernis, des liants et adhésifs divers…
155
Le plus souvent, le catalyseur et éventuellement l’accélérateur sont ajoutés l’un après l’autre au mélange juste avant la mise en œuvre.
Il est impératif de ne jamais mettre au contact le catalyseur et l’accélérateur avant leur introduction dans le mélange, sinon la décomposition immédiate du catalyseur se fait d’une manière explosive.
1. – Moulage.
Par coulée : on opère avec la résine exempte de solvants autres que le monomère et le plastifi ant, contenant en outre les charges, les adjuvants de durcissement et les pigments éventuels.
Le durcissement s’effectue soit à froid sous l’action du catalyseur et de l’accélérateur, soit à chaud sous l’action du catalyseur seul vers 110-130 °C.
Cette réaction est toujours exothermique (dégagement de chaleur).
Par compression : la mise en œuvre s’effectue à partir de mélanges pâteux, appelés « compounds » comprenant de la résine pure mélangée à des fi bres de verre (environ 20 % du poids de la résine), les charges minérales et les pigments.
Ces mélanges peuvent être livrés prêts à l’emploi. Ils peuvent également
être préparés à partir des divers constituants dans un malaxeur.
La pâte ainsi préparée est introduite dans des moules chauffants (100-
120 °C) puis soumise à des pressions de l’ordre de 50-100 bars sur une presse
à plateaux.
Il existe également des systèmes catalytiques spéciaux qui permettent de préparer des « préimprégnés », c’est-à-dire des tissus ou mâts de verre imprégnés de résine et de catalyseur et protégés par deux pellicules cellulosiques.
Ces imprégnés (ou prépregs) ne se conservent que quelques mois à l’abri de la chaleur. On les forme et les durcit comme précédemment sous presse en moules chauffants.
2. – Stratifi cation [121], [129].
Dans la plupart des cas, on applique d’abord sur le moule revêtu de l’agent de démoulage, une première couche de résine pure dans du styrène, appelée « gel-coat » ou couche de surface, diluée ou non dans de l’acétone ou de l’acétate d’éthyle.
Moulage par contact : ce procédé ne fait intervenir qu’un seul moule et le moulage est réalisé sans application de pression. Après enduction du moule avec un agent de démoulage et un « gel-coat », on y applique le renfort de verre que l’on imprègne ensuite de résine au rouleau ou à la raclette. Le durcissement se fait à froid (avec accélérateur) ou à chaud (en étuve).
Dans une variante de ce procédé, appelée « moulage au sac » après imprégnation à l’aide de la résine, l’ensemble est recouvert d’une membrane et on fait le vide entre la membrane et le moule.
156
Moulage par pression : les deux moules chauffants mâle et femelle sont montés sur les plateaux d’une presse. La résine est versée sur le renforcement disposé au préalable sur le moule. Suivant les cas, le renforcement peut être soit un tissu, soit des fi bres coupées et préalablement mises en forme selon le procédé dit « de préforme ».
Moulage par injection : le tissu de verre est placé dans un moule fermé et on y injecte la résine.
Enroulement fi lamentaire : on enroule sur un mandrin-moule tournant des couches croisées de fi l continu imprégné.
Procédés continus : une bande de feutre ou tissus de verre passe dans un bac de résine puis dans une étuve où elle est successivement mise en forme et durcie. Le stratifi é est sectionné à la sortie.
3. – Revêtements.
Les supports qui se prêtent aux revêtements par les résines polyesters sont très nombreux : bois, métal, ciment, etc. Après avoir mis sur le support une première couche d’accrochage, l’application de la résine se fait le plus souvent par projection au pistolet.
4. – Usinage.
En particulier sciage, perçage et fraisage.
Les outils servant au travail des alliages légers peuvent être utilisés.
Il est nécessaire de lubrifi er et de refroidir (habituellement à l’eau).
III – RISQUES*
1. – Résines et adjuvants.
Les polyesters réticulés après durcissement sont généralement considérés comme infl ammables.
Totalement polymérisés, ils ne présentent pas de risque toxicologique particulier à température ordinaire, à l’exception du danger dû au dégagement, lors de l’usinage, de poussières d’adjuvants en particulier.
Avant durcissement par contre, donc tout au long de la mise en œuvre, les risques sont importants [126], [127]. Ils sont dus principalement : a) Aux résines polyesters insaturés.
Ces résines sont infl ammables.
également le tableau en fi n de volume.
157
Elles peuvent être à l’origine de certaines sensibilisations de contact notamment si de petites quantités des produits de départ (diacides, diols) y subsistent [32].
b) Aux monomères.
Le styrène et le méthacrylate de méthyle sont des produits très réactifs, infl ammables, susceptibles de former avec l’air des mélanges explosifs.
Ils se dégagent au cours de la polycondensation en particulier pendant les premières heures [122], [125], [128].
Le styrène est un irritant des yeux, des voies respiratoires et de la peau.
À forte concentration, ses vapeurs peuvent exercer une action dépressive sur le système nerveux central.
Le méthacrylate de méthyle est un irritant des muqueuses oculaires et respiratoires, il peut être sensibilisant et exercer une action narcotique.
Parmi les composés « allyle » parfois utilisés, le phtalate de diallyle est irritant [27]. Le cyanurate de triallyle, nocif par inhalation, est aussi irritant pour la peau et les yeux [19], [30].
c) Aux catalyseurs.
