CNC 8070 Solutions d’erreurs. (Ref: 1901) TRADUCTION DU MANUEL ORIGINAL SÉCURITÉS DE LA MACHINE Ce manuel est une traduction du manuel original. Ce manuel, ainsi que les documents découlant de celui-ci, ont été rédigés en espagnol. En cas de contradictions entre le document en espagnol et ses traductions, la rédaction en langue espagnole prévaudra. Le manuel original portera la mention "MANUEL ORIGINAL". Il est de la responsabilité du fabricant de la machine d'activer les sécurités de celle-ci dans le but d'éviter des accidents personnels et des dommages à la CNC ou aux installations qui y sont connectées. Pendant le démarrage et la validation des paramètres de la CNC, il y a lieu de vérifier l'état des sécurités suivantes. Si l'une des sécurités est désactivée, la CNC affiche un message d'avertissement. • Alarme de mesure pour axes analogiques. • Limites de logiciel pour axes linéaires analogiques et sercos. • Surveillance de l'erreur de poursuite pour axes analogiques et sercos (sauf la broche), aussi bien sur la CNC que sur les asservissements. • Test de tendance sur les axes analogiques. FAGOR AUTOMATION n'assume aucune responsabilité en cas d'accidents personnels et de dommages physiques ou matériels subis ou provoqués par la CNC s'ils sont dus à l'annulation d'une sécurité quelconque. AMPLIATIONS DE HARDWARE FAGOR AUTOMATION n'assume aucune responsabilité en cas d'accidents personnels et de dommages physiques ou matériels subis ou provoqués la CNC s'ils sont dus à la modification du hardware par du personnel non autorisé par Fagor Automation. La modification du hardware de la CNC par du personnel non autorisé par Fagor Automation implique l'annulation de la garantie. PAGE VIERGE VIRUS INFORMATIQUES FAGOR AUTOMATION garantit que le logiciel installé ne contient aucun virus informatique. L'usager est tenu de filtrer l'équipement de tout virus afin d'en garantir son bon fonctionnement. La présence de virus informatiques dans la CNC peut provoquer son mauvais fonctionnement. FAGOR AUTOMATION n'assume aucune responsabilité en cas d'accidents personnels et de dommages physiques ou matériels subis ou provoqués par la CNC s'ils sont dus à la présence d'un virus informatique dans le système. La présence de virus informatiques dans le système implique la perte de la garantie. PRODUITS À DOUBLE USAGE. Pour les produits fabriqués par FAGOR AUTOMATION à partir du 1er avril 2014, chaque produit inclus suivant le Règlement UE 428/2009 dans la liste de produits à double usage, comprendra dans son identification le texte MDU et aura besoin de la licence d'exportation suivant la destination. Tous droits réservés. La reproduction totale ou partielle de cette documentation est interdite, de même que sa transmission, transcription, traduction ou son enregistrement dans un système de récupération de données sans autorisation expresse de Fagor Automation. Toute copie ou utilisation, totale ou partielle, non autorisée du logiciel est interdite. L'information contenue dans ce manuel peut être sujette à des variations dues à des modifications techniques. Fagor Automation se réserve le droit de modifier le contenu du manuel sans être tenue à en communiquer les changements. Toutes les marques enregistrées ou commerciales figurant dans le manuel appartiennent à leurs propriétaires respectifs. L’utilisation de ces marques par des tiers pour leurs propres fins peut aller à l’encontre des droits des propriétaires. ·2· La CNC peut réaliser d’autres fonctions que celles figurant dans la documentation associée, mais Fagor Automation ne garantit pas la validité de ces applications. En conséquence, sauf autorisation expresse de Fagor Automation, toute application de la CNC ne figurant pas dans la documentation doit être considérée comme "impossible". En tous cas, Fagor Automation n'assume aucune responsabilité en cas de blessures, dommages physiques ou matériels, subis ou provoqués par la CNC, si celle-ci est utilisée de manière différente de celle expliquée dans la documentation concernée. Le contenu de ce manuel et sa validité pour le produit décrit ont été vérifiés. Même ainsi, il se peut qu'une erreur involontaire ait été commise et c'est pour cela que la coïncidence absolue n'est pas garantie. De toute façon, on vérifie régulièrement l'information contenue dans le document et on effectue les corrections nécessaires qui seront comprises dans une édition ultérieure. Nous vous remercions de vos suggestions d’amélioration. Les exemples décrits dans ce manuel sont orientés à l'apprentissage. Avant de les utiliser dans des applications industrielles, ils doivent être convenablement adaptés et il faut s'assurer aussi que les normes de sécurité sont respectées. S o l ut i o n s d ’ e r r e ur s . INDEX 0000-0999.......................................................................................5 1000-1999.....................................................................................21 2000-2999...................................................................................107 3000-3999...................................................................................129 4000-4999...................................................................................150 5000-5999...................................................................................160 6000-6999...................................................................................166 7000-7999...................................................................................177 8000-8999...................................................................................182 9000-9999...................................................................................221 23000-23999...............................................................................226 24000-24999...............................................................................227 Module RCS-S. ..........................................................................229 Table d'outils et de magasin....................................................234 Éditeur de profils ......................................................................236 CNC 8070 (REF: 1901) ·3· PAGE VIERGE ·4· S o l ut i o n s d ’ e r r e ur s . 0000-0999 0001 'ERREUR DU SYSTÈME' DÉTECTION CAUSE SOLUTION 0002 'WARNING DU SYSTÈME' DÉTECTION CAUSE SOLUTION 0003 Au cours de l'exécution. Avis de situations internes pouvant terminer en erreurs du système. La CNC se récupère normalement en fermant le warning. Si l'erreur persiste, contacter votre fournisseur. 'Erreur dans la demande de mémoire. Réinitialiser Windows et la CNC' DÉTECTION CAUSE SOLUTION 0004 Au cours de l'exécution. Erreurs de logiciel ou de hardware qui provoquent des données corrompues et/ou des résultats incohérents. Ce type d’erreurs force normalement la sortie de la CNC. Si l'erreur persiste, contacter votre fournisseur. Au cours du démarrage de la CNC. La CNC n’a pas assez de mémoire ou la mémoire est excessivement fragmentée. Redémarrer l'équipement et réinitialiser la CNC. Si la mémoire est trop fragmentée, l’erreur disparaîtra au redémarrage de l’équipement et de la CNC. Si l’erreur se répète à plusieurs démarrages successifs, veuillez contacter votre fournisseur. 'Erreur de checksum dans les données du PLC' DÉTECTION CAUSE Au cours du démarrage de la CNC. Les données du PLC relatives aux marques, compteurs, temporisateurs et registres emmagasinés dans le disque ne sont pas valables. Le fichier plcdata.bin contenant ces données n’existe pas, n’est pas accessible ou il est corrompu. EN CONSÉQUENCELes données du PLC relatives aux marques compteurs, temporisateurs et registres ont été perdues. SOLUTION Si l’erreur est répétée à plusieurs démarrages successifs de la CNC, veuillez contacter votre fournisseur. 0005 'La CNC n’est pas mise hors tension correctement, on doit la référencer' DÉTECTION CAUSE Au cours du démarrage de la CNC. Les données de la CNC relatives aux cotes, décalages d’origines, etc. sont sauvegardées sur le disque ne sont pas valables. Le fichier orgdata.tab contenant ces données n’existe pas, n’est pas accessible ou est corrompu. EN CONSÉQUENCELes données de la CNC relatives aux cotes, décalages d’origines, compteur de pièces, cinématiques, etc. ont été perdues. SOLUTION Si l’erreur est répétée à plusieurs démarrages successifs de la CNC, veuillez contacter votre fournisseur. 0006 'La préparation dépasse la moitié du temps de cycle' DÉTECTION Au cours du démarrage de la CNC ou pendant l'exécution. CAUSE La préparation de données dans la CNC par cycle de PLC a une durée excessive. EN CONSÉQUENCELe paramètre PREPFREQ n'a pas l'effet souhaité. SOLUTION Diminuer la valeur du paramètre PREPFREQ du canal. 0007 CNC 8070 'Pour terminer la RAZ on doit réinitialiser la CNC' DÉTECTION CAUSE SOLUTION Après une RAZ de la CNC. L’utilisateur a exécuté deux RAZ consécutives de la CNC et aucune d’elles n’a finalisé correctement. Réinitialiser la CNC. Si l’utilisateur tape sur la touche [RAZ] une troisième fois, l’application CNC se ferme. (REF: 1901) ·5· S o l ut i o n s d ’ e r r e ur s . 0008 'La touche a été refusée' DÉTECTION CAUSE SOLUTION 0010 Au cours du démarrage de la CNC ou pendant l'exécution. La CNC a détecté que deux touches incompatibles ont été tapées en même temps. La touche [START], les touches de démarrage de la broche et la touche d’arrêt orienté de la broche doivent toujours être tapées seules; en les tapant simultanément avec une autre touche, les deux s’annulent automatiquement. Si cela a été un acte involontaire de l’utilisateur, ignorer l’erreur. Si l’erreur persiste ou est affichée au démarrage, vérifier sur le clavier qu’aucune touche n’est tapée (engagée). Si l’erreur est répétée à plusieurs démarrages successifs de la CNC, veuillez contacter votre fournisseur. 'Erreur dans le test RAM avec batterie' DÉTECTION CAUSE Au cours du démarrage de la CNC. Le test de démarrage a détecté une erreur de checksum dans les données de la NVRAM et par conséquent une défaillance dans celle-ci. EN CONSÉQUENCELes données enregistrées peuvent ne pas être correctes (données relatives aux cotes, décalages d’origines, compteur de pièces, cinématiques, etc.). SOLUTION Si l’erreur est répétée à plusieurs démarrages successifs de la CNC, veuillez contacter votre fournisseur. 0011 'Erreur de checksum dans les données de la recherche de bloc' DÉTECTION CAUSE Au cours du démarrage de la CNC. Erreur de cheksum des données nécessaires pour exécuter une recherche de bloc automatique. EN CONSÉQUENCEIl n’est pas possible d’exécuter une recherche de bloc automatique. SOLUTION Si l’erreur est répétée à plusieurs démarrages successifs de la CNC, veuillez contacter votre fournisseur. 0016 Arrêt/Redémarrage détecté pendant le démarrage du système d'exploitation. DÉTECTION CAUSE SOLUTION 0017 Arrêt/redémarrage détecté en raison d'une chute de l'alimentation. DÉTECTION CAUSE SOLUTION 0020 CNC 8070 (REF: 1901) ·6· Au cours du démarrage de la CNC ou lors du changement de la page. La CNC accède à une variable d’interface qui n’existe pas. Veuillez contacter le fabricant de la machine ou le créateur des pages de votre interface pour supprimer ou corriger l’accès à la variable. Absence de clavier CAN. DÉTECTION CAUSE SOLUTION 0022 Au cours du démarrage de la CNC. La CNC a détecté un arrêt/redémarrage imprévu en raison d'une chute de l'alimentation. Les données de la CNC relatives aux cotes, transfert d’origines, compteur de pièces, cinématiques, etc. peuvent être perdues. Si l’erreur est répétée à plusieurs démarrages successifs de la CNC, veuillez contacter votre fournisseur. 'Accès à variable incorrect' DÉTECTION CAUSE SOLUTION 0021 Au cours du démarrage de la CNC. La CNC a détecté un arrêt/redémarrage imprévu lors du démarrage du système d'exploitation. Les données de la CNC relatives aux cotes, transfert d’origines, compteur de pièces, cinématiques, etc. peuvent être perdues. Si l’erreur persiste lors de démarrages successifs de la CNC, veuillez contacter Fagor. Au cours du démarrage de la CNC. La CNC n'a pas détecté le clavier CAN. Vérifier dans le mode diagnosis l'état du bus CAN et si la CNC reconnaît le clavier. Si l’erreur persiste, veuillez contacter le service après-vente. 'Variable interdite dans l’environnement de la mise au point' DÉTECTION CAUSE SOLUTION Lors de la définition des variables dans l'environnement de la mise au point. Dans l’environnement de la mise au point une variable interdite est définie. Consulter la liste des variables permises dans le manuel d'utilisation. S o l ut i o n s d ’ e r r e ur s . 0023 'Il faut arrêter le programme afin d’initier l'enregistrement pour la première fois' DÉTECTION CAUSE SOLUTION 0024 'Erreur en initiant l'enregistrement' DÉTECTION CAUSE SOLUTION 0025 CAUSE SOLUTION SOLUTION SOLUTION Lors de la définition des variables dans un canal de l'oscilloscope. La variable affectée au canal de l'oscilloscope n'est pas Mlink-II. L’accès aux variables et/ou paramètres des dispositifs de Mechatrolink n'est disponible que pour le mode Mlink-II à 32 octets. 'Il faut programmer l'axe de la variable avec son nom' DÉTECTION CAUSE SOLUTION 0031 Lors de la définition des variables dans un canal de l'oscilloscope. Le paramètre défini dans l'oscillateur appartient à un axe Mechatrolink. L'accès à des variables et/ou des paramètres des dispositifs Mechatrolink est uniquement disponible pour le mode Mlink-II à 32 bytes. 'Uniquement MLINKI permet des variables DRV ou MLINK dans un canal de l'oscilloscope' DÉTECTION CAUSE SOLUTION 0030 Lors de la définition des variables dans un canal de l'oscilloscope. La variable ou le paramètre est exclusif à un axe mechatrolink, mais l'axe pour lequel la variable ou le paramètre est sollicité n'est pas un axe mechatrolink Sélectionner un axe Mechatrolink. La variable ou le paramètre de l'axe doit exister pour l'axe demandé. Ne permet pas d'associer un paramètre mechatrolink avec un canal de l'oscillateur. DÉTECTION CAUSE SOLUTION 0029 Lors de la définition des variables dans un canal de l'oscilloscope. La variable assignée au canal de l’oscilloscope est de simulation, est asynchrone ou est un string. Consulter la liste des variables permises dans le manuel d'utilisation. L'axe n'est pas mechatrolink. DÉTECTION CAUSE 0028 Pendant l’enregistrement des variables associées aux symboles externes PDEF définis dans le programme de PLC. Le fichier plc_prg.sym contenant l’information nécessaire pour créer les variables associées aux symboles externes PDEF est corrompu. Supprimer le fichier plc_prg.sym et compiler le programme PLC pour créer de nouveau ce fichier. Si l'erreur persiste, contacter votre fournisseur. 'Variable interdite dans l'environnement de l'oscilloscope' DÉTECTION CAUSE 0027 À l'initialisation de l'enregistrement dans l'oscilloscope. Il n’y a aucune variable définie dans les canaux de l’oscilloscope, il y a plus de deux variables Sercos du même asservissement ou la syntaxe d’une des variables n’est pas correcte. Vérifier les variables définies dans les canaux de l'oscilloscope. L'oscilloscope ne peut accéder qu'aux variables Sercos de chaque asservissement. 'Erreur en enregistrant les données du PLC'. DÉTECTION 0026 À l'initialisation de l'enregistrement dans l'oscilloscope. C’est la première fois que l’oscilloscope commence un enregistrement et qu’il y a un programme en exécution. L'enregistrement utilise des variables de l'asservissement qui ou bien ne sont pas dans la table de paramètres machine ou bien sont dans cette table mais sont asynchrones. Arrêter le programme en exécution. Au cours de l'exécution. Dans une des variables de l'asservissement (DRV), l'axe est programmé avec son numéro logique ou indice dans le canal. Dans ces variables l'axe doit être programmé avec son nom. CNC 8070 'Uniquement MLINKI permet des paramètres mechatrolink dans l'oscilloscope' DÉTECTION CAUSE SOLUTION Lors de la définition des paramètres dans un canal de l'oscilloscope. Le paramètre affecté au canal de l'oscilloscope n'est pas Mlink-II. L’accès aux variables et/ou paramètres des dispositifs de Mechatrolink n'est disponible que pour le mode Mlink-II à 32 octets. (REF: 1901) ·7· S o l ut i o n s d ’ e r r e ur s . 0032 Paramètre ou variable mechatrolink hors plage. DÉTECTION CAUSE SOLUTION 0036 Incohérence lors de la récupération de l'outil actif. DÉTECTION CAUSE SOLUTION 0037 SOLUTION SOLUTION SOLUTION 0042 ·8· Pendant la validation des paramètres machine. Dans la table des fonctions M, une fonction est répétée. Corriger la définition des fonctions. Dans la table il ne peut y avoir deux fonctions M avec le même numéro. 'Valeur de paramètre machine non valide' DÉTECTION CAUSE SOLUTION (REF: 1901) Pendant la validation des paramètres machine. Dans la table de fonctions M, il y a une fonction avec sous-routine associée et le type de synchronisation Avant-Avant ou Avant-Après. La CNC exécute toujours la sous-routine associée à une fonction M à la fin du bloc dans lequel la fonction est programmée. Définir la fonction M sans synchronisation ou bien avec synchronisation Après-Après. 'M en double dans la table' DÉTECTION CAUSE SOLUTION CNC 8070 Au cours du démarrage de la CNC. Les informations des correcteurs enregistrées sur le disque ne correspondent pas à celles conservées par le gestionnaire des outils, en raison d'un arrêt inapproprié ou d'un défaut du système. Le fichier qui contient ces données n’existe pas, n’est pas accessible ou est corrompu. Vérifier les correcteurs appropriés avant de continuer. Définir dans le tableau des outils les correcteurs d'outil et, le cas échéant, réaliser un changement d'outil. Si l’erreur est répétée à plusieurs démarrages successifs de la CNC, veuillez contacter votre fournisseur. 'M Avant-Avant ou Avant-Après avec sous-routine n'admet pas de mouvements dans le bloc' DÉTECTION CAUSE 0041 Au cours du démarrage de la CNC. Les informations de l'outil suivant enregistrées sur le disque ne correspondent pas à celles conservées par le gestionnaire des outils, en raison d'un arrêt inapproprié ou d'un défaut du système. Le fichier qui contient ces données n’existe pas, n’est pas accessible ou est corrompu. S'assurer de l'outil approprié avant de continuer. Définir dans la CNC l'outil suivant (par exemple, depuis MDI) et, le cas échéant, réaliser un changement d'outil. Si l’erreur est répétée à plusieurs démarrages successifs de la CNC, veuillez contacter votre fournisseur. Inconsistance dans la récupération des correcteurs d'outil. DÉTECTION CAUSE 0040 Au cours du démarrage de la CNC. Les informations de l'outil actif enregistrées sur le disque ne correspondent pas à celles conservées par le gestionnaire des outils, en raison d'un arrêt inapproprié ou d'un défaut du système. Le fichier qui contient ces données n’existe pas, n’est pas accessible ou est corrompu. S'assurer de l'outil approprié avant de continuer. Définir dans le tableau des outils celui qui est actif et, le cas échéant, réaliser un changement d'outil. Si l’erreur est répétée à plusieurs démarrages successifs de la CNC, veuillez contacter votre fournisseur. Inconsistance dans la récupération de l'outil suivant. DÉTECTION CAUSE 0038 Pendant la validation des paramètres machine. Le paramètre ou la variable présente une valeur erronée. Affecter au paramètre ou variable une valeur dans les limites autorisées. La fenêtre d’erreur affiche le paramètre ou la variable erroné et les valeurs maximale et minimale autorisée. Pendant la validation des paramètres machine. Le paramètre machine à une valeur non valide. Affecter au paramètre machine une valeur dans les limites permises. La fenêtre d’erreur affiche le paramètre erroné et la valeur maximale et minimale permise. S o l ut i o n s d ’ e r r e ur s . 0043 'La CNC doit être redémarrée pour assumer la nouvelle valeur' DÉTECTION CAUSE SOLUTION 0044 'Nom d'axe non valide ou non défini' DÉTECTION CAUSE SOLUTION 0045 SOLUTION SOLUTION Pendant la validation des paramètres machine. L’axe esclave d’un axe gantry est déjà défini comme axe esclave sur un autre axe gantry. Corriger la table d'axes gantry. Un axe ne peut pas être esclave de plusieurs maîtres. 'Un axe maître ne peut pas être en même temps esclave et vice-versa' DÉTECTION CAUSE SOLUTION 0050 Pendant la validation des paramètres machine. L’axe esclave d’un axe gantry est l’axe maître d'un autre axe gantry. Corriger la table d'axes gantry. L’axe maître d’un axe gantry ne peut pas être esclave sur un autre axe gantry. 'Un axe ne peut pas être esclave de plusieurs maîtres' DÉTECTION CAUSE 0049 Pendant la validation des paramètres machine. Les possibles causes sont les suivantes: • L’utilisateur a assigné à un paramètre machine le nom d’un axe qui n’existe pas. • Dans la compensation volumétrique de base, l'un des axes VMOVAXIS ou VCOMPAXIS n'a pas été défini. Corriger les paramètres machine. Les noms d’axe valables sont ceux définis dans le paramètre AXISNAME. 'Un axe principal ne peut pas être défini comme esclave' DÉTECTION CAUSE SOLUTION 0048 Pendant la validation des paramètres machine. L’utilisateur a défini le paramètre machine avec un nom de broche incorrect. Corriger les paramètres machine. Les noms de broche valables sont ceux définis dans le paramètre SPDLNAME. Dans le paramètre SPDLNAME, le nom de la broche sera défini par 1 ou 2 caractères. Le premier caractère doit être la lettre S. Le deuxième caractère est optionnel et sera un suffixe numérique de 1 à 9. Ainsi, le nom des broches pourra être n'importe lequel du rang S, S1…S9. 'Axe inexistant.' DÉTECTION CAUSE 0047 Pendant la validation des paramètres machine. Le paramètre machine n'est pas défini ou bien il a un nom d'axe incorrect. Corriger les paramètres machine. Les noms d’axe valables sont ceux définis dans le paramètre AXISNAME. Dans le paramètre AXISNAME, le nom de l'axe sera défini par 1 ou 2 caractères. Le premier caractère doit être une des lettres X - Y - Z - U - V - W - A - B - C. Le deuxième caractère est optionnel et sera un suffixe numérique entre 1 et 9. Ainsi le nom des axes pourra être n'importe lequel du rang X, X1…X9,...C, C1…C9.. 'Nom de broche non valable' DÉTECTION CAUSE SOLUTION 0046 Pendant la validation des paramètres machine. L’utilisateur a modifié un paramètre machine et l’application CNC doit être redémarrée pour que le paramètre assume sa nouvelle valeur. Réinitialiser la CNC. Pendant la validation des paramètres machine. L’axe maître d’un axe gantry est l’axe esclave sur un autre axe gantry ou vice-versa. Corriger la table d'axes gantry. L’axe maître d’un axe gantry ne peut être esclave sur un autre axe gantry ni vice-versa. 'Les axes maître et esclave doivent être du même type (AXISTYPE)' DÉTECTION CAUSE SOLUTION Pendant la validation des paramètres machine. Les deux axes d’un couple gantry ne sont pas du même type; linéaires ou rotatifs. Les axes d’un couple gantry doivent être du même type, linéaires ou rotatifs (paramètre AXISTYPE. Réviser la table d'axes gantry et / ou le paramètre AXISTYPE de deux axes. CNC 8070 (REF: 1901) ·9· S o l ut i o n s d ’ e r r e ur s . 0051 'Les axes maître et esclave doivent avoir certains paramètres avec la même valeur' DÉTECTION CAUSE SOLUTION 0052 'Différence de modules trop petite' DÉTECTION CAUSE SOLUTION 0053 SOLUTION SOLUTION SOLUTION SOLUTION SOLUTION 0058 SOLUTION 0059 Pendant la validation des paramètres machine. Pour que les changements réalisés dans la table de HMI prennent effet, l’application CNC doit être redémarrée. Réinitialiser la CNC. 'Il faut redémarrer la CNC pour assumer les changements dans la table du magasin' DÉTECTION CAUSE SOLUTION ·10· Pendant la validation des paramètres machine (table de compensation de vis). Dans les tables de compensation de vis, la différence entre deux erreurs consécutives est supérieure à la distance qui sépare les deux points. Dans les tables de compensation de vis la pente de l’erreur ne peut pas être supérieure à 1. Augmenter la distance entre points ; si cela n’est pas possible, l’erreur saisie pour la vis de l’axe est tellement grande qu’il n’est pas possible de la compenser. 'Il faut redémarrer la CNC pour assumer les changements dans la table de HMI' DÉTECTION CAUSE (REF: 1901) Pendant la validation des paramètres machine. Dans les tables de compensation, les points à compenser ne sont pas ordonnés correctement ou la valeur à compenser dans tous les points a une valeur zéro. Le paramètre POSITION dans les tables de compensation doit prendre des valeurs ascendantes. La valeur à compenser ne peut pas être zéro sur tous les points. 'Table de compensation avec pente d'erreur supérieure à 1' DÉTECTION CAUSE CNC 8070 Pendant la validation des paramètres machine. Dans les tables de compensation croisée, en suivant les différentes associations d’axes compensés (paramètre COMPAXIS) et d’axes dont les déplacements altèrent les axes qui se compensent (paramètre MOVAXIS), il y a un axe dont le déplacement dépend de lui-même. Réviser la relation entre les compensations croisées définies. Vérifier les paramètres MOVAXIS et COMPAXIS des compensations croisées définies. 'Positions de la table de compensation non ascendantes' DÉTECTION CAUSE 0057 Pendant la validation des paramètres machine. Dans une des tables de compensation croisée, l’axe compensé coïncide avec l’axe dont le déplacement altère l’axe qui est compensé. Sur chaque table de compensation croisée, les deux axes doivent être différents (paramètres MOVAXIS et COMPAXIS) 'Un même axe est en même temps cause et effet de la compensation croisée' DÉTECTION CAUSE 0056 Pendant la validation des paramètres machine. Dans la table de paramètres de manuel, il y a deux manivelles ou plus assignées au même axe. Un axe ne peut avoir affecté qu'une seule manivelle. 'Les axes MOVAXIS et COMPAXIS doivent être différents' DÉTECTION CAUSE 0055 Pendant la validation des paramètres machine. La différence entre les paramètres machine MODUPLIM et MODLOWLIM est inférieure à la résolution de l’axe. Vérifier la résolution de l'axe; si elle est correcte, augmenter MODUPLIM ou diminuer MODLOWLIM. 'Paramètre MPGAXIS répété sur plusieurs manivelles' DÉTECTION CAUSE 0054 Pendant la validation des paramètres machine. Les deux axes d’un axe gantry n’ont pas les mêmes propriétés. Réviser la table d'axes gantry et / ou les suivants paramètres machine des axes. • Les axes linéaires doivent avoir les paramètres AXISMODE, FACEAXIS et LONGAXIS égaux. • Les axes rotatifs doivent avoir les paramètres AXISMODE, SHORTESTWAY et CAXIS égaux. Pendant la validation des paramètres machine. Pour que les changements réalisés dans la table du magasin prennent effet, l’application CNC doit être redémarrée. Réinitialiser la CNC. S o l ut i o n s d ’ e r r e ur s . 0060 'La vitesse maximale de manuel dépasse la vitesse maximale de l'axe' DÉTECTION CAUSE SOLUTION 0061 'La vitesse rapide du mode manuel dépasse la vitesse maximale de l'axe' DÉTECTION CAUSE SOLUTION 0062 SOLUTION SOLUTION Pendant la validation des paramètres machine. Dans les tables d'assignation de noms d'axes (paramètre AXISNAME), l'axe esclave est défini avant l'axe maître. Définir l’axe maître dans la table avant l’axe esclave ou permuter l’axe maître et l’axe esclave dans le couple gantry ou tandem. 'Axes Gantry: L'axe esclave ne peut pas avoir DECINPUT (micro de référence) si l'axe maître ne l'a pas' DÉTECTION CAUSE SOLUTION 0070 Pendant la validation des paramètres machine. Un axe rotatif unidirectionnel ne peut faire partie d’un axe gantry. L'axe ne peut être unidirectionnel (paramètre UNIDIR). Utiliser un autre type d'axe pour construire l'axe gantry. 'Axes Gantrys/Tandem: L'axe esclave ne peut pas précéder à l'axe maître en AXISNAME' DÉTECTION CAUSE 0069 Pendant la validation des paramètres machine. L’un des axes formant l’axe gantry, dans un jeu de paramètres a le paramètre REFSHIFT défini avec une valeur différente de 0. Définir le paramètre REFSHIFT de toutes les gammes avec une valeur 0. 'Un axe Gantry ne peut pas être unidirectionnel' DÉTECTION CAUSE SOLUTION 0068 Pendant la validation des paramètres machine. Un axe hirth ne peut pas faire partie d’un axe gantry. L'axe ne peut pas être hirth (paramètre HIRTH). Utiliser un autre type d'axe pour construire l'axe gantry. 'Un axe Gantry ne peut pas avoir REFSHIFT' DÉTECTION CAUSE 0067 Pendant la validation des paramètres machine. Le type d’I0 ne coïncide pas sur les deux axes du couple gantry. Les deux axes doivent avoir le même type de I0 (paramètre I0TYPE). 'Un axe Hirth ne peut pas être Gantry' DÉTECTION CAUSE SOLUTION 0066 Pendant la validation des paramètres machine. Le paramètre INCJOGFEED est supérieur à G00FEED. Diminuer la valeur du paramètre INCJOGFEED; il doit être inférieur à G00FEED. 'Les axes maître et esclave doivent avoir le même I0TYPE' DÉTECTION CAUSE SOLUTION 0065 Pendant la validation des paramètres machine. Le paramètre JOGFEED est supérieur à G00FEED. Diminuer la valeur du paramètre JOGFEED; il doit être inférieur à G00FEED. 'La vitesse de jog incrémental dépasse la vitesse maximale de l'axe' DÉTECTION CAUSE SOLUTION 0064 Pendant la validation des paramètres machine. Le paramètre JOGRAPFEED est supérieur à G00FEED. Diminuer la valeur du paramètre JOGRAPFEED; il doit être inférieur à G00FEED. 'La vitesse de jog continu dépasse la vitesse maximale de l'axe' DÉTECTION CAUSE SOLUTION 0063 Pendant la validation des paramètres machine. Le paramètre MAXMANFEED est supérieur à G00FEED. Diminuer la valeur du paramètre MAXMANFEED; il doit être inférieur à G00FEED. Pendant la validation des paramètres machine. L’axe esclave d’un axe gantry a un micro et l’axe maître non. Sur un axe gantry l’axe maître, les deux axes ou aucun (paramètre DECINPUT) pourront avoir un micro de référence. CNC 8070 'Axes Gantrys/Tandem: LIMIT+ et LIMIT- ne peuvent pas être différents sur le maître et l'esclave' DÉTECTION CAUSE SOLUTION Pendant la validation des paramètres machine. Dans un couple gantry ou tandem, les limites de logiciel des deux axes sont différentes. Définir les deux axes avec les mêmes limites de logiciel (paramètres LIMIT+ et LIMIT-). (REF: 1901) ·11· S o l ut i o n s d ’ e r r e ur s . 0071 'Surveillance d'erreur de poursuite non active dans la CNC' DÉTECTION CAUSE SOLUTION 0072 'Alarme de mesure sans activer' DÉTECTION CAUSE SOLUTION 0073 SOLUTION SOLUTION SOLUTION SOLUTION 0079 ·12· Pendant la validation des paramètres machine. Un axe gantry est formé par des axes de canaux différents. Sur un axe gantry, les deux axes doivent appartenir au même canal. 'Un axe esclave Gantry ne peut pas être stationné' DÉTECTION CAUSE SOLUTION (REF: 1901) Pendant la validation des paramètres machine. Il y a un axe ou une broche affectés à plusieurs canaux. Corriger les paramètres machine CHAXISNAME et CHSPDLNAME sur tous les canaux. Un axe ou une broche ne peut appartenir qu’à un canal ou n’appartenir à aucun. 'Les axes maître et esclave doivent appartenir au même canal' DÉTECTION CAUSE SOLUTION CNC 8070 Pendant la validation des paramètres machine. La valeur du paramètre CHNAXIS est supérieure à la valeur du paramètre NAXIS ou la valeur du paramètre CHNSPDL est supérieure à la valeur du paramètre NSPDL. Corriger les paramètres machine. 'Axe ou broche assignée à plus d'un canal' DÉTECTION CAUSE SOLUTION 0078 Pendant la validation des paramètres machine. Les paramètres NDIMOD et NDOMOD doivent être égaux au nombre de modules d’entrées et de sorties détectées par hardware. Corriger les paramètres NDIMOD et NDOMOD. 'La somme d'axes et de broches par canal dépasse le nombre totald'axes ou de broches' DÉTECTION CAUSE 0077 Pendant la validation des paramètres machine. Sur un axe ou sur une broche, le test de tendance est désactivé. Cette situation ne devrait être permise que pendant la mise au point ; une fois la mise au point terminée, le test de tendance doit être activé. Sur les axes et broches, activer le test de tendance (paramètre TENDENCY). 'Table de configuration des IOs non valable' DÉTECTION CAUSE 0076 Pendant la validation des paramètres machine. Dans un axe, les limites de logiciel ne sont pas activées. Les paramètres LIMIT+ et LIMIT- de l'axe ont tous les deux la valeur 0. Définir les limites de logiciel de tous les axes (paramètres LIMIT+ et LIMIT-). 'Test de tendance sans activer' DÉTECTION CAUSE 0075 Pendant la validation des paramètres machine. Dans un set de paramètres d’un axe ou d’une broche analogique, l’alarme de mesure n’est pas active. Cette situation ne devrait être permise que pendant la mise au point ; une fois la mise au point finie, cette surveillance doit être activée. Sur les axes et broches analogiques, activer l'alarme de mesure sur tous les sets (paramètre FBACKAL). 'Limites de logiciel sans activer' DÉTECTION CAUSE 0074 Pendant la validation des paramètres machine. Dans un set de paramètres, la surveillance de l’erreur de poursuite n’est pas active. Cette situation ne devrait être permise que pendant la mise au point ; une fois la mise au point finie, cette surveillance doit être activée. Activer la surveillance de l'erreur de poursuite sur tous les sets de paramètre (paramètre FLWEMONITOR). Au cours du démarrage de la CNC ou la validation des paramètres machine. La CNC a détecté que l’axe esclave d’un couple gantry est stationné ; le signal PARKED de l’axe esclave est actif. Récupérer l'axe ou annuler l'axe gantry. S o l ut i o n s d ’ e r r e ur s . 0080 'Pour valider l'axe, il faut valider la table des PARAMÈTRES GÉNÉRAUX' DÉTECTION CAUSE SOLUTION 0081 'La fenêtre d’arrêt ne peut pas être inférieure à la résolution de l’axe' DÉTECTION CAUSE SOLUTION 0082 SOLUTION SOLUTION SOLUTION SOLUTION SOLUTION Pendant la validation des paramètres machine. Une variable d'asservissement (DRV) est définie pour un axe qui n’est pas numérique (Sercos/Mechatrolink). Éliminer la variable de cet axe. 'Nombre maximum de variables DRV surpassé' DÉTECTION CAUSE SOLUTION 0088 Pendant la validation des paramètres machine. Dans la table de paramètres OEM, des variables d'asservissement (DRV) sont définies et il n’y a pas d’axes numériques (Sercos/Mechatrolink) dans le système. Éliminer les variables de l'asservissement (DRV) définies ou définir les axes numériques adéquats. 'Il n'est pas un axe numérique (Sercos/Mechatrolink)' DÉTECTION CAUSE 0087 Pendant la validation des paramètres machine. Il y a un axe ou une broche sans permission d’échange qui n’est assigné à aucun canal. Les broches ou les axes qui ne sont pas d’échange (paramètre AXISEXCH) doivent être obligatoirement assignés à un canal. 'Il n'existe pas d'axe numérique (Sercos/Mechatrolink)' DÉTECTION CAUSE 0086 Pendant la validation des paramètres machine. Les deux axes d'un couple gantry n'ont pas le même asservissement, Sercos ou Mechatrolink. Les axes d’un couple gantry doivent avoir le même type d'asservissement (paramètre DRIVETYPE). 'Un axe ou une broche non interchangeable ne peut pas rester sans assigner à un canal' DÉTECTION CAUSE 0085 Pendant la validation des paramètres machine. Dans une compensation, l’axe qui se déplace (paramètre MOVAXIS) est rotatif et n’a pas les mêmes limites de module dans tous les sets de paramètres. Affecter les mêmes limites du module (paramètres MODUPLIM et MODLOWLIM) sur tous les sets de paramètres. 'Les axes maître et esclave doivent être du même type (DRIVETYPE DÉTECTION CAUSE 0084 Pendant la validation des paramètres machine. La fenêtre d’arrêt est inférieure à la résolution de l’axe. Augmenter la fenêtre d'arrêt de l'axe (paramètre INPOSW). 'Compensation de la vis ou croisée impossible pour toutes les gammes de l’axe' DÉTECTION CAUSE 0083 Pendant la validation des paramètres machine. L’utilisateur a ajouté un axe au système (paramètre NAXIS) et a essayé de valider la table de paramètres de l’un des nouveaux axes sans valider la table de paramètres généraux. Valider la table de paramètres généraux avant de valider la table de paramètres de l’axe. Pendant la validation des paramètres machine. Dans la table de paramètres OEM, il y a plus de variables d'asservissement (DRV) définies que celles permises. Dans la table de paramètres OEM il peut y avoir 100 variables d'asservissement. 'Enregistrement de variables internes activé' DÉTECTION CAUSE SOLUTION Pendant la validation des paramètres machine. La CNC est en cours d'exécuter un enregistrement d'une variable interne. Contacter Fagor. CNC 8070 (REF: 1901) ·13· S o l ut i o n s d ’ e r r e ur s . 0089 'On démarre avec un seul canal à cause d'erreurs dans les paramètres machine' DÉTECTION CAUSE SOLUTION 0090 'On démarre avec la configuration d’axes par défaut à cause d’erreurs dans les paramètres machine' DÉTECTION CAUSE SOLUTION 0091 SOLUTION SOLUTION SOLUTION CNC 8070 (REF: 1901) ·14· Pendant la validation des paramètres machine. Tous les canaux du système sont définis comme cachés. La CNC ne permet pas que tous les canaux du système soient cachés ; l’un d’eux doit être visible (paramètre HIDDENCH). 'Un axe ne peut pas être MASTERAXIS de plusieurs couples de gantrys' DÉTECTION CAUSE SOLUTION 0096 Pendant la validation des paramètres machine. Dans les paramètres machine OEM, des variables d'asservissement (DRV) ont la même mnémonique et un identificateur Sercos (ID) différent, un type d’accès (synchrone ou asynchrone) ou un mode d’accès (lecture ou écriture) différent. Les variables DRV avec la même mnémonique doivent avoir le même identificateur Sercos (paramètre ID), le même type d’accès (paramètre TYPE) et le même mode d’accès (paramètre MODE). 'Un des canaux doit avoir le paramètre HIDDENCH = Non' DÉTECTION CAUSE SOLUTION 0095 Pendant la validation des paramètres machine. Dans les paramètres machine OEM, il y a des variables d'asservissement (DRV) avec le même identificateur Sercos (ID) et différent type d’accès (synchrone ou asynchrone) ou un mode d’accès (lecture ou écriture) différent. Les variables DRV avec le même identificateur doivent avoir le même type d’accès (paramètre TYPE) et le même mode d’accès (paramètre MODE). 'Variables DRV avec nom identique (MNEMONIC) ne peuvent pas avoir ID, MODE ou TYPE différent' DÉTECTION CAUSE 0094 Pendant la validation des paramètres machine. Dans les paramètres machine OEM, il y a des variables d'asservissement (DRV) avec le même identificateur (ID) et mnémonique différente' Les variables DRV avec le même identificateur doivent avoir la même mnémonique. 'Variables DRV avec identificateur identique (ID) ne peuvent pas avoir MODE ou TYPE différent' DÉTECTION CAUSE 0093 Pendant la validation des paramètres machine. La validation de paramètres machine a détecté des erreurs ou des warnings en rapport avec les axes ou broches d’un canal. Par exemple, le nombre d’axes dans le système est supérieur au nombre d’axes définis dans le paramètre AXISNAME. Du fait qu’il est impossible de démarrer avec la configuration de l’utilisateur, la CNC démarre avec la configuration par défaut. Corriger la configuration de paramètres machine pour supprimer les autres erreurs et warnings. 'Variables DRV avec identificateur identique (ID) il n'est pas possible une mnémonique différente' DÉTECTION CAUSE 0092 Pendant la validation des paramètres machine. La validation de paramètres machine a détecté des erreurs ou des warnings en rapport avec les axes ou broches d’un canal. Par exemple, un canal a un axe associé qui ne se trouve pas dans la liste des axes du système. Du fait qu’il est impossible de démarrer avec la configuration de l’utilisateur, la CNC démarre avec la configuration par défaut. Corriger la configuration de paramètres machine pour supprimer les autres erreurs et warnings. On supprime ce warning sans avoir à changer le paramètre NCHANNEL (nombre de canaux). Pendant la validation des paramètres machine. Il y a deux axes gantry avec le même axe maître. Corriger la configuration d'axes gantry. Un axe tandem doit être Sercos et avec le même OPMODEP que le maître. DÉTECTION CAUSE SOLUTION Pendant la validation des paramètres machine. Les axes d'un axe tandem ne sont pas Sercos vitesse. Les deux axes d'un axe tandem doivent être Sercos vitesse (paramètres DRIVETYPE et OPMODEP). S o l ut i o n s d ’ e r r e ur s . 0097 'Couple tandem\gantry éliminé car il est précédé de couple vide' DÉTECTION CAUSE SOLUTION 0098 'L’axe maître et l’esclave ont différent paramètre AXISEXCH' DÉTECTION CAUSE SOLUTION 0099 SOLUTION SOLUTION SOLUTION Pendant la validation des paramètres machine. L’utilisateur a essayé de valider un tableau de paramètres machine avec un programme pièce en cours d'exécution ou interrompu, ou un mouvement indépendant en cours d'exécution. Patienter jusqu'à la fin du programme ou de la commande indépendante, ou annuler ces derniers. 'Impossible de valider des paramètres : Broche ou axe mouvement ou en cours de synchronisation' DÉTECTION CAUSE SOLUTION 0107 Au cours de l'exécution. La CNC ne termine pas avec succès la lecture ou l’écriture d’une variable externe. Si l'erreur persiste, contacter votre fournisseur. 'Il est impossible de valider des paramètres pendant l'exécution d'un programme' DÉTECTION CAUSE 0106 Pendant la validation des paramètres machine. Le paramétrage a causé un blocage de la validation des paramètres machine. Vérifier les paramètres machine qui ont causé le blocage (s'ils sont connus) ou redémarrer la CNC. 'Time out de communication' DÉTECTION CAUSE SOLUTION 0105 Au cours de l'exécution. Le nombre de variables modifiées dans la CNC et qu’il faut reporter vers l’interface dépasse le maximum permis. Si l'erreur persiste, contacter votre fournisseur. Validation des paramètres machine inachevée (timeout). DÉTECTION CAUSE SOLUTION 0104 Pendant la validation des paramètres machine. L’avance maximum de palpage (paramètre PROBEFEED) est supérieure à l’avance nécessaire pour freiner dans l’espace défini dans PROBERANGE, en respectant les valeurs d’accélération et de jerk de l’axe. La valeur de ce paramètre doit être inférieure à l’avance nécessaire pour freiner dans l’espace défini en PROBERANGE avec les valeurs d’accélération et de jerk de l’axe. La fenêtre du warning informe de l’avance maximum pouvant être atteinte. 'Trop de variables en attente de report' DÉTECTION CAUSE 0103 Pendant la validation des paramètres machine. Il y a un couple gantry ou tandem dont les axes maître et esclave ont le paramètre AXISEXCH avec une valeur différente. Affecter au paramètre AXISEXCH la même valeur des deux axes. 'La valeur du PROBEFEED est trop haute pour freiner en respectant DECEL et JERK' DÉTECTION CAUSE 0100 Pendant la validation des paramètres machine. Les couples d’axes gantry ou tandem n’occupent pas de positions consécutives dans leurs tables ; il y a une place ou une position non définie dans l'une d'elles. Les couples d’axes gantry ou tandem doivent occuper des positions consécutives dans les tables. S’il y a une place dans la table, c’est-à-dire une position non assignée, la CNC annule les couples définis ensuite. Pendant la validation des paramètres machine. L'utilisateur a essayé de valider une table de paramètres machine alors qu'il y a un axe en mouvement. Un axe peut être en déplacement suite à une instruction d’axe indépendante. Arrêter le déplacement de l’axe ou de la broche. CNC 8070 'Erreur en enregistrant les variables DRV' DÉTECTION CAUSE SOLUTION Pendant la validation des paramètres machine. La CNC a généré une erreur en essayant d’enregistrer les variables définies dans la table de paramètres OEM. Contacter Fagor. (REF: 1901) ·15· S o l ut i o n s d ’ e r r e ur s . 0108 'Oscillo: Il n’est pas possible de régler le temps d’échantillonnage avec le nouveau LOOPTIME' DÉTECTION CAUSE SOLUTION 0109 'Il n’est pas possible de valider des paramètres: broche en synchronisation' DÉTECTION CAUSE SOLUTION 0110 SOLUTION SOLUTION SOLUTION SOLUTION 0115 (REF: 1901) Au cours du démarrage de la CNC. Le type de CPU défini dans le code de validation n'est pas valable pour ce hardware. Veuillez contacter Fagor pour obtenir un code de validation approprié. 'Erreur en lisant le tableau technologique' DÉTECTION CAUSE SOLUTION ·16· Pendant la validation des paramètres machine. L'utilisateur a essayé de valider les paramètres pendant la simulation d'un programme. Arrêter la simulation du programme pour valider les paramètres. Code de validation -type de CPU-, NON cohérent avec le hardware. DÉTECTION CAUSE SOLUTION 0116 En activant une cinématique d'utilisateur. Erreur dans la fonction d’initialisation de la cinématique (UserTransforParamInit) implantée dans le fichier Kin_impl.c. Analyser et corriger les éventuelles causes pour lesquelles la fonction affiche une erreur. Impossible de valider des paramètres pendant la simulation d'un programme dans le canal. DÉTECTION CAUSE CNC 8070 En activant une cinématique d'utilisateur. Erreur dans la fonction d’initialisation de la cinématique (UserTransforInit) implantée dans le fichier Kin_impl.c. Analyser et corriger les éventuelles causes pour lesquelles la fonction affiche une erreur. 'Erreur lors de l'initialisation de paramètres de la cinématique d'utilisateur' DÉTECTION CAUSE 0114 Au cours du démarrage de la CNC. Erreur dans la fonction d'initialisation et chargement des données de la cinématique (UserTransforParamInit) implantée dans le fichier Kin_iniData.c. Analyser et corriger les éventuelles causes pour lesquelles la fonction affiche une erreur. 'Erreur lors de l'initialisation de la cinématique d'utilisateur' DÉTECTION CAUSE 0113 Au cours du démarrage de la CNC. La CNC ne trouve pas le fichier \windows\system32\drivers\kinematic.sys. Vérifier qu’en faisant le make de cinématique il ne se produit pas d’erreurs d’utilisateur et que le driver kinematic.sys est généré correctement. 'Erreur lors de l'initialisation de données de la cinématique d'utilisateur' DÉTECTION CAUSE 0112 Pendant la validation des paramètres machine ou la compilation du programme PLC. La CNC n’admet pas ce type d’actions avec des broches synchronisées actives car elles impliquent une RAZ du système. La validation de paramètres ou la compilation du programme PLC doit se faire avant la synchronisation de broches ; il est aussi possible de désynchroniser les broches momentanément pour réaliser l’action souhaitée. 'Il est impossible de charger la cinématique d'utilisateur' DÉTECTION CAUSE SOLUTION 0111 Au cours de l'exécution. L’utilisateur a utilisé l’oscilloscope sans valider un enregistrement, a modifié le paramètre LOOPTIME et validé les paramètres machine. Le warning n’est plus affiché lorsque l’utilisateur exécute un enregistrement dans l’oscilloscope. Le réglage du temps d’échantillonnage d’un enregistrement de l’oscilloscope dépend du paramètre LOOPTIME. Pour que la CNC puisse réaliser ce réglage elle doit avoir un enregistrement de l’oscilloscope validé, c’est-à-dire que l'enregistrement ait été exécuté au moins une fois. Pendant l'activation d'un tableau technologique. Le fichier du tableau technologique n'existe pas ou le tableau a été modifié (de nouvelles variables ont été insérées, des types énumérés ont été modifiés ou la CNC n'a pas été réinitialisée). Vérifier le nom du tableau. Si le tableau existe, réinitialiser la CNC. S o l ut i o n s d ’ e r r e ur s . 0117 Le nombre de cores défini dans le code de validation N'EST PAS cohérent avec le hardware. DÉTECTION CAUSE SOLUTION 0118 Il n'y a pas de hardware de SERCOS III ou d'erreur dans la charge du driver. DÉTECTION CAUSE SOLUTION 0119 SOLUTION SOLUTION Pendant l'exécution d'un programme pièce avec les sous-routines globales. Le nombre de fichiers ouverts (programme principal plus sous-routines externes) est supérieur à 20. Réduire le nombre de sous-routines externes ouvertes simultanément dans le programme pièce. #WRITE : texte ou fichier cncWrite.txt non trouvé. DÉTECTION CAUSE SOLUTION 0151 Pendant l'exécution. Le handle du fichier indiqué dans l'instruction #OPEN est utilisé par l'instruction #OPEN d'un autre fichier. Utiliser un handle de fichier différent. 'Trop de fichiers ouverts' DÉTECTION CAUSE 0151 Au cours du démarrage de la CNC. La CNC n'a pas pu mettre à jour le logiciel des dispositifs connectés au bus Sercos III. La CNC informe que la mise à jour a échoué, aucune action n'est nécessaire. Le dispositif fonctionne avec la version logicielle antérieure. #OPEN : handle du fichier utilisé. DÉTECTION CAUSE 0150 Au cours du démarrage de la CNC. La CNC n'a pas pu mettre à jour le logiciel des dispositifs connectés au bus Sercos III. La CNC informe que la mise à jour a échoué, aucune action n'est nécessaire. Le dispositif fonctionne avec la version logicielle antérieure. Erreur dans l'actualisation de SW des dispositifs raccordés à SERCOS3 - Cheksum error. DÉTECTION CAUSE SOLUTION 0150 Au cours du démarrage de la CNC. La CNC n'a pas pu mettre à jour le logiciel des dispositifs connectés au bus Sercos III. La CNC informe que la mise à jour a échoué, aucune action n'est nécessaire. Le dispositif fonctionne avec la version logicielle antérieure. Erreur dans l'actualisation de SW des dispositifs raccordés à SERCOS3 - S3 connect FAILED. DÉTECTION CAUSE SOLUTION 0123 Au cours du démarrage de la CNC. La CNC a mis à jour le logiciel des PwC. La CNC informe de la mise à jour, aucune action n’est nécessaire. Erreur dans l'actualisation de SW des dispositifs raccordés à SERCOS3 - FAILED. DÉTECTION CAUSE SOLUTION 0121 Au cours du démarrage de la CNC. La CNC ne détecte pas le hardware associé à Sercos III ou ne peut pas charge le pilote. Redémarrez l'équipement. Si l'erreur persiste, contacter Fagor. Actualisation correcte de SW des dispositifs PwC raccordés à SERCOS3 - OK. DÉTECTION CAUSE SOLUTION 0120 Au cours du démarrage de la CNC. Le nombre de cores défini dans le code de validation n'est pas approprié pour ce hardware. Veuillez contacter Fagor pour obtenir un code de validation approprié. Pendant l'exécution. Le texte correspondant à l'identificateur programmé est introuvable. Il est possible que le fichier cncWrite.txt n'existe pas ou que l'identificateur ne soit pas défini. Vérifier que le fichier cncWrite.txt existe et qu'il contient l'identificateur. CNC 8070 'Accès d'écriture refusé' DÉTECTION CAUSE SOLUTION En accédant à un fichier. La CNC a essayé d’écrire dans un fichier qui n’a pas de permission d’écriture. Donner au fichier permission d'écriture. (REF: 1901) ·17· S o l ut i o n s d ’ e r r e ur s . 0152 'Il est impossible d'ouvrir le fichier' DÉTECTION CAUSE SOLUTION 0153 'Accès de lecture refusé' DÉTECTION CAUSE SOLUTION 0154 SOLUTION CNC 8070 ·18· Pendant l'exécution. Un canal a essayé d'ouvrir un fichier ouvert par un autre canal. Les possibles solutions sont les suivantes: • Fermer le fichier (#CLOSE). • Il n'est pas nécessaire d'ouvrir le même canal dans tous les canaux. Un canal peut écrire dans un fichier ouvert par un autre canal, si l'identificateur du fichier est connu (F1 à F4). 'Axe/Set non disponible dans le système' DÉTECTION CAUSE SOLUTION (REF: 1901) Pendant l'exécution. La CNC a essayé d'écrire (#WRITE) dans un fichier qui n'est pas ouvert. La CNC doit ouvrir un fichier (#OPEN) pour pouvoir écrire dans ce dernier (#WRITE). #OPEN: Fichier déjà ouvert par un autre canal. DÉTECTION CAUSE SOLUTION 0160 Pendant l’édition et l’exécution. L’identificateur du clavier n’est pas correct. Vérifier dans le manuel de programmation la syntaxe de l'instruction. Les identificateurs valables sont F1 à F4, et leur programmation es facultative. L'identificateur du fichier permet à un canal d'écrire dans un fichier ouvert dans un autre canal. #WRITE exige une instruction #OPEN préalable. DÉTECTION CAUSE SOLUTION 0159 Pendant l'exécution. L'instruction #OPEN a essayé d'ouvrir trop de fichiers. Fermer un fichier. #OPEN/#CLOSE: Handle de fichier non valable. DÉTECTION CAUSE SOLUTION 0158 Au cours de l’accès à un fichier. La CNC a essayé de lire un fichier dont la taille dépasse l’espace libre de la zone de mémoire, assignée pour le chargement rapide de fichiers. Exécuter depuis la mémoire RAM (sous-routines avec extension fst) uniquement les fichiers qui sont appelés le plus fréquemment. Trop de fichiers ouverts pour l'écriture. DÉTECTION CAUSE SOLUTION 0157 Au cours de l’accès à un fichier. La CNC a essayé de lire un fichier crypté, sans avoir permission d’accès. Contactez le fabricant de la machine pour obtenir les codes du cryptage du fichier. 'Il n'est pas possible d'effectuer le chargement rapide de fichier' DÉTECTION CAUSE 0156 En accédant à un fichier. La CNC a essayé de lire dans un fichier qui n’a pas de permission de lecture. Donner au fichier permission de lecture. 'Programme ou routine protégée' DÉTECTION CAUSE SOLUTION 0155 En accédant à un fichier. La CNC n'a pas pu ouvrir un fichier pour sa lecture ou écriture. Le fichier n’a pas les permissions adéquates, il n’est pas accessible ou est corrompu. Vérifier que le fichier existe et qu'il a les permissions adéquates pour l’action à réaliser (lecture/écriture). Si le fichier est corrompu, ses données ont été perdues. Au cours de l'exécution. Les possibles causes sont les suivantes: • Les instructions #SET AX ou #CALL AX sont en train d’essayer d’ajouter au canal un axe inexistant ou se trouvant dans un autre canal. • Un set de paramètres inexistant est programmé dans la fonction G112. Réviser la programmation. Si l’axe est dans un autre canal, le libérer avec l'instruction #FREE AX. S o l ut i o n s d ’ e r r e ur s . 0161 #OPEN: Mode APPEND non autorisé sur un fichier non Unicode. DÉTECTION CAUSE SOLUTION 0165 'RT IT Overflow' DÉTECTION CAUSE SOLUTION 0166 SOLUTION Au cours du fonctionnement de la CNC. L’intégrité de l'équipement est en risque. La CNC réalise toutes les minutes un contrôle de la température ambiante de l'équipement; si après trois échantillons consécutifs la température dépasse 60ºC (140ºF), la CNC affiche l'avis et active la marque OVERTEMP. La cause de l’augmentation de température peut être une défaillance dans le système de réfrigération du hardware ou une température ambiante très élevée. Le warning affiche la température actuelle. Respecter les dimensions recommandées pour l’habitacle et la distance minimale recommandée entre les parois de l’habitacle et l’unité centrale. Au besoin, installer des ventilateurs pour aérer l’habitacle. Si l’erreur persiste, mettre la CNC hors tension et veuillez contacter le service d'assistance technique. 'Tension de pile basse' DÉTECTION CAUSE SOLUTION 0171 Au cours du fonctionnement de la CNC. Le temps de la boucle de position des axes Sercos dépasse le temps permis. Régler le paramètre LOOPTIME. La température de sécurité est dépassée. L’intégrité de l'équipement est en danger. Contacter le SAT. DÉTECTION CAUSE 0170 Au cours du fonctionnement de la CNC. L’interruption de temps réel ne rentre pas. Réinitialiser la CNC. Si l'erreur persiste, contacter votre fournisseur. Position Loop Overflow. DÉTECTION CAUSE SOLUTION 0169 Au cours de l’exécution d’un programme pièce. L’axe est en train de dépasser sa limite de jerk permise. Analyser les cas où cela se produit et contacter le fabricant de la machine. 'Non RT IT' DÉTECTION CAUSE SOLUTION 0168 Au cours du fonctionnement de la CNC. Les interruptions du temps réel dépassent le temps permis. La cause pourra être éventuellement l’installation d’un dispositif, d'un driver ou d’une application incompatible avec la CNC. Si l’erreur se répète fréquemment, il peut être nécessaire de régler le paramètre LOOPTIME. Analysez les cas où l’erreur apparaît et contactez votre fournisseur. 'Limite de jerk surpassée' DÉTECTION CAUSE SOLUTION 0167 Pendant l'exécution. Un canal a essayé d'ouvrir un fichier non-Unicode avec un mode d'accès « APPEND ». Le mode d'accès « APPEND » permet d'ouvrir uniquement des fichiers Unicode. Le mode d'accès « DELETE » peut ouvrir des fichiers non-Unicode, mais effacer le contenu. Au cours de démarrage de la CNC ou après une RAZ. La CNC vérifie la tension de la pile dans le processus de démarrage et à chaque RAZ. La pile est déchargée ; son cycle de vie utile est terminé. Contacter le fabricant de la machine pour changer la pile. Lorsque la CNC est hors tension, la pile est chargée de maintenir les données nécessaires pour la CNC (les cotes, par exemple). 'Dépassement du LOOPTIME' DÉTECTION CAUSE SOLUTION En conditions de CNCREADY. Les interruptions du temps réel dépassent le temps permis. Si l’erreur se répète fréquemment, il peut être nécessaire de régler le paramètre LOOPTIME. Analyser les cas où cela se produit et contacter le fabricant de la machine. CNC 8070 (REF: 1901) ·19· S o l ut i o n s d ’ e r r e ur s . 0172 Le ventilateur de la cpu est arrêté. Risque de température excessive. Contacter le SAT. DÉTECTION CAUSE SOLUTION 0173 Marche interdite car la température de sécurité est dépassée. Éteindre la CNC et contacter le SAT. DÉTECTION CAUSE SOLUTION 0200 SOLUTION (REF: 1901) ·20· Pendant l'exécution. Le PLC a essayé d'activer une compensation volumétrique qui n'existe pas. Vérifier la liste des compensations volumétriques définies (paramètre VOLCOMP n). Variable inexistante sans un matériel actif. DÉTECTION CAUSE SOLUTION CNC 8070 Pendant l'exécution. La variable V.G.DYNOVR a une valeur hors des limites fixées par les paramètres MINDYNOVR et MAXDYNOVR. Définir la variable avec une valeur appropriée ou modifier la dynamique à l'aide de la barre-override ([CTRL][H]). Compensation volumétrique inexistante. DÉTECTION CAUSE SOLUTION 0252 En lisant l'état de la batterie. Il y a une coupure d’alimentation de la CNC et la batterie de secours alimente la CNC. Que la coupure soit fortuite ou provoquée par l’utilisateur, laisser la CNC terminer la séquence automatique de mise hors tension. Si la coupure d’alimentation a été fortuite, vérifier les possibles causes. DYNOVR hors de la plage autorisée par MINDYNOVR et MAXDYNOVR. DÉTECTION CAUSE 0251 En lisant l'état de la batterie. La CNC ne peut pas se raccorder avec VcompciD. Contacter votre fournisseur. 'Coupure du réseau. PC alimenté par batterie' DÉTECTION CAUSE SOLUTION 0250 Au cours du fonctionnement de la CNC. Chaque fois que l'on tape sur [START], la CNC vérifie que la température ambiance ne dépasse pas 65ºC (149ºF) et en cas de dépasser cette valeur, invalide [START] et affiche une erreur. La cause de l’augmentation de température peut être une défaillance dans le système de réfrigération du hardware ou une température ambiante très élevée. L'erreur affiche la température actuelle. Respecter les dimensions recommandées pour l’habitacle et la distance minimale recommandée entre les parois de l’habitacle et l’unité centrale. Au besoin, installer des ventilateurs pour aérer l’habitacle. Si l’erreur persiste, mettre la CNC hors tension et veuillez contacter le service d'assistance technique. 'Défaut à la demande d’un VxD' DÉTECTION CAUSE SOLUTION 0201 Au cours du fonctionnement de la CNC. Risque de surtempérature de l'équipement. La CNC a détecté que le ventilateur de la CPU est arrêté. Lorsque la CPU dispose de ventilateur, au cours du régime du fonctionnement de la CNC, celle-ci surveille le fonctionnement du ventilateur. Ce testage sera effectué toutes les minutes, de même que la surveillance de la température. Si l’erreur persiste, veuillez contacter le service après-vente. Pendant l'exécution. Une tentative de lecture du nom du matériel actif a été faite et aucun n'a été trouvé. Activer un matériel depuis les tableaux technologiques. S o l ut i o n s d ’ e r r e ur s . 1000-1999 1000 'La fonction ou instruction requiert la programmation des axes' DÉTECTION CAUSE SOLUTION 1004 'Vitesse de broche nulle' DÉTECTION CAUSE SOLUTION 1005 SOLUTION SOLUTION SOLUTION Au cours de l'exécution. Dans le même bloc, la fonction G4 a programmé deux fois le temps d’attente, directement avec un numéro et le paramètre K. Programmer une seule fois le temps d’attente de la fonction G4. 'Programmer G4 K' DÉTECTION CAUSE SOLUTION 1011 Au cours de l'exécution. Les possibles causes sont les suivantes: • La cote programmée pour l'axe est trop grande. • La fonction G101 essaie d'inclure sur un axe un offset trop grand. Réviser la programmation. 'G4: le temps d'attente a été programmé en double, directement et avec K' DÉTECTION CAUSE 1010 Au cours de l'exécution. La fonction programmée a besoin d'un ou de deux axes principaux mais ceux-ci n’existent pas dans le canal. Réviser la programmation. Les fonctions G11, G12, G13 et G14 ont besoin des deux axes du plan principal. Les fonctions G2, G3, G8, G9, G30, G36, G37, G38, G39, G73 ont besoin des deux axes du plan principal. Il manque aussi les deux axes du plan principal pour activer la détection de collisions (#CD) et pour la fonction G20 lorsque la détection de collisions est active. 'Coordonnées hors de rang' DÉTECTION CAUSE 1009 Au cours de l'exécution. La fonction G20 n'admet pas la programmation de broche. Réviser la programmation. 'La fonction programmée requiert un axe principal non existant' DÉTECTION CAUSE 1008 Au cours de l'exécution. Il n'y a pas d'avance active dans le canal. Programmer l'avance F. 'G20: broche non admise' DÉTECTION CAUSE SOLUTION 1007 Au cours de l'exécution. La broche utilisée avec la fonction G63 a une vitesse zéro. Programmer une vitesse de broche. 'Bloc de déplacement avec avance nulle' DÉTECTION CAUSE SOLUTION 1006 Au cours de l'exécution. Il faut programmer les axes sur lesquels doit agir l'instruction ou la fonction G programmée. Réviser la programmation. Au cours de l'exécution. Dans la fonction G4 le temps d'attente n'est pas programmé. Programmer la fonction G4 comme G4 <time> ou G4 K<time>, où le paramètre <time> est le temps d'attente, en secondes. Dans les deux cas, le temps d'attente sera programmé après la fonction G4. CNC 8070 (REF: 1901) 'G4: temps d'attente hors de rang' DÉTECTION CAUSE SOLUTION Au cours de l'exécution. Le temps d’attente programmé dans la fonction G4 est trop long. La valeur maximale admissible pour le temps d'attente est 2147483646. ·21· S o l ut i o n s d ’ e r r e ur s . 1012 'G4: le temps d'attente ne peut pas être programmé avec K' DÉTECTION CAUSE SOLUTION 1013 'G4: le temps d'attente ne peut pas être négatif' DÉTECTION CAUSE SOLUTION 1014 SOLUTION SOLUTION SOLUTION SOLUTION 1021 ·22· Au cours de l'exécution. Le temps de rampe de la fonction G132 est négatif. Programmer une valeur supérieure ou égale à zéro. 'Temps de rampe hors de rang' DÉTECTION CAUSE SOLUTION 1022 (REF: 1901) Au cours de l'exécution. La fonction G101 essaie d’inclure l’offset de mesure sur un axe qui n’est pas intervenu dans la mesure ou l’offset a été annulé (G102). Pour inclure un offset de mesure (G101), l’axe doit avoir effectué une mesure. 'Temps de rampe négatif' DÉTECTION CAUSE SOLUTION CNC 8070 Au cours de l'exécution. La limite positive de logiciel a une valeur trop haute. Réviser la programmation. 'Pas de mesure réalisée sur l'axe(s) sollicité(s)' DÉTECTION CAUSE 1020 Au cours de l'exécution. La limite négative de logiciel a une valeur trop haute. Réviser la programmation. 'G199: limite de logiciel positive hors de rang' DÉTECTION CAUSE SOLUTION 1019 Au cours de l'exécution. Il n’est pas possible de programmer des cotes négatives en coordonnées absolues (G90) et la programmation en diamètres active (paramètre DIAMPROG). La programmation en coordonnées absolues et en diamètres n’admet pas de cotes négatives. 'G198: limite de logiciel négative hors de rang' DÉTECTION CAUSE SOLUTION 1018 Au cours de l'exécution. Une des valeurs I, J, K est trop élevée comme le centre d’une interpolation circulaire ou le centre d’une rotation du système de coordonnées. Programmer une valeur inférieure. 'Les valeurs négatives ne sont pas admises dans la programmation d'un axe en diamètres' DÉTECTION CAUSE 1017 Au cours de l'exécution. L’axe frontal (paramètre FACEAXIS) ne peut avoir actives simultanément l’image miroir et la programmation en diamètres. Réviser la programmation. 'Coordonnées du centre hors de rang' DÉTECTION CAUSE 1016 Au cours de l'exécution. Le temps d’attente dans la fonction G4 est négatif. Programmer une valeur supérieure ou égale à zéro. 'La programmation en diamètres n'est pas admise avec image miroir sur l'axe frontal' DÉTECTION CAUSE 1015 Au cours de l'exécution. La lettre K est associée au troisième axe du canal et dans ce cas il n’existe pas de troisième axe. Si on ne veut pas avoir de troisième axe dans le canal, on peut programmer le temps d’attente directement avec un numéro. Au cours de l'exécution. Le temps de rampe de la fonction G132 est trop haut. Réviser la programmation. 'Pourcentage de Feed-Forward hors de rang' DÉTECTION CAUSE SOLUTION Au cours de l'exécution. Le pourcentage de feed forward (G134) ou AC forward (G135) est trop haut. Le pourcentage de feed forward ou AC forward doit être supérieur à zéro et inférieur à 120. S o l ut i o n s d ’ e r r e ur s . 1023 'Numéro de gamme non valable' DÉTECTION CAUSE SOLUTION 1024 'Numéro de gamme hors de rang' DÉTECTION CAUSE .SOLUTION 1025 SOLUTION SOLUTION SOLUTION Au cours de l'exécution. Dans le même bloc que la fonction G01, l'instruction #AXIS n'est pas programmée. Réviser la programmation. 'La broche pour M19 n'a pas de position' DÉTECTION CAUSE SOLUTION 1035 Au cours de l'exécution. Dans le même bloc que l'instruction #AXIS il reste à programmer G200, G201 ou G202. Réviser la programmation. 'On attend #AXIS' DÉTECTION CAUSE SOLUTION 1032 Au cours de l'exécution. Les possibles causes sont les suivantes: • Rayon nul sur une l'interpolation circulaire. • Avec la fonction G265 active, la CNC calcule un rayon nul à partir des coordonnées du centre programmées dans l’interpolation circulaire. • Avec la fonction G264 active, les deux coordonnées du centre sont zéro. Le rayon d'une l'interpolation circulaire ne peut pas être nul. Les deux coordonnées du centre d’une interpolation circulaire ne peuvent pas être nulles. '#AXIS programmé sans G200/202/202' DÉTECTION CAUSE 1031 Au cours de l'exécution. Dans une interpolation circulaire avec la fonction G265 active, la différence entre rayon initial et final dépasse les paramètres machine CIRINERR et CIRINFACT. Réviser la programmation. 'Rayon nul pour trajectoire circulaire' DÉTECTION CAUSE 1030 Au cours de l'exécution. Rayon nul pour l’interpolation circulaire ; les solutions sont infinies. Réviser la programmation. 'Différence trop grande entre le centre programmé et celui calculé' DÉTECTION CAUSE 1029 Au cours de l'exécution. Rayon trop petit pour l'interpolation circulaire. Réviser la programmation. 'Point initial et fin de trajectoire circulaire identiques (solutions infinies)' DÉTECTION CAUSE SOLUTION 1028 Au cours de l'exécution. Déplacement nul sur le bloc de G63. Réviser la programmation. 'Trajectoire circulaire incorrecte avec le rayon programmé' DÉTECTION CAUSE SOLUTION 1027 Au cours de l'exécution. Le numéro de gamme (set) de l'axe est trop haut. La gamme (set) programmée pour l’axe doit être supérieure à zéro et inférieure ou égale au paramètre machine NPARSETS de l’axe. 'Distance programmée égale à zéro' DÉTECTION CAUSE SOLUTION 1026 Au cours de l'exécution. Le numéro de gamme (set) de l'axe est incorrect. La gamme (set) programmée pour l’axe doit être supérieure à zéro et inférieure ou égale au paramètre machine NPARSETS de l’axe. Au cours de l'exécution. Dans le même bloc que la fonction M19, la position de la broche n'est pas programmée. Réviser la programmation. CNC 8070 (REF: 1901) '#SLOPE: paramètre hors de rang' DÉTECTION CAUSE SOLUTION Au cours de l'exécution. Dans l'instruction #SLOPE un paramètre a une valeur trop haute. Programmer valeurs inférieures. ·23· S o l ut i o n s d ’ e r r e ur s . 1037 'Coordonnées du centre ignorées avec G0/G1/G100/G63 actives' DÉTECTION CAUSE SOLUTION 1038 'La compensation de rayon ne peut pas être active pendant la mesure' DÉTECTION CAUSE SOLUTION 1039 SOLUTION SOLUTION SOLUTION SOLUTION SOLUTION SOLUTION 1046 Au cours de l'exécution. Dans la fonction G20 (changement de plan), le premier axe du plan (paramètre 1) est incorrect. Le premier axe du plan doit être l’un des trois premiers axes du canal. 'Erreur de programmation du second axe du plan' DÉTECTION CAUSE (REF: 1901) SOLUTION ·24· Au cours de l'exécution. Dans la fonction G20 (changement de plan), le premier axe du plan (paramètre 1) et le second (paramètre 2) sont le même axe. Réviser la programmation. 'Erreur de programmation du premier axe du plan' DÉTECTION CAUSE CNC 8070 Au cours de l'exécution. Dans la fonction G20 (changement de plan), le paramètre 5 coïncide avec le paramètre 1 ou 2. Si l’axe longitudinal de l’outil (paramètre 3) coïncide avec le premier ou le deuxième axe du plan (paramètres 1 et 2), il faut programmer le troisième axe avec le paramètre 5. Ce paramètre ne devra pas coïncider avec le premier ni le deuxième axe. 'Le premier et le deuxième axe du plan ne peuvent pas coïncider' DÉTECTION CAUSE 1045 Au cours de l'exécution. Dans une interpolation circulaire programmée bien avec le rayon et les coordonnées du point final ou bien avec les coordonnées du point moyen, du point final et avec la fonction G265 active. Les coordonnées du centre de l’interpolation calculées par la CNC sont trop grandes. Les coordonnées programmées pour le centre, le point moyen ou le rayon sont trop grands. Réviser la programmation. 'Le troisième axe du plan ne peut pas coïncider avec le premier ou le deuxième' DÉTECTION CAUSE 1044 Au cours de l'exécution. La CNC ne peut réaliser la recherche de référence d’un axe qui est en mode manuel additif (G201). Annuler le mode manuel additif de l’axe avec la fonction G202 pour réaliser la recherche de référence machine. Après la recherche de référence, activer de nouveau le mode manuel additif (G201). 'Centre de la trajectoire circulaire corrigé hors de rang' DÉTECTION CAUSE 1043 Au cours de l'exécution. La CNC essaie de réaliser une mesure (G100) sur un axe qui a un offset de mesure antérieur. Utiliser la fonction G102 pour annuler l'offset de mesure compris dans l'axe. 'Recherche de zéro impossible pour un axe actif en G201' DÉTECTION CAUSE 1041 Au cours de l'exécution. La CNC essaie d'exécuter la fonction G100 avec la compensation de rayon active (G41/G42). Réviser la programmation. 'Il existe déjà une valeur de mesure pour l'axe(s)' DÉTECTION CAUSE 1040 Au cours de l'exécution. La CNC a trouvé les paramètres I, J, K avec la fonction G0, G1, G100 ou G63 active. La CNC ignore ces paramètres. Ces fonctions n’ont pas besoin de ces paramètres. Au cours de l'exécution. Dans la fonction G20 (changement de plan), le second axe du plan (paramètre 2) est incorrect. Le second axe du plan doit être l’un des trois premiers axes du canal. S o l ut i o n s d ’ e r r e ur s . 1047 'Il faut un troisième axe pour le plan (indice 5)' DÉTECTION CAUSE SOLUTION 1048 'Compensation de longueur d'outil avec rayon hors de rang' DÉTECTION CAUSE SOLUTION 1049 SOLUTION SOLUTION SOLUTION Au cours de l'exécution. La CNC ne permet pas de modifier le rayon de l’outil (variable (V.)G.TOR) ni de programmer un changement d’outil et/ou de correcteur dans le même bloc. Programmer les deux instructions dans des blocs différents. 'Trop de variables externes' DÉTECTION CAUSE SOLUTION 1057 Au cours de l'exécution. Le numéro de mors programmé n'existe pas. Le numéro de mors doit être une valeur entre zéro et dix. 'D et le rayon de l'outil ne peuvent pas être modifiés dans le même bloc' DÉTECTION CAUSE 1056 Au cours de l'exécution. La CNC a réalisé une mesure avec la fonction G100 et la cote ou l’offset obtenu est trop grand. La valeur obtenue dans le palpage doit être entre -2147483647 et 2147483646. 'Mors inexistant' DÉTECTION CAUSE SOLUTION 1055 Au cours de l'exécution. Les possibles causes sont les suivantes: • La CNC a essayé d'exécuter un déplacement indépendant dans une broche. • L'axe programmé dans une variable n'est pas disponible. Réviser la programmation. Pour pouvoir interpoler la broche comme axe indépendant, celui-ci doit être actif comme axe C. 'Valeurs du résultat de la mesure hors de rang' DÉTECTION CAUSE 1054 Au cours de l'exécution. Les dimensions de l'outil excèdent les valeurs minimums. Modifier les dimensions de l'outil. 'Axe inexistant ou non disponible dans le canal' DÉTECTION CAUSE 1052 Au cours de l'exécution. Les deux axes du plan principal sont des axes frontaux (paramètre FACEAXIS). Dans le plan du travail il ne peut y avoir qu'un axe frontal. 'Le rang de données est excédé lorsque les offsets d'outils sont considérés' DÉTECTION CAUSE SOLUTION 1051 Au cours de l'exécution. Les dimensions de l'outil excèdent les valeurs minimums. Modifier les dimensions de l'outil. 'Axe frontal (FACEAXIS) défini deux fois dans le plan actif' DÉTECTION CAUSE SOLUTION 1050 Au cours de l'exécution. Dans la fonction G20 (changement de plan), il manque le troisième axe ou bien il est incorrect. Si l’axe longitudinal de l’outil (paramètre 3) coïncide avec le premier ou le deuxième axe du plan (paramètres 1 et 2), il faut programmer le troisième axe avec le paramètre 5. Le paramètre ne devra pas coïncider ni le premier ni avec le deuxième axe et devra être l’un des trois premiers axes du canal. Au cours de l'exécution. La CNC a atteint le nombre de variables externes admissibles. Réviser la programmation. La CNC admet 500 variables externes. 'Variable sans permission de lecture' DÉTECTION CAUSE SOLUTION Au cours de l'exécution. La CNC a essayé de lire depuis le programme pièce ou MDI une variable qui n’a pas de permission de lecture par programme. Il n'est pas possible de lire la variable depuis le programme pièce ou MDI. Consulter dans la documentation les permis de la variable. CNC 8070 (REF: 1901) ·25· S o l ut i o n s d ’ e r r e ur s . 1058 'Variable d’utilisateur non initialisée' DÉTECTION CAUSE SOLUTION 1059 'Variable sans autorisation d'écriture' DÉTECTION CAUSE SOLUTION 1060 1068 (REF: 1901) ·26· Au cours de l'exécution. Dans un bloc il y a deux fonctions G ou plus programmées incompatibles entre elles. Programmer les fonctions dans des blocs différents. 'Fonctions G incompatibles (G151/G152)' DÉTECTION CAUSE SOLUTION 1069 Au cours de l'exécution. Dans un bloc il y a deux fonctions G ou plus programmées incompatibles entre elles. Programmer les fonctions dans des blocs différents. 'Fonctions G incompatibles (G40/G41/G42)' DÉTECTION CAUSE SOLUTION CNC 8070 Au cours de l'exécution. Dans un bloc il y a deux fonctions G ou plus programmées incompatibles entre elles. Programmer les fonctions dans des blocs différents. 'Fonctions G incompatibles (G136/G137)' DÉTECTION CAUSE SOLUTION 1067 Au cours de l'exécution. Dans un bloc il y a deux fonctions G ou plus programmées incompatibles entre elles. Programmer les fonctions dans des blocs différents. 'Fonctions G incompatibles (G17/G18/G19/G20)' DÉTECTION CAUSE SOLUTION 1066 Au cours de l'exécution. Dans un bloc il y a deux fonctions G ou plus programmées incompatibles entre elles. Programmer les fonctions dans des blocs différents. 'Fonctions G incompatibles (G196/G197)' DÉTECTION CAUSE SOLUTION 1065 Au cours de l'exécution. Dans le bloc il y a des fonctions G programmées contraires entre elles. Programmer les fonctions dans des blocs différents. 'Fonctions G incompatibles (G108/G109/G193)' DÉTECTION CAUSE SOLUTION 1064 Au cours de l'exécution. La fonction G programmée n'existe pas. Réviser la programmation. 'Fonctions G incompatibles' DÉTECTION CAUSE SOLUTION 1063 Au cours de l'exécution. Le numéro de bloc "N" n'est pas valable. Le numéro de bloc doit être une valeur positive ou inférieure à 2147483646. 'Fonction G inexistante' DÉTECTION CAUSE SOLUTION 1062 Au cours de l'exécution. La CNC a essayé d’écrire depuis le programme pièce ou MDI une variable qui n’a pas de permission d’écriture par programme. Il n'est pas possible d'écrire la variable depuis le programme pièce ou MDI. Consulter dans la documentation les permis de la variable. 'Valeur d'étiquette N hors de rang' DÉTECTION CAUSE SOLUTION 1061 Au cours de l'exécution. La variable d’utilisateur V.P.name ou V.S.name n’a pas été définie. Réviser la programmation. Définir adéquatement la variable. Au cours de l'exécution. Dans un bloc il y a deux fonctions G ou plus programmées incompatibles entre elles. Programmer les fonctions dans des blocs différents. 'Fonctions G incompatibles (G54-G59/G159)' DÉTECTION CAUSE SOLUTION Au cours de l'exécution. Dans un bloc il y a deux fonctions G ou plus programmées incompatibles entre elles. Programmer les fonctions dans des blocs différents. S o l ut i o n s d ’ e r r e ur s . 1070 'Fonctions G incompatibles (G5/G7/G50/G60/G61)' DÉTECTION CAUSE SOLUTION 1071 'Fonctions G incompatibles (G70/G71)' DÉTECTION CAUSE SOLUTION 1072 Au cours de l'exécution. Dans un bloc il y a deux fonctions G ou plus programmées incompatibles entre elles. Programmer les fonctions dans des blocs différents. 'Fonctions G incompatibles (G6/G261/G262)' DÉTECTION CAUSE SOLUTION 1081 Au cours de l'exécution. Dans un bloc il y a deux fonctions G ou plus programmées incompatibles entre elles. Programmer les fonctions dans des blocs différents. 'Fonctions G incompatibles (G138/G139)' DÉTECTION CAUSE SOLUTION 1080 Au cours de l'exécution. Dans un bloc il y a deux fonctions G ou plus programmées incompatibles entre elles. Programmer les fonctions dans des blocs différents. 'Fonctions G incompatibles (G134/G135)' DÉTECTION CAUSE SOLUTION 1079 Au cours de l'exécution. Dans un bloc il y a deux fonctions G ou plus programmées incompatibles entre elles. Programmer les fonctions dans des blocs différents. 'Fonctions G incompatibles (G115/G116/G117)' DÉTECTION CAUSE SOLUTION 1078 Au cours de l'exécution. Dans un bloc il y a deux fonctions G ou plus programmées incompatibles entre elles. Programmer les fonctions dans des blocs différents. 'Fonctions G incompatibles (G100/G101/G102)' DÉTECTION CAUSE SOLUTION 1077 Au cours de l'exécution. Dans un bloc il y a deux fonctions G ou plus programmées incompatibles entre elles. Programmer les fonctions dans des blocs différents. 'Fonctions G incompatibles (G96/G97/G192)' DÉTECTION CAUSE SOLUTION 1076 Au cours de l'exécution. Dans un bloc il y a deux fonctions G ou plus programmées incompatibles entre elles. Programmer les fonctions dans des blocs différents. 'Fonctions G incompatibles (G93/G94/G95)' DÉTECTION CAUSE SOLUTION 1075 Au cours de l'exécution. Dans un bloc il y a deux fonctions G ou plus programmées incompatibles entre elles. Programmer les fonctions dans des blocs différents. 'Fonctions G incompatibles (G90/G91)' DÉTECTION CAUSE SOLUTION 1074 Au cours de l'exécution. Dans un bloc il y a deux fonctions G ou plus programmées incompatibles entre elles. Programmer les fonctions dans des blocs différents. 'Fonctions G incompatibles (G80-G88/G160-G166/G281-G286/G287-G297)' DÉTECTION CAUSE SOLUTION 1073 Au cours de l'exécution. Dans un bloc il y a deux fonctions G ou plus programmées incompatibles entre elles. Programmer les fonctions dans des blocs différents. Au cours de l'exécution. Dans un bloc il y a deux fonctions G ou plus programmées incompatibles entre elles. Programmer les fonctions dans des blocs différents. CNC 8070 'Fonctions G incompatibles (G264/G265)' DÉTECTION CAUSE SOLUTION Au cours de l'exécution. Dans un bloc il y a deux fonctions G ou plus programmées incompatibles entre elles. Programmer les fonctions dans des blocs différents. (REF: 1901) ·27· S o l ut i o n s d ’ e r r e ur s . 1082 'Fonctions G incompatibles (G200/G201/G202)' DÉTECTION CAUSE SOLUTION 1083 'Fonctions G incompatibles (G36/G37/G38/G39)' DÉTECTION CAUSE SOLUTION 1084 SOLUTION SOLUTION SOLUTION CNC 8070 (REF: 1901) ·28· Au cours de l'exécution. Il y a plus d'une fonction T dans le même bloc. Il ne peut y avoir qu'une seule fonction T dans chaque bloc. Programmer les deux fonctions dans des blocs différents. 'Fonction D programmée en double' DÉTECTION CAUSE SOLUTION 1094 Au cours de l'exécution. La fonction H n'existe pas. Le numéro de la fonction doit être entre 1 et 65534. 'Fonction T programmée en double' DÉTECTION CAUSE SOLUTION 1093 Au cours de l'exécution. Deux fonctions M ou plus incompatibles entre elles sont programmées dans un bloc pour la même broche. Programmer les fonctions M dans la même broche dur des blocs différents. 'Fonction H inexistante' DÉTECTION CAUSE SOLUTION 1091 Au cours de l'exécution. Dans la fonction G159, le décalage d'origine programmé n'existe pas' Réviser la programmation. 'Fonctions M incompatibles (M3/M4/M5/M19)' DÉTECTION CAUSE 1090 Au cours de l'exécution. La syntaxe de l'instruction ou la fonction programmée n’est pas correcte. Réviser la programmation. 'G159: numéro d'offset non valable' DÉTECTION CAUSE SOLUTION 1089 Au cours de l'exécution. Il est impossible de compenser le rayon d’outil s’il manque l’un des deux axes du plan actif dans le canal. Définir le plan de travail. Si le canal a cédé ses axes à d’autres canaux, récupérer l’axe manquant avec les instructions #CALL AX ou #SET AX. 'On attend "="' DÉTECTION CAUSE SOLUTION 1088 Au cours de l'exécution. La CNC a essayé de changer le plan de travail ou les axes composant le plan avec la compensation du rayon active. Annuler la compensation pour définir le nouveau plan de travail. 'G41/G42 non admise s'il manque le premier ou deuxième axe du plan actif' DÉTECTION CAUSE 1087 Au cours de l'exécution. Dans un bloc il y a deux fonctions G ou plus programmées incompatibles entre elles. Programmer les fonctions dans des blocs différents. 'Pas de changement de plan admis avec compensation de rayon active' DÉTECTION CAUSE 1085 Au cours de l'exécution. Dans un bloc il y a deux fonctions G ou plus programmées incompatibles entre elles. Programmer les fonctions dans des blocs différents. Au cours de l'exécution. Il y a plus d'une fonction D dans le même bloc. Il ne peut y avoir qu'une seule fonction D dans chaque bloc. Programmer les deux fonctions dans des blocs différents. 'Vitesse F programmée en double' DÉTECTION CAUSE SOLUTION Au cours de l'exécution. Il y a plus d'une fonction F dans le même bloc. Il ne peut y avoir qu'une seule fonction F dans chaque bloc. Programmer les deux fonctions dans des blocs différents. S o l ut i o n s d ’ e r r e ur s . 1095 'La vitesse F ne peut pas être négative ou zéro' DÉTECTION CAUSE SOLUTION 1096 'La vitesse ne peut pas être programmée avec E' DÉTECTION CAUSE SOLUTION 1097 SOLUTION SOLUTION MINLOCP - MAXLOCP Paramètres arithmétiques locaux. MINGLBP - MAXGLBP Paramètres arithmétiques globaux. MINCOMP - MAXCOMP Paramètres arithmétiques communs. Au cours de l'exécution. La syntaxe de l'instruction n’est pas correcte ou il y a plus d’information dans le bloc. Réviser la programmation. Les instructions doivent être programmées seules dans le bloc et on ne peut ajouter que l’étiquette du bloc. Au cours de l'exécution. Le rayon ne peut être programmé qu’avec R ou R1. Réviser la programmation. Au cours de l'exécution. La fonction O n'existe pas. Réviser la programmation. 'Le caractère "%" n'est pas admis dans le programme principal' DÉTECTION CAUSE SOLUTION 1105 Rang valable. 'Fonction O inexistante' DÉTECTION CAUSE SOLUTION 1104 Paramètres machine. 'L'indice pour R doit être 1' DÉTECTION CAUSE SOLUTION 1103 Au cours de l'exécution. Le paramètre arithmétique n’existe pas ; il n’est pas dans la gamme permise par les paramètres machine. Réviser la programmation. Réviser dans les paramètres machine la gamme de paramètres arithmétiques valable. 'Instruction #SET IPOPOS mal programmée' DÉTECTION CAUSE SOLUTION 1102 Au cours de l'exécution. Deux fonctions S ou plus sont programmées dans un bloc pour la même broche. Dans un même bloc il ne peut y avoir qu’une vitesse pour chaque broche. 'Indice de paramètre hors de rang' DÉTECTION CAUSE 1101 Au cours de l'exécution. Le nom de la broche n’est pas valable, la broche n’existe pas dans le système ou la broche n’appartient pas au canal. Les noms de broche valables sont S, S1, …, S9. La broche programmée dans le bloc doit exister dans la configuration du système et en fonction de l'instruction, aussi dans la configuration du canal. Un canal ne peut commander que ses broches. 'Vitesse S programmée en double' DÉTECTION CAUSE SOLUTION 1100 Au cours de l'exécution. L'avance a été programmée avec la fonction E. Programmer l'avance avec la fonction F. 'Nom inconnu de broche' DÉTECTION CAUSE 1098 Au cours de l'exécution. L'avance (F) doit être une valeur positive et non nulle. Réviser la programmation. Au cours de l'exécution. On ne peut utiliser le caractère "%" que comme premier caractère dans la définition du nom du programme principal ou d’une sous-routine locale. Éliminer le caractère du programme. CNC 8070 'On attend opérateur d'assignation' DÉTECTION CAUSE SOLUTION Au cours de l'exécution. Il manque un opérateur d'assignation après la variable ou paramètre. Les opérateurs d'affectation valables sont "=", "+=", "-=", "*=", "/=". (REF: 1901) ·29· S o l ut i o n s d ’ e r r e ur s . 1106 'On attend "]"' DÉTECTION CAUSE SOLUTION 1107 'Axe inexistant ou non disponible' DÉTECTION CAUSE SOLUTION 1108 SOLUTION SOLUTION SOLUTION CNC 8070 (REF: 1901) ·30· Au cours de l'exécution. L'instruction n’est pas programmée seule dans le bloc et l’information additionnelle n’est pas un $GOTO. Réviser la programmation. Les instructions doivent être programmées seules dans le bloc et on ne peut ajouter que l’étiquette du bloc. La seule exception est de programmer $IF et $GOTO dans le même bloc. 'On n'attend pas $ELSE' DÉTECTION CAUSE SOLUTION 1114 Au cours de l'exécution. Une instruction n’est pas programmée seule dans le bloc. Réviser la programmation. Les instructions doivent être programmées seules dans le bloc et on ne peut ajouter que l’étiquette du bloc. La seule exception est de programmer $IF et $GOTO dans le même bloc. 'L'instruction $IF <condition> ne peut être suivie que de $GOTO' DÉTECTION CAUSE 1113 Au cours de l'exécution. L’un des paramètres I, J, K est programmé plus d’une fois dans le même bloc. Réviser la programmation. 'Les instructions de commande $ se programment seules dans le bloc' DÉTECTION CAUSE SOLUTION 1112 Au cours de l'exécution. Dans les fonctions G20 et G74, l’indice programmé à côté du nom de l’axe est incorrect. L’indice de l’axe doit être une valeur entre 1 et le nombre maximum d’axes du système ou du canal. 'Valeurs pour I, J, K programmées en double' DÉTECTION CAUSE SOLUTION 1111 Au cours de l'exécution. Dans l'une des fonctions suivantes, un axe est programmé plus d’une fois. • Déplacement des axes sur G0, G1, G2, G3, G8 ou G9. • Filetage G33 ou G63. • Instructions #FACE ou #CYL. • Sélection du plan, G20. Avec les fonctions impliquant un déplacement d’axes, la double programmation d’un axe peut être due au fait d’avoir programmé l’axe en coordonnées cartésiennes et en coordonnées polaires. Réviser la programmation. 'Indice d'axe incorrect' DÉTECTION CAUSE 1110 Au cours de l'exécution. La CNC essaie de déplacer un axe qui n’existe pas ou qui n’est pas disponible dans le système ou dans le canal. L’axe programmé dans une instruction ou une variable n’existe pas dans le système ou dans le canal. Vérifier que l’axe programmé existe dans le canal et qu’il est disponible (pas stationné). 'Axe programmé en double' DÉTECTION CAUSE 1109 Au cours de l'exécution. Il manque le crochet de fermeture "]" dans l’expression ou l'instruction programmée. Réviser la programmation. Au cours de l'exécution. La CNC a détecté une instruction $ELSE sans une instruction $IF préalable. Réviser la programmation. 'L'instruction $ELSE doit être programmée seule dans le bloc' DÉTECTION CAUSE SOLUTION Au cours de l'exécution. L'instruction n’est pas programmée seule dans le bloc. Réviser la programmation. S o l ut i o n s d ’ e r r e ur s . 1115 'On n'attend pas $ELSEIF' DÉTECTION CAUSE SOLUTION 1116 'L'instruction $ELSEIF <condition> doit être programmée seule dans le bloc' DÉTECTION CAUSE SOLUTION 1117 SOLUTION SOLUTION Au cours de l'exécution. La CNC a détecté une instruction $ENDSWITCH sans une instruction $SWITCH préalable. Réviser la programmation. 'L'instruction $ENDSWITCH doit être programmée seule dans le bloc' DÉTECTION CAUSE SOLUTION 1126 Au cours de l'exécution. L'instruction n’est pas programmée seule dans le bloc. Réviser la programmation. 'On n'attend pas $ENDSWITCH' DÉTECTION CAUSE 1125 Au cours de l'exécution. La CNC a détecté une instruction $DEFAULT sans une instruction $SWITCH préalable. Réviser la programmation. 'L'instruction $DEFAULT doit être programmée seule dans le bloc' DÉTECTION CAUSE SOLUTION 1124 Au cours de l'exécution. L'instruction n’est pas programmée seule dans le bloc. Réviser la programmation. 'On n'attend pas $DEFAULT' DÉTECTION CAUSE 1123 Au cours de l'exécution. La CNC a détecté une instruction $CASE sans une instruction $SWITCH préalable. Réviser la programmation. 'L'instruction $CASE <expression> doit être programmée seule dans le bloc' DÉTECTION CAUSE SOLUTION 1122 Au cours de l'exécution. L'instruction n’est pas programmée seule dans le bloc. Réviser la programmation. 'On n'attend pas $CASE' DÉTECTION CAUSE SOLUTION 1121 Au cours de l'exécution. L'instruction n’est pas programmée seule dans le bloc. Réviser la programmation. 'L'instruction $SWITCH <expression> doit être programmée seule dans le bloc' DÉTECTION CAUSE SOLUTION 1120 Au cours de l'exécution. La CNC a détecté une instruction $ENDIF sans une instruction $IF préalable. Réviser la programmation. 'L'instruction $ENDIF doit être programmée seule dans le bloc' DÉTECTION CAUSE SOLUTION 1119 Au cours de l'exécution. L'instruction n’est pas programmée seule dans le bloc. Réviser la programmation. 'On n'attend pas $ENDIF' DÉTECTION CAUSE SOLUTION 1118 Au cours de l'exécution. La CNC a détecté une instruction $ELSEIF sans une instruction $IF préalable. Réviser la programmation. Au cours de l'exécution. L'instruction n’est pas programmée seule dans le bloc. Réviser la programmation. CNC 8070 '$FOR: variable compteur non valable' DÉTECTION CAUSE SOLUTION Au cours de l'exécution. Le compteur de l'instruction $FOR n'est pas valable. Le compteur de l’instruction $FOR pourra être une variable ou un paramètre arithmétique. (REF: 1901) ·31· S o l ut i o n s d ’ e r r e ur s . 1127 'L'instruction $FOR <condition> doit être programmée seule dans le bloc' DÉTECTION CAUSE SOLUTION 1128 '$FOR: trop de caractères dans la condition' DÉTECTION CAUSE SOLUTION 1129 SOLUTION SOLUTION 1137 (REF: 1901) ·32· Au cours de l'exécution. La CNC a détecté une instruction $ENDDO sans une instruction $DO préalable. Réviser la programmation. 'L'instruction $ENDDO <expression> doit être programmée seule dans le bloc' DÉTECTION CAUSE SOLUTION 1138 Au cours de l'exécution. L'instruction n’est pas programmée seule dans le bloc. Réviser la programmation. 'On n'attend pas $ENDDO' DÉTECTION CAUSE SOLUTION CNC 8070 Au cours de l'exécution. L'instruction n’est pas programmée seule dans le bloc. Réviser la programmation. 'L'instruction $DO doit être programmée seule dans le bloc' DÉTECTION CAUSE SOLUTION 1136 Au cours de l'exécution. La CNC a détecté une instruction $ENDWHILE sans une instruction $WHILE préalable. Réviser la programmation. 'L'instruction $ENDWHILE doit être programmée seule dans le bloc' DÉTECTION CAUSE SOLUTION 1135 Au cours de l'exécution. La condition de l’instruction $WHILE dépasse le nombre maximum de caractères permis. Le nombre maximum de caractères permis est 5000. 'On n'attend pas $ENDWHILE' DÉTECTION CAUSE 1134 Au cours de l'exécution. L'instruction n’est pas programmée seule dans le bloc. Réviser la programmation. '$WHILE: trop de caractères dans la condition' DÉTECTION CAUSE 1133 Au cours de l'exécution. L'instruction n’est pas programmée seule dans le bloc. Réviser la programmation. 'L'instruction $WHILE <condition> doit être programmée seule dans le bloc' DÉTECTION CAUSE SOLUTION 1132 Au cours de l'exécution. La CNC a détecté une instruction $ENDFOR sans une instruction $FOR préalable. Réviser la programmation. 'L'instruction $ENDFOR doit être programmée seule dans le bloc' DÉTECTION CAUSE SOLUTION 1131 Au cours de l'exécution. Le bloc contenant l'instruction $FOR a plus de 5100 caractères. Écrire le bloc contenant l’instruction $FOR la plus brève. 'On n'attend pas $ENDFOR' DÉTECTION CAUSE SOLUTION 1130 Au cours de l'exécution. L'instruction n’est pas programmée seule dans le bloc. Réviser la programmation. Au cours de l'exécution. L'instruction n’est pas programmée seule dans le bloc. Réviser la programmation. 'L'instruction $BREAK doit être programmée seule dans le bloc' DÉTECTION CAUSE SOLUTION Au cours de l'exécution. L'instruction n’est pas programmée seule dans le bloc. Réviser la programmation. S o l ut i o n s d ’ e r r e ur s . 1139 'On n'attend pas $BREAK' DÉTECTION CAUSE SOLUTION 1140 'On n'attend pas $CONTINUE' DÉTECTION CAUSE SOLUTION 1141 SOLUTION Au cours de l'exécution. La CNC ne dispose pas d’un deuxième bloc de déplacement pour réaliser la trajectoire de jonction. Ne programmer aucun bloc entre la fonction G qui définit la trajectoire de jonction et le deuxième bloc de déplacement. 'Les fonctions G8/G36/G37/G38/G39 doivent être précédées d'un bloc de mouvement' DÉTECTION CAUSE SOLUTION 1152 Au cours de l'exécution. La CNC ne peut pas effectuer la trajectoire d'union avec le rayon programmé. Vérifier le rayon programmé. Vérifier que la jonction est réellement possible entre les blocs initial et final. 'Les fonctions G36/G37/G38/G39 doivent être suivies d'un bloc de mouvement' DÉTECTION CAUSE 1151 Au cours de l'exécution. Le bloc de déplacement postérieur à la sortie tangentielle n'est pas linéaire. Réviser la programmation. 'Il est impossible d'exécuter G36/G37/G38/G39 programmée' DÉTECTION CAUSE SOLUTION 1150 Au cours de l'exécution. Le bloc de déplacement antérieur à l'entrée tangentielle n'est pas linéaire. Réviser la programmation. 'La trajectoire postérieure à G38 doit être linéaire' DÉTECTION CAUSE SOLUTION 1149 Au cours de l'exécution. L'instruction n’est pas programmée seule dans le bloc. Réviser la programmation. 'La trajectoire antérieure à G37 doit être linéaire' DÉTECTION CAUSE SOLUTION 1147 Au cours de l'exécution. L'instruction n’est pas programmée seule dans le bloc. Réviser la programmation. 'L'instruction #TIME doit être programmée seule dans le bloc' DÉTECTION CAUSE SOLUTION 1146 Au cours de l'exécution. La CNC a détecté une instruction $CONTINUE mais aucune boucle de contrôle n’est ouverte ; $FOR, $WHILE ou $DO. Réviser la programmation. La CNC utilise l’instruction $CONTINUE pour retourner au point de départ d’une boucle $FOR, $WHILE ou $DO. 'L'instruction $CONTINUE doit être programmée seule dans le bloc' DÉTECTION CAUSE SOLUTION 1142 Au cours de l'exécution. La CNC a détecté une instruction $BREAK mais aucune boucle de contrôle n’est ouverte ; $IF, $ELSE, $FOR, $WHILE, $DO ou $CASE. Réviser la programmation. La CNC utilise l’instruction $BREAK pour terminer un $CASE ou pour sortir d’une boucle $IF, $ELSE, $WHILE, $FOR ou $DO avant qu’elle ne termine. Au cours de l'exécution. La CNC ne dispose pas d'un premier bloc de déplacement pour réaliser la trajectoire de jonction. Ne programmer aucun bloc entre la fonction G qui définit la trajectoire de jonction et le premier bloc de déplacement. CNC 8070 'Excès d'emboîtement de sous-routines' DÉTECTION CAUSE SOLUTION Au cours de l'exécution. La CNC a dépassé le nombre maximum de niveaux d'imbrication. Corriger le programme en réduisant le nombre d’appels aux sous-routines (locales et globales) qui impliquent un nouveau niveau d’imbrication. La CNC permet 20 niveaux d'imbrication. (REF: 1901) ·33· S o l ut i o n s d ’ e r r e ur s . 1153 'Trop de sous-routines locales définies dans le programme' DÉTECTION CAUSE SOLUTION 1154 'Nom de fichier trop long' DÉTECTION CAUSE SOLUTION 1155 SOLUTION (REF: 1901) SOLUTION 1161 Pendant l'exécution. la CNC ne trouve pas la sous-routine locale. Les possibles causes sont les suivantes: • La sous-routine locale n'est pas définie au début du programme principal. • Le programme a activé une sous-routine locale comme modale, puis a exécuté une sous-routine d'utilisateur (par exemple, G500 à G599) avec des blocs de mouvement. La sous-routine d'utilisateur ne trouve pas la sous-routine locale, car elle appartient à un autre programme. Les possibles solutions sont les suivantes: • Vérifier que le nom de la sous-routine locale dans le bloc d’appel est identique au nom figurant dans sa définition. Les sous-routines locales doivent être définies au début du programme. • Définir la sous-routine locale comme globale. 'Blocs de commande $ ouverts' DÉTECTION CAUSE SOLUTION ·34· Au cours de l'exécution. Le nom de la sous-routine dépasse le nombre de caractères permis par la CNC. Le nom d'une sous-routine peut avoir un maximum de 63 caractères. Réviser la programmation. 'Sous-routine locale non trouvée' DÉTECTION CAUSE CNC 8070 Au cours de l'exécution. la CNC ne trouve pas la sous-routine globale. Vérifier que le nom et le chemin de la sous-routine sont corrects. Si dans l’appel à la sous-routine le chemin n’est pas défini, la CNC appliquera le critère de recherche par défaut (consulter le manuel de programmation). 'Nom de sous-routine locale trop long' DÉTECTION CAUSE 1160 Au cours de l'exécution. La CNC ne trouve pas le programme principal. Dans un programme avec des sous-routines locales, le programme principal doit avoir un nom (%nom). 'Sous-routine globale non trouvée' DÉTECTION CAUSE SOLUTION 1159 Au cours de l'exécution. La CNC ne peut pas accéder au programme ou sous-routine. Vérifier que les fichiers sont valides et ne sont pas corrompus. Dans le cas des appels à des sous-routines, vérifier que le nom et le chemin sont corrects. Si dans l’appel à la sous-routine le chemin n’est pas défini, la CNC appliquera le critère de recherche par défaut (consulter le manuel de programmation). 'Programme principal non trouvé' DÉTECTION CAUSE SOLUTION 1157 Au cours de l'exécution. Le nom du fichier dépasse le nombre de caractères permis par la CNC. Le nom d’un programme ou d’une sous-routine peut avoir un maximum de 63 caractères et le chemin 120 caractères. Si on programme le nom d’un programme ou d’une sousroutine avec le chemin, le nombre maximum de caractères sera la somme des deux valeurs. Réduire le nombre de caractères dans le nom de programme ou sous-programme. Changer l’emplacement du programme ou de la sous-routine pour réduire le nombre de caractères dans le chemin. 'Il est impossible d'accéder au fichier' DÉTECTION CAUSE SOLUTION 1156 Au cours de l'exécution. Le programme a plus de sous-routines locales que celles permises par la CNC. Réduire le nombre de sous-routines locales; regrouper plusieurs sous-routines en une seule ou utiliser des sous-routines globales. La CNC permet 100 sous-routines locales par programme. Au cours de l'exécution. La CNC a trouvé un bloc de contrôle "$" qui n’a pas son instruction de fermeture correspondante. Réviser la programmation. S o l ut i o n s d ’ e r r e ur s . 1162 'On n'attend pas M17/M29/#RET' DÉTECTION CAUSE SOLUTION 1163 'On n'attend pas M30/M02' DÉTECTION CAUSE SOLUTION 1164 SOLUTION SOLUTION SOLUTION Au cours de l'exécution. L'instruction n’est pas programmée seule dans le bloc. Réviser la programmation. Les instructions doivent être programmées seules dans le bloc et on ne peut ajouter que l’étiquette du bloc. 'Les instructions # sont programmées seules dans le bloc' DÉTECTION CAUSE SOLUTION 1172 Au cours de l'exécution. L’un des indices définis dans la variable d’array est incorrect. L’indice minimum admissible pour une variable d’array est 1 et le maximum dépend de la variable dont il s’agit. Dans certains cas l'indice 0 est admis: G.GS, G.MS, G.LUP1 à G.LUP7, G.LUPACT et MTB.P. 'L'instruction #SYNC POS doit être programmée seule dans le bloc' DÉTECTION CAUSE SOLUTION 1171 Au cours de l'exécution. L’expression mathématique comporte un logarithme (LOG/LN) d’un nombre négatif ou zéro. Réviser la programmation. 'Indice de variable hors de rang' DÉTECTION CAUSE SOLUTION 1170 Au cours de l'exécution. L’expression mathématique comporte une racine carrée (SQRT) d’un nombre négatif. Réviser la programmation. 'Logarithme d'un nombre négatif ou de zéro' DÉTECTION CAUSE 1168 Au cours de l'exécution. Les possibles causes sont les suivantes: • La variable demandée n'existe pas. • Erreur syntactique dans le nom de la variable. • La variable est un array et l'indice de l'array n'a pas été indiqué. • Une variable générale a été sollicitée pour un axe déterminé ou à l’inverse. Réviser la programmation. 'Racine d'un nombre négatif.’ DÉTECTION CAUSE 1167 Au cours de l'exécution. L'expression mathématique est incorrecte. Vérifier tous les termes de l’expression ; variables, paramètres, opérateurs, etc. 'Variable inexistante' DÉTECTION CAUSE 1166 Au cours de l'exécution. La CNC a détecté une fonction M02 ou M30 comme fin de la sous-routine. Vérifier que toutes les sous-routines locales et globales terminent avec M17, M29 ou #RET. 'Terme inconnu dans expression mathématique' DÉTECTION CAUSE SOLUTION 1165 Au cours de l'exécution. La CNC a détecté une fonction M17, M29 ou #RET comme fin du programme. Programmer M30/M02 comme fin du programme principal. Si l'erreur persiste, vérifier que toutes les sous-routines locales terminent avec M17, M29 ou #RET. Au cours de l'exécution. L'instruction n’est pas programmée seule dans le bloc. Réviser la programmation. Les instructions doivent être programmées seules dans le bloc et on ne peut ajouter que l’étiquette du bloc. La seule exception est l'instruction #AXIS laquelle doit être programmée dans le même bloc que la fonction G201. CNC 8070 'Instruction non autorisée avec compensation de rayon d'outil active' DÉTECTION CAUSE SOLUTION Au cours de l'exécution. La CNC a essayé d’exécuter une instruction incompatible avec la compensation de rayon. Désactiver la compensation de rayon pour exécuter l'instruction. (REF: 1901) ·35· S o l ut i o n s d ’ e r r e ur s . 1173 'L'instruction #UNLINK doit être programmée seule dans le bloc' DÉTECTION CAUSE SOLUTION 1174 '#LINK: on ne peut pas définir un nouvel accouplement alors qu'un antérieur reste actif' DÉTECTION CAUSE SOLUTION 1175 SOLUTION SOLUTION SOLUTION CNC 8070 (REF: 1901) Au cours de l'exécution. Le nombre de couplages définis dépasse le maximum permis. Le nombre maximum de couplages pouvant être actifs dans un canal est égal au nombre d’axes du canal moins trois. 'L'instruction #LINK doit être programmée seule dans le bloc' DÉTECTION CAUSE SOLUTION ·36· Au cours de l'exécution. L'axe esclave d'un couplage est actif en mode manuel aditif (G201). Annuler le mode manuel additif pour pouvoir accoupler l'axe. '#LINK: excès de couplages programmés' DÉTECTION CAUSE SOLUTION 1183 Au cours de l'exécution. Les axes maître et esclave du couplage sont rotatifs mais ils ne sont pas du même type, linearlike ou module. Les deux axes d’un couplage doivent être du même type (paramètre AXISMODE). '#LINK: il est impossible de définir un axe actif comme esclave sur G201' DÉTECTION CAUSE SOLUTION 1182 Au cours de l'exécution. Les axes maître et esclave du couplage ne sont pas du même type, linéaire ou rotatif. Les deux axes d’un couplage doivent être du même type (paramètre AXISTYPE). '#LINK: les axes maître et esclave doivent avoir le même mode (AXISMODE)' DÉTECTION CAUSE 1181 Au cours de l'exécution. L'axe esclave du couplage est un des trois axes principaux. Réviser la programmation. '#LINK: les axes maître et esclave doivent être du même type (AXISTYPE)' DÉTECTION CAUSE SOLUTION 1180 Au cours de l'exécution. Les possibles causes sont les suivantes: • L’axe esclave du couplage n’existe pas ou n’est pas disponible dans le canal. • La CNC a essayé d’annuler un couplage dont l’axe esclave n’existe pas ou n’est pas disponible dans le canal. Les axes maître et esclave doivent exister dans le canal qui exécute l'instruction. '#LINK: l'axe esclave ne peut pas être un axe du plan principal' DÉTECTION CAUSE SOLUTION 1179 Au cours de l'exécution. Les possibles causes sont les suivantes: • L’axe maître du couplage n’existe pas ou n’est pas disponible dans le canal. • La CNC a essayé d’annuler un couplage dont l’axe maître n’existe pas ou n’est pas disponible dans le canal. Les axes maître et esclave doivent exister dans le canal qui exécute l'instruction. '#LINK: l'axe esclave n'appartient pas à la configuration actuelle d'axes' DÉTECTION CAUSE 1178 Au cours de l'exécution. Il n’y a aucun couplage d’axes défini dans l'instruction #LINK. Programmer les axes maître et esclave dans l'instruction #LINK. '#LINK: l'axe maître n'appartient pas à la configuration actuelle d'axes' DÉTECTION CAUSE 1177 Au cours de l'exécution. La CNC a essayé d’activer un deuxième couplage d’axes sans désactiver le premier. Réviser la programmation. Désactiver le premier couplage avant d’activer le deuxième. Pour avoir les deux couplages, désactiver le premier couplage et activer les deux avec une seule instruction #LINK. '#LINK: le couplage n'a pas été défini' DÉTECTION CAUSE SOLUTION 1176 Au cours de l'exécution. L'instruction n’est pas programmée seule dans le bloc. Réviser la programmation. Au cours de l'exécution. L'instruction n’est pas programmée seule dans le bloc. Réviser la programmation. S o l ut i o n s d ’ e r r e ur s . 1184 '#LINK: les axes maître et esclave coïncident' DÉTECTION CAUSE SOLUTION 1185 '#LINK: un axe ne peut pas être esclave de plusieurs maîtres' DÉTECTION CAUSE SOLUTION 1186 Au cours de l'exécution. L'instruction #INCJOG essaie de définir une avance négative ou nulle. L’avance de l’axe sur chaque position du commutateur doit être une valeur positive et non nulle. '#CONTJOG/#INCJOG: avance programmée hors de rang' DÉTECTION CAUSE SOLUTION 1194 Au cours de l'exécution. L'instruction #INCJOG essaie de définir une distance négative ou nulle. Le déplacement incrémental de l’axe sur chaque position du commutateur doit être une valeur positive et non nulle. '#INCJOG: vitesses de jog incrémental négatives ou nulles non autorisées' DÉTECTION CAUSE SOLUTION 1193 Au cours de l'exécution. L'instruction #MPG essaie de définir une résolution de manivelle négative ou nulle. Le déplacement par impulsion de la manivelle doit être une valeur positive et non nulle. '#INCJOG: distances de jog incrémental négatives ou nulles non autorisées' DÉTECTION CAUSE SOLUTION 1192 Au cours de l'exécution. L'instruction a plus de paramètres que ceux permis. L'instruction #MPG admet un maximum de trois paramètres. Chacun d’eux représente le déplacement par impulsion de la manivelle sur chaque position du commutateur. '#MPG: résolutions de manivelle négatives ou nulles non autorisées' DÉTECTION CAUSE SOLUTION 1191 Au cours de l'exécution. Erreur dans la syntaxe de l'instruction. Réviser la programmation. '#MPG: trop de paramètres' DÉTECTION CAUSE SOLUTION 1190 Au cours de l'exécution. Le même axe est programmé plus d'une fois dans l'instruction. Réviser la programmation. 'On n'attend pas "["' DÉTECTION CAUSE SOLUTION 1189 Au cours de l'exécution. Un axe ne peut pas être esclave dans un couplage et maître dans un autre. Un axe ne peut pas être maître dans un couplage et esclave dans un autre. '#AXIS: nom de l'axe répété' DÉTECTION CAUSE SOLUTION 1188 Au cours de l'exécution. Un axe est esclave de plusieurs maîtres. Un axe peut être esclave d'un axe maître. '#LINK: un axe maître ne peut pas être esclave dans un autre couplage et vice-versa. DÉTECTION CAUSE SOLUTION 1187 Au cours de l'exécution. Les axes maître et esclave du couplage sont le même axe. Les axes maître et esclave doivent être différents. Au cours de l'exécution. L'avance programmée est trop haute. Réviser la programmation. CNC 8070 '#INCJOG: trop de paramètres' DÉTECTION CAUSE SOLUTION Au cours de l'exécution. L'instruction a plus de paramètres que ceux permis. L'instruction #INCJOG admet un maximum de cinq groupes de paramètres. Chacun d’eux représente l’avance et le déplacement de l’axe pour chaque position du commutateur en jog incrémental. (REF: 1901) ·37· S o l ut i o n s d ’ e r r e ur s . 1195 '#CONTJOG: trop de paramètres' DÉTECTION CAUSE SOLUTION 1196 '#CONTJOG: vitesses de jog continu négatives ou nulles non autorisées' DÉTECTION CAUSE SOLUTION 1197 SOLUTION SOLUTION CNC 8070 (REF: 1901) ·38· Au cours de l'exécution. L'instruction n'existe pas ou elle est mal programmée. Réviser la programmation. '#CALL AX/#SET AX: type d'offset inconnu' DÉTECTION CAUSE SOLUTION 1206 Au cours de l'exécution. L'instruction n’est pas programmée seule dans le bloc. Réviser la programmation. 'Instruction mal programmée ou inexistante' DÉTECTION CAUSE SOLUTION 1205 Au cours de l'exécution. Les limites de parcours de l’axe pour le déplacement manuel sont nulles. Réviser la programmation. 'L'instruction #SET IPOPOS doit être programmée seule dans le bloc' DÉTECTION CAUSE SOLUTION 1204 Au cours de l'exécution. La valeur de la limite de parcours supérieur est trop haute. Réviser la programmation. '#SET OFFSET: offsets supérieurs et inférieurs nuls' DÉTECTION CAUSE SOLUTION 1203 Au cours de l'exécution. La limite de parcours supérieur de l'axe pour le déplacement manuel a une valeur négative. La limite de parcours supérieure pour le déplacement manuel doit être une valeur positive ou zéro. '#SET OFFSET: limite positif hors de rang' DÉTECTION CAUSE SOLUTION 1201 Au cours de l'exécution. La valeur de la limite de parcours inférieur est trop basse. Réviser la programmation. '#SET OFFSET: offset inférieur négatif'' DÉTECTION CAUSE 1200 Au cours de l'exécution. La limite de parcours inférieur de l'axe pour le déplacement manuel a une valeur positive. La limite de parcours inférieure pour le déplacement manuel doit être une valeur négative ou zéro. '#SET OFFSET: limite négative hors de rang' DÉTECTION CAUSE SOLUTION 1199 Au cours de l'exécution. L'instruction #CONTJOG essaie de définir une avance négative ou nulle. L’avance de l’axe en jog continu doit être une valeur positive et non nulle. '#SET OFFSET: offset inférieur positif' DÉTECTION CAUSE 1198 Au cours de l'exécution. L'instruction a plus de paramètres que ceux permis. L'instruction #CONTJOG n’admet qu’un paramètre, qui représente l’avance de l’axe lorsque le commutateur est en jog continu. Au cours de l'exécution. Le type d'offset programmé dans l'instruction n’existe pas. Les types d'offset valables sont ALL, LOCOF, FIXOF, TOOLOF, ORGOF, MEASOF, MANOF. 'On attend ","' DÉTECTION CAUSE SOLUTION Au cours de l'exécution. Il faut programmer "," dans l'instruction ou fonction. Réviser la programmation. S o l ut i o n s d ’ e r r e ur s . 1209 'Indice d'axe hors de rang' DÉTECTION CAUSE SOLUTION 1210 '#CALL AX/#SET AX: nom de l'axe répété' DÉTECTION CAUSE SOLUTION 1211 SOLUTION Au cours de l'exécution. Le nom d'un des axes est utilisé par un axe C. Réviser la programmation. '#CALL AX: indice utilisé actuellement' DÉTECTION CAUSE SOLUTION 1218 Au cours de l'exécution. L'instruction n’est pas programmée seule dans le bloc. Réviser la programmation. '#CALL AX/#CAX: nom d'axe utilisé actuellement' DÉTECTION CAUSE SOLUTION 1217 Au cours de l'exécution. Trop d’axes programmés; le nombre d’axes programmés dépasse le nombre d’axes du système. Réviser la configuration d'axes définie pour le canal. Le nombre d'axes d'un canal ne peut pas dépasser le nombre d'axes du système. 'L'instruction #CALL AX/#SET AX doit être programmée seule dans le bloc' DÉTECTION CAUSE SOLUTION 1216 Au cours de l'exécution. Il n'est pas permis de programmer #CALL AX avec la fonction G63 active. Désactiver le filetage G63 avant de modifier la configuration d’axes. '#CALL AX/#SET AX: trop d'axes requis' DÉTECTION CAUSE 1215 Au cours de l'exécution. Deux axes tentent d'occuper la même position dans le canal. Réviser la programmation. '#CALL AX/#SET AX: il est impossible avec G63 active' DÉTECTION CAUSE SOLUTION 1214 Au cours de l'exécution. Deux axes tentent d'occuper la même position dans le canal. Réviser la programmation. '#CALL AX/#SET AX :nom de l'axe répété' DÉTECTION CAUSE SOLUTION 1213 Au cours de l'exécution. Le même axe est programmé plus d'une fois dans l'instruction. Réviser la programmation. '#CALL AX/#SET AX: indice de l'axe répété' DÉTECTION CAUSE SOLUTION 1212 Au cours de l'exécution. Les possibles causes sont les suivantes: • Dans les instructions #CALL AX/#SET AX la position pour un axe n’est pas correcte ; la position est occupée, elle dépasse le maximum permis ou il n’y a pas de place pour l’axe. • Programmation du nom de l'axe avec un caractère générique incorrect. Les possibles solutions sont les suivantes: • L'instruction peut placer les axes sur n’importe quelle position libre comprise entre 1 et un numéro égal au total d’axes en plus des broches du système. • Les caractères génériques possibles sont de @1 à @6 et @SM. Au cours de l'exécution. Unes des positions est occupée par un autre axe. Repasser la configuration d’axes définie pour le canal ; deux axes ne peuvent pas être sur la même position. Un axe peut utiliser toute position libre comprise entre 1 et un numéro égal au maximum de broches et d'axes permis par le système. CNC 8070 'L'instruction #FREE AX doit être programmée seule dans le bloc' DÉTECTION CAUSE SOLUTION Au cours de l'exécution. L'instruction n’est pas programmée seule dans le bloc. Réviser la programmation. (REF: 1901) ·39· S o l ut i o n s d ’ e r r e ur s . 1219 'On attend "," ou "]"' DÉTECTION CAUSE SOLUTION 1220 '#FREE AX: il est impossible d'éliminer un axe actif en mode manuel' DÉTECTION CAUSE SOLUTION 1221 SOLUTION SOLUTION CNC 8070 (REF: 1901) ·40· Au cours de l'exécution. Aucun axe du plan n’est défini comme axe longitudinal. Définir l'un des axes du plan comme axe longitudinal (paramètre LONGAXIS). 'Le transfert programmé excède le rang de données' DÉTECTION CAUSE SOLUTION 1236 Au cours de l'exécution. Aucun axe du plan n’est défini comme axe frontal. Définir l'un des axes du plan comme axe frontal (paramètre FACEAXIS). 'Pas d'axe latéral (LONGAXIS) dans le plan actif pour compensation de rayon' DÉTECTION CAUSE SOLUTION 1233 Au cours de l'exécution. Une des opérations programmées réalise une division par zéro. Réviser la programmation. Si l'on travaille avec des paramètres, il se peut, que dans l’historique du programme, ce paramètre ait acquis une valeur zéro. Vérifier que le paramètre n’arrive pas à l’opération avec cette valeur. 'Pas d'axe frontal (FACEAXIS) dans le plan actif pour compensation de rayon' DÉTECTION CAUSE SOLUTION 1227 Au cours de l'exécution. Il manque un opérateur d'assignation après la variable ou paramètre. Les opérateurs d'affectation valables sont "=", "+=", "-=", "*=", "/=". 'Division par zéro' DÉTECTION CAUSE SOLUTION 1226 Au cours de l'exécution. La CNC ne trouve pas la fin du programme. Il est probable qu’il y ait un bloc de début de commentaire (#COMMENT BEGIN) mais il manque le bloc de fin de commentaire (#COMMENT END). Réviser la programmation. 'Opérateur manquant ou inconnu' DÉTECTION CAUSE SOLUTION 1225 Au cours de l'exécution. Il y a un bloc de fin de commentaire (#COMMENT END) mais il manque le bloc de début de commentaire (#COMMENT BEGIN). Réviser la programmation. 'Caractère de fin de fichier dans bloc commentaire' DÉTECTION CAUSE 1224 Au cours de l'exécution. L'instruction n’est pas programmée seule dans le bloc. Réviser la programmation. 'On n'attend pas #COMMENT END' DÉTECTION CAUSE 1223 Au cours de l'exécution. Un axe en mode manuel additif (G201) ne peut pas être supprimé du canal. Annuler le mode manuel additif de l’axe avec la fonction G202 pour réaliser supprimer l’axe du canal. 'L'instruction #SET AX doit être programmée seule dans le bloc' DÉTECTION CAUSE SOLUTION 1222 Au cours de l'exécution. Erreur dans la syntaxe de l'instruction. Réviser la programmation. Au cours de l'exécution. Le décalage d'origine défini dépasse le maximum permis. Réviser la programmation. 'Nom de macro trop long' DÉTECTION CAUSE SOLUTION Au cours de l'exécution. Le nom de la macro dépasse le nombre maximum de caractères permis. Le nombre maximum de caractères permis est 30. S o l ut i o n s d ’ e r r e ur s . 1237 'On attend "\" dans le texte associé à la macro' DÉTECTION CAUSE SOLUTION 1238 'Texte de remplacement de la macro trop long' DÉTECTION CAUSE SOLUTION 1239 SOLUTION SOLUTION Au cours de l'exécution. La CNC a essayé d’exécuter un taraudage rigide (G63) alors que la fonction G95 (avance par tour de la broche) était active. Activer l'avance en fonction du temps (G94). 'Le filetage avec G96 active n'est pas admis' DÉTECTION CAUSE SOLUTION 1248 Au cours de l'exécution. Aucun axe du plan n’est défini comme axe frontal. Définir l'un des axes du plan comme axe frontal (paramètre FACEAXIS). 'Le filetage avec avance sur G95 n'est pas admis' DÉTECTION CAUSE 1247 Au cours de l'exécution. En travaillant en vitesse de coupe constante (G96), la CNC a limité la vitesse de la broche à cause de la proximité de l’axe frontal au centre de rotation. Augmenter la limite de vitesse (G192) ou accepter la limitation. 'G96: il n'y a pas d'axe frontal (FACEAXIS) défini dans le plan actif' DÉTECTION CAUSE SOLUTION 1246 Au cours de l'exécution. Le texte de remplacement associé à la macro est une chaîne de caractères vide. Associer à la macro le texte de remplacement adéquat suivant la fonctionnalité souhaitée. Le texte de remplacement doit être écrit entre guillemets. 'Axe frontal proche du centre: la vitesse de la broche sur G96 a été limitée' DÉTECTION CAUSE 1245 Au cours de l'exécution. La macro n'est pas définie dans le programme. Définir la macro avant de l'utiliser. La macro peut être définie dans un programme. La CNC enregistre dans une table les macros définies depuis un programme ou depuis le mode MDI/MDA, de manière à les avoir disponibles pour tous les programmes exécutés ensuite. La CNC initialise la table de macros au démarrage ou avec l'instruction #INIT MACROTAB. 'Il manque le texte de remplacement de la macro' DÉTECTION CAUSE SOLUTION 1244 Au cours de l'exécution. Nombre maximum de macros dans la CNC dépassé. Maximum 50 macros. On peut supprimer la table de macros avec l'instruction #INIT MACROTAB. 'Macro inexistante' DÉTECTION CAUSE SOLUTION 1241 Au cours de l'exécution. Le nombre de caractères du texte de remplacement de la macro dépasse le maximum permis. Le nombre maximum de caractères permis est 140. 'Nombre maximum de macros dépassé' DÉTECTION CAUSE SOLUTION 1240 Au cours de l'exécution. Une macro qui ne commence pas par le caractère "\" a été incluse dans le texte de remplacement d’une macro. Le texte de remplacement d’une macro doit être placé entre guillemets et peut inclure d’autres macros, qui doivent être délimitées par les caractères \"; par exemple "macro"="\"macro1\" \"macro2\"". Au cours de l'exécution. La CNC a essayé d’exécuter un taraudage rigide (G63) alors que la fonction G96 (vitesse de coupe constante) était active. Activer le mode de vitesse de rotation constante (G97). CNC 8070 'Le filetage et G192 ne sont pas admis dans le même bloc' DÉTECTION CAUSE SOLUTION Au cours de l'exécution. La CNC ne permet pas de programmer les fonctions G63 (taraudage rigide) et G192 (limitation de la vitesse de rotation) dans le même bloc. Programmer les deux instructions dans des blocs différents. (REF: 1901) ·41· S o l ut i o n s d ’ e r r e ur s . 1249 'Le changement de gamme avec G96 active n'est pas admis' DÉTECTION CAUSE SOLUTION 1251 'Le mode manuel avec G96 active n'est pas admis' DÉTECTION CAUSE SOLUTION 1252 SOLUTION SOLUTION SOLUTION 1262 ·42· Au cours de l'exécution. La CNC a essayé d’activer la fonction RTCP, TLC ou une transformation de coordonnées (CS/ACS) en mode 6 sans avoir une cinématique active. Activer d’abord la cinématique puis la fonction souhaitée. 'Le groupe d'axes est insuffisant pour la transformation' DÉTECTION CAUSE (REF: 1901) Au cours de l'exécution. Le pas de filet programmé dans la fonction G33 est trop élevé. Réviser la programmation. 'Type de cinématique inconnue' DÉTECTION CAUSE CNC 8070 Au cours de l'exécution. Dans la fonction G33, le pas de filet a valeur 0. Réviser la programmation. Programmer le pas de filet avec les paramètres I J K. 'Pas de vis hors de rang' DÉTECTION CAUSE SOLUTION 1261 Au cours de l'exécution. Dans la fonction G33, le pas de filet est programmé plus d'une fois. Réviser la programmation. Définir le pas du filet une seule fois dans le bloc. 'Pas de vis égal à zéro' DÉTECTION CAUSE SOLUTION 1259 Au cours de l'exécution. Le pourcentage d’accélération programmé dans la fonction G130 est trop élevé. Réviser la programmation. 'Double programmation du pas de vis' DÉTECTION CAUSE SOLUTION 1258 Au cours de l'exécution. Le pourcentage d’accélération programmé dans la fonction G130 est négatif. Le pourcentage d'accélération doit être supérieur ou égal à zéro. 'Pourcentage d'accélération hors de rang' DÉTECTION CAUSE SOLUTION 1257 Au cours de l'exécution. La CNC ne permet pas de programmer les fonctions M19 (positionnement de la broche) et G192 (limitation de la vitesse de rotation) dans le même bloc. Programmer les deux instructions dans des blocs différents. 'Pourcentage d'accélération négatif' DÉTECTION CAUSE SOLUTION 1256 Au cours de l'exécution. La CNC a essayé d'éliminer l'axe frontal de la configuration du canal (#FREE AX) avec la fonction G96 active. Désactiver la fonction G96 pour supprimer l’axe frontal de la configuration du canal. 'G192 et M19 ne sont pas admises dans le même bloc' DÉTECTION CAUSE 1255 Au cours de l'exécution. La CNC a essayé d'accéder au mode manuel avec la fonction G96 active. Désactiver l fonction G96 pour accéder au mode manuel. '#FREE AX: il est impossible d'éliminer l'axe de rotation frontal avec G96 active' DÉTECTION CAUSE 1254 Au cours de l'exécution. La CNC a essayé de changer la gamme de la broche (G112) avec la fonction G96 active. Désactiver la fonction G96 pour exécuter le changement de gamme de la broche. SOLUTION Au cours de l'exécution. Le canal n’a pas suffisamment d’axes pour activer la fonction RTCP, TLC ou la transformation de coordonnées. Le nombre d'axes nécessaire dépendra de la cinématique à activer. Corriger la configuration d’axes du canal (instruction #SET AX) pour pouvoir activer la cinématique. S o l ut i o n s d ’ e r r e ur s . 1263 'Axe(s) rotatif(s) manquant(s) pour la transformation' DÉTECTION CAUSE SOLUTION 1264 'Programmation non autorisée avec CS/ACS actif' DÉTECTION CAUSE SOLUTION 1265 SOLUTION SOLUTION SOLUTION Au cours de l'exécution. La CNC n’a pas pu résoudre une transformation de coordonnées pièce à coordonnées machine ou vice-versa. Désactiver la transformation, changer la position des axes et activer de nouveau la transformation. 'Les axes de la cinématique active ne peuvent pas être exclus ou modifiés' DÉTECTION CAUSE SOLUTION 1272 Au cours de l'exécution. L'angle programmé n'est pas valide. Programmer un angle entre ±360º. 'Calcul de la transformation de coordonnées impossible' DÉTECTION CAUSE 1271 Au cours de l'exécution. La syntaxe de l'instruction n'est pas correcte. Réviser la programmation. '#CS ON/#ACS ON: l'angle programmé n'est pas valide' DÉTECTION CAUSE SOLUTION 1270 Au cours de l'exécution. Avec la fonction RTCP active, il y a une instruction programmée #RTCP différente de #RTCP OFF. Pour désactiver la fonction RTCP, programmer #RTCP OFF. Pour modifier les valeurs de la fonction RTCP, il faut d’abord la désactiver. '#CS ON/#ACS ON: erreur de syntaxe' DÉTECTION CAUSE SOLUTION 1269 Au cours de l'exécution. La CNC a essayé de modifier la fonction TLC pendant qu'elle est active. La CNC ne permet pas de modifier la fonction TLC pendant qu'elle est active. Pour modifier la fonction TLC, il faut la désactiver et l'activer de nouveau. 'La fonctionnalité RTCP se désactive avec l'instruction #RTCP OFF' DÉTECTION CAUSE 1268 Au cours de l'exécution. La CNC ne permet pas d’exécuter la fonction programmée si la fonction RTCP ou TLC est active. Certaines fonctions incompatibles sont G74, G198, G199, #KIN ID. LINK. Désactiver la fonction RTCP ou TLC pour pouvoir exécuter les autres fonctions. 'La fonctionnalité TLC se désactive avec l'instruction #TLC OFF' DÉTECTION CAUSE SOLUTION 1267 Au cours de l'exécution. La CNC ne permet pas d’exécuter la fonction programmée si la transformation de coordonnées est active. Certaines fonctions incompatibles sont G74, G198, G199, #LINK, cycles de palpage, etc. Désactiver la transformation de coordonnées pour pouvoir exécuter les autres fonctions. 'Programmation non autorisée avec RTCP/TLC actif' DÉTECTION CAUSE 1266 Au cours de l'exécution. Une instruction #TOOL ORI est programmée mais il n’y a aucun axe rotatif pour pouvoir placer l’outil perpendiculaire au plan incliné défini. Ne pas programmer l'instruction #TOOL ORI ou activer une cinématique permettant de placer l’outil perpendiculairement au plan incliné. Au cours de l'exécution. La CNC a essayé de modifier la configuration d’axes de la cinématique pendant qu'elle est active. Désactiver la cinématique pour modifier la configuration d’axes du canal. CNC 8070 'Les axes de la transformation active ne peuvent pas être exclus ou modifiés' DÉTECTION CAUSE SOLUTION Au cours de l'exécution. La CNC a essayé de modifier la configuration d’axes d’un plan incliné alors que celuici était actif. Désactiver la transformation de plan incliné pour modifier la configuration d’axes du canal. (REF: 1901) ·43· S o l ut i o n s d ’ e r r e ur s . 1275 'Position calculée par la transformation cinématique inverse hors de rang' DÉTECTION CAUSE SOLUTION 1277 'Le décalage programmé excède le rang de données' DÉTECTION CAUSE SOLUTION 1278 SOLUTION SOLUTION SOLUTION SOLUTION CNC 8070 (REF: 1901) Au cours de l'exécution. La longueur de l’outil est programmée plus d’une fois dans le bloc. Programmer la longueur de l'outil une seule fois dans le bloc. 'On attend "["' DÉTECTION CAUSE SOLUTION ·44· Au cours de l'exécution. Le rayon de l’outil est programmé plus d’une fois dans le bloc. Programmer le rayon de l'outil une seule fois dans le bloc. 'Double écriture de la longueur d'outil' DÉTECTION CAUSE SOLUTION 1287 Au cours de l'exécution. Dans l'instruction #MSG, #ERROR ou #WARNING il y a d'identificateurs de données programmés (%D ou %d) mais il manque des paramètres à afficher. Réviser la programmation. 'Double écriture du rayon d'outil' DÉTECTION CAUSE SOLUTION 1286 Au cours de l'exécution. Dans l'instruction #MSG, #ERROR ou #WARNING, il y a plus de 5 identificateurs de données (%D ou %d). Réduire le numéro d'identificateurs de données. 'On attend l'expression arithmétique' DÉTECTION CAUSE 1285 Au cours de l'exécution. Dans l'instruction #MSG, #ERROR ou #WARNING, le texte du message est trop long. Le nombre maximum de caractères permis est 69, y compris les caractères remplaçant les identificateurs de données. 'Limite de spécificateurs de format dépassée' DÉTECTION CAUSE 1284 Au cours de l'exécution. Le nombre d’identificateurs de données (%D ou %d) indiqués dans l'instruction #MSG, #ERREUR ou #WARNING ne coïncide avec le nombre de paramètres à afficher. Réviser la programmation. 'Message trop long' DÉTECTION CAUSE SOLUTION 1283 Au cours de l'exécution. Dans l'expression ou l'instruction programmée il manque les guillemets. Réviser la programmation. 'Le nombre de paramètres et de spécificateurs de format ne coïncident pas' DÉTECTION CAUSE 1282 Au cours de l'exécution. Dans la fonction G131 ou G133, le pourcentage d’accélération ou de jerk programmé n’est pas valide. Programmer un pourcentage d’accélération ou jerk positif et inférieur ou égal à 100. 'On attend "' DÉTECTION CAUSE SOLUTION 1281 Au cours de l'exécution. Le décalage calculé à partir des cotes programmées dans la fonction G92 est trop grand. Réviser la programmation. 'G131/G133: valeur non valable' DÉTECTION CAUSE 1279 Au cours de l'exécution. La CNC a essayé de faire une transformation non résolue de coordonnées machine à coordonnées pièce. Désactiver la transformation, changer la position à laquelle on veut accéder activer de nouveau la transformation. Vérifier la transformée en cas de transformation d’utilisateur. Au cours de l'exécution. Il manque le crochet d’ouverture "[" dans l’expression ou l'instruction programmée. Réviser la programmation. S o l ut i o n s d ’ e r r e ur s . 1288 'Trop de paramètres programmés dans l'instruction. DÉTECTION CAUSE SOLUTION 1290 'Programmation de coordonnées I, J, K incorrecte' DÉTECTION CAUSE SOLUTION 1291 Au cours de l'exécution. Caractère non valide dans le nom de l'étiquette, sous-routine ou variable. Réviser la programmation. 'Nom de variable trop long' DÉTECTION CAUSE SOLUTION 1304 Au cours de l'exécution. La transformation de longueur d'outil excède le format numérique valide. Modifier les valeurs de la transformation de longueur ou de l'outil. 'Caractère non valide dans le nom' DÉTECTION CAUSE SOLUTION 1303 Au cours de l'exécution. La même fonction H est programmée plus d’une fois dans le bloc. Programmer les deux fonctions dans des blocs différents. 'La transformation de longueur d'outil excède le format numérique valide' DÉTECTION CAUSE SOLUTION 1302 Au cours de l'exécution. La même fonction F est programmée plus d’une fois dans le bloc. Programmer les deux fonctions dans des blocs différents. 'Fonction H programmée en double' DÉTECTION CAUSE SOLUTION 1301 Au cours de l'exécution. Il y a plus de fonctions S que celles permises dans un même bloc. Le nombre maximum de fonctions S permis dans un même bloc est 4. 'Fonction M programmée en double' DÉTECTION CAUSE SOLUTION 1293 Au cours de l'exécution. Les possibles causes sont les suivantes: • Les valeurs programmées pour le centre d’une interpolation circulaire, origine polaire ou centre de rotation du système de coordonnées sont trop élevées. • Les valeurs programmées pour le centre d’une interpolation circulaire, avec la fonction G264 active sont incorrectes. Réviser la programmation. 'On n'admet pas d'autres fonctions S' DÉTECTION CAUSE SOLUTION 1292 Au cours de l'exécution. La syntaxe de l'instruction n'est pas correcte. Réviser la programmation. Au cours de l'exécution. Nombre maximum de caractères permis pour le nom de la variable dépassé. Le nombre maximum de caractères permis est 13. 'Vitesse de broche non valide' DÉTECTION CAUSE SOLUTION Au cours de l'exécution. La vitesse programmée est trop petite. Réviser la programmation. CNC 8070 (REF: 1901) ·45· S o l ut i o n s d ’ e r r e ur s . 1305 'Programmation non autorisée avec #MCS actif' DÉTECTION CAUSE SOLUTION 1306 'Le changement de cinématique avec compensation de rayon active n'est pas admis' DÉTECTION CAUSE SOLUTION 1308 SOLUTION 1315 ·46· Au cours de l'exécution. Dans ces instructions, le numéro du système de coordonnées n'est pas valide. Programmer une valeur entre 1 et 5. '#CS ON/#ACS ON: système non défini' DÉTECTION CAUSE SOLUTION (REF: 1901) Au cours de l'exécution. La fonction G102 essaie d’exclure l’offset de mesure d’un axe qui n’a inclus aucun offset de mesure. La fonction G102 n'a pas de sens pour un axe sans offset de mesure. '#CS ON/#ACS ON: identificateur non valable' DÉTECTION CAUSE SOLUTION CNC 8070 Au cours de l'exécution. Le nombre de caractères de l'instruction #EXBLK dépasse le maximum permis. Le nombre maximum de caractères permis est 128. 'Offset de mesure non inclus sur l'axe(s) programmés' DÉTECTION CAUSE 1314 Au cours de l'exécution. Il n'y à aucun programme sélectionné pour l'exécution. Sélectionner le programme à exécuter. 'Ligne de programme trop longue' DÉTECTION CAUSE SOLUTION 1311 Au cours de l'exécution. L'axe esclave d'un couplage fait partie de la cinématique active. Désactiver la cinématique pour accoupler l'axe. L’axe participant à la cinématique active peut être l’axe maître d’un couplage. 'On attend nom de fichier' DÉTECTION CAUSE SOLUTION 1310 Au cours de l'exécution. La CNC a essayé de changer la cinématique avec la compensation de rayon active. Annuler la compensation pour définir le nouveau plan de travail. 'Un axe de la transformation cinématique active ne peut pas être esclave' DÉTECTION CAUSE SOLUTION 1309 Au cours de l'exécution. La CNC ne permet pas d’exécuter la fonction programmée si la fonction MCS est active. Certaines fonctions incompatibles sont: • Activation / désactivation des décalages d'origine (G54-G59, G159, G92, G158, G53). • Activation / désactivation de l'offset de mesure (G101, G102). • Activation / désactivation de mors (variable "V.G.FIX"). • Activation / désactivation de l'image miroir (G11/G12/G13/G14). • Programmation en rayons / diamètres (G151/G152). • Activation de la programmation incrémentale (G91). • Programmation en millimètres / pouces (G70/G71). • Facteur d'échelle (G72). • Déplacement sur G0, G1, G2, G3, G8 ou G9 en polaires. • Filetage G63 ou G33 en polaires. • Origine polaire (G30). • Rotation du système (G73). • Instructions #FACE, #CYL et #RTCP. Réviser la programmation. Au cours de l'exécution. Les instructions n’ont pas de paramètres et aucun système de coordonnées n’est emmagasiné. En programmant l'une de ces instructions sans paramètres, la CNC essaie d’activer la dernière transformation emmagasinée. Réviser la programmation. Définir et emmagasiner le système de coordonnées. S o l ut i o n s d ’ e r r e ur s . 1316 '#CS/#ACS DEF: paramètres manquants' DÉTECTION CAUSE SOLUTION 1318 '#CS ON/#ACS ON: changements non admis avec le système de coordonnées actif. DÉTECTION CAUSE SOLUTION 1319 SOLUTION SOLUTION SOLUTION Au cours de l'exécution. L’étiquette de bloc définie dans l’instruction $GOTO ou #RPT n’existe pas dans le programme. Définir l'étiquette de saut sur un point du programme. 'Numéro de bloc défini plusieurs fois' DÉTECTION CAUSE SOLUTION 1326 Au cours de l'exécution. Une étiquette ne peut être définie qu’avec une chaîne de caractères entre crochets ou avec le caractère "N" suivi d’un nombre positif et inférieur à 2147483646. Réviser la programmation. 'Étiquette non définie' DÉTECTION CAUSE 1325 Au cours de l'exécution. L'étiquette du bloc est répétée dans le programme. Éliminer les étiquettes répétées. '$GOTO: Étiquette non valide' DÉTECTION CAUSE 1324 Au cours de l'exécution. Le nom de l’étiquette dépasse le nombre de caractères permis. Le nombre maximum de caractères permis est 15. 'Étiquette définie plusieurs fois' DÉTECTION CAUSE SOLUTION 1323 Au cours de l'exécution. Le programme a plus d’étiquettes de bloc que celles permises. Les étiquettes pour identifier un bloc peuvent être du type Le nombre maximum d’étiquettes permises de chaque type est 128. Les étiquettes peuvent être représentées avec la lettre N suivie du numéro de bloc ou avec des étiquettes du type [nom]. 'Nom d'étiquette trop long' DÉTECTION CAUSE SOLUTION 1322 Au cours de l'exécution. La CNC a dépassé la limite de combinaisons de systèmes de coordonnées. La CNC permet de combiner différents systèmes de coordonnées entre eux pour en construire de nouveaux. La CNC permet de combiner 10 systèmes de coordonnées. 'Nombre maximum d'étiquettes dépassé' DÉTECTION CAUSE 1321 Au cours de l'exécution. La CNC a essayé de changer les paramètres d'un système de coordonnées actif. Réviser la programmation. La CNC ne permet pas de modifier les paramètres d’un système de coordonnées actif mais elle permet de modifier les paramètres d’un système de coordonnées déjà défini mais non actif. 'Excès d'emboîtement des instructions #CS ON/#ACS ON' DÉTECTION CAUSE SOLUTION 1320 Au cours de l'exécution. Il faut programmer un ou plusieurs paramètres obligatoires. Réviser la programmation. Ces instructions exigent de programmer le numéro du système de coordonnées, le mode de définition, les composants du vecteur de translation et les angles de rotation. Au cours de l'exécution. Le numéro de bloc "N" est répété dans le programme. Ne pas répéter le numéro de bloc. CNC 8070 'Valeur erronée pour affecter une variable' DÉTECTION CAUSE SOLUTION Au cours de l'exécution. La variable a une valeur trop haute. Réviser la programmation. (REF: 1901) ·47· S o l ut i o n s d ’ e r r e ur s . 1327 'Vitesse de positionnement de broche programmée en double' DÉTECTION CAUSE SOLUTION 1328 'Instruction $FOR sans $ENDFOR' DÉTECTION CAUSE SOLUTION 1330 SOLUTION SOLUTION 1340 ·48· Au cours de l'exécution. L'instruction programmée n’a pas d’effet car elle est déjà active ; la même instruction avec les mêmes paramètres est programmée dans un bloc antérieur. Réviser la programmation. 'La désélection n'a pas d'effet' DÉTECTION CAUSE (REF: 1901) Au cours de l'exécution. Aucun des axes programmés dans l'instruction #FACE/#CYL est axe C. L’un des deux axes programmés doit être axe C (paramètre CAXIS). 'La sélection n'a pas d'effet' DÉTECTION CAUSE CNC 8070 Au cours de l'exécution. Les deux axes programmés dans l'instruction #FACE/#CYL sont axe C. Seul l'un des deux axes programmés peut être axe C (paramètre CAXIS). 'L'axe CAXIS n'a pas été défini' DÉTECTION CAUSE SOLUTION 1339 Au cours de l'exécution. Un déplacement d’axes est programmé dans le même bloc que la fonction G200. Réviser la programmation. 'Configuration erronée: deux axes CAXIS' DÉTECTION CAUSE SOLUTION 1337 Au cours de l'exécution. Avec la compensation de rayon active, la CNC a essayé de modifier la configuration d’axes du canal et la modification affecte les deux premiers axes du plan de travail. Désactiver la compensation de rayon pour réaliser des changements dans la configuration des axes du canal qui affectent le plan de travail. 'G200: n'admet le déplacement dans le même bloc' DÉTECTION CAUSE SOLUTION 1336 Au cours de l'exécution. Il manque la programmation de l'orientation de l'outil. Réviser la programmation. 'Changement du premier et/ou deuxième axe du plan avec compensation de rayon active' DÉTECTION CAUSE 1334 Au cours de l'exécution. Le rayon programmé est inférieur ou égal à zéro. Réviser la programmation. '#TOOL AX: on attend orientation +/- après la désignation de l'axe' DÉTECTION CAUSE SOLUTION 1333 Au cours de l'exécution. Programmation incorrecte de la fonction G14 (image miroir). Réviser la programmation. '#TANGFEED RMIN: rayon négatif interdit' DÉTECTION CAUSE SOLUTION 1332 Au cours de l'exécution. Une instruction $FOR est programmée mais il manque son $ENDFOR. Réviser la programmation. 'Programmation d'image miroir incorrecte' DÉTECTION CAUSE SOLUTION 1331 Au cours de l'exécution. La vitesse de positionnement de la broche (M19) a été programmée plus d’une fois dans le bloc. Réviser la programmation. Programmer la vitesse de positionnement une seule fois dans le bloc. SOLUTION Au cours de l'exécution. La CNC a essayé d’exécuter l'instruction #CAX OFF et aucune broche ne travaille comme axe C. Réviser la programmation. S o l ut i o n s d ’ e r r e ur s . 1342 '#CAX OFF non admise si une transformation est active' DÉTECTION CAUSE SOLUTION 1343 '#FACE OFF non admise avec le type de cinématique active' DÉTECTION CAUSE SOLUTION 1344 SOLUTION SOLUTION SOLUTION SOLUTION SOLUTION SOLUTION Au cours de l'exécution. Un caractère non valide est programmé dans l'un des blocs compris entre ces instructions. Entre ces instructions, seule est admise la déclaration de variables d’utilisateur (séparées par des virgules s’il y en a plusieurs sur une même ligne) ou la programmation du numéro de bloc. '#VAR/#ENDVAR/#DELETE: type de variable interdite' DÉTECTION CAUSE SOLUTION 1352 Au cours de l'exécution. L’axe linéaire faisant partie de la transformation d’axe C frontal est positionné sur la partie négative, par rapport au centre de rotation. La CNC ne permet pas cette option (paramètre ALINGC). Positionner l’axe sur la partie positive, par rapport au centre de rotation avant d’activer l’usinage sur l’axe frontal. 'Caractère non valide entre les instructions #VAR/#ENDVAR' DÉTECTION CAUSE 1351 Au cours de l'exécution. Le rayon programmé dans l'instruction #CYL est négatif ou zéro. Si le rayon est variable, il essaie de passer par le centre du cylindre en générant un rayon nul. Réviser la programmation. Le rayon doit être positif et s’il s'agit d’un rayon variable, il ne peut pas passer par le centre du cylindre. 'Cote négative de l'axe dans l'activation #FACE' DÉTECTION CAUSE 1350 Au cours de l'exécution. La CNC a essayé d’exécuter l'instruction #CYL OFF et aucun usinage n’est actif sur la surface cylindrique. Réviser la programmation. '#CYL: rayon non valide' DÉTECTION CAUSE 1349 Au cours de l'exécution. Dans la fonction G20 (changement de plan), les deux premiers axes du plan (paramètres 1 et 2) sont incorrects. Les deux axes doivent être différents et parmi les trois premiers axes du canal. '#CYL OFF non admise avec le type de cinématique active' DÉTECTION CAUSE 1348 Au cours de l'exécution. La CNC a essayé de changer le plan de travail (G17-G20) alors que l’usinage sur la surface latérale est actif. Réviser la programmation. 'G20: programmation incorrecte d'axes' DÉTECTION CAUSE 1347 Au cours de l'exécution. La CNC a essayé d’exécuter l'instruction #FACE OFF et aucun usinage n’est actif sur la surface frontale. Réviser la programmation. 'Pas de changement de plan admis pendant l'usinage en surface latérale' DÉTECTION CAUSE 1345 Au cours de l'exécution. La CNC ne permet pas de désactiver l’axe C avec la fonction RTCP ou TLC active. Réviser la programmation. Au cours de l'exécution. La CNC a essayé de définir ou de supprimer une variable qui n’est pas d’utilisateur. Réviser la programmation. CNC 8070 '#VAR/#ENDVAR: la variable définie existe déjà' DÉTECTION CAUSE SOLUTION Au cours de l'exécution. La variable d'utilisateur existe déjà. Réviser la programmation. (REF: 1901) ·49· S o l ut i o n s d ’ e r r e ur s . 1353 'Trop de valeurs pour initialiser l'array' DÉTECTION CAUSE SOLUTION 1354 'Erreur dans la lecture de la variable' DÉTECTION CAUSE SOLUTION 1355 SOLUTION CNC 8070 ·50· Au cours de l'exécution. La variable d’utilisateur est un array multidimensionnel avec plus de 4 dimensions. Réviser la programmation. 'Vitesse de la broche négative non admise' DÉTECTION CAUSE SOLUTION (REF: 1901) Au cours de l'exécution. Les variables d’utilisateur qui sont array doivent être déclarées entre les instructions #VAR et #ENDVAR. Réviser la programmation. 'Trop d'indices de variable d'array' DÉTECTION CAUSE SOLUTION 1365 Au cours de l'exécution. La variable est d’array mais le nombre d’arrays programmés est incorrect. Vérifier la syntaxe de la variable. 'Déclaration incorrecte de variables d'array' DÉTECTION CAUSE 1364 Au cours de l'exécution. La CNC a essayé d’exécuter une fonction G33/G63/G95/G96/G97 avec l’axe C actif. Désactiver l'axe C pour exécuter la fonction. 'Dimension d'array incorrecte' DÉTECTION CAUSE SOLUTION 1363 Au cours de l'exécution. La variable d'utilisateur n'existe pas. Réviser la programmation. 'G33/G63/G95/G96/G97 non admises avec axe C actif' DÉTECTION CAUSE SOLUTION 1362 Au cours de l'exécution. Détection de caractère non valide dans le bloc. Vérifier la syntaxe du bloc. L'instruction doit être programmée seule dans le bloc ou avec l’étiquette du bloc. Cette instruction ne permet que des variables d'utilisateur. '#DELETE: la variable à effacer n'existe pas' DÉTECTION CAUSE SOLUTION 1360 Au cours de l'exécution. Programmation incorrecte de l'instruction $IF EXIST. L’instruction $IF EXIST ne permet que des paramètres arithmétiques ou des variables. '#DELETE: caractère non valide' DÉTECTION CAUSE SOLUTION 1358 Au cours de l'exécution. La CNC a essayé de supprimer une variable du système. La CNC ne peut supprimer que des variables d’utilisateur (préfixes P et S). 'On attend une variable ou un paramètre' DÉTECTION CAUSE SOLUTION 1357 Au cours de l'exécution. La CNC ne peut pas lire la variable. Réviser la programmation. 'Il est impossible d'effacer la variable' DÉTECTION CAUSE SOLUTION 1356 Au cours de l'exécution. Dans l’initialisation d’une variable d’array d’utilisateur, la CNC initialise plus de positions que celles disponibles. Réviser la programmation. Au cours de l'exécution. Vitesse de la broche négative. La vitesse de broche doit être positive ; la valeur négative n’est permise que si elle est programmée dans le même bloc que la fonction G63. S o l ut i o n s d ’ e r r e ur s . 1367 'Il est impossible de changer de gamme et déplacer la broche simultanément' DÉTECTION CAUSE SOLUTION 1368 'Il est impossible de programmer le centre et le rayon du cercle simultanément' DÉTECTION CAUSE SOLUTION 1369 SOLUTION SOLUTION Au cours de l'exécution. Il faut programmer M17, M29 ou #RET à la fin de la sous-routine. Réviser la programmation. 'Le nom par défaut pour l'axe C n'a pas été défini' DÉTECTION CAUSE SOLUTION 1377 Au cours de l'exécution. Il faut programmer M02 ou M30 à la fin du programme principal. Réviser la programmation. 'On attend M17/M29/#RET' DÉTECTION CAUSE SOLUTION 1376 Au cours de l'exécution. Le paramètre FAST ou le paramètre CORNER de l'instruction #HSC ont une valeur incorrecte. Réviser la programmation. 'On attend M02/M30' DÉTECTION CAUSE SOLUTION 1375 Au cours de l'exécution. La CNC a essayé d’activer le mode HSC avec un paramètre inconnu ou a essayé de changer le mode de travail sans le désactiver auparavant. Réviser la programmation. '#HSC: paramètre incorrect' DÉTECTION CAUSE 1374 Au cours de l'exécution. L’activation et la désactivation du mode HSC sont programmées dans un même bloc. Vérifier dans le manuel de programmation la syntaxe des instructions. '#HSC: mode non valide' DÉTECTION CAUSE 1373 Au cours de l'exécution. La syntaxe de l'instruction n'est pas correcte. Réviser la programmation. '#HSC: double programmation' DÉTECTION CAUSE SOLUTION 1371 Au cours de l'exécution. L’interpolation circulaire est définie avec le rayon et le centre. Dans une interpolation circulaire il faut programmer les cotes du point final ainsi que le rayon ou le centre du cercle. '#HSC: programmation interdite' DÉTECTION CAUSE SOLUTION 1370 Au cours de l'exécution. Une fonction M de déplacement de broche et la fonction G112 de modification du set de paramètres ont été programmées dans le même bloc. Réviser la programmation. Au cours de l'exécution. Le nom de l’axe C n’est pas indiqué dans l'instruction #CAX et le nom par défaut (paramètre CAXIS) n’est pas indiqué dans les paramètres machine. Indiquer dans l'instruction #CAX le nom identifiant l’axe C. 'Écriture de paramètre avec indice non valide' DÉTECTION CAUSE SOLUTION Au cours de l'exécution. Le paramètre arithmétique n’existe pas ou est protégé contre l’écriture. Réviser la programmation. Réviser dans les paramètres machine la gamme de paramètres arithmétiques valable. Paramètres machine. Rang valable. MINLOCP - MAXLOCP Paramètres arithmétiques locaux. MINGLBP - MAXGLBP Paramètres arithmétiques globaux. MINCOMP - MAXCOMP Paramètres arithmétiques communs. CNC 8070 (REF: 1901) Les paramètres globaux protégés contre l’écriture sont ceux définis par les paramètres machine ROPARMIN - ROPARMAX. ·51· S o l ut i o n s d ’ e r r e ur s . 1378 'Lecture de paramètre avec indice non valide' DÉTECTION CAUSE SOLUTION 1380 SOLUTION SOLUTION SOLUTION CNC 8070 SOLUTION (REF: 1901) ·52· MINCOMP - MAXCOMP Paramètres arithmétiques communs. Au cours de l'exécution. Dans le bloc de définition d’un cycle fixe, on ne peut rien programmer après les paramètres du cycle. Réviser la programmation. Au cours de l'exécution. Le cycle fixe programmé n'existe pas' Réviser la programmation. Au cours de l'exécution. L'un des paramètres programmés n’est pas permis pour ce cycle fixe. Vérifier dans le manuel de programmation les paramètres obligatoires et permis pour chaque cycle fixe. Au cours de l'exécution. Il faut programmer un paramètre obligatoire du cycle fixe. Vérifier dans le manuel de programmation les paramètres obligatoires et permis pour chaque cycle fixe. Au cours de l'exécution. Un déplacement et une fonction M avec sous-routine associée et exécution avant le déplacement ont été programmés dans le même bloc. Les sous-routines sont toujours exécutées à la fin du bloc et par conséquent la fonction M ne sera jamais exécutée avant le déplacement programmé. Programmer la fonction M dans un autre bloc ou définir la fonction M dans les paramètres machine avec exécution après le déplacement. Au cours de l'exécution. La CNC a essayé d’écrire la variable "V.G.TOL" dans le même bloc où a été programmé un changement d’outil ou de correcteur. Réviser la programmation. 'D et les offsets de l'outil ne peuvent pas être modifiés dans le même bloc' DÉTECTION CAUSE 1387 Paramètres arithmétiques globaux. 'D et la longueur de l'outil ne peuvent pas être modifiées dans le même bloc' DÉTECTION CAUSE 1386 MINGLBP - MAXGLBP 'Fonction M interdite avec déplacement' DÉTECTION CAUSE 1385 Paramètres arithmétiques locaux. 'Un paramètre obligatoire n’a pas été programmé dans le cycle fixe' DÉTECTION CAUSE SOLUTION 1384 MINLOCP - MAXLOCP 'Paramètre interdit en cycle fixe' DÉTECTION CAUSE SOLUTION 1383 Rang valable. 'Cycle fixe inexistant' DÉTECTION CAUSE SOLUTION 1382 Paramètres machine. 'Cycle fixe mal programmé' DÉTECTION CAUSE 1381 Au cours de l'exécution. Le paramètre arithmétique n’existe pas ; il n’est pas dans la gamme permise par les paramètres machine. Réviser la programmation. Réviser dans les paramètres machine la gamme de paramètres arithmétiques valable. Au cours de l'exécution. La CNC a essayé d’écrire la variable "V.G.TOFL.xn" dans le même bloc où a été programmé un changement d’outil ou de correcteur. Réviser la programmation. 'Limite de fonctions M dans un même bloc dépassée' DÉTECTION CAUSE SOLUTION Au cours de l'exécution. Il y a plus de fonctions M que celles permises dans un même bloc. A partir de la version V2.00, la CNC permet jusqu’à 14 fonctions M par bloc ; dans des versions antérieures, la limite était de 7 fonctions par bloc. S o l ut i o n s d ’ e r r e ur s . 1388 'On n'admet pas d'autres fonctions H' DÉTECTION CAUSE SOLUTION 1389 'Fonctions G incompatibles (G10/G11/G12/G13/G14)' DÉTECTION CAUSE SOLUTION 1390 SOLUTION SOLUTION SOLUTION Au cours de l'exécution. Il n'est pas permis d'exécuter cet ordre dans MDI. Exécuter cet ordre dans un programme. 'La position programmée pour l'axe Hirth est incorrecte' DÉTECTION CAUSE SOLUTION 1398 Au cours de l'exécution. Si la fonction G74 a une sous-routine associée, elle doit être programmée seule dans le bloc ou avec l’étiquette du bloc. Réviser la programmation. 'Programmation non autorisée dans MDI' DÉTECTION CAUSE SOLUTION 1397 Au cours de l'exécution. Une fonction G180 à G189 est programmée et la sous-routine associée n’existe pas. Une fonction G74 est programmée seule dans le bloc et la sous-routine associée n’existe pas. Programmer avec la fonction G74 les axes à référencer ou définir la sous-routine associée (paramètre REFPSUB). Pour les fonctions G180 à G189, définir la sousroutine associée (paramètre OEMSUB). 'La fonction G74 avec sous-routine associée est programmée seule dans le bloc' DÉTECTION CAUSE 1396 Au cours de la recherche de bloc. Après une inspection d’outil, le correcteur D actif ne coïncide pas avec le correcteur D programmé avant d’arrêter l’exécution. La CNC a les blocs de déplacement préparés pour usiner la pièce après le repositionnement, avec le rayon de l’outil programmé. Si l’outil sur la broche est différent et si dans le programme le rayon de l’outil n'est pas compensé, la CNC usinera une pièce différente. Changer l’outil de la broche pour qu’elle coïncide avec l’outil programmé. 'La sous-routine associée à la fonction G n'existe pas' DÉTECTION CAUSE 1395 Au cours de l'exécution. Le même paramètre est programmé plus d’une fois dans l'instruction ou la fonction. Réviser la programmation. 'L'outil et le correcteur actuels ne coïncident pas avec ceux programmés' DÉTECTION CAUSE 1394 Au cours de l'exécution. Dans le bloc il y a des fonctions G programmées contraires entre elles. Programmer les fonctions dans des blocs différents. 'Paramètre programmé en double' DÉTECTION CAUSE SOLUTION 1393 Au cours de l'exécution. Dans le bloc il y a des fonctions G programmées contraires entre elles. Programmer les fonctions dans des blocs différents. 'Fonctions G incompatibles (G98/G99)' DÉTECTION CAUSE SOLUTION 1392 Au cours de l'exécution. Il y a plus de fonctions H que celles permises dans un même bloc. Le nombre maximum de fonctions H admis dans un même bloc est 7. Au cours de l'exécution. La cote programmée pour l’axe Hirth ne correspond pas à un pas entier. L'axe hirth n'admet que des cotes multiple de son pas. 'Un axe avec le paramètre HIRTH = NON ne peut pas être activé comme Hirth' DÉTECTION CAUSE SOLUTION Au cours de l'exécution. La CNC a essayé d’activer (G171) ou de désactiver (G170) comme axe hirth un axe qui ne l’est pas (paramètre HIRTH). Réviser la programmation. L'axe ne peut pas être activé comme axe hirth. CNC 8070 (REF: 1901) ·53· S o l ut i o n s d ’ e r r e ur s . 1399 'L'axe ne peut pas être activé comme Hirth' DÉTECTION CAUSE SOLUTION 1400 'Pas de changement de longueur d'outil admis avec RTCP actif' DÉTECTION CAUSE SOLUTION 1401 SOLUTION SOLUTION SOLUTION 1407 Au cours de l'exécution. L'instruction #CALL n’admet pas de programmation de paramètres. Réviser la programmation. 'Erreur dans la lecture de données de la poche' DÉTECTION CAUSE (REF: 1901) SOLUTION ·54· Au cours de l'exécution. La broche a un changement de gamme automatique (paramètre AUTOGEAR) et la vitesse programmée est supérieure à la maximale de n’importe quelle des gammes existant pour cette broche. Programmer une vitesse de broche inférieure, qui puisse être atteinte avec une des gammes existantes pour cette broche. Vérifier que la vitesse maximale définie dans chaque gamme est correcte. '#CALL: n'admet pas de programmation de paramètres' DÉTECTION CAUSE SOLUTION CNC 8070 Au cours de l'exécution. La CNC a essayé de réaliser un changement de gamme de broche, avec une fonction M41 à M44 et la gamme n’existe pas. Le nombre de gammes disponibles dans la broche est défini dans les paramètres machine (paramètre NPARSETS). La CNC n’acceptera que les fonctions M41 à M44 des gammes de broche existantes. 'La valeur de la S dépasse la gamme maximale' DÉTECTION CAUSE 1406 Au cours de l'exécution. La CNC a essayé d'accoupler deux axes hirth mais l’un d’eux est désactivé' Pour pouvoir accoupler deux axes hirth, les deux axes doivent être actifs (G171). 'La gamme associée à M programmée n'existe pas' DÉTECTION CAUSE 1405 Au cours de l'exécution. La CNC a essayé d'accoupler deux axes hirth mais l’un d’eux n’est pas hirth ou les deux axes ont un pas différent. Pour pouvoir inclure un axe hirth dans un couplage, les deux axes doivent être hirth (paramètre HIRTH) et avoir le même pas (paramètre HPITCH). '#LINK: il est impossible de définir un couplage avec un axe Hirth désactivé' DÉTECTION CAUSE SOLUTION 1404 Au cours de l'exécution. La CNC a essayé d’activer la fonction TLC et celle-ci est déjà active. Réviser la programmation. '#LINK: les axes maître et esclave doivent avoir les mêmes paramètres HIRTH et HPITCH' DÉTECTION CAUSE 1403 Au cours de l'exécution. La CNC a essayé de faire un changement d’outil avec la fonction RTCP active. Désactiver la fonction RTCP pour faire le changement d’outil. '#TLC ON non admise sans désélection préalable' DÉTECTION CAUSE SOLUTION 1402 Au cours de l'exécution. Les possibles causes sont les suivantes: • L’axe hirth est un des axes du plan et la compensation de rayon et/ou la détection de collisions est active. • L’axe hirth fait partie de la transformation de coordonnées active. • L’axe hirth fait partie de la cinématique active et il y aussi une instruction #RTCP, #TLC ou #TOOL ORI active. Réviser la programmation. Au cours de l'exécution. En exécutant une poche 2D ou 3D, la CNC n’a pas pu décoder une des données. Cela peut se produire lorsque les données de la poche ont été éditées manuellement et une valeur numérique a été remplacée par une variable ou si le crochet final des instructions #DATAP2D, #DATAP3D a été supprimé, etc. Éditer à nouveau la poche avec l'éditeur de cycles. S o l ut i o n s d ’ e r r e ur s . 1408 'Programmation interdite sans broche commandée en position' DÉTECTION CAUSE SOLUTION 1409 'Emboîtement de fonctions T avec sous-routine non autorisé' DÉTECTION CAUSE SOLUTION 1411 SOLUTION SOLUTION Au cours de l'exécution. La CNC a essayé de stationner un axe faisant partie de la cinématique active ou des transformées #CS, #ACS, #ANGAX, #TANGCTRL. Réviser la programmation. Pour stationner cet axe, il faut désactiver la cinématique ou la transformation active. 'Il n’est pas permis de stationner des axes accouplés, Gantry ou Tandem' DÉTECTION CAUSE SOLUTION 1420 Au cours de l'exécution. Le nombre maximum de caractères permis pour le chemin d’un programme ou d’une sous-routine a été dépassé. Le chemin d’un programme ou d’une sous-routine peut avoir au maximum 120 caractères. Changer le programme ou la sous-routine de répertoire pour réduire le nombre de caractères dans le chemin. 'Il n'est pas permis de stationner les axes de la cinématique ou les transformées actives' DÉTECTION CAUSE 1419 Au cours de l'exécution. L'instruction #PARK ne permet de stationner qu'un seul axe. Programmer un bloc #PARK par axe à stationner. 'Path de fichier trop long' DÉTECTION CAUSE 1418 Au cours de l'exécution. La vitesse de positionnement programmée pour la fonction M19 est zéro. Programmer une vitesse de positionnement supérieure à zéro avec la commande "S.POS". '#PARK: l'instruction n'admet qu'un axe' DÉTECTION CAUSE SOLUTION 1417 Au cours de l'exécution. Dans l'instruction les limites des axes ont été mal définies. Les deux limites peuvent être positives ou négatives, mais les limites inférieures d'un axe doivent toujours être inférieures aux limites supérieures de cet axe. 'Vitesse nulle non admise pour positionnement de broche' DÉTECTION CAUSE SOLUTION 1414 Au cours de l'exécution. Le nombre de blocs programmé dans l'instruction est incorrect. Le nombre maximum de blocs à analyser dépend du modèle de CNC; 200 blocs (CNC 6065) ou 40 (CNC 8060). '#DGWZ: zone d'affichage pour graphiques mal définie' DÉTECTION CAUSE SOLUTION 1413 Au cours de l'exécution. La CNC a essayé d’exécuter un changement d’outil et un autre changement d’outil est programmé dans la sous-routine associée à la fonction T (paramètre TOOLSUB). On ne peut pas programmer une fonction T dans la sous-routine associée au changement d’outil. '#CD: nombre de blocs non valide' DÉTECTION CAUSE SOLUTION 1412 Au cours de l'exécution. La CNC ne peut pas exécuter la fonction ou l'instruction programmée si la broche n’est pas commandée en position. Il est nécessaire que dans la broche soit une broche. Au cours de l'exécution. La CNC a essayé de stationner un axe faisant partie d’un couple gantry, tandem ou d’un couplage actif (#LINK). Réviser la programmation. Pour stationner cet axe, il faut désactiver le couplage. Les axes faisant partie d'un couple gantry ou tandem ne peuvent pas être stationnés. CNC 8070 'Blocs de commande ouverts à la fin de programme' DÉTECTION CAUSE SOLUTION Au cours de l'exécution. Une instruction $IF, $FOR, etc. n’a pas son instruction de fermeture correspondante. Réviser la programmation. (REF: 1901) ·55· S o l ut i o n s d ’ e r r e ur s . 1421 'Les axes de la transformation active ne peuvent pas être esclaves ou stationnés' DÉTECTION CAUSE SOLUTION 1422 '#CS ON/#ACS ON: mode programmé non valable' DÉTECTION CAUSE SOLUTION 1423 SOLUTION SOLUTION SOLUTION CNC 8070 ·56· Au cours de l'exécution. Le nombre maximum de sous-routines pouvant être exécutées dans un même bloc a été dépassé. Le nombre maximum de sous-routines pouvant être exécutées dans un même bloc est 5. Programmer les sous-routines dans des blocs différents ou utiliser l’imbrication de sous-routines, selon la convenance. 'Format numérique dépassé' DÉTECTION CAUSE (REF: 1901) Au cours de l'exécution. Les coordonnées du point initial du cycle sont définies après la fonction G qui définit le cycle. Le cycle considère les coordonnées du point initial comme des paramètres propres. Programmer les cotes des axes avant la fonction G du cycle. 'Limite de sous-routines dans un même bloc dépassée' DÉTECTION CAUSE 1430 Au cours de l'exécution. Erreur dans la syntaxe de programmation de l'instruction ou fonction G ; un axe est répété sur un déplacement, il faut programmer l’ordre de la recherche de zéro des axes dans la fonction G74 ou il faut programmer l’ordre des axes dans le système dans la fonction G20. Réviser la programmation. 'Le déplacement dans le plan principal doit être programmé avant la G du cycle' DÉTECTION CAUSE 1429 Au cours de l'exécution. La CNC a généré la poche avec un rayon d’outil différent de l’actuel. Créer à nouveau la poche. 'Axe mal programmé' DÉTECTION CAUSE 1428 Au cours de l'exécution. Le caractère "/" n’est admis qu’au commencement de la ligne de programme. Réviser la programmation. 'La poche a été résolue avec un rayon d'outil différent' DÉTECTION CAUSE SOLUTION 1427 Au cours de l'exécution. On ne peut pas exécuter la fonction G programmée avec #MCS actif. Réviser la programmation. 'Le saut de bloc n'est admis qu'en début de ligne' DÉTECTION CAUSE SOLUTION 1426 Au cours de l'exécution. La valeur programmée comme mode pour aligner le plan n’est pas valide. Réviser la programmation. 'Fonction G interdite avec MCS actif' DÉTECTION CAUSE SOLUTION 1425 Au cours de l'exécution. Le paramètre MODE programmé n'est pas valide. La valeur du paramètre MODE doit être comprise entre 1 et 6. '#CS ON/#ACS ON: le paramètre d'axe aligné doit être 0 ou 1' DÉTECTION CAUSE SOLUTION 1424 Au cours de l'exécution. Un des axes participant à la transformation de coordonnées programmée est stationné, est esclave d’un couple gantry ou esclave d’un couplage actif. Arrêter le stationnement, désactiver le couplage actif ou défaire le couple gantry pour pouvoir utiliser l’axe dans la transformation de coordonnées. SOLUTION Au cours de l'exécution. La valeur affectée à une donnée, variable ou paramètre, est supérieure au format établi. Réviser la programmation. S o l ut i o n s d ’ e r r e ur s . 1431 'Position de broche en M19 non valide' DÉTECTION CAUSE SOLUTION 1432 'Il est impossible de programmer un axe esclave d'un couplage ou Gantry' DÉTECTION CAUSE SOLUTION 1433 SOLUTION SOLUTION SOLUTION Au cours de l'exécution. Il faut définir le bloc d’arrêt de la recherche de bloc. Après avoir sélectionné l’option de recherche de bloc, le menu de touches logiciel affiche l’option pour sélectionner le bloc arrêt. Sélectionner le bloc où l’on veut terminer la recherche de bloc. 'Les axes de la transformation active ne peuvent pas être Hirth' DÉTECTION CAUSE SOLUTION 1440 Au cours de l'exécution. La CNC a essayé d’inclure dans la configuration du canal (#CALL ou #SET) l’axe maître d’un couplage actif ou d’un couple Gantry. En incluant l’axe maître, la CNC inclut aussi l’axe esclave, qui ne peut jamais occuper une des trois positions principales du canal. La CNC affiche erreur parce que le nom de l’axe esclave est déjà occupé par un autre axe dans la configuration actuelle du canal. Renommer l’axe esclave à inclure ou celui qui existe déjà dans la configuration. 'Il manque la programmation du bloc d'arrêt dans la recherche de bloc' DÉTECTION CAUSE SOLUTION 1439 Au cours de l'exécution. La CNC a essayé d’inclure dans la configuration du canal (#CALL ou #SET) l’axe maître d’un couplage actif ou d’un couple Gantry. En incluant l’axe maître, la CNC inclut aussi l’axe esclave, qui ne peut jamais occuper une des trois positions principales du canal. La CNC affiche erreur parce qu’il n’existe pas une position libre pour l’axe esclave différente des trois principales. Pour pouvoir inclure uniquement l’axe maître il faut d’abord désactiver le couplage actif (#UNLINK) ou défaire le couple Gantry. Pour pouvoir inclure les axes maître et esclave, il faut supprimer du canal un autre axe ou bien augmenter le nombre d’axes du canal. 'Un nom n'a pas pu être assigné à un axe esclave associé du fait d'être répété' DÉTECTION CAUSE 1436 Au cours de l'exécution. La CNC a essayé d’inclure (#CALL / #SET) un axe stationné dans les trois premiers axes du canal. Un axe stationné ne peut pas faire partie des trois premiers axes du canal ; arrêter le stationnement l’axe (#UNPARK). 'Il n'est pas possible d'inclure dans la configuration un axe esclave associé' DÉTECTION CAUSE 1435 Au cours de l'exécution. L’axe esclave d’un couplage actif ou d’un couple Gantry est programmé dans l'instruction. Pour pouvoir travailler avec l’axe dans ces instructions, il faut désactiver le couplage actif (#UNLINK) ou défaire le couple Gantry (par paramètre machine). 'Un axe stationné ne peut pas faire partie du plan principal' DÉTECTION CAUSE 1434 Au cours de l'exécution. La valeur programmée pour la position de broche sur M19 est trop élevée. Programmer une valeur plus petite. Au cours de l'exécution. La CNC a essayé d’activer une transformation de coordonnées (#TLC, #RTCP, #TOOL ORI, #CS ou #ACS) et un des axes intervenant dans la transformation est Hirth. Un axe hirth ne peut pas faire partie de la transformation de coordonnées. Pour que l’axe puisse intervenir dans la transformation, l'axe ne doit plus être Hirth (G170). 'Outil ou tranchant non valide' DÉTECTION CAUSE SOLUTION CNC 8070 Au cours de l'exécution. L’outil et/ou le correcteur indiqué dans la variable n’existe pas. Réviser la programmation. Consulter les outils et les correcteurs existants. (REF: 1901) ·57· S o l ut i o n s d ’ e r r e ur s . 1441 'La cinématique n'a pas été activée'. DÉTECTION CAUSE SOLUTION 1442 'La cinématique a été désactivée' DÉTECTION CAUSE SOLUTION 1443 CAUSE SOLUTION SOLUTION SOLUTION CNC 8070 SOLUTION (REF: 1901) Au cours de l'exécution. Les possibles causes sont les suivantes: • Le type de broche ne permet pas de placer l’outil perpendiculairement au plan, comme dans le cas des broches angulaires. • Placer l’outil perpendiculairement au plan actif implique dépasser les limites. Définir un autre plan ou placer l’outil à un autre point. Dans la mesure du possible, utiliser une autre broche. 'Instruction #PATH mal programmée' DÉTECTION CAUSE SOLUTION ·58· Au cours de l'exécution. La CNC ne dispose pas de l’option de logiciel nécessaire pour exécuter l’ordre programmé. Le mode diagnostic permet de consulter les options de logiciel disponibles dans la CNC. 'Il est impossible de placer l'outil perpendiculairement au plan actif' DÉTECTION CAUSE 1449 Au cours de l'exécution. Le bloc de départ ne peut pas être un bloc d’une sous-routine locale. Sélectionner un autre bloc initial. 'Option de logiciel non autorisée' DÉTECTION CAUSE 1448 Au cours de l'exécution. Dans une instruction ou un cycle fixe, un paramètre présente une valeur non valable. Réviser la programmation. 'Bloc de départ interdit dans la sous-routine locale' DÉTECTION CAUSE SOLUTION 1447 Au cours de l'exécution. Un des trois premiers axes participant à la transformation ou à la cinématique programmée n’est pas linéaire. Les trois premiers axes de la transformation ou cinématique doivent être linéaires (paramètre AXISTYPE). 'Valeur de paramètre non valable' DÉTECTION CAUSE SOLUTION 1446 Après une RAZ de la CNC, au commencement de l’exécution d’un programme pièce ou pendant la recherche de référence. Les axes utilisés sur le plan incliné ne sont pas les adéquats. La CNC a essayé de faire une recherche de référence avec la fonction #CS/ACS active. Pour construire un plan incliné, les trois premiers axes du canal doivent être définis, être linéaires, ne pas être stationnés et ne pas être esclaves d’un couplage ou d’un gantry. Pour exécuter une recherche de référence il faut désactiver les fonctions #CS/ACS. 'Les trois axes principaux de la transformation doivent être linéaires' DÉTECTION CAUSE 1445 Après une RAZ de la CNC ou au commencement l’exécution d’un programme pièce. La CNC a désactivé une cinématique parce qu’elle est inconnue ou parce que les axes nécessaires pour cette cinématique ne sont pas adéquats. Vérifier que le type de cinématique est correct et que les axes qui y interviennent sont bien définis et font partie du canal. Les axes doivent toujours être les premiers du canal, ne pas être des axes hirth, ne pas être stationnés et ne pas être esclaves d’un couplage ou d’un gantry. '#CS/ACS a été désactivé' DÉTECTION 1444 Au cours du démarrage de la CNC ou la validation des paramètres machine. La cinématique appliquée par la CNC par défaut (paramètre KINID) est inconnue ou les axes nécessaires pour la cinématique ne sont pas adéquats. Vérifier que le type de cinématique est correct et que les axes qui y interviennent sont bien définis et font partie du canal. Les axes doivent toujours être les premiers du canal, ne pas être des axes hirth, ne pas être stationnés et ne pas être esclaves d’un couplage ou d’un gantry. Au cours de l'exécution. La syntaxe de l'instruction #PATH n'est pas correcte. Réviser la programmation. S o l ut i o n s d ’ e r r e ur s . 1450 'Solution non valide de broche perpendiculaire au plan actif' DÉTECTION CAUSE SOLUTION 1451 'Variable inexistante pour le type d'axe' DÉTECTION CAUSE SOLUTION 1452 SOLUTION SOLUTION SOLUTION Au cours de l'exécution. Les possibles causes sont les suivantes: • Les paramètres d’interpolation du polynôme ne sont pas corrects. • Le rayon de courbure programmé est inférieur ou égal à zéro. Les paramètres d’interpolation du polynôme doivent être positifs, le paramètre initial de l’interpolation (SP) doit être inférieur au paramètre final (EP) et le rayon de courbure doit être supérieur à zéro. '#POLY: Trop d'axes programmés' DÉTECTION CAUSE SOLUTION 1459 Au cours de l'exécution. Il manque un paramètre obligatoire dans la programmation de l'instruction #POLY. Réviser la programmation. '#POLY: 'Valeur de paramètre non valide' DÉTECTION CAUSE 1458 Au cours de l'exécution. Les possibles causes sont les suivantes: • Le fichier contenant le profil n’a pas été indiqué dans le cycle de profil de l’éditeur de cycles. • Le fichier indiqué dans le cycle de profil de l’éditeur de cycles est vide. Il faut indiquer le fichier contenant le profil dans le cycle de profil de l’éditeur de cycles. '#POLY: Paramètres manquants' DÉTECTION CAUSE SOLUTION 1457 Au cours de l'exécution. Le nom de l’axe dépasse la longueur maximale permise de deux caractères. Le nom de l'axe sera défini par 1 ou 2 caractères. Le premier caractère doit être une des lettres X - Y - Z - U - V - W - A - B - C. Le deuxième caractère est optionnel et sera un suffixe numérique entre 1 et 9. Ainsi le nom des axes pourra être n'importe lequel du rang X, X1…X9,...C, C1…C9.. 'PROFIL: Profil nul' DÉTECTION CAUSE 1456 Au cours de l'exécution. La variable n’existe pas pour le type d'asservissement programmé (analogique, simulé ou Sercos). Réviser la programmation. 'Nom d'axe trop long' DÉTECTION CAUSE SOLUTION 1455 Au cours de l'exécution. La variable n’existe pas pour le type d’axe programmé (linéaire, rotatif ou broche). Réviser la programmation. 'Variable inexistante pour le type d'asservissement' DÉTECTION CAUSE 1453 Au cours de l'exécution. La valeur de la variable V.G.TOOLORIF1 ou V.G.TOOLORIF2 n’est pas valide parce que la CNC ne peut pas placer l’outil perpendiculairement au plan actif. Les possibles causes sont les suivantes: • Le type de broche ne permet pas de placer l’outil perpendiculairement au plan, comme dans le cas des broches angulaires. • Placer l’outil perpendiculairement au plan actif implique dépasser les limites. Définir un autre plan ou placer l’outil à un autre point. Dans la mesure du possible, utiliser une autre broche. Au cours de l'exécution. Il y a plus de trois axes dans le polynôme. Seuls trois axes peuvent intervenir dans l’interpolation polynomiale. CNC 8070 '#POLY: Point initial non valide' DÉTECTION CAUSE SOLUTION Au cours de l'exécution. Le point initial du polynôme ne coïncide pas avec la position actuelle. Modifier le terme indépendant du polynôme pour chaque axe, de manière à ce que le point initial du polynôme coïncide avec la position finale du bloc précédent. (REF: 1901) ·59· S o l ut i o n s d ’ e r r e ur s . 1461 'G9: Programmation incorrecte du point intermédiaire de l'arc' DÉTECTION CAUSE SOLUTION 1462 'G8: Calcul de la trajectoire tangente impossible' DÉTECTION CAUSE SOLUTION 1463 SOLUTION SOLUTION SOLUTION (REF: 1901) ·60· 1469 Au cours de l'exécution. La valeur à écrire dans les variables V.A.POSLIMIT.xn et V.A.NEGLIMIT.xn ne doit pas dépasser la valeur du paramètre machine POSLIMIT et NEGLIMIT de cet axe. Réviser la programmation. 'G30: Programmation incorrecte de l'origine polaire' DÉTECTION CAUSE CNC 8070 Au cours de l'exécution. Un bloc G8 ne peut pas être le deuxième bloc de déplacement d’une des fonctions G36/G37/G38/G39. D’une part, ces fonctions ne disposent pas d’un bloc intermédiaire pour réaliser la trajectoire de jonction entre deux blocs et d’autre part, la fonction G8 ne dispose pas d’un bloc antérieur pour y être tangent. Le deuxième bloc de déplacement d’une fonction G36/G37/G38/G39 doit être G0/G1/G2/G3. 'POSLIMIT/NEGLIMIT ne peut pas dépasser la valeur du paramètre machine' DÉTECTION CAUSE 1468 Au cours de l'exécution. La CNC a essayé d’activer l’une des fonctions alors que l’autre était active. Les deux fonctions ne peuvent pas être actives simultanément. 'On ne peut pas programmer G8 comme deuxième bloc de déplacement pour G36/G37/G38/G39' DÉTECTION CAUSE 1467 Au cours de l'exécution. La cote absolue (G90) programmée pour l’axe rotatif type MODULE n’est pas valide. La cote programmée pour l’axe doit se trouver entre les limites fixées pour ses paramètres machine MODUPLIM et MODLOWLIM. 'Les fonctions RTCP et TLC sont incompatibles' DÉTECTION CAUSE SOLUTION 1466 Au cours de l'exécution. Il est impossible de réaliser un arc passant par les trois points disponibles. Définir deux points dans le bloc avec G9 qui, avec le point final du déplacement précédent, définissent un arc. Il faut tenir compte que les trois points doivent être différents et ne doivent pas être alignés. 'Axe rotatif programmé hors du rang du module' DÉTECTION CAUSE SOLUTION 1465 Au cours de l'exécution. On ne peut pas réaliser un arc tangent à la trajectoire antérieure avec le rayon et le point final programmés. Réviser la programmation. 'G9: 'Trajectoire circulaire mal programmée' DÉTECTION CAUSE SOLUTION 1464 Au cours de l'exécution. Il faut programmer l’une ou les deux coordonnées du point intermédiaire de l’arc. La fonction G9 exige la programmation des deux coordonnées du point intermédiaire de l’arc. Au cours de l'exécution. L’une des deux coordonnées de l’origine polaire doit être programmée dans la fonction G30. Réviser la programmation. Il faut programmer les coordonnées de l’origine polaire sur les deux axes principaux. 'Rayon négatif ou nul non autorisé' DÉTECTION CAUSE SOLUTION Au cours de l'exécution. Dans un déplacement en coordonnées polaires, le rayon polaire est négatif ou nul. Le rayon polaire doit toujours être supérieur à zéro. Si on programme en cotes incrémentales, la valeur programmée pourra être négative ou nulle mais pas le rayon polaire absolu. S o l ut i o n s d ’ e r r e ur s . 1470 'Axe rotatif UNIDIR avec programmation incrémentale incorrecte' DÉTECTION CAUSE SOLUTION 1471 'G73: programmation incorrecte du centre de rotation' DÉTECTION CAUSE SOLUTION 1472 SOLUTION Au cours de l'exécution. La CNC a généré la poche avec un angle d’entrée d’outil différent de l’actuel. Créer à nouveau la poche. 'G74: il faut associer une sous-routine' DÉTECTION CAUSE SOLUTION 1480 Au cours de l'exécution. La CNC a généré la poche avec une longueur de coupe d’outil différente de l’actuelle. Créer à nouveau la poche. 'La poche a été résolue avec un angle différent d'entrée d'outil' DÉTECTION CAUSE SOLUTION 1479 Au cours de l'exécution. La CNC a généré la poche avec un rayon d’outil différent de l’actuel. Créer à nouveau la poche. 'La poche a été résolue avec une longueur différente de coupe d'outil' DÉTECTION CAUSE SOLUTION 1478 Au cours de l'exécution. Le rayon ("R" ou "R1") est programmé plus d’une fois dans le même bloc. Définir un seul rayon dans le bloc. 'La poche a été résolue avec un rayon différent de la pointe de l'outil' DÉTECTION CAUSE SOLUTION 1477 Au cours de l'exécution. La CNC a essayé d’exécuter l'instruction #POLY avec une rotation du système de coordonnées active (G73). Réviser la programmation. 'Rayon programmé en double' DÉTECTION CAUSE SOLUTION 1476 Au cours de l'exécution. Dans la fonction G73, l'angle de rotation n'est pas programmé. Réviser la programmation. Il faut programmer l’angle de rotation du système de coordonnées, en même temps que les coordonnées du centre de rotation sur les deux axes principaux. 'Programmation #POLY interdite avec rotation active' DÉTECTION CAUSE 1475 Au cours de l'exécution. L’une des deux coordonnées du centre de rotation doit être programmée dans la fonction G73. Réviser la programmation. Il faut programmer les coordonnées du centre de rotation sur les deux axes principaux. 'G73: Il manque la programmation de l'angle de rotation' DÉTECTION CAUSE SOLUTION 1473 Au cours de l'exécution. La cote incrémentale programmée pour l’axe rotatif unidirectionnel (paramètre UNIDIR) n’est pas valide. Si le paramètre machine UNIDIR de l’axe rotatif est POSITIF, la cote incrémentale programmée doit être positive ou nulle. Si le paramètre machine UNIDIR de l’axe rotatif est NÉGATIF, la cote incrémentale programmée doit être négative ou nulle. Au cours de l'exécution. Une fonction G74 est programmée seule dans le bloc et la sous-routine associée n’existe pas. Programmer avec la fonction G74 les axes à référencer ou définir la sous-routine associée (paramètre REFPSUB). CNC 8070 'Programmer: #EXEC ["path+programme",canal]' DÉTECTION CAUSE SOLUTION Au cours de l'exécution. La syntaxe de l'instruction n’est pas correcte ou il y a plus d’information dans le bloc. Réviser la programmation. Les instructions doivent être programmées seules dans le bloc et on ne peut ajouter que l’étiquette du bloc. (REF: 1901) ·61· S o l ut i o n s d ’ e r r e ur s . 1481 'Numéro de canal non valide' DÉTECTION CAUSE SOLUTION 1483 'Programmer: #WAIT/#MEET [signal, canal, canal, ...]' DÉTECTION CAUSE SOLUTION 1484 SOLUTION SOLUTION SOLUTION SOLUTION (REF: 1901) ·62· 1492 Au cours de l'exécution. La CNC a essayé de faire un filetage G63 avec une broche Sercos sans la positionner avant avec M19. Programmer M19 avant de réaliser le filetage. 'Numéro de palpeur incorrect' DÉTECTION CAUSE CNC 8070 Au cours de l'exécution. L'instruction #RENAME a essayé de renommer plus d’un axe avec le même nom. Renommer les axes de manière à ce qu’il n’y en ait pas deux avec le même nom dans le canal. 'G63 a besoin de programmer M19 préalablement' DÉTECTION CAUSE 1491 Au cours de l'exécution. La syntaxe de l'instruction n’est pas correcte ou il y a plus d’information dans le bloc. Réviser la programmation. Les instructions doivent être programmées seules dans le bloc et on ne peut ajouter que l’étiquette du bloc. 'Nom d'axe répété dans le groupe résultant' DÉTECTION CAUSE SOLUTION 1490 Au cours de l'exécution. La syntaxe de l'instruction n’est pas correcte ou il y a plus d’information dans le bloc. Réviser la programmation. Les instructions doivent être programmées seules dans le bloc et on ne peut ajouter que l’étiquette du bloc. 'Programmer: #CLEAR [signal, signal, signal, ...]' DÉTECTION CAUSE SOLUTION 1489 Au cours de l'exécution. L'instruction #WAIT ou #MEET ne va produire aucune attente car la marque de synchronisation est programmée pour le même canal que les instructions. Réviser la programmation. 'Programmer: #SIGNAL [signal, signal, signal, ...]' DÉTECTION CAUSE SOLUTION 1487 Au cours de l'exécution. Le numéro de signal programmé dans l'instruction #WAIT, #MEET ou #SIGNAL est incorrect. Réviser la programmation. '#WAIT/#MEET non effectif' DÉTECTION CAUSE 1486 Au cours de l'exécution. La syntaxe de l'instruction n’est pas correcte ou il y a plus d’information dans le bloc. Réviser la programmation. Les instructions doivent être programmées seules dans le bloc et on ne peut ajouter que l’étiquette du bloc. 'Numéro de signal hors de rang' DÉTECTION CAUSE 1485 Au cours de l'exécution. Numéro de canal non valide dans l'instruction #EXEC, #MEET ou #WAIT. Le numéro de canal doit être compris entre 1 et 4. Au cours de l'exécution. Le numéro de palpeur sélectionné avec l'instruction #SELECT PROBE n’est pas correct. Le numéro de palpeur sélectionné doit être 1 ou 2. 'L'entrée numérique associée au palpeur n'existe pas (PRBDI1/2)' DÉTECTION CAUSE SOLUTION Au cours de l'exécution. La CNC a essayé de sélectionner un palpeur (#SELECT PROBE) ou de réaliser un déplacement de palpage (G100) et il n’existe aucune entrée numérique associée au palpeur. Associer une entrée numérique au palpeur (paramètre PRBDI1 ou PRBDI2). S o l ut i o n s d ’ e r r e ur s . 1493 'Programmation simultanée de #SPLINE ON, G41/G42 et G136 non autorisée' DÉTECTION CAUSE SOLUTION 1494 'Indice incorrect' DÉTECTION CAUSE SOLUTION 1495 SOLUTION SOLUTION SOLUTION SOLUTION SOLUTION Au cours de l'exécution. La variable est un array et l'indice n'a pas été indiqué. Consulter dans les manuels la liste de variables. CNC 8070 'La variable exige la programmation de l'axe' DÉTECTION CAUSE SOLUTION 1504 Au cours de l'exécution. Dans l'instruction #RPT l’étiquette initiale et finale est la même. Définir étiquettes initiale et final différentes. 'La variable exige la programmation de l'index array' DÉTECTION CAUSE SOLUTION 1503 Au cours de l'exécution. Avec l'instruction #EXEC, la CNC a essayé d’exécuter un programme dans un canal qui est à l’état d’erreur, qui est en train d’exécuter un autre programme ou qui est en mode manuel et ne peut pas passer au mode automatique. Attendre la fin du programme dans l’autre canal ou faire une RAZ. 'Étiquettes répétées en #RPT' DÉTECTION CAUSE SOLUTION 1502 Au cours de l'exécution. Il y a emboîtement lorsque l'instruction #RPT est programmée entre deux étiquettes qui définissent le rayon d’action d’une autre instruction #RPT. La CNC affiche erreur lorsque le nombre d’emboîtements d'instructions RPT et de sous-routines, le cas échéant, est dépassé. Le nombre maximum d'emboîtements permis est 20. '#EXEC: on ne peut pas exécuter le programme dans le canal indiqué' DÉTECTION CAUSE 1501 Au cours de l'exécution. La CNC a essayé de modifier avec les opérateurs "+=", "-=", "*=" et "/=" une variable non numérique. Réviser la programmation. 'Nombre d'emboîtements de #RPT et sous-routines surpassé' DÉTECTION CAUSE 1500 Au cours de l'exécution. La CNC a essayé d’exécuter le cycle PROBE1 avec l’outil orienté dans le sens négatif de l’axe. Programmer #TOOL AX[+] avant d’exécuter le cycle PROBE1 pour orienter l’outil dans le sens positif de l’axe. 'Opérateur incorrect pour le type de variable' DÉTECTION CAUSE 1499 Au cours de l'exécution. Le cycle PROBE1 affiche erreur parce que les trois premiers axes de la configuration actuelle ne coïncident pas avec les trois premiers axes de la configuration initiale. Restaurer la configuration initiale des trois premiers axes du canal. '#PROBE1: programmation interdite avec #TOOL AX[-] actif' DÉTECTION CAUSE 1497 Au cours de l'exécution. Le numéro d’erreur indiqué dans l'instruction #ERROR ou #WARNING n’existe pas. Réviser la programmation. '#PROBE1: axe non valide pour le cycle de palpeur' DÉTECTION CAUSE 1496 Au cours de l'exécution. La CNC a essayé d’activer simultanément les fonctions #SPLINE ON, G41, G42 et G136. Désactiver une des ces fonctions. Au cours de l'exécution. La variable est d’axe et le nom de l’axe n’a pas été indiqué. Consulter dans les manuels la liste de variables. (REF: 1901) 'La variable ne permet pas la programmation de l'index d'array' DÉTECTION CAUSE SOLUTION Au cours de l'exécution. La syntaxe de la variable est incorrecte. Consulter dans les manuels la liste de variables. ·63· S o l ut i o n s d ’ e r r e ur s . 1505 'La variable ne permet pas la programmation de l'axe' DÉTECTION CAUSE SOLUTION 1506 'Étiquette non définie ou étiquettes de la commande #RPT interchangées' DÉTECTION CAUSE SOLUTION 1507 SOLUTION SOLUTION SOLUTION SOLUTION SOLUTION 1512 ·64· Au cours de l'exécution. La CNC a essayé de lire avec la variable V.TM.P la position dans le magasin d’un outil qui n’y figure pas. On ne peut lire que la position des outils qui se trouvent dans le magasin. 'Position du magasin libre ou inexistante' DÉTECTION CAUSE (REF: 1901) Au cours de l'exécution. Les possibles causes sont les suivantes: • La CNC essaie de déplacer un axe qui n'existe pas ou qui n'est pas disponible dans le canal. • La CNC essaie d'exécuter une instruction qui concerne un axe qui n'existe pas ou qui n'est pas disponible dans le canal. • La CNC essaie de lire ou d'écrire une variable d'un axe qui n'existe pas ou qui n'est pas disponible dans le canal. Réviser la programmation. 'L'outil n'est pas dans le magasin' DÉTECTION CAUSE CNC 8070 Au cours de l'exécution. Tous les axes programmés dans l'instruction appartiennent à la configuration actuelle et par conséquent l'instruction implique uniquement un changement d'ordre. Dans ce cas, l’option d’offsets programmée n’a pas d’effet. Réviser la programmation. 'Axe inexistant ou pas disponible dans le canal' DÉTECTION CAUSE 1511 Au cours de l'exécution. Les possibles causes sont les suivantes: • Un des axes impliqués dans la fonction G201 est axe C et fait partie des trois premiers axes du canal. • L’un des axes programmés dans l'instruction #FACE est en mode manuel additif, G201. Annuler l'axe C ou le mode manuel additif. '#SET AX/#CALL AX: la programmation des offsets n'a pas d'effet' DÉTECTION CAUSE 1510 Au cours de l'exécution. Dans une répétition de blocs (#RPT), la deuxième étiquette doit être programmée seule dans le bloc, sans aucune autre information. L'étiquette finale doit être programmée seule dans le bloc. Programmer la commande dans la ligne précédente si on veut qu’elle s’exécute avec le #RPT ou dans la ligne inférieure si on ne veut pas qu’elle s’exécute avec le #RPT. 'G201 et l'axe C actif sont interdits dans les axes du plan principal' DÉTECTION CAUSE 1509 Au cours de l'exécution. Les possibles causes sont les suivantes: • La deuxième étiquette n'est pas définie. • M30 a été programmée entre la première et la deuxième étiquette. • Dans l'instruction #RPT, la deuxième étiquette a été programmée avant la première. Réviser la programmation. 'La seconde étiquette du #RPT doit être programmée seule dans le bloc' DÉTECTION CAUSE 1508 Au cours de l'exécution. La syntaxe de la variable est incorrecte. Consulter dans les manuels la liste de variables. SOLUTION Au cours de l'exécution. La CNC a essayé de lire avec la variable V.TM.T le numéro d’outil situé sur une position du magasin qui n’existe pas. On ne peut lire que l’outil qui est sur une position valide du magasin. S o l ut i o n s d ’ e r r e ur s . 1513 'Erreur dans l'écriture de la variable' DÉTECTION CAUSE SOLUTION 1514 'Il est impossible d'exécuter une poche 2D-3D avec G72 actif' DÉTECTION CAUSE SOLUTION 1515 SOLUTION SOLUTION SOLUTION SOLUTION Au cours de l'exécution. Une répétition de blocs (NR) est programmée dans un bloc contenant une fonction M, T, D ou H. La programmation de la répétition de blocs avec NR n’est valide qu’avec des blocs qui impliquent un déplacement. La répétition d’un autre type de blocs devra être réalisée avec les instructions de commande de flux dont dispose la commande. 'NR: on ne peut pas programmer $GOTO dans le même bloc' DÉTECTION CAUSE SOLUTION 1521 Au cours de l'exécution. Une répétition de blocs (NR) est programmée dans un bloc qui n’implique pas de déplacement. La programmation de la répétition de blocs avec NR n’est valide qu’avec des blocs qui impliquent un déplacement. La répétition d’un autre type de blocs devra être réalisée avec les instructions de commande de flux dont dispose la commande. 'NR: on ne peut pas programmer M/T/D/H dans le même bloc' DÉTECTION CAUSE 1520 Au cours de l'exécution. La liste de paramètres d’appel à une sous-routine a été programmée incorrectement avec #PCALL ou G180-189. Réviser la programmation. 'NR exige la programmation d'un déplacement dans le bloc' DÉTECTION CAUSE 1519 Au cours de l'exécution. Un canal a cédé un axe avec permission de changement temporaire (paramètre AXISEXCH) et on ne peut pas le récupérer avec la RAZ ou au commencement du programme parce que le canal qui l’a pris ne l’a pas encore libéré. L’autre canal cédera l’axe avec une RAZ ou avec le démarrage d’un autre programme. On peut aussi programmer explicitement la libération de l’axe avec l'instruction #FREE AX. 'Une valeur était attendue' DÉTECTION CAUSE 1518 Au cours de l'exécution. La CNC a essayé d’exécuter la poche avec un facteur d’échelle actif. Annuler le facteur d'échelle. 'Un ou plusieurs axes de la configuration originale ne sont pas disponibles' DÉTECTION CAUSE 1516 Au cours de l'exécution. Les possibles causes sont les suivantes: • La variable n'existe pas. • La variable est d'axe mais l'axe n'existe pas. • La variable est d’axe mais n’existe pas pour le type d'axe (linéaire ou rotatif). • La variable est d’axe mais n’existe pas pour le type d'asservissement de l’axe. • Opérateur composé (+= -= *= /=) interdit pour cette variable. • La valeur de la variable n’est pas valide. Réviser la programmation. Au cours de l'exécution. Une répétition de blocs (NR) est programmée dans un bloc contenant l’instruction $GOTO. La programmation de la répétition de blocs avec NR n’est valide qu’avec des blocs qui impliquent un déplacement. La répétition d’un autre type de blocs devra être réalisée avec les instructions de commande de flux dont dispose la commande. CNC 8070 'NR: on ne peut pas programmer appel à sous-routine dans le même bloc' DÉTECTION CAUSE SOLUTION Au cours de l'exécution. Une répétition de blocs (NR) est programmée dans un bloc contenant un appel à une sous-routine (L, LL, #CALL, #PCALL, #MCALL ou G180-G189). La programmation de la répétition de blocs avec NR n’est valide qu’avec des blocs qui impliquent un déplacement. La répétition d’un autre type de blocs devra être réalisée avec les instructions de commande de flux dont dispose la commande. (REF: 1901) ·65· S o l ut i o n s d ’ e r r e ur s . 1522 'Valeur négative interdite' DÉTECTION CAUSE SOLUTION 1523 'Il faut programmer POS et T dans le même bloc' DÉTECTION CAUSE SOLUTION 1525 SOLUTION SOLUTION SOLUTION SOLUTION SOLUTION 1532 1533 Au cours de l'exécution. La syntaxe de l'instruction n’est pas correcte ou il y a plus d’information dans le bloc. Réviser la programmation. Les instructions doivent être programmées seules dans le bloc et on ne peut ajouter que l’étiquette du bloc. 'Programmer: #FREESP [sp1, sp2, ..]' DÉTECTION CAUSE SOLUTION ·66· Au cours de l'exécution. La syntaxe de l'instruction n’est pas correcte ou il y a plus d’information dans le bloc. Réviser la programmation. Les instructions doivent être programmées seules dans le bloc et on ne peut ajouter que l’étiquette du bloc. 'Programmer: #MASTER <nom de broche>' DÉTECTION CAUSE SOLUTION (REF: 1901) Au cours de l'exécution. Dans la fonction G53, les cotes du point final sont définies en coordonnées polaires ou cylindriques. Programmer par rapport au zéro machine, seules les cotes en coordonnées cartésiennes peuvent être définies. 'Programmer: #EXBLK [bloc, canal]' DÉTECTION CAUSE SOLUTION CNC 8070 Au cours de l'exécution. Dans l'instruction #MSG, #ERROR ou #WARNING, un caractère non valide est programmé après le message à afficher. Réviser la programmation. Les virgules finales du message à afficher ne peuvent être suivies que de la liste de variables ou de paramètres à inclure dans le texte. 'Il est impossible de programmer G53 avec des coordonnées polaires' DÉTECTION CAUSE 1531 Au cours de l'exécution. Dans l'instruction #MSG, #ERROR ou #WARNING, un identificateur non valide est programmé. Les identificateurs valides sont %D ou %d pour afficher un numéro et %% pour afficher le caractère "%". 'Liste d'identificateurs ou "]" après les guillemets finaux attendus' DÉTECTION CAUSE 1530 Au cours de l'exécution. Avec l'instruction #EXEC, la CNC a essayé d’exécuter un programme dans un canal qui n’est pas de CNC, mais de PLC. Réviser la programmation. 'Identificateur non valide après ' DÉTECTION CAUSE 1529 Au cours de l'exécution. La CNC a essayé de changer un axe de canal (#CALL, #SET ou #FREE) et l’axe n’a pas de permission de changement (paramètre AXISEXCH). Pour que la CNC puisse changer les axes et les broches de canal, ceux-ci doivent avoir de l'autorisation. Le paramètre AXISEXCH établit si l’axe ou la broche a l’autorisation de changement de canal, et en cas affirmatif, si le changement est temporaire ou permanent ; c’est-à-dire, si le changement est conservé au redémarrage du programme pièce, après une RAZ ou un redémarrage de la CNC. '#EXEC: le canal indiqué n'est pas de CNC' DÉTECTION CAUSE 1527 Au cours de l'exécution. L’outil T et la position POS n’ont pas été programmés dans le même bloc. L’outil T et la position que celui-ci doit occuper dans le magasin doivent être programmés dans le même bloc. 'L'échange d'axe est interdit' DÉTECTION CAUSE 1526 Au cours de l'exécution. Un nombre négatif de répétitions de bloc (NR) a été programmé. Réviser la programmation. Au cours de l'exécution. La syntaxe de l'instruction n’est pas correcte ou il y a plus d’information dans le bloc. Réviser la programmation. Les instructions doivent être programmées seules dans le bloc et on ne peut ajouter que l’étiquette du bloc. S o l ut i o n s d ’ e r r e ur s . 1534 'Programmer: #CALLSP [sp1, sp2, ..]' DÉTECTION CAUSE SOLUTION 1535 'Programmer: #SETSP [sp1, sp2, ..]' DÉTECTION CAUSE SOLUTION 1538 SOLUTION SOLUTION SOLUTION SOLUTION Au cours de l'exécution. La CNC a essayé de supprimer du canal (#FREE ou #SET) une broche qui travaille comme axe C. Désactiver l’axe C avant de supprimer la broche du canal. 'L'échange de broche est interdit' DÉTECTION CAUSE SOLUTION 1544 Au cours de l'exécution. Les possibles causes sont les suivantes: • La CNC essaie de lire ou d’écrire une variable de la broche master et celle-ci n’existe pas dans le canal. • La fonction G ou l'instruction ne peut pas être exécutée s’il n’y a pas de broche master dans le canal. Définir une broche master pour le canal. 'Il est interdit d'éliminer la broche avec l'axe C actif' DÉTECTION CAUSE 1542 Au cours de l'exécution. L'instruction #RENAME a essayé de renommer plus d’une broche avec le même nom. Renommer les broches de manière à ce qu’il n’y en ait pas deux avec le même nom dans le canal. 'Programmation interdite sans broche master dans le canal' DÉTECTION CAUSE 1541 Au cours de l'exécution. Un canal a cédé une broche avec permission de changement temporaire (paramètre AXISEXCH) et on ne peut pas la récupérer avec la RAZ ou au commencement du programme parce que le canal qui l’a prise ne l’a pas encore libérée. L’autre canal cédera la broche avec une RAZ ou le démarrage d’un autre programme. On peut aussi programmer explicitement la libération de la broche avec l'instruction #FREE SP. 'Nom de broche répété dans le groupe résultant' DÉTECTION CAUSE 1540 Au cours de l'exécution. La syntaxe de l'instruction n’est pas correcte ou il y a plus d’information dans le bloc. Réviser la programmation. Les instructions doivent être programmées seules dans le bloc et on ne peut ajouter que l’étiquette du bloc. 'Une broche ne peut pas être récupérée du canal' DÉTECTION CAUSE 1539 Au cours de l'exécution. La syntaxe de l'instruction n’est pas correcte ou il y a plus d’information dans le bloc. Réviser la programmation. Les instructions doivent être programmées seules dans le bloc et on ne peut ajouter que l’étiquette du bloc. Au cours de l'exécution. La CNC a essayé de changer une broche de canal (#CALL, #SET ou #FREE) et la broche n’a pas de permission de changement (paramètre AXISEXCH). Pour que la CNC puisse changer les axes et les broches de canal, ceux-ci doivent avoir de l'autorisation. Le paramètre AXISEXCH établit si l’axe ou la broche a l’autorisation de changement de canal, et en cas affirmatif, si le changement est temporaire ou permanent ; c’est-à-dire, si le changement est conservé au redémarrage du programme pièce, après une RAZ ou un redémarrage de la CNC. 'On n'admet pas G63 et M3/M4/M5/M19/M41-M44 dans le même bloc' DÉTECTION CAUSE SOLUTION Au cours de l'exécution. Aucune fonction M associée à la broche n’est permise dans le même bloc où est programmé un taraudage rigide G63. Il peut se faire dans le bloc antérieur ou postérieur en fonction du résultat prévu. Si cela est fait dans le bloc suivant, ces fonctions M désactivent le filetage modal G63 et pour continuer à fileter il faudra reprogrammer la G63 avec le déplacement suivant. CNC 8070 (REF: 1901) ·67· S o l ut i o n s d ’ e r r e ur s . 1545 'On n'admet pas changement de gamme de broche avec G63 ou #CAX actifs' DÉTECTION CAUSE SOLUTION 1546 'On n'admet pas G63 sans gamme préalable sur la broche' DÉTECTION CAUSE SOLUTION 1547 SOLUTION SOLUTION SOLUTION SOLUTION CNC 8070 SOLUTION (REF: 1901) Au cours de l'exécution. Depuis le programme pièce ou le MDI le nom d’une variable a été écrit sans le préfixe "V". Ajouter le préfixe "V" au nom de la variable. 'Nombre de variables d'utilisateur dépassé' DÉTECTION CAUSE SOLUTION ·68· Au cours de l'exécution. L’emboîtement d’appels à sous-routines avec l'instruction #PCALL ou avec la fonction G180-G189 augmente le niveau d’imbrication de paramètres locaux. Il y a erreur parce que le niveau maximum d’imbrication de paramètres locaux (7) est dépassé. Réduire l’emboîtement de sous-routines ou utiliser les instructions #CALL, L ou LL pour les appeler, qui n’augmentent pas le niveau d’imbrication de paramètres locaux. 'Le nom de la variable doit commencer par "V"'. DÉTECTION CAUSE 1553 Au cours de l'exécution. La CNC a essayé d'activer un axe C avec un autre actif. Désactiver un axe C avant d'activer un autre. 'Imbrication des paramètres locaux dépassée' DÉTECTION CAUSE 1552 Au cours de l'exécution. Si en définissant une poche 2D ou 3D avec l’éditeur de cycles, le nom de la poche n’a pas été défini ou ce nom est incorrect. Les instructions #DATAP2D et #DATAP3D générées par l’éditeur de cycles ne sont pas permises comme nom de poche. Affecter à la poche un nom différent. 'Il n'est pas permis de programmer deux axes C dans le même canal' DÉTECTION CAUSE SOLUTION 1551 Au cours de l'exécution. Les fonctions G63 et G96 utilisent la broche master du canal. Le canal ne peut pas supprimer cette broche alors que les fonctions sont actives. Désactiver G63 ou G96 avant de céder la broche. 'Nom de la poche nul ou incorrect' DÉTECTION CAUSE 1550 Au cours de l'exécution. On ne peut pas activer une broche comme axe C si ce dernier est utilisé par la fonction G63. Désactiver G63 avant de désactiver l’axe C ou utiliser une autre broche du canal pour l’axe C. 'On ne peut pas changer la broche master avec G33/G63/G95/G96 actives' DÉTECTION CAUSE 1549 Au cours de l'exécution. Cette situation n’est possible que si après le démarrage du système ou une RAZ, le PLC n’indique aucune gamme avec GEAR1 à GEAR4 pour la broche. Alors la broche n’a aucune gamme active et si on ne travaille pas avec avant de programmer G63, la CNC ne générera pas non plus de gamme automatiquement. Avant de commencer un filetage G63 la broche doit avoir une gamme activée. Si la broche a le changement de gamme automatique (paramètre AUTOGEAR), la CNC génère la gamme en programmant une vitesse ; dans le cas contraire, il faut programmer la gamme (M41-M44) avec la vitesse. 'On n'admet pas #CAX avec G63 active' DÉTECTION CAUSE 1548 Au cours de l'exécution. La CNC ne peut pas changer la gamme de la broche si le filetage G63 est actif ou si la broche travaille comme axe C. Pour changer la gamme de la broche, désactiver le filetage et l’axe C. Au cours de l'exécution. La CNC a dépassé le nombre maximum de variables d’utilisateur (préfixes P et S) permises. Le nombre maximum de variables d’utilisateur permis est 20. S o l ut i o n s d ’ e r r e ur s . 1554 'Le PLC n’a pas reconnu START dans une instruction #EXEC' DÉTECTION CAUSE SOLUTION 1555 'Programmer #MOVE / #MOVE ABS/ADD/INF[...]' DÉTECTION CAUSE SOLUTION 1556 SOLUTION Au cours de l'exécution. Dans les instructions #CAM ou #FOLLOW, l'axe esclave est incorrect. L'axe doit appartenir au canal. 'La fonction G74 est programmée avec axes ou seule dans le bloc' DÉTECTION CAUSE SOLUTION 1564 Au cours de l'exécution. Dans les instructions #CAM ou #FOLLOW, l'axe maître est incorrect. L'axe doit appartenir au canal. 'Axe esclave non valide' DÉTECTION CAUSE SOLUTION 1563 Au cours de l'exécution. La syntaxe de l'instruction #FOLLOW est incorrecte. Réviser la programmation. Avec l'instruction il faut programmer une des commandes ON/OFF et ensuite les paramètres d’appel entre crochets. 'Axe maître non valide' DÉTECTION CAUSE SOLUTION 1562 Au cours de l'exécution. Dans l'instruction #CAM, le type de came est incorrect ; le type de came se définit avec les commandes ONCE (came non périodique) et CONT (came périodique). Réviser la programmation. 'Programmer #FOLLOW ON/OFF[...]' DÉTECTION CAUSE SOLUTION 1561 Au cours de l'exécution. Dans l'instruction #CAM, le numéro de la came est incorrect. Le numéro de came doit être compris entre 1 et le paramètre NCAMES. 'Programmer type de came: ONCE ou CONT' DÉTECTION CAUSE 1560 Au cours de l'exécution. La syntaxe de l'instruction #CAM est incorrecte. Réviser la programmation. Avec l'instruction il faut programmer une des commandes ON, OFF, SELECT ou DESELECT et ensuite les paramètres d’appel entre crochets. 'Numéro de came incorrect' DÉTECTION CAUSE SOLUTION 1559 Au cours de l'exécution. Dans l'instruction #MOVE, le type de liaison entre déplacements est incorrect. Réviser la programmation. 'Programmer #CAM ON/OFF/SELECT/DESELECT[...]' DÉTECTION CAUSE SOLUTION 1558 Au cours de l'exécution. La syntaxe de l'instruction #MOVE est incorrecte. Réviser la programmation. Avec l'instruction il faut programmer une des commandes ABS/ADD/INF et ensuite les paramètres d’appel entre crochets. 'Programmer type de liaison: PRESENT, NEXT, NULL, WAITINPOS' DÉTECTION CAUSE SOLUTION 1557 Au cours de l'exécution. Au moment de donner l’ordre d’exécution d’un programme dans un autre canal, le PLC doit approuver le démarrage de programme (START). En cas contraire cette erreur sera générée. Vérifier le programme de PLC. Au cours de l'exécution. Programmation incorrecte de la fonction G74. La fonction G74 peut être programmée bien avec les axes pour lesquels on veut réaliser la recherche de zéro ou bien seule dans le bloc. Si la fonction G74 est programmée seule dans le bloc, la CNC exécute sa sous-routine associée (paramètre REFPSUB). 'On ne peut pas programmer un axe stationné' DÉTECTION CAUSE SOLUTION CNC 8070 (REF: 1901) Au cours de l'exécution. L’instruction programmée ne peut pas être exécutée sur un axe stationné. Réviser la programmation. ·69· S o l ut i o n s d ’ e r r e ur s . 1565 'La broche ne peut pas travailler comme axe C, CAXIS = Non' DÉTECTION CAUSE SOLUTION 1566 'L’image miroir n’est pas admise avec les axes UNIDIR' DÉTECTION CAUSE SOLUTION 1567 SOLUTION SOLUTION SOLUTION SOLUTION SOLUTION CNC 8070 SOLUTION (REF: 1901) Au cours de l'exécution. Il s’est produit une erreur alors que l’oscilloscope essayait de lire la valeur de la variable assignée à l’un de ses canaux. Faire une RAZ à la CNC et capturer à nouveau l'enregistrement. 'Paramètre non modifiable depuis l’oscilloscope' DÉTECTION CAUSE SOLUTION ·70· Au cours de l'exécution. La CNC a essayé d’accéder à une variable de préparation d’outil d’un autre canal (préfixe "G" ou "A"). Les seules variables d’outils accessibles depuis un autre canal sont celles associées au gestionnaire (préfixe "TM"). 'Erreur en capturant échantillons de la variable' DÉTECTION CAUSE 1574 Au cours de l'exécution. Le caractère "%" est programmé dans une sous-routine globale, dans une ligne différente de celle de la définition du nom de la sous-routine. Réviser la programmation. 'Variable accessible uniquement pour son canal' DÉTECTION CAUSE 1573 Au cours de l'exécution. Une fonction M de déplacement de broche et la fonction G74 de recherche de zéro ont été programmées dans le même bloc. Réviser la programmation. 'Le caractère "%" n'est pas admis dans la sous-routine principale' DÉTECTION CAUSE 1572 Au cours de l'exécution. Lorsque le canal est uniquement de PLC, la CNC n’a pas de permission pour y exécuter des programmes, des blocs de MDI, des déplacements de jog ou toute autre action depuis le mode manuel. Pour exécuter ces actions dans ce canal, il faut le configurer comme canal de CNC ou de CNC+PLC (paramètre CHTYPE). 'G74 et le déplacement de la broche ne sont pas permis simultanément' DÉTECTION CAUSE 1571 Au cours de l'exécution. Le numéro de magasin programmé dans la commande MZ n’est pas valide. Le numéro de magasin doit être une valeur entre 1 et 4. 'Exécution interdite, le canal est exclusif du PLC' DÉTECTION CAUSE 1570 Au cours de l'exécution. Le rayon d’un déplacement en coordonnées polaires est programmé avec le paramètre R1 ou avec la fonction G263. Programmer le rayon polaire avec le paramètre R. 'Numéro de magasin incorrect' DÉTECTION CAUSE SOLUTION 1569 Au cours de l'exécution. On ne peut pas programmer d’image miroir sur un axe rotatif unidirectionnel (paramètre UNIDIR), étant donné que ce type d’axes ne peut pas tourner dans le sens contraire à celui défini. Changer le type d’axe ou ne pas programmer l’image miroir. 'Le rayon polaire ne peut s'utiliser qu'avec R' DÉTECTION CAUSE 1568 Au cours de l'exécution. Une broche qui n’a pas de permission pour travailler comme axe C (paramètre CAXIS) a été programmée dans l’instruction #CAX,. Réviser la programmation. Au cours de l'exécution. L’utilisateur a essayé de modifier depuis l’écran de l’oscilloscope un paramètre machine qui n’a pas de permission d’écriture. Ce paramètre ne peut être modifié que depuis la table de paramètres machine. S o l ut i o n s d ’ e r r e ur s . 1575 'L'instruction n'est valide que sur les programmes avec l’extension FBS' DÉTECTION CAUSE SOLUTION 1576 'On n'attend pas "]"' DÉTECTION CAUSE SOLUTION 1577 SOLUTION SOLUTION SOLUTION SOLUTION SOLUTION Au cours de l'exécution. L’instruction NR est programmée plus d’une fois dans le même bloc. Réviser la programmation. '#FOLLOW ON: l'axe maître et l'esclave ne peuvent pas être égaux' DÉTECTION CAUSE SOLUTION 1584 Au cours de l'exécution. Les instructions #SET AX et #FREE AX ne peuvent pas supprimer l’axe C de la configuration s’il est actif. Désactiver l’axe C avant de le supprimer de la configuration. 'NR: double programmation du nombre de répétitions. DÉTECTION CAUSE SOLUTION 1583 Au cours de l'exécution. La CNC a essayé de faire activer une broche Sercos comme axe C sans l’avoir positionnée avant avec M19. Programmer M19 avant d'activer la broche comme axe C. 'Il n’est pas permis d’éliminer un axe C actif' DÉTECTION CAUSE 1582 Au cours de l'exécution. La CNC a exécuté une fonction G74 sur l’axe maître d’un couplage avec plusieurs esclaves. Défaire le couplage d’axes et effectuer la recherche de référence des axes séparément. '#CAX: On a besoin de la programmation de M19 en Sercos de position' DÉTECTION CAUSE 1581 Au cours de l'exécution. La CNC a essayé d’activer un couplage (#LINK) avec deux axes rotatifs unidirectionnels qui ne sont pas égaux. Lorsque les axes sont unidirectionnels, les deux axes doivent avoir le même sens de rotation prédéterminée (paramètre UNIDIR). 'Il n’est pas permis de faire la recherche de zéro sur l’axe maître avec plusieurs esclaves' DÉTECTION CAUSE 1580 Au cours de l'exécution. Le paramètre qui définit le type de synchronisation dans l'instruction #FOLLOW est incorrect. Réviser la programmation. Le paramètre peut prendre les valeurs VEL (vitesse) et POS (position). '#LINK: Un axe esclave UNIDIR doit être du même type que le maître (UNIDIR)' DÉTECTION CAUSE 1579 Au cours de l'exécution. Erreur dans la syntaxe de l'instruction. Réviser la programmation. 'Programmer type de synchronisation: VEL ou POS' DÉTECTION CAUSE 1578 Au cours de l'exécution. Programmation des instructions #SPLINE ou #BSPLINE. Ces instructions ne sont valides que dans des programmes avec extension fbs. Au cours de l'exécution. Les axes maître et esclave sont le même axe. Réviser la programmation. '#FOLLOW ON: le numérateur et le dénominateur doivent être des nombres entiers' DÉTECTION CAUSE SOLUTION Au cours de l'exécution. Le numérateur et/ou dénominateur sont programmés avec des décimales. Programmer des nombres entiers dans les paramètres qui définissent le numérateur et le dénominateur du rapport de transmission. CNC 8070 (REF: 1901) ·71· S o l ut i o n s d ’ e r r e ur s . 1585 'Les axes de la transformation active ne peuvent pas être des axes d'échange temporaire. DÉTECTION CAUSE SOLUTION 1586 'Le numéro de magasin (MZ) n'et pas programmé' DÉTECTION CAUSE SOLUTION 1587 SOLUTION SOLUTION SOLUTION SOLUTION 1593 Au cours de l'exécution. Dans la synchronisation de broches, la valeur du dénominateur du rapport de transmission n’est pas valide ; par exemple, elle est zéro. La valeur peut être positive ou négative, pas nécessairement entière, mais différente de zéro. 'La broche esclave à désynchroniser doit appartenir au canal' DÉTECTION CAUSE (REF: 1901) SOLUTION ·72· Au cours de l'exécution. Dans la synchronisation de broches, la valeur du numérateur du rapport de transmission n’est pas valide ; par exemple, elle est zéro. La valeur peut être positive ou négative, pas nécessairement entière, mais différente de zéro. 'Dénominateur non valide' DÉTECTION CAUSE CNC 8070 Au cours de l'exécution. La syntaxe de l'instruction n’est pas correcte ou il y a plus d’information dans le bloc. Réviser la programmation. 'Numérateur non valide' DÉTECTION CAUSE 1592 Au cours de l'exécution. Dans la synchronisation, la broche esclave est la même que le maître. Réviser la programmation. 'Programmer #SYNC[Sm,Ss,Nx,Dx,Ox,CLOOP/OLOOP,CANCEL/NOCANCEL]' DÉTECTION CAUSE SOLUTION 1591 Au cours de l'exécution. La broche master d’une synchronisation peut être de n’importe quel canal, mais la broche esclave doit être du canal dans lequel la synchronisation a été programmée. Synchroniser la broche esclave depuis son canal, l’ajouter à la configuration du canal actuel ou utiliser une autre broche du canal comme esclave. 'La broche esclave ne peut pas coïncider avec le maître' DÉTECTION CAUSE SOLUTION 1590 Au cours de l'exécution. Le paramètre machine n’a pas de permission d’écriture, depuis l’environnement de mise au point. Le paramètre machine pourra être modifié directement dans la table de paramètres machine. 'La broche esclave à synchroniser doit appartenir au canal' DÉTECTION CAUSE 1589 Au cours de l'exécution. Dans un système avec plusieurs magasins, l’outil et la position sont programmés dans le même bloc, mais pas le magasin où l’on veut envoyer cet outil. Dans un système multi-magasins, il faut programmer dans le même bloc l’outil, la position et le magasin. 'Paramètre non modifiable depuis la mise au point' DÉTECTION CAUSE 1588 Au cours de l'exécution. Les axes de la transformée ne peuvent pas être des axes d’échange temporaire, car la transformée définie est maintenue une fois activée. Si cela est possible, définir les axes comme d’échange maintenu, sinon utiliser d’autres axes pour la transformée. Les axes d’échange temporaire ne peuvent être utilisés que dans leur canal et lorsque les axes sont sur leurs positions originales dans le canal. Dans les transformées #FACE et #CYL des axes d’échange temporaire peuvent être utilisés du fait que ces transformées sont annulées avec M30 et après une RAZ. Au cours de l'exécution. Un canal ne peut pas annuler la synchronisation d’une broche esclave appartenant à un autre canal. Annuler la synchronisation depuis le canal auquel appartient la broche. S o l ut i o n s d ’ e r r e ur s . 1594 'La broche esclave est synchronisée à une autre broche' DÉTECTION CAUSE SOLUTION 1595 'Une broche ne peut pas être en même temps master et esclave d'une synchronisation' DÉTECTION CAUSE SOLUTION 1596 SOLUTION SOLUTION SOLUTION SOLUTION SOLUTION SOLUTION Au cours de l'exécution. La CNC a essayé de stationner une broche qui n’est pas arrêtée. Arrêter la broche avant le stationnement. 'FOLLOW OFF: Programmer l’axe esclave' DÉTECTION CAUSE SOLUTION 1604 Au cours de l'exécution. Les instructions #SET SP et #FREE SP ne peuvent pas supprimer une broche si elle est synchronisée. Annuler la synchronisation pour supprimer la broche de la configuration. 'Pour stationner une broche celle-ci doit être arrêtée (M5)' DÉTECTION CAUSE SOLUTION 1603 Au cours de l'exécution. La CNC a essayé de synchroniser une broche et celle-ci travaille comme axe C ou la fonction G63 est active. La CNC a essayé d’activer la broche comme axe C ou la fonction G63 et la broche est synchronisée. Désactiver l’axe C ou la fonction G63 pour synchroniser les broches. Pour travailler avec l’axe C ou la fonction G63, annuler la synchronisation de broches. 'On n'admet pas libérer une broche synchronisée' DÉTECTION CAUSE 1602 Au cours de l'exécution. Pendant la synchronisation de deux broches, la CNC ne permet le changement de gamme sur aucune d’elles. Annuler la synchronisation pour changer la gamme de la broche. 'Une broche synchronisée ne peut pas travailler comme axe C ou en G63' DÉTECTION CAUSE 1601 Au cours de l'exécution. Une vitesse S ou une fonction M est programmée pour la broche esclave d’une synchronisation. Supprimer cette programmation ou désynchroniser la broche. 'On n'admet pas le changement de gamme dans les broches synchronisées' DÉTECTION CAUSE 1600 Au cours de l'exécution. On ne peut pas synchroniser simultanément une broche esclave à deux maîtres différents. Décider laquelle des deux synchronisations on veut activer. 'On ne peut pas programmer une broche esclave pendant la synchronisation' DÉTECTION CAUSE 1599 Au cours de l'exécution. La CNC a essayé de désynchroniser une broche esclave qui n’est pas actuellement synchronisée. Réviser la programmation. 'On ne peut pas synchroniser la même broche esclave à deux maîtres' DÉTECTION CAUSE 1598 Au cours de l'exécution. La broche esclave d’une synchronisation est la broche maître d’une autre. Réviser la programmation. 'La broche n’est pas synchronisée' DÉTECTION CAUSE 1597 Au cours de l'exécution. La broche esclave est synchronisée à une autre broche. Une broche ne peut esclave que d'un axe maître. Défaire la synchronisation précédente ou synchroniser une autre broche disponible. Au cours de l'exécution. L’axe programmé n’est esclave dans aucune synchronisation. Réviser la programmation. 'G31 demande G02/G03 actives' DÉTECTION CAUSE SOLUTION CNC 8070 (REF: 1901) Au cours de l'exécution. La fonction G31 ne peut être programmée que s’il existe une interpolation circulaire active. Programmer G02/G03 dans le bloc de G31. ·73· S o l ut i o n s d ’ e r r e ur s . 1605 'G31 exige programmation de l'angle polaire et centre d'interpolation' DÉTECTION CAUSE SOLUTION 1606 '#ANGAX: Les axes angulaire et orthogonal doivent appartenir au même canal' DÉTECTION CAUSE SOLUTION 1607 SOLUTION SOLUTION SOLUTION SOLUTION SOLUTION SOLUTION 1613 SOLUTION ·74· Au cours de l'exécution. La CNC a essayé de supprimer du canal les axes qui formaient la transformation angulaire. Désactiver la transformation angulaire avant de supprimer les axes du canal. 'La transformation angulaire #ANGAX est désactivée' DÉTECTION CAUSE (REF: 1901) Au cours de l'exécution. La CNC a essayé de changer le plan de travail dans un tour avec configuration d’axes type plan. Dans un tour avec configuration d’axes type plan, le plan actif est toujours G18. Pour changer l’axe longitudinal uniquement, utiliser la fonction G20. 'Les axes de la transformation angulaire active #ANGAX, ne peuvent pas être exclus' DÉTECTION CAUSE CNC 8070 Au cours de l'exécution. Une broche configurée comme Sercos position ne peut pas être synchronisée en boucle fermée. Utiliser une autre broche comme maître. 'Dans le modèle TOUR XZ il n’y à pas de changement de plan actif' DÉTECTION CAUSE 1612 Au cours de l'exécution. Un cycle de tour est programmé dans un canal avec moins de deux axes ou bien le premier axe n’est pas longitudinal (paramètre LONGAXIS) ou le deuxième axe n’est pas frontal (paramètre FACEAXIS). Deux axes dans le canal sont nécessaires pour exécuter les cycles de tour. 'Une broche master SERCOS en POSITION n’admet pas CLOOP' DÉTECTION CAUSE 1611 Au cours de l'exécution. Certaines commandes et instructions de CNC n’admettent pas la lecture de variables qui impliquent une synchronisation entre la préparation et l’exécution de blocs. Pour éviter cette erreur, assigner la valeur de la variable à un paramètre arithmétique local et lire ce paramètre lorsque cela sera nécessaire. 'Pour exécuter un cycle de tour ils sont nécessaires deux axes dans le canal' DÉTECTION CAUSE 1610 Au cours de l'exécution. Un cycle de machine à fraiser est programmé dans un canal avec moins de trois axes ou l’axe longitudinal n’existe pas. Trois axes dans le canal sont nécessaires pour exécuter les cycles de machine à fraiser. 'Il est impossible de consulter cette variable. Affecter la valeur de la variable à Pn et consulter Pn. DÉTECTION CAUSE 1609 Au cours de l'exécution. La CNC a essayé d’activer une transformation angulaire avec deux axes qui n’appartiennent pas au même canal. Les axes d’une transformation angulaire doivent appartenir au même canal. 'Pour exécuter un cycle de fraiseuse ils sont nécessaires trois axes principaux dans le canal' DÉTECTION CAUSE 1608 Au cours de l'exécution. L’angle polaire ou une coordonnée du centre doit être programmé dans la fonction G31. Réviser la programmation. Au cours de l'exécution. La CNC a supprimé du canal les axes qui formaient la transformation angulaire et celle-ci a été désactivée. La transformation angulaire est désactivée; pour l'activer, remettre dans le canal les axes formant la transformation angulaire. S o l ut i o n s d ’ e r r e ur s . 1614 'Programmation interdite avec la transformation angulaire #ANGAX active' DÉTECTION CAUSE SOLUTION 1615 'On ne peut pas activer l'axe comme Hirth, car il fait partie de la transformation #ANGAX'. DÉTECTION CAUSE SOLUTION 1616 SOLUTION Au cours de l'exécution. Un paramètre Q1 sans G33 est programmé dans le bloc ou sans la fonction G63 active. Le paramètre Q doit aller dans le même bloc que G33. Le paramètre Q ne peut être seul dans le bloc que si la fonction G63 est active. 'Une broche d'échange temporaire ne peut pas fonctionner comme axe C maintenu' DÉTECTION CAUSE SOLUTION 1623 Au cours de l'exécution. L'axe ou broche est Sercos position. Cette instruction ne permet que des axes Sercos vitesse. 'Q1 n'est pas admis sans G33 dans le bloc ou G63 active' DÉTECTION CAUSE 1622 Au cours de l'exécution. Le paramètre Q1 est programmé plus d’une fois dans le même bloc. Réviser la programmation. 'On n'admet pas #SERVO ON pour axe ou broche SERCOS POSITION' DÉTECTION CAUSE SOLUTION 1621 Au cours de l'exécution. Le paramètre Q est programmé plus d’une fois dans le même bloc. Réviser la programmation. 'Valeur Q1 programmée en double' DÉTECTION CAUSE SOLUTION 1620 Au cours de l'exécution. L’indice du paramètre Q est incorrect ; on n'admet que Q ou Q1. Réviser la programmation. Pour la programmation en polaires, utiliser le paramètre Q. Pour la fonction G33, utiliser le paramètre Q1. 'Valeur Q programmée en double. ' DÉTECTION CAUSE SOLUTION 1619 Au cours de l'exécution. Il y a un rayon polaire défini pour la fonction G31. La fonction G31 n'admet pas la programmation du rayon polaire. La fonction G31 n'admet que des coordonnées polaires de la forme G31 Q I J; c'est-à-dire en programmant l'angle et l'une ou les deux coordonnées du centre. 'Indice de Q interdit' DÉTECTION CAUSE SOLUTION 1618 Au cours de l'exécution. La CNC a essayé d’activer un axe hirth qui fait partie de la transformation angulaire active. Désactiver la transformation angulaire pour activer l’axe hirth. 'G31 ne permet pas la programmation du rayon polaire' DÉTECTION CAUSE SOLUTION 1617 Au cours de l'exécution. La CNC a essayé d’exécuter une fonction incompatible avec la transformation angulaire, par exemple une recherche de zéro (G74), modifier les limites de logiciel (G198 - G199), instruction #OSC. Désactiver la transformation angulaire active pour exécuter les fonctions incompatibles. Au cours de l'exécution. La CNC peut activer comme axe C maintenu (paramètre PERCAX) une broche d’échange temporaire. Si cela est possible, définir la broche comme d’échange maintenu, sinon utiliser une autre broche comme axe C. CNC 8070 'Gamme de synchronisation SYNCSET non valide' DÉTECTION CAUSE SOLUTION Au cours de l'exécution. Le paramètre SYNCSET à une valeur non valide. Affecter au paramètre une valeur correcte. (REF: 1901) ·75· S o l ut i o n s d ’ e r r e ur s . 1624 'Programmer #TANGCTRL ON/OFF/SUSP [ ]' DÉTECTION CAUSE SOLUTION 1625 'Un axe en contrôle tangentiel actif doit être rotatif non HIRTH et ne pas appartenir au trièdre actif' DÉTECTION CAUSE SOLUTION 1626 SOLUTION SOLUTION SOLUTION SOLUTION CNC 8070 1633 Au cours de l'exécution. La CNC a essayé d’activer le contrôle tangentiel sur un axe rotatif de module différent de 360º. Le contrôle tangentiel ne peut être activé que sur les axes rotatifs avec module 360º. La limite supérieure du module est définie par le paramètre MODUPLIM et la limite inférieure par le paramètre MODLOWLIM. 'Programmer: #DGSPSL <nom de la broche>' DÉTECTION CAUSE SOLUTION ·76· Au cours de l'exécution. Dans l’appel au cycle, les paramètres définissant le commencement et la fin du profil (paramètres S et E), la sous-routine contenant le profil (paramètre P) ou le fichier contenant le profil (paramètre Q) ont été incorrectement désignés. Réviser la programmation. 'Un axe en contrôle tangentiel actif doit être rotatif avec module 360º' DÉTECTION CAUSE SOLUTION (REF: 1901) Au cours de l'exécution. Dans l’appel au cycle, les paramètres qui définissent le commencement et la fin du profil (paramètres S et E) ont été incorrectement désignés. Affecter une valeur correcte aux paramètres S et E. 'Programmation de profil interdite: [S,E,<Q>] ou [P,<Q>]' DÉTECTION CAUSE 1632 Au cours de l'exécution. Avec le contrôle tangentiel actif, un déplacement ou une autre opération pour l’axe tangentiel est programmé. Avec le contrôle tangentiel actif, on ne peut pas programmer des déplacements de l’axe tangentiel; c’est la CNC qui se charge d’orienter cet axe. Pour utiliser cet axe, annuler le contrôle tangentiel. 'Programmation de profil incorrecte avec des étiquettes' DÉTECTION CAUSE 1631 Au cours de l'exécution. La CNC ne peut pas supprimer l’axe tangentiel de la configuration si le contrôle tangentiel est actif. Pour supprimer cet axe de la configuration, annuler le contrôle tangentiel. 'On ne peut pas programmer un axe en contrôle tangentiel' DÉTECTION CAUSE 1630 Au cours de l'exécution. L'angle programmé dans l'instruction est incorrect. Réviser la programmation. La valeur de l’angle doit être entre 0 et ±359.9999. 'On ne peut pas éliminer de la configuration un axe avec contrôle tangentiel actif' DÉTECTION CAUSE 1629 Au cours de l'exécution. Dans l'instruction il faut programmer l'axe ou axes. Réviser la programmation. '#TANGCTRL: programmer les valeurs de l'angle entre 0 et +/-359.9999' DÉTECTION CAUSE SOLUTION 1628 Au cours de l'exécution. Les axes à activer sur le contrôle tangentiel doivent être rotatifs, non hirth et ne doivent pas faire partie du trièdre actif ni être l’axe longitudinal. Réviser la programmation. 'Programmer un axe pour #TANGCTRL ON/OFF/SUSP/RESUME' DÉTECTION CAUSE SOLUTION 1627 Au cours de l'exécution. La syntaxe de l'instruction n’est pas correcte ou il y a plus d’information dans le bloc. Réviser la programmation. Avec l'instruction il faut programmer une des commandes ON/SUSP/OFF et ensuite les paramètres d’appel entre crochets. On peut aussi programmer une des commandes SUSP/OFF sans paramètres d’appel. Au cours de l'exécution. La syntaxe de l'instruction n’est pas correcte ou il y a plus d’information dans le bloc. Réviser la programmation. S o l ut i o n s d ’ e r r e ur s . 1634 'L'instruction #MOVE n'admet qu'un axe et doit appartenir au canal' DÉTECTION CAUSE SOLUTION 1635 'Le nombre d'axes dans la transformation dépasse celui permis' DÉTECTION CAUSE SOLUTION 1636 SOLUTION Au cours de l'exécution. Il manque la valeur du rayon de développement dans l'instruction #CYL. Vérifier la programmation pour un rayon variable, définir la valeur zéro pour que la CNC calcule le rayon en fonction d’où se trouve l’outil. 'Il n'est pas permis de programmer les broches esclaves TANDEM' DÉTECTION CAUSE SOLUTION 1643 Au cours de l'exécution. La CNC a essayé d'utiliser une broche stationnée. Utiliser une broche non stationnée ou arrêter le stationnement de la broche. '#CYL: On attend la programmation du rayon de développement du cylindre' DÉTECTION CAUSE SOLUTION 1642 Au cours de l'exécution. La CNC a essayé d'utiliser une broche d'un autre canal. Un canal ne peut commander que ses broches. Utiliser une broche appartenant au canal ou inclure dans la configuration du canal la broche indiquant l'erreur. 'Il est interdit de programmer les broches stationnées' DÉTECTION CAUSE SOLUTION 1641 Au cours de l'exécution. La CNC a essayé d’activer une transformation angulaire avec un axe rotatif. Les axes de la transformation angulaire doivent être linéaires. 'La broche programmée n’appartient pas au canal' DÉTECTION CAUSE SOLUTION 1640 Au cours de l'exécution. Le sens de rotation prédéterminé de l’outil est incompatible avec le sens de rotation actuel de la broche. Changer le sens de rotation de la broche ou corriger le sens de rotation défini pour l’outil. 'Les axes de la transformation angulaire, #ANGAX, doivent être linéaires' DÉTECTION CAUSE SOLUTION 1639 Au cours de l'exécution. La CNC essayé d’activer l'instruction #FACE ou #CYL avec une d’elles active. Désactiver une instruction avant d'activer l'autre. 'Sens de rotation de la broche incompatible avec l'outil' DÉTECTION CAUSE 1638 Au cours de l'exécution. La transformation de coordonnées a plus d’axes définis dans le paramètre NKINAX que ceux permis dans la CNC. Corriger le paramètre machine NKINAX. 'Les transformées FACE et CYL ne peuvent pas être actives en même temps' DÉTECTION CAUSE SOLUTION 1637 Au cours de l'exécution. Le nom d’axe programmé n'est pas correct, l’axe est dans un autre canal ou n’est pas un axe du système. La programmation de broches n’est pas permise, sauf en travaillant comme axe C et dans ce cas elle doit être programmée avec le nom de l’axe C. Réviser la programmation. Au cours de l'exécution. L’utilisateur a essayé de déplacer ou de faire référence à la broche esclave d’un couple tandem. La broche esclave d’un couple tandem est commandée par la CNC, elle ne peut pas se déplacer individuellement. Pour déplacer une broche esclave, il faut déplacer la broche à laquelle il se trouve associée. CNC 8070 'Il est interdit de stationner les broches TANDEM' DÉTECTION CAUSE SOLUTION Au cours de l'exécution. La CNC a essayé de stationner une broche appartenant à un couple tandem. Il est interdit de stationner les broches tandem. (REF: 1901) ·77· S o l ut i o n s d ’ e r r e ur s . 1644 'Il est interdit de stationner les broches en G33/G95' DÉTECTION CAUSE SOLUTION 1645 'Impossible #RET/M17/M29 entre les étiquettes d'un #RPT' DÉTECTION CAUSE SOLUTION 1646 SOLUTION SOLUTION SOLUTION SOLUTION SOLUTION CNC 8070 SOLUTION 1655 Au cours de l'exécution. Avec le bus Sercos, l'anneau n'et pas dans la phase 4. Avec le Mechatrolink, le bus n'a pas atteint la phase 3. L'anneau Sercos n'est pas en phase 4. Conditionner l’écriture de la variable à la marque SERCOSRDY en Sercos ou à la marque MLINKRDY dans Mechatrolink. 'Le bus numérique (Sercos/Mechatrolink) n'est pas prêt pour l'écriture de la variable' DÉTECTION CAUSE SOLUTION ·78· Au cours de l'exécution. La CNC a essayé de définir comme axe esclave d’un couplage un axe faisant partie du plan incliné. Désactiver le plan incliné pour pouvoir activer le couplage. Un axe faisant partie d’un plan incliné ne peut pas être l’axe esclave dans un couplage ; par contre l’axe maître d’un couplage peut l’être. 'Le bus numérique (Sercos/Mechatrolink) n'est pas prêt pour la lecture de la variable' DÉTECTION CAUSE (REF: 1901) Au cours de l'exécution. La CNC ne peut pas accoupler des axes avec permission d’échange temporaire (paramètre AXISEXCH) s’ils n’appartiennent pas à un autre canal et si les couplages du canal sont définis comme maintenus (paramètre LINKCANCEL). Accoupler les axes dans son canal. 'Un axe de la transformation du plan incliné ne peut pas être esclave' DÉTECTION CAUSE 1654 Au cours de l'exécution. Il manque la fonction de coordonnées McsToPcs en essayant de réaliser la transformation de coordonnées machine à pièce dans une cinématique d’utilisateur. Vérifier le processus d’intégration de cinématiques d’utilisateur. 'On n'admet pas LINK maintenu avec les axes temporaires d'un autre canal' DÉTECTION CAUSE 1653 Au cours de l'exécution. Il manque la fonction de coordonnées PcsToMcs en essayant de réaliser la transformation de coordonnées pièce à machine dans une cinématique d’utilisateur. Vérifier le processus d’intégration de cinématiques d’utilisateur. 'On ne trouve pas la fonction de transformation directe d'utilisateur' DÉTECTION CAUSE 1651 Au cours de l'exécution. Un changement de gamme est programmé sur un axe ou une broche tandem. La gamme existe sur l’axe ou sur la broche maître mais pas sur l’esclave. Définir les mêmes gammes sur les axes et les broches maître et esclave du tandem. 'On ne trouve pas la fonction de transformation inverse d'utilisateur' DÉTECTION CAUSE 1650 Au cours de l'exécution. La syntaxe de l'instruction n’est pas correcte ou il y a plus d’information dans le bloc. Réviser la programmation. Les instructions doivent être programmées seules dans le bloc et on ne peut ajouter que l’étiquette du bloc. 'La gamme n'existe pas dans l'esclave TANDEM' DÉTECTION CAUSE 1649 Au cours de l'exécution. La CNC a détecté une fonction M17, M29 ou #RET entre les étiquettes initiale et finale d’une répétition de blocs #RPT. On ne peut pas terminer une sous-routine dans une répétition de blocs. 'Programmer: #ABORT [étiquette]/#ABORT Nxxxx/#ABORT OFF' DÉTECTION CAUSE SOLUTION 1647 Au cours de l'exécution. La CNC a essayé de stationner une broche avec la fonction G33 ou G95 active. Désactiver G33 et G95 avant de stationner une broche. Au cours de l'exécution. Avec le bus Sercos, l'anneau n'et pas dans la phase 4. Avec le Mechatrolink, le bus n'a pas atteint la phase 3. Conditionner l’écriture de la variable à la marque SERCOSRDY en Sercos ou à la marque MLINKRDY dans Mechatrolink. S o l ut i o n s d ’ e r r e ur s . 1656 'Un des axes du plan est en diamètres' DÉTECTION En simulant ou en exécutant sur un tour un cycle fixe de fraiseuse contenant des déplacements sur les axes du plan. CAUSE Les données des cotes des cycles fixes de fraiseuse sont considérées en rayons. Si l'un des axes du plan est en diamètres, la CNC interprète ses données comme des rayons et avise l’utilisateur au cas où il les programmerait en diamètres. EN CONSÉQUENCELe cycle peut exécuter une géométrie différente de celle attendue. SOLUTION Programmer les données en rayons. 1657 'Variable non valable pour broche qui ne soit pas axe C' DÉTECTION CAUSE SOLUTION 1658 'Numéro de magasin non valable' DÉTECTION CAUSE SOLUTION 1659 SOLUTION Au cours de l'exécution. Il faut indiquer les variables à supprimer dans l'instruction #DELETE. Indiquer avec l'instruction #DELETE les variables à supprimer. 'La fonction G174 n'admet qu'un axe ou une broche' DÉTECTION CAUSE SOLUTION 1666 Au cours de l'exécution. Il n’existe pas le type de variable programmé. Réviser la programmation. Vérifier la syntaxe de la variable. '#DELETE: Il faut indiquer variable(s) à supprimer' DÉTECTION CAUSE SOLUTION 1665 Au cours de l'exécution. Le numéro de canal doit être entre crochets et suivi du caractère ".". Réviser la programmation. Vérifier la syntaxe de la variable. 'Type inconnu de variable' DÉTECTION CAUSE SOLUTION 1663 Au cours de l'exécution. Un indice d’array programmé dans la variable est hors de gamme. Réviser la programmation. Consulter la variable et sa gamme de valeurs. 'Il reste à programmer "." après [numéroCanal]' DÉTECTION CAUSE SOLUTION 1662 Au cours de l'exécution. La macro existe déjà ; elle a été définie avec la commande #DEF FIX. Rappeler que la table de macros ne s’initialise pas avec le commencement et la fin de programme, mais uniquement avec l'instruction #INIT MACROTAB. Définir la macro avec un nom différent. Les macros définies avec la commande #DEF FIX ne sont pas supprimées après une RAZ. Utiliser la commande #INIT MACROTAB pour recommencer la table de macros, ce qui supprime les macros définies avec #DEF et avec #DEF FIX. 'Indice d’array incorrect' DÉTECTION CAUSE SOLUTION 1661 Au cours de l'exécution. Le numéro de magasin n'est pas valide. Réviser la programmation. Le nombre de magasins est défini dans le paramètre NTOOLMZ. 'Macro définie auparavant au moyen du paramètre #DEF FIX' DÉTECTION CAUSE 1660 Au cours de l'exécution. La CNC a essayé de lire une variable d’axe mais la broche n’est pas activée comme axe C. La variable n’existe que pour des axes et des broches travaillant comme axe C. Au cours de l'exécution. Dans la fonction G174 est programmé plus d'un axe ou broche. Programmer une fonction G174 par chaque axe ou broche. CNC 8070 'G174: on n'admet pas des axes accouplés, GANTRY ou TANDEM' DÉTECTION CAUSE SOLUTION Au cours de l'exécution. La CNC a essayé d’initialiser la cote machine (G174) d’un axe faisant partie d’un couple d’axes gantry, tandem ou d’un couplage actif (#LINK). Pour initialiser la cote machine sur cet axe, désactiver le couplage. On ne peut pas initialiser la cote machine d’axes gantry ou tandem. (REF: 1901) ·79· S o l ut i o n s d ’ e r r e ur s . 1667 'G174: On n'admet pas des axes de la cinématique ou les transformées actives' DÉTECTION CAUSE SOLUTION 1668 'Groupe multi-axe hors de rang' DÉTECTION CAUSE SOLUTION 1669 SOLUTION SOLUTION SOLUTION SOLUTION 1678 Au cours de l'exécution. La CNC a essayé de faire une recherche de référence avec la fonction #RTCP ou #TLC active. Pour exécuter une recherche de référence, il faut désactiver les fonctions #RTCP/TLC. ' Variable existante uniquement pour la mesure externe analogique' DÉTECTION CAUSE (REF: 1901) SOLUTION ·80· Au cours de l'exécution. Après la mise sous tension, la CNC a récupéré le plan incliné qui était actif à la mise hors tension. Le plan incliné peut être désactivé avec l'instruction #CS OFF. '#RTCP/TLC a été désactivé' DÉTECTION CAUSE CNC 8070 Au cours de l'exécution. La syntaxe de l'instruction n’est pas correcte ou il y a plus d’information dans le bloc. Réviser la programmation. 'Le plan incliné actif a été récupéré' DÉTECTION CAUSE 1677 Au cours de l'exécution. La variable programmée, bien qu'elle existe, n’a pas de permission d’accès depuis le programme. Consulter dans les manuels les permissions d’accès des variables. 'Programmer #SELECT PROBE [ Nº palpeur, POS/NEG]' DÉTECTION CAUSE SOLUTION 1676 Au cours de l'exécution. Une fois la synchronisation de broches réalisée, la CNC ne permet pas de programmer une recherche de zéro ni de forcer de cote sur aucune broche. La CNC référence les broches avant de les synchroniser. Pour réaliser une nouvelle recherche de référence ou forcer la cote, désactiver la synchronisation. 'Variable non accessible par programme ou MDI' DÉTECTION CAUSE 1674 Au cours de l'exécution. L'instruction #ROTATEMZ n’est valide que pour un magasin de type tourelle. Réviser la programmation. Vérifier que le magasin est de type tourelle. 'G74-G174 n'est pas admis pour les broches synchronisées' DÉTECTION CAUSE 1673 Au cours de l'exécution. La syntaxe de l'instruction n’est pas correcte ou il y a plus d’information dans le bloc. Réviser la programmation. Programmer la position à sélectionner sur la tourelle ou le nombre de positions à tourner. 'Le magasin indiqué doit être type TOURELLE' DÉTECTION CAUSE SOLUTION 1672 Pendant la lecture de variables (V.)MPA.MULAXISNAMEn[groupe]. L’indice (groupe) ne correspond à aucun groupe multi-axe défini dans les paramètres machine. Réviser la programmation. Programmer adéquatement le numéro du groupe multiaxe. 'Programmer #ROTATEMZ1-4 Pn/+n/-n' DÉTECTION CAUSE SOLUTION 1670 Au cours de l'exécution. La CNC a essayé d’initialiser la cote machine (G174) d’un axe faisant partie de la cinématique active ou des transformées #CS, #ACS, #ANGAX, #TANGCTRL. Pour initialiser la cote machine sur cet axe, désactiver la cinématique ou la transformation active. Au cours de l'exécution. La variable programmée n’existe que pour des axes avec mesure externe analogique et l’axe indiqué ne remplit pas cette condition. Réviser la programmation. Consulter dans les manuels les variables accessibles suivant le type d’axe. S o l ut i o n s d ’ e r r e ur s . 1679 '#CAM SELECT n'est pas admis avec la came en exécution ou en processus de chargement' DÉTECTION CAUSE SOLUTION 1680 'Numéro de pièce non valide' DÉTECTION CAUSE SOLUTION 1681 SOLUTION SOLUTION Au cours de l'exécution. L'instruction #REPOS est mal programmée. L'instruction #REPOS peut inclure un paramètre optionnel INT ou INI, suivi d’une séquence d’axes et/ou de broches du canal sans un ordre déterminé. 'Les instructions #REPOS de différent type ne sont pas admises' DÉTECTION CAUSE SOLUTION 1689 Au cours de l'exécution. L’instruction $GOTO n’est pas dans une boucle mais est en train de sauter à une étiquette définie dans une boucle $IF, $FOR, etc. Réviser la programmation. Il est interdit de réaliser des sauts à l'intérieur d'une boucle. 'Programmer: #REPOS <INT/INI> <séquence d'axes/broches>' DÉTECTION CAUSE SOLUTION 1688 Au cours de l'exécution. Un même bloc de programme est en train d’exécuter un appel à une sous-routine locale et une fonction M, T ou G avec une sous-routine associée. Programmer l’appel à la sous-routine locale dans un autre bloc de programme. '$GOTO: Saut aux blocs imbriqués dans $IF, $FOR, $WHILE... interdit' DÉTECTION CAUSE 1687 Au cours de l'exécution. L’instruction #REPOS n’est pas programmée dans une sous-routine d’interruption. Il n'est permis de programmer l'instruction #REPOS que dans les sous-routines d’interruption. Supprimer cette instruction de n’importe quelle autre sous-routine ou programme. 'Sous-routine locale et M, T ou G avec sous-routine dans le même bloc' DÉTECTION CAUSE 1685 Au cours de l'exécution. Il y a plus d’un numéro de pièce programmé dans l'instruction #DGWZ. Programmer un seul numéro de pièce P1-P4. 'L'instruction #REPOS n'est admise que dans les sous-routines d'interruption' DÉTECTION CAUSE SOLUTION 1684 Au cours de l'exécution. Il y a plus d’un numéro de canal programmé dans l'instruction #DGWZ. Programmer un seul numéro de canal C1-C4. 'On ne peut programmer qu'un seul numéro de pièce' DÉTECTION CAUSE SOLUTION 1683 Au cours de l'exécution. Un numéro de pièce non valide est programmé dans l'instruction #DGWZ. Programmer le numéro de pièce dans la gamme P1-P4. 'Il y a trop d’axes programmés dans l'instruction' DÉTECTION CAUSE SOLUTION 1682 Au cours de l'exécution. La CNC a sollicité le chargement d’une came qui est en exécution ou dans un processus préalable de chargement. Attendre la fin de l’exécution ou le chargement de la came. Au cours de l'exécution. Des instructions #REPOS de différent type (INT/INI) sont programmées dans la même sous-routine d’interruption. Toutes les instructions #REPOS doivent être du même type. 'Les blocs après #REPOS ne sont pas admis' DÉTECTION CAUSE SOLUTION Au cours de l'exécution. Dans une sous-routine d’interruption, un bloc est programmé entre les instructions #REPOS et le bloc de fin de sous-routine. Les instructions #REPOS doivent être les derniers blocs de la sous-routine d’interruption, sauf le bloc de fin de sous-routine. CNC 8070 (REF: 1901) ·81· S o l ut i o n s d ’ e r r e ur s . 1690 'Axe multiple programmé en double' DÉTECTION CAUSE SOLUTION 1691 'Sous-routine de G imbriquée' DÉTECTION CAUSE SOLUTION 1692 CNC 8070 (REF: 1901) ·82· Pendant l'exécution du cycle. Le paramètre S a une valeur 0. Il n’y a pas de vitesse programmée. Affecter au paramètre une valeur supérieure à 0. 'POINTAGE: T = 0' DÉTECTION CAUSE SOLUTION 1703 Pendant l'exécution du cycle. Le paramètre F a une valeur 0. Il n’y a pas d’avance programmée. Affecter au paramètre une valeur supérieure à 0. 'POINTAGE: S = 0' DÉTECTION CAUSE SOLUTION 1702 Au cours de l'exécution. Les axes rotatifs de la cinématique doivent être servocommandés de façon continue. Désactiver l'instruction #CSROT. 'POINTAGE: F = 0' DÉTECTION CAUSE SOLUTION 1701 Au cours de l'exécution. L'instruction et/ou un de ses paramètres sont mal programmés. Réviser la programmation. 'La fonction CSROT n'est pas applicable aux cinématiques avec les axes manuels ou Hirth' DÉTECTION CAUSE SOLUTION 1700 Au cours de l'exécution. L'instruction et/ou un de ses paramètres sont mal programmés. Réviser la programmation. 'Programmer #DEFROT [procédure, critère, angle]' DÉTECTION CAUSE SOLUTION 1699 Au cours de l'exécution. L'instruction n’est pas admissible avec l’actuelle cinématique active. Programmer l'instruction #FACE ou #CYL pour activer cette transformée. 'Programmer #CSROT [ON]/OFF' DÉTECTION CAUSE SOLUTION 1698 Au cours de l'exécution. L'instruction et/ou un de ses paramètres sont mal programmés. Réviser la programmation. 'Il n'est pas permis de programmer #RTCP avec la cinématique actuelle. Programmer #FACE ou #CYL' DÉTECTION CAUSE SOLUTION 1697 Au cours de l'exécution. Dans une sous-routine associée à une fonction G, on ne peut pas programmer la fonction G qui appelle cette même sous-routine. Réviser la programmation. Ne pas programmer la fonction G dans la sous-routine. Dans le cas de G74, il est permis de programmer la fonction dans la sous-routine à condition qu’elle soit suivie des axes à référencer. 'Programmer #VOLCOMP ON/OFF [n]' DÉTECTION CAUSE SOLUTION 1693 Au cours de l'exécution. Il n’est pas permis de programmer plus d’un axe du même groupe multi-axe dans le même bloc. Réviser la programmation. Programmer uniquement l’axe actif du groupe multiple. Pendant l'exécution du cycle. Le paramètre T a une valeur 0. Il n’y a pas d'outil programmé. Affecter au paramètre une valeur supérieure à 0. 'POINTAGE: P = 0' DÉTECTION CAUSE SOLUTION Pendant l'exécution du cycle. Le paramètre P a une valeur 0. Il n’y a pas de profondeur programmée. Affecter au paramètre une valeur supérieure à 0. S o l ut i o n s d ’ e r r e ur s . 1704 'POINTAGE: ALPHA = 0' DÉTECTION CAUSE SOLUTION 1705 'POINTAGE: DIAMÈTRE = 0' DÉTECTION CAUSE SOLUTION 1706 Pendant l'exécution du cycle. Le paramètre P a une valeur 0. Il n’y a pas de profondeur programmée. Affecter au paramètre une valeur supérieure à 0. 'PERÇAGE 2: B = 0' DÉTECTION CAUSE SOLUTION 1715 Pendant l'exécution du cycle. Le paramètre T a une valeur 0. Il n’y a pas d'outil programmé. Affecter au paramètre une valeur supérieure à 0. 'PERÇAGE 2: P = 0' DÉTECTION CAUSE SOLUTION 1714 Pendant l'exécution du cycle. Le paramètre S a une valeur 0. Il n’y a pas de vitesse programmée. Affecter au paramètre une valeur supérieure à 0. 'PERÇAGE 2: T = 0' DÉTECTION CAUSE SOLUTION 1713 Pendant l'exécution du cycle. Le paramètre F a une valeur 0. Il n’y a pas d’avance programmée. Affecter au paramètre une valeur supérieure à 0. 'PERÇAGE 2: S = 0' DÉTECTION CAUSE SOLUTION 1712 Pendant l'exécution du cycle. Le paramètre P a une valeur 0. Il n’y a pas de profondeur programmée. Affecter au paramètre une valeur supérieure à 0. 'PERÇAGE 2: F = 0' DÉTECTION CAUSE SOLUTION 1711 Pendant l'exécution du cycle. Le paramètre T a une valeur 0. Il n’y a pas d'outil programmé. Affecter au paramètre une valeur supérieure à 0. 'PERÇAGE 1: P = 0' DÉTECTION CAUSE SOLUTION 1710 Pendant l'exécution du cycle. Le paramètre S a une valeur 0. Il n’y a pas de vitesse programmée. Affecter au paramètre une valeur supérieure à 0. 'PERÇAGE 1: T = 0' DÉTECTION CAUSE SOLUTION 1709 Pendant l'exécution du cycle. Le paramètre F a une valeur 0. Il n’y a pas d’avance programmée. Affecter au paramètre une valeur supérieure à 0. 'PERÇAGE 1: S = 0' DÉTECTION CAUSE SOLUTION 1708 Pendant l'exécution du cycle. Le paramètre à définir le diamètre a une valeur 0. Affecter au paramètre une valeur supérieure à 0. 'PERÇAGE 1: F = 0' DÉTECTION CAUSE SOLUTION 1707 Pendant l'exécution du cycle. Le paramètre alpha a une valeur 0. Il n’y a pas d’angle programmé. Affecter au paramètre une valeur supérieure à 0. Pendant l'exécution du cycle. Le paramètre B a une valeur 0. Il n’y a pas de pas de perçage programmé. Affecter au paramètre une valeur supérieure à 0. CNC 8070 'FILETAGE: F = 0' DÉTECTION CAUSE SOLUTION Pendant l'exécution du cycle. Le paramètre F a une valeur 0. Il n’y a pas d’avance programmée. Affecter au paramètre une valeur supérieure à 0. (REF: 1901) ·83· S o l ut i o n s d ’ e r r e ur s . 1716 'FILETAGE: S = 0' DÉTECTION CAUSE SOLUTION 1717 'FILETAGE: T = 0' DÉTECTION CAUSE SOLUTION 1718 CNC 8070 (REF: 1901) ·84· Pendant l'exécution du cycle. Le paramètre T a une valeur 0. Il n’y a pas d'outil programmé. Affecter au paramètre une valeur supérieure à 0. 'ALÉSAGE À MANDRIN 1: P = 0' DÉTECTION CAUSE SOLUTION 1727 Pendant l'exécution du cycle. Le paramètre S a une valeur 0. Il n’y a pas de vitesse programmée. Affecter au paramètre une valeur supérieure à 0. 'ALÉSAGE À MANDRIN 1: T = 0' DÉTECTION CAUSE SOLUTION 1726 Pendant l'exécution du cycle. Le paramètre F a une valeur 0. Il n’y a pas d’avance programmée. Affecter au paramètre une valeur supérieure à 0. 'ALÉSAGE À MANDRIN 1: S = 0' DÉTECTION CAUSE SOLUTION 1725 Pendant l'exécution du cycle. Le paramètre P a une valeur 0. Il n’y a pas de profondeur programmée. Affecter au paramètre une valeur supérieure à 0. 'ALÉSAGE À MANDRIN 1: F = 0' DÉTECTION CAUSE SOLUTION 1724 Pendant l'exécution du cycle. Le paramètre T a une valeur 0. Il n’y a pas d'outil programmé. Affecter au paramètre une valeur supérieure à 0. 'ALÉSAGE: P = 0' DÉTECTION CAUSE SOLUTION 1723 Pendant l'exécution du cycle. Le paramètre S a une valeur 0. Il n’y a pas de vitesse programmée. Affecter au paramètre une valeur supérieure à 0. 'ALÉSAGE: T = 0' DÉTECTION CAUSE SOLUTION 1722 Pendant l'exécution du cycle. Le paramètre F a une valeur 0. Il n’y a pas d’avance programmée. Affecter au paramètre une valeur supérieure à 0. 'ALÉSAGE: S = 0' DÉTECTION CAUSE SOLUTION 1721 Pendant l'exécution du cycle. Le paramètre P a une valeur 0. Il n’y a pas de profondeur programmée. Affecter au paramètre une valeur supérieure à 0. 'ALÉSAGE: F = 0' DÉTECTION CAUSE SOLUTION 1720 Pendant l'exécution du cycle. Le paramètre T a une valeur 0. Il n’y a pas d'outil programmé. Affecter au paramètre une valeur supérieure à 0. 'FILETAGE: P = 0' DÉTECTION CAUSE SOLUTION 1719 Pendant l'exécution du cycle. Le paramètre S a une valeur 0. Il n’y a pas de vitesse programmée. Affecter au paramètre une valeur supérieure à 0. Pendant l'exécution du cycle. Le paramètre P a une valeur 0. Il n’y a pas de profondeur programmée. Affecter au paramètre une valeur supérieure à 0. 'PERÇAGE 3: F = 0' DÉTECTION CAUSE SOLUTION Pendant l'exécution du cycle. Le paramètre F a une valeur 0. Il n’y a pas d’avance programmée. Affecter au paramètre une valeur supérieure à 0. S o l ut i o n s d ’ e r r e ur s . 1728 'PERÇAGE 3: S = 0' DÉTECTION CAUSE SOLUTION 1729 'PERÇAGE 3: T = 0' DÉTECTION CAUSE SOLUTION 1730 SOLUTION SOLUTION Pendant l'exécution du cycle. Un paramètre S a une valeur 0; il faut programmer la vitesse pour l’ébauchage ou la finition. Affecter au paramètre une valeur supérieure à 0. 'POCHE RECTANGULAIRE: T = 0' DÉTECTION CAUSE SOLUTION 1738 Pendant l'exécution du cycle. Un paramètre F a une valeur 0 ; il faut programmer l’avance d’ébauchage, de finition ou de pénétration sur Z. Un paramètre F a une valeur 0. Il n’y a pas d’avance programmée. Affecter au paramètre une valeur supérieure à 0. 'POCHE RECTANGULAIRE: S = 0' DÉTECTION CAUSE 1737 Pendant l'exécution du cycle. Le paramètre P a une valeur 0. Il n’y a pas de profondeur programmée. Affecter au paramètre une valeur supérieure à 0. 'POCHE RECTANGULAIRE: F = 0' DÉTECTION CAUSE 1736 Pendant l'exécution du cycle. Le paramètre T a une valeur 0. Il n’y a pas d'outil programmé. Affecter au paramètre une valeur supérieure à 0. 'ALÉSAGE À MANDRIN 2: P = 0' DÉTECTION CAUSE SOLUTION 1735 Pendant l'exécution du cycle. Le paramètre S a une valeur 0. Il n’y a pas de vitesse programmée. Affecter au paramètre une valeur supérieure à 0. 'ALÉSAGE À MANDRIN 2: T = 0' DÉTECTION CAUSE SOLUTION 1734 Pendant l'exécution du cycle. Le paramètre F a une valeur 0. Il n’y a pas d’avance programmée. Affecter au paramètre une valeur supérieure à 0. 'ALÉSAGE À MANDRIN 2: S = 0' DÉTECTION CAUSE SOLUTION 1733 Pendant l'exécution du cycle. Le paramètre P a une valeur 0. Il n’y a pas de profondeur programmée. Affecter au paramètre une valeur supérieure à 0. 'ALÉSAGE À MANDRIN 2: F = 0' DÉTECTION CAUSE SOLUTION 1732 Pendant l'exécution du cycle. Le paramètre T a une valeur 0. Il n’y a pas d'outil programmé. Affecter au paramètre une valeur supérieure à 0. 'PERÇAGE 3: P = 0' DÉTECTION CAUSE SOLUTION 1731 Pendant l'exécution du cycle. Le paramètre S a une valeur 0. Il n’y a pas de vitesse programmée. Affecter au paramètre une valeur supérieure à 0. Pendant l'exécution du cycle. Le paramètre T des opérations d’ébauchage et de finition a une valeur 0. Il n’y a pas d’outil programmé. Programmer un outil pour l’opération d’ébauchage ou de finition. Si une opération n’a pas d’outil, le cycle ne l’exécute pas ; une opération au moins doit avoir un outil. CNC 8070 'POCHE RECTANGULAIRE: P = 0' DÉTECTION CAUSE SOLUTION Pendant l'exécution du cycle. Le paramètre P a une valeur 0. Il n’y a pas de profondeur programmée. Affecter au paramètre une valeur supérieure à 0. (REF: 1901) ·85· S o l ut i o n s d ’ e r r e ur s . 1739 'POCHE RECTANGULAIRE: Diamètre de l'outil inférieur à DELTA' DÉTECTION CAUSE SOLUTION 1740 'POCHE RECTANGULAIRE: Diamètre de l'outil supérieur à la poche' DÉTECTION CAUSE SOLUTION 1741 SOLUTION SOLUTION SOLUTION SOLUTION SOLUTION SOLUTION 1748 ·86· Pendant l'exécution du cycle. Dans l’opération d’ébauchage ou de finition, le diamètre de l’outil est supérieur aux dimensions de la poche (paramètres L ou H). Choisir un outil avec diamètre inférieur. 'POCHE PRÉVIDÉE: Diamètre de l'outil FINITION inférieur à delta' DÉTECTION CAUSE (REF: 1901) Pendant l'exécution du cycle. Dans l’opération d’ébauchage ou de finition, le diamètre de l’outil est inférieur au pas de fraisage (paramètre ). Réduire le pas de fraisage ou utiliser un outil avec un plus grand diamètre. 'POCHE PRÉVIDÉE: Diamètre de l'outil supérieur à la poche' DÉTECTION CAUSE CNC 8070 Pendant l'exécution du cycle. Le paramètre P a une valeur 0. Il n’y a pas de profondeur programmée. Affecter au paramètre une valeur supérieure à 0. 'POCHE PRÉVIDÉE: Diamètre de l'outil inférieur à DELTA' DÉTECTION CAUSE 1747 Pendant l'exécution du cycle. Le paramètre T des opérations d’ébauchage et de finition a une valeur 0. Il n’y a pas d’outil programmé. Programmer un outil pour l’opération d’ébauchage ou de finition. Si une opération n’a pas d’outil, le cycle ne l’exécute pas ; une opération au moins doit avoir un outil. 'POCHE PRÉVIDÉE: P = 0' DÉTECTION CAUSE SOLUTION 1746 Pendant l'exécution du cycle. Un paramètre S a une valeur 0; il faut programmer la vitesse pour l’ébauchage ou la finition. Affecter au paramètre une valeur supérieure à 0. 'POCHE PRÉVIDÉE: T = 0' DÉTECTION CAUSE 1745 Pendant l'exécution du cycle. Un paramètre F a une valeur 0 ; il faut programmer l’avance d’ébauchage, de finition ou de pénétration sur Z. Affecter au paramètre une valeur supérieure à 0. 'POCHE PRÉVIDÉE: S = 0' DÉTECTION CAUSE 1744 Pendant l'exécution du cycle. Le diamètre de l’outil de finition est inférieur aux surépaisseurs sur les parois latérales (paramètre ). Choisir un outil avec un plus grand diamètre pour la passe de finition. 'POCHE PRÉVIDÉE: F = 0' DÉTECTION CAUSE 1743 Pendant l'exécution du cycle. Dans l’opération d’ébauchage ou de finition, le diamètre de l’outil est supérieur aux dimensions de la poche (paramètres L ou H). Choisir un outil avec diamètre inférieur. 'POCHE RECTANGULAIRE: Diamètre de l'outil FINITION inférieur à delta' DÉTECTION CAUSE 1742 Pendant l'exécution du cycle. Dans l’opération d’ébauchage ou de finition, le diamètre de l’outil est inférieur au pas de fraisage (paramètre ). Réduire le pas de fraisage ou utiliser un outil avec un plus grand diamètre. SOLUTION Pendant l'exécution du cycle. Le diamètre de l’outil de finition est inférieur aux surépaisseurs sur les parois latérales (paramètre ). Choisir un outil avec un plus grand diamètre pour la passe de finition. S o l ut i o n s d ’ e r r e ur s . 1749 'POCHE PRÉVIDÉE: R < r' DÉTECTION CAUSE SOLUTION 1750 'MOYEU RECTANGULAIRE: F = 0' DÉTECTION CAUSE SOLUTION 1751 SOLUTION SOLUTION SOLUTION SOLUTION SOLUTION Pendant l'exécution du cycle. Un paramètre F a une valeur 0 ; il faut programmer l’avance d’ébauchage, de finition ou de pénétration sur Z. Affecter au paramètre une valeur supérieure à 0. 'MOYEU CIRCULAIRE: S = 0' DÉTECTION CAUSE SOLUTION 1758 Pendant l'exécution du cycle. Le diamètre de l’outil de finition est inférieur aux surépaisseurs sur les parois latérales (paramètre ). Choisir un outil avec un plus grand diamètre pour la passe de finition. 'MOYEU CIRCULAIRE: F = 0' DÉTECTION CAUSE 1757 Pendant l'exécution du cycle. Dans l’opération d’ébauchage ou de finition, le diamètre de l’outil est inférieur au pas de fraisage (paramètre ). Réduire le pas de fraisage ou utiliser un outil avec un plus grand diamètre. 'MOYEU RECTANGULAIRE: Diamètre de l'outil FINITION inférieur à delta' DÉTECTION CAUSE 1756 Pendant l'exécution du cycle. Le paramètre P a une valeur 0. Il n’y a pas de profondeur programmée. Affecter au paramètre une valeur supérieure à 0. 'MOYEU RECTANGULAIRE: Diamètre de l'outil inférieur à DELTA' DÉTECTION CAUSE 1755 Pendant l'exécution du cycle. Le paramètre T des opérations d’ébauchage et de finition a une valeur 0. Il n’y a pas d’outil programmé. Programmer un outil pour l’opération d’ébauchage ou de finition. Si une opération n’a pas d’outil, le cycle ne l’exécute pas ; une opération au moins doit avoir un outil. 'MOYEU RECTANGULAIRE: P = 0' DÉTECTION CAUSE SOLUTION 1754 Pendant l'exécution du cycle. Un paramètre S a une valeur 0; il faut programmer la vitesse pour l’ébauchage ou la finition. Affecter au paramètre une valeur supérieure à 0. 'MOYEU RECTANGULAIRE: T = 0' DÉTECTION CAUSE 1753 Pendant l'exécution du cycle. Un paramètre F a une valeur 0 ; il faut programmer l’avance d’ébauchage, de finition ou de pénétration sur Z. Affecter au paramètre une valeur supérieure à 0. 'MOYEU RECTANGULAIRE: S = 0' DÉTECTION CAUSE 1752 Pendant l'exécution du cycle. Le rayon de la poche (paramètre R) doit être inférieur au rayon de prévidage (paramètre r). Le rayon de la poche (rayon extérieur) doit être supérieur au rayon de prévidage (rayon intérieur). Pendant l'exécution du cycle. Un paramètre S a une valeur 0; il faut programmer la vitesse pour l’ébauchage ou la finition. Affecter au paramètre une valeur supérieure à 0. CNC 8070 'MOYEU CIRCULAIRE: T = 0' DÉTECTION CAUSE SOLUTION Pendant l'exécution du cycle. Le paramètre T des opérations d’ébauchage et de finition a une valeur 0. Il n’y a pas d’outil programmé. Programmer un outil pour l’opération d’ébauchage ou de finition. Si une opération n’a pas d’outil, le cycle ne l’exécute pas ; une opération au moins doit avoir un outil. (REF: 1901) ·87· S o l ut i o n s d ’ e r r e ur s . 1759 'MOYEU CIRCULAIRE: P = 0' DÉTECTION CAUSE SOLUTION 1760 'MOYEU CIRCULAIRE: R = 0' DÉTECTION CAUSE SOLUTION 1761 SOLUTION SOLUTION SOLUTION SOLUTION SOLUTION CNC 8070 SOLUTION (REF: 1901) Pendant l'exécution du cycle. Un paramètre F a une valeur 0 ; il faut programmer l’avance d’ébauchage, de finition ou de pénétration sur Z. Affecter au paramètre une valeur supérieure à 0. 'PROFIL DE POINTS: S = 0' DÉTECTION CAUSE SOLUTION ·88· Pendant l'exécution du cycle. La longueur (paramètre L) et/ou la largeur du surfaçage (paramètre H) sont 0. Définir les deux dimensions du surfaçage avec une valeur différente de zéro. 'PROFIL DE POINTS: F = 0' DÉTECTION CAUSE 1769 Pendant l'exécution du cycle. Le paramètre P a une valeur 0. Il n’y a pas de profondeur programmée. Affecter au paramètre une valeur supérieure à 0. 'SURFAÇAGE: L = 0 et H = 0' DÉTECTION CAUSE SOLUTION 1768 Pendant l'exécution du cycle. Le paramètre T des opérations d’ébauchage et de finition a une valeur 0. Il n’y a pas d’outil programmé. Programmer un outil pour l’opération d’ébauchage ou de finition. Si une opération n’a pas d’outil, le cycle ne l’exécute pas ; une opération au moins doit avoir un outil. 'SURFAÇAGE: P = 0' DÉTECTION CAUSE SOLUTION 1767 Pendant l'exécution du cycle. Un paramètre S a une valeur 0; il faut programmer la vitesse pour l’ébauchage ou la finition. Affecter au paramètre une valeur supérieure à 0. 'SURFAÇAGE: T = 0' DÉTECTION CAUSE 1766 Pendant l'exécution du cycle. Un paramètre F a une valeur 0 ; il faut programmer l’avance d’ébauchage, de finition ou de pénétration sur Z. Affecter au paramètre une valeur supérieure à 0. 'SURFAÇAGE: S = 0' DÉTECTION CAUSE 1765 Pendant l'exécution du cycle. Le diamètre de l’outil de finition est inférieur aux surépaisseurs sur les parois latérales (paramètre ). Choisir un outil avec un plus grand diamètre pour la passe de finition. 'SURFAÇAGE: F = 0' DÉTECTION CAUSE 1764 Pendant l'exécution du cycle. Dans l’opération d’ébauchage ou de finition, le diamètre de l’outil est inférieur au pas de fraisage (paramètre ). Réduire le pas de fraisage ou utiliser un outil avec un plus grand diamètre. 'MOYEU CIRCULAIRE: Diamètre de l'outil FINITION inférieur à delta' DÉTECTION CAUSE 1763 Pendant l'exécution du cycle. Le paramètre R a une valeur 0. Il n’y a pas de rayon programmé. Affecter au paramètre une valeur supérieure à 0. 'MOYEU CIRCULAIRE: Diamètre de l'outil inférieur à DELTA' DÉTECTION CAUSE 1762 Pendant l'exécution du cycle. Le paramètre P a une valeur 0. Il n’y a pas de profondeur programmée. Affecter au paramètre une valeur supérieure à 0. Pendant l'exécution du cycle. Un paramètre S a une valeur 0; il faut programmer la vitesse pour l’ébauchage ou la finition. Affecter au paramètre une valeur supérieure à 0. S o l ut i o n s d ’ e r r e ur s . 1770 'PROFIL DE POINTS: T = 0' DÉTECTION CAUSE SOLUTION 1771 'PROFIL DE POINTS: P = 0' DÉTECTION CAUSE SOLUTION 1772 SOLUTION SOLUTION SOLUTION SOLUTION SOLUTION Pendant l'exécution du cycle. Le paramètre P a une valeur 0. Il n’y a pas de profondeur programmée. Affecter au paramètre une valeur supérieure à 0. 'PROFIL: (FINITION): Longueur de coupe de l'outil < P' DÉTECTION CAUSE SOLUTION 1779 Pendant l'exécution du cycle. Le paramètre T des opérations d’ébauchage et de finition a une valeur 0. Il n’y a pas d’outil programmé. Programmer un outil pour l’opération d’ébauchage ou de finition. Si une opération n’a pas d’outil, le cycle ne l’exécute pas ; une opération au moins doit avoir un outil. 'PROFIL: P = 0' DÉTECTION CAUSE SOLUTION 1778 Pendant l'exécution du cycle. Un paramètre S a une valeur 0; il faut programmer la vitesse pour l’ébauchage ou la finition. Affecter au paramètre une valeur supérieure à 0. 'PROFIL: T = 0' DÉTECTION CAUSE 1777 Pendant l'exécution du cycle. Un paramètre F a une valeur 0 ; il faut programmer l’avance d’ébauchage, de finition ou de pénétration sur Z. Affecter au paramètre une valeur supérieure à 0. 'PROFIL: S = 0' DÉTECTION CAUSE 1776 Pendant l'exécution du cycle. Le rayon d’un des outils utilisés dans le cycle est égal ou supérieur au rayon de l’entrée tangentielle (rayon du point P1) ou de la sortie tangentielle (rayon du point P12). Augmenter le rayon de l’entrée/sortie tangentielle ou exécuter le cycle avec un outil au rayon inférieur. 'PROFIL: F = 0' DÉTECTION CAUSE 1775 Pendant l'exécution du cycle. Les deux premiers points du profil (P1 et P2) sont égaux ; le cycle considère qu’il n’y a pas de profil défini. Définir correctement les points du profil. Deux points égaux indiquent la fin du profil. 'PROFIL DE POINTS: Rayon d'outil supérieur ou égal au rayon d'entrée/sortie tangentielle' DÉTECTION CAUSE 1774 Pendant l'exécution du cycle. Le paramètre P a une valeur 0. Il n’y a pas de profondeur programmée. Affecter au paramètre une valeur supérieure à 0. 'PROFIL DE POINTS: Profil nul' DÉTECTION CAUSE 1773 Pendant l'exécution du cycle. Le paramètre T des opérations d’ébauchage et de finition a une valeur 0. Il n’y a pas d’outil programmé. Programmer un outil pour l’opération d’ébauchage ou de finition. Si une opération n’a pas d’outil, le cycle ne l’exécute pas ; une opération au moins doit avoir un outil. Pendant l'exécution du cycle. La longueur de coupe de l’outil de finition est inférieure à la profondeur du profil (paramètre P). Choisir comme outil de finition un outil avec une plus grande longueur de coupe. CNC 8070 'RAINURAGE: F = 0' DÉTECTION CAUSE SOLUTION Pendant l'exécution du cycle. Un paramètre F a une valeur 0 ; il faut programmer l’avance d’ébauchage, de finition ou de pénétration sur Z. Affecter au paramètre une valeur supérieure à 0. (REF: 1901) ·89· S o l ut i o n s d ’ e r r e ur s . 1780 'RAINURAGE: S = 0' DÉTECTION CAUSE SOLUTION 1781 'RAINURAGE: T = 0' DÉTECTION CAUSE SOLUTION 1782 SOLUTION SOLUTION SOLUTION SOLUTION SOLUTION 1789 SOLUTION (REF: 1901) Pendant l'exécution du cycle. Le paramètre T des opérations d’ébauchage et de finition a une valeur 0. Il n’y a pas d’outil programmé. Programmer un outil pour l’opération d’ébauchage ou de finition. Si une opération n’a pas d’outil, le cycle ne l’exécute pas ; une opération au moins doit avoir un outil. 'POCHE CIRCULAIRE: P = 0' DÉTECTION CAUSE SOLUTION ·90· Pendant l'exécution du cycle. Un paramètre S a une valeur 0; il faut programmer la vitesse pour l’ébauchage ou la finition. Affecter au paramètre une valeur supérieure à 0. 'POCHE CIRCULAIRE: T = 0' DÉTECTION CAUSE 1790 Pendant l'exécution du cycle. Un paramètre F a une valeur 0 ; il faut programmer l’avance d’ébauchage, de finition ou de pénétration sur Z. Affecter au paramètre une valeur supérieure à 0. 'POCHE CIRCULAIRE: S = 0' DÉTECTION CAUSE CNC 8070 Pendant l'exécution du cycle. Le diamètre de l’outil de finition est inférieur aux surépaisseurs sur les parois latérales (paramètre ). Choisir un outil avec un plus grand diamètre pour la passe de finition. 'POCHE CIRCULAIRE: F = 0' DÉTECTION CAUSE 1788 Pendant l'exécution du cycle. Dans l’opération d’ébauchage ou de finition, le diamètre de l’outil est supérieur aux dimensions de la rainure (paramètres L ou H). Choisir un outil avec diamètre inférieur. 'RAINURAGE: Diamètre de l'outil FINITION inférieur à delta' DÉTECTION CAUSE 1787 Pendant l'exécution du cycle. Dans l’opération d’ébauchage ou de finition, le diamètre de l’outil est inférieur au pas de fraisage (paramètre ). Réduire le pas de fraisage ou utiliser un outil avec un plus grand diamètre. 'RAINURAGE: Diamètre de l'outil supérieur à la poche' DÉTECTION CAUSE 1786 Pendant l'exécution du cycle. Le paramètre L a une valeur 0. La rainure n'a pas de longueur. Affecter au paramètre une valeur supérieure à 0. 'RAINURAGE: Diamètre de l'outil inférieur à DELTA' DÉTECTION CAUSE 1785 Pendant l'exécution du cycle. Le paramètre P a une valeur 0. Il n’y a pas de profondeur programmée. Affecter au paramètre une valeur supérieure à 0. 'RAINURAGE: L = 0' DÉTECTION CAUSE SOLUTION 1784 Pendant l'exécution du cycle. Le paramètre T des opérations d’ébauchage et de finition a une valeur 0. Il n’y a pas d’outil programmé. Programmer un outil pour l’opération d’ébauchage ou de finition. Si une opération n’a pas d’outil, le cycle ne l’exécute pas ; une opération au moins doit avoir un outil. 'RAINURAGE: P = 0' DÉTECTION CAUSE SOLUTION 1783 Pendant l'exécution du cycle. Un paramètre S a une valeur 0; il faut programmer la vitesse pour l’ébauchage ou la finition. Affecter au paramètre une valeur supérieure à 0. Pendant l'exécution du cycle. Le paramètre P a une valeur 0. Il n’y a pas de profondeur programmée. Affecter au paramètre une valeur supérieure à 0. S o l ut i o n s d ’ e r r e ur s . 1791 'POCHE CIRCULAIRE: Diamètre de l'outil inférieur à DELTA' DÉTECTION CAUSE SOLUTION 1792 'POCHE CIRCULAIRE: Diamètre de l'outil supérieur à la poche' DÉTECTION CAUSE SOLUTION 1793 SOLUTION Au cours de l'exécution d'un cycle. Le rayon d'ébauchage ou de finition a une valeur 0. Corriger la valeur du rayon dans la table d’outils ou sélectionner un autre outil. 'POCHE RECTANGULAIRE: Bêta ou thêta< 0 Bêta ou thêta > 90' DÉTECTION CAUSE SOLUTION 1802 Au cours de l'exécution d'un cycle. Le rayon d'ébauchage ou de finition a une valeur 0. Corriger la valeur du rayon dans la table d’outils ou sélectionner un autre outil. 'RAINURAGE: Diamètre d'outil = 0' DÉTECTION CAUSE SOLUTION 1801 Au cours de l'exécution d'un cycle. Le rayon d'ébauchage ou de finition a une valeur 0. Corriger la valeur du rayon dans la table d’outils ou sélectionner un autre outil. 'SURFAÇAGE: Diamètre d'outil = 0' DÉTECTION CAUSE SOLUTION 1800 Au cours de l'exécution d'un cycle. Le rayon d'ébauchage ou de finition a une valeur 0. Corriger la valeur du rayon dans la table d’outils ou sélectionner un autre outil. 'MOYEU CIRCULAIRE: Diamètre d'outil = 0' DÉTECTION CAUSE SOLUTION 1799 Au cours de l'exécution d'un cycle. Le rayon d'ébauchage ou de finition a une valeur 0. Corriger la valeur du rayon dans la table d’outils ou sélectionner un autre outil. 'MOYEU RECTANGULAIRE: Diamètre d'outil = 0' DÉTECTION CAUSE SOLUTION 1798 Au cours de l'exécution d'un cycle. Le rayon d'ébauchage ou de finition a une valeur 0. Corriger la valeur du rayon dans la table d’outils ou sélectionner un autre outil. 'POCHE PRÉVIDÉE: Diamètre de l'outil = 0' DÉTECTION CAUSE SOLUTION 1797 Au cours de l'exécution d'un cycle. Le rayon d'ébauchage ou de finition a une valeur 0. Corriger la valeur du rayon dans la table d’outils ou sélectionner un autre outil. 'POCHE CIRCULAIRE: Diamètre de l'outil = 0' DÉTECTION CAUSE SOLUTION 1796 Pendant l'exécution du cycle. Le diamètre de l’outil de finition est inférieur aux surépaisseurs sur les parois latérales (paramètre ). Choisir un outil avec un plus grand diamètre pour la passe de finition. 'POCHE RECTANGULAIRE: Diamètre de l'outil = 0' DÉTECTION CAUSE SOLUTION 1795 Pendant l'exécution du cycle. Dans l’opération d’ébauchage ou de finition, le rayon de l’outil est supérieur au rayon de la poche (paramètre R). Choisir un outil avec diamètre inférieur. 'POCHE CIRCULAIRE: Diamètre de l'outil FINITION inférieur à delta' DÉTECTION CAUSE 1794 Pendant l'exécution du cycle. Dans l’opération d’ébauchage ou de finition, le diamètre de l’outil est inférieur au pas de fraisage (paramètre ). Réduire le pas de fraisage ou utiliser un outil avec un plus grand diamètre. Au cours de l’exécution d’une poche. Dans le cycle de poche, l'angle de pénétration latérale pour l'ébauchage (paramètre ) ou pour la finition (paramètre ) n'est pas compris entre 0º et 90º. Corriger l’angle de pénétration latérale; programmer une valeur entre 0º et 90º. 'POCHE CIRCULAIRE: Bêta ou thêta< 0 Bêta ou thêta > 90' DÉTECTION CAUSE SOLUTION CNC 8070 (REF: 1901) Au cours de l’exécution d’une poche. Dans le cycle de poche, l'angle de pénétration latérale pour l'ébauchage (paramètre ) ou pour la finition (paramètre ) n'est pas compris entre 0º et 90º. Corriger l’angle de pénétration latérale; programmer une valeur entre 0º et 90º. ·91· S o l ut i o n s d ’ e r r e ur s . 1803 'POCHE PRÉVIDÉE: Bêta ou thêta< 0 Bêta ou thêta > 90' DÉTECTION CAUSE SOLUTION 1804 'G87: Profondeur = 0' DÉTECTION CAUSE SOLUTION 1805 SOLUTION 1812 (REF: 1901) ·92· Pendant l'exécution du cycle. Le rayon de l'outil est supérieur aux dimensions de la poche (paramètre J). Sélectionner un outil avec un diamètre inférieur. 'G88: Diamètre de l'outil inférieur à L' DÉTECTION CAUSE SOLUTION 1813 Pendant l'exécution du cycle. La profondeur résultante de la poche est zéro. La profondeur programmée (paramètre I) coïncide avec la somme des paramètres Z et D ; si le paramètre Z n’a pas été programmé, la profondeur programmée (paramètre I) coïncide avec le paramètre D. Corriger la programmation des paramètres I Z D. 'G88: Diamètre de l'outil supérieur à la poche' DÉTECTION CAUSE SOLUTION CNC 8070 Pendant l'exécution du cycle. Le diamètre de l'outil est inférieur au pas de fraisage (paramètre C). Réduire le pas de fraisage ou utiliser un outil avec un plus grand diamètre. 'G88: Profondeur = 0' DÉTECTION CAUSE 1811 Pendant l'exécution du cycle. Dans la broche il n'y a pas d'outil. Programmer un outil avant le cycle ou charger un outil sur la broche. 'G87: Diamètre de l'outil inférieur à C' DÉTECTION CAUSE SOLUTION 1810 Pendant l'exécution du cycle. L'outil a un diamètre 0. Corriger la valeur du rayon dans la table d’outils ou sélectionner un autre outil. 'G87: Il n'y a pas d'outil' DÉTECTION CAUSE SOLUTION 1809 Pendant l'exécution du cycle. Le diamètre de l'outil est inférieur à la surépaisseur de finition (paramètre L). Sélectionner un outil avec un diamètre supérieur. 'G87: Diamètre de l'outil = 0' DÉTECTION CAUSE SOLUTION 1808 Pendant l'exécution du cycle. Le rayon de l'outil est supérieur aux dimensions de la poche (paramètres J et/ou K). Sélectionner un outil avec un diamètre inférieur. 'G87: Diamètre de l'outil inférieur à L' DÉTECTION CAUSE SOLUTION 1807 Pendant l'exécution du cycle. La profondeur résultante de la poche est zéro. La profondeur programmée (paramètre I) coïncide avec la somme des paramètres Z et D ; si le paramètre Z n’a pas été programmé, la profondeur programmée (paramètre I) coïncide avec le paramètre D. Corriger la programmation des paramètres I Z D. 'G87: Diamètre de l'outil supérieur à la poche' DÉTECTION CAUSE SOLUTION 1806 Au cours de l’exécution d’une poche. Dans le cycle de poche, l'angle de pénétration latérale pour l'ébauchage (paramètre ) ou pour la finition (paramètre ) n'est pas compris entre 0º et 90º. Corriger l’angle de pénétration latérale; programmer une valeur entre 0º et 90º. Pendant l'exécution du cycle. Le diamètre de l'outil est inférieur à la surépaisseur de finition (paramètre L). Sélectionner un outil avec un diamètre supérieur. 'G88: Diamètre de l'outil = 0' DÉTECTION CAUSE SOLUTION Pendant l'exécution du cycle. L'outil a un diamètre 0. Corriger la valeur du rayon dans la table d’outils ou sélectionner un autre outil. S o l ut i o n s d ’ e r r e ur s . 1814 'G88: Il n'y a pas d'outil' DÉTECTION CAUSE SOLUTION 1815 'G88: Diamètre de l'outil inférieur à C' DÉTECTION CAUSE SOLUTION 1816 SOLUTION SOLUTION SOLUTION SOLUTION SOLUTION SOLUTION Au cours de l'exécution d'un cycle d'usinage multiple. La longueur de l’usinage (paramètre Y) doit être multiple du pas entre usinages (paramètre J). Affecter aux paramètres une valeur correcte. 'Deux des paramètres Y, J, D doivent être programmés' DÉTECTION CAUSE SOLUTION 1824 Au cours de l'exécution d'un cycle d'usinage multiple. La longueur angulaire de l’usinage (paramètre B) doit être multiple du pas angulaire entre usinages (paramètre I). Affecter aux paramètres une valeur correcte. 'Le paramètre Y doit être multiple du paramètre J' DÉTECTION CAUSE 1823 Au cours de l'exécution d'un cycle d'usinage multiple. Il faut programmer deux des paramètres suivants : X (longueur de l’usinage), I (pas entre usinages), K (nombre d’usinages). Affecter aux paramètres une valeur correcte. 'B doit être multiple d'I' DÉTECTION CAUSE 1822 Au cours de l'exécution d'un cycle d'usinage multiple. Dans un usinage multiple, le paramètre K (nombre d'usinages) a une valeur 0. Affecter au paramètre une valeur correcte. 'Deux des paramètres X, I, K doivent être programmés' DÉTECTION CAUSE 1821 Au cours de l'exécution d'un cycle d'usinage multiple. Dans un usinage multiple, le paramètre J (pas entre usinages dans l’axe des ordonnées) a une valeur 0. Affecter au paramètre une valeur correcte. 'K = 0' DÉTECTION CAUSE SOLUTION 1820 Au cours de l'exécution d'un cycle d'usinage multiple. Il faut programmer le pas entre usinages (paramètre I) ou le nombre d’usinages (paramètre K). Affecter au paramètre une valeur correcte. 'J = 0' DÉTECTION CAUSE 1819 Au cours de l'exécution d'un cycle d'usinage multiple. La longueur de l’usinage (paramètre X) doit être multiple du pas entre usinages (paramètre I). Affecter aux paramètres une valeur correcte. 'L'un des paramètres I, K doit être programmé' DÉTECTION CAUSE 1818 Pendant l'exécution du cycle. Le diamètre de l'outil est inférieur au pas de fraisage (paramètre C). Réduire le pas de fraisage ou utiliser un outil avec un plus grand diamètre. 'Le paramètre X doit être multiple du paramètre I' DÉTECTION CAUSE 1817 Pendant l'exécution du cycle. Dans la broche il n'y a pas d'outil. Programmer un outil avant le cycle ou charger un outil sur la broche. Au cours de l'exécution d'un cycle d'usinage multiple. Il faut programmer deux des paramètres suivants : Y (longueur de l’usinage), J (pas entre usinages), D (nombre d’usinages). Affecter aux paramètres une valeur correcte. CNC 8070 'L'un des paramètres I, K doit être programmé' DÉTECTION CAUSE SOLUTION Au cours de l'exécution d'un cycle d'usinage multiple. Il faut programmer l'un des paramètres suivants : I (pas entre usinages), K (nombre d’usinages). Affecter aux paramètres une valeur correcte. (REF: 1901) ·93· S o l ut i o n s d ’ e r r e ur s . 1825 'L'un des paramètres I, A doit être programmé' DÉTECTION CAUSE SOLUTION 1826 'Le paramètre I multiplié par K doit être égal à 360' DÉTECTION CAUSE SOLUTION 1827 SOLUTION CNC 8070 SOLUTION (REF: 1901) ·94· Pendant l'exécution du cycle. Le paramètre N (nombre de passes de pénétration) a une valeur 0 et l’outil de finition n’a pas une longueur de coupe définie. Programmer le nombre de passes de pénétration (paramètre N) ou définir la longueur de coupe dans la table d’outils. 'FINITION: Delta z supérieur à longueur de coupe d'outil' DÉTECTION CAUSE 1835 Pendant l'exécution du cycle. Le paramètre I (pas maximum de pénétration) a une valeur 0. Assigner au paramètre une valeur différente de zéro et inférieure à la longueur de coupe de l’outil. 'FINITION: N = 0 et longueur de coupe d'outil non définie' DÉTECTION CAUSE 1834 Pendant l'exécution du cycle. Le paramètre C (cote d'approche) a valeur 0. Affecter au paramètre une valeur différente de zéro. 'ÉBAUCHAGE: I = 0' DÉTECTION CAUSE SOLUTION 1833 Au cours de l'exécution d'un cycle. L'outil a un diamètre 0. Corriger la valeur du rayon dans la table d’outils ou sélectionner un autre outil. 'G82: C = 0' DÉTECTION CAUSE SOLUTION 1832 Au cours de l'exécution d'un cycle d'usinage multiple. Dans un usinage multiple, le paramètre I (pas entre d'usinages) a une valeur 0. Affecter au paramètre une valeur différente de zéro. 'Diamètre d'outil = 0' DÉTECTION CAUSE SOLUTION 1831 Au cours de l'exécution d'un cycle d'usinage multiple. Le pas angulaire (paramètre I) doit être sous-multiple de 360º. Affecter au paramètre une valeur correcte. 'I = 0' DÉTECTION CAUSE SOLUTION 1830 Au cours de l'exécution d'un cycle d'usinage multiple. Les paramètres X Y (centre de l'arc d'usinage) ont une valeur 0. Affecter au paramètre une valeur correcte. '360 doit être multiple du paramètre I' DÉTECTION CAUSE SOLUTION 1829 Au cours de l'exécution d'un cycle d'usinage multiple. Le pas angulaire entre usinages (paramètre I) par le nombre d’usinages (paramètre K) doit être 360º. Affecter au paramètre une valeur correcte. 'Les paramètres X et Y son égaux à 0' DÉTECTION CAUSE SOLUTION 1828 Au cours de l'exécution d'un cycle d'usinage multiple. Il faut programmer deux des paramètres suivants : I (pas angulaire entre usinages), A (nombre d’usinages). Affecter au paramètre une valeur correcte. Pendant l'exécution du cycle. Le paramètre z (surépaisseur de finition dans le fond) dépasse la longueur de coupe de l’outil de finition. Programmer une surépaisseur de finition inférieure (paramètre z) ou bien utiliser un autre outil. 'Poche avec îlots: Z de sécurité non valide' DÉTECTION CAUSE SOLUTION Pendant l'exécution du cycle. Le plan de sécurité (paramètre Zs) se trouve dans la pièce. Affecter au paramètre une valeur correcte. S o l ut i o n s d ’ e r r e ur s . 1836 'Poche avec îlots: Profil sur Z non valide' DÉTECTION CAUSE SOLUTION 1837 'Poche avec îlots: Profil sur XY se coupe lui-même' DÉTECTION CAUSE SOLUTION 1838 SOLUTION SOLUTION SOLUTION Pendant l'exécution du cycle. Le rayon de l'outil d'ébauchage a une valeur 0 ou l'outil est trop grand pour la géométrie de la poche, en tenant compte de la surépaisseur latérale (paramètre ). Corriger la valeur du rayon dans la table d’outils ou sélectionner un autre outil. Vérifier la valeur de la surépaisseur latérale. 'Poche avec îlots: Rayon de l'outil de finition non valide' DÉTECTION CAUSE SOLUTION 1845 Pendant l'exécution du cycle. Le diamètre de l'outil de finition est inférieur au pas de fraisage (paramètre ). Réduire le pas de fraisage ou utiliser un outil avec un plus grand diamètre. 'Poche avec îlots: Rayon de l'outil d'ébauchage non valide' DÉTECTION CAUSE 1844 Pendant l'exécution du cycle. Au moment d’exécuter le cycle, la pointe de l’outil se trouve entre le plan de référence et la surface de la pièce. Pour exécuter le cycle, situer l’outil au-dessus du plan de référence. 'Diamètre d'outil inférieur à DELTA' DÉTECTION CAUSE SOLUTION 1843 Pendant l'exécution du cycle. Le système ne dispose pas de mémoire pour continuer à résoudre la poche. Contacter FAGOR. 'Position d’outil non valable avant le cycle fixe' DÉTECTION CAUSE 1842 Pendant l'exécution du cycle. Deux profils de surface ont un segment droit ou courbe en commun. Vérifier que les profils de surface n’ont pas de segments en commun, l’intersection des profils devant se produire à des points. 'Poche avec îlots: Mémoire insuffisante pour la résolution' DÉTECTION CAUSE SOLUTION 1841 Pendant l'exécution du cycle. Un profil de surface n’est pas un profil fermé, ses points initial et final ne sont pas les mêmes. Vérifier que tous les profils de surface sont fermés. 'Poche avec îlots: Intersection de profils sur XY non valide' DÉTECTION CAUSE SOLUTION 1840 Pendant l'exécution du cycle. Un profil de surface forme plus d’un profil fermé. Vérifier que les profils de surface ne s’entrecoupent pas et qu’ils n’ont que le point initial en commun. 'Poche avec îlots: Profil sur XY n'est pas fermé' DÉTECTION CAUSE 1839 Pendant l'exécution du cycle. Un profil de profondeur est fermé ou le cycle ne peut pas usiner un profil de profondeur avec l’outil programmé. Vérifier que les profils de profondeur sont corrects. Pendant l'exécution du cycle. Le rayon de l’outil de finition a une valeur 0 ou l’outil est trop grand pour la géométrie de la poche. Corriger la valeur du rayon dans la table d’outils ou sélectionner un autre outil. 'G165: Longueur de la corde (I) supérieure au diamètre' DÉTECTION CAUSE SOLUTION Au cours de l'exécution d'un cycle d'usinage multiple. La longueur de la corde (paramètre) est supérieure au diamètre du cercle. Affecter au paramètre une valeur correcte. CNC 8070 (REF: 1901) ·95· S o l ut i o n s d ’ e r r e ur s . 1846 'Rayon de l'arc nul' DÉTECTION CAUSE SOLUTION 1847 'MOYEU RECTANGULAIRE: Q = 0' DÉTECTION CAUSE SOLUTION 1848 SOLUTION SOLUTION SOLUTION CNC 8070 SOLUTION (REF: 1901) ·96· Au cours de l’exécution du cycle de palpeur #PROBE 2 ou #PROBE 9. Le paramètre J (diamètre théorique du trou) a une valeur incorrecte. Affecter au paramètre une valeur positive. 'Diamètre de l'outil supérieur à celui du trou' DÉTECTION CAUSE 1856 Au cours de l'exécution d'un cycle de palpeur #PROBE. Le palpeur n’a pas touché la pièce pendant le déplacement de palpage. Corriger la définition du cycle fixe. 'Le diamètre J doit être supérieur à zéro' DÉTECTION CAUSE SOLUTION 1855 Au cours de l'exécution d'un cycle fixe. Il n’y a pas d’outil ni de palpeur sur la broche pour pouvoir exécuter le cycle. Placer un outil ou un palpeur sur la broche, en fonction du cycle fixe. 'Le signal du palpeur n'a pas été reçu' DÉTECTION CAUSE SOLUTION 1854 Au cours de l'exécution d'un cycle d'usinage multiple. La longueur de l’usinage (paramètre Ly) doit être un multiple de la distance entre les usinages (paramètre Iy). Affecter aux paramètres une valeur correcte. 'Il n'y a pas d'outil programmé' DÉTECTION. CAUSE SOLUTION 1853 Au cours de l'exécution d'un cycle d'usinage multiple. La longueur de l’usinage (paramètre Lx) doit être un multiple de la distance entre les usinages (paramètre Ix). Affecter aux paramètres une valeur correcte. 'Ly doit être multiple de Iy' DÉTECTION CAUSE 1852 Pendant l'exécution du cycle. La taille de la poche moins le diamètre de l’outil est inférieure aux surépaisseurs de finition latérales (deux fois le paramètre ). Affecter au paramètre une valeur correcte. 'Lx doit être multiple de Ix' DÉTECTION CAUSE 1851 Pendant l'exécution du cycle. Le paramètre Q (matière à enlever) a valeur 0. Affecter au paramètre une valeur différente de zéro. 'POCHE RECTANGULAIRE: Surépaisseur de finition DELTA supérieur à la poche' DÉTECTION CAUSE 1850 Pendant l'exécution du cycle. Le paramètre Q (matière à enlever) a valeur 0. Affecter au paramètre une valeur différente de zéro. 'MOYEU CIRCULAIRE: Q = 0' DÉTECTION CAUSE SOLUTION 1849 Au cours de l'exécution d'un cycle d'usinage multiple. Les possibles causes sont les suivantes: • Dans le profil il y a un segment courbe avec rayon zéro. • Dans un usinage multiple en arc ou en circonférence, les deux coordonnées du centre coïncident avec le point initial. Réviser la programmation. Au cours de l’exécution du cycle de palpeur #PROBE 2 ou #PROBE 9. Le diamètre du palpeur est supérieur au diamètre du trou à mesurer ou au trou utilisé pour calibrer le palpeur. Corriger la définition du cycle fixe. 'Distance de retour E incorrecte' DÉTECTION CAUSE SOLUTION Au cours de l’exécution du cycle de palpeur #PROBE 2 ou #PROBE 9. Le paramètre E (distance de recul) a une valeur incorrecte. Affecter au paramètre une valeur entre 0 et le diamètre du trou. S o l ut i o n s d ’ e r r e ur s . 1857 'Il n'y a pas de correcteur sélectionné' DÉTECTION CAUSE SOLUTION 1858 'Programmer I = 0/1' DÉTECTION CAUSE SOLUTION 1859 SOLUTION SOLUTION Pendant l'exécution du cycle. L’avance pour l’opération d'ébauchage a une valeur 0. Définir une avance supérieure à 0. CNC 8070 'Poche avec îlots: S d'ébauchage non valide' DÉTECTION CAUSE SOLUTION 1868 Pendant l'exécution du cycle. L'outil programmé n'existe pas dans la table des outils. Définir l’outil dans la table ou sélectionner un autre outil. 'Poche avec îlots: F d'ébauchage non valide' DÉTECTION CAUSE SOLUTION 1867 Au cours de l'exécution du cycle de palpeur #PROBE 1. La position du palpeur d’établi dans le cycle est mal définie. Un des paramètres X Y Z est supérieur à son paramètre U V W correspondant. Les paramètres X Y Z font référence aux cotes minimales du palpeur et les paramètres U V W aux cotes maximales. Définir la position du palpeur de sorte que U > X, V > Y, W > Z. 'Poche avec îlots: Il n'existe pas T d'ébauchage' DÉTECTION CAUSE SOLUTION 1866 Au cours de l'exécution du cycle de palpeur #PROBE 1. Le cycle a détecté que l’outil est usé. L’usure mesurée est supérieure à la tolérance permise (paramètres L ou M). Changer d’outil et exécuter de nouveau le cycle. '#PROBE 1: les paramètres U, V, W doivent être supérieurs à X, Y, Z' DÉTECTION CAUSE 1865 Au cours de l'exécution du cycle de palpeur #PROBE 1. À l’heure d’exécuter le cycle, un plan de travail défini avec G20 est actif. Activer un plan principal G17, G18 ou G19 pour exécuter le cycle. 'Outil usé' DÉTECTION CAUSE 1864 Au cours de l'exécution d'un cycle de palpeur #PROBE. Le paramètre B a une valeur négative. Affecter au paramètre une valeur positive. '#PROBE 1: interdit avec G20 active' DÉTECTION CAUSE SOLUTION 1863 Au cours de l'exécution du cycle de palpeur #PROBE 3. Le paramètre K (axe de palpage) a une valeur incorrecte. Le paramètre K n'admet que les valeurs 0 (axe d'abscisses), 1 (axe d'ordonnées) ou 2 (axe longitudinal). 'La distance de sécurité B doit être supérieur à zéro' DÉTECTION CAUSE SOLUTION 1862 Au cours de l'exécution du cycle de palpeur #PROBE 2. À l’heure d’exécuter le cycle, un plan de travail défini avec G20 est actif. Activer un plan principal G17, G18 ou G19 pour exécuter le cycle. 'Programmer K = 0/1/2' DÉTECTION CAUSE SOLUTION 1861 Au cours de l'exécution d'un cycle de palpeur #PROBE. Le paramètre I (type de calibrage) a une valeur incorrecte. Le paramètre I n’admet que les valeurs 0 (calibrage simple) ou 1 (calibrage double). 'Le plan actif pour le calibrage du palpeur doit être G17, G18 ou G19' DÉTECTION CAUSE SOLUTION 1860 Au cours de l’exécution du cycle de palpeur #PROBE 1 ou #PROBE 2. Il n’y a pas de correcteur d’outil actif pour le cycle de calibrage d’outil. Programmer le correcteur (fonction D) avant du cycle. Pendant l'exécution du cycle. La vitesse pour l’opération d'ébauchage a une valeur 0. Définir une vitesse supérieure à 0. (REF: 1901) 'Poche avec îlots: Il n'existe pas T de finition' DÉTECTION CAUSE SOLUTION Pendant l'exécution du cycle. L'outil programmé n'existe pas dans la table des outils. Définir l’outil dans la table ou sélectionner un autre outil. ·97· S o l ut i o n s d ’ e r r e ur s . 1869 'Poche avec îlots: F de finition non valide' DÉTECTION CAUSE SOLUTION 1870 'Poche avec îlots: S de finition non valide' DÉTECTION CAUSE SOLUTION 1871 SOLUTION SOLUTION 1879 SOLUTION 1880 Pendant l'exécution du cycle. Le rayon de l’outil de semi-finition a une valeur 0 ou il est trop grand pour la géométrie de la poche. Définir l’outil dans la table ou sélectionner un autre outil. 'Poche avec îlots: Il n'existe pas T de semi-finition' DÉTECTION CAUSE SOLUTION ·98· Pendant l'exécution du cycle. Le rayon de la pointe (Rp) de l’outil de finition est supérieur à son rayon (R). Corriger la valeur du rayon de la pointe. 'Poche avec îlots: Rayon de l'outil de semi-finition non valide' DÉTECTION CAUSE (REF: 1901) Pendant l'exécution du cycle. Le profil de profondeur programmé n'existe pas. Sélectionner un profil existant ou générer le profil programmé. 'Poche avec îlots: Rayon de la pointe de l'outil de finition non valide' DÉTECTION CAUSE SOLUTION CNC 8070 Pendant l'exécution du cycle. Géométrie du profil de surface mal programmée. Corriger la géométrie du profil depuis l’éditeur de profils. 'Poche avec îlots: Le profil sur Z n'existe pas' DÉTECTION CAUSE SOLUTION 1878 Pendant l'exécution du cycle. Le profil de surface programmé n'existe pas. Sélectionner un profil existant ou générer le profil programmé. 'Poche avec îlots: Profil sur XY non valide' DÉTECTION CAUSE SOLUTION 1877 Pendant l'exécution du cycle. Le paramètre P (profondeur de la poche) a une valeur 0. Affecter au paramètre une valeur correcte. 'Poche avec îlots: Le profil sur XY n'existe pas' DÉTECTION CAUSE SOLUTION 1876 Pendant l'exécution du cycle. La surépaisseur latérale pour la finition (paramètre ) est supérieur au diamètre de l’outil. Corriger la surépaisseur latérale pour la finition ou sélectionner un autre outil. 'Poche avec îlots: Profondeur non valide' DÉTECTION CAUSE SOLUTION 1875 Pendant l'exécution du cycle. Sur une poche 2D, le pas d’usinage pour la finition (paramètre ) est supérieur au diamètre de l’outil. Sur une poche 2D, le pas d'usinage pour la finition (paramètre ) est zéro. Corriger le pas d'usinage. 'Poche avec îlots: Surépaisseur latérale non valide' DÉTECTION CAUSE 1874 Pendant l'exécution du cycle. Le pas d’usinage pour l’ébauchage (paramètre ) est supérieur au diamètre de l’outil. Corriger le pas d’usinage ou sélectionner un autre outil. 'Poche avec îlots: Pas de finition non valide' DÉTECTION CAUSE 1873 Pendant l'exécution du cycle. La vitesse pour l’opération de finition a une valeur 0. Définir une vitesse supérieure à 0. 'Poche avec îlots: Pas d'ébauchage non valide' DÉTECTION CAUSE SOLUTION 1872 Pendant l'exécution du cycle. L’avance pour l’opération de finition a une valeur 0. Définir une avance supérieure à 0. Pendant l'exécution du cycle. L'outil programmé n'existe pas dans la table des outils. Définir l’outil dans la table ou sélectionner un autre outil. S o l ut i o n s d ’ e r r e ur s . 1881 'Poche avec îlots: F de semi-finition non valide' DÉTECTION CAUSE SOLUTION 1882 'Poche avec îlots: S de semi-finition non valide' DÉTECTION CAUSE SOLUTION 1883 SOLUTION SOLUTION SOLUTION SOLUTION Exécution du déplacement de va-et-vient pour le réglage du moment d’inertie. La distance programmée dans le déplacement de va-et-vient est insuffisante. Programmer une distance supérieure. 'Déplacement de va-et-vient: Distance parcourue trop grande' DÉTECTION CAUSE SOLUTION 1900 Pendant l'exécution du cycle. Le type de finition (paramètre Q) n'est pas valide. Affecter aux paramètres une valeur correcte. 'Déplacement de va-et-vient: Distance parcourue trop petite' DÉTECTION CAUSE SOLUTION 1890 Pendant l'exécution du cycle. L’angle de pénétration pour la finition (paramètre ) n’est pas compris entre 0º et 90º. Corriger l’angle de pénétration; programmer une valeur entre 0º et 90º. 'Poche avec îlots: Type de finition non valable' DÉTECTION CAUSE SOLUTION 1889 Pendant l'exécution du cycle. L’angle de pénétration pour l'ébauchage (paramètre ) n’est pas compris entre 0º et 90º. Corriger l’angle de pénétration; programmer une valeur entre 0º et 90º. 'Poche avec îlots: Angle de pénétration de l'outil de semi-finition non valable' DÉTECTION CAUSE SOLUTION 1888 Pendant l'exécution du cycle. Dans un profil de la poche un segment est mal défini (arrondissements, chanfreins, etc.). Corriger la géométrie du profil depuis l’éditeur de profils. 'Poche avec îlots: Angle de pénétration de l'outil d'ébauchage non valable' DÉTECTION CAUSE 1887 Pendant l'exécution du cycle. Dans un profil de la poche un arc est mal défini ou le profil a été modifié avec un programme différent de l’éditeur de profils. Corriger la géométrie du profil depuis l’éditeur de profils. 'Poche avec îlots: Géométrie de la poche non valide' DÉTECTION CAUSE 1886 Pendant l'exécution du cycle. La CNC ne peut pas simuler ou exécuter la poche parce que celle-ci se trouve déjà en exécution ou en simulation. Attendre à ce que la CNC finisse la simulation ou l’exécution. 'Poche avec îlots: Arc mal programmé dans le profil' DÉTECTION CAUSE 1885 Pendant l'exécution du cycle. La vitesse pour l’opération de semi-finition a une valeur 0. Définir une vitesse supérieure à 0. 'Poche avec îlots: Poche en exécution' DÉTECTION CAUSE 1884 Pendant l'exécution du cycle. L’avance pour l’opération de semi-finition a une valeur 0. Définir une avance supérieure à 0. Exécution du déplacement de va-et-vient pour le réglage du moment d’inertie. La distance programmée dans le déplacement de va-et-vient est trop grande. Programmer une distance inférieure. CNC 8070 'Donnée obligatoire non programmée' DÉTECTION CAUSE SOLUTION Pendant l'exécution du cycle. Il faut programmer un ou plusieurs paramètres obligatoires. Le paramètre incorrect sera indiqué dans le message d’erreur. Programmer tous les paramètres obligatoires du cycle. (REF: 1901) ·99· S o l ut i o n s d ’ e r r e ur s . 1901 'Donnée non valide' DÉTECTION CAUSE SOLUTION 1902 'La position initiale et le facteur de forme de l'outil sont incompatibles' DÉTECTION CAUSE SOLUTION 1903 1911 (REF: 1901) ·100· Pendant l'exécution du cycle. Le pas d’ébauchage est supérieur à la largeur de la plaquette. Programmer un pas d’ébauchage inférieur ou égal à la largeur de la plaquette. 'Facteur de forme non valide dans le cycle d’ébauchage' DÉTECTION CAUSE SOLUTION 1912 Pendant l'exécution du cycle. Le pas d'usinage a une valeur 0. Définir un pas d'usinage supérieur à 0. 'Pas d’ébauchage supérieur à la largeur de la plaquette' DÉTECTION CAUSE SOLUTION CNC 8070 Pendant l'exécution du cycle. La surépaisseur pour la finition a une valeur 0. Définir une surépaisseur pour la finition supérieure à 0. 'Pas d'ébauchage nul' DÉTECTION CAUSE SOLUTION 1910 Pendant l'exécution du cycle. L'avance de l'usinage a une valeur 0. Définir une avance supérieure à 0. 'La surépaisseur de matière n’a pas été programmée' DÉTECTION CAUSE SOLUTION 1909 Pendant l'exécution du cycle. Le facteur de forme n’est pas valide pour le cycle programmé. Corriger le facteur de forme ou sélectionner un autre outil. 'Avance F nulle antérieure au cycle' DÉTECTION CAUSE SOLUTION 1908 Pendant l'exécution du cycle. La largeur de l'outil a une valeur 0. Corriger la valeur de la largeur de l’outil ou sélectionner un autre outil. 'Facteur de forme de l'outil non valide' DÉTECTION CAUSE SOLUTION 1907 Pendant l'exécution du cycle. Il n'y a pas d'outil programmé. Programmer un outil avant le cycle ou charger un outil sur la broche. 'RAINURAGE: Largeur de la plaquette nulle. DÉTECTION CAUSE SOLUTION 1906 Pendant l'exécution du cycle. Arc mal défini dans la géométrie du cycle fixe. Corriger la programmation. 'L’outil n’a pas été programmé' DÉTECTION CAUSE SOLUTION 1905 Pendant l'exécution du cycle. La position initiale de l’outil n’est pas compatible avec le facteur de forme et la géométrie de l’outil. Positionner l’outil adéquatement ou changer d’outil. 'Arc mal programmé' DÉTECTION CAUSE SOLUTION 1904 Pendant l'exécution du cycle. Un paramètre du cycle a une valeur incorrecte. Le paramètre incorrect sera indiqué dans le message d’erreur. Corriger la programmation. Pendant l'exécution du cycle. Le facteur de forme n’est pas valide pour le cycle programmé. Corriger le facteur de forme ou sélectionner un autre outil. 'Angle de la plaquette non valide' DÉTECTION CAUSE SOLUTION Pendant l'exécution du cycle. L’angle de la plaquette n’est pas valide pour le cycle programmé. Corriger l’angle de la plaquette ou sélectionner un autre outil. S o l ut i o n s d ’ e r r e ur s . 1913 'Angle de coupe de la plaquette non valide' DÉTECTION CAUSE SOLUTION 1914 'F d'ébauchage non valide' DÉTECTION CAUSE SOLUTION 1915 SOLUTION SOLUTION Pendant l'exécution du cycle. La géométrie programmée dans le cycle fixe ne correspond pas à une géométrie intérieure, comme indiqué dans le cycle. Changer la géométrie ou définir dans le cycle que la géométrie est extérieure. 'Géométrie non valide' DÉTECTION CAUSE SOLUTION 1924 Pendant l'exécution du cycle. La géométrie programmée dans le cycle fixe ne correspond pas à une géométrie extérieure, comme indiqué dans le cycle. Changer la géométrie ou définir dans le cycle que la géométrie est intérieure. 'Géométrie non intérieure programmée' DÉTECTION CAUSE 1923 Pendant l'exécution du cycle. Il faut programmer le profil qui définit la géométrie du cycle fixe. Définir le profil qui définit la géométrie du cycle. 'Géométrie non extérieure programmée' DÉTECTION CAUSE 1922 Pendant l'exécution du cycle. Le profil défini dans le cycle fixe n’est pas valide parce qu’il se coupe lui-même. Programmer un profil qui ne se coupe pas lui-même. 'Le profil n’a pas été programmé' DÉTECTION CAUSE SOLUTION 1921 Pendant l'exécution du cycle. Le profil défini dans le cycle fixe n'est pas valide parce qu'il est fermé. Programmer un profil ouvert. 'Le profil programmé se coupe lui-même' DÉTECTION CAUSE SOLUTION 1920 Pendant l'exécution du cycle. La vitesse pour l’opération de finition a une valeur 0. Définir une vitesse supérieure à 0. 'Le profil programmé est fermé' DÉTECTION CAUSE SOLUTION 1919 Pendant l'exécution du cycle. La vitesse pour l’opération d'ébauchage a une valeur 0. Définir une vitesse supérieure à 0. 'S de finition non valide' DÉTECTION CAUSE SOLUTION 1918 Pendant l'exécution du cycle. L’avance pour l’opération de finition a une valeur 0. Définir une avance supérieure à 0. 'S d'ébauchage non valide' DÉTECTION CAUSE SOLUTION 1917 Pendant l'exécution du cycle. L’avance pour l’opération d'ébauchage a une valeur 0. Définir une avance supérieure à 0. 'F de finition non valide' DÉTECTION CAUSE SOLUTION 1916 Pendant l'exécution du cycle. L’angle de coupe n’est pas valide pour le cycle programmé. Corriger l'angle de coupe ou sélectionner un autre outil. Pendant l'exécution du cycle. La géométrie du cycle fixe est incorrecte. Corriger la programmation. CNC 8070 'Mémoire insuffisante' DÉTECTION CAUSE SOLUTION Pendant l'exécution du cycle. Le système ne dispose pas de mémoire pour continuer à résoudre la poche. Contacter FAGOR. (REF: 1901) ·101· S o l ut i o n s d ’ e r r e ur s . 1925 'Ébauchage et finition non programmés' DÉTECTION CAUSE SOLUTION 1926 'Sommet mal programmé' DÉTECTION CAUSE SOLUTION 1927 SOLUTION 1935 (REF: 1901) Pendant l'exécution du cycle. Aucun axe longitudinal a été défini dans le canal. Mettre le paramètre machine LONGAXIS à TRUE pour que l'axe soit longitudinal. 'Aucun axe n'a été défini comme FACEAXIS dans le cycle d'axe C' DÉTECTION CAUSE SOLUTION ·102· Pendant l'exécution du cycle. La largeur de la plaquette est supérieure à la rainure ou le cycle ne peut pas laisser la surépaisseur programmée. Vérifier que l’outil sélectionné peut usiner la rainure programmée, en laissant la surépaisseur de finition programmée. 'Aucun axe n'a été défini comme LONGAXIS dans le cycle d'axe C' DÉTECTION CAUSE SOLUTION 1936 Pendant l'exécution du cycle. Le canal qui exécute le cycle ne dispose pas de broche pour l’outil motorisé. Céder un outil motorisé au canal ou exécuter le cycle dans un canal avec outil motorisé. 'Largeur de l'outil non valide' DÉTECTION CAUSE CNC 8070 Pendant l'exécution du cycle. Le canal qui exécute le cycle ne dispose pas de broche. Céder une broche au canal ou exécuter le cycle dans un canal avec broche. 'L'outil motorisé pour exécuter le cycle n'existe pas' DÉTECTION CAUSE SOLUTION 1934 Pendant l'exécution du cycle. La profondeur d'usinage a une valeur 0. Définir une profondeur d’usinage différente de 0. 'La broche pour exécuter le cycle n'existe pas' DÉTECTION CAUSE SOLUTION 1933 Pendant l'exécution du cycle. Le pas de perçage a une valeur 0. Définir un pas de perçage différent de 0. 'La profondeur n’a pas été programmée' DÉTECTION CAUSE SOLUTION 1932 Pendant l'exécution du cycle. La vitesse de la broche a une valeur 0. Définir une avance supérieure à 0. 'Le pas de perçage programmé est nul' DÉTECTION CAUSE SOLUTION 1931 Pendant l'exécution du cycle. Le pas de rainurage est plus grand que la largeur de la plaquette. Programmer un pas de rainurage inférieur ou égal à la largeur de la plaquette. 'L’avance de la broche n’a pas été programmée' DÉTECTION CAUSE SOLUTION 1930 Pendant l'exécution du cycle. L’outil n’est pas valide pour la géométrie du cycle programmé. Sélectionner un autre outil. 'Pas de rainurage supérieur à la largeur de la plaquette' DÉTECTION CAUSE SOLUTION 1929 Pendant l'exécution du cycle. La géométrie du cycle fixe est incorrecte. Corriger la programmation. 'Plaquette non valide pour le profil programmé' DÉTECTION CAUSE SOLUTION 1928 Pendant l'exécution du cycle. Aucune opération n'est définie dans le cycle fixe. Dans le cycle fixe, on doit définir l'opération d'ébauchage ou de finition. Si une opération n’a pas d’outil, le cycle ne l’exécute pas ; une opération au moins doit avoir un outil. Pendant l'exécution du cycle. Aucun axe longitudinal n'a été défini dans le canal. Mettre le paramètre machine FACEAXIS à TRUE pour que l'axe soit frontal. S o l ut i o n s d ’ e r r e ur s . 1937 'On n'a pas défini un axe ou broche pour l'axe C' DÉTECTION CAUSE SOLUTION 1938 'Aucun axe n'est défini pour l'axe Y' DÉTECTION CAUSE SOLUTION 1949 Pendant l'exécution du cycle. Le cycle fixe est défini pour l'axe C et aucun axe C est dans le canal. Définir un axe ou broche dans le canal comme axe C (paramètre CAXIS). Pendant l'exécution du cycle. Le cycle fixe est programmé pour l'axe Y et aucun axe Y ne se trouve dans le canal. Définir une configuration d’axes type trièdre dans le canal (paramètre GEOCONFIG) avec un axe Y. 'La plaquette ne peut pas usiner complètement le profil' DÉTECTION Pendant l’exécution d’un cycle fixe d’ébauche et poursuite de profil de tour. CAUSE La géométrie de l’outil ne lui permet pas d'usiner tout le profil programmé. EN CONSÉQUENCELe cycle ne peut pas usiner entièrement le profil programmé. SOLUTION Modifier le profil ou changer d’outil pour qu’il puise usiner le profil. 1950 'La cote Z de la surface de la pièce n'est pas programmée' DÉTECTION CAUSE SOLUTION 1951 'La cote Z de sécurité n'est pas programmée' DÉTECTION CAUSE SOLUTION 1952 Pendant l'exécution du cycle. Le rayon de l’outil de finition a une valeur 0. Corriger la valeur du rayon dans la table d’outils ou sélectionner un autre outil. 'Rayon outil de semi-finition nul' DÉTECTION CAUSE SOLUTION 1958 Pendant l'exécution du cycle. Le rayon de l’outil d’ébauchage a une valeur 0. Corriger la valeur du rayon dans la table d’outils ou sélectionner un autre outil. 'Rayon outil de finition nul' DÉTECTION CAUSE SOLUTION 1957 Pendant l'exécution du cycle. Il faut programmer le pas d'ébauchage (paramètre D) Corriger la programmation. 'Rayon outil d'ébauchage nul' DÉTECTION CAUSE SOLUTION 1956 Pendant l'exécution du cycle. Il faut programmer le pas de pénétration (paramètre I) Corriger la programmation. 'Le pas d'ébauchage n'est pas programmé' DÉTECTION CAUSE SOLUTION 1955 Pendant l'exécution du cycle. Il faut programmer la profondeur de la pièce (paramètre P). Corriger la programmation. 'Le pas de profondeur n'est pas programmé' DÉTECTION CAUSE SOLUTION 1954 Pendant l'exécution du cycle. Il faut programmer le plan de sécurité (paramètre Zs). Corriger la programmation. 'La profondeur de la pièce n'est pas programmée' DÉTECTION CAUSE SOLUTION 1953 Pendant l'exécution du cycle. Il faut programmer la cote Z de la surface de la pièce (paramètre Z). Corriger la programmation. Pendant l'exécution du cycle. Le rayon de l’outil de semi-finition a une valeur 0. Corriger la valeur du rayon dans la table d’outils ou sélectionner un autre outil. CNC 8070 'Rayon d'outil d'ébauchage trop grand' DÉTECTION CAUSE SOLUTION Pendant l'exécution du cycle. Le rayon de l’outil d'ébauchage est trop grand pour la géométrie de la poche. Corriger la valeur du rayon dans la table d’outils ou sélectionner un autre outil. (REF: 1901) ·103· S o l ut i o n s d ’ e r r e ur s . 1959 'Rayon d'outil de finition trop grand' DÉTECTION CAUSE SOLUTION 1960 'Rayon d'outil de semi-finition trop grand' DÉTECTION CAUSE SOLUTION 1961 CNC 8070 (REF: 1901) ·104· Pendant l'exécution du cycle. Le plan de sécurité se trouve dans la pièce. Affecter au paramètre une valeur correcte. 'Le profil sur XY n'est pas programmé' DÉTECTION CAUSE SOLUTION 1970 Pendant l'exécution du cycle. La cote Z de commencement du cycle se trouve dans de la pièce. La cote Z de commencement du cycle doit être au-dessus du plan de référence. 'Cote Z de sécurité non valide' DÉTECTION CAUSE SOLUTION 1969 Pendant l'exécution du cycle. Le type de finition n'est pas valide. Affecter aux paramètres une valeur correcte. 'Cote Z du plan de départ non valide' DÉTECTION CAUSE SOLUTION 1968 Pendant l'exécution du cycle. Le pas d’usinage pour la finition est supérieur au diamètre de l’outil. Corriger le pas d’usinage ou sélectionner un autre outil. 'Type de finition non valide' DÉTECTION CAUSE SOLUTION 1967 Pendant l'exécution du cycle. Le pas d’usinage pour l’ébauchage est supérieur au diamètre de l’outil. Corriger le pas d’usinage ou sélectionner un autre outil. 'Le pas de finition programmé est supérieur au diamètre de l'outil' DÉTECTION CAUSE SOLUTION 1966 Pendant l'exécution du cycle. L’angle de pénétration pour la semi-finition n’est pas compris entre 0º et 90º. Corriger l’angle de pénétration; programmer une valeur entre 0º et 90º. 'Le pas d'ébauchage programmé est supérieur au diamètre de l'outil' DÉTECTION CAUSE SOLUTION 1965 Pendant l'exécution du cycle. L’angle de pénétration pour l'ébauchage n’est pas compris entre 0º et 90º. Corriger l’angle de pénétration; programmer une valeur entre 0º et 90º. 'Angle de pénétration dans la semi-finition non valide' DÉTECTION CAUSE SOLUTION 1964 Pendant l'exécution du cycle. Le rayon de la pointe (Rp) de l’outil de finition est supérieur à son rayon (R). Corriger la valeur du rayon de la pointe. 'Angle de pénétration dans l'ébauchage non valide' DÉTECTION CAUSE SOLUTION 1963 Pendant l'exécution du cycle. Le rayon de l’outil de semi-finition est trop grand pour la géométrie de la poche. Corriger la valeur du rayon dans la table d’outils ou sélectionner un autre outil. 'Rayon de la pointe de l'outil de finition non valide' DÉTECTION CAUSE SOLUTION 1962 Pendant l'exécution du cycle. Le rayon de l’outil de finition est trop grand pour la géométrie de la poche. Corriger la valeur du rayon dans la table d’outils ou sélectionner un autre outil. Pendant l'exécution du cycle. Le profil de surface n'existe pas. Éditer le profil. La CNC enregistre les profils dans le dossier ..\Users\Profile. 'Le profil sur Z n'est pas programmé' DÉTECTION CAUSE SOLUTION Pendant l'exécution du cycle. Le profil de profondeur n'existe pas. Éditer le profil. La CNC enregistre les profils dans le dossier ..\Users\Profile. S o l ut i o n s d ’ e r r e ur s . 1971 'Profil programmé sur XY ouvert' DÉTECTION CAUSE SOLUTION 1972 'Profil sur XY non valide' DÉTECTION CAUSE SOLUTION 1973 SOLUTION SOLUTION SOLUTION Au cours de l'exécution. En exécutant le cycle de calibrage de cinématiques, le palpeur a touché la sphère alors qu'il ne devait pas la toucher. Réviser la programmation. Avant d’exécuter le cycle, placer le palpeur su la position correcte : au dessus de la bille, à une distance d’environ 10 mm (0,4 pouces). 'Absence de contact avec la sphère' DÉTECTION CAUSE SOLUTION 1988 Au cours de l'exécution. En exécutant le cycle de calibrage de cinématiques, le palpeur n’a pas touché la sphère. Réviser la programmation. Avant d’exécuter le cycle, placer le palpeur su la position correcte : au dessus de la bille, à une distance d’environ 10 mm (0,4 pouces). 'Le palpeur a touché la sphère sans le prévoir' DÉTECTION CAUSE 1987 Au cours de l'exécution. Le rayon de l’outil de perçage est trop grand pour la géométrie de la poche. Corriger la valeur du rayon dans la table d’outils ou sélectionner un autre outil. 'Le palpeur n’a pas touché la sphère' DÉTECTION CAUSE 1986 Pendant l'exécution du cycle. Aucune opération n'est définie dans le cycle fixe. Dans le cycle fixe, on doit définir l'opération d'ébauchage ou de finition. Si une opération n’a pas d’outil, le cycle ne l’exécute pas ; une opération au moins doit avoir un outil. 'Rayon d'outil de perçage trop grand' DÉTECTION CAUSE SOLUTION 1985 Au cours de l'exécution d'un cycle de palpeur. Le palpeur n’a pas touché la pièce pendant le déplacement de palpage. Corriger la définition du cycle fixe. 'ÉBAUCHE et FINITION non programmés' DÉTECTION CAUSE SOLUTION 1977 Pendant l'exécution du cycle. Deux profils de surface génèrent une intersection non valide. Vérifier que les profils de surface n’ont pas de segments en commun, l’intersection des profils devant se produire à des points. 'Le palpage n'existe pas' DÉTECTION CAUSE SOLUTION 1976 Pendant l'exécution du cycle. Un profil de profondeur est fermé ou le cycle ne peut pas usiner un profil de profondeur avec l’outil programmé. Vérifier que les profils de profondeur sont corrects. 'Intersection des profils non valide' DÉTECTION CAUSE SOLUTION 1975 Pendant l'exécution du cycle. Le profil de surface n'existe pas. Éditer le profil. La CNC enregistre les profils dans le dossier ..\Users\Profile. 'Profil sur z non valide' DÉTECTION CAUSE 1974 Pendant l'exécution du cycle. Un profil de surface n’est pas un profil fermé, ses points initial et final ne sont pas les mêmes. Vérifier que tous les profils de surface sont fermés. Au cours de l'exécution. Le signal du palpeur n'est pas arrivé lorsqu'on prévoyait de toucher la sphère. Vérifier que les paramètres de cinématique présente une erreur maximale de 1 mm. 'Le type de palpeur n'est pas valable (P6)' DÉTECTION CAUSE SOLUTION CNC 8070 (REF: 1901) Au cours de l'exécution. Le type de palpeur sélectionné n'est pas valide. Le paramètre P6 n’admet que les valeurs 0 et 1. ·105· S o l ut i o n s d ’ e r r e ur s . 1989 'Impossible de calibrer ce type de cinématique' DÉTECTION CAUSE 1990 'Absence de contact avec la sphère. Vérifier que le palpeur se trouve au-dessus de la bille à une distance inférieure au double de la distance de sécurité' DÉTECTION CAUSE SOLUTION 1991 SOLUTION (REF: 1901) ·106· Au cours de l'exécution. Les axes rotatifs ne se trouvent pas en position de repos. Placer les axes rotatifs en position de repos. 'La position de repos des axes rotatifs de la cinématique doit être zéro' DÉTECTION CAUSE CNC 8070 Au cours de l'exécution. Les positions initiale et finale des axes rotatifs sont les mêmes. La position finale des axes rotatifs doit être différente de la position initiale. 'Les axe rotatifs de la cinématique doivent se trouver en position de repos' DÉTECTION CAUSE SOLUTION 1993 Au cours de l'exécution. Le palpeur ne se trouve pas au-dessus de la bille ou très loin. Le palpeur doit se trouver au-dessus de la bille à une distance inférieure au double de la distance de sécurité. 'Erreur de paramétrage. Les positions initiale et finale ne peuvent pas être égales' DÉTECTION CAUSE SOLUTION 1992 Au cours de l'exécution. Le calibrage de ce type de cinématique n'est pas implémenté. Au cours de l'exécution. Dans les paramètres machine de la cinématique, la position de repos des axes doit être 0. Mettre sur zéro la position de repos dans les paramètres machine. S o l ut i o n s d ’ e r r e ur s . 2000-2999 2000 'Rayon d'outil supérieur au rayon de l'arc' DÉTECTION CAUSE SOLUTION 2001 'Profil endommagé par compensation de rayon' DÉTECTION CAUSE SOLUTION 2002 SOLUTION SOLUTION SOLUTION Au cours de l'exécution. Avec la compensation de rayon active, il y a des trop de blocs de non-déplacement (assignations de paramètres P, variables, etc.) entre deux blocs de déplacement. Réduire le nombre de blocs de non déplacement programmés; par exemple, regrouper plusieurs de ces blocs en un seul. 'Le dernier bloc de compensation de rayon doit être linéaire' DÉTECTION CAUSE SOLUTION 2006 Au cours de l'exécution. Dans l’usinage de deux arcs consécutifs formant une boucle (les deux arcs se coupent), le rayon de l’outil est trop grand pour pouvoir usiner l’intérieur de la boucle. Utiliser un outil de rayon inférieur. 'Trop de blocs sans déplacement entre deux blocs avec compensation de rayon' DÉTECTION CAUSE 2005 Au cours de l'exécution. Après avoir activé la compensation de rayon (G41 ou G42), le bloc suivant de déplacement est un bloc circulaire. La compensation de rayon ne peut pas commencer dans un bloc circulaire. La compensation de rayon doit commencer dans un bloc de déplacement linéaire. Par conséquent, le bloc de déplacement après G41-G42 doit être un bloc de déplacement linéaire. 'Rayon d'outil trop grand sur des arcs consécutifs' DÉTECTION CAUSE 2004 Au cours de l'exécution. Le rayon de l’outil est trop grand pour le profil programmé ; l’outil endommage le profil. Utiliser un outil de rayon inférieur. 'Le premier bloc de compensation de rayon doit être linéaire' DÉTECTION CAUSE 2003 Au cours de l'exécution. Le rayon de l’outil est supérieur au rayon de l’arc que l’on essaie d’usiner. Utiliser un outil de rayon inférieur. Au cours de l'exécution. Après avoir désactivé la compensation de rayon (G40), le bloc suivant de déplacement est un bloc circulaire. La compensation de rayon ne peut pas finir dans un bloc circulaire. La compensation de rayon doit terminer dans un bloc de déplacement linéaire. Par conséquent, le bloc de déplacement après G40 doit être un bloc de déplacement linéaire. 'Le changement de compensation (G41/G42) doit se faire sur une trajectoire linéaire' DÉTECTION CAUSE SOLUTION Au cours de l'exécution. Le programme a changé le type de compensation de rayon (de G41 a G42 ou viceversa) et le bloc de déplacement suivant est un bloc circulaire. Il n’est pas permis de changer le type de compensation de rayon si le bloc suivant de déplacement est un arc. Changer le type de compensation de rayon sur une trajectoire linéaire. CNC 8070 (REF: 1901) ·107· S o l ut i o n s d ’ e r r e ur s . 2007 'Avec G138; G40 n'est pas admise après le premier bloc de compensation' DÉTECTION CAUSE SOLUTION 2008 'Avec G138, le changement G41/G42 n'est pas admis après le premier bloc de compensation' DÉTECTION CAUSE SOLUTION 2009 SOLUTION SOLUTION CNC 8070 (REF: 1901) ·108· Au cours de l'exécution. En usinant un arc avec la compensation de rayon active, le rayon de l’outil a changé par rapport au bloc précédent. Avec la compensation de rayon active, ne pas changer le rayon de l’outil pendant l’exécution d’un arc. Il n'existe pas intersection entre ligne et arc: rayon de l'outil trop grand. DÉTECTION CAUSE SOLUTION 2015 Pendant l'exécution. La compensation de rayon a supprimé un bloc inutile. Accepter la modification proposée et poursuivre l'exécution. 'Rayon d'outil différent entre la trajectoire antérieure et un arc' DÉTECTION CAUSE 2014 Pendant l'exécution. Le rayon de l'outil est trop grand pour l'arc programmé. Utiliser un outil avec un rayon inférieur, supprimer l'arc du profil ou programmer un arc plus grand. Un bloc de transition non pertinent a été supprimé. DÉTECTION CAUSE SOLUTION 2013 Pendant l'exécution. Le rayon de l'outil est trop grand pour l'arc programmé. Utiliser un outil avec un rayon inférieur, supprimer l'arc du profil ou programmer un arc plus grand. 'Mouvement de compensation sur trajectoire circulaire (profil endommagé)' DÉTECTION CAUSE SOLUTION 2012 Au cours de l'exécution. Dans l’arc programmé, la différence entre le rayon initial et le rayon final est supérieure à la tolérance permise. Vérifier la programmation de l'arc. 'Rayon d'outil trop grand en calculant la compensation entre les arcs' DÉTECTION CAUSE SOLUTION 2011 Au cours de l'exécution. Après avoir activé la compensation de rayon avec le mode direct (G138), un changement du type de compensation (de G41 a G42 ou vice-versa) est programmé avant le premier bloc de déplacement. Pour activer la compensation de rayon avec le mode direct (G138), la CNC a besoin d’un bloc de déplacement supplémentaire dans le plan, en plus du bloc d’activation. Après ce déplacement, la CNC permet de changer le type de compensation de rayon. S’il n’est pas possible de programmer ce bloc, utiliser le mode indirect (G139) pour activer la compensation de rayon. 'Différence entre le rayon initial et final de l'arc trop grande' DÉTECTION CAUSE 2010 Au cours de l'exécution. Après avoir activé la compensation de rayon avec le mode direct (G138), il existe une annulation de la compensation avant le premier bloc de déplacement. Pour activer la compensation de rayon avec le mode direct (G138), la CNC a besoin d’un bloc de déplacement supplémentaire dans le plan, en plus du bloc d’activation. Après ce déplacement, la CNC permet d'annuler la compensation de rayon. S’il n’est pas possible de programmer ce bloc, utiliser le mode indirect (G139) pour activer la compensation de rayon. Pendant l'exécution. Le rayon de l'outil est trop grand pour usiner la partie du profil indiquée. Utiliser un outil de rayon inférieur. Il n'existe pas intersection entre ligne et arc: rayon de l'outil trop grand. DÉTECTION CAUSE SOLUTION Pendant l'exécution. Le rayon de l'outil est trop grand pour usiner la partie du profil indiquée. Utiliser un outil de rayon inférieur. S o l ut i o n s d ’ e r r e ur s . 2016 'Le profil a été modifié pour éviter une collision' DÉTECTION CAUSE SOLUTION 2017 'Programmation non autorisée avec détection de collisions active' DÉTECTION CAUSE SOLUTION 2051 SOLUTION SOLUTION SOLUTION Pendant l'exécution. Le type d'arrondissement programmé n'est pas valide. Consulter le manuel de programmation pour voir le format de cette instruction. #HSC : tangente initiale indéterminée. DÉTECTION CAUSE SOLUTION 2105 Pendant l'exécution. L’erreur de contour programmé est trop petite pour être traitée. Programmer l'instruction avec une erreur de contour supérieure à 20 microns. #ROUNDPAR : paramètre erroné. DÉTECTION CAUSE SOLUTION 2104 Au cours de l'exécution. La trajectoire générée par la CNC sur G05, G60 ou HSC reste hors des limites actives du parcours. Vérifier que la trajectoire programmée se trouve dans les limites de logiciel et l’exécuter en G7 ou G50 pour éviter le dépassement. Au besoin, désactiver le mode HSC (#HSC OFF). #ROUNDPAR : paramètre trop petit. DÉTECTION CAUSE SOLUTION 2103 Au cours de l'exécution. La trajectoire générée par la CNC sur G05, G60 ou HSC reste hors des limites actives du parcours. Vérifier que la trajectoire programmée se trouve dans les limites de logiciel et l’exécuter en G7 ou G50 pour éviter le dépassement. Au besoin, désactiver le mode HSC (#HSC OFF). 'Limite logiciel négative dépassée sur G5, G60 ou HSC' DÉTECTION CAUSE 2102 Au cours de l'exécution. La CNC ne permet pas d’activer le contrôle tangentiel avec les splines actifs ni viceversa. Désactiver les splines avant d’activer le contrôle tangentiel ou vice-versa. 'Limite logiciel positive dépassée sur G5, G60 ou HSC' DÉTECTION CAUSE 2101 Au cours de l'exécution. La détection de collisions n’admet pas certains processus comme recherche de zéro, déplacement avec palpeur, etc. Ne pas activer la détection de collisions si un de ces processus est programmé. 'Programmation de splines et contrôle tangentiel incompatibles' DÉTECTION CAUSE 2100 Au cours de l'exécution. La détection de collisions pendant la compensation de rayon a détecté une trajectoire qui endommage le profil programmé et l’a supprimée. En fonction de la collision détectée, sa solution peut consister à utiliser un outil avec un rayon inférieur, programmer le profil autrement ou simplement accepter la modification proposée par le processus de détection de collisions. Pendant l'exécution. Les possibles causes sont les suivantes: • Le point pour commencer le #HSC coïncide avec le point antérieur et la tangente est indéterminée. • Un axe seulement de la tangente a été programmé. Programmer un point antérieur différent du point d'entrée du #HSC et les deux axes de la tangente. CNC 8070 #HSC : tangente finale indéterminée. DÉTECTION CAUSE SOLUTION Pendant l'exécution. Les possibles causes sont les suivantes: • Le point pour finir le #HSC coïncide avec le point antérieur et la tangente est indéterminée. • Un axe seulement de la tangente a été programmé. Programmer un point de sortie différent du point final du #HSC et les deux axes de la tangente. (REF: 1901) ·109· S o l ut i o n s d ’ e r r e ur s . 2106 HSC: Erreur interne dans le mode HSC. DÉTECTION CAUSE SOLUTION 2108 'HSC: Changement de mode interdit' DÉTECTION CAUSE SOLUTION 2109 SOLUTION SOLUTION SOLUTION SOLUTION CNC 8070 (REF: 1901) ·110· Pendant l'exécution. Le type de tangence n'est pas valide. Consulter dans le manuel de programmation le format correct. SPLINE : Erreur lors de l'activation. DÉTECTION CAUSE SOLUTION 2118 Pendant l'exécution. On ne peut pas activer le mode spline sans terminer un spline préalable. Désactiver le mode spline actif avant de définir un autre. #ASPLINE : paramètre non valable. DÉTECTION CAUSE SOLUTION 2116 Pendant l'exécution. Le point initial du spline coïncide avec le point antérieur et la tangente reste indéterminée ou seul un axe de la tangente a été programmé. Programmer un point de sortie après le point final du spline ou les deux axes de la tangente. SPLINE : Activation non autorisée. DÉTECTION CAUSE SOLUTION 2115 Pendant l'exécution. Le point initial du spline coïncide avec le point précédent et la tangente reste indéterminée ou bien il n’a été programmé qu’un axe de la tangente. Programmer un point préalable au point d'entrée au spline ou aux deux axes de la tangente. SPLINE : Tangente finale indéterminée. DÉTECTION CAUSE 2114 Au cours de l'exécution. La trajectoire générée par la CNC pour travailler en mode HSC arrive hors des limites de parcours actives. Désactiver le mode HSC dans le ou les blocs provoquant l’erreur. SPLINE : Tangente initiale indéterminée. DÉTECTION CAUSE 2113 Au cours de l'exécution. La trajectoire générée par la CNC pour travailler en mode HSC arrive hors des limites de parcours actives. Désactiver le mode HSC dans le ou les blocs provoquant l’erreur. 'Limite de logiciel négative dépassée dans le mode HSC' DÉTECTION CAUSE 2112 Au cours de l'exécution. L’erreur de contour programmé est trop petite pour être traitée. Programmer l'instruction avec une erreur de contour supérieure à 20 microns. 'Limite de logiciel positive dépassée dans le mode HSC' DÉTECTION CAUSE 2111 Au cours de l'exécution. On ne peut pas changer le mode HSC sans désactiver le mode précédent. Désactiver le mode HSC avant d’en programmer un autre. 'HSC: Erreur de contour trop grande' DÉTECTION CAUSE SOLUTION 2110 Pendant l'exécution. Erreur dans le calcul de la trajectoire pour travailler en mode HSC. Désactiver le mode HSC dans le ou les blocs provoquant l’erreur. Pendant l'exécution. On ne peut pas activer un mode spline sans désactiver le mode précédent. Désactiver le mode spline actif avant de définir un autre. 'SPLINE: 'Type de spline non valide' DÉTECTION CAUSE SOLUTION Au cours de l'exécution. Un type de spline interdit a été programmé. Consulter dans le manuel de programmation le format correct. S o l ut i o n s d ’ e r r e ur s . 2119 'SPLINE: Il est impossible de changer le type avec des splines activés' DÉTECTION CAUSE SOLUTION 2121 'Trajectoires circulaires interdites avec les splines actifs' DÉTECTION CAUSE SOLUTION 2122 SOLUTION SOLUTION SOLUTION SOLUTION Au cours de l'exécution. Il manque un paramètre de la trajectoire hélicoïdale ou il est incorrect. Le pas est programmé mais il manque la profondeur, il manque le pas et le point final ou bien la profondeur, le pas et le point final ne sont pas compatibles. Programmer le point final compatible avec le pas et la profondeur. Si la trajectoire hélicoïdale sont des tours entiers, programmer le pas et la profondeur. 'Erreur dans la transformation de RTCP' DÉTECTION CAUSE SOLUTION 2130 Au cours de l'exécution. La trajectoire générée par la CNC pour travailler en mode spline arrive hors des limites de parcours actives. Désactiver le mode spline dans le ou les blocs provoquant l’erreur. 'Trajectoire hélicoïdale mal programmée' DÉTECTION CAUSE 2129 Au cours de l'exécution. La trajectoire générée par la CNC pour travailler en mode spline arrive hors des limites de parcours actives. Désactiver le mode spline dans le ou les blocs provoquant l’erreur. 'Limite de logiciel négative dépassée dans le spline' DÉTECTION CAUSE 2128 Au cours de l'exécution. Il y a des points programmés. Programmer des points différents. 'Limite de logiciel positive dépassée dans le spline' DÉTECTION CAUSE 2127 Au cours de l'exécution. Le mode spline ne peut pas être activé avec un seul axe dans le canal. Configurer le canal avec deux axes ou programmer les déplacements sans mode spline. 'SPLINE: Erreur dans le calcul de la tangente' DÉTECTION CAUSE SOLUTION 2126 Au cours de l'exécution. Avec le mode spline actif, un changement de système de coordonnées ou des instructions qui arrêtent la préparation de blocs sont programmés. Désactiver le mode spline avant de changer le système de coordonnées ou programmer des instructions qui arrêtent la préparation de blocs. 'SPLINE: Il faut au moins deux axes principaux' DÉTECTION CAUSE SOLUTION 2125 Au cours de l'exécution. Un déplacement polynomial est programmé avec le mode spline actif. Désactiver le mode spline avant de programmer le polynôme. 'Programmation interdite avec les splines actifs' DÉTECTION CAUSE 2124 Au cours de l'exécution. Un déplacement circulaire est programmé avec le mode spline actif. Désactiver le mode spline avant de programmer l'arc. 'Blocs polynomiaux interdits avec les splines actifs' DÉTECTION CAUSE SOLUTION 2123 Au cours de l'exécution. Un changement de type de spline a été programmé sans annuler le spline. Désactiver le mode spline actif avant de définir un autre. Au cours de l'exécution. Une transformation RTCP a été programmée et tous les axes nécessaires ne sont pas dans le canal. Avant d’activer la transformation RTCP, configurer le canal avec les axes nécessaires. CNC 8070 (REF: 1901) 'Erreur dans la transformation de plan incliné' DÉTECTION CAUSE SOLUTION Au cours de l'exécution. Un plan incliné est programmé et il n’y a pas trois axes dans le canal. Avant d’activer le plan incliné, configurer le canal avec les axes nécessaires. ·111· S o l ut i o n s d ’ e r r e ur s . 2131 'Erreur interne en mode axe C' DÉTECTION CAUSE SOLUTION 2132 Paramètre machine PROBERANGE non programmé. DÉTECTION CAUSE SOLUTION 2133 SOLUTION 2141 ·112· 2142 Pendant l'exécution. Un paramètre de l'instruction de programmation #SLOPE est incorrect. Consulter dans le manuel de programmation le format correct. Trajectoire circulaire non autorisée sans deux axes sur le plan principal. DÉTECTION CAUSE SOLUTION (REF: 1901) Pendant l'exécution. Il n’y a pas de déplacement programmé pour l’axe de filetage. Programmer le déplacement pour l'axe de filetage. SLOPE: Paramètre non valable. DÉTECTION CAUSE SOLUTION CNC 8070 Pendant l'exécution. L'axe de filetage n'est pas dans le canal. Programmer le filetage avec les axes disponibles ou configurer les axes du canal pour pouvoir réaliser le filet. 'Mouvement nul en filetage' DÉTECTION CAUSE SOLUTION 2140 Pendant l'exécution. Sans définition de l'axe frontal. Mettre le paramètre machine FACEAXIS à TRUE pour que l'axe soit frontal. Aucun axe de filetage n'a été défini. DÉTECTION CAUSE SOLUTION 2139 Au cours de l'exécution. En vitesse de coupe constante, la vitesse de coupe n’a pas été programmée. Programmer la vitesse de coupe. FACEAXIS n'a pas été défini. DÉTECTION CAUSE SOLUTION 2138 Au cours de l'exécution. En vitesse de coupe constante, la vitesse maximale de broche n’a pas été programmée. Programmer les tours maximums de la broche. 'Une vitesse maximale de coupe nulle a été programmée' DÉTECTION CAUSE SOLUTION 2137 Pendant l'exécution. L’axe esclave du couplage n’est pas disponible dans le canal. Programmer les couplages avec les axes du canal. 'Une vitesse maximale de broche nulle a été programmée' DÉTECTION CAUSE 2136 Pendant l'exécution. L’axe maître du couplage n’est pas disponible dans le canal. programmer les couplages avec les axes du canal. L'axe esclave n'existe pas. DÉTECTION CAUSE SOLUTION 2135 Pendant l'exécution. Le paramètre PROBERANGE n'a pas été défini. Définir le paramètre PROBERANGE. L'axe maître n'existe pas. DÉTECTION CAUSE SOLUTION 2134 Pendant l'exécution. Impossible la transformation de l'axe C pour le bloc. Éliminer le bloc ou blocs provoquant l'erreur. Contacter Fagor Automation. Pendant l'exécution. Les trajectoires circulaires ne sont pas permises s’il n’y a pas au moins deux axes dans le canal. Configurer le canal avec au moins deux axes. 'Programmation interdite avec axe(s) Hirth' DÉTECTION CAUSE SOLUTION Au cours de l'exécution. Une commande incompatible avec un axe hirth a été programmée. Vérifier la programmation. S o l ut i o n s d ’ e r r e ur s . 2143 'Il est impossible de calculer la tangente au spline' DÉTECTION CAUSE SOLUTION 2144 'Erreur dans la génération du spline' DÉTECTION CAUSE SOLUTION 2145 SOLUTION SOLUTION SOLUTION Au cours de l'exécution. Il n’est pas permis d’activer le contrôle tangentiel avec le mode splines actif ni viceversa. Ne pas programmer des splines avec le contrôle tangentiel. 'Position théorique impossible dans FACE, à cause du désalignement de l'outil' DÉTECTION CAUSE SOLUTION 2153 Pendant l'exécution. La CNC introduit un bloc supplémentaire de positionnement pour l’axe tangentiel, entre deux polynômes. Contacter Fagor Automation. 'Programmation de splines et contrôle tangentiel incompatibles' DÉTECTION CAUSE 2152 Pendant l'exécution. Il n'est pas possible de réaliser le contrôle tangentiel. Éliminer le bloc provoquant l'erreur. Contacter Fagor Automation. #TANGCTRL: bloc supplémentaire entre deux polynômes. DÉTECTION CAUSE 2151 Au cours de l'exécution. Avec le mode spline actif, il y a trop de blocs de non-déplacement (assignations de paramètres P, variables, etc.) entre deux blocs de déplacement. Réduire le nombre de blocs de non déplacement programmés; par exemple, regrouper plusieurs de ces blocs en un seul. #TANGCTRL: Erreur interne dans le contrôle tangentiel. DÉTECTION CAUSE SOLUTION 2150 Au cours de l'exécution. Avec le mode HSC actif il est interdit d'activer le spline. Désactiver le mode HSC pour activer le mode spline. 'Trop de blocs sans déplacement entre deux blocs sous le mode spline' DÉTECTION CAUSE 2149 Au cours de l'exécution. Nombre insuffisant de blocs pour désactiver le spline. Pour exécuter un seul bloc ne pas programmer le spline. 'Programmation de splines interdite sous le mode HSC' DÉTECTION CAUSE SOLUTION 2148 Au cours de l'exécution. La CNC a atteint la fin du programme avec le mode spline actif. Annuler le spline avant de terminer le programme. 'Impossible la désactivation du spline' DÉTECTION CAUSE SOLUTION 2147 Au cours de l'exécution. Pour activer le spline il faut programmer le premier bloc. Programmer un déplacement avant d’activer le spline. 'Fin de programme sans désactiver les splines' DÉTECTION CAUSE SOLUTION 2146 Au cours de l'exécution. On ne peut pas calculer la tangente pour désélectionner le spline. Désélectionner le spline à un autre point ou programmer une autre tangente. Au cours de l'exécution. L’axe C ne peut pas atteindre la position à cause du désalignement de l’outil par rapport à l’axe de rotation. Changer la trajectoire d’usinage ou travailler sans désalignement d’outil. CNC 8070 'Trajectoire hélicoïdale proche du centre de rotation du FACE' DÉTECTION CAUSE SOLUTION Au cours de l'exécution. Une trajectoire hélicoïdale de plus d'un tour a été programmée dans une zone proche du centre de rotation du FACE. Modifier la trajectoire de l'usinage. (REF: 1901) ·113· S o l ut i o n s d ’ e r r e ur s . 2154 Retard du palpeur mal réglé. Paramétrer PROBEDELAY %f. DÉTECTION CAUSE SOLUTION 2300 'Solution d'orientation #CSROT non valide ou pas trouvée' DÉTECTION CAUSE SOLUTION 2301 SOLUTION SOLUTION SOLUTION CNC 8070 2308 Au cours de l'exécution. La CNC a essayé d’activer un axe Hirth alors qu’il faisait partie de la transformation de l’axe virtuel de l’outil, #VIRTAX. Désactiver d’abord la transformation de l’axe virtuel de l’outil #VIRTAX puis activer l’axe comme un axe Hirth. La transformation de l'axe virtuel de l'outil a été désactivée, #VIRTAX. DÉTECTION CAUSE SOLUTION ·114· Pendant l'exécution. La CNC a essayé d'activer le PWM, mais il n'a aucune sortie numérique locale attribuée. Définir dans les paramètres des machines la sortie numérique locale associée au PWM (paramètre PWMOUTPUT). 'On ne peut pas activer l'axe comme Hirth, car il fait partie de la transformation #VIRTAX'. DÉTECTION CAUSE SOLUTION (REF: 1901) Pendant l'exécution. Certaines commandes de l'instruction #PWMOUT ont une valeur erronée. Réviser la programmation. Le paramètre machine PWMOUTPUT est 0. DÉTECTION CAUSE 2307 Pendant l'exécution. La syntaxe de l'instruction n’est pas correcte ou il y a plus d’information dans le bloc. Réviser la programmation. Paramètre PWM hors plage. DÉTECTION CAUSE SOLUTION 2306 Au cours de l'exécution. Le type de cinématique n'est pas compatible avec la fonction #CSROT. Désactiver la fonction #CSROT. Programmer #PWMOUT ON<[FREQ/F valeur, DUTY/D valeur]>/OFF. DÉTECTION CAUSE SOLUTION 2305 Au cours de l'exécution. L’orientation des axes rotatifs de la cinématique dans le système de référence machine requiert un déplacement par rapport à la valeur programmée supérieure à l’angle défini #DEFROT. Augmenter la valeur de l'angle défini dans #DEFROT. 'La fonction CSROT n’est applicable qu’aux cinématiques à deux axes type broche, table ou broche-table' DÉTECTION CAUSE SOLUTION 2304 Au cours de l'exécution. Les axes rotatifs de la cinématique n’ont pas pu être orientés sur la position programmée dans le système de référence machine, suivant le critère sélectionné dans #DEFROT. Désactiver la fonction #CSROT ou changer d'orientation. 'Solution d'orientation #CSROT discontinue suivant la programmation. Rotatif principal / Rotatif secondaire' DÉTECTION CAUSE 2303 Au cours de l'exécution. Les axes rotatifs de la cinématique n’ont pas pu être orientés sur la position programmée, dans le système de référence machine. Désactiver la fonction #CSROT ou changer d'orientation. 'La solution d'orientation #CSROT n'est pas trouvée suivant le critère défini dans #DEFROT' DÉTECTION CAUSE 2302 Pendant l'exécution. Le paramètre PROBEDELAY à une valeur erroné. Définir le paramètre PROBEDELAY avec la valeur indiquée dans le message. On peut également utiliser le cycle de calibrage du palpeur (#PROBE 2) pour calculer la valeur adéquate. Pendant l'exécution. Il y a eu un changement dans la situation des axes qui font partie de la transformation de l’axe virtuel de l’outil(#VIRTAX). Réviser la programmation. S o l ut i o n s d ’ e r r e ur s . 2309 #VIRTAX: Programmation interdite avec l'axe virtuel de l'outil actif. DÉTECTION CAUSE SOLUTION 2310 #VIRTAX: L'axe virtuel de l'outil doit être linéaire et appartenir au canal. DÉTECTION CAUSE SOLUTION 2311 SOLUTION SOLUTION SOLUTION Au cours de l'exécution. Le profil ProGTL3 programmé finit sans être résolu complètement. Réviser la programmation. 'On n’admet pas d’autres points dans la fonction G809-G820' DÉTECTION. CAUSE SOLUTION 2318 Au cours de l'exécution. Le profil ProGTL3 programmé est incorrect ou il n'a pas de solution. Réviser la programmation. 'La terminaison du profil PROGTL3 n'est pas résolue' DÉTECTION. CAUSE SOLUTION 2317 Pendant l'exécution. La fonction programmée n'est pas permise dans la définition d'un profil ProGTL3. Supprimer cette fonction, la remplacer par une fonction équivalente autorisée ou terminer la définition du profil. 'Erreur pendant le processus de résolution du profil PROGTL' DÉTECTION. CAUSE SOLUTION 2316 Pendant l'exécution. Les fonctions G810, G811, G813, G820, G821, G840, G841, G842, G850 et G841 ne sont permises que dans la définition d'un profil ProGTL3. Programmer la fonction G après le début du profil avec G841 ou G842. Programmation interdite dans un profil PROGTL3. DÉTECTION CAUSE SOLUTION 2315 Au cours de l'exécution. La CNC a essayé d’activer une cinématique qui n'est pas définie dans la table de cinématiques des paramètres machine. Vérifier la programmation. Programmation interdite hors d'un profil PROGTL3 ou MACRO. DÉTECTION CAUSE 2314 Pendant l'exécution. La CNC a essayé d’activer la transformation de l’axe virtuel de l’outil (#VIRTAX) avec un axe faisant partie du trièdre principal ou d’une cinématique. Réviser la programmation. '#KIN ID[]: Programmer des valeurs comprises entre 0 et le paramètre machine NKIN' DÉTECTION CAUSE 2313 Pendant l'exécution. La CNC a essayé d’activer la transformation de l’axe virtuel de l’outil (#VIRTAX) avec un axe rotatif ou bien avec un axe qui n'appartient pas au canal. Réviser la programmation. #VIRTAX: L'axe virtuel de l'outil ne peut pas être un axe primaire ni faire partie d'une cinématique. DÉTECTION CAUSE 2312 Pendant l'exécution. La CNC a essayé d’exécuter une des fonctions suivantes alors que la transformation de l’axe virtuel de l’outil était active. • Recherche de zéro; G74. • Modifier les limites de logiciel; G198 - G199. • Instruction #OSC. Désactiver d’abord la transformation de l’axe virtuel de l’outil (#VIRTAX) puis exécuter les fonctions #OSC, G74 ou G198-G199 et finalement activer de nouveau la transformation #VIRTAX. Au cours de l'exécution. Dans les fonctions G809 ou G820 il y a plus de points que ceux permis. Réviser la programmation. CNC 8070 'L'entité géométrique n'est pas définie' DÉTECTION. CAUSE SOLUTION Au cours de l'exécution. L'entité programmée n'est pas définie ou initialisé. Avant d'utiliser cette entité, elle doit être définie auparavant. (REF: 1901) ·115· S o l ut i o n s d ’ e r r e ur s . 2319 'On n’admet pas d’autres éléments dans la définition de l'entité géométrique' DÉTECTION. CAUSE SOLUTION 2320 'L'élément n'est pas tangent' DÉTECTION. CAUSE SOLUTION 2321 CNC 8070 (REF: 1901) ·116· Au cours de l'exécution. G808 a été programmée et aucun élément précédent a été programmé. Réviser la programmation. Programmer l'élément précédent. 'G808 point précédent sans définir' DÉTECTION. CAUSE SOLUTION 2330 Au cours de l'exécution. L'élément précédent à G802/G803 doit être un cercle. Réviser la programmation. 'G808 sans élément précédent' DÉTECTION. CAUSE SOLUTION 2329 Au cours de l'exécution. Le point final n'appartient pas au cercle. Réviser la programmation. 'G802/G803 XY l'élément précédent doit être un cercle' DÉTECTION. CAUSE SOLUTION 2328 Au cours de l'exécution. Le point final n'appartient pas au cercle. Réviser la programmation. 'Il manque le point final dans G802/G803' DÉTECTION. CAUSE SOLUTION 2327 Au cours de l'exécution. Le point initial n'appartient pas au cercle. Réviser la programmation. 'Le point final n'appartient pas au cercle' DÉTECTION. CAUSE SOLUTION 2326 Au cours de l'exécution. L'arc programmé n'est pas possible avec les donnés fournies. Réviser la programmation. 'Le point initial n'appartient pas au cercle' DÉTECTION. CAUSE SOLUTION 2325 Pendant l'exécution. L'élément indiqué est mal programmé. Réviser la programmation. 'L'arc n'est pas possible' DÉTECTION. CAUSE SOLUTION 2324 Au cours de l'exécution. L'élément programmé ne peut pas être tangent au précédent. Réviser la programmation. 'L'élément n'est pas valide' DÉTECTION CAUSE SOLUTION 2323 Au cours de l'exécution. L'élément indiqué n'est pas tangent au précédent. Réviser la programmation. 'La tangence n'est pas possible' DÉTECTION. CAUSE SOLUTION 2322 Au cours de l'exécution. Le nombre maximum d’éléments admis pour définir une entité géométrique a été dépassé. Modifier l'entité ou bien utiliser plusieurs. Au cours de l'exécution. G808 a été programmée et aucun point précédent a été programmé. Réviser la programmation. Programmer l'élément précédent. 'G809 point précédent sans définir' DÉTECTION. CAUSE SOLUTION Au cours de l'exécution. G809 a été programmée et aucun point précédent a été programmé. Réviser la programmation. Programmer l'élément précédent. S o l ut i o n s d ’ e r r e ur s . 2331 'Il manque des données pour définir correctement l'entité' DÉTECTION. CAUSE SOLUTION 2332 'L'entité n'est pas valide' DÉTECTION. CAUSE SOLUTION 2333 SOLUTION SOLUTION Au cours de l'exécution. La CNC a essayé d’activer la compensation de rayon (G41/G42) alors que la compensation d’outil 3D (#COMP3D ON) est active ou vice versa. Réviser la programmation. Les deux types de compensation sont incompatibles. 'Vecteur défini doublement' DÉTECTION. CAUSE SOLUTION 2341 Au cours de l'exécution. On ne peut programmer H que dans les blocs du profil plan défini dans G8736 ou comme paramètre de G8737. Réviser la programmation. Ne pas programmer H dans d'autres blocs. 'La compensation active de rayon n'est pas compatible avec 3D' DÉTECTION. CAUSE 2340 Au cours de l'exécution. Le profil de la macro est écrit en deux langages, ProGTL3 et ISO. Les profils des macros peuvent être définis en langage ProGTL3 ou ISO, mais il n’est pas permis de mélanger les deux dans un même profil. Programmer le profil pour la macro dans un seul langage ProGTL3 ou ISO. 'Il n'est pas permis de programmer la section H' DÉTECTION. CAUSE 2339 Au cours de l'exécution. Une des fonctions G8727 ou G8728 a été programmée hors d'une macro G8726. Réviser la programmation. Les fonctions G8727 ou G8728 doivent être programmées après la macro G8726. 'Programmation PROGTL3 interdite dans un profil ISO' DÉTECTION. CAUSE SOLUTION 2338 Au cours de l'exécution. Une fonction G8724 a été programmée hors d'une macro G8725. Réviser la programmation. La fonction G8724 doit être programmée après la macro G8725. 'Programmation interdite hors d'une macro G8726' DÉTECTION. CAUSE SOLUTION 2337 Au cours de l'exécution. Une fonction G8734 a été programmée hors d'une macro G8735. Réviser la programmation. La fonction G8734 doit être programmée après la macro G8735. 'Programmation interdite hors d'une macro G8725' DÉTECTION. CAUSE SOLUTION 2336 Au cours de l'exécution. Une des fonctions G8737 ou G8738 a été programmée hors d'une macro G8736. Réviser la programmation. Les fonctions G8737 ou G8738 doivent être programmées après la macro G8736. 'Programmation interdite hors d'une macro G8735' DÉTECTION. CAUSE SOLUTION 2335 Au cours de l'exécution. L'entité programmée n'est pas valide. Réviser la programmation. 'Programmation interdite hors d'une macro G8736' DÉTECTION. CAUSE SOLUTION 2334 Au cours de l'exécution. Il manque des données pour la programmation de l'entité. Réviser la programmation. Au cours de l'exécution. Compensation d'outil 3D. Il y a deux vecteurs N[a,b,c] programmés dans le même bloc. Réviser la programmation. Programmer un seul vecteur par bloc. 'Programmation incorrecte du vecteur' DÉTECTION. CAUSE SOLUTION CNC 8070 (REF: 1901) Au cours de l'exécution. Compensation d'outil 3D. Le vecteur N[a,b,c] est incorrect. Réviser la programmation. Programmer les trois composants du vecteur. ·117· S o l ut i o n s d ’ e r r e ur s . 2342 'Il est nécessaire de programmer le vecteur N[-,-,-] pour la compensation 3D' DÉTECTION. CAUSE SOLUTION 2343 'Outil actif inadéquat pour la compensation 3D' DÉTECTION. CAUSE SOLUTION 2344 SOLUTION SOLUTION SOLUTION SOLUTION SOLUTION 2351 ·118· Pendant l'exécution. La CNC a détecte la fin du programme alors que la macro définie n’est pas encore terminée. Réviser la programmation. Achever correctement la définition des macros. 'Le profil n’a pas été programmé' DÉTECTION. CAUSE SOLUTION 2352 (REF: 1901) Au cours de l'exécution. Un nouveau profil a commencé à être défini alors que le précédent n’est pas encore terminé. Réviser la programmation. Achever correctement la définition des profils. On attend la fin de la macro: G8738/G8734/G8728/G8724 DÉTECTION CAUSE CNC 8070 Pendant l'exécution. Une nouvelle macro a commencé à être définie alors que la précédente n’est pas encore terminée. Réviser la programmation. Achever correctement la définition des macros. 'Commencement du profil G841/G842 défini doublement' DÉTECTION. CAUSE 2350 Au cours de l'exécution. Il n'est pas permis d'initier un profil avec G91 active, ni de programmer G91 dans un profil G841-G842. Programmer G90 avant du commencement du profil. Pour programmer des cotes incrémentales dans des profils, utiliser la programmation prévue pour cela. 'Macro G8735/G8736/G8725/G8726 définie doublement' DÉTECTION CAUSE 2349 Au cours de l'exécution. La mémoire réservée pour l'affichage 2D du programme est insuffisante dans ce programme ou le nombre maximum de blocs (500) a été dépassé. Modifier le programme ou l'afficher par sections. 'Le profil PROGTL3 avec G91 active n'est pas permis' DÉTECTION. CAUSE 2348 Au cours de l'exécution. Il y a plus d’un profil plan ou plus d’un profil dans une section. Réviser la programmation. Définir un seul profil. 'Le nombre maximum de blocs pour l'affichage 2D est dépasse' DÉTECTION. CAUSE 2347 Au cours de l'exécution. La syntaxe de l'instruction n'est pas correcte. Réviser la programmation. 'Profil défini doublement' DÉTECTION. CAUSE SOLUTION 2346 Au cours de l'exécution. L'outil n'est pas plan, torique ou sphérique. La compensation d’outil 3D en mode "NORMAL" n’admet que des outils de fraisage plans, toriques ou sphériques. 'Programmer #COMP3D ON/OFF [PARAX/NORMAL]' DÉTECTION. CAUSE SOLUTION 2345 Au cours de l'exécution. Avec la compensation de l'outil 3D actif, il manque le vecteur N[a,b,c] dans un bloc. Réviser la programmation. Avec la compensation d’outil 3D actif, il faut obligatoirement programmer un vecteur dans chaque bloc de déplacement. Au cours de l'exécution. Il manque programmer un profil dans la macro ProGTL3. Pour exécuter correctement la macro, il faut définir tous les profils. 'Entité non initialisée' DÉTECTION. CAUSE SOLUTION Au cours de l'exécution. Le programme a essayé d'utiliser une entité non initialisée. Avant d'utiliser cette entité, elle doit être initialisée auparavant. S o l ut i o n s d ’ e r r e ur s . 2353 Programmer #LSFIT [type, pLocal <,data1, data2, data3> ] DÉTECTION CAUSE SOLUTION 2354 #LSFIT, paramètre local non valable. DÉTECTION CAUSE SOLUTION 2355 SOLUTION Au cours de l'exécution. Dans DGWZ CYL, il faut obligatoirement programmer un axe de rotation et cela n'a pas été fait. Programmer axe de rotation pour DGWZ CYL. G8/G9: Programmation incorrecte du point final de l'arc DÉTECTION CAUSE SOLUTION 2364 Au cours de l'exécution. L'axe de rotation a été programmé dans DGWZ ou DGWZ RECT. Il est uniquement possible de programme un axe de rotation dans DGWZ CYL. Supprimer l'axe de rotation de la programmation de DGWZ ou DGWZ RECT. #DGWZ CYL: Axe de rotation non programmé. DÉTECTION CAUSE 2363 Au cours de l'exécution. Il y a un axe programmé dans la fonction ou instruction. Réviser la programmation. #DGWZ <RECT>: L'axe de rotation ne peut pas être programmé. DÉTECTION CAUSE SOLUTION 2362 Au cours de l'exécution. L'axe programmé dans l'instruction #DGWZ n'appartient pas au plan ou trièdre. Sélectionner comme axe longitudinal un axe du plan ou du trièdre. 'La fonction ou instruction ne permet pas la programmation d'axes' DÉTECTION CAUSE SOLUTION 2361 Au cours de l'exécution. L'axe programmé dans l'instruction #DGWZ n'est pas linéaire. Sélectionner comme axe longitudinal un axe linéaire. '#DGWZ CYL: L'axe programmé doit appartenir au plan ou trièdre' DÉTECTION CAUSE SOLUTION 2360 Au cours de l'exécution. Les deux axes rotatifs sélectionnés coïncident ou sont incorrects. Réviser la programmation. Les valeurs possibles pour sélectionner les axes rotatifs sont HEAD1, HEAD2, TABLE1, TABLE2. '#DGWZ CYL: L'axe programmé doit être un axe linéaire' DÉTECTION CAUSE SOLUTION 2359 Au cours de l'exécution. La syntaxe de l'instruction n'est pas correcte. Réviser la programmation. 'Axes rotatifs sélectionnés égaux ou incorrects' DÉTECTION. CAUSE SOLUTION 2358 Au cours de l'exécution. Erreur interne générique du processus #LSFIT. Réviser la programmation. 'Programmer #SELECT ORI [HEAD1-2/TABLE1-2, HEAD1-2/TABLE1-2]' DÉTECTION. CAUSE SOLUTION 2357 Pendant l'exécution. Le paramètre TYPE de l'instruction #LSFIT n'est pas valide. Réviser la programmation. 'Erreur dans le processus #LSFIT' DÉTECTION. CAUSE SOLUTION 2356 Pendant l'exécution. La syntaxe de l'instruction n'est pas correcte. Réviser la programmation. Au cours de l'exécution. Dans les fonctions G8 et G9, il faut obligatoirement programmer le point final de l'arc. Programmer le point final de l'arc. Point final du mouvement existant. DÉTECTION CAUSE SOLUTION CNC 8070 Au cours de l'exécution. La cote programmée au moyen d'une coordonnée cartésienne et un angle est erronée. La trajectoire qui part du point antérieur ne peut pas atteindre le point programmé. Programmer correctement le point final de mouvement. (REF: 1901) ·119· S o l ut i o n s d ’ e r r e ur s . 2365 G34: Double programmation de l'augmentation/réduction du pas de vis. DÉTECTION CAUSE SOLUTION 2366 G34: Augmentation/réduction du pas de vis égale à zéro. DÉTECTION CAUSE SOLUTION 2367 SOLUTION SOLUTION SOLUTION 2375 ·120· 2376 Au cours de l'exécution. Erreur dans le cycle de calibrage de cinématique. Contacter Fagor. #LSFIT, erreur de calcul (SVD), vérifier les données d'entrée. DÉTECTION CAUSE SOLUTION (REF: 1901) Au cours de l'exécution. Erreur dans le cycle de calibrage de cinématique. Contacter Fagor. #LSFIT, erreur de calcul (rayon=0), vérifier les données d'entrée. DÉTECTION CAUSE SOLUTION CNC 8070 Au cours de l'exécution. Erreur dans le cycle de calibrage de cinématique. Contacter Fagor. #LSFIT, nombre de données insuffisant. DÉTECTION CAUSE SOLUTION 2374 Au cours de l'exécution. Erreur dans le cycle de calibrage de cinématique. Contacter Fagor. #LSFIT, nombre maximum de données dépassé. DÉTECTION CAUSE SOLUTION 2373 Au cours de l'exécution. L'axe de filetage est défini par la lettre avec laquelle le pas de vis est programmé dans le bloc. L'axe programmé n'existe pas. Programmer le pas de vis selon un axe valable. #LSFIT, l'algorithme ne converge pas, vérifier les données d'entrée. DÉTECTION CAUSE SOLUTION 2372 Au cours de l'exécution. Avec le pas de vis et la réduction du pas de vis programmées en G34, le pas de vis final calculé par la commande est négatif ou égal à zéro. Programmer correctement le pas et la réduction du pas de vis en G34 Axe pour fileter inexistant. DÉTECTION CAUSE 2371 Au cours de l'exécution. L'augmentation du pas de vis programmée est plus de deux fois supérieure au pas de vis. Programmer une valeur correct de l'augmentation du pas de vis (K1). G34: Pas de vis final négatif ou nul. DÉTECTION CAUSE 2370 Au cours de l'exécution. La valeur de l'augmentation/réduction du pas de vis en G34 est erronée. Programmer une valeur correcte de l'augmentation/réduction du pas de vis (K1). G34: Augmentation/réduction du pas de vis trop importante. DÉTECTION CAUSE 2369 Au cours de l'exécution. L'augmentation/réduction du pas de vis (K1) pour G34 est zéro. Programmer une augmentation/réduction du pas de vis (K1) pour G34. G34: Augmentation/réduction du pas de vis hors plage. DÉTECTION CAUSE SOLUTION 2368 Au cours de l'exécution. L'augmentation/réduction du pas de vis (K1) a été programmée plus d'une fois Programmer l'augmentation/réduction du pas de vis une seul fois en blic. Au cours de l'exécution. Erreur dans le cycle de calibrage de cinématique. Contacter Fagor. #LSFIT, erreur de calcul (SVBK), vérifier les données d'entrée. DÉTECTION CAUSE SOLUTION Au cours de l'exécution. Erreur dans le cycle de calibrage de cinématique. Contacter Fagor. S o l ut i o n s d ’ e r r e ur s . 2377 #LSFIT, l'instruction n'est pas valable. DÉTECTION CAUSE SOLUTION 2378 #GAPCTRL: Il reste à programme l'axe ou le GAP. DÉTECTION CAUSE SOLUTION 2379 SOLUTION SOLUTION Pendant la préparation des blocs. Le numéro de zone n'a pas été programmé dans G120/G121/G122/G123. Programmer le numéro de zone dans le paramètre « K », de 1 à 5. Zone de travail inexistante. DÉTECTION CAUSE SOLUTION 2387 Au cours de l'exécution. Le dossier de destination n'existe pas ou le nom du fichier est erroné. Sélectionner un dossier qui existe et un nom de fichier correct. Zone de travail non programmée. DÉTECTION CAUSE SOLUTION 2386 Pendant l’édition et l’exécution. La syntaxe de l'instruction n'est pas correcte. Vérifier dans le manuel de programmation la syntaxe de l'instruction. #ISO ON[]. Nom de fichier non valable. DÉTECTION CAUSE SOLUTION 2385 Au cours de l'exécution. La commande #ABORT OFF n'a pas été programmée. Si l'on programme la commande #ABORT uniquement dans le bloc, en annulant le programme, l'exécution continue dans la commande #ABORT OFF. Programmer #ABORT OFF. #ISO ON[]. Syntaxe erronée. DÉTECTION CAUSE SOLUTION 2383 Au cours de l'exécution. Erreur dans le cycle de calibrage de cinématique. Contacter Fagor. #ABORT OFF n'est pas programmé dans la même sous-routine que #ABORT. DÉTECTION CAUSE 2382 Au cours de l'exécution. L'entrée analogique à laquelle le capteur du gap (paramètre GAPANAINID) est attribuée n'a pas été définie. Attribuer la valeur correcte au paramètre machine GAPANAINID. #LSFIT, erreur interne. DÉTECTION CAUSE SOLUTION 2381 Au cours de l'exécution. Dans la commande #GAPCTRL l'axe ou la distance n'ont pas été programmés (gap). Programmer l'axe et/ou le GAP. #GAPCTRL: Paramètre machine GAPANAINID nul ou non attribué. DÉTECTION CAUSE 2380 Au cours de l'exécution. Erreur dans le cycle de calibrage de cinématique. Contacter Fagor. Pendant la préparation des blocs. Le numéro de zone programmée dans G120/G121/G122/G123 ne possède pas une valeur adéquate. Programmer le numéro de zone dans le paramètre « K », de 1 à 5. Surveillance de l'outil non valable dans la zone de travail. DÉTECTION CAUSE SOLUTION Pendant la préparation des blocs. La surveillance de l'outil dans la zone de travail ne possède pas une valeur adéquate. Deux possibilités existent. • La valeur programmée dans G122 est erronée. • La valeur récupérée après un processus de récupération des données (démarrage, réinitialisation, inspection) es erronée. Programmer une valeur adéquate pour la surveillance de l'outil, de 0 à 2. • Dans le premier cas, programmer une valeur adéquate dans le paramètre « I » de la fonction G122. • Dans le second cas, écrire depuis le PLC la valeur adéquate dans la variable "G.ZONETOOLWATCH[zone]". CNC 8070 (REF: 1901) ·121· S o l ut i o n s d ’ e r r e ur s . 2388 État de la zone de travail non valable. DÉTECTION CAUSE SOLUTION 2389 'Le rayon ne peut être programmé qu'avec R' DÉTECTION CAUSE SOLUTION 2390 SOLUTION SOLUTION CNC 8070 (REF: 1901) ·122· Pendant la préparation des blocs. L’état de la zone de travail dans G122 n'a pas été programmé. Programmer l'état de la zone de travail dans le paramètre « E », de 0 à 2. 'Il est interdit de programmer le centre avec des axes rotatifs de type module' DÉTECTION CAUSE SOLUTION 2396 Au cours de la préparation des blocs. Le paramètre "E" est programmé plus d’une fois dans le bloc. Programmer le paramètre "E" une seule fois dans le bloc. État de la zone de travail non programmé. DÉTECTION CAUSE SOLUTION 2395 Au cours de la préparation des blocs. La CNC a essayé d’activer une zone de travail où la limite inférieure sur un axe est supérieure à la limite supérieure. Dans une zone linéaire, la limite inférieure de l'axe doit être inférieure à la limite supérieure. Modifier la limite inférieure (G120) ou supérieure (G121) de l'axe. La vérification ne s’effectue pas si la zone est désactivée. 'Fonction E programmée en double' DÉTECTION CAUSE SOLUTION 2394 Au cours de la préparation des blocs. Dans la fonction G123 le centre de la zone circulaire n'a pas été programmé correctement. Le centre de la zone circulaire G123 doit être défini avec deux axes du canal. La fonction G123 n’admet que deux axes, qui doivent être différents et appartenir au canal où la zone s’active. 'Zone linaire: La limite inférieure doit être plus petite que la limite supérieure sur chaque axe' DÉTECTION CAUSE 2393 Au cours de la préparation des blocs. Le rayon n'a pas été programmé. Programmer le rayon. 'Zone circulaire: Il est obligatoire de programmer le centre avec deux axes du canal' DÉTECTION CAUSE 2392 Au cours de la préparation des blocs. L'instruction programmée permet uniquement la programmation du rayon "R"; Elle n'admet pas "R1" et G263. Programmer le rayon avec "R". 'Il manque la programmation du rayon' DÉTECTION CAUSE SOLUTION 2391 Pendant la préparation des blocs. L'état de la zone de travail ne possède pas une valeur adéquate. Deux possibilités existent. • La valeur programmée dans G122 est erronée. • La valeur récupérée après un processus de récupération des données (démarrage, réinitialisation, inspection) es erronée. Programmer une valeur adéquate pour l'état de la zone, de 0 à 2. • Dans le premier cas, programmer une valeur adéquate dans le paramètre « E » de la fonction G122. • Dans le second cas, écrire depuis le PLC la valeur adéquate dans la variable "G.ZONEST[zone]". Pendant la préparation des blocs. Il est interdit de programmer le centre avec des axes rotatifs de type module. Il est interdit de définir le centre avec des axes rotatifs de type module. Réviser la programmation. #GAPCTRL programmé dans un autre canal. DÉTECTION CAUSE SOLUTION Pendant l'exécution. On a tenté d'activer le contrôle du gap dans un canal, alors qu'il est actif dans un autre. Un seul contrôle de gap peut être actif dans la CNC. S o l ut i o n s d ’ e r r e ur s . 2397 #GAPCTRL ON actif. #GAPCTRL OFF nécessaire pour modifier les paramètres. DÉTECTION CAUSE SOLUTION 2398 #LEAP/#LEAPBEGIN : programmation de POSLIMIT manquante. DÉTECTION CAUSE SOLUTION 2399 SOLUTION SOLUTION Pendant la préparation des blocs. La CNC a essayé d'activer une zone de travail, mais l'un des axes qui la définissent est stationné. Supprimer le stationnement de l'axe avant d'activer la zone de travail. #GAPCTRL: L'indice dans le canal de l'axe contrôlé a été altéré. DÉTECTION CAUSE SOLUTION 2405 Pendant la préparation des blocs. La CNC a essayé de stationner un axe qui fait partie d’une zone de travail active. Désactiver la zone de travail avant de stationner l'axe. 'Il est interdit d'activer une zone si l'un de ses axes est stationné' DÉTECTION CAUSE 2404 Pendant la préparation des blocs. La CNC a essayé de supprimer de la configuration un axe qui fait partie d’une de travail active. Désactiver la zone de travail avant de libérer l'axe. '#PARK: Il est interdit de stationner un axe qui définit une zone de travail active' DÉTECTION CAUSE SOLUTION 2403 Au cours de l'exécution. Le numéro logique programmé n'est pas correct. Programmer un axe correct; de 1 à NAXIS. '#FREE/SET AX: Il est interdit de libérer un axe qui définit une zone de travail active' DÉTECTION CAUSE 2402 Pendant l'exécution. On a essayé de modifier les paramètres de #LEAP alors qu'il était actif. Désactiver #LEAP avant de modifier ses paramètres. 'Numéro logique d'axe hors de gamme' DÉTECTION CAUSE SOLUTION 2401 Pendant l'exécution. Dans les commandes #LEAP ou #LEAPBEGIN la commande POSLIMIT n'est pas programmée. La première fois que #LEAP ou #LEAPBEGIN sont programmées, il faut impérativement programmer la commande POSLIMIT. #LEAP active. #LEAPEND nécessaire pour modifier des paramètres. DÉTECTION CAUSE SOLUTION 2400 Pendant l'exécution. On a essayé de modifier les paramètres de #GAPCTRL alors qu'il était actif. Désactiver #GAPCTRL avant de modifier ses paramètres. Pendant la préparation des blocs. Les possibles causes sont les suivantes: • Avec le contrôle du gap actif (#GAPCTRL ON), une instruction qui altère l'axe en question dans le canal a été programmée (#SET AX, #CALL AX, #FREE AX). • Si la valeur du paramètre machine GAPCTRLCANCEL est « NON », l'axe continue à être contrôlé après la fin du programme ou une réinitialisation. Si dans ces conditions, l'indice de l'axe est altéré, une erreur se produit également. Il est impossible de modifier la position de l'axe dans le canal avec le contrôle de gap actif. Bloc de mouvement annulé en raison d'un axe avec #GAPCTRL. DÉTECTION CAUSE SOLUTION Pendant l'inspection de l'outil ou en mode MDI. Tentative de déplacer en MDI un axe qui est contrôlé au moyen de la commande #GAPCTRL. Programmer #GAPCTRL OFF. CNC 8070 (REF: 1901) ·123· S o l ut i o n s d ’ e r r e ur s . 2406 #LEAP avec #GAPCTRL ON: Le saut doit commencer et finir à la même cote. DÉTECTION CAUSE SOLUTION 2407 #LEAP avec #GAPCTRL ON: POSLIMIT inférieur à cote initiale du saut. DÉTECTION CAUSE SOLUTION 2408 SOLUTION SOLUTION CNC 8070 (REF: 1901) ·124· Pendant l’édition et l’exécution. La syntaxe de l'instruction n'est pas correcte. Vérifier dans le manuel de programmation la syntaxe de l'instruction. Pendant l’édition et l’exécution. La syntaxe de l'instruction n'est pas correcte. Vérifier dans le manuel de programmation la syntaxe de l'instruction. Pendant l’édition et l’exécution. L'une des commandes de l'instruction #PERCTRL possède une valeur non valable. Vérifier dans le manuel de programmation la syntaxe de l'instruction. Il est obligatoire de programmer DUTY/OUT. DÉTECTION CAUSE SOLUTION 2414 <,OVRMAXvalue> Paramètre PWRCTRL hors plage. DÉTECTION CAUSE SOLUTION 2413 <,OVRMINvalue> #PWRCTRL OFF<[DUTY/D/OUT/O]> DÉTECTION CAUSE SOLUTION 2412 Pendant la préparation des blocs. Le nom d'axe esclave dans #FOLLOW ON [MASTER, axe esclave] correspond au paramètre machine LASERFOLLOWAXIS. Ne pas programmer l'axe esclave de #FOLLOW [MASTER]. #PWRCTRL ON/OFF [<DUTY/D/OUT/O> <,FMINvalue> <,FMAXvalue>] DÉTECTION CAUSE SOLUTION 2411 Pendant la préparation des blocs. Les commandes #LEAP, #GAPCTRL ON et #SWTOUT ON ne peuvent pas être actives simultanément. Désactiver l'une des deux autres commandes actives. Il est impossible de programmer l'axe esclave 'LASER FOLLOW AXIS'. DÉTECTION CAUSE 2410 Pendant la préparation des blocs. Il existe un axe contrôlé à travers l'instruction #GAPCTRL ON. Dans cette situation, l'instruction #LEAP a été programmée avec POSLIMIT (valeur maximale du saut) inférieure aux cotes initiale et finale du saut. Les possibles solutions sont les suivantes: • Programmer POSLIMIT dans la commande#LEAP avec une cote supérieure à la position initiale du saut. • Annuler le contrôle du gap (#GAPCTRL OFF). #LEAP, #GAPCTRL ON #SWTOUT ON: Les trois commandes ne peuvent être activées. DÉTECTION CAUSE 2409 Pendant la préparation des blocs. Il existe un axe contrôlé à travers l'instruction #GAPCTRL ON. Dans cette situation, l'instruction #LEAP a été programmée pour exécuter un saut dont les cotes initiale et finale (paramètre POS de l'instruction #LEAP) ne correspondent pas. Les possibles solutions sont les suivantes: • Ne pas programmer POS dans la commande #LEAP • Annuler le contrôle du gap (#GAPCTRL OFF). Pendant l’édition et l’exécution. Il reste à programmer la commande DUTY/OUT dans la fonction #PWRCTRL. Vérifier dans le manuel de programmation la syntaxe de l'instruction. Pour activer le contrôle de puissance (#PWRCTRL), il est obligatoire de programme l'une des commandes DUTY ou OUT. PWCTRL DUTY n'est pas autorisé en l'absence de l'option logicielle PWM . DÉTECTION CAUSE SOLUTION Au cours de l'exécution. Pour activer le contrôle du duty del PWM, il faut disposer de l'option logicielle PWM. Activer le contrôle de puissance (commande OUT) pour l'acquisition de l'option logicielle correspondante. S o l ut i o n s d ’ e r r e ur s . 2415 PWCTRL OUT non autorisé sans broche maître dans le canal. DÉTECTION CAUSE SOLUTION 2416 #PWRCTRL ON [<DUTY/D/OUT/O> <,OVRMINvalue> <,OVRMAXvalue> <,FMINvalue> <,FMAXvalue>] DÉTECTION CAUSE SOLUTION 2417 SOLUTION SOLUTION SOLUTION SOLUTION Au cours de l'exécution. Il est interdit de changer ou de stationner la broche master avec PWRCTRL actif. Le contrôle de puissance s'applique à la broche maître. Pour changer ou stationner la broche maître, désactiver le contrôle de puissance (#PWRCTRL). #TFOLLOW ON [MASTER] n'est pas autorisée. Autorisé: #FOLLOW ON [MASTER] DÉTECTION CAUSE SOLUTION 2423 Pendant l'exécution. Deux possibilités existent. • Le nom d'axe esclave dans #FOLLOW ON [MASTER, axe esclave] correspond au paramètre machine LASERFOLLOWAXIS. • L'axe esclave de la synchronisation est déjà esclave dans une autre synchronisation. Ne pas programmer #FOLLOW ON avec l'axe esclave qui apparaît dans le message d'erreur ou effectuer au préalable un #FOLLOW OFF de l'axe en question. Un axe ne peut pas être esclave dans deux synchronisations. Il est interdit de changer ou de stationner la broche master avec PWRCTRL actif. DÉTECTION CAUSE SOLUTION 2422 Au cours de l'exécution. La fonction #PWRCTRL est programmée pour la première fois et il manque un paramètre. La première fois que la fonction #PWRCTRL est paramétrée, il faut impérativement programmer tous les paramètres. #FOLLOW ON[MASTER, ]. L'axe esclave ne peut pas être esclave d'un autre maître. DÉTECTION CAUSE 2421 Au cours de l'exécution. Dans la fonction #PWRCTRL, l'override minimale est supérieure à l'override maximale. L'override minimale (OVRMIN) doit être inférieure à l'override maximale (OVRMAX). #PWRCTRL ON: la première fois, il faut impérativement programmer tous les paramètres. DÉTECTION CAUSE 2420 Au cours de l'exécution. Dans la fonction #PWRCTRL, l'avancée minimale est supérieure à l'avancée maximale. L'avancée minimale (FZMIN) doit être inférieure à l'avancée maximale (FZMAX). #PWRCTRL ON: OVRMIN doit être inférieur à OVRMAX. DÉTECTION CAUSE 2419 Pendant l’édition et l’exécution. La syntaxe de l'instruction n'est pas correcte. Vérifier dans le manuel de programmation la syntaxe de l'instruction. #PWRCTRL ON: FMIN doit être inférieur à FMAX. DÉTECTION CAUSE 2418 Au cours de l'exécution. Le contrôle de puissance s'applique à la broche maître. On a tenté d'activer le contrôle de puissance et aucune broche maître n'est active. Sélectionner une broche maître (#MASTER) avant d'activer le contrôle de puissance. Pendant la préparation des blocs. Lorsqu'un axe est programmé pour être esclave de la variable FLWMASTER, la synchronisation peut uniquement être réalisée sur les cotes réelles. Il est impossible de synchroniser sur les cotes théoriques. Réaliser la synchronisation avec les cotes réelles. CNC 8070 Type de #CUTTING ou #PIERCING non défini. DÉTECTION CAUSE SOLUTION Pendant la préparation des blocs. Le type de piercing o cutting est nul. Le paramètre T est absent de l'instruction et aucune valeur de T (type) n'a été programmée au préalable. Activer un tableau technologique, programmer la commande matériau ou programmer la commande #PIERCING ou #CUTTING qui produit l'erreur avec un paramètre T correct (valeur entre 1 et 10). (REF: 1901) ·125· S o l ut i o n s d ’ e r r e ur s . 2424 Aucun tableau technologique actif (#MATERIAL). DÉTECTION CAUSE SOLUTION 2425 #PLC[PLCmark=0/1,PLCmark=0/1...] DÉTECTION CAUSE SOLUTION 2426 CNC 8070 (REF: 1901) ·126· Au cours de l'exécution. La CNC a tenté d'activer le DMC sur une broche analogique. Le DMC peut uniquement être activé sur des broches numériques. Il est obligatoire de programmer ON/OFF. DÉTECTION CAUSE SOLUTION 2434 Au cours de l'exécution. Dans la fonction #DMC, l'override minimale est supérieure à l'override maximale. L'override minimale (OVRMIN) doit être inférieure à l'override maximale (OVRMAX). #DMC ON: Programmation non autorisée avec broche analogique. DÉTECTION CAUSE SOLUTION 2433 Au cours de l'exécution. Dans la fonction #DMC, l'avancée minimale est supérieure à l'avancée maximale. L'avancée minimale (FZMIN) doit être inférieure à l'avancée maximale (FZMAX). #DMC ON: OVRMIN doit être inférieur à OVRMAX. DÉTECTION CAUSE SOLUTION 2432 Pendant l’édition et l’exécution. L'une des commandes de l'instruction #DMC possède une valeur non valable. Vérifier dans le manuel de programmation la syntaxe de l'instruction. #DMC ON: FZMIN doit être inférieur à FZMAX. DÉTECTION CAUSE SOLUTION 2431 Pendant l’édition et l’exécution. La syntaxe de l'instruction n'est pas correcte. Vérifier dans le manuel de programmation la syntaxe de l'instruction. Paramètre DMC hors plage DÉTECTION CAUSE SOLUTION 2430 Pendant l’édition et l’exécution. La syntaxe de l'instruction n'est pas correcte. Vérifier dans le manuel de programmation la syntaxe de l'instruction. #DMC OFF DÉTECTION CAUSE SOLUTION 2429 Pendant l’édition et l’exécution. La marque programmée dans l'instruction #PLC n'est pas modifiable. L'instruction #PLC peut uniquement activer ou désactiver des marques modifiables. #DMC ON[<PWRSP value><,OVRMIN value><,OVRMAX value><,FZMIN value><,FZMAX value>] DÉTECTION CAUSE SOLUTION 2428 Pendant l’édition et l’exécution. La syntaxe de l'instruction n'est pas correcte. Vérifier dans le manuel de programmation la syntaxe de l'instruction. #PLC: marque non modifiable. DÉTECTION CAUSE SOLUTION 2427 Pendant la préparation des blocs. Les commandes #PIERCING et #CUTTING ont été programmées, et aucun tableau technologique n'est actif. Activer un tableau technologique depuis l'IHM ou programmer la commande #MATERIAL. Au cours de l'exécution. Il reste à programmer la commande ON/OFF pour activer ou annuler la fonction. Vérifier dans le manuel de programmation la syntaxe de l'instruction. Inclure la commande ON pour activer la fonction (par exemple, #DMC ON [...]) ou la commande OFF pour annuler (par exemple, #DMC OFF). Programmation interdite hors d'une macro G8077. DÉTECTION CAUSE SOLUTION Pendant l'exécution. Une fonction G8078 a été programmée hors d'une macro G8077. Réviser la programmation. Les fonctions G8078 doivent être programmées après la macro G8077. S o l ut i o n s d ’ e r r e ur s . 2436 Programmation interdite hors d'une macro G8777. DÉTECTION CAUSE SOLUTION 2438 #LEAP[GAP] XY sans avoir programmé au préalable #GAPCTRL ON. DÉTECTION CAUSE SOLUTION 2441 SOLUTION CAUSE SOLUTION Pendant la préparation des blocs. Un paramètre de l'instruction a été programmé plus d'une fois. Programmer une seule fois chaque paramètre de l'instruction. Préfixe de variable inexistant. DÉTECTION CAUSE SOLUTION 2456 Pendant la préparation des blocs. L'identificateur de fichier (commande F) est erroné. L'identificateur de fichier (commande F) doit posséder une valeur de 1 à 4. #OPEN/#CLOSE/#WRITE : double programmation. DÉTECTION CAUSE SOLUTION 2446 Pendant l'exécution de la commande #MATERIAL ou en activant/validant un tableau technologique. Le format du tableau a été modifié (unités, nouvelles variables, plage de type énuméré, etc). Pour que la CNC prenne le nouveau format en compte, il faut réinitialiser. Réinitialiser la CNC. #OPEN/#CLOSE/#WRITE : valeur de handle du fichier hors plage. DÉTECTION CAUSE SOLUTION 2445 Pendant l'exécution. Une fonction G8753 a été programmée hors d'une macro G8754. Réviser la programmation. La fonction G8753 doit être programmée après la macro G8754. Pour appliquer les modifications sur le fichier de matériau, il faut réinitialiser la CNC. DÉTECTION 2444 Pendant la préparation des blocs. La commande #FINALSUB a été programmée plus d'une fois dans le programme principal. Une seule programmation est autorisée. Dans des boucles ($IF, $FOR, etc. ou dans des sous-routines aucune erreur n'est détectée). Programmer une seule fois #FINALSUB. Programmation interdite hors d'une macro G8754. DÉTECTION CAUSE SOLUTION 2443 Pendant la préparation des blocs. Un saut a été programmé avec la commande #LEAP, qui doit s'achever à un certaine distance sur la tôle (paramètre GAP). La commande #GAPCTRL ON n'a pas été programmée au préalable. Il se peut que le paramètre GAP ne soit pas programmé dans le bloc où l'erreur se produit, mais dans un #LEAP antérieur. Les possibles solutions sont les suivantes: • Programmer #GAPCTRL ON avant le #LEAP où l'erreur est détectée • Éliminer le paramètre GAP des commandes #LEAP. Double programmation de #FINALSUB. DÉTECTION CAUSE 2442 Pendant l'exécution. L'une des fonctions G8778, G8701 ou G8702 a été programmée hors d'une macro G8777. Réviser la programmation. Les fonctions G8778, G8701 ou G8702 doivent être programmées après la macro G8777. Pendant l'exécution. Le préfixe de la variable n'existe pas. Consulter dans les documents la liste des variables autorisées. Avec #GAPPOS actif, il n'est pas permis de changer les trois premiers axes. DÉTECTION CAUSE SOLUTION Pendant la préparation des blocs. On a essayé de modifier les trois premiers axes du canal (#FREE AX ou #SET AX) alors que l'instruction #GAPPOS est active. Ne pas modifier les trois premiers axes du canal alors que l'instruction #GAPPOS ou #GAPCTRL est active. CNC 8070 (REF: 1901) ·127· S o l ut i o n s d ’ e r r e ur s . 2457 #GAPPOS : paramètres trop nombreux. DÉTECTION CAUSE SOLUTION 2458 #DMC ON: La broche master doit avoir le paramètre DMCSPDL = Oui. DÉTECTION CAUSE SOLUTION CNC 8070 (REF: 1901) ·128· Pendant la préparation des blocs. Plus de trois axes de l'instruction #GAPPOS ont été définis. Seuls les trois premiers axes du canal doivent être définis dans l'instruction #GAPPOS. Au cours de l'exécution. On a tenté d'activer le DMC sur une broche qui n'est pas autorisée pour cela. Pour activer le DMC sur une broche, cette dernière doit avoir son paramètre machine DMCSPDL=Oui. S o l ut i o n s d ’ e r r e ur s . 3000-3999 3000 'Il est impossible de programmer une trajectoire circulaire avec un axe esclave' DÉTECTION CAUSE SOLUTION 3001 'Il est impossible de déplacer un axe en mode de visualisation' DÉTECTION CAUSE SOLUTION 3002 SOLUTION SOLUTION SOLUTION Après avoir détecté le signal de palpeur. Processus de palpage activé sans G100 programmée. Contacter votre fournisseur. 'Erreur dans le processus de palpeur' DÉTECTION CAUSE SOLUTION 3010 À l'initialisation du processus de palpage' C’est une sécurité d’activation du processus de palpage. Un axe programmé n’est pas valide ou n’est pas disponible. Vérifier la validité et la disponibilité des axes programmés. 'Signal du palpeur reçu avant le déplacement' DÉTECTION CAUSE SOLUTION 3008 Pendant le repositionnement d’un axe. Pendant le déplacement de repositionnement, l’axe a atteint les limites de logiciel. Si le point de renouvellement est hors des limites de logiciel, l’axe ne peut pas atteindre ce point. Les axes doivent toujours être dans les limites de logiciel. Vérifier que les limites de logiciel sont correctes, qu’elles n’ont pas été modifiées depuis le programme pièce ou le PLC. 'Erreur de la commande de position dans l'initialisation du processus de palpeur' DÉTECTION CAUSE 3007 Pendant le repositionnement d’un axe. Pendant le déplacement de repositionnement, l’axe a atteint les limites de logiciel. Si le point de renouvellement est hors des limites de logiciel, l’axe ne peut pas atteindre ce point. Les axes doivent toujours être dans les limites de logiciel. Vérifier que les limites de logiciel sont correctes, qu’elles n’ont pas été modifiées depuis le programme pièce ou le PLC. 'Limite négative de logiciel dépassée' DÉTECTION CAUSE 3005 Au cours de l'exécution. La CNC essaie de déplacer un axe se trouvant en mode de visualisation. La CNC ne peut pas déplacer les axes actifs en mode de visualisation. Pour déplacer l'axe, désactiver le mode de visualisation (marque DRO(axis) du PLC). 'Limite positive de logiciel dépassée' DÉTECTION CAUSE 3003 Au cours de l'exécution. La CNC essaie de déplacer individuellement l’axe esclave d’un couplage ou d’un axe gantry. Un axe esclave ne peut pas être déplacé individuellement. Pour déplacer un axe esclave, il faut déplacer l'axe maître à lequel il se trouve associée. Après avoir détecté le signal de palpeur. C’est une sécurité d’activation du processus de palpage. Vérifier la validité et la disponibilité des axes programmés. CNC 8070 'L'axe n'a pas été défini comme palpeur (PROBEAXIS)' DÉTECTION CAUSE SOLUTION Au cours de l'exécution. Un déplacement de palpage est programmé sur un axe qui n’est pas défini comme axe participant à un déplacement avec palpeur. Le paramètre PROBEAXIS établit si l’axe peut participer à des déplacements avec palpeur. (REF: 1901) ·129· S o l ut i o n s d ’ e r r e ur s . 3011 'Trop d'axes programmés comme palpeur' DÉTECTION CAUSE SOLUTION 3013 'Distance de freinage supérieur au paramètre PROBERANGE' DÉTECTION CAUSE SOLUTION 3015 SOLUTION SOLUTION CNC 8070 (REF: 1901) ·130· Au cours de l'exécution. La vitesse maximale de la broche est égale à zéro. Programmer une vitesse. 'Erreur à l'initialisation des cotes des axes' DÉTECTION CAUSE SOLUTION 3023 Au cours de l'exécution. La vitesse de la broche est égale à zéro. Programmer une vitesse. 'Vitesse maximale de coupe constante égale à zéro' DÉTECTION CAUSE SOLUTION 3022 Au cours de l'exécution. L’avance résultante est très petite pour la vitesse programmée. Augmenter l’avance ou augmenter les tours de la broche. 'On n'a pas programmé S dans G96' DÉTECTION CAUSE SOLUTION 3021 Au cours de l'exécution. La broche n’a pas eu le temps d’atteindre la vitesse programmée. Diminuer l’avance, diminuer la vitesse de la broche ou programmer la vitesse avant pour permettre à la broche d’atteindre sa vitesse. 'Avance programmée en G95 trop petite' DÉTECTION CAUSE SOLUTION 3020 Au cours de la recherche de bloc. La CNC a essayé d’activer une recherche de bloc alors qu’une autre était active. Contacter votre fournisseur. 'Vitesse de coupe constante pas encore atteinte' DÉTECTION CAUSE SOLUTION 3019 Au cours de l'exécution. L’utilisateur a essayé d’activer le mode manuel pendant une recherche de bloc et la CNC l’a ignoré. La CNC ne permet pas d’activer le mode manuel pendant la recherche de bloc. 'Recherche de bloc déjà activée' DÉTECTION CAUSE SOLUTION 3018 Au cours de l'exécution. Pendant une recherche de bloc, la CNC a trouvé une recherche de référence et l’a ignorée. Effectuer la recherche de référence machine hors du programme. 'Le mode manuel est omis dans la recherche de bloc' DÉTECTION CAUSE 3017 Au cours de l'exécution. La distance nécessaire pour freiner avec l’avance active est supérieure à la distance maximale admissible (paramètre PROBERANGE), probablement due à l’erreur de poursuite. Diminuer l’avance de palpage ou diminuer l’erreur de poursuite. 'Recherche de référence machine omise dans la recherche de bloc' DÉTECTION CAUSE 3016 Au cours de l'exécution. Le nombre d’axes programmés dans le déplacement de palpage dépasse le nombre maximum d’axes du canal. Corriger la programmation du bloc de palpage. Au cours de l'exécution. Les cotes d'un axe ne coïncident pas. Contacter Fagor. 'Axe(s) manquant(s) dans le nouveau système de coordonnées' DÉTECTION CAUSE SOLUTION Au cours de l'exécution. Un des trois premiers axes du nouveau système de coordonnées n’existe pas. Définir les trois premiers axes du canal avec l'instruction #SET AX. S o l ut i o n s d ’ e r r e ur s . 3025 'Limite positive de logiciel dépassée' DÉTECTION CAUSE SOLUTION 3026 'Limite négative de logiciel dépassée' DÉTECTION CAUSE SOLUTION 3027 SOLUTION SOLUTION SOLUTION Au cours de l'exécution. La CNC a essayé de faire une recherche de référence d’un axe de visualisation. La CNC ne permet pas de réaliser une recherche de référence d’un axe de visualisation. 'Il est impossible de passer au mode manuel si l'axe est dans le centre de rotation' DÉTECTION CAUSE SOLUTION 3034 Au cours de l'exécution. La CNC a essayé d’activer une des compensations RTCP ou TLC alors que l’autre était active. Les deux compensations ne peuvent pas être actives simultanément; en désactiver une (#RTCP OFF / TLC OFF) avant d’activer l’autre. 'Recherche de zéro non admise en mode de visualisation' DÉTECTION CAUSE SOLUTION 3033 Au cours de l'exécution. Dans le processus de mesure avec palpeur, il y a des axes simulés et non simulés. Tous les axes intervenant dans un processus de mesure avec palpeur doivent être du même type. 'Compensation (RTCP/TLC) interdite dans l'état actuel' DÉTECTION CAUSE 3032 Au cours de l'exécution. La CNC ne peut pas exécuter la transformation de coordonnées machine à coordonnées pièce. Contacter Fagor. 'Il est impossible de mélanger des axes simulés et des non simulés' DÉTECTION CAUSE SOLUTION 3031 Au cours de l'exécution. La CNC ne peut pas exécuter la transformation de coordonnées pièce à coordonnées machine. Contacter Fagor. 'Erreur dans le calcul de la transformation directe de RTCP' DÉTECTION CAUSE 3030 Au cours de l'exécution. La CNC a essayé de déplacer un axe sur un point se trouvant hors des limites de logiciel. Les axes doivent toujours être dans les limites de logiciel. Vérifier que les limites de logiciel sont correctes, qu’elles n’ont pas été modifiées depuis le programme pièce ou le PLC. 'Erreur dans le calcul de la transformation inverse de RTCP' DÉTECTION CAUSE 3029 Au cours de l'exécution. La CNC a essayé de déplacer un axe sur un point se trouvant hors des limites de logiciel. Les axes doivent toujours être dans les limites de logiciel. Vérifier que les limites de logiciel sont correctes, qu’elles n’ont pas été modifiées depuis le programme pièce ou le PLC. Au cours de l'exécution. La CNC essaie d’activer le mode manuel avec la transformation d’axe C frontal active et les axes dans le centre de rotation. Activer le mode manuel avec les axes sur une position différente de celle du centre de rotation. 'Numéro de gamme non valable' DÉTECTION CAUSE SOLUTION CNC 8070 Au cours de l'exécution. La CNC essaie d’accéder à un set de paramètres qui n’existe pas. Le numéro de set doit être compris entre 1 et le paramètre NPARSET. (REF: 1901) ·131· S o l ut i o n s d ’ e r r e ur s . 3035 'Différence d'erreurs de poursuite d'axes accouplements trop grande' DÉTECTION CAUSE SOLUTION 3036 'Processus de changement de gamme incorrect' DÉTECTION CAUSE SOLUTION 3037 SOLUTION SOLUTION SOLUTION 3043 Pendant l'exécution. Une fonction G33, G34 ou G95 est active et la valeur du registre SYNC du PLC n’est pas valide. La valeur du registre SYNC du PLC doit être comprise entre 1 et le nombre de broches du système. La valeur peut aussi être zéro. 'Broche sur M5 en activant le filetage électronique' DÉTECTION CAUSE (REF: 1901) SOLUTION ·132· Pendant l'exécution. Les fonctions G33, G34 et G95 ont besoin d'une broche pour travailler. Cette broche est par défaut la broche maître du canal, mais si le registre SYNC du PLC indique une autre broche, le canal utilisera cette dernière. La CNC affichera erreur si aucune des deux broches n'est définie. Définir une broche maître dans le canal ou affecter une broche au registre SYNC du PLC. 'La broche indiquée sur le registre SYNC n’existe pas' DÉTECTION CAUSE CNC 8070 Au cours de l'exécution. L’axe hirth n’est pas positionné sur un nombre multiple de son pas. Positionner correctement l’axe hirth sur une position valide ou les désactiver comme axe hirth. 'La broche pour G33/G34/G95 n'a pas été définie' DÉTECTION CAUSE 3042 Pendant l'exécution à vide. La recherche de bloc ne passe pas par le bloc d'arrêt. Changer le bloc d'arrêt. 'Axe Hirth incorrectement positionné' DÉTECTION CAUSE SOLUTION 3041 Au cours de l'exécution. Le système est surchargé. Fermer les applications qui ne sont pas en rapport avec la CNC. Si l'erreur persiste, contacter Fagor. 'Le bloc d'arrêt dans la recherche de bloc n'a pas été trouvé' DÉTECTION CAUSE SOLUTION 3040 Pendant l'exécution. La CNC essaie de déplacer un axe, mais le PLC n'a pas mis le signal SERVO(axis)ON. Vérifier dans le programme de PLC le traitement du signal SERVO(axis)ON ou augmenter la valeur du paramètre DWELL de l’axe. La CNC peut afficher cette erreur lorsqu’elle travaille avec jonction de blocs (G50, G5 ou HSC) et qu’il faut forcer l’arrêt de l’axe (avec un M ou G7) avant le déplacement de l’axe en position. 'Trop de paramètres en attente de reporter' DÉTECTION CAUSE SOLUTION 3039 Au cours de l'exécution. La gamme de broche dans l’historique de la CNC ne coïncide pas avec la gamme marquée par le PLC comme gamme active. Vérifier le programme de PLC. Axe bloqué. DÉTECTION CAUSE 3038 Au cours de l'exécution. Sur un axe gantry, la différence entre l’erreur de poursuite de l’axe maître et de l’esclave est supérieure à celle définie dans le paramètre MAXCOUPE ; dans un couplage d’axes, la différence est supérieure à la valeur définie. Régler de façon similaire le comportement dynamique les deux axes ou augmenter erreur permise. Pendant l'exécution. La broche utilisée pour un filetage électronique (G33/G34) est arrêtée ou une M5 a été programmée dans le même bloc que G33/G34. La broche utilisée pour le filetage électronique doit être en marche. Mettre la broche en marche dans un bloc précédent ou dans le même bloc que G33/G34. S o l ut i o n s d ’ e r r e ur s . 3044 'La recherche de zéro d'un axe actif comme axe indépendant est interdite' DÉTECTION CAUSE SOLUTION 3045 'M6 n'est pas admise' DÉTECTION CAUSE SOLUTION 3046 SOLUTION SOLUTION SOLUTION SOLUTION Au cours de l'exécution. Après avoir interrompu un programme et passé au mode MHFS, l’utilisateur a édité certaines fonctions M3, M4, M5, M19 ou M41 à M44 interdites pour la même broche. Décider quelle est la fonction M à exécuter ou exécuter les deux successivement mais pas simultanément. 'L'état de la broche doit coïncider avec celui du moment de l'interruption' DÉTECTION CAUSE SOLUTION 3056 Pendant l'exécution. L'utilisateur a essayé de changer la vitesse d'une broche activée comme axe C. Programmer une avance F pour l’axe C ou le désactiver (#CAX) pour programmer une vitesse. 'Ms incompatibles pour la même broche' DÉTECTION CAUSE 3052 Au cours de l'exécution. Après avoir interrompu un programme et changé au mode MHFS, l'utilisateur a édité une fonction M associée à une gamme que n'existe pas dans la broche. Programmer la gamme correcte. 'On n'admet pas le changement de S si la broche travaille comme axe C' DÉTECTION CAUSE SOLUTION 3051 Au cours de l'exécution. Après avoir interrompu un programme avec G63 active et passé au mode MHFS, l’utilisateur a édité une fonction M3, M4, M5, M19 ou M41 à M44 interdite pour G63. Désactiver la fonction G63 ou attendre la fin de cette fonction avant d’interrompre le programme. 'La gamme programmée n’existe pas' DÉTECTION CAUSE 3050 Au cours de l'exécution. Après avoir interrompu un programme et passé au mode MHFS, l’utilisateur a édité une M ou une S référée à une broche qui n’existe pas dans le canal ou dans le système. Associer la fonction à la broche correcte. Accéder à la broche depuis le canal où elle se trouve. 'On n’admet pas M3/M4/M5/M19/M41-M44 avec G63 active' DÉTECTION CAUSE 3048 Au cours de l'exécution. Après avoir interrompu un programme et passé au mode MHFS, l’utilisateur a édité une M6 interdite. Le changement d’outil ne permet pas de continuer l’exécution du programme interrompu. Taper sur RAZ et exécuter M6 depuis le mode MDI. 'La broche associée n’appartient pas au canal' DÉTECTION CAUSE 3047 Au cours de l'exécution. La CNC essaie de réaliser la recherche de référence d’un axe indépendant. Si l’axe doit réaliser un déplacement indépendant, attendre à ce qu’il termine ou interrompre le déplacement depuis le PLC (marque IABORT) ou avec une RAZ dans le canal. Si l’axe est synchronisé, annuler la synchronisation ou effectuer une RAZ dans le canal. Au cours de l'exécution. Après avoir interrompu un programme et changé au mode MSF, l'utilisateur essai de sortir de ce mode avec la broche à un état M3, M4, M5 ou M19 différent à l'état initial. Programmer un nouveau changement d’état de la broche, de manière à ce que celleci ait le même état qu’avant l’interruption. CNC 8070 'Erreur de calcul de la transformation inverse de l’axe d’inclinaison #ANGAX' DÉTECTION CAUSE SOLUTION Pendant l'exécution. Dans une transformation angulaire, l’axe incliné et l'axe orthogonal forment un angle de 90º. Si les axes forment un angle de 90º, la transformation angulaire n'est pas nécessaire. Annuler la transformation angulaire (#ANGAX OFF) ou définir un angle différent de 90º. (REF: 1901) ·133· S o l ut i o n s d ’ e r r e ur s . 3057 'Erreur de calcul de la transformation directe de l’axe d’inclinaison #ANGAX' DÉTECTION CAUSE SOLUTION 3058 'Les fonctions M3/M4/M5/M19 et M41-M44 de la broche doivent être envoyées au PLC' DÉTECTION CAUSE SOLUTION 3059 SOLUTION SOLUTION SOLUTION SOLUTION SOLUTION CNC 8070 (REF: 1901) ·134· Au cours de l'exécution. L’utilisateur a programmé une synchronisation en boucle ouverte (OLOOP) pour la broche maître, mais celle-ci était en train de travailler en boucle fermée. La CNC informe du changement; aucune action n’est nécessaire. 'La broche master de la synchronisation passe à boucle fermée' DÉTECTION CAUSE 3064 Pendant l'exécution. La CNC ne peut pas synchroniser en boucle fermée une broche maître si celle-ci n’a pas été référencée auparavant. Effectuer une recherche de référence de la broche maître avant de synchroniser les broches. 'La broche master de la synchronisation ne passe pas à boucle ouverte' DÉTECTION CAUSE 3063 Au cours de l'exécution. Après avoir interrompu un programme et changé au mode MHFS, l'utilisateur a programmé une vitesse et une nouvelle gamme; la vitesse dépasse la gamme maximale. Changer la vitesse ou la gamme programmée ou n’en programmer qu’une pour qu’elles ne soient pas contradictoires. Une broche master non référencée n'accepte pas de synchronisation en boucle fermée. DÉTECTION CAUSE 3062 Au cours de l'exécution. L'utilisateur a interrompu le programme pendant l'exécution de M19 ou G74 dans une broche. La CNC ne peut pas envoyer les fonctions M3, M4, M5, M19 ou M41a M44 à la broche. Continuer l'exécution jusqu'à la fin de la fonction M19 ou G74. Ensuite, interrompre le programme et envoyer les fonctions souhaitées à la broche. 'On n’admet pas une S supérieure à la gamme programmée' DÉTECTION CAUSE 3061 Au cours de l'exécution. Après une recherche de bloc et avant de continuer l’exécution du programme, la CNC a détecté qu’une fonction de la broche n’a pas été envoyée au PLC. Avec le programme interrompu, passer au mode MHFS et envoyer les fonctions nécessaires au PLC. 'On n’admet pas M3/M4/M5/M19/M41-M44 avec M19 ou G74 actives' DÉTECTION CAUSE 3060 Pendant l'exécution. Dans une transformation angulaire, l’axe incliné et l'axe orthogonal forment un angle de 90º. Si les axes forment un angle de 90º, la transformation angulaire n'est pas nécessaire. Annuler la transformation angulaire (#ANGAX OFF) ou définir un angle différent de 90º. Au cours de l'exécution. L’utilisateur a programmé une synchronisation en boucle fermée (CLOOP) pour la broche maître, mais celle-ci était en train de travailler en boucle ouverte. La CNC informe du changement ; aucune action n’est nécessaire. 'La broche à fileter avec G33/G34 doit être référencée' DÉTECTION CAUSE SOLUTION Pendant l'exécution. La broche utilisée dans le filetage G33/G34 n’est pas référencée. Si la CNC utilise la broche maître du canal, elle effectue toujours une recherche de référence avant G33/G34. Si le PLC sélectionne une autre broche (indique SYNC), effectuer une recherche de référence de la broche. S o l ut i o n s d ’ e r r e ur s . 3065 'La vitesse de rotation de la broche programmée pour G33/G34 dépasse le seuil du codeur' DÉTECTION CAUSE SOLUTION 3066 'Erreur de poursuite de l'axe tangentiel sur la trajectoire' DÉTECTION CAUSE SOLUTION 3067 SOLUTION SOLUTION SOLUTION SOLUTION Pendant l'exécution. L'utilisateur a interrompu le programme pendant le changement de gamme et a essayé de modifier les fonctions S, M ou H depuis le mode MHFS. Continuer l’exécution jusqu’à la fin du changement de gamme. Ensuite, interrompre le programme et envoyer les fonctions souhaitées à la broche. 'Le pas et S de broche programmés pour G33/G34 dépassent l'avance maximum permise' DÉTECTION CAUSE SOLUTION 3073 Pendant l'exécution. La broche associée à la fonction G33, G34 ou G95 est arrêtée. Vérifier la vitesse de la broche associée à ces fonctions, qui sera la broche maître du canal ou la broche indiquée dans le registre SYNC, associée au canal. 'On n'admet pas S, M ou H avec processus de changement actif de gamme' DÉTECTION CAUSE 3072 Au cours de l'exécution. La CNC n’a pas terminé correctement le changement de gamme d’un axe ou d’une broche parce que l'asservissement ne répond pas à la demande de changement de gamme. Vérifier l'état de l'asservissement. 'La vitesse de broche associée à G33/G34/G95 est nulle' DÉTECTION CAUSE SOLUTION 3071 Au cours de l'exécution. Après avoir terminé l’exécution en retrace, la marque RETRACE du PLC continue active. Le PLC doit désactiver la marque RETRACE pour que le programme continue. Changement de gamme erroné, le régulateur ne répond pas. DÉTECTION CAUSE 3070 Au cours de l'exécution. La fonction programmée a besoin de que la broche soit commandée en position. La CNC ne peut pas commander la broche en position parce que celle-ci ne dispose pas de codeur. La broche a besoin d’un codeur. Contacter votre fournisseur. 'RETRACE fini, désactiver la marque pour continuer' DÉTECTION CAUSE 3069 Au cours de l'exécution. L’axe tangentiel ne suit pas fidèlement la trajectoire du plan de travail. Contacter FAGOR. 'G33/G34: Programmation interdite sans broche commandée en position' DÉTECTION CAUSE 3068 Pendant l'exécution. La vitesse programmée pour la fonction G33/G34 dépasse le seuil permis par le codeur installé sur la broche. Dépasser le seuil de vitesse du codeur provoque une erreur dans la lecture du comptage de la broche. La CNC ne permet pas d’exécuter la G33/G34 avec la vitesse programmée, car elle ne peut pas garantir la validité du filet. Si la broche a dépassé la vitesse seuil, la CNC a besoin de référencer la broche pour récupérer la cote. Pendant l'exécution. Au commencement d’un filetage G33/G34, la CNC a détecté que le pas et la vitesse programmés impliquent une avance dépassant le maximum permis. L’avance maximum peut être limitée par les paramètres machine ou par le PLC. Vérifier la programmation de la fonction G33/G34. Pour maintenir le pas programmé, modifier la vitesse programmée ou, si cela est possible, augmenter depuis le PLC l’avance maximum du canal. Au besoin, réviser les paramètres machine en rapport avec l’avance maximum des axes, impliqués dans le filet. CNC 8070 'La limite de vitesse de l'angle est dépassée' DÉTECTION CAUSE SOLUTION Au cours de l'exécution. La CNC a dépassé la dynamique d’un axe, pendant la transition entre deux blocs. Contacter Fagor. (REF: 1901) ·135· S o l ut i o n s d ’ e r r e ur s . 3074 'Fonction non-compatible avec Motion Control actif' DÉTECTION CAUSE SOLUTION 3075 'Axe multiple désactivé' DÉTECTION CAUSE SOLUTION 3076 SOLUTION SOLUTION SOLUTION SOLUTION SOLUTION CNC 8070 Pendant l'exécution de découpe au laser (commutation synchronisée). La vitesse de découpe est trop élevée pour la taille de la grille. Diminuer la vitesse ou le temps de cycle. 'Il y a trop d'anticipation pour activer la sortie numérique' DÉTECTION CAUSE (REF: 1901) SOLUTION ·136· Au cours de l'exécution. La CNC a essayé de déplacer un axe qui n’avait pas été repositionné auparavant sur une trajectoire circulaire. Il n’est pas possible de déplacer un axe qui n’a pas été repositionné sur une trajectoire circulaire. 'Vitesse trop grande' DÉTECTION CAUSE SOLUTION 3082 Pendant l'exécution. L’utilisateur a programmé une synchronisation (#SYNC) en boucle fermée (commande OLOOP) pour la broche maître, mais celle-ci travaillait en boucle ouverte pour une autre synchronisation préalable et continuera en boucle ouverte. La broche ne change pas de boucle. Laisser la broche en boucle ouverte ou supprimer la synchronisation préalable pour que la broche passe en boucle fermée. 'Il n'est pas possible d'assumer l'offset de l'axe non repositionné' DÉTECTION CAUSE 3081 Pendant l'exécution. L’utilisateur a programmé une synchronisation (#SYNC) en boucle ouverte (commande OLOOP) pour la broche maître, mais celle-ci travaillait en boucle fermée pour une autre synchronisation préalable et continuera en boucle fermée. La broche ne change pas de boucle. Laisser la broche en boucle fermée ou supprimer la synchronisation préalable pour que la broche passe à boucle ouverte. 'La broche master de la synchronisation ne passe pas à boucle fermée' DÉTECTION CAUSE 3080 Pendant l'exécution. On a essayé d'activer le mode Bloc par Bloc pendant le retrace dans un programme avec de nombreux blocs effectuant des mouvements très courts. Pour évite la saturation des ressources du système, la CNC ne permet pas la fonction Bloc par Bloc dans ce type de programmes. 'La broche master de la synchronisation ne passe pas à boucle ouverte' DÉTECTION CAUSE 3079 Au cours de l'exécution. L’utilisateur a essayé d’abandonner le mode MHFS alors que la marque RETRACE du PLC était active. Désactiver la marque RETRACE du PLC avant d’abandonner le mode MHFS. 'Pendant ce processus de RETRACE le Bloc par Bloc n'est pas accepté. Désactiver Bloc par Bloc' DÉTECTION CAUSE 3078 Au cours de l'exécution. L’axe ne peut pas se déplacer parce qu’il appartient à un groupe multi-axe et qu’il est désactivé. Activer l’axe pour pouvoir le déplacer (marque SWITCH du PLC). 'Il n'est pas possible de sortir de MHFS avec Retrace actif. Désactiver' DÉTECTION CAUSE 3077 Au cours de l'exécution. La CNC a essayé de modifier le système de coordonnées ou la transformation de coordonnées en ayant une fonction de motion control active et le paramètre IMOVEMACH désactivé. Désactiver les fonctions de motion control avant de changer le système de coordonnées ou la transformation de coordonnées. Pendant l'exécution de découpe au laser (commutation synchronisée). Le retard calculé pour le laser est négatif, ce qui signifie qu'il ne reste pas assez de marge suffisante de cycles pour l'anticipation. Diminuer le temps de cycle ou la valeur des paramètres d’anticipation. S o l ut i o n s d ’ e r r e ur s . 3083 'Il y a trop de retard pour activer la sortie numérique' DÉTECTION CAUSE SOLUTION 3084 'Erreur du driver dans l'activation/désactivation du laser' DÉTECTION CAUSE SOLUTION 3087 SOLUTION SOLUTION Au cours de l'exécution. La CNC a essayé de déplacer un axe à une cote se trouvant en dehors d'une zone de travail de non sortie. La zone peut être définie par programme ou par PLC (avec les variables relatives aux zones de travail). Maintenir les axes dans les limites de la zone de travail de non sortie. Si un axe se trouve en dehors des limites, le déplacer dans le bon sens à l’aide du clavier de jog. 'Point dans la zone interdite' DÉTECTION CAUSE SOLUTION 3095 Au cours de l'exécution. La transformation de coordonnées machine à pièce ne peut pas être exécutée. Contacter Fagor. 'La limite de zone de travail est dépassée' DÉTECTION CAUSE 3093 Au cours de l'exécution. La transformation de coordonnées pièce à machine ne peut pas être exécutée. Contacter Fagor. 'Erreur de calcul de la transformée directe de l'axe virtuel de l'outil #VIRTAX' DÉTECTION CAUSE SOLUTION 3092 Pendant l'exécution de découpe au laser (commutation synchronisée). Les conditions de hardware ou de paramétrage nécessaires pour pouvoir utiliser la performance de découpe au laser ne sont pas accomplies. Vérifier les conditions suivantes: • Il doit y avoir une carte d’expansion type Sercos, avec logiciel ID égal ou supérieur à 1.2. • Le paramètre NLOCOUT doit être 8. • Le paramètre PWMOUTPUT ne peut pas être supérieur à 2 (0, 1, 2). 'Erreur de calcul de la transformée inverse de l'axe virtuel de l'outil #VIRTAX' DÉTECTION CAUSE SOLUTION 3090 Pendant l'exécution de découpe au laser (PWM). La performance PWM est déjà activée dans un canal autre que celui souhaité. Vérifier la programmation du PWM. 'Erreur dans la programmation du masque du laser' DÉTECTION CAUSE 3089 Pendant l'exécution de découpe au laser (commutation synchronisée). Les conditions de hardware ou de paramétrage nécessaires pour pouvoir utiliser la performance de découpe au laser ne sont pas accomplies. Vérifier les conditions suivantes: • Il doit y avoir une carte d’expansion type Sercos, avec logiciel ID égal ou supérieur à 1.2. • Le paramètre NLOCOUT doit être 8. • Le paramètre PWMOUTPUT ne peut pas être supérieur à 2 (0, 1, 2). 'PWM activé dans un autre canal' DÉTECTION CAUSE SOLUTION 3088 Pendant l'exécution de découpe au laser (commutation synchronisée). Le retard programmé pour le laser est excessif. Vérifier la valeur des paramètres d'anticipation TON / TOF. Au cours de l'exécution. La CNC a essayé de déplacer un axe à une cote se trouvant dans une zone de travail de non entrée. La zone peut être définie par programme ou par PLC (avec les variables relatives aux zones de travail). Maintenir les axes dans les limites de la zone de travail de non entrée. Si l’outil se trouve dans la zone interdite, désactiver temporairement cette zone, déplacer l’axe dans le bon sens à l’aide du clavier de jog jusqu’à ce qu’elle sorte de la zone interdite et activer à nouveau la zone de non entrée. CNC 8070 Point final mal programmé dans #GAPCTRL ou #LEAP. DÉTECTION CAUSE SOLUTION Au cours de l'exécution. Pendant les instructions #GAPCTRL ou #LEAP, la CNC ne peut pas corriger la position après avoir reçu le signal du capteur. Vérifier que le point final indiqué dans les instructions #GAPCTRL ou #LEAP est correct. (REF: 1901) ·137· S o l ut i o n s d ’ e r r e ur s . 3096 PWRCTRL DUTY activé dans un autre canal. DÉTECTION CAUSE SOLUTION 3097 PWRCTRL OUT activé dans un autre canal. DÉTECTION CAUSE SOLUTION 3098 SOLUTION SOLUTION SOLUTION SOLUTION SOLUTION CNC 8070 CAUSE SOLUTION ·138· Au cours de l'exécution. Les valeurs de la puissance à vide et la puissance objectif pendant l'usinage sont semblables. Il est possible que le DMC ne puisse pas distinguer avec exactitude les entrées et les sorties de la pièce. La puissance objectif (programmée ou obtenue par l'apprentissage) doit atteindre au moins 20 % de la puissance à vide. Dans ce cas, il est recommandé de désactiver la fonction DMC dans cet usinage. Programmer une puissance objectif supérieure, que l'on ne va pas vraiment atteindre, peut avoir pour conséquence que le DMC ne détecte jamais d'entrées à la pièce et réalise tout l'usinage comme si l'outil travaillait à vide. Une collision a été détectée. DÉTECTION (REF: 1901) Au cours de l'exécution. On a tenté d'exécuter l'instruction #HSC ou #SWT dans un axe avec un mouvement indépendant. Ces instructions ne peuvent pas être programmées dans un axe avec un mouvement indépendant. Puissance objectif insuffisante pour le bon fonctionnement avec DMC. DÉTECTION CAUSE 3104 Au cours de l'exécution. Le DMC a détecté que la puissance instantanée (variable TV51 du régulateur) est supérieure à la puissance cible dans une plage fixée au préalable. Cela peut indiquer que l'outil est entré en collision avec la pièce, ce qui explique que la CNC arrête les axes sans arrêter la rotation de la broche. Vérifier l'état de l'outil et de l'usinage. La CNC permet de reprendre l'exécution en appuyant sur [START], entrer en mode inspection d'outil ou considérer comme achevée l'exécution. Instruction non compatible avec un mouvement indépendant actif. DÉTECTION CAUSE 3103 Au cours de l'exécution. Le DMC a détecté une consommation de puissance (variable TV51 du régulateur) excessive pendant un certain temps. Cela peut indiquer que l'outil est usé, détérioré ou est entré en collision avec la pièce. Réviser l'outil et/ou la programmation de la passe de pénétration et de la passe radiale. 'Puissance excessive dans la broche détectée pendant DMC. Appuyez sur MARCHE pour continuer' DÉTECTION CAUSE 3102 Au cours de l'exécution. On a tenté d'activer #PWRCTRL DUTY dans un canal sans avoir activé au préalable le PWM dans le même canal. Activer le PWM avant d'activer #PWRCTRL DUTY. 'Puissance excessive dans la broche détectée pendant DMC' DÉTECTION CAUSE 3101 Au cours de l'exécution. On a tenté d'activer #PWRCTRL OUT dans un canal, alors qu'il est actif dans un autre. Le #PWRCTRL OUT peut uniquement se trouver actif dans un canal. PWRCTRL DUTY exige PWM actif dans le même canal. DÉTECTION CAUSE 3100 Au cours de l'exécution. On a tenté d'activer #PWRCTRL DUTY dans un canal, alors qu'il est actif dans un autre. Le #PWRCTRL DUTY peut uniquement se trouver actif dans un canal. Au cours de l’exécution ou de la simulation d’un programme pièce. Pendant l'exécution en mode MDI. FCAS (Fagor Collision Avoidance System) a détecté une collision dans l'un des mouvements à exécuter ou à simuler. Revoir la programmation et modifier le programme pièce. S o l ut i o n s d ’ e r r e ur s . 3400 'Axe indépendant inexistant ou non disponible' DÉTECTION CAUSE SOLUTION 3401 'Came inexistante ou non disponible' DÉTECTION CAUSE SOLUTION 3402 SOLUTION SOLUTION SOLUTION Au cours de l'exécution. La synchronisation programmée implique dépasser l’avance maximum de l’axe. Programmer la synchronisation avec l’axe maître en se déplaçant à une avance inférieure ou programmer un ratio de synchronisation inférieur. 'La cote programmée pour l'axe indépendant est supérieure à la limite positive' DÉTECTION CAUSE SOLUTION 3408 Au cours de l'exécution. L’axe programmé dans l'instruction #MOVE INF a des limites de parcours définies. Supprimer les limites de logiciel ou interrompre le déplacement avant que l’axe n’atteigne la limite. 'La vitesse nécessaire pour synchroniser est supérieure à la maximale' DÉTECTION CAUSE SOLUTION 3407 Au cours de l'exécution. La CNC essaie d’exécuter une instruction #FOLLOW OFF mais il y a une opération en attente. Depuis le PLC interrompre les instructions en attente (marque ABORT) ou bien attendre l'espace pour l’emmagasiner (marque FREE). 'On n’admet pas #MOVE INF pour un axe avec limites' DÉTECTION CAUSE SOLUTION 3406 Au cours de l'exécution. La CNC essaie d’exécuter une opération d’axe indépendant mais il y a une synchronisation active. Ne pas programmer d’opérations d’axe indépendant avec des cames actives ni programmer deux synchronisations de suite. Depuis le PLC interrompre les instructions en attente (marque ABORT) ou bien attendre la fin de la synchronisation. 'On n’admet pas #FOLLOW OFF avec une autre opération en attente' DÉTECTION CAUSE 3405 Au cours de l'exécution. La CNC essaie d’exécuter une opération d’axe indépendant mais il y a déjà deux opérations en attente. Depuis le PLC interrompre les instructions en attente (marque ABORT) ou bien attendre l'espace pour l’emmagasiner (marque FREE). Pour savoir si l’interpolateur indépendant a terminé toutes les opérations, consulter la marque BUSY. 'Les opérations avec des axes indépendants sont interdites. En synchronisation' DÉTECTION CAUSE 3404 Au cours de l'exécution. Le numéro de came programmé dans l'instruction #CAM n’existe pas. Programmer une came correcte ou définir la came dans les paramètres machine. Les opérations avec des axes indépendants sont interdites. Tableau plein. DÉTECTION CAUSE 3403 Au cours de l'exécution. L’utilisateur a programmé une opération d’axe indépendant pour un axe qui n’est assigné à aucun canal ou est en train de changer de canal. Assigner l’axe indépendant à n’importe quel canal ou attendre à ce que la CNC termine l’échange d’axe. Au cours de l'exécution. La cote programmée dans l'instruction #MOVE est hors des limites de logiciel. Les axes doivent toujours être dans les limites de logiciel. Vérifier que les limites de logiciel sont correctes, qu’elles n’ont pas été modifiées depuis le programme pièce ou le PLC. 'La cote programmée pour l'axe indépendant est inférieure à la limite négative' DÉTECTION CAUSE SOLUTION Au cours de l'exécution. La cote programmée dans l'instruction #MOVE est hors des limites de logiciel. Les axes doivent toujours être dans les limites de logiciel. Vérifier que les limites de logiciel sont correctes, qu’elles n’ont pas été modifiées depuis le programme pièce ou le PLC. CNC 8070 (REF: 1901) ·139· S o l ut i o n s d ’ e r r e ur s . 3409 'L'axe n'est pas valable comme axe indépendant' DÉTECTION CAUSE SOLUTION 3410 'Le temps maximum permis pour synchroniser est dépassé' DÉTECTION CAUSE SOLUTION 3411 SOLUTION SOLUTION SOLUTION SOLUTION SOLUTION 3500 3501 Au cours du démarrage ou pendant l'exécution. L'accélération programmée a valeur zéro. Programmer une valeur positive pour l'accélération. 'Accélération linéaire du segment 1 supérieure à la maximale' DÉTECTION CAUSE SOLUTION ·140· Pendant l'exécution. La CNC ne peut pas exécuter le saut (#LEAP/#LEAPBEGIN) avec les données programmées. Réviser la programmation. 'Accélération linéaire du segment 1 inférieure ou égale à zéro' DÉTECTION CAUSE SOLUTION (REF: 1901) Au cours de l'exécution. Le PLC essaie d’effectuer une recherche de référence pendant que la CNC est en train d’en exécuter un autre. Le PLC doit attendre à ce que la CNC termine sa recherche de référence. LEAPFROG est impossible selon les cotes fournies. DÉTECTION CAUSE CNC 8070 Au cours de l'exécution. Dans la synchronisation de la came, l’axe maître et l’axe esclave ont des modules différents. Les deux axes doivent avoir le même module (paramètres MODUPLIM et MODLOWLIM égaux). 'La recherche de zéro indépendant n'est pas permisse dans l'exécution' DÉTECTION CAUSE 3417 Au cours de l'exécution. Dans la synchronisation en position, l’axe maître a un module et le ratio de transmission est différent de 1. Dans une synchronisation en position où l’axe maître a un module, le ratio de transmission doit avoir la valeur 1. Programmer un ratio de transmission de 1 ou une synchronisation en vitesse. 'On ne peut pas programmer la came pour des axes avec différente valeur de module' DÉTECTION CAUSE 3415 Au cours de l'exécution. Dans la synchronisation, le dénominateur du ratio de transmission a la valeur zéro. Le dénominateur du ratio ne peut pas valoir zéro. 'On ne peut pas synchroniser en position avec module et ratio différent de 1' DÉTECTION CAUSE 3414 Au cours de l'exécution. Un déplacement d’axe indépendant est programmé avec une synchronisation active et la somme des deux composants de vitesse dépasse la maximale permise de l’axe. Si la vitesse de l’axe maître est élevée, il faut programmer le déplacement supplémentaire avec une vitesse plus petite. 'On ne peut pas programmer dénominateur 0 en synchronisation' DÉTECTION CAUSE SOLUTION 3413 Au cours de l'exécution. La synchronisation n'atteint pas la position souhaitée dans le temps défini. Augmenter le temps de synchronisation, commencer la synchronisation à des vitesses plus semblables ou augmenter l’accélération de l’esclave. 'On essaie de dépasser la vitesse maximale MAXFEED' DÉTECTION CAUSE 3412 Au cours de l'exécution. La CNC essaie d’exécuter une opération d’axe indépendante dans laquelle intervient un axe qui dépend d’autres axes ou duquel dépendant d’autres axes (par exemple des axes gantry, accouplés ou faisant partie d'une transformation) ou bien parce qu’il s’agit d’un axe afficheur ou d’un module et la limite inférieure du module est négative. Désactiver le couplage ou les transformations existantes. Au cours du démarrage ou de l'exécution. L'accélération programmée est supérieure à la maximale. Programmer une valeur inférieure à la maximale pour l'accélération. S o l ut i o n s d ’ e r r e ur s . 3502 'Accélération linéaire du segment 2 inférieure ou égale à zéro' DÉTECTION CAUSE SOLUTION 3503 'Accélération linéaire du segment 2 supérieure à la maximale' DÉTECTION CAUSE SOLUTION 3504 SOLUTION SOLUTION Au cours de l'exécution. La vitesse programmée pour la broche dépasse la vitesse maximale définie dans les paramètres machine pour la gamme active. Vérifier le paramètre G00FEED de broche. 'Il est impossible de déplacer la broche en mode de visualisation' DÉTECTION CAUSE SOLUTION 3603 Au cours de l'exécution. Il n’y a pas de vitesse de positionnement de broche programmée. Vérifier la programmation et que les paramètres REFFEED2 et G00FEED de la gamme active de la broche soient différents de zéro. 'Vitesse de broche programmée supérieure à la limite maximale' DÉTECTION CAUSE 3602 Pendant l’exécution de la commande d’analyses de fréquences. La vitesse additive est inférieure à celle résultant pour la fréquence maximum. Réduire la fréquence maximale ou programmer une vitesse additive supérieure. 'Vitesse de broche nulle' DÉTECTION CAUSE SOLUTION 3601 Au cours de l'exécution. Dépassement d'accélération dans cette trajectoire. Contacter Fagor. 'Fréquence trop grande pour la vitesse programmée' DÉTECTION CAUSE SOLUTION 3600 Pendant l’exécution de la commande d’analyses de fréquences. La fréquence est trop grande pour l’amplitude programmée. Réduire la fréquence maximale ou réduire l'amplitude. 'Limite d'accélération surpassée' DÉTECTION CAUSE SOLUTION 3508 Au cours de l'exécution. Dépassement de jerk dans cette trajectoire. Contacter Fagor. 'La limite de Jerk va être dépassée' DÉTECTION CAUSE SOLUTION 3507 Au cours du démarrage ou de l'exécution. La vitesse programmée pour le changement d’accélération est supérieure à la maximale. Programmer une vitesse inférieure à la maximale. 'Limite de jerk surpassée' DÉTECTION CAUSE SOLUTION 3506 Au cours du démarrage ou de l'exécution. L'accélération programmée est supérieure à la maximale. Programmer une valeur inférieure à la maximale pour l'accélération. 'Vitesse de changement d'accélération supérieure à la maximale' DÉTECTION CAUSE 3505 Au cours du démarrage ou pendant l'exécution. L'accélération programmée a valeur zéro. Programmer une valeur positive pour l'accélération. Pendant l'exécution. La CNC essaie de commander une broche qui se trouve en mode de visualisation. La CNC ne peut pas commander les broches actives en mode de visualisation. Pour déplacer l’axe, désactiver le mode de visualisation (marque DRO(axis) du PLC) et vérifier l’état de la marque SERVOON de la broche. CNC 8070 'La position de la broche commandée excède le rang du module' DÉTECTION CAUSE SOLUTION Au cours de l'exécution. La CNC est en train d’essayer de positionner la broche sur une cote qui est hors de la gamme permise (paramètres MODUPLIM et MODLOWLIM). Vérifier les paramètres MODUPLIM et MODLOWLIM. (REF: 1901) ·141· S o l ut i o n s d ’ e r r e ur s . 3604 'Sens du positionnement de broche contraire à celui du paramètre machine' DÉTECTION CAUSE SOLUTION 3605 'Sens de rotation de broche contraire à celui du paramètre machine' DÉTECTION CAUSE SOLUTION 3606 SOLUTION SOLUTION SOLUTION SOLUTION SOLUTION 3612 DÉTECTION CAUSE 3700 Au cours de l'exécution. Le PLC a activé la marque SPDLEREV sur une broche qui est synchronisée, que ce soit comme maître ou comme esclave. Désactiver la marque SPDLEREV du PLC. 'Limite de parcours de l’axe dépassées (PLC)' DÉTECTION CAUSE SOLUTION ·142· Au cours de l'exécution. La broche maître ou esclave n’est pas dans la gamme adéquate, paramètre SYNCSET ou paramètre CAXSET si la broche maître est comme axe C. Changer la gamme de la broche maître et/ou esclave dans son canal ou passer la broche maître au canal de l’esclave pour que le changement de gamme soit automatique. SPDLEREV n'est pas acceptée si la broche est synchronisée ou en M19. SOLUTION (REF: 1901) Au cours de l'exécution. Une instruction #SERVO ON est programmée pour une broche qui est en M19. L'instruction #SERVO OFF annule l'instruction #SERVO ON et ouvre la boucle. Si la broche est en M19, l'instruction #SERVO OFF ne peut pas ouvrir la boucle; pour ouvrir la boucle, programmer M3, M4, M5 ou faire une RAZ. 'La broche master de la synchronisation ne se trouve pas dans la gamme adéquate (SYNCSET ou CAXSET)' DÉTECTION CAUSE CNC 8070 Au cours de l'exécution. Une instruction #SERVO ON est programmée pour une broche qui n’est pas référencée. Effectuer une recherche de référence de la broche avec M19 ou G74 avant d’utiliser l’instruction #SERVO ON. 'On ne peut pas ouvrir la boucle étant en M19 ou en synchronisation' DÉTECTION CAUSE SOLUTION 3611 Au cours de l'exécution. Le PLC a activé la marque PLCCNTL sur une broche qui est synchronisée, que ce soit comme maître ou comme esclave. Désactiver la marque PLCCNTL du PLC. 'On ne permet pas # SERVO ON si on n'a pas cherché préalablement le zéro de la broche' DÉTECTION CAUSE 3610 Au cours de l'exécution. La CNC a essayé de réaliser une synchronisation pendant que la marque PLCCNTL est active. Désactiver la marque PLCCNTL du PLC. 'On n’admet pas PLCCNTL si la broche est synchronisée' DÉTECTION CAUSE 3609 Au cours de l'exécution. Après une rotation de la broche en boucle ouverte, le positionnement doit être en cotes absolues. Programmer le positionnement en cotes absolues. 'On ne peut pas synchroniser la broche avec PLCCNTL actif' DÉTECTION CAUSE 3608 Au cours de l'exécution. La rotation programmée exige un déplacement de la broche dans le sens contraire à celui indiqué par paramètre machine avec UNIDIR. Vérifier la programmation et le paramètre machine UNIDIR de la broche. 'Le positionnement de la broche exige une cote absolue' DÉTECTION CAUSE 3607 Au cours de l'exécution. Le positionnement programmé demande un déplacement de la broche dans le sens contraire à celui indiqué par paramètre machine avec UNIDIR. Vérifier la programmation et le paramètre machine UNIDIR de la broche. Au cours du déplacement de l'axe. Le PLC a essayé de dépasser les limites de parcours. Réviser la programmation. S o l ut i o n s d ’ e r r e ur s . 3701 'La position de référence dépasse les limites de logiciel' DÉTECTION CAUSE SOLUTION 3702 'Erreur de suivi de l’axe hors limites' DÉTECTION CAUSE SOLUTION 3703 SOLUTION SOLUTION SOLUTION SOLUTION SOLUTION Au cours de l'exécution. Le temps nécessaire pour que l’axe rentre dans la fenêtre d’arrêt, pour que la CNC le considère en position, dépasse le temps défini dans le paramètre INPOMAX. Régler le paramètre INPOMAX. 'Erreur dans le rafraîchissement des entrées analogiques' DÉTECTION CAUSE SOLUTION 3710 Au cours de la recherche de référence. Erreur dans le processus de recherche de référence. Cela peut être du à un mauvais paramétrage de l’axe, à un défaut dans le module de comptage ou dans l'asservissement Sercos, dans le système de mesure ou à une erreur dans le branchement. Vérifier les paramètres en rapport avec la recherche de référence, l’état du module de comptage ou de l'asservissement Sercos, le système de mesure ou le branchement. 'Temps maximum dépassé pour rentrer dans la fenêtre d'arrêt' DÉTECTION CAUSE 3709 Pendant l’initialisation du palpeur. L'entrée numérique affectée au palpeur n'est pas valide. Vérifier les paramètres du palpeur. 'Erreur dans la recherche de zéro' DÉTECTION CAUSE 3708 Au cours de l'exécution. La CNC a perdu la référence de la broche dans la transition de boucle ouverte à boucle fermée. Contacter votre fournisseur. 'Erreur dans l'opération avec palpeur' DÉTECTION CAUSE SOLUTION 3707 Au cours du déplacement de l'axe. L’axe a dépassé la cote définie par le paramètre machine LIMIT- ou par la variable V.A.RTNEGLIMIT.xn. Réviser la programmation. 'La recherche de zéro est nécessaire' DÉTECTION CAUSE 3706 Au cours du déplacement de l'axe. L’axe a dépassé la cote définie par le paramètre machine LIMIT+ ou par la variable V.A.RTPOSLIMIT.xn. Réviser la programmation. 'Limite négative de logiciel dépassée' DÉTECTION CAUSE 3705 Pendant l'exécution. L’axe a dépassé l’erreur de poursuite permise définie dans les paramètres machine (MAXFLWE, MINFLWE, FEDYNFAC, ESTDELAY). Cela peut être du à un mauvais réglage de l’axe, à ce qu’il faille activer l’axe, à un défaut dans le moteur, dans l'asservissement, dans le système de mesure et/ou dans la mécanique. Réviser les paramètres machine, le réglage de l’axe, le branchement, l’état de l'asservissement et le système mesure-moteur. 'Limite positive de logiciel dépassée' DÉTECTION CAUSE 3704 Au cours de la validation de paramètres machine. La valeur du paramètre REFVALUE dépasse les limites de logiciel de l'axe. Vérifier le paramètre REFVALUE et les limites de logiciel. Pendant la lecture d’entrées analogiques. Défaut dans le processus cyclique de lecture d’entrées analogiques. Cela peut être du à des problèmes dans la COMPCI, le bus CAN, le module d’entrées analogiques, etc. Vérifier l’état du bus CAN, des modules d’entrées analogiques, le branchement, etc. 'Rang de valeurs de la consigne de position dépassé' DÉTECTION CAUSE SOLUTION CNC 8070 (REF: 1901) Au cours de l'exécution. Overflow dans la variable de la consigne de position. Vérifier le paramétrage de l'axe. ·143· S o l ut i o n s d ’ e r r e ur s . 3711 'Erreur dans le rafraîchissement de comptages CAN' DÉTECTION CAUSE SOLUTION 3712 'Micro de l'axe maître appuyé pendant la recherche de zéro de l'axe esclave' DÉTECTION CAUSE SOLUTION 3713 SOLUTION SOLUTION SOLUTION SOLUTION SOLUTION 3718 ·144· Au cours de l'exécution. Le codeur de l’axe ou de la broche a dépassé la vitesse de rotation maximale permise. En dépassant cette limite, l’axe ou broche a perdu le point de référence, par conséquent les cotes lues ne sont pas correctes. Effectuer une recherche de référence machine pour travailler en boucle fermée. 'RAZ pour stationner les axes en déplacement ou de la transformation / couplage actif' DÉTECTION CAUSE (REF: 1901) Au cours du déplacement d'un axe ou broche. Sur les axes Sercos vitesse, la CNC envoie la consigne au régulateur en dix millièmes de t/min. La valeur de la consigne a dépassé la plage autorisée. Même si la vitesse programmée ne dépasse pas G00FEED, la consigne envoyée à l'asservissement après avoir appliqué Kv dépasse la vitesse maximale permise. Vérifier les paramètres machine PITCH, INPUTREV, OUTPUTREV et PROGAIN. Limiter la vitesse maximale (paramètre G00FEED) à la valeur indiquée par le warning pour éviter le dépassement. Seuil de comptage de l'encodeur dépassé. Rechercher zéro pour récupérer la cote. DÉTECTION CAUSE CNC 8070 Au cours du déplacement d'un axe rotatif ou broche. Sur les axes Sercos position, la CNC maintient le comptage de la compensation de module de façon absolue; si tous les déplacements de l’axe se réalisent dans le même sens, la CNC accumule la compensation. Réaliser une recherche de référence machine. 'Consigne de vitesse maximale dépassée' DÉTECTION CAUSE 3717 En cours de stationnement d'un axe ou broche depuis le PLC. Le PLC essaie de stationner un axe faisant partie d’un couple gantry ou un axe ou broche faisant partie d’un couple tandem. Ces axes ou ces broches ne peuvent pas être stationnés, ni depuis le PLC ni depuis la CNC. Supprimer le signal de stationner l’axe ou broche depuis PLC. 'Dépassement dans la compensation de module' DÉTECTION CAUSE 3716 Au cours de l'exécution. La CNC n’a pas pu initialiser la commande de couple supplémentaire parce que l’information d’un paramètre n’est pas disponible. Définir et valider les paramètres machine de l’axe tandem ou activer l’axe esclave et remettre la CNC à zéro. 'Les axes gantry ou tandem ne peuvent pas être stationnés' DÉTECTION CAUSE 3715 Au cours de l'exécution. Pendant la recherche de référence d’un axe gantry, la CNC a détecté le micro de l’axe maître avant celui de l’axe esclave. Régler la position des micros des axes gantry; l’axe esclave doit être le premier à activer le micro. 'Le contrôle tandem n'est pas actif' DÉTECTION CAUSE 3714 Pendant la lecture des comptages d’axes analogiques. Si l'erreur indique le nom de l'axe, la CNC n'a pas achevé la lecture des comptages de cet axe. Si l’erreur n’affiche le nom d’aucun axe, la CNC ne complète pas le rafraîchissement cyclique des compteurs. L’erreur peut être due à une erreur dans le bus CAN, à un défaut dans un comptage, dans le module de comptage ou à la saturation du bus CAN. Vérifier la connexion et la configuration du bus CAN, le module de comptage ou augmenter le paramètre LOOPTIME en cas de saturation dans le bus. SOLUTION En cours de stationnement d'un axe depuis le PLC. Le PLC essaie de stationner un axe en déplacement, faisant partie de la cinématique active, d’un axe angulaire actif, du contrôle tangentiel active ou d’une transformation de coordonnées #CS ou #ACS. Le PLC ne peut pas stationner un axe dans cette situation. Taper sur RAZ pour arrêter le déplacement ou désactiver la cinématique active, l’axe angulaire actif, le contrôle tangentiel actif ou la transformation de coordonnées #CS ou #ACS. S o l ut i o n s d ’ e r r e ur s . 3719 'RAZ pour stationner broches en déplacement ou G33/G34/G63/G95/G96/#CAX/#SYNC' DÉTECTION CAUSE SOLUTION 3720 'Palpeur non disponible. Occupé par un autre processus' DÉTECTION CAUSE SOLUTION 3723 SOLUTION SOLUTION SOLUTION Au cours de la désactivation de la marque SWITCH de l'axe. La CNC a essayé de désactiver un axe d’un groupe multiple avant que l’axe ne soit en position, c’est-à-dire, avec déplacement en attente. Dans la manœuvre du PLC, conditionner la désactivation de l’axe à ce que celui-ci soit en position, c’est-à-dire pas en déplacement. 'Il est interdit l'axe multiple avec une commande en exécution dans l'asservissement, SWITCH' DÉTECTION CAUSE SOLUTION 3729 Au démarrage du déplacement d'un axe tandem. La CNC a essayé de déplacer l’axe maître du tandem sans attendre à ce que l’axe esclave soit activé. Dans la manœuvre du PLC, conditionner la permission du déplacement pour que les deux axes du tandem soient activés. 'Il est interdit de désactiver un axe multiple sans entrer en position' DÉTECTION CAUSE 3728 Au cours de l'exécution. La CNC a détecté la fonction G174 pour un axe qui n’est pas synchronisé. Réviser la programmation. Pour forcer la cote d'un axe (G174) il faut que l'axe ne soit pas synchronisé avec un autre. Désynchroniser l’axe avant de forcer la cote ou vérifier dans le programme de PLC la logique de la marque INSYNC de l’axe. 'Absence de Drive Status Ready (DRSTAF/DRSTAS) de l'axe esclave du tandem' DÉTECTION CAUSE 3727 Au cours de l'exécution. La CNC a détecté la fonction G174 pour un axe qui n’est pas en position. Réviser la programmation. Pour forcer la cote d’un axe (G174), l’axe doit être en position, c’est-à-dire, pas en déplacement et avec sa marque INPOS(axis) active. 'G174 interdite pour un axe synchronisé' DÉTECTION CAUSE SOLUTION 3726 Au cours de l'exécution. La CNC a détecté la fonction G174 pour un axe qui est en mode de visualisation (marque DRO). Réviser la programmation. Pour forcer la cote d’un axe (G174), celui-ci ne peut pas être en mode de visualisation ; c’est-à-dire, il faut désactiver sa marque DRO(axis) et activer sa marque SERVO(axis)ON. 'G174 est interdite si l'axe n'est pas en position' DÉTECTION CAUSE SOLUTION 3725 Au cours de l'exécution. La CNC a essayé d’exécuter un palpage mais le palpeur est utilisé par un processus antérieur (G100 ou commande TOUCHPROBE). Attendre la fin d’un palpage avant d’exécuter le suivant. 'G174 interdite pour l'axe sous le mode de visualisation' DÉTECTION CAUSE 3724 En cours de stationnement d'un axe depuis le PLC. Le PLC essaie de stationner une broche en déplacement, synchronisée, activée comme axe C ou avec unes des fonctions G33, G34, G63, G95 ou G96 active. Le PLC ne peut pas stationner une broche dans cette situation. Taper sur RAZ pour arrêter le déplacement, la synchronisation, désactiver l’axe C ou désactiver les fonctions G33, G34, G63, G95 ou G96. Au cours de la désactivation de la marque SWITCH de l'axe. La CNC a essayé de désactiver un axe d’un groupe multiple avant que ne termine une commande Sercos pour stationnement, arrêt de stationnement ou de changement de gamme ou de set. Dans la manœuvre du PLC, conditionner la désactivation de l’axe à ce que la manœuvre de stationnement, arrêt de stationnement ou changement de gamme ou de set ait terminé. 'Il n'est permis qu'un axe du groupe multiple actif' DÉTECTION CAUSE SOLUTION Au cours de la désactivation de la marque SWITCH de l'axe. La CNC a essayé d’activer un axe d’un groupe multiple avant de désactiver l’axe précédent. Dans la manœuvre du PLC, désactiver d’abord le dernier axe actif puis activer le nouvel axe. CNC 8070 (REF: 1901) ·145· S o l ut i o n s d ’ e r r e ur s . 3730 'TOUCHPROBE: Le flanc sélectionné va être ignoré car il est différent de l'actif' DÉTECTION CAUSE SOLUTION 3731 'G174: Déplacement non valide, valeur trop grande' DÉTECTION CAUSE SOLUTION 3734 SOLUTION SOLUTION 3740 (REF: 1901) Pendant l'exécution. Avec le contrôle du gap actif, la CNC lit une distance supérieure au maximum possible (paramètre GAPDISTLIMIT). Les possibles causes sont les suivantes: • La sonde fonctionne mal. • Le signal reçu par la CNC ne provient pas de la sonde (sonde mal connectée). • La sonde est mal paramétrée (paramètres GAPDISTLIMIT et GAPVOLTLIMIT). Revoir la connexion et le paramétrage de la sonde. Si l'erreur persiste, contacter votre fournisseur. ENABLEGAP: #GAPCTRL ne peut pas être activé, car il est trop différent du GAP programmé. DÉTECTION CAUSE SOLUTION ·146· Au cours du démarrage de la CNC. La cote absolue de l'asservissement ne correspond pas à la cote enregistrée dans la dernière session de CNC. L'axe a fait un déplacement supérieur à celui indiqué dans le paramètre MAXDIFREF. Vérifier si la position de l'axe est correcte. Erreur au niveau du signal de la sonde pendant le processus de #GAPCTRL. DÉTECTION CAUSE CNC 8070 Pendant l'exécution de découpe au laser (PWM). Le hardware n’est pas préparé pour la performance PWM. Vérifier qu’il n’y a pas de carte d'expansion type Sercos, avec les 2 premières sorties locales prêtes pour la commutation rapide. Le logiciel ID de la FPGA d'expansion doit être égal ou supérieur à 1.3, et son hardware ID égal ou supérieur à 1.2. 'L'axe est déplacé avec la CNC mise hors tension' DÉTECTION. CAUSE 3739 Pendant l'exécution de découpe au laser (PWM). Le paramètre PWMOUTPUT ne peut pas prendre la valeur 0. Affecter au paramètre PWMOUTPUT une valeur dans la gamme (1-2). 'Carte d'expansion incompatible avec PWM' DÉTECTION CAUSE SOLUTION 3738 Pendant l'exécution de découpe au laser (PWM). Le paramétrage du PWM est incorrect. Vérifier les conditions suivantes: • Le paramètre NLOCOUT doit être 8. • Le paramètre PWMOUTPUT ne peut pas être supérieur à 2 (1, 2). 'Le paramètre machine PWMOUTPUT est 0' DÉTECTION CAUSE SOLUTION 3737 Au cours du démarrage de la CNC. La CNC n'a pas active l'option de logiciel pour la performance PWM. Convenir l'option correspondante. 'Erreur dans l'activation/désactivation du PWM' DÉTECTION CAUSE SOLUTION 3736 Au cours de l'exécution de G174. En calculant le déplacement programmé en unités de l'asservissement, on obtient une valeur hors de la gamme admise par l'asservissement. Modifier la valeur programmée dans G174. 'Option de logiciel PWM non autorisée' DÉTECTION CAUSE SOLUTION 3735 Lorsque le PLC exécute une commande TOUCHPROBE. Le PLC a essayé d’activer un palpage, mais le palpeur est utilisé par une commande TOUCHPROBE antérieure et les deux commandes utilisent des flancs différents. Dans des opérations de palpage simultanées sur différents axes, il est obligatoire de sélectionner le même flanc de palpage ou bien d’effectuer les palpages avec des palpeurs différents. Pendant l'exécution. Le contrôle du gap est actif (#GAPCTRL), mais il est désactivé pour le PLC (indique ENABLEGAP). La CNC ne peut pas activer le contrôle du gap, car la sonde se trouve hors du gap. Rapprocher la sonde du gap programmé. S o l ut i o n s d ’ e r r e ur s . 3741 #GAPCTRL : hors plage [GAPMAX - GAPMIN]. DÉTECTION CAUSE SOLUTION 3742 #GAPCTRL : hors plage GAPTOL. DÉTECTION CAUSE SOLUTION 3744 SOLUTION Pendant l'exécution du PWM. Le hardware n’est pas préparé pour la performance PWM. Vérifier que la CNC dispose de 2 sorties numériques locales préparées pour la commutation rapide. Différence de position supérieure à MAXDIFREF. Appuyer sur ENTER + RESET pour confirmer. DÉTECTION CAUSE SOLUTION 3800 Pendant l'exécution de la coupe en grille. Le hardware n’est pas préparé pour la prestation « Commutation synchronisée ». Vérifier que la CNC dispose de 2 sorties numériques locales préparées pour la commutation rapide. Hardware non-compatible avec PWM. DÉTECTION CAUSE SOLUTION 3753 Au cours de l'exécution. Le PLC a indiqué à travers la marque GAPCOLLISION qu'une collision s'est produite avec le capteur. Pour éviter la collision avec la tôle, réduire l'avancée. Si l'erreur persiste, l'OEM il faudra modifier le paramètre machine GAPCOLLISIONMODE. Hardware non-compatible avec SWT. DÉTECTION CAUSE SOLUTION 3748 Au cours de l'exécution. Aucun signal du capteur qui permet à la CNC de calculer la distance. Vérifier les connexions du capteur et les paramètres machine liés à ce dernier (GAPANAINTYPE et GAPAANAINID). Le capteur est entré en collision. DÉTECTION CAUSE 3747 Pendant l'exécution. Le gap a dépassé la tolérance autorisée pour considérer comme achevé le mouvement d'approche. Réviser la programmation. Modifier la valeur du paramètre GAPTOLCANCEL pour que la CNC n'affiche pas une erreur. #GAPCTRL: Aucun signal du capteur. DÉTECTION CAUSE SOLUTION 3745 Pendant l'exécution. Le gap a dépassé les valeurs maximales ou minimales autorisées, définies par GAPMAX ou GAPMIN. Il est possible que le capteur ne fournissent pas une lecture adéquate. Réviser la programmation. Modifier la valeur du paramètre GAPERRORCANCEL pour que la CNC n'affiche pas une erreur. Au cours du démarrage de la CNC. La cote absolue du capteur ne correspond pas à la cote enregistrée dans la dernière session de la CNC. Les possibles solutions sont les suivantes: • Vérifier que la position de l'axe indiquée dans « Cota actuelle » est correcte. Si c'est le cas, appuyer sur [ENTER], puis sur [RESET] pour éliminer l'erreur et continuer. Si la position de l'axe est erronée, il est possible qu'une erreur soit survenue dans le capteur. • Si la position que devrait présenter l'axe n'est pas « Cote actuelle » mais « Cote prévue », éliminer l'erreur en appuyant sur [ENTER]", puis sur [RESET]". Exécuter ensuite G174 avec la position indiquée dans « Cote prévue », puis redémarrer la CNC pour récupérer ladite position. CNC 8070 'Vitesse en jog continu égale à zéro' DÉTECTION CAUSE SOLUTION Au cours de l’exécution ou changement du mode à jog continu. L’avance pour le mode jog continu est zéro. Aucune avance n'est programmée pour le mode manuel et le paramètre machine JOGFEED est zéro. Définir une nouvelle avance depuis le mode manuel. Vérifier le paramètre machine d'axes JOGFEED. (REF: 1901) ·147· S o l ut i o n s d ’ e r r e ur s . 3801 'Distance ou vitesse en mode jog incrémental égale à zéro' DÉTECTION CAUSE SOLUTION 3802 'Vitesse en jog incrémental trop petite' DÉTECTION CAUSE SOLUTION 3803 CAUSE SOLUTION SOLUTION CAUSE SOLUTION SOLUTION SOLUTION SOLUTION CNC 8070 DÉTECTION CAUSE 3810 Au cours de l'exécution. La CNC a essayé de déplacer un axe en jog continu ou incrémental avec la fonction G95 active et vitesse zéro sur la broche utilisée pour la synchronisation. Programmer une vitesse pour la broche maître du canal ou pour la broche utilisée pour la synchronisation (registre SYNC). 'Le mode Manivelle n'est pas permis avec l'axe Hirth' DÉTECTION CAUSE SOLUTION ·148· Au cours de l'exécution. Les possibles causes sont les suivantes: • L’axe n’était pas en mode manuel en abandonnant ce mode. • La CNC a détecté la fonction G101 ou G102 pour l'axe esclave d'un couple gantry. Pour en sortir du mode manuel il faut taper sur RAZ. Les fonctions G101 et G102 doivent être programmées pour l’axe maître du couple gantry. 'Vitesse programmée de broche nulle sur G95' SOLUTION (REF: 1901) Au cours de l'exécution. Le PLC a essayé de sélectionner une position de jog incrémental qui est hors de la gamme permise. Vérifier dans le programme de PLC l'écriture de la variable (V.)PLC.INCJOGIDX. 'Axe inexistant ou non disponible' DÉTECTION CAUSE 3809 Au cours de l'exécution. La vitesse définie en paramètres machine pour jog incrémental est supérieure à la maximale permise. Repasser les paramètres machine MAXMANFEED, INCJOGFEED et G00FEED. 'Indice de jog incrémental hors de rang (positions du commutateur 1-5)' DÉTECTION CAUSE 3808 Pendant un changement dans l’avance ou dans la distance à parcourir en jog incrémental. La position de jog incrémental sélectionné depuis le commutateur ou PLC est zéro. Vérifier les paramètres machines des axes INCJOGDIST et INCJOGFEED. 'Vitesse de jog incrémental supérieure à la valeur maximale' DÉTECTION CAUSE 3807 Pendant un changement dans la résolution de manivelle. Le PLC a essayé de sélectionner une position manivelle qui est hors de la gamme permise. Vérifier dans le programme de PLC l'écriture de la variable (V.)PLC.MPGIDX. 'Vitesse ou distance zéro en mode jog incrémental' DÉTECTION 3806 Pendant un changement dans la résolution de la manivelle depuis le panneau de commande. La position de manivelle sélectionnée depuis le commutateur ou PLC a une résolution de zéro associée. Vérifier le paramètre machine d'axes MPGRESOL. 'Indice de manivelle hors de rang (positions du commutateur 1-3)' DÉTECTION CAUSE 3805 Au cours de l'exécution. L’incrément de position calculé pour un cycle de PLC est trop petit. Vérifier les paramètres machine des axes INCJOGFEED et LOOPTIME. 'La résolution de manivelle zéro est interdite' DÉTECTION 3804 Au cours de l'exécution. L’avance ou la distance à se déplacer en jog incrémental est zéro. Aucune avance n’est programmée pour le mode manuel et le paramètre machine INCJOGFEED est zéro ou le paramètre machine INCJOGDIST est zéro. Définir une nouvelle avance depuis le mode manuel. Vérifier les paramètres machine des axes INCJOGFEED et INCJOGDIST. Au cours de l'exécution. LA CNC a essayé de sélectionner l'axe Hirth pour le déplacer sous le mode manivelle. Il n’est pas permis de déplacer un axe Hirth en mode manivelle ; on peut le déplacer en mode jog continu et jog incrémental. S o l ut i o n s d ’ e r r e ur s . 3811 'La limite d'incrément de la manivelle est dépassée' DÉTECTION. CAUSE SOLUTION 3812 Sous le mode manuel, pendant la lecture du comptage d'une manivelle. Incrément trop grand dans le comptage de la manivelle. Vérifier la mesure connectée à l’entrée de manivelle, les niveaux du signal, la fréquence, etc. 'Erreur dans le rafraîchissement des manivelles' DÉTECTION. CAUSE SOLUTION Sous le mode manuel, pendant la lecture du comptage d'une manivelle. Lecture incorrecte de la manivelle. En fonction du type de manivelle (clavier CAN, compteur CAN, local, module RCS.S, etc.), vérifier la cohérence et le niveau de communication du bus correspondant ainsi que le paramétrage et la connexion de l’entrée de mesure. CNC 8070 (REF: 1901) ·149· S o l ut i o n s d ’ e r r e ur s . 4000-4999 4000(1) 'Erreur dans l'initialisation de l'anneau Sercos' CLASSE CAUSE SOLUTION 4000(2) 'Erreur dans l'initialisation de l'anneau Sercos' CLASSE TRANSITION CAUSE SOLUTION 4000(3) (REF: 1901) ·150· 1. 0. Timeout dans l'initialisation de l'anneau Sercos. Contacter le service d'assistance technique. 'Erreur dans l'initialisation de l'anneau Sercos' AXE TRANSITION 1. TRANSITION 2. CNC 8070 0. Erreur dans la phase d'initialisation du chip. La CNC ne détecte pas la carte Sercos ou overflow dans la DPRAM du SERCON en raison d’un nombre excessif d’axes et de données à transmettre dans le canal cyclique. Vérifier que la carte est installée et que la CNC la détecte correctement. Si l’erreur persiste, veuillez contacter le service après-vente. Nom de l'axe avec erreur. ID Sercos qui provoque l'erreur. Consulter le manuel de l'asservissement. Point de la séquence d’initialisation où se produit l’erreur. Point. Signification. 0 Timeout. 1 Erreur en changeant à la phase 0. (Problème dans la fibre optique) 2 Erreur en changeant à la phase 1. (Un asservissement ne répond pas; défaut de hardware ou sélecteur de nœud mal placé). 3 Erreur en changeant à la phase 2. 4 Erreur dans la lecture de la version du fabricant. 5 Erreur dans la lecture de T1mim. 6 Erreur dans la lecture de Tatmt. 7 Erreur dans la lecture de T4min. 8 Erreur dans la lecture de Tmtsy 9 Erreur dans la lecture de Tmtsg. 10 Erreur dans la lecture de SlaveNr. 11 Erreur dans la lecture de Tatat. 12 Erreur dans le calcule de temps. 13 Erreur dans l'écriture du mot de passe de fabricant. 14 Erreur dans l'écriture de T1. 15 Erreur dans l'écriture de T4. 16 Erreur dans l'écriture de T3. 17 Erreur dans l'écriture de T2. 18 Erreur dans l'écriture de Tncyc. 19 Erreur dans l'écriture de Tscyc. 20 Erreur dans l'écriture de MDTlen. 21 Erreur dans l'écriture de TelegramType. 22 Erreur dans l'écriture de MDT List. S o l ut i o n s d ’ e r r e ur s . VALEUR 1 Point. Signification. 23 Erreur dans l'écriture de AT List. 24 Erreur dans l'écriture de MDT Offset 25 Erreur dans l'écriture de RealTime Control Bit 1. 26 Erreur dans l'écriture de RealTime Control Bit 2. 27 Erreur dans l'écriture de RealTime Status Bit1. 28 Erreur dans l'écriture de OpMode. 29 Erreur dans la commande Reset. 30 Erreur dans la commande Park. 31 Erreur dans la commande Phase 3. 32 Erreur en changeant à la phase 3. 33 Erreur dans la commande Phase 4. 34 Erreur en changeant à la phase 4. 35 Erreur dans la lecture de Class Diagnostics 1. 36 Erreur par défaut. 37 Erreur dans la lecture de Tncyc. 38 Erreur dans la lecture de OpMode. 39 Erreur dans la lecture de AxisType. 40 Erreur dans la lecture de G00Feed. 41 Erreur dans la lecture de Monit Window. 42 Erreur dans la lecture de SP100. 43 Erreur dans la lecture de KV. 44 Erreur dans la lecture de Checksum. 45 Erreur dans la lecture de DV33. 46 Erreur dans l'écriture de DV33. 47 Erreur dans la lecture d'attributs des variables Sercos. 48 Erreur dans la reconfiguration de MTD et AT. 49 Erreur dans la lecture de MP2. 50 Erreur dans la lecture de MP3. 51 Erreur dans l’écriture des paramètres d’homogénéisation. 52 Erreur dans la lecture de PP55. 53 Erreur dans la lecture de PP115. 54 Erreur dans la lecture de PP147. 55 Erreur dans la lecture de Checksum. 56 Erreur dans la lecture de MP244. 57 Erreur dans la lecture de RP77. 58 Erreur dans la lecture de PP76. 59 Erreur dans la lecture de GV9. 60 Erreur dans la lecture de SP10. Erreurs dans le driver Sercos. Erreur. Signification. 0 SERC_NO_ERROR 1 ERROR_PHASE_CHANGE 5 Demande de Abort/Suspend/Resume d'une commande non active. 7 Numéro d'axe logique incorrect. 0x0040 READY_FOR_SCDATA 0x0080 ERROR_DEFAULT CNC 8070 (REF: 1901) ·151· S o l ut i o n s d ’ e r r e ur s . CNC 8070 VALEUR 2 CAUSE SOLUTION (REF: 1901) ·152· Erreur. Signification. 0x0101 NOT_READY 0x0102 BUSYTIMEOUT 0x0201 ERROR_ATMISS 0x0202 ERROR_NERR 0x0203 ERROR_MSTMISS 0x0204 ERROR_DISTORSION 0x0205 ERROR_FIBRA_ROTA 0x0400 ERROR_SCTRANS 0x0801 ERROR_SCTRANSNODATA 0x0802 ERROR_SCNODATA 0x0803 NOT_READY_FOR_SCDATA 0x1002 ERROR_DPRAMOVERFLOW 0x1004 ERROR_SCNOTINIT 0x1008 ERROR_WRONGCHANNELNUMBER 0x2001 ERROR_WRONGPHASE 0x2002 ERROR_WRONGADDRESS 0x2004 ERROR_WRONGATNUMBER 0x2008 ERROR_SCTRANSNOTREADY 0x4000 ERROR_CALCULATE_T1 0x4001 ERROR_CALCULATE_T2 0x4002 ERROR_CALCULATE_T3 0x4004 ERROR_CALCULATE_T4 0x4008 ERROR_CALCULATE_TEND 0x7002 Erreur dans le canal de service: Longueur de la variable inférieure. 0x7003 Erreur dans le canal de service: Longueur de la variable supérieure. 0x7004 Erreur dans le canal de service: Variable sans permission de lecture. 0x7005 Erreur dans le canal de service: Variable sans permission de lecture dans la phase actuelle. 0x7006 Erreur dans le canal de service: La valeur de la variable est inférieure à celle permise. 0x7007 Erreur dans le canal de service: La valeur de la variable est supérieure à celle permise. 0x7008 Erreur dans le canal de service: Variable invalide. 0x7009 Erreur dans le canal de service: Accès à variable protégée par mot de passe. 0x700A Erreur dans le canal de service: Variable configurée dans le canal cyclique. 0x8001 ERROR_HSTIMEOUT 0x8002 ERROR_SCHSTIMEOUT 0x8004 SERC_ERROR_TIMEOUT Sans utilisation actuellement. Défaut dans le processus d’initialisation de l'anneau Sercos à cause de problèmes de connexion dans la fibre optique, paramétrage dans la CNC et l'asservissement, problèmes dans les cartes de Sercos ou les asservissements, etc. Effectuer les vérifications suivantes: • Analyser les codes d’erreur pour essayer de déterminer l’origine de l’erreur. • Garantir la connexion correcte et l’intégrité de la fibre optique. • Vérifier le paramétrage dans la CNC et les asservissements. Sélecteur de nœud de l'asservissement (DriveID), paramètres LOOPTIME, SERPOWSE, SERBRATE, OPMODE, etc. S o l ut i o n s d ’ e r r e ur s . 4000(4) 'Erreur dans l'initialisation de l'anneau Sercos' CAUSE SOLUTION 4000(5) 'Erreur dans l'initialisation de l'anneau Sercos' VALEUR TRANSITION VALEUR CAUSE SOLUTION 4001 0. Valeur du paramètre PP159 dans l'asservissement. Numéro logique de l'axe. Surveillance d’erreur de poursuite désactivée dans l'asservissement. Activer paramètre PP159 dans l'asservissement. 'Le paramètre SP100 de l'asservissement doit être 0' VALEUR VALEUR AXE CAUSE SOLUTION 4007 Valeur du paramètre dans la CNC. Valeur du paramètre dans l'asservissement. Numéro logique de l'axe. Valeur du paramètre G00FEED différente dans la CNC et dans l'asservissement. Mettre la même valeur dans la CNC et l'asservissement. 'Surveillance d'erreur de poursuite non active dans l'asservissement' VALEUR VALEUR AXE CAUSE SOLUTION 4006 Valeur du paramètre dans la CNC. Valeur du paramètre dans l'asservissement. Numéro logique de l'axe. Valeur du paramètre AXISTYPE différente dans la CNC et dans l'asservissement. Mettre la même valeur dans la CNC et l'asservissement. 'Paramètre G00FEED supérieur dans la CNC que dans l'Asservissement' VALEUR VALEUR AXE CAUSE SOLUTION 4005 Valeur du paramètre dans la CNC. Valeur du paramètre dans l'asservissement. Numéro logique de l'axe. Valeur du paramètre OPMODE différente dans la CNC et dans l'asservissement. Mettre la même valeur dans la CNC et l'asservissement. 'Paramètre AXISMODE différent sur la CNC et l'asservissement' VALEUR VALEUR AXE CAUSE SOLUTION 4004 Valeur du paramètre dans la CNC. Valeur du paramètre dans l'asservissement. Numéro logique de l'axe. Valeur du paramètre LOOPTIME différente dans la CNC et dans l'asservissement. Mettre la même valeur dans la CNC et l'asservissement. 'Paramètre OPMODE différent sur la CNC et l'asservissement' VALEUR VALEUR AXE CAUSE SOLUTION 4003 5. 3. 35. Erreur dans le RAZ d’erreurs après l'initialisation de l'anneau Sercos. Contacter le service d'assistance technique. 'Paramètre LOOPTIME différent sur la CNC et l'Asservissement' VALEUR VALEUR AXE CAUSE SOLUTION 4002 Timeout dans la RAZ d’erreurs après avoir initialisé l'anneau Sercos. Contacter le service d'assistance technique. 0. Valeur du paramètre SP100 dans l'asservissement. Numéro logique de l'axe. L'asservissement a une consigne supplémentaire activée. Mettre à 0 le paramètre SP100 de l'asservissement. CNC 8070 'Broche Sercos a besoin d'un gain différent de 0' VALEUR VALEUR AXE CAUSE SOLUTION 0. Valeur de la KV dans l'asservissement. Numéro logique de l'axe. La KV de la broche est 0. Définir la KV de l'asservissement avec une valeur différente de 0. (REF: 1901) ·153· S o l ut i o n s d ’ e r r e ur s . 4008 'Erreur+ sur l'anneau Sercos à cause d'une RAZ de l'asservissement' AXE CAUSE SOLUTION 4009 'Le nombre de variables permises dans un télégramme Sercos est dépassé' AXE CAUSE SOLUTION 4010 CAUSE SOLUTION CAUSE SOLUTION CAUSE SOLUTION CAUSE SOLUTION CAUSE SOLUTION SOLUTION CNC 8070 DÉTECTION SOLUTION ·154· A l’initialisation du bus Sercos, démarrage de la CNC, validation des paramètres machine et RAZ. Vérifier la configuration et le paramétrage de Sercos. 'L'Asservissement n'est pas Fagor. Option de logiciel non autorisée' CAUSE (REF: 1901) A l’initialisation du chip de Sercos, démarrage de la CNC, validation des paramètres machine et RAZ. Nombre d’axes Sercos ou temps de Sercos erronés. Mémoire insuffisante dans le chip SERCON pour la configuration de Sercos paramétrée. Vérifier la configuration et le paramétrage de Sercos. 'TimeOut dans l'initialisation de l'anneau Sercos' DÉTECTION 4016 En écrivant les paramètres de l'asservissement pendant l’initialisation de l'anneau Sercos; démarrage de la CNC, validation des paramètres machine et RAZ. Paramètre protégé contre l’écriture. Vérifier les permissions et le niveau d’accès dans l'asservissement. 'Erreur dans l'initialisation du SERCON' DÉTECTION 4015 En écrivant les paramètres de l'asservissement pendant l’initialisation de l'anneau Sercos; démarrage de la CNC, validation des paramètres machine et RAZ. La valeur du paramètre machine est hors de la gamme permise. Corriger la valeur du paramètre dans la CNC. 'On ne peut pas écrire un paramètre dans l'asservissement: Protégé' DÉTECTION 4014 En écrivant les paramètres de l'asservissement pendant l’initialisation de l'anneau Sercos; démarrage de la CNC, validation des paramètres machine et RAZ. Le paramètre n’existe pas dans l'asservissement. Actualiser la version de logiciel de l'asservissement. 'On ne peut pas écrire un paramètre dans l'asservissement:: Hors de rang' DÉTECTION 4013 En écrivant les paramètres de l'asservissement pendant l’initialisation de l'anneau Sercos; démarrage de la CNC, validation des paramètres machine et RAZ. Erreur générique dans l'écriture du paramètre. Vérifier l’état de la communication avec l'asservissement, la version de logiciel et les options de paramétrage permises. 'On ne peut pas écrire un paramètre dans l'asservissement: Non IDN' DÉTECTION 4012 Numéro logique de l’axe affecté par l’erreur. Le nombre maximum de variables Sercos à traiter cycliquement dans un télégramme est limité à 8. Dans la table de variables Sercos il y a plus de 6/7 variables de lectureécriture synchrone définies pour un même axe. Réduire le nombre de variables synchrones à traiter sur cet axe. Définir quelquesunes de ces variables comme d’accès asynchrone. 'On ne peut pas écrire un paramètre dans l'asservissement' DÉTECTION 4011 Numéro logique de l'axe. Avis indiquant que l'asservissement a été remis à zéro. Écarter les RAZ volontaires de l'asservissement depuis le bouton de RAZ, WinDDS (enregistrement de version, soft RAZ) ou des problèmes de hardware dans l'asservissement. Si l’erreur persiste, veuillez contacter le service après-vente. A l’initialisation du bus Sercos, démarrage de la CNC, validation des paramètres machine et RAZ. Le système a détecté un asservissement non Fagor mais ne dispose pas de l’option de logiciel correspondante. Il faut activer dans la CNC l’option de régulation numérique non Fagor pour pouvoir connecter la régulation Sercos de tiers. S o l ut i o n s d ’ e r r e ur s . 4017 'Il est nécessaire de recalculer la valeur du paramètre PP4(HomingSwitchOffset) de l'asservissement. DÉTECTION CAUSE SOLUTION 4018 Mesure à distance Sercos avec FEEDBACKTYPE incohérent dans différentes gammes. DÉTECTION CAUSE SOLUTION 4019 CAUSE SOLUTION CAUSE SOLUTION CAUSE SOLUTION A l’initialisation du bus Sercos, démarrage de la CNC, validation des paramètres machine et RAZ. Un reset s'est produit par watchdog dans le module RCS-S, en raison d'une cause interne du software du nœud. Contacter Fagor. Impossible de configurer la trace programmée dans Sercos. DÉTECTION CAUSE SOLUTION 4024 A l’initialisation du bus Sercos, démarrage de la CNC, validation des paramètres machine et RAZ. Paramétrage erroné du module RCS-S ou ses ressources. Corriger le paramétrage. Erreur dans l'anneau Sercos en raison d'un Reset du compteur par Watchdog. DÉTECTION 4023 A l’initialisation du bus Sercos, démarrage de la CNC, validation des paramètres machine et RAZ. Un reset s'est produit dans le module RCS-S, soit pour une cause physique (chute d'alimentation, etc) ou interne au logiciel du nœud. Résoudre la cause du problème. Si l'erreur persiste, contacter Fagor. Paramétrage incohérent. DÉTECTION 4022 A l’initialisation du bus Sercos, démarrage de la CNC, validation des paramètres machine et RAZ. Dans l'une des entrées de mesure du module RCS-S, le type de mesure (paramètre FEEDBACKTYPE) n'est pas pareil dans tous les groupes. Corriger le paramétrage. Erreur dans l'anneau Sercos en raison d'un Reset de compteur. DÉTECTION 4020 À la mise sous tension de la CNC. Le calcul de module est passé de l'asservissement à la CNC, ce qui implique que la valeur de PP4 n’est pas valide et il faut recalculer. A la mise sous tension, la CNC vérifie si sur les broches et les axes rotatifs avec module il y a un rapport de transmission non entier et si le paramètre PP76(7)=1. Dans ce cas, au lieu d'écrire un 0 dans ce bit, la CNC affiche un message indiquant qu'il y a un mauvais paramétrage dans l'asservissement et qu'il faut recalculer la valeur de PP4 avec PP76(7)=0. Depuis le mode DDSsetup, définir le paramètre PP76(7)=0, le valider et exécuter la commande GC6 pour que l'asservissement recalcule la nouvelle valeur de PP4. Finalement enregistrer des paramètres dans la mémoire flash de l'asservissement. A l’initialisation du bus Sercos, démarrage de la CNC, validation des paramètres machine et RAZ. Erreur pendant la configuration des télégrammes AT-MDT pour mesurer la trace programmée. La trace programmée ne peut pas être appliquée, soit parce qu'il s'agit d'un régulateur non Fagor, soit parce qu'il n'existe pas de place disponible pour elle. Réduire le nombre de variables dans le télégramme. Si la largeur de bande est limitée, augmenter la fréquence SERBRATE ou éliminer les régulateurs de l'anneau. Version du Régulateur non valable pour axe TANDEM en position ou pour REFMODE CNC. DÉTECTION CAUSE SOLUTION A l’initialisation du bus Sercos, démarrage de la CNC, validation des paramètres machine et RAZ. La version d'un régulateur ne prend pas en charge le tandem avec contrôle de couple ou le mode de référence CNC. Pour bénéficier des prestations précédentes, installer dans les régulateurs une version postérieure à la v6.28 ou v8.08. CNC 8070 (REF: 1901) ·155· S o l ut i o n s d ’ e r r e ur s . 4025 Absence d'identification Multi-Axis Box (MAB) dans l'anneau Sercos. DÉTECTION CAUSE SOLUTION 4026 Incohérence dans les données de l'encodeur FeeDat/EnDat. Il faut valider la nouvelle configuration. DÉTECTION CAUSE SOLUTION 4027 CAUSE SOLUTION SOLUTION SOLUTION (REF: 1901) ·156· 4203 Numéro logique de l'axe. Erreurs dans le driver Sercos. Voir les codes d'erreur décrits dans l'erreur 4000. Erreurs dans le driver Sercos. Voir les codes d'erreur décrits dans l'erreur 4000. État de la commande qui provoque l’erreur. Erreur le canal de service de Sercos, dans les processus déclenchés depuis la boucle: • Lecture de variables. Liste d'erreurs. • Écriture de variables. Feedforward, ACforward, présélection de la gamme et KV. • Exécution de commandes. Stationner l'axe ou broche, changement de gamme. Analyser les codes d’erreur pour essayer de déterminer l’origine de l’erreur. Contacter le service d'assistance technique. 'Il manque le Drive Enable (DRENA)' AXE CAUSE SOLUTION CNC 8070 Numéro logique de l'axe. Erreur dans les processus de lecture ou d’écriture du canal cyclique (télégramme invalide ou phase différente de 4) Contacter le service d'assistance technique. 'Erreur dans le canal de service de Sercos' AXE VALEUR 1 VALEUR 2 VALEUR 3 CAUSE 4202 A l’initialisation du bus Sercos, démarrage de la CNC, validation des paramètres machine et RAZ. Une mesure FeeDat/EnDat a été paramétrée dans un module RCS-S qui ne le permet pas. Il faut mettre à jour le module RCS-S ou le remplacer par un autre nœud prenant en charge les protocoles numériques FeeDat/EnDat. 'Erreur dans le canal cyclique de Sercos' AXE CAUSE 4201 A l’initialisation du bus Sercos, démarrage de la CNC, validation des paramètres machine et RAZ. Il existe une ou plusieurs mesures FeeDat/EnDat pour lesquelles les données lues de l'encodeur sont différentes de celles conservées sur le disque. L'encodeur de la mesure est donc différent de celui qui a été validée pendant la mise au point du système. Il faut connecter à nouveau l'encodeur qui a été validé lors de chaque mesure FeeDat/EnDat, ou valider le nouvel encodeur connecté. Mesure FeeDat/EnDat paramétrée dans un compteur Sercos qui ne prend pas en charge le protocole. DÉTECTION 4200 A l’initialisation du bus Sercos, démarrage de la CNC, validation des paramètres machine et RAZ. Aucun tiroir MAB n'a été détecté dans le système. Avec l'option MABSYSTEM et plus d'un régulateur dans l'anneau Sercos, il doit exister un tiroir MAB. Éliminer l'option MABSYSTEM ou inclure un tiroir MAB dans la configuration Sercos. Numéro logique de l'axe. Pendant le déplacement d’un axe, l’activation DRENA de PLC descend. Analyser la manœuvre de PLC pour déterminer ce qui provoque la chute du signal DRENA. 'Il manque Speed Enable (SPENA)' AXE CAUSE SOLUTION Numéro logique de l'axe. Pendant le déplacement d’un axe, accoupler l’activation SPENA de PLC. Analyser la manœuvre de PLC pour déterminer ce qui provoque la chute du signal SPENA. S o l ut i o n s d ’ e r r e ur s . 4204 'Erreur lors de la remise à zéro de SERCOS. AXE VALEUR 1 VALEUR 2 CAUSE SOLUTION 4205 'Erreur dans l’anneau SERCOS' VALEUR CAUSE SOLUTION 4206 Signification. 0x00000002 Rupture de fibre optique. 0x00000100 Perte de Ats. 0x00000200 Perte de MSTs. 0x00008000 Erreur dans la transmission de Ats. (RAZ de la fibre optique ou de l'asservissement) 0xFFFF0000 Défaut dans l’accès à la RAM commune du SERCON. Erreur dans le bus Sercos qui provoque une perte de phase 4. Analyser les codes d’erreur pour essayer de déterminer l’origine de l’erreur. Contacter le service d'assistance technique. Numéro logique de l'axe. L'asservissement indique erreur. Analyser les codes d'erreur. Consulter le manuel de l'asservissement. Au cours de l'exécution. Surveillance DRSTAF, DRSTAS ou du tandem, lorsque l’axe est en déplacement. Vérifier les signaux d’activation et l’état de l'asservissement. 'Erreur dans l'anneau Sercos (fibre optique)' VALEUR CAUSE SOLUTION 4210 Code. 'Il manque Drive Status Ready (DRSTAF/DRSTAS)' DÉTECTION CAUSE SOLUTION 4209 Codes d’erreur identifiant l'origine ou les origines du problème. 'Erreur dans l’asservissement SERCOS' AXE CAUSE SOLUTION 4207 Numéro logique de l'axe. Erreurs dans le driver Sercos. Voir les codes d'erreur décrits dans l'erreur 4000. Erreurs dans le driver Sercos. Voir les codes d'erreur décrits dans l'erreur 4000. Erreur en exécutant la commande RAZ d’erreurs d'un asservissement (ID 99). La boucle exécute cette commande pendant le traitement d’un RAZ de la CNC si l'asservissement rapporte des erreurs. Analyser les codes d’erreur pour essayer de déterminer l’origine de l’erreur. Contacter le service d'assistance technique. Codes d’erreur identifiant l'origine ou les origines du problème. Code. Signification. 0x00000002 Rupture de fibre optique. Rupture de l'anneau Sercos, qui entraîne une perte de phase 4. Effectuer les vérifications suivantes: • Garantir la connexion correcte et l’intégrité de la fibre optique. • Vérifier le paramétrage dans la CNC et les asservissements. Sélecteur de nœud de l'asservissement (DriveID), paramètres LOOPTIME, SERPOWSE, SERBRATE, OPMODE, etc. 'Erreur dans l'anneau Sercos (MST perdu)' VALEUR CAUSE SOLUTION Codes d’erreur identifiant l'origine ou les origines du problème. Code. Signification. 0x00000200 Perte de MSTs. Perte d’un message de synchronisme, qui provoque une perte de phase 4. Garantir la connectivité à travers l'anneau (fibre optique, maître et esclaves). CNC 8070 (REF: 1901) ·157· S o l ut i o n s d ’ e r r e ur s . 4211 'Erreur dans l'anneau Sercos (2 ATs perdus)' AXE VALEUR CAUSE SOLUTION 4212 CAUSE SOLUTION SOLUTION SOLUTION SOLUTION 4303 Code. Signification. 0x00008000 Erreur dans la transmission de Ats. (RAZ de la fibre optique ou de l'asservissement) Erreur dans le bus Sercos qui provoque une perte de phase 4. Garantir la connectivité à travers l'anneau (fibre optique, maître et esclaves). ID Sercos du nœud de l'Unité de Comptage. Code d'erreur du module. Voir "Module RCS-S." à la page 229. L'Unité de Comptage indique erreur. Analyser les codes d'erreur (consulter le manuel de l'Unité de Comptage). ID Sercos du nœud de l'Unité de Comptage. Codes d'erreur du driver de Sercos. Codes d'erreur du driver de Sercos. État de la commande qui provoque l’erreur. IDN de la commande qui provoque l’erreur. Erreur dans la recherche d'I0 d'un axe, avec système de mesure à distance Sercos. Analyser le paramétrage du processus; en particulier le paramètre REFPULSE. Dans l'oscilloscope. Dans un canal de l’oscilloscope, une variable Sercos est définie mais il n’y a aucun serveur de variables Sercos pour répondre à la demande. Vérifier si la CNC a démarré correctement. Depuis l'interface. Une variable du régulateur Sercos a été demandée depuis l'interface, mais le serveur de variables n'a pas été correctement réinitialisé et ne peut pas accéder aux informations des variables Sercos. Vérifier si la CNC a démarré correctement. Depuis l'interface. Une variable du régulateur Sercos a été demandée depuis l'interface, mais la variable est inconnue. Vérifier que le nom de la variable Sercos est correct. 'La variable Sercos n’a pas des sets' DÉTECTION CAUSE (REF: 1901) SOLUTION ·158· Numéro logique de l'axe. Codes d’erreur identifiant l'origine ou les origines du problème. Variable Sercos non identifiée. DÉTECTION CAUSE CNC 8070 Perte de réponses d’un asservissement, qui provoque une perte de phase 4. Déterminer l'asservissement défectueux et changer la carte Sercos ou le même asservissement. Contacter le service d'assistance technique. Impossible d'accéder aux variables Sercos. DÉTECTION CAUSE 4302 Perte de Ats. 'Aucun serveur de variables sercos est enregistré' DÉTECTION CAUSE 4301 0x00000100 'Erreur dans la recherche d'I0 de l'Unité de Comptage SERCOS' NŒUD VALEUR 1 VALEUR 2 VALEUR 3 VALEUR 4 CAUSE SOLUTION 4300 Signification. 'Erreur dans l'Unité de Comptage SERCOS' NŒUD CODE CAUSE SOLUTION 4214 Code. 'Erreur dans l'anneau Sercos (réception de AT)' AXE VALEUR 4213 Numéro logique de l'axe. Codes d’erreur identifiant l'origine ou les origines du problème. Dans l'oscilloscope. Dans un canal de l'oscilloscope, il y a une variable Sercos définie, dont la syntaxe indique le set mais cette variable n'a pas de set. Supprimer l’indicatif du set du nom de la variable. S o l ut i o n s d ’ e r r e ur s . 4500 'Erreur dans l'initialisation du Hw de Mechatrolink' DÉTECTION CAUSE SOLUTION 4501 'Erreur dans la commande Mechatrolink' DÉTECTION CAUSE SOLUTION 4502 SOLUTION SOLUTION SOLUTION CAUSE SOLUTION Pendant l’exécution de la CNC, une fois qu’elle est rentrée à l’état de déplacement interpolé. Un des esclaves Mechatrolink ne peut pas compléter une commande de déplacement par manque de puissance. Vérifier le branchement de puissance de l’armoire et la manœuvre de PLC chargée d’activer les asservissements. 'Alarme dans la sous-commande Mechatrolink' DÉTECTION CAUSE SOLUTION 4508 Pendant l'exécution de la CNC. L’exécution d’une commande Mechatrolink depuis le maître à un certain esclave provoque une situation de warning dans ce dispositif. Identifier le code du warning rapporté et consulter le manuel de l’esclave Mechatrolink pour obtenir de l’information plus spécifique. 'Il manque de la puissance dans l'esclave Mechatrolink' DÉTECTION 4507 Pendant l'exécution de la CNC. Défaut dans le transfert d’information cyclique entre le maître Mechatrolink et un esclave. Vérifier le hardware du maître et l’intégrité physique du bus (câblage, résistances de terminaison, assignation de la numérotation de chaque station, etc.). 'Avis dans la commande Mechatrolink' DÉTECTION CAUSE 4506 Pendant l'exécution de la CNC. L’exécution d’une commande Mechatrolink depuis le maître à un certain esclave provoque une situation d'alarme dans ce dispositif. Identifier le code de l’alarme rapportée et consulter le manuel de l’esclave Mechatrolink pour obtenir de l’information plus spécifique. 'Erreur de communication dans le Bus Mechatrolink' DÉTECTION CAUSE 4505 Au cours du démarrage de la CNC. L’initialisation de la communication Mechatrolink a terminé. Vérifier le paramétrage de la communication (protocole, taille des données, nombre d’axes Mechatrolink, etc.) et l’intégrité physique du bus (câblage, résistances de terminaison, assignation de la numérotation de chaque station, etc.). 'Alarme de la commande Mechatrolink' DÉTECTION CAUSE 4504 Pendant l'exécution de la CNC. Défaut dans l’exécution d’une commande Mechatrolink depuis le maître à un esclave déterminé. Identifier la commande qui a produit l’erreur et l’esclave associé. Vérifier, le cas échéant, les conditions pour que la commande puisse être complétée avec succès (état de l'asservissement, alimentation, puissance, branchement du moteur, etc.). 'Time out à l'initialisation de Mechatrolink' DÉTECTION CAUSE SOLUTION 4503 Au cours du démarrage de la CNC. La phase d’initialisation de la communication Mechatrolink n’a pas pu être achevée avec succès. Vérifier le paramétrage de la communication (protocole, taille des données, nombre d’axes Mechatrolink, etc.) et l’intégrité physique du bus (câblage, résistances de terminaison, assignation de la numérotation de chaque station, etc.). Pendant l'exécution de la CNC. L’exécution d’une sous-commande Mechatrolink depuis le maître à un certain esclave provoque une situation d'alarme dans ce dispositif. Identifier le code de l’alarme rapportée et consulter le manuel de l’esclave Mechatrolink pour obtenir de l’information plus spécifique. 'Avis dans la sous-commande Mechatrolink' DÉTECTION CAUSE SOLUTION Pendant l'exécution de la CNC. L’exécution d’une sous-commande Mechatrolink depuis le maître à un certain esclave provoque une situation de warning dans ce dispositif. Identifier le code du warning rapporté et consulter le manuel de l’esclave Mechatrolink pour obtenir de l’information plus spécifique. CNC 8070 (REF: 1901) ·159· S o l ut i o n s d ’ e r r e ur s . 5000-5999 5000 'Erreur de PLC: Le temporisateur n'existe pas' DÉTECTION CAUSE SOLUTION 5001 'Erreur de PLC: Le compteur n'existe pas' DÉTECTION CAUSE SOLUTION 5002 SOLUTION (REF: 1901) 5008 Au cours de l'exécution d'une instruction CNCWR. Écriture d’un paramètre arithmétique global ou local qui n’existe pas. Vérifier le paramétrage des paramètres globaux et locaux ainsi que le programme de PLC. 'Erreur syntactique dans la lecture de variable depuis le PLC' DÉTECTION CAUSE SOLUTION ·160· Au cours de l'exécution d'une instruction CNCWR. La variable n’existe pas ou n’a pas de permission d’écriture depuis le PLC. Vérifier la syntaxe et les permissions de la variable. 'L'écriture de la variable depuis le PLC n'a pas pu être réalisée' DÉTECTION CAUSE SOLUTION 5009 Au cours de l'exécution d'une instruction CNCWR. La valeur affectée à la variable n’est pas valide. Vérifier la syntaxe de la variable et des valeurs valides. 'Erreur syntactique dans l'écriture de variable depuis le PLC' DÉTECTION CAUSE SOLUTION CNC 8070 Au cours de l'exécution d'une instruction CNCWR. Écriture d’une variable qui n’a pas de permission d’écriture depuis le PLC. Vérifier les permissions de la variable. 'Écriture de variable depuis le PLC hors de rang' DÉTECTION CAUSE SOLUTION 5007 Au cours de l'exécution d'une instruction CNCRD. Lecture d’une variable qui n’a pas de permission de lecture depuis le PLC. Vérifier les permissions de la variable. 'Variable sans permission d'écriture pour le PLC' DÉTECTION CAUSE SOLUTION 5006 Au cours de l'exécution d'une instruction CNCWR. La variable n'existe pas. Vérifier la syntaxe de la variable. 'Variable sans permission de lecture pour le PLC' DÉTECTION CAUSE SOLUTION 5005 Au cours de l'exécution d'une instruction CNCRD. La variable n'existe pas. Si l’erreur se produit au démarrage, le PLC peut être en train d’essayer d’exécuter une instruction CNCRD avant que la marque SERCOSRDY soit active. Vérifier la syntaxe de la variable. Si l'erreur est produite au démarrage, conditionner la lecture de la variable au fait de que la marque SERCOSRDY soit active. 'CNCWR: Variable sans identifier' DÉTECTION CAUSE SOLUTION 5004 Processus de lecture des données des compteurs de PLC. Demande de lecture d’un compteur qui n’existe pas. Vérifier le numéro des compteurs; compteurs valides T1 à T 256. 'CNCRD: Variable sans identifier' DÉTECTION CAUSE 5003 Processus de lecture des données des temporisateurs du PLC. Demande de lecture d’un temporisateur qui n’existe pas. Vérifier le numéro du temporisateur; temporisateurs valides T1 à T 256. Au cours de l'exécution d'une instruction CNCRD. La variable n’existe pas ou n’a pas de permission d’écriture depuis le PLC. Vérifier la syntaxe et les permissions de la variable. S o l ut i o n s d ’ e r r e ur s . 5010 'Division par zéro dans le PLC' DÉTECTION CAUSE SOLUTION 5013 'Erreur dans la lecture d'entrées numériques du PLC DÉTECTION CAUSE SOLUTION 5014 SOLUTION SOLUTION SOLUTION SOLUTION Au cours de l'exécution d'une instruction CNCEX. Le canal programmé dans l’instruction CNCEX n’est pas disponible. Le canal est en train d’exécuter un autre bloc, un autre programme ou est à un état inadéquat. Vérifier l’état du canal programmé dans l’instruction CNCEX. 'CNCEX: Exécution non finie' DÉTECTION CAUSE SOLUTION 5021 Au cours de l'exécution d'une instruction CNCEX. La marque programmée dans l’instruction CNCEX est déjà active en exécutant l’instruction. Cela peut être dû à une mauvaise programmation de l’instruction ou au fait que le canal est occupé avec autre instruction CNCEX. Vérifier dans le programme de PLC la logique de l’instruction CNCEX et des marques utilisées. 'CNCEX: Canal d’exécution non disponible' DÉTECTION CAUSE 5020 Au cours de l'exécution d'une instruction CNCEX. Le bloc programmé dans l’instruction CNCEX est nul ou le canal programmé n’est pas disponible. Vérifier le bloc à exécuter et l’état du canal. 'CNCEX n'a pas pu être exécutée du fait que la marque de communication était à "1"' DÉTECTION CAUSE 5019 Au cours de l'exécution d'une instruction CNCRD. Donnée lue hors de rang. Vérifier la syntaxe de l’instruction. 'Bloc nul de CNCEX' DÉTECTION CAUSE 5018 Au cours de l'exécution d'une instruction CNCRD. Lecture d’un paramètre arithmétique global ou local qui n’existe pas. Vérifier le paramétrage des paramètres globaux et locaux ainsi que le programme de PLC. 'Valeur de lecture hors de rang' DÉTECTION CAUSE SOLUTION 5017 Au cours de l'écriture des sorties numériques du PLC. La table de configuration des I/O numériques n’est pas valide ou le PLC a reçu une demande d’écriture avant de terminer la précédente. Vérifier la table de configuration d’I/O numériques, réaliser les vérifications opportunes pour garantir l’intégrité du bus CAN ou augmenter le temps de cycle dans le paramètre PLCFREQ. Si l'erreur persiste, contacter Fagor. 'La lecture de la variable depuis le PLC n'a pas pu être réalisée' DÉTECTION CAUSE SOLUTION 5016 Au cours de la lecture des entrées numériques du PLC. La table de configuration des I/O numériques n’est pas valide. Vérifier la table de configuration des I/Os numériques. Si l'erreur persiste, contacter Fagor. 'Erreur dans l'écriture de sorties numériques du PLC' DÉTECTION CAUSE 5015 Au cours de l'exécution d'une instruction DVS ou MDS. Le dénominateur d'une opération DVS ou MDS est 0. Vérifier le programme PLC. Ne pas réaliser des divisions par 0. Au cours de l'exécution d'une instruction CNCEX. L'instruction CNCEX ne peut pas exécuter le bloc dans le canal indiqué. Vérifier l’état du canal programmé dans l’instruction CNCEX. CNC 8070 'CNCEX: Le canal indiqué n'est pas du PLC' DÉTECTION CAUSE SOLUTION Au cours de l'exécution d'une instruction CNCEX. Le canal programmé dans l’instruction CNCEX n’est pas du PLC. Vérifier la syntaxe de l’instruction. Vérifier dans les paramètres machine le type de canal (paramètre CHTYPE). (REF: 1901) ·161· S o l ut i o n s d ’ e r r e ur s . 5022 'PLC: Trop de CNCRD et CNCWR de variables asynchrones' DÉTECTION CAUSE SOLUTION 5023 'Erreur dans la lecture d'entrées numériques locales' DÉTECTION CAUSE SOLUTION 5024 SOLUTION SOLUTION CAUSE SOLUTION CNC 8070 5031 Au cours du démarrage de la CNC. Erreur de configuration des modules à distance. Vérifier la configuration des modules à distance. Erreur interne de configuration des ressources à distance. DÉTECTION CAUSE SOLUTION ·162· Au cours du fonctionnement de la CNC. Alarme dans un module à distance, lors de l'écriture de données. Vérifier les connexions des modules à distance. Erreur de configuration des ressources à distance. DÉTECTION CAUSE SOLUTION (REF: 1901) Au cours du fonctionnement de la CNC. Alarme dans un module à distance, lors de la lecture des données. Vérifier les connexions des modules à distance. Erreur dans une ressource à distance. DÉTECTION CAUSE SOLUTION 5030 Le PLC a détecté une alarme de surcharge de courant lors de l’écriture de la sortie analogique locale. Court-circuit dans la sortie analogique locale de la CNC. Vérifier le branchement de la sortie analogique de la CNC. Erreur dans une ressource à distance. DÉTECTION CAUSE SOLUTION 5029 Au cours de l'exécution des commandes CNCWR Le PLC a essayé d’écrire une valeur différente de 0 dans une variable qui n’admet que la valeur 0 (zéro). Vérifier le programme PLC. Écrire la valeur 0 dans la variable ou supprimer l'instruction CNCWR. 'Court-circuit dans la sortie analogique locale (report depuis PLC' DÉTECTION 5028 Au cours du démarrage de la CNC. Le compteur est désactivé, depuis le programme de PLC ou depuis la surveillance. Après cet avis, le PLC force l’activation du compteur (CEN = 1) automatiquement. 'CNCWR: La variable n'admet que la valeur '0'' DÉTECTION CAUSE 5027 En écrivant les sorties numériques locales (unités centrales ICU et MCU). L’écriture est directe dans les unités centrales ICU et MCU, ce serait donc une erreur formelle dans la demande au driver. Vérifier l’installation des drivers de la CNC. 'Compteur de PLC désactivé' DÉTECTION CAUSE SOLUTION 5026 Au cours de la lecture des entrées numériques locales (unités centrales ICU et MCU). La lecture est directe dans les unités centrales ICU et MCU, ce serait donc une erreur formelle dans la demande au driver. Vérifier l’installation des drivers de la CNC. 'Erreur dans l'écriture de sorties numériques locales' DÉTECTION CAUSE 5025 Pendant l’exécution de commandes CNCRD et CNCWR de variables asynchrones, ainsi que pendant l’exécution commandes CNCEX. Nombre excessif de demandes asynchrones depuis le PLC. • Commande CNCEX. • Commandes CNCRD et CNCWR de variables asynchrones des asservissements. • Instructions CNCWR de variables d’outils. • Instruction CNCRD de variables d’outils qui ne sont pas dans le magasin. Les valeurs figurant dans le warning sont les numéros des marques de PLC qui commandent les processus CNCRD, CNCWR et CNCEX causant l’erreur. Pour supprimer l’erreur, vérifier la manœuvre du PLC pour qu’il n’y ait pas autant de demandes asynchrones à la fois. Au cours du démarrage de la CNC. Erreur de configuration des modules à distance. Vérifier la configuration des modules à distance. S o l ut i o n s d ’ e r r e ur s . 5032 Erreur dans l'ordre des commandes de configuration du routeur de ressources à distance. DÉTECTION CAUSE SOLUTION 5033 Erreur de configuration du routeur de ressources à distance. DÉTECTION CAUSE SOLUTION 5034 SOLUTION Au cours du fonctionnement de la CNC. La tension appliquée à l'entrée analogique est supérieure à la plage autorisée. Vérifier le circuit raccordé à l'entrée analogique à distance. CNC 8070 Une entrée analogique à distance a détecté une erreur de plage minimale dépassée. DÉTECTION CAUSE SOLUTION 5043 Au cours du fonctionnement de la CNC. Le module de la sortie analogique à distance a une erreur. Vérifier le module de la sortie analogique à distance. Une entrée analogique à distance a détecté une erreur de plage dépassée. DÉTECTION CAUSE SOLUTION 5042 Au cours du fonctionnement de la CNC. Le module de la sortie analogique à distance ne fonctionne pas correctement. Vérifier le module de la sortie analogique à distance. Une sortie analogique à distance a détecté une erreur inconnue. DÉTECTION CAUSE SOLUTION 5041 Au cours du fonctionnement de la CNC. L'alimentation de la sortie analogique à distance n'est pas correcte. Vérifier l'alimentation de la sortie analogique à distance. Une sortie analogique à distance a détecté une erreur dans le module. DÉTECTION CAUSE SOLUTION 5040 Au cours du fonctionnement de la CNC. La configuration d'une sortie analogique à distance n'est pas correcte. Vérifier la configuration de la sortie analogique à distance. Une sortie analogique à distance a détecté une erreur d'alimentation. DÉTECTION CAUSE SOLUTION 5039 Au cours du fonctionnement de la CNC. Court-circuit dans une sortie analogique à distance. Vérifier les connexions de la sortie analogique de la CNC. Une sortie analogique à distance est mal configurée. DÉTECTION CAUSE SOLUTION 5038 Au cours du fonctionnement de la CNC. Le circuit raccordé à une sortie analogique à distance est ouvert. Vérifier les connexions de la sortie analogique de la CNC. Erreur de court-circuit dans une sortie analogique à distance. DÉTECTION CAUSE SOLUTION 5037 Au cours du démarrage de la CNC. Erreur de configuration des modules à distance. Un paramètre des ressources à distance n'est pas correct. Vérifier la configuration des modules à distance. Erreur de circuit ouvert dans une sortie analogique à distance. DÉTECTION CAUSE SOLUTION 5036 Au cours du démarrage de la CNC. Erreur de configuration des modules à distance. Le bus utilise un canal qui n'existe dans aucun module à distance. Vérifier la configuration des modules à distance. Erreur de paramétrage d'une ressource à distance. DÉTECTION CAUSE 5035 Au cours du démarrage de la CNC. Erreur de configuration des modules à distance. L'ordre des commandes d'initialisation du routeur de ressources n'est pas correct. Vérifier la configuration des modules à distance. Au cours du fonctionnement de la CNC. La tension appliquée à l'entrée analogique est inférieure à la plage autorisée. Vérifier le circuit raccordé à l'entrée analogique à distance. Une entrée analogique à distance a détecté une erreur de conversion. DÉTECTION CAUSE SOLUTION (REF: 1901) Au cours du fonctionnement de la CNC. L'entrée analogique ne peut réaliser la lecture correctement. Vérifier le module de l'entrée analogique à distance. ·163· S o l ut i o n s d ’ e r r e ur s . 5044 Une entrée analogique à distance est mal configurée. DÉTECTION CAUSE SOLUTION 5045 Une entrée analogique à distance a détecté une erreur d'alimentation. DÉTECTION CAUSE SOLUTION 5046 CNC 8070 (REF: 1901) ·164· Au cours du fonctionnement de la CNC. Le module du capteur de température à distance ne fonctionne pas correctement. Vérifier le module du capteur de température à distance. n capteur de température à distance a détecté une erreur inconnue. DÉTECTION CAUSE SOLUTION 5055 Au cours du fonctionnement de la CNC. L'alimentation du capteur de température à distance n'est pas correcte. Vérifier l'alimentation du capteur de température à distance. Un capteur de température à distance a détecté une erreur dans le module. DÉTECTION CAUSE SOLUTION 5054 Au cours du fonctionnement de la CNC. La configuration d'un capteur de température à distance n'est pas correcte. Vérifier la configuration du capteur de température à distance. Un capteur de température à distance a détecté une erreur d'alimentation. DÉTECTION CAUSE SOLUTION 5053 Au cours du fonctionnement de la CNC. Le capteur de température à distance ne peut réaliser la lecture correctement. Vérifier le module du capteur de température à distance. Un capteur de température à distance est mal configuré. DÉTECTION CAUSE SOLUTION 5052 Au cours du fonctionnement de la CNC. La température mesurée par le capteur est inférieure à la plage autorisée. Vérifier le circuit raccordé au capteur de température à distance. Un capteur de température à distance a détecté une erreur de conversion. DÉTECTION CAUSE SOLUTION 5051 Au cours du fonctionnement de la CNC. Le circuit raccordé à un capteur de température à distance est ouvert. Vérifier les connexions du capteur de température à distance. Un capteur de température à distance a détecté une erreur de plage minimale dépassée. DÉTECTION CAUSE SOLUTION 5050 Au cours du fonctionnement de la CNC. Le module de l'entrée analogique à distance a une erreur. Vérifier le module de l'entrée analogique à distance. Erreur de circuit ouvert dans un capteur de température à distance. DÉTECTION CAUSE SOLUTION 5049 Au cours du fonctionnement de la CNC. Le module de l'entrée analogique à distance ne fonctionne pas correctement. Vérifier le module de l'entrée analogique à distance. Une entrée analogique à distance a détecté une erreur inconnue. DÉTECTION CAUSE SOLUTION 5048 Au cours du fonctionnement de la CNC. L'alimentation de l'entrée analogique à distance n'est pas correcte. Vérifier l'alimentation de l'entrée analogique à distance. Une entrée analogique à distance a détecté une erreur dans le module. DÉTECTION CAUSE SOLUTION 5047 Au cours du fonctionnement de la CNC. La configuration d'une entrée analogique à distance n'est pas correcte. Vérifier la configuration de l'entrée analogique à distance. Au cours du fonctionnement de la CNC. Le module du capteur de température à distance a une erreur. Vérifier le module du capteur de température à distance. Un capteur de température à distance a détecté une erreur de plage dépassée. DÉTECTION CAUSE SOLUTION Au cours du fonctionnement de la CNC. La température mesurée par le capteur est supérieure à la plage autorisée. Vérifier le circuit raccordé au capteur de température à distance. S o l ut i o n s d ’ e r r e ur s . 5056 Erreur d'exécution dans le traitement d'une sortie analogique à distance. DÉTECTION CAUSE SOLUTION 5057 Au cours du fonctionnement de la CNC. Fonctionnement incorrect dans le traitement des données. Contacter Fagor Automation. Erreur d'exécution dans le traitement d'une entrée analogique à distance. DÉTECTION CAUSE SOLUTION Au cours du fonctionnement de la CNC. Fonctionnement incorrect dans le traitement des données. Contacter Fagor Automation. CNC 8070 (REF: 1901) ·165· S o l ut i o n s d ’ e r r e ur s . 6000-6999 6000 'Alarme du système de mesure' DÉTECTION CAUSE SOLUTION 6001 'Alarme du test de tendance activée' DÉTECTION CAUSE SOLUTION 6002 SOLUTION (REF: 1901) ·166· Pendant le démarrage de la CNC ou la surveillance du programme du PLC. La marque _ARRÊT D'URGENCE du PLC est désactivée. Vérifier l’état des boutons-poussoir d’arrêt d’urgence. Vérifier la logique du signal _ARRÊT D'URGENCE dans le programme de PLC. 'Erreur dans l'initialisation du Bus CAN' DÉTECTION CAUSE CNC 8070 Pendant le démarrage de la CNC ou la surveillance du programme du PLC. Le programme de PLC n’est pas en marche. • Installation d’une nouvelle version de logiciel. • L’utilisateur a arrêté le PLC et a oublié de le remettre en marche. Mettre en marche le programme PLC. Au besoin, compiler le programme de PLC. 'Arrêt d'urgence externe activé' DÉTECTION CAUSE SOLUTION 6004 Lorsqu’un axe s’emballe et que la surveillance du test de tendance est active. Réalimentation positive sur l’axe pendant un temps supérieur à celui défini dans le paramètre ESTDELAY. Régler le signe de la consigne (paramètre AXISCHG), le comptage (LOOPCHG) et le temps affecté au paramètre ESTDELAY. 'Le programme PLC n'est pas en marche' DÉTECTION CAUSE 6003 Au cours de l'exécution. Alarme de mesure sur un axe analogique (paramètre FBACKAL). Pour un signal TTL différentiel. • Un ou plusieurs câbles sectionnés (signaux A, B ou les relais de retenue). • Entrée de mesure déconnectée dans le compteur. Pour signal sinusoïdal différentiel. • Un ou plusieurs câbles sectionnés (signaux A, B ou les relais de retenue). • Entrée de mesure déconnectée dans le compteur. • Amplitude de signal d’entrée au-dessus de 1,45 Vpp environ. • Amplitude de signal d’entrée en dessous de 0,4 Vpp environ. • Déphasage excessif entre signaux A et B (en quadrature, en théorie). Pour des signaux non différentiels, l’alarme de mesure doit être désactivée. Vérifier les câbles et la connexion des entrées de mesure. Si l’erreur persiste, veuillez contacter le service après-vente. Au cours du démarrage de la CNC. Erreur dans l’initialisation du bus CAN qui a lieu au démarrage afin de mettre en marche le clavier de CAN. Les codes d’erreur sont différents pour les cas de bus CANfagor et du bus CANopen. Codes d'erreur pour le bus CANopen. Code. Signification. 14 Défaut dans le RAZ du micro de la COMPCI (mauvais fonctionnement du micro, contacts inadéquats, etc.). 15 Problèmes dans la connexion ou dans la configuration des esclaves CANopen. S o l ut i o n s d ’ e r r e ur s . Codes d'erreur pour le bus CANfagor.. SOLUTION 6005 Signification. -1 / -2 / -3 165 en état d’erreur ou ne répond pas (problème dans la COMPCI). -4 / -5 Structure de mémoire différente pour PC et COMPCI (éventuelles différences de versions). -6 Erreur sur EnableCyclicRead(MD_JOG). -7 Problèmes dans l’identification de nœuds (même groupe et numéro de nœud). -8 Problèmes dans l’identification de nœuds (détection d’un nœud supplémentaire). -9 Mot de passe d'accès à IniCan non valide. -10 Défaut dans le test de hardware de la COMPCI. -11 Défaut dans le test de hardware du nœud à distance. Si l’erreur persiste, veuillez contacter le service après-vente. 'Erreur en sélectionnant la fréquence de travail du BUS CAN' DÉTECTION CAUSE SOLUTION 6006 Code. Au cours du démarrage du système. Un ou plusieurs nœuds ne syntonisent pas à la fréquence paramétrée. Effectuer les vérifications suivantes. Si l’erreur persiste, veuillez contacter le service après-vente. • Vérifier que la longueur du câble CAN est l’adéquate pour la fréquence. • Dans le mode diagnostic, vérifier que la CNC reconnaît tous les modules. • Utiliser l’outil itfcCAN.exe pour vérifier le bus CAN (uniquement service d’assistance technique). 'Un ou plusieurs nœuds CAN ne répondent pas' DÉTECTION CAUSE Au cours de l'exécution. Un ou plusieurs nœuds à distance ne répondent plus par RAZ, courts-circuits, mauvais fonctionnement, etc. Les codes d’erreur sont différents pour les cas de bus CANfagor et du bus CANopen. Pour le bus CANopen, la fenêtre d’erreur indique le module qui provoque l’erreur. Codes d'erreur pour le bus CANfagor.. Code. Signification. -1 / -6 Il y a plus de trois nœuds perdus. -3 1 nœud perdu. -4 2 nœud perdu. -5 3 nœud perdu. Codes d'erreur pour le bus CANopen. SOLUTION 6007 Signification. 2 Timeout (le nœud ne répond pas). 3 Erreur dans le bit de toggle. 4 Le nœud répond mais son état n’est pas correct. Dans le mode diagnostic, vérifier que la CNC reconnaît tous les modules. Vérifier le pinout du câble CAN. Si l’erreur persiste, veuillez contacter le service après-vente. 'Watchdog dans la COMPCI' DÉTECTION CAUSE SOLUTION 6008 Code. CNC 8070 Au cours de l'exécution. La COMPCI ne répond pas; possibilité de mauvais fonctionnement, contacts, etc. Si l’erreur persiste, veuillez contacter le service après-vente. 'Watchdog dans le PC + COMPCI' DÉTECTION CAUSE SOLUTION Au cours de l'exécution. La COMPCI et le PC ne répondent pas pour cause de mauvais fonctionnement, contacts, pertes de RT IT, etc. Dans le mode diagnostic, vérifier la configuration du bus CAN et s’il se produit des pertes d’IT. Si l’erreur persiste, veuillez contacter le service après-vente. (REF: 1901) ·167· S o l ut i o n s d ’ e r r e ur s . 6009 'Watchdog dans le PC' DÉTECTION CAUSE SOLUTION 6010 'Erreur dans le processus de la COMPCI' DÉTECTION CAUSE SOLUTION 6011 Au cours de l'exécution. Le Pc ne répond pas par pertes de RT IT. Dans le mode diagnostic, vérifier s’il se produit des pertes d’IT et la configuration du bus CAN. Si l’erreur persiste, veuillez contacter le service après-vente. Au cours de l'exécution. Erreurs diverses dans les processus gérés par la COMPCI. Si l’erreur persiste, veuillez contacter le service après-vente. 'Erreur de CAN dans le nœud à distance' DÉTECTION CAUSE Au cours de l'exécution. Erreur rapportée par un nœud. Les codes d’erreur sont différents pour les cas de bus CANfagor et du bus CANopen. La fenêtre d’erreur indique le module qui provoque l’erreur. Codes d'erreur pour le bus CANfagor.. Code. Signification. 1 Overrun dans le contrôleur de CAN. Perte éventuelle de messages reçus. 2 BusOFF. Le nœud détecte la chute du bus. 3 Overrun dans la fifo de réception. Perte éventuelle de messages reçus. 4 Warning. Le compteur de trames d’erreur dépasse le niveau 1 (96). 11 Le nœud informe que la COMPCI ne répond pas aux contrôles de présence. 12 RAZ du nœud (problèmes d’alimentation, courts-circuits, watchdog, etc.). 13 Défaut dans la transmission d'un message. Type de module produisant l’erreur pour le bus CANfagor. SOLUTION CNC 8070 (REF: 1901) ·168· Module. Signification. 1 Sorties analogiques. 2 Compteurs. 3 Sorties numériques. 4 Entrés numériques. 5 Entrées analogiques. 7 Entrées PT100. 8 Manivelle du clavier CAN. 9 Palpeurs. 10 Clavier jog. 11 Clavier alphanumérique. 12 Défaut dans un nœud des I/Os. Contacter le service d'assistance technique. S o l ut i o n s d ’ e r r e ur s . 6011 'Report de nœud CANopen: Arrêt d’urgence indéfini.' 'Report de nœud CANopen: Arrêt d'urgence générique.' 'Report de nœud CANopen: Arrêt d'urgence du courant.' 'Report de nœud CANopen: Surcharge de courant dans les sorties.' 'Report de nœud CANopen: Arrêt d'urgence de la tension.' 'Report de nœud CANopen: Il manque l’alimentation.' 'Report de nœud CANopen: Arrêt d'urgence de la température.' 'Report de nœud CANopen: Arrêt d'urgence hardware.' 'Report de nœud CANopen: Entrée PT100 interrompue ou pas branchée.' 'Report de nœud CANopen: Il manque la tension dans les sorties.' 'Report de nœud CANopen: Arrêt d'urgence logiciel.' 'Report de nœud CANopen: Erreur au code interne.' 'Report de nœud CANopen: Arrêt d'urgence des modules supplémentaires.' 'Report de nœud CANopen: Arrêt d'urgence de communication.' 'Report de nœud CANopen: Temps excessif entre synchronismes.' 'Report de nœud CANopen: Overrun, message perdu.' 'Report de nœud CANopen: Erreurs dans le bus, bus passif.' 'Report de nœud CANopen: Défaut du contrôle de présence.' 'Report de nœud CANopen: Récupération du bus-off.' 'Report de nœud CANopen: Erreur de protocole.' 'Report de nœud CANopen: PDO trop court.' 'Report de nœud CANopen: PDO trop long.' 'Report de nœud CANopen: Arrêt d'urgence externe.' 'Report de nœud CANopen: Arrêt d’urgence spécifique du fabricant.' DÉTECTION CAUSE VALEUR 1 VALEUR 2 VALEUR 3 Au cours de l'exécution. Cette erreur indique qu'un nœud CANOPEN a envoyé un message d'arrêt d'urgence. Le texte d'erreur dépend du code spécifique de l'arrêt d'urgence envoyé (valeur 3). Numéro de noeud. Codes d’erreur pour le bus CANopen (codage par bits). Code. Signification. 0x01 Erreur générique. 0x02 Erreur de courant. 0x04 Erreur de tension. 0x08 Erreur de température. 0x10 Erreur de communications. 0x20 Erreur de dispositif. 0x40 Réservé. 0x80 Erreur spécifique du fabricant. Table d’arrêt d’urgences pour le bus CANopen (codage par bits). Arrêt d'urgence. Signification. 0x0000 Erreur corrigée. 0x1000 Erreur générique. 0x2000 Courant. 0x2100 Courant, côté d'entrée du dispositif. 0x2200 Courant dans le dispositif. 0x2300 Courant, côté de sortie du dispositif. 0x2310 Surcharge de courant dans les sorties. 0x3000 Tension. 0x3100 Tension de réseau. 0x3200 Tension dans le dispositif. 0x3300 Tension de sortie. 0x4000 Température. 0x4100 Température d'ambiance. 0x4200 Température dans le dispositif. 0x5000 Hardware du dispositif. CNC 8070 (REF: 1901) ·169· S o l ut i o n s d ’ e r r e ur s . SOLUTION 6012 SOLUTION SOLUTION (REF: 1901) ·170· 0x5030 PT100 cassée ou non branchée. 0x5112 Tension d'alimentation des sorties. 0x6000 Logiciel du dispositif. 0x6100 Logiciel interne. 0x6200 Logiciel d'utilisateur. 0x6300 Ensemble de données. 0x7000 Modules supplémentaires. 0x8000 Surveillance. 0x8100 Communication. 0x8110 Messages perdus. 0x8120 Trop d'erreurs dans le bus. 0x8130 Erreur de contrôle de présence détectée par le nœud. 0x8140 Récupération du BUS OFF. 0x8200 Erreur de protocole. 0x8210 PDO non traité pour cause d’erreur dans sa longueur. 0x8220 PDO avec trop de variables. 0x9000 Erreur externe. 0xF000 Fonctions supplémentaires. 0xFF00 Dispositif spécifique. Contacter le service d'assistance technique. Au cours de l'exécution. La COMPCI détecte BUSOFF et le bus descend. Codes d'erreur pour le bus CANopen. Code. Signification. 0 Erreur du système. 1 Erreur du CAN. 2 Erreur dans les files d'attente Tx/Rx. Dans le mode diagnostic, vérifier que la CNC reconnaît tous les modules et le compteur d’erreurs CAN ; en cas d’erreurs, effectuer les vérifications correspondantes pour garantir l’intégrité du bus CAN. Si l’erreur persiste, veuillez contacter le service après-vente. 'Timeout dans l'initialisation de CAN' DÉTECTION CAUSE CNC 8070 Signification. 'Erreur dans l'unité de commande de CAN' DÉTECTION CAUSE 6013 Arrêt d'urgence. Au cours du démarrage du système. Défaut dans le processus d'initialisation du bus CAN par problèmes dans le bus. Séquence de mise hors et sous tension trop rapide. Réaliser les vérifications et actions suivantes pour garantir l’intégrité du bus CAN : • Il n’y a pas de groupes CAN avec la même direction sélectionnée. • Le sélecteur du nœud dans la COMPCI doit être 0. • Résistances de terminaison de ligne. • Connexion à terre. • Continuité du câble CAN. • Connecteurs du câble CAN (s’il faut, les démonter et remonter). • Connexion du câble plat entre les nœuds et la source. • Sources d’alimentation des groupes CAN (niveaux, possibles RAZ, etc.). • Voir dans le mode diagnostic si tous les modules sont reconnus. • Utiliser l’outil itfcCAN.exe pour vérifier le bus CAN (uniquement service d’assistance technique). Si l’erreur persiste, veuillez contacter le service après-vente. S o l ut i o n s d ’ e r r e ur s . 6014 'Défaut dans l'accès au DPRAM de la COMPCI' DÉTECTION CAUSE SOLUTION 6015 'Le compteur d'erreurs CAN dépasse le niveau 1' DÉTECTION CAUSE SOLUTION 6016 SOLUTION SOLUTION SOLUTION Au cours de l'exécution. Défaut dans les processus cycliques de lecture des entrées numériques, analogiques, compteurs et manivelles de clavier. Un des nœuds n’a pas envoyé le message à temps. Dans le mode diagnostic, vérifier que la CNC reconnaît tous les modules et le compteur d’erreurs CAN ; en cas d’erreurs, effectuer les vérifications correspondantes pour garantir l’intégrité du bus CAN. Au besoin, augmenter les temps de cycle (paramètres LOOPTIME et PLCFREQ). Si l’erreur persiste, veuillez contacter le service après-vente. 'Chevauchement du cycle de CAN' DÉTECTION CAUSE SOLUTION 6021 Au cours de l'exécution. Overflow dans la FIFO de réception de la COMPCI. Perte éventuelle de messages reçus. Consulter le service d’assistance technique. 'Timeout dans les lectures de CAN' DÉTECTION CAUSE 6020 Au cours de l'exécution. Overflow dans la FIFO de réception du contrôleur de CAN. Perte éventuelle de messages reçus. Consulter le service d’assistance technique. 'Overrun dans FIFO CAN de la COMPCI' DÉTECTION CAUSE 6019 Au cours de l'exécution. Le compteur de trames d’erreur (Rx/Tx) dépasse le niveau critique (127). Réaliser les vérifications opportunes pour garantir l’intégrité du bus CAN. Si l’erreur persiste, veuillez contacter le service après-vente. 'Overrun dans FIFO de la commande CAN' DÉTECTION CAUSE 6018 Au cours de l'exécution. Le compteur de trames d’erreur (Rx/Tx) dépasse le niveau 1 (96). Réaliser les vérifications opportunes pour garantir l’intégrité du bus CAN. Si l’erreur persiste, veuillez contacter le service après-vente. 'Le compteur d'erreurs CAN atteint le niveau critique' DÉTECTION CAUSE SOLUTION 6017 Au cours de l'exécution. Défaillance dans l’accès à la mémoire RAM commune de la COMPCI pour cause d’erreur de hardware, mauvais contact, etc. Au démarrage et cycliquement, la CNC et la COMPCI réalisent des tests de lecture et d’écriture de la mémoire RAM commune. Le mode diagnostic offre de l’information supplémentaire au défaut. Consulter le service d’assistance technique. Au cours de l'exécution. Défaut dans les processus cycliques de lecture des entrées numériques, analogiques, compteurs et manivelles de clavier. Un des nœuds n’a pas envoyé le message à temps. Dans le mode diagnostic, vérifier que la CNC reconnaît tous les modules et le compteur d’erreurs CAN ; en cas d’erreurs, effectuer les vérifications correspondantes pour garantir l’intégrité du bus CAN. Au besoin, augmenter les temps de cycle (paramètres LOOPTIME et PLCFREQ). Si l’erreur persiste, veuillez contacter le service après-vente. 'Problèmes dans la transmission de CAN' DÉTECTION CAUSE SOLUTION Au cours de l'exécution. Défaut dans les processus de transmission de sorties numériques, analogiques, etc. Possible affaissement du bus. Dans le mode diagnostic, vérifier que la CNC reconnaît tous les modules et le compteur d’erreurs CAN ; en cas d’erreurs, effectuer les vérifications correspondantes pour garantir l’intégrité du bus CAN. Au besoin, augmenter les temps de cycle (paramètres LOOPTIME et PLCFREQ). Si l’erreur persiste, veuillez contacter le service après-vente. CNC 8070 (REF: 1901) ·171· S o l ut i o n s d ’ e r r e ur s . 6022 'Erreur dans l'initialisation du compteur de l'axe' DÉTECTION CAUSE SOLUTION 6023 'Erreur dans l'initialisation du compteur de la manivelle' DÉTECTION CAUSE SOLUTION 6024 SOLUTION SOLUTION SOLUTION SOLUTION CNC 8070 SOLUTION (REF: 1901) 1 Sorties analogiques. 3 Sorties numériques. Consulter le service d’assistance technique. Au cours du démarrage du système. Erreur dans le test de hardware de la COMPCI. Les tests suivants sont réalisés au démarrage : Flash, RAM commun, RAM externe, RAM interne et commande CAN. Le mode diagnostic présente de l’information en détail sur le type d’erreur. Vérifier que la version de logiciel de la COMPCI est la correcte. Consulter le service d’assistance technique. Au cours du démarrage du système. Erreur dans le test de hardware des nœuds à distance. Les tests suivants sont réalisés au démarrage : Flash, RAM et commande CAN. Le mode diagnostic présente de l’information en détail sur le type d’erreur. Vérifier que la version de logiciel de la COMPCI est la correcte. Consulter le service d’assistance technique. Au cours du démarrage du système ou pendant l'exécution. Erreur dans le test de la RAM commun du SERCON (accès R/W en modes Byte/Word). La CNC réalise ce test au démarrage et à chaque cycle de Sercos, pendant la phase 4, pour vérifier l’intégrité des données de la mémoire RAM du SERCON. Problème de hardware de la carte Sercos ou branchement au Bus PCI. Consulter le service d’assistance technique. 'Limite d'incrément de position dépassée dans la CNC' DÉTECTION CAUSE SOLUTION ·172· Signification. 'Erreur dans l'accès à la RAM du SERCON' DÉTECTION CAUSE 6029 Code. 'Erreur de hardware dans le nœud à distance CAN' DÉTECTION CAUSE 6028 Au cours de l'exécution. Erreur dans le cheksum des données des sorties numériques ou analogiques qui ont été envoyées du PC à la COMPCI à travers la mémoire RAM commune. Codes d'erreur pour le bus CANfagor.. 'Erreur de hardware dans la COMPCI' DÉTECTION CAUSE 6027 Au cours du démarrage de la CNC. L'entrée de la manivelle n'existe pas. La fenêtre d’erreur indique la manivelle qui provoque l’erreur. Vérifier les paramètres machine. Si l’erreur persiste, veuillez contacter le service après-vente. 'Erreur de checksum de la COMPCI' DÉTECTION CAUSE 6026 Au cours du démarrage de la CNC. Le compteur n'existe pas. La fenêtre d’erreur indique le compteur qui provoque l’erreur. Vérifier les paramètres machine. Si l’erreur persiste, veuillez contacter le service après-vente. 'Erreur dans l'initialisation de la manivelle du clavier' DÉTECTION CAUSE 6025 Au cours du démarrage de la CNC. Le compteur n'existe pas. La fenêtre d’erreur indique le compteur qui provoque l’erreur. Vérifier les paramètres machine. Si l’erreur persiste, veuillez contacter le service après-vente. Au cours de l'exécution. Incrément de position excessive sur un axe analogique. Défaut de hardware du nœud du compteur, accès à la COMPCI (branchement), etc. Consulter le service d’assistance technique. S o l ut i o n s d ’ e r r e ur s . 6030 'Limite d'incrément de position dépassée dans le nœud du compteur de CAN' DÉTECTION CAUSE SOLUTION 6031 'Version logiciel incompatible en COMPCI/Nœuds à distance' DÉTECTION CAUSE SOLUTION 6032 SOLUTION SOLUTION SOLUTION Au cours du démarrage du système. Un élément du bus CAN dépasse le maximum permis; nombre d’entrées ou de sorties analogiques, entrées ou sorties numériques ou compteurs. Mettre la CNC hors tension et enlever des éléments du bus jusqu’à rentrer dans les limites. CNC 8070 'Erreur dans l'activation d'entrée PT100' DÉTECTION CAUSE SOLUTION 6040 Au cours du démarrage du système. La valeur du paramètre LOOPTIME est trop petite ou n’est pas valide. Vérifier que la valeur assignée au paramètre LOOPTIME est multiple de 0,5 ms et supérieure à 1,5 ms. Augmenter la valeur si la configuration CAN le conseille. 'La limite maximale d'éléments CAN dans le système est dépassée' DÉTECTION CAUSE 6039 Au cours de l'exécution. Il manque l’alimentation dans les I/O locaux (unités centrales ICU et MCU). Alimenter les I/Os locaux avec 24 V. 'Paramètre LOOPTIME non valide pour la configuration de CAN' DÉTECTION CAUSE SOLUTION 6038 Au cours du démarrage du système. Il y a plus de sorties numériques locales configurées dans la CNC que celles existant réellement. Définir un maximum de 8 sorties numériques locales. 'Il manque l'alimentation des IOs locaux' DÉTECTION CAUSE SOLUTION 6037 Au cours de l'exécution. Un nœud CAN a été remis à zéro. La fenêtre d'erreur indique le numéro de nœud. Vérifier que l’alimentation du nœud est correcte. S’il n’y a pas de problèmes dans le bus, remplacer le nœud. Consulter le service d’assistance technique. 'Erreur dans l'initialisation des IOs locaux' DÉTECTION CAUSE 6036 Au cours du démarrage du système ou pendant l'exécution. La configuration hardware enregistrée sur le disque ne coïncide pas avec celle détectée au démarrage. Modifications potentielles dans la configuration CAN non sauvegardés, modifications non souhaitées dans les paramètres machine, etc. Dans le mode diagnostic, vérifier si la configuration CAN détectée coïncide avec la réelle; dans ce cas, sauvegarder la configuration. Dans le cas contraire, vérifier si c’est une erreur dans le paramétrage ou dans la détection des nœuds. 'RAZ dans le nœud CAN' DÉTECTION CAUSE SOLUTION 6035 Au cours de l'exécution. Le 165 ne répond pas ou il y a des problèmes dans la communication CAN. Vérifier la connexion à travers le bus CAN et la version de la COMPCI. 'La configuration hardware ne coïncide pas avec celle enregistrée dans le fichier' DÉTECTION CAUSE 6034 Au cours du démarrage du système. Version de logiciel incompatible dans CNC et COMPCI ou modules à distance. Actualiser le logiciel de la COMPCI et les modules à distance. 'Erreur dans la configuration du clavier CAN' DÉTECTION CAUSE SOLUTION 6033 Au cours de l'exécution. Incrément de position excessive sur un axe analogique. Défaut de hardware du nœud du compteur. Consulter le service d’assistance technique. Au cours du démarrage du système. Paramétrage incorrect d’une des entrées PT100. Vérifier les paramètres machine généraux NPT100 et PT100. (REF: 1901) 'Erreur au cours de la lecture du jog local' DÉTECTION CAUSE SOLUTION Pendant l'exécution de la CNC. Erreur réitérée dans la lecture du module local de jog de l’unité centrale ICU MCU. Vérifier le hardware et la communication entre le jog local et l’unité centrale. ·173· S o l ut i o n s d ’ e r r e ur s . 6041 'Détection du clavier configuré sous le mode 15"' DÉTECTION CAUSE SOLUTION 6042 'Alarme de surcharge de courant' DÉTECTION CAUSE SOLUTION 6043 CAUSE SOLUTION SOLUTION 6050 (REF: 1901) ·174· La boucle a détecté une alarme d’amplitude Vpp dans le comptage local. Le signal sinusoïdal connecté au comptage local a une amplitude hors limites, trop petite ou trop grande. Vérifier les niveaux du signal Vpp dans le système de mesure local de la CNC. 'Court-circuit sur les I0s locaux (alarme de surcharge de courant)' DÉTECTION CAUSE SOLUTION 6051 La boucle a détecté une alarme externe dans le comptage local. Le capteur connecté au comptage local indique alarme. Vérifier le capteur branché au système de mesure local de la CNC. 'Alarme d'amplitude' DÉTECTION CAUSE CNC 8070 La boucle a détecté le câble cassé dans le signal AL du comptage local. Le comptage local de la CNC ne reçoit pas le signal AL. Vérifier le signal AL du système de mesure local de la CNC. 'Alarme externe du système de mesure' DÉTECTION CAUSE SOLUTION 6049 La boucle a détecté le câble cassé dans le signal I0 du comptage local. Le comptage local de la CNC ne reçoit pas le signal I0. Vérifier le signal I0 du système de mesure local de la CNC. 'Alarme de câble cassé dans le signal AL' DÉTECTION CAUSE SOLUTION 6048 La boucle a détecté le câble cassé dans le signal B du comptage local. Le comptage local de la CNC ne reçoit pas le signal B. Vérifier le signal B du système de mesure local de la CNC. 'Alarme de câble cassé dans le signal I0' DÉTECTION CAUSE SOLUTION 6047 La boucle a détecté le câble cassé dans le signal A du comptage local. Le comptage local de la CNC ne reçoit pas le signal A. Vérifier le signal A du système de mesure local de la CNC. 'Alarme de câble cassé dans le signal B' DÉTECTION CAUSE SOLUTION 6046 La boucle a détecté une alarme générique de câble cassé, dans l’entrée locale du système de mesure. Un des signaux du comptage local de la CNC est endommagé. Vérifier le branchement correct et les niveaux de signal du système de mesure local de la CNC. 'Alarme de câble cassé dans le signal A' DÉTECTION CAUSE SOLUTION 6045 La boucle a détecté une alarme de surcharge de courant lors de la lecture de l’entrée locale du système de mesure. Court-circuit dans le comptage local de la CNC. Vérifier le branchement correct et les niveaux de signal du système de mesure local de la CNC. 'Alarme de câble cassé' DÉTECTION 6044 Après une RAZ de la CNC. La CNC a détecté un clavier 8065 (qwerty ou jog) configuré pour se communiquer avec des versions antérieures à V04.10. Identifier les claviers 8065 (qwerty et jog) et les configurer correctement. Contacter le service d'assistance technique. Au cours du fonctionnement de la CNC. Alarme de surcharge de courant dans les I0s locaux. Vérifier le branchement et l'alimentation des I0s locaux. 'Court-circuit dans le palpeur local (alarme de surcharge de courant)' DÉTECTION CAUSE SOLUTION Pendant l'exécution de la CNC. Alarme de surcharge de courant dans le palpeur local. Vérifier le branchement et l'alimentation du palpeur local. S o l ut i o n s d ’ e r r e ur s . 6052 'Court-circuit dans la sortie analogique locale (report depuis LR)' DÉTECTION CAUSE SOLUTION 6053 'Erreur dans l'initialisation du jog local' DÉTECTION CAUSE SOLUTION 6054 SOLUTION SOLUTION Au cours de démarrage de la CNC ou après une RAZ. Lors de l'initialisation du bus CANopen, l'une des entrées paramétrées en cours n'a pas pu être correctement configurée. Vérifier le paramétrage des entrées analogiques en cours. Erreur de configuration d'un sortie analogique. DÉTECTION CAUSE SOLUTION 6061 Après une RAZ de la CNC. Lors de la réinitialisation de CANopen qui a lieu à la RAZ de la CNC, un des nœuds n’a pas réussi à parvenir à la phase opérationnelle. Vérifier le branchement et la configuration des nœuds CANopen. Erreur dans la configuration d'une entrée analogique. DÉTECTION CAUSE 6060 Pendant l'exécution de la CNC. Alarme du système de mesure dans la manivelle branchée au comptage local. Vérifier le branchement et l'alimentation des manivelles locales. 'Un des nœuds CANopen ne se trouve pas en phase opérationnelle' DÉTECTION CAUSE 6059 Pendant l'exécution de la CNC. Alarme de surcharge de courant dans la manivelle branchée au job local. Vérifier le branchement et l'alimentation des manivelles locales. 'Alarme du système de mesure dans la manivelle' DÉTECTION CAUSE SOLUTION 6058 Pendant l'exécution de la CNC. Erreur dans la lecture cyclique des manivelles locales. Vérifier le branchement et l'alimentation des manivelles locales. 'Court-circuit dans la manivelle de jog (alarme de surcharge de courant)' DÉTECTION CAUSE SOLUTION 6057 Au cours du démarrage du système. La carte locale des manivelles n’a pas pu s’initialiser correctement. Vérifier le branchement et l'alimentation de la carte des manivelles. 'Erreur dans la lecture périodique des manivelles locales' DÉTECTION CAUSE SOLUTION 6056 Au cours du démarrage du système. Le panneau local de jog n’a pas pu s’initialiser correctement. Vérifier le branchement et l'alimentation du job local. 'Erreur dans l'initialisation des manivelles locales' DÉTECTION CAUSE SOLUTION 6055 La boucle a détecté une alarme de surcharge de courant lors de l’écriture de la sortie analogique locale. Court-circuit dans la sortie analogique locale de la CNC. Vérifier le branchement de la sortie analogique de la CNC. Au cours de démarrage de la CNC ou après une RAZ. Lors de l'initialisation du bus CANopen, l'une des sorties paramétrées en cours n'a pas pu être correctement configurée. Vérifier le paramétrage des sorties analogiques en cours. Nœuds CANopen non Fagor. Option de logiciel non autorisée. DÉTECTION CAUSE SOLUTION Lors de l'initialisation du bus CANopen, pendant le démarrage de la CNC ou après un reset. Lors de l'initialisation du bus CANopen, des nœuds de tiers ont été détectés en l'absence de l'option logicielle correspondante. Déconnecter du bus CANopen les nœuds non Fagor ou acheter l'option logicielle qui permet leur utilisation. CNC 8070 (REF: 1901) ·175· S o l ut i o n s d ’ e r r e ur s . 6062 Relais d'arrêt d'urgence ouvert par erreur lors de la réinitialisation du bus. DÉTECTION CAUSE VALEUR 1 VALEUR 2 VALEUR 3 VALEUR 4 VALEUR 8 VALEUR 12 SOLUTION CNC 8070 (REF: 1901) ·176· Après un reset de la CNC ou pendant la validation des paramètres machine. Pendant le reset ou la validation de paramètres machine, il a été impossible d'achever correctement l'exécution du processus en question, à cause d'une erreur pendant le redémarrage du bus CAN ou de l'anneau Sercos. Par conséquent, le relais d'arrêt d'urgence est resté ouvert. Erreur dans Sercos pendant le reset de la CNC. Erreur dans CAN pendant le reset de la CNC. Erreur dans Sercos et CAN pendant le reset de la CNC. Erreur dans Sercos pendant un processus de validation des paramètres machine. Erreur dans CAN pendant un processus de validation des paramètres machine. Erreur dans Sercos et CAN pendant un processus de validation des paramètres machine. Corriger le problème dans CAN ou Sercos qui empêche la fermeture du relais d'arrêt d'urgence. S o l ut i o n s d ’ e r r e ur s . 7000-7999 7001 'Deux Ts consécutives dans le magasin cyclique (M6 nécessaire)' DÉTECTION CAUSE SOLUTION 7002 'L'outil n'est pas dans le magasin et les outils de terre ne sont pas autorisés' DÉTECTION CAUSE SOLUTION 7003 SOLUTION Au cours de l'exécution. Magasin en mode chargement. L'outil programmé est déjà dans le magasin. Programmer un outil qui ne soit pas chargé. CNC 8070 'En mode chargement: M6 sans T' DÉTECTION CAUSE SOLUTION 7010 Au cours de l'exécution. Magasin en mode chargement. Il n'est pas permis de programmer T0. Programmer l'outil à charger dans le magasin. 'En mode chargement: Cet outil est déjà charge' DÉTECTION CAUSE SOLUTION 7009 Au cours de l'exécution. Correcteur d'outil non valide. L’outil a moins de correcteurs que l’outil programmé. Programmer un correcteur existant ou ajouter des nouveaux correcteurs à l’outil. 'En mode chargement: T0 n'est pas admise' DÉTECTION CAUSE SOLUTION 7008 Au cours de l'exécution. L’outil programmé est usé ou a été refusé par le PLC et il n’y a pas d’autre outil de la même famille dans le magasin. Réparer l’outil ou activer dans le magasin un outil de la même famille pouvant être utilisé. 'D n'est pas admise pour cet outil' DÉTECTION CAUSE SOLUTION 7007 Au cours de l'exécution. L'outil programmé est usé ou il a été refusé par le PLC. Réparer l’outil ou utiliser un outil équivalent. 'Outil refusé ou usé et sans remplacement' DÉTECTION CAUSE 7006 Au cours de l'exécution. L'outil programmé n'est pas défini dans la table des outils. Tous les outils, même ceux de terre, doivent être définis dans la table d’outils. 'Outil de terre refusé ou usé' DÉTECTION CAUSE SOLUTION 7005 Au cours de l'exécution. On a programmé un outil qui est dans la table d’outils mais n’est pas dans la table du magasin. Dans ce cas, la CNC assume que l’outil est de terre, mais dans les paramètres machine il est spécifié que les outils de terre ne sont pas admis. Configurer la machine pour accepter des outils de terre ou inclure l’outil dans la table du magasin. 'T n'est pas définie dans la table' DÉTECTION CAUSE SOLUTION 7004 Au cours de l'exécution. Le magasin est cyclique et deux outils consécutifs sans M06 sont programmés. Dans un magasin cyclique il faut programmer M06 après chaque outil. Au cours de l'exécution. Magasin en mode chargement. Il n'est pas permis de programmer une M sans outil. Programmer l'outil à charger et ensuite la fonction M6. 'En mode chargement: T avec deux M6' DÉTECTION CAUSE SOLUTION (REF: 1901) Au cours de l'exécution. Magasin en mode chargement. Deux M6 consécutives ont été programmées sans outil. Programmer l'outil à charger et ensuite la fonction M6. ·177· S o l ut i o n s d ’ e r r e ur s . 7011 'En mode chargement: D seule n'est pas admise' DÉTECTION CAUSE SOLUTION 7012 'En mode chargement: L'outil est usé ou refusé' DÉTECTION CAUSE SOLUTION 7013 SOLUTION SOLUTION SOLUTION SOLUTION SOLUTION 7020 (REF: 1901) Au cours de l'exécution. Magasin en mode setting. Le correcteur n'est pas programmé. Programmer le correcteur. 'En mode setting: D seule n'est pas admise' DÉTECTION CAUSE SOLUTION ·178· Au cours de l'exécution. Magasin en mode setting. Il n'est pas permis de programmer T0. Programmer un outil différent de 0. 'En mode setting: D obligatoire' DÉTECTION CAUSE SOLUTION 7021 Au cours de l'exécution. Magasin en mode déchargement. Il y a deux M06 consécutives, programmées pour un même outil. Programmer l'outil à décharger et ensuite la fonction M6. 'En mode setting: T0 n'est pas admise' DÉTECTION CAUSE SOLUTION CNC 8070 Au cours de l'exécution. Magasin en mode déchargement. Il n'est pas permis de programmer une M sans outil. Programmer l'outil à décharger et ensuite la fonction M6. 'En mode déchargement: T avec deux M6' DÉTECTION CAUSE 7019 Au cours de l'exécution. Magasin en mode déchargement. Il n'est pas permis de programmer uniquement le correcteur. Cette programmation n'est pas admise. 'En mode déchargement: M6 sans T' DÉTECTION CAUSE 7018 Au cours de l'exécution. Magasin en mode déchargement. On ne peut pas programmer le correcteur avec l’outil. Cette programmation n'est pas admise. 'En mode déchargement: D seule n'est pas admise' DÉTECTION CAUSE 7017 Au cours de l'exécution. Magasin en mode déchargement. L'outil n'est pas dans le magasin. Programmer un outil valide. 'En mode déchargement: D n'est pas admise avec T' DÉTECTION CAUSE 7016 Au cours de l'exécution. Magasin en mode chargement. Le magasin est plein ou la position spécifiée est occupée. S’il n’y a pas d’espace dans le magasin il faudra décharger d’abord un outil. Si la position spécifiée est occupée, il faudra choisir un autre emplacement. 'En mode déchargement: T n'est pas dans le magasin' DÉTECTION CAUSE SOLUTION 7015 Au cours de l'exécution. Magasin en mode chargement. L’outil à charger dans le magasin est usé ou refusé. Programmer un outil valide. 'En mode chargement: Position non valide ou pas de place dans le magasin' DÉTECTION CAUSE 7014 Au cours de l'exécution. Magasin en mode chargement. Il n'est pas permis de programmer uniquement le correcteur. Cette programmation n'est pas admise. Au cours de l'exécution. Magasin en mode setting. Il n'est pas permis de programmer uniquement le correcteur. Cette programmation n'est pas admise. S o l ut i o n s d ’ e r r e ur s . 7022 'En mode setting: M6 n'est pas admise' DÉTECTION CAUSE SOLUTION 7023 'En mode chargement: M6 obligatoire' DÉTECTION CAUSE SOLUTION 7024 SOLUTION SOLUTION SOLUTION SOLUTION Au cours de l'exécution. Magasin en état d'arrêt d'urgence. Le PLC a activé une marque non valide de la manœuvre, le PLC a activé la marque SETTMEM ou il y a une erreur dans la manœuvre. Corriger dans le programme de PLC la manœuvre de changement d’outil. Si le PLC a activé la marque SETTMEM, corriger la cause du déclenchement par le PLC du signal d’arrêt d’urgence. 'M6 sans T' DÉTECTION CAUSE SOLUTION 7031 Au cours de l'exécution. Le magasin de type tourelle n’admet pas T0. Dans un magasin type tourelle, le changement d’outil se réalise en tournant la tourelle; il suffit de programmer l’outil. Cette programmation n'est pas admise. 'L’opération n’a pas pu être effectuée : Gestionnaire d’outils à l’état d’erreur' DÉTECTION CAUSE 7030 Au cours de l'exécution. Une M06 est programmée sans son outil correspondant. Il y a un paramètre machine qui indique à la CNC que faire dans cette situation, afficher une erreur, un warning ou ne rien faire. Programmer un outil puis la fonction M06 ou modifier le paramètre machine pour modifier le comportement de la CNC. 'T0 n'est pas admise' DÉTECTION CAUSE 7029 Au cours de l'exécution. Magasin en mode déchargement. L'outil n'est pas dans le magasin. Programmer l'outil à décharger dans le magasin. 'M6 sans T' DÉTECTION CAUSE 7028 Au cours de l'exécution. Magasin en mode déchargement. Deux outils consécutifs ont été programmés sans M06. Programmer M06 après chaque outil. 'En mode déchargement: Cet outil est déjà décharge' DÉTECTION CAUSE SOLUTION 7027 Au cours de l'exécution. Magasin en mode déchargement. Il n'est pas permis de programmer T0. Programmer l'outil à décharger dans le magasin. 'En mode déchargement: M6 obligatoire' DÉTECTION CAUSE 7026 Au cours de l'exécution. Magasin en mode chargement. Deux outils consécutifs ont été programmés sans M06. Programmer M06 après chaque outil. 'En mode déchargement: T0 n'est pas admise' DÉTECTION CAUSE SOLUTION 7025 Au cours de l'exécution. Magasin en mode setting. Il n'est pas permis de programmer M06. Cette programmation n'est pas admise. Au cours de l'exécution. Une M06 est programmée sans son outil correspondant. Il y a un paramètre machine qui indique à la CNC que faire dans cette situation, afficher une erreur, un warning ou ne rien faire. Programmer un outil puis la fonction M6 ou modifier le paramètre machine pour modifier le comportement de la CNC. CNC 8070 'T avec deux M6' DÉTECTION CAUSE SOLUTION Au cours de l'exécution. Il y a deux M06 consécutives, programmées pour un même outil. Programmer une M06 pour chaque outil. (REF: 1901) ·179· S o l ut i o n s d ’ e r r e ur s . 7032 'Erreur dans l'opération du PLC' DÉTECTION CAUSE SOLUTION 7033 'Le PLC a généré un arrêt d'urgence dans le magasin d'outils' DÉTECTION CAUSE SOLUTION 7034 SOLUTION SOLUTION SOLUTION SOLUTION CNC 8070 SOLUTION (REF: 1901) ·180· Au cours de l'exécution. Un correcteur est programmé et il n’y a pas d’outil actif sur la broche. Mettre un outil dans la broche. 'POS programmée et le magasin n'est pas en mode CHARGEMENT' DÉTECTION CAUSE 7043 Au cours de l'exécution. Magasin asynchrone ou synchrone avec bras échangeur. Le magasin demande le même outil qui est sur le bras 1. Renvoyer l’outil du bras au magasin et continuer normalement le changement d’outil. 'Il n'y a pas d'outil actif' DÉTECTION CAUSE SOLUTION 7042 Au cours de l'exécution. Magasin asynchrone ou synchrone avec bras échangeur. Le magasin demande le même outil qui est sur le bras 2. Renvoyer l’outil du bras au magasin et continuer normalement le changement d’outil. 'Erreur dans l'opération: Vider d'abord le bras 1' DÉTECTION CAUSE 7041 Au cours de l'exécution. Pour changer le mode du magasin au mode chargement ou déchargement, la broche et les bras dans les magasins (là où il a lieu) doivent être vides. Vider la broche et les bras. 'Il ne peut pas y avoir d'outil sur la broche et sur le bras 2 simultanément' DÉTECTION CAUSE 7040 Pendant l'édition ou l'exécution des tables. Pour des raisons de sécurité, on ne peut pas changer la famille d’un outil qui se trouve dans le magasin. Décharger d'abord l'outil. 'La broche doit être vide pour les modes CHARGEMENT ou DÉCHARGEMENT' DÉTECTION CAUSE 7039 Au cours de l'exécution. Erreur dans le magasin pendant une manœuvre. Vérifier l'état du magasin. Il se peut qu’il n’y ait pas d’espace libre dans le magasin. 'On n'admet pas de changement de famille pour des outils dans le magasin ou sur la broche' DÉTECTION CAUSE 7037 Au cours de l'exécution. La manœuvre du PLC provoque une erreur. Vérifier le programme de PLC. 'Erreur dans la table d'emmagasinage' DÉTECTION CAUSE SOLUTION 7036 Si le PLC et en fonctionnement. Le PLC active le signal d’arrêt d’urgence dans le gestionnaire d’outils. Désactiver l’arrêt d’urgence et analyser les causes de son activation par le PLC. 'Erreur d'opération: Il est impossible de trouver de la place dans le magasin' DÉTECTION CAUSE SOLUTION 7035 Au cours de l'exécution. Séquence erronée dans le programme du PLC. Vérifier le programme de PLC. Au cours de l'exécution. Une position de magasin est programmée et le gestionnaire n’est pas en mode chargement. La programmation de la position de chargement n’est admise qu’en mode chargement. 'L'outil demandé est l'outil actif d'un autre canal' DÉTECTION CAUSE SOLUTION Au cours de l'exécution. L’outil programmé est l’outil actif dans un autre canal. Décharger l'outil de l'autre canal. S o l ut i o n s d ’ e r r e ur s . 7044 'Le nombre d'arêtes de l'outil actif ne peut pas être modifié' DÉTECTION CAUSE SOLUTION 7051 Au cours de l'exécution. Vous avez essayé de changer le nombre d’arêtes d’un outil et cet outil est actif sur un canal. Placer l’outil dans le magasin ou à terre pour modifier le nombre d’arêtes. 'Numéro d'arête non valide' DÉTECTION CAUSE SOLUTION Au cours de l'exécution. L’outil a moins d'arêtes que l’outil programmé. Programmer une arête existante ou ajouter de nouvelles arêtes à l’outil. CNC 8070 (REF: 1901) ·181· S o l ut i o n s d ’ e r r e ur s . 8000-8999 8000 'Le Kernel de simulation n'est pas activé' DÉTECTION CAUSE SOLUTION 8001 'Le Kernel de simulation n'est pas activé' DÉTECTION CAUSE SOLUTION 8002 SOLUTION SOLUTION SOLUTION CNC 8070 (REF: 1901) ·182· Au cours du démarrage du système. Erreur dans la préparation du processus de chargement de la COMPCI ou des modules à distance. Vérifier la reconnaissance de la COMPCI, la valeur du paramètre CANMODE et l’installation du driver de communications. 'Erreur au cours du chargement du programme de la COMPCI' DÉTECTION CAUSE SOLUTION 8008 Au cours de l'exécution. Il n’est pas permis de changer de mode si un canal du groupe est en exécution. Arrêter les programmes en exécution de tous les canaux du groupe. 'Erreur en initiant le processus de chargement' DÉTECTION CAUSE 8007 Au cours de l'exécution. Il n’est pas permis de fermer la CNC si un canal est en exécution, interrompu ou a un axe occupé en motion control. Arrêter les programme en exécution. 'Changement de mode non permis pendant qu’un canal du groupe est en exécution' DÉTECTION CAUSE SOLUTION 8006 Au cours de l'exécution. Il n’est pas permis de mettre la CNC hors tension si elle est en exécution, interrompue ou a un axe occupé en motion control. Arrêter les programme en exécution. 'Fermeture interdite alors qu'un canal est en cours d'exécution ou interrompu' DÉTECTION CAUSE 8005 Au cours du démarrage du système. LA CNC n’a pas pu registrer une des touches logiciel ou des touches de raccourci. Vérifier si la CNC a démarré correctement. 'Fermeture interdite si la CNC est en exécution ou interruption' DÉTECTION CAUSE 8004 Au cours du démarrage du système. Le Kernel de simulation est démarré mais n’est pas activé. Vérifier si la CNC a démarré correctement. 'Erreur en registrant la touche' DÉTECTION CAUSE SOLUTION 8003 Au cours du démarrage du système. Le Kernel de simulation est démarré mais n’est pas activé. Vérifier si la CNC a démarré correctement. Mettre la CNC hors et sous tension. Si l’erreur persiste, veuillez contacter le service après-vente. Au cours du démarrage du système. Erreur au cours du processus de chargement de la COMPCI. Vérifier la reconnaissance et l’installation correcte de la COMPCI. Contacter le service d'assistance technique. 'Erreur au cours de l'emmagasinage de la configuration du système' DÉTECTION CAUSE SOLUTION Au cours du démarrage du système. Erreur dans la configuration CAN pendant le processus de chargement. Depuis le mode diagnostic, vérifier la configuration CAN et la comparer avec la réelle, pour déterminer s’il y a un problème dans la détection des nœuds. S o l ut i o n s d ’ e r r e ur s . 8009 'Erreur chargement logiciel des nœuds IO' DÉTECTION CAUSE SOLUTION 8010 'Erreur au cours du chargement logiciel de clavier' DÉTECTION CAUSE SOLUTION 8011 SOLUTION SOLUTION SOLUTION En essayant de fermer la CNC. L’utilisateur a essayé de mettre la CNC hors tension alors qu’il y avait une broche synchronisée. Désynchroniser la broche. 'On ne peut pas générer le PLC alors qu'il est en cours d'exécution ou interrompu' DÉTECTION CAUSE SOLUTION 8019 En essayant de fermer la CNC. L’utilisateur a essayé de mettre la CNC hors tension alors qu’il y avait une broche en déplacement. Arrêter le déplacement de la broche. Fermeture non permise: Broche en synchronisation' DÉTECTION CAUSE 8018 En essayant de fermer la CNC. L’utilisateur a essayé de mettre la CNC hors tension alors qu’un axe est en déplacement ou synchronisé. Arrêter le déplacement des axes ou désynchroniser l’axe. 'Fermeture non permise: Broche en marche' DÉTECTION CAUSE 8017 Au cours du démarrage du système. Erreur au cours du processus de chargement des nœuds RIOS (I/Os CANopen). Vérifier la configuration CAN, la connexion du système et les versions de boot des nœuds à distance. Si l’erreur persiste, veuillez contacter le service après-vente. 'Fermeture non permise: Axe en déplacement ou en synchronisation' DÉTECTION CAUSE 8016 Au cours du démarrage du système. Erreur au cours du processus de chargement du nœud du clavier de 10". Vérifier la configuration CAN, la connexion du système et les versions de boot des nœuds à distance. Si l’erreur persiste, veuillez contacter le service après-vente. 'Erreur au cours du chargement logiciel de RIOS' DÉTECTION CAUSE SOLUTION 8015 Au cours du démarrage du système. Erreur au cours du processus de chargement des nœuds du compteur. Vérifier la configuration CAN, la connexion du système et les versions de boot des nœuds à distance. Si l’erreur persiste, veuillez contacter le service après-vente. 'Erreur au cours du chargement des claviers compacts' DÉTECTION CAUSE SOLUTION 8014 Au cours du démarrage du système. Erreur au cours du processus de chargement des nœuds du compteur. Vérifier la configuration CAN, la connexion du système et les versions de boot des nœuds à distance. Si l’erreur persiste, veuillez contacter le service après-vente. 'Erreur au cours du chargement logiciel des compteurs' DÉTECTION CAUSE SOLUTION 8013 Au cours du démarrage du système. Erreur au cours du processus de chargement du nœud du clavier de 12". Vérifier la configuration CAN, la connexion du système et les versions de boot des nœuds à distance. Si l’erreur persiste, veuillez contacter le service après-vente. 'Erreur au cours du chargement logiciel des compteurs' DÉTECTION CAUSE SOLUTION 8012 Au cours du démarrage du système. Erreur au cours du processus de chargement des nœuds des I/Os. Vérifier la configuration CAN, la connexion du système et les versions de boot des nœuds à distance. Si l’erreur persiste, veuillez contacter le service après-vente. En essayant de compiler le PLC. Il n’est pas permis de compiler le PLC si la CNC est en exécution ou interrompue. Arrêter les programme en exécution. 'On ne peut pas générer le PLC alors qu'un canal est en cours d'exécution ou interrompu' DÉTECTION CAUSE SOLUTION CNC 8070 (REF: 1901) En essayant de compiler le PLC. Il n’est pas permis de compiler le PLC si un canal est en exécution ou interrompu. Arrêter les programme en exécution. ·183· S o l ut i o n s d ’ e r r e ur s . 8020 'Il n’est pas permis de générer le PLC: Axe en déplacement ou en synchronisation' DÉTECTION CAUSE SOLUTION 8021 'Il n’est pas permis de générer le PLC : Broche en marche' DÉTECTION CAUSE SOLUTION 8022 SOLUTION SOLUTION CNC 8070 ·184· Au cours du démarrage du système. La CNC n’a pas trouvé le dossier où est installé le compilateur de PLC. Contacter le service d'assistance technique. 'Includes" du PLC non disponibles' DÉTECTION CAUSE (REF: 1901) Au cours du démarrage du système. Le kernel est démarré mais n’est pas activé. Vérifier si la CNC a démarré correctement. Mettre la CNC hors et sous tension. Si l’erreur persiste, veuillez contacter le service après-vente. 'Compilateur non disponible' DÉTECTION CAUSE SOLUTION 8029 Pendant l’édition de programmes, de programme PLC ou de paramètres machine. La CNC est en mode utilisateur, avec la protection d’OEM activée, ce qui implique que tout changement sera temporaire et disparaîtra à la mise hors tension de la CNC. Mettre la CNC hors tension et utiliser l’utilité DiskMonitor pour passer au mode mise au point. Redémarrer la CNC. 'Erreur lors du démarrage de Kernel' DÉTECTION CAUSE SOLUTION 8028 Au cours de l'exécution. La CNC a détecté un changement de date et d’heure et les a restaurés à leurs valeurs souhaitées. Vérifier si la date et l’heure sont correctes. Si l’erreur persiste, veuillez contacter le service après-vente. 'Protection d’OEM activée: Les changements auront un caractère temporaire' DÉTECTION CAUSE 8027 Au démarrage du système, en mode mise en point. La CNC a démarré en mode mise au point et travaille avec le disque dur déprotégé. Si on ne va pas effectuer la mise au point de la CNC, la mettre hors tension et utiliser l’utilité DiskMonitor pour passer au mode utilisateur et travailler avec le disque protégé. Redémarrer la CNC. 'On a détecté un changement de date et il a été nécessaire de la restaurer' DÉTECTION CAUSE 8026 Au cours du démarrage du système. La CNC a détecté moins de 50 MB de mémoire libre dans le disque. Vérifier si une application de tiers est lancée et consomme des ressources du système et le cas échéant, la fermer. Mettre la CNC hors et sous tension. Si l’erreur persiste, veuillez contacter le service après-vente. 'La CNC travaille sous le Mode Mise au Point' DÉTECTION. CAUSE SOLUTION 8025 En essayant de compiler le PLC. Il n’est pas permis de compiler le PLC s’il y a une broche synchronisée. Désynchroniser la broche. 'Mémoire en disque au-dessous du minimum préconisé' DÉTECTION CAUSE SOLUTION 8024 En essayant de compiler le PLC. Il n’est pas permis de compiler le PLC si une broche est en déplacement. Arrêter le déplacement de la broche. 'Il n’est pas permis de générer le PLC : Broche en synchronisation' DÉTECTION CAUSE SOLUTION 8023 En essayant de compiler le PLC. Il n’est pas permis de compiler le PLC s’il y a un axe un axe en déplacement ou synchronisé. Arrêter le déplacement des axes ou désynchroniser l’axe. SOLUTION Au cours du démarrage du système. La CNC n’a pas trouvé le dossier où sont installés les includes nécessaires pour compiler le PLC. Contacter le service d'assistance technique. S o l ut i o n s d ’ e r r e ur s . 8030 'Bibliothèques du PLC non disponibles' DÉTECTION CAUSE SOLUTION 8031 Le dossier DRIVERS n'existe pas' DÉTECTION CAUSE SOLUTION 8032 SOLUTION SOLUTION Au cours de l'exécution. La CNC a détecté que la mémoire RAM disponible est inférieur à 10% de la mémoire RAM totale. Vérifier si une application de tiers est lancée et consomme des ressources du système et le cas échéant, la fermer. Mettre la CNC hors et sous tension. Si l’erreur persiste, veuillez contacter le service après-vente. 'MDI n'est pas admis à l'INSPECTION dans l'état actuel' DÉTECTION CAUSE SOLUTION 8039 Au démarrage du système, en mode setup. Il n'est permis de travailler avec la CNC que dans les modes utilisateur et mise au point. Utiliser l’utilité DiskMonitor pour passer au mode utilisateur ou mise au point et redémarrer la CNC. 'Mémoire au-dessous du minimum préconisé. Il faut réinitialiser la CNC' DÉTECTION CAUSE 8038 Au démarrage d’une CNC ouverte, en mode mise au point. Les codes d’accès indiqués dans l’avis ne sont pas définis. Avec la CNC démarrée, accéder au mode utilités et depuis l’option "Codes d’accès" du menu de touches logiciel saisir les codes indiqués. 'Pour travailler avec la CNC, passer au Mode Utilisateur ou Mode Mise au Point' DÉTECTION CAUSE 8037 Au démarrage du système, en mode mise en point. La CNC n’a trouvé aucune copie de sécurité de la mise au point. En mettant la CNC hors tension, sélectionner l’option "Fermer et faire copie de sécurité", pour que la CNC fasse une copie de sécurité de la mise au point. 'Les passwords d'accès suivants ne sont pas encore définis' DÉTECTION CAUSE SOLUTION 8036 Au cours du démarrage du système. La CNC n’a pas trouvé le dossier de travail de l’utilisateur (C:\CNC8070\Users). Depuis le mode utilités, utiliser l’option "Nouveau répertoire" du menu de touches logiciel pour créer le dossier. 'Mise au point incomplète : Aucune copie de sécurité a été trouvée' DÉTECTION CAUSE SOLUTION 8035 Au cours du démarrage du système. La CNC n’a pas trouvé le dossier où sera situé le PLC une fois généré (C:\CNC8070\Drivers). Depuis le mode utilités, utiliser l’option "Nouveau répertoire" du menu de touches logiciel pour créer le dossier. 'Le dossier USERS n'existe pas' DÉTECTION CAUSE SOLUTION 8034 Au cours du démarrage du système. La CNC n’a pas trouvé le dossier où sont installées les bibliothèques nécessaires pour compiler le PLC. Contacter le service d'assistance technique. Au cours de l'édition et exécution dans le mode MDI/MDA. Il est interdit d'entrer dans le mode MDI/MDA depuis l'état actuel de l'inspection d'outil. Sortir du mode inspection d'outil pour accéder au mode MDI/MDA. 'Erreur au cours du chargement logiciel de clavier' DÉTECTION CAUSE SOLUTION Au cours du démarrage de la CNC. Erreur pendant le processus de chargement du logiciel du nœud clavier. Vérifier la configuration CAN, la connexion du système et les versions de boot des nœuds à distance. Si l’erreur persiste, veuillez contacter le service après-vente. CNC 8070 (REF: 1901) ·185· S o l ut i o n s d ’ e r r e ur s . 8040 'Mémoire dans le disque au-dessous du minimum préconisé pour le bon fonctionnement de la CNC. Avant de démarrer la CNC, libérer la mémoire dans le disque' DÉTECTION CAUSE SOLUTION 8041 'Mémoire au-dessous du minimum préconisé pour l'exécution' DÉTECTION CAUSE SOLUTION 8042 SOLUTION CNC 8070 SOLUTION (REF: 1901) ·186· Au cours du démarrage de la CNC ou pendant l'exécution. La CNC a détecté que le code de validation temporaire a expiré. La CNC ne permettra pas le fonctionnement jusqu'à ce que l'utilisateur ne réinitialise pas la CNC. Réinitialiser la CNC. 'Le code de validation temporaire a été annulé. Réinitialiser la CNC' DÉTECTION CAUSE 8047 Pendant l'édition ou l'exécution. Le programme conversationnel a plus de 10 MB. Passer au mode CNC standard pour éditer ou exécuter le programme. 'Le code de validation a expiré. Réinitialiser la CNC' DÉTECTION CAUSE 8046 Au cours de l'édition. Mémoire insuffisante pour charger le fichier. Il faut libérer la mémoire pour charger le fichier. • Vérifier si la CNC est en cours d'exécuter un programme et dans ce cas, arrêter l'exécution et essayer à nouveau de charger le programme. • Vérifier si une application de tiers est lancée et consomme des ressources du système et le cas échéant, la fermer. • Mettre la CNC hors et sous tension. Si l’erreur persiste, veuillez contacter le service après-vente. 'Programme trop grand pour être édité en mode conversationnel. Passer au mode CNC standard pour son édition ou exécution' DÉTECTION CAUSE SOLUTION 8045 Au cours de l'exécution. La CNC a détecté moins de 50 MB de mémoire libre dans le disque. Il faut libérer la mémoire dans le disque dur pour pouvoir démarrer la CNC. • Vérifier si une application de tiers est lancée et consomme des ressources du système et le cas échéant, la fermer. • Mettre la CNC hors et sous tension. Si l’erreur persiste, veuillez contacter le service après-vente. 'Mémoire insuffisante pour charger le fichier' DÉTECTION CAUSE SOLUTION 8044 Au cours de l'exécution. La CNC a détecté moins de 50 MB de mémoire libre dans le disque. Il faut libérer la mémoire dans le disque dur pour pouvoir démarrer la CNC. • Vérifier si une application de tiers est lancée et consomme des ressources du système et le cas échéant, la fermer. • Mettre la CNC hors et sous tension. Si l’erreur persiste, veuillez contacter le service après-vente. 'Mémoire au-dessous du minimum préconisé' DÉTECTION CAUSE SOLUTION 8043 Au cours du démarrage de la CNC. La CNC a détecté moins de 50 MB de mémoire libre dans le disque. Il faut libérer la mémoire dans le disque dur pour pouvoir démarrer la CNC. • Vérifier si une application de tiers est lancée et consomme des ressources du système et le cas échéant, la fermer. • Mettre la CNC hors et sous tension. Si l’erreur persiste, veuillez contacter le service après-vente. Au cours de l'exécution. La CNC a détecté que le code de validation temporaire a été annulé par l'utilisateur. La CNC ne permettra pas le fonctionnement jusqu'à ce que l'utilisateur ne réinitialise pas la CNC. Réinitialiser la CNC. 'La CNC travaille de manière NON sûre' DÉTECTION CAUSE SOLUTION Au cours du démarrage de la CNC. La CNC travaille sous le mode Setup (mise au point). Mettre la CNC hors tension et utiliser la fonction DiskMonitor pour passer au mode Utilisateur. S o l ut i o n s d ’ e r r e ur s . 8048 'Mise au point incomplète' DÉTECTION CAUSE SOLUTION Au cours du démarrage de la CNC. Sous le mode Utilisateur, une des conditions suivantes est accomplie: • Les mots de passe de protection ne sont pas définis. • Il n'y a pas de copie de sécurité. Pour achever la mise au point, suivre les pas suivants. 1. Mettre la CNC hors tension et utiliser l’utilité DiskMonitor pour passer au mode mise au point (setup). 2. Sous le mode fonctions, entrer dans la fenêtre de codes d'accès et saisir le "Code d'accès général". 3. Taper sur [ALT][F4] pour mettre la CNC hors tension et sélectionner l'option "Fermer et faire une copie de sécurité". 4. Utiliser la fonction DiskMonitor pour passer au mode Utilisateur. 8050 'Erreur au cours du chargement logiciel de RIOR' DÉTECTION CAUSE SOLUTION 8051 'Erreur restauration de la session d'Utilisateur en cours' DÉTECTION CAUSE SOLUTION 8200 SOLUTION SOLUTION SOLUTION Au cours de l'édition. Le caractère de fermeture de commentaire a été programmé sans avoir programmé avant le caractère de commencement. Vérifier que les commentaires ont le caractère d’ouverture "(" et le caractère de fermeture ")". 'Il manque '$' ou '#'' DÉTECTION CAUSE SOLUTION 8205 Au cours de l'édition et exécution dans MDI. Erreur en convertissant une chaîne de caractères à une valeur numérique. Une valeur programmée dans l'instruction ou la variable n’est pas correcte. Vérifier dans le manuel de programmation, les valeurs admissibles pour les paramètres de l'instruction ou les indices de la variable. 'Il manque l'ouverture des commentaires' DÉTECTION CAUSE 8204 Au cours de l'édition et exécution dans MDI. Erreur en convertissant une chaîne de caractères à une valeur numérique. Une valeur programmée dans l'instruction ou la variable n’est pas correcte. Vérifier dans le manuel de programmation, les valeurs admissibles pour les paramètres de l'instruction ou les indices de la variable. 'Défaut du lexer en reconnaissant les flottants' DÉTECTION CAUSE 8203 Au cours du démarrage de la CNC. Un des fichiers de la session d'utilisateur n'est pas accessible ou il est corrompu. Les données de la CNC relatives aux cotes, décalages d’origines, compteur de pièces, cinématiques, etc. peuvent être perdues. Si l’erreur est répétée à plusieurs démarrages successifs de la CNC, veuillez contacter votre fournisseur. 'Défaut du lexer en reconnaissant des nombres entiers' DÉTECTION CAUSE 8201 Au cours du démarrage de la CNC. Erreur au cours du processus de chargement du logiciel des nœuds RIOR. Vérifier la configuration CAN, la connexion du système et les versions de boot des nœuds à distance. Si l’erreur persiste, veuillez contacter le service après-vente. Au cours de l'édition et exécution dans MDI. Une instruction a été programmée sans le caractère "#" ou une instruction de contrôle de flux sans le caractère "$". Toute instruction doit commencer par le caractère "#" et toute instruction de contrôle de flux par le caractère "$". CNC 8070 'Il manque '$'' DÉTECTION CAUSE SOLUTION Au cours de l'édition. Une instruction de contrôle a été programmée sans le caractère de commencement "$". Programmer "$" avant le nom de l’instruction de contrôle. (REF: 1901) ·187· S o l ut i o n s d ’ e r r e ur s . 8206 'Il manque '#'' DÉTECTION CAUSE SOLUTION 8207 'Nom de programme ou de sous-routine trop long' DÉTECTION CAUSE SOLUTION 8209 CNC 8070 (REF: 1901) ·188· Pendant l’édition et l’exécution. La syntaxe de l'instruction n'est pas correcte. Vérifier dans le manuel de programmation la syntaxe de l'instruction. 'Caractère non valide' DÉTECTION CAUSE SOLUTION 8219' Pendant l’édition et l’exécution. La syntaxe de l'instruction n'est pas correcte. Vérifier dans le manuel de programmation la syntaxe de l'instruction. Les limites pour les flottants sont excédées' DÉTECTION CAUSE SOLUTION 8218 Au cours de l'édition. L’instruction programmée après le caractère "$" n’est pas correcte. Vérifier la syntaxe de l’instruction. 'Le format pour la fonction est excédé' DÉTECTION CAUSE SOLUTION 8217 Au cours de l'édition. Nombre maximum de chiffres permis pour la partie décimale d’un numéro dépassé. Le nombre maximum de chiffres permis pour la partie décimale d’un nombre est 5. 'Instruction de contrôle de flux inconnue' DÉTECTION CAUSE SOLUTION 8215 Au cours de l'édition. La partie décimale d'un numéro a une valeur non valide. Le rang de valeurs valides pour la partie décimale d’un numéro est ±0.99999. 'Format excédé pour partie fractionnaire' DÉTECTION CAUSE SOLUTION 8214 Au cours de l'édition. La partie entière d'un numéro a une valeur non valide. Le rang de valeurs valides pour la partie entière d’un numéro est ±99999. 'Les limites pour partie fractionnaire sont dépassées' DÉTECTION CAUSE SOLUTION 8213 Au cours de l'édition. Un nombre entier trop élevé a été programmé. La valeur maximale admissible pour une valeur entière est 4294967295. 'Les limites pour partie entière sont dépassées' DÉTECTION CAUSE SOLUTION 8212 Au cours de l'édition. Le nom de l’axe a été programmé avec un caractère générique non valide. Les noms d’axe avec caractère générique valides sont @1 à @5. 'Les limites pour nombres entiers sont dépassées' DÉTECTION CAUSE SOLUTION 8211 Au cours de l'édition. Nombre maximum de caractères permis pour le nom de programme ou sous-routine dépassé. Le nombre maximum de caractères permis est 14. 'Axe actif invalide' DÉTECTION CAUSE SOLUTION 8210 Au cours de l'édition. Une instruction a été programmée sans le caractère de commencement "#". Programmer "#" avant le nom de l’instruction. Au cours de l'édition. Détection de caractère non valide dans le bloc. Vérifier la syntaxe du bloc. 'Chaîne d’erreur vide' DÉTECTION CAUSE SOLUTION Pendant l’édition et l’exécution. La syntaxe de l'instruction n'est pas correcte. Vérifier dans le manuel de programmation la syntaxe de l'instruction. S o l ut i o n s d ’ e r r e ur s . 8220 'Chaîne de Warning vide' DÉTECTION CAUSE SOLUTION 8221 'Erreur syntactique' DÉTECTION CAUSE SOLUTION 8222 SOLUTION SOLUTION Pendant l’édition et l’exécution. La syntaxe de l'instruction n'est pas correcte. Vérifier dans le manuel de programmation la syntaxe de l'instruction. CNC 8070 'Vitesse F programmée en double' DÉTECTION CAUSE SOLUTION 8232 Au cours de l'édition. Un numéro d'outil négatif a été programmé. Le numéro d’outil doit toujours être positif ou nul. 'F ou E hors gamme' DÉTECTION CAUSE SOLUTION 8230 Au cours de l'édition. Une vitesse de broche négative a été programmée sans avoir programmé la fonction G63 dans le bloc. La vitesse de broche doit être positive ; la valeur négative n’est permise que si elle est programmée dans le même bloc que la fonction G63. 'Numéro d’outil hors de gamme' DÉTECTION CAUSE SOLUTION 8229 Au cours de l'édition. La fonction H programmée n'existe pas. Vérifier dans le manuel de programmation les fonctions H existantes. 'Avec G63 il n'est permis qu'une S négative' DÉTECTION CAUSE 8228 Au cours de l'édition et exécution dans MDI. La fonction G programmée n'existe pas. Vérifier dans le manuel de programmation les fonctions G existantes. 'Fonction H hors de rang' DÉTECTION CAUSE SOLUTION 8227 Au cours de l'édition. La fonction M programmée n'existe pas. Vérifier dans le manuel de programmation les fonctions M existantes. 'Fonction G hors de rang' DÉTECTION CAUSE SOLUTION 8226 Au cours de l'édition et exécution dans MDI. Il y a une fonction M programmée plus d’une fois dans le même bloc ou il y a deux fonctions M incompatibles dans le même bloc. Une fonction M ne doit être programmée qu’une fois dans le bloc. Vérifier le manuel de programmation pour examiner l’exclusivité mutuelle des fonctions M. 'Fonction M hors de rang' DÉTECTION CAUSE SOLUTION 8225 Au cours de l'édition. La fonction M programmée n'existe pas. Vérifier dans le manuel de programmation les fonctions M existantes. 'Exclusivité mutuelle ou fonctions M égales’ DÉTECTION CAUSE 8224 Au cours de l'édition et exécution dans MDI. La syntaxe de l'instruction ou variable programmée n’est pas correcte. Vérifier dans le manuel de programmation la syntaxe de l'instruction ou variable. 'Fonction M inexistante' DÉTECTION CAUSE SOLUTION 8223 Pendant l’édition et l’exécution. La syntaxe de l'instruction n'est pas correcte. Vérifier dans le manuel de programmation la syntaxe de l'instruction. Au cours de l'édition. La fonction F est programmée plus d’une fois dans le bloc. Programmer la fonction F une seule fois dans le bloc. 'A programmée en double' DÉTECTION CAUSE SOLUTION (REF: 1901) Au cours de l'édition. L’axe A est programmé plus d’une fois dans le bloc. Programmer l'axe A une seule fois dans le bloc. ·189· S o l ut i o n s d ’ e r r e ur s . 8233 'B programmée en double' DÉTECTION CAUSE SOLUTION 8234 'C programmée en double' DÉTECTION CAUSE SOLUTION 8235 SOLUTION CNC 8070 (REF: 1901) ·190· Au cours de l'édition et exécution dans MDI. Les paramètres de l'instruction programmée doivent être programmés entre crochets. La variable exige la programmation d’un indice entre crochets. Vérifier dans le manuel de programmation la syntaxe de l'instruction ou variable. 'I programmée en double' DÉTECTION CAUSE SOLUTION 8244 Au cours de l'exécution. Une valeur trop élevée a été programmée pour un paramètre de l'instruction. Programmer une valeur inférieure pour le paramètre dans l'instruction. 'Il manque crochet' DÉTECTION CAUSE 8243 Au cours de l'édition. L’axe Z est programmé plus d’une fois dans le bloc. Programmer l'axe Z une seule fois dans le bloc. 'Paramètre hors de rang' DÉTECTION CAUSE SOLUTION 8242 Au cours de l'édition. L’axe Y est programmé plus d’une fois dans le bloc. Programmer l'axe Y une seule fois dans le bloc. 'Z programmée en double' DÉTECTION CAUSE SOLUTION 8241 Au cours de l'édition. L’axe X est programmé plus d’une fois dans le bloc. Programmer l'axe X une seule fois dans le bloc. 'Y programmée en double' DÉTECTION CAUSE SOLUTION 8240 Au cours de l'édition. L’axe W est programmé plus d’une fois dans le bloc. Programmer l'axe W une seule fois dans le bloc. 'X programmée en double' DÉTECTION CAUSE SOLUTION 8239 Au cours de l'édition. L’axe V est programmé plus d’une fois dans le bloc. Programmer l'axe V une seule fois dans le bloc. 'W programmée en double' DÉTECTION CAUSE SOLUTION 8238 Au cours de l'édition. L’axe U est programmé plus d’une fois dans le bloc. Programmer l'axe U une seule fois dans le bloc. 'V programmée en double' DÉTECTION CAUSE SOLUTION 8237 Au cours de l'édition. L’axe C est programmé plus d’une fois dans le bloc. Programmer l'axe C une seule fois dans le bloc. 'U programmée en double' DÉTECTION CAUSE SOLUTION 8236 Au cours de l'édition. L’axe B est programmé plus d’une fois dans le bloc. Programmer l'axe B une seule fois dans le bloc. Au cours de l'édition. Le paramètre I est programmé plus d’une fois dans le bloc. Programmer le paramètre I une seule fois dans le bloc. 'J programmée en double' DÉTECTION CAUSE SOLUTION Au cours de l'édition. Le paramètre J est programmé plus d’une fois dans le bloc. Programmer le paramètre J une seule fois dans le bloc. S o l ut i o n s d ’ e r r e ur s . 8245 'K programmée en double' DÉTECTION CAUSE SOLUTION 8247 'Uniquement R1 peut pas faire partie des expressions' DÉTECTION CAUSE SOLUTION 8250 SOLUTION Au cours de l'édition et exécution dans MDI. Instruction #TIME programmée incorrectement. Cette instruction #TIME se programme de la façon #TIME [<time>] (les crochets sont optionnels), où le paramètre <time> peut être un nombre entier, un paramètre arithmétique ou une variable. 'Mot inconnu ou incomplet' DÉTECTION CAUSE SOLUTION 8267 Au cours de l'édition. Il y a un caractère incorrect dans le nom du programme principal ou de la sousroutine. La définition du nom du programme principal ou de la sous-routine ne peut être accompagnée que de commentaire. Les caractères interdits sont: • Programme principal: \ / : * ? " < > | et espace en blanc. • Sous-routine locale: / ? " < > | ) et espace en blanc. 'On attendait une expression après #TIME' DÉTECTION CAUSE SOLUTION 8265 Au cours de l'édition et exécution dans MDI. L'instruction programmée n’existe pas. Vérifier le manuel de programmation. 'Il ne peut rien y avoir après le nom du programme ou de la sous-routine' DÉTECTION CAUSE 8258 Au cours de l'édition. Certains paramètres programmés pour la fonction G20 sont interdits. Réviser la syntaxe de programmation de la fonction G 20. 'Instruction de cycle d’interpolateur inexistante' DÉTECTION CAUSE SOLUTION 8257 Au cours de l'édition. Tous les paramètres obligatoires n’ont pas été programmés dans la fonction G20. Réviser la syntaxe de programmation de la fonction G 20. 'Trop d'axes dans G20' DÉTECTION CAUSE SOLUTION 8256 Au cours de l'édition. La variable n'a pas permission d'écriture. La variable est uniquement de lecture. 'Il manque des axes dans G20' DÉTECTION CAUSE SOLUTION 8254 Au cours de l'édition. La variable n'a pas permission d'écriture. La variable est uniquement de lecture. 'Variable globale sans permission d'écriture' DÉTECTION CAUSE SOLUTION 8253 Au cours de l'édition. La programmation du rayon est incorrecte. Le rayon ne peut pas être programmé avec "R" ou "R1". 'Variable d'axe sans permission d'écriture' DÉTECTION CAUSE SOLUTION 8251 Au cours de l'édition. Le paramètre K est programmé plus d’une fois dans le bloc. Programmer le paramètre K une seule fois dans le bloc. Au cours de l'édition. Les possibles causes sont les suivantes: • La fonction, instruction ou expression programmée n’est pas valide. • Programmation incorrecte de la fonction M pour une certaine broche. • Programmation incorrecte de l'instruction #TOOL AX. Vérifier dans le manuel de programmation la syntaxe de l'instruction, la fonction ou l’expression à programmer. CNC 8070 (REF: 1901) 'Variable de cycle sans permission d'écriture' DÉTECTION CAUSE SOLUTION Au cours de l'édition. La variable n'a pas permission d'écriture. La variable est uniquement de lecture. ·191· S o l ut i o n s d ’ e r r e ur s . 8268 'Argument hors de limites dans la fonction' DÉTECTION CAUSE SOLUTION 8269 'Dépassement au-dessus dans la fonction' DÉTECTION CAUSE SOLUTION 8270 8279 ·192· Au cours de l'édition. Le nombre maximum de fonctions H permises sur un même bloc est dépassé. Le nombre maximum de fonctions H permises sur un même bloc est 7. 'Image miroir dépassée' DÉTECTION CAUSE SOLUTION (REF: 1901) Au cours de l'édition. Le nombre maximum de fonctions M permises sur un même bloc est dépassé. Le nombre maximum de fonctions M permises sur un même bloc est 7. 'Limite de fonctions H dans un même bloc dépassée' DÉTECTION CAUSE SOLUTION CNC 8070 Au cours de l'édition. L’argument programmé dans la fonction mathématique n’est pas valide. Programmer un argument correct dans la fonction mathématique (LN, LOG, SQRT, EXP, DEXP, SIN, COS, TAN, ASIN, ACOS, ATAN). 'Limite de fonctions M dans un même bloc dépassée' DÉTECTION CAUSE SOLUTION 8276 Au cours de l'édition. L’argument programmé dans la fonction mathématique n’est pas valide. Programmer un argument correct dans la fonction mathématique (LN, LOG, SQRT, EXP, DEXP, SIN, COS, TAN, ASIN, ACOS, ATAN). 'Type inconnu d’exception' DÉTECTION CAUSE SOLUTION 8275 Au cours de l'édition. L’argument programmé dans la fonction mathématique n’est pas valide. Programmer un argument correct dans la fonction mathématique (LN, LOG, SQRT, EXP, DEXP, SIN, COS, TAN, ASIN, ACOS, ATAN). 'Dépassement en dessous dans la fonction' DÉTECTION CAUSE SOLUTION 8274 Au cours de l'édition. L’argument programmé dans la fonction mathématique n’est pas valide. Programmer un argument correct dans la fonction mathématique (LN, LOG, SQRT, EXP, DEXP, SIN, COS, TAN, ASIN, ACOS, ATAN). 'Perte totale dans la fonction' DÉTECTION CAUSE SOLUTION 8273 Au cours de l'édition. L’argument programmé dans la fonction mathématique n’est pas valide. Programmer un argument correct dans la fonction mathématique (LN, LOG, SQRT, EXP, DEXP, SIN, COS, TAN, ASIN, ACOS, ATAN). 'Argument interdit dans la fonction' DÉTECTION CAUSE SOLUTION 8272 Au cours de l'édition. L’argument programmé dans la fonction mathématique n’est pas valide. Programmer un argument correct dans la fonction mathématique (LN, LOG, SQRT, EXP, DEXP, SIN, COS, TAN, ASIN, ACOS, ATAN). 'Perte partielle de la fonction' DÉTECTION CAUSE SOLUTION 8271 Au cours de l'édition. L’argument programmé dans la fonction mathématique n’est pas valide. Programmer un argument correct dans la fonction mathématique (LN, LOG, SQRT, EXP, DEXP, SIN, COS, TAN, ASIN, ACOS, ATAN). Au cours de l'édition. Les fonctions G11, G12 ou G13 sont programmées plus d'une fois dans le même bloc. La fonction G10 ou G14 est programmée avec les fonctions G11, G12 ou G13 dans le même bloc. Les fonctions G11, G12 et G13 peuvent être combinées dans un même bloc mais chacune d’elles ne peut être programmée qu’une fois. Les fonctions G10 et G14 ne peuvent pas être programmées dans le même bloc que les fonctions G11, G12 ou G13. S o l ut i o n s d ’ e r r e ur s . 8280 'Vitesse de positionnement de la broche négative' DÉTECTION CAUSE SOLUTION 8281 'Vitesse de positionnement de broche programmée en double' DÉTECTION CAUSE SOLUTION 8282 SOLUTION Au cours de l'édition. La variable n'a pas permission d'écriture. La variable est uniquement de lecture. 'Liste de paramètres vide' DÉTECTION CAUSE SOLUTION 8296 Au cours de l'édition. La variable n'a pas permission d'écriture. La variable est uniquement de lecture. 'Variable du paramètre machine sans permission d'écriture' DÉTECTION CAUSE SOLUTION 8295 Pendant l’édition et l’exécution. La syntaxe de l'instruction n'est pas correcte. Vérifier dans le manuel de programmation la syntaxe de l'instruction. 'Variable du gestionnaire d'outils sans permission d'écriture' DÉTECTION CAUSE SOLUTION 8291 Pendant l’édition et l’exécution. La syntaxe de l'instruction n'est pas correcte. Vérifier dans le manuel de programmation la syntaxe de l'instruction. 'Les limites pour partie fractionnaire sont dépassées' DÉTECTION CAUSE SOLUTION 8290 Au cours de l'édition. Dans la fonction G20 un axe avec signe négatif est programmé et il n’est pas l’axe longitudinal. Dans la fonction G20 seul l’axe longitudinal peut avoir le signe négatif. 'Les limites pour partie entière sont dépassées' DÉTECTION CAUSE SOLUTION 8288 Au cours de l'édition. La variable n'a pas permission d'écriture. La variable est uniquement de lecture. 'G20: n’admet que le signe négatif sur l’axe longitudinal' DÉTECTION CAUSE 8287 Au cours de l'édition. Un paramètre non valide pour ce cycle fixe a été programmé. Vérifier dans le manuel de programmation les paramètres obligatoires et permis pour chaque cycle fixe. 'Variable de PLC sans permission d'écriture' DÉTECTION CAUSE SOLUTION 8285 Au cours de l'édition. Un paramètre du cycle fixe est programmé plus d’une fois dans le bloc. Chaque paramètre du cycle fixe ne peut être programmé qu’une fois dans le bloc. 'Paramètre non valide dans le cycle fixe' DÉTECTION CAUSE SOLUTION 8284 Au cours de l'édition et exécution dans MDI. Dans un même bloc, la vitesse de positionnement de la broche en M19 est programmée plus d’une fois. Programmer une seule fois la vitesse de positionnement de la broche "Sn.POS". 'Paramètre de cycle fixe répété' DÉTECTION CAUSE SOLUTION 8283 Au cours de l'édition. Une vitesse de positionnement négative a été programmée dans M19. La vitesse de positionnement "Sn.POS" doit être positive. Pendant l’édition et l’exécution. La syntaxe de l'instruction n'est pas correcte. Vérifier dans le manuel de programmation la syntaxe de l'instruction. 'Paramètre répété ou incomplet' DÉTECTION CAUSE SOLUTION CNC 8070 Pendant l’édition et l’exécution. La syntaxe de l'instruction n'est pas correcte. Vérifier dans le manuel de programmation la syntaxe de l'instruction. (REF: 1901) ·193· S o l ut i o n s d ’ e r r e ur s . 8297 'Paramètre répété' DÉTECTION CAUSE SOLUTION 8299 'Il manque des crochets autour de la liste de paramètres' DÉTECTION CAUSE SOLUTION 8300 SOLUTION SOLUTION SOLUTION CNC 8070 (REF: 1901) ·194· Au cours de l'édition. Dans l'instruction G20, le paramètre 5 est égal au paramètre 1 ou 2. Le paramètre 5 doit être différent au paramètre 1 ou 2. 'On attendait l'expression K après G04' DÉTECTION CAUSE SOLUTION 8309 Au cours de l'édition. L'instruction #AXIS n’a pas été programmée dans le même bloc que la fonction G201. La fonction G201 exige la programmation dans le même bloc de l'instruction #AXIS. Il faut indiquer dans cette instruction les axes affectés par la fonction G. 'Programmation incorrecte du troisième axe primaire' DÉTECTION CAUSE SOLUTION 8308 Au cours de l'édition. Dans l'instruction #DGWZ, la coordonnée Z minimale est supérieure ou égale à la maximale. La coordonnée minimale doit être inférieure à la maximale. 'G201 a besoin de la programmation de la fonction spéciale #AXIS' DÉTECTION CAUSE SOLUTION 8307 Au cours de l'édition. Dans l'instruction #DGWZ, la coordonnée Y minimale est supérieure ou égale à la maximale. La coordonnée minimale doit être inférieure à la maximale. 'La coordonnée Z minimale doit être inférieure à la maximale' DÉTECTION CAUSE 8306 Au cours de l'édition. Dans l'instruction #DGWZ, la coordonnée X minimale est supérieure ou égale à la maximale. La coordonnée minimale doit être inférieure à la maximale. 'La coordonnée Y minimale doit être inférieure à la maximale' DÉTECTION CAUSE 8304 Au cours de l'édition. Avec les fonctions G170, G171 ou G157 aucun axe n'a été programmé. Programmer le ou les axes devant être affectés par la fonction G170, G171 ou G157. 'La coordonnée X minimale doit être inférieure à la maximale' DÉTECTION CAUSE 8303 Au cours de l'édition et exécution dans MDI. La liste des paramètres de l'instruction programmée doit être programmée entre crochets. Vérifier dans le manuel de programmation la syntaxe de l'instruction. 'Au moins un axe est nécessaire pour G170, G171 ou G157' DÉTECTION CAUSE SOLUTION 8302 Au cours de l'édition. Les possibles causes sont les suivantes: • Dans l'instruction #HSC le paramètre CONTERROR a été programmé plus d'une fois. • Un paramètre a été programmé plus d’une fois dans l'instruction d’appel à sousroutine #PCALL, #MCALL ou fonction G avec sous-routine associée. • Dans l'instruction #PROBE ou #POLY un paramètre a été programmé plus d’une fois. Programmer chaque paramètre une seule fois dans le bloc. Au cours de l'édition. Fonction G4 mal programmée. La fonction G4 peut être programmée comme G4 <time> ou G4K<time>, où <time> est le temps d'attente. 'Trop d'axes programmés' DÉTECTION CAUSE SOLUTION Au cours de l'édition. Trop d’axes programmés dans l'instruction #POLY. Le nombre maximum d’axes que l’on peut programmer est 3. S o l ut i o n s d ’ e r r e ur s . 8310 'Il manque un paramètre obligatoire' DÉTECTION CAUSE SOLUTION 8311 'Valeur de paramètre non valide' DÉTECTION CAUSE SOLUTION 8312 Au cours de l'édition. L’axe @2 est programmé plus d’une fois dans le bloc. Programmer l’axe @2 une seule fois dans le bloc. CNC 8070 'Il n'est permis qu'un axe actif 3 par bloc' DÉTECTION CAUSE SOLUTION 8321 Au cours de l'édition. L’axe @1 est programmé plus d’une fois dans le bloc. Programmer l’axe @1 une seule fois dans le bloc. 'Il n'est permis qu'un axe actif 2 par bloc' DÉTECTION CAUSE SOLUTION 8320 Au cours de l'édition. Correcteur d'outil négatif. Le correcteur d’outil doit être positif. 'Il n'est permis qu'un axe actif 1 par bloc' DÉTECTION CAUSE SOLUTION 8319 Au cours de l'édition et exécution dans MDI. Un des paramètres du cycle ou l'instruction ne sont pas valides. Vérifier dans le manuel de programmation les paramètres valides pour chaque cycle et instruction. 'Fonction D négative' DÉTECTION CAUSE SOLUTION 8318 Au cours de l'édition et exécution dans MDI. Le numéro de cycle du palpeur n'est pas valide. Consulter dans la documentation les cycles de palpeur valides. 'Paramètre interdit' DÉTECTION CAUSE SOLUTION 8317 Au cours de l'édition. Dans la fonction G30/G73 un seul des paramètres I, J a été programmé. Programmer les deux paramètres I, J ou n’en programmer aucun. 'Numéro de cycle du palpeur non valide' DÉTECTION CAUSE SOLUTION 8316 Au cours de l'édition. Valeur non valide pour le numéro du système dans l'instruction #CS ou #ACS. Le numéro de système doit avoir une valeur entre 1 et 5, les deux compris. 'Programmation incorrecte G30/G73' DÉTECTION CAUSE SOLUTION 8315 Au cours de l'édition. Valeur non valide pour la commande MODE de l'instruction #CS ou #ACS. Vérifier dans le manuel de programmation la syntaxe des instructions. '#CS/#ACS: numéro de système de coordonnées non valide' DÉTECTION CAUSE SOLUTION 8314 Au cours de l'édition. Valeur non valide dans un argument de l'instruction #CS, #ACS, #HSC ou #POLY. Valeur non valide pour l'indice d'un paramètre arithmétique. Vérifier dans le manuel de programmation la syntaxe des instructions. L’indice d’un paramètre arithmétique doit être toujours positif ou nul. '#CS/#ACS: mode non valide' DÉTECTION CAUSE SOLUTION 8313 Au cours de l'édition. Il manque un paramètre obligatoire dans l'instruction #POLY, #CS, #ACS ou #PROBE Vérifier dans le manuel de programmation la syntaxe des instructions. Au cours de l'édition. L’axe @3 est programmé plus d’une fois dans le bloc. Programmer l’axe @3 une seule fois dans le bloc. 'Il n'est permis qu'un axe actif 4 par bloc' DÉTECTION CAUSE SOLUTION (REF: 1901) Au cours de l'édition. L’axe @4 est programmé plus d’une fois dans le bloc. Programmer l’axe @4 une seule fois dans le bloc. ·195· S o l ut i o n s d ’ e r r e ur s . 8322 'Il n'est permis qu'un axe actif 5 par bloc' DÉTECTION CAUSE SOLUTION 8323 'On attend comparaison' DÉTECTION CAUSE SOLUTION 8324 SOLUTION CNC 8070 8333 Pendant l’édition et l’exécution. La syntaxe de l'instruction n'est pas correcte. Vérifier dans le manuel de programmation la syntaxe de l'instruction. '#MSG["Texte <%d>"<,valeur>]' DÉTECTION CAUSE SOLUTION ·196· Au cours de l'édition et exécution dans MDI. L'instruction ou variable programmée n’accepte pas un nom ou un numéro d’axe. Vérifier dans le manuel de programmation la syntaxe de l'instruction ou variable. '#WARNING/#ERROR["Texte <%d>"<,valeur>]/[nombre-entier]' DÉTECTION CAUSE SOLUTION (REF: 1901) Au cours de l'édition et exécution dans MDI. L'instruction ou la variable programmée exige un nom ou numéro d’axe. Vérifier dans le manuel de programmation la syntaxe de l'instruction ou variable. 'On n'attendait pas nom ou numéro d'axe' DÉTECTION CAUSE SOLUTION 8332 Au cours de l'édition. On a programmé un nom de variable qui ne commence pas par le préfixe "V.". Tout nom de variable dans le programme pièce et par MDI doit commencer par le préfixe "V.". 'On attendait nom ou numéro d'axe' DÉTECTION CAUSE SOLUTION 8331 Au cours de l'édition. Dans l'instruction #SET AX une valeur entière différente de zéro a été programmée. L'instruction #SET AX ne permet de programmer que la valeur zéro pour indiquer que la position n’est occupée par aucun axe. 'On attendait V' DÉTECTION CAUSE SOLUTION 8330 Au cours de l'édition et exécution dans MDI. Le nombre de parenthèses d’ouverture ne coïncide pas avec le nombre de parenthèses de fermeture. Vérifier que chaque parenthèse d’ouverture a sa parenthèse de fermeture correspondante. '#SET AX: uniquement la position zéro est permise' DÉTECTION CAUSE SOLUTION 8329 Au cours de l'édition. Un espace en blanc est incorrect. Supprimer l’espace en blanc. 'Il manque une parenthèse' DÉTECTION CAUSE 8328 Au cours de l'édition. Un saut de ligne est incorrect. Supprimer le saut de ligne. 'Espace non attendu' DÉTECTION CAUSE SOLUTION 8327 Au cours de l'édition. Un tabulateur est incorrect. Supprimer le tabulateur. 'Saut de ligne non attendu' DÉTECTION CAUSE SOLUTION 8326 Au cours de l'édition. On a programmé "=" au lieu de "==". Programmer "==" au lieu de "=". 'Tabulation non attendue' DÉTECTION CAUSE SOLUTION 8325 Au cours de l'édition. L’axe @5 est programmé plus d’une fois dans le bloc. Programmer l’axe @5 une seule fois dans le bloc. Pendant l’édition et l’exécution. La syntaxe de l'instruction n'est pas correcte. Vérifier dans le manuel de programmation la syntaxe de l'instruction. S o l ut i o n s d ’ e r r e ur s . 8334 '#FREE AX[axe, ...]' DÉTECTION CAUSE SOLUTION 8335 '#WAIT FOR[expression]' DÉTECTION CAUSE SOLUTION 8336 Au cours de l'exécution. La syntaxe de l'instruction n'est pas correcte. Vérifier dans le manuel de programmation la syntaxe de l'instruction. '#SET OFFSET[inférieur, supérieur]axe' DÉTECTION CAUSE SOLUTION 8345 Au cours de l'exécution. La syntaxe de l'instruction n'est pas correcte. Vérifier dans le manuel de programmation la syntaxe de l'instruction. '#INCJOG[[valeurIncrément, valeurAvance],..., [...]] nomAxe' DÉTECTION CAUSE SOLUTION 8344 Au cours de l'exécution. La syntaxe de l'instruction n'est pas correcte. Vérifier dans le manuel de programmation la syntaxe de l'instruction. '#CONTJOG[valeurAvance] nomAxe' DÉTECTION CAUSE SOLUTION 8343 Pendant l’édition et l’exécution. La syntaxe de l'instruction n'est pas correcte. Vérifier dans le manuel de programmation la syntaxe de l'instruction. '#MPG