Les peroxydes organiques sont très dangereux, car ce sont des composés instables pouvant donner lieu à des décompositions explosives.
Il est impératif de respecter certaines règles relatives à leur stockage et leur manipulation. Se reporter au chapitre III.5 des généralités.
d) Aux accélérateurs.
Les sels de cobalt, notamment le naphténate couramment utilisé, peuvent avoir une action sensibilisante [123] (cf. également chapitre III.5 des généralités).
Le toluène, dans lequel ils sont solubilisés, est nocif et irritant.
Les amines tertiaires : le durcissement des résines polyesters étant exothermique (dégagement de chaleur), il favorise le dégagement de vapeurs nocives. La diméthylaniline et la diéthylaniline sont toxiques par inhalation et contact cutané. Elles peuvent entraîner une dépression du système nerveux central et avoir des effets méthémoglobinisants.
e) Aux charges.
Les charges pulvérulentes présentent des risques au moment de leur incorporation dans la résine et lors de l’usinage :
— risques d’irritation respiratoire dans le cas de poussières inertes ;
— risques de silicose pour la silice, le talc ou le kaolin, qui peuvent contenir des quantités variables de silice libre cristallisée.
L’oxyde d’antimoine est irritant pour les voies respiratoires et nocif.
Parmi les charges fi breuses, l’amiante peut être responsable, d’une part de l’asbestose, d’autre part de cancers bronchiques et de mésothéliomes.
Les fi bres de verre très utilisées sont irritantes pour les voies respiratoires et la peau [124]. De plus, l’action mécanique qu’elles exercent sur l’épiderme favorise la pénétration des autres composants nocifs. Elles se dégagent
158
principalement au cours des opérations de revêtement et d’imprégnation et lors de l’usinage. f) Aux pigments.
Ils peuvent être particulièrement nocifs, lorsque la résine et ses adjuvants sont appliqués au pistolet.
Le jaune de chrome (chromate de plomb) en particulier présente les risques de sels de plomb et du chrome hexavalent. Se reporter au tableau en fi n de volume.
g) Aux solvants de nettoyage.
Les solvants de nettoyage des outils et récipients ayant servi à la mise en œuvre des résines polyesters sont surtout l’acétone et les solvants chlorés, notamment le dichlorométhane.
Les vapeurs d’acétone sont irritantes et très infl ammables.
Le dichlorométhane exerce une action narcotique.
h) Aux agents anti-UV.
La benzophénone est légèrement irritante.
Pour les mesures de prévention à appliquer au cours de la mise en
œuvre des polyesters insaturés, se reporter notamment aux documents cités en référence 121, 125, 128 et 163.
2. – Dégradation thermique. a) Au cours de la mise en œuvre.
Le durcissement par réticulation étant exothermique, il se produit des dégagements importants des monomères styrène, méthacrylate de méthyle et de certains adjuvants notamment les amines tertiaires servant d’accélérateurs comme il a été dit au paragraphe précédent.
b) En cas de pyrolyse ou de combustion.
Les polyesters insaturés et les monomères dans lesquels ils sont livrés sont infl ammables. Les polyesters réticulés rigides le sont aussi.
Toutefois, il existe certains polyesters diffi cilement infl ammables :
— ceux fabriqués à partir de certains produits de base contenant des atomes de chlore ou de brome ;
— ceux renfermant des retardateurs de combustion (trioxyde d’antimoine notamment) [8].
Il faut noter alors la plus grande toxicité des fumées (présence d’acide chlorhydrique ou bromhydrique) lorsque l’incendie se déclenche malgré la présence des ignifugeants ou en cas de pyrolyse sans air (feux qui couvent).
Les produits qui se dégagent lors de la combustion sont [22], [33] :
— l’anhydride carbonique, l’oxyde de carbone, et des hydrocarbures divers ;
— les acides chlorhydrique et bromhydrique corrosifs, dans le cas des produits ignifugés ;
— des composés azotés toxiques (ammoniac…), s’il reste dans la résine une partie des amines utilisées pour accélérer le durcissement.
159
PHÉNOPLASTES
PHÉNOL-FORMALDÉHYDE OU PHÉNOL-FORMOL
Abréviation normalisée : PF
Matières à mouler
Noms commerciaux
Résines
AZOLONE AÉRODUX FRÉQUENCITE
DUREZ AMBROLITHE
FATURAN CASCOPHEN
FIBÉRITE EPOK ERVAPHÈNE
MOLDÉSITE NORSOPHEN
PROGILITE PHÉNARON
RÉSART PHÉNOREZ
RÉSINOL PLYOPHEN
ROCKITE REDUX
RUTAFORM RÉSOPHÈNE
SÉTACÉGÉITE RÉSURFÈNE
SIRFEN SOLUPHÈNE
TROLITAN SYNRÉSOL
VYNCOLITE TECHNOPHEN
URAVAR
VARCUM
XYLOK
I. – CARACTÉRISTIQUES
Les résines phénoplastes sont obtenues par polycondensation de phénols (phénol, crésol, résorcine…) et d’aldéhydes (formol, furfuraldéyde…).
Les plus courantes sont les résines phénol-formol.
160
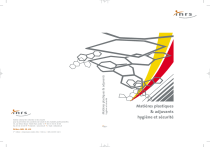
Lien public mis à jour
Le lien public vers votre chat a été mis à jour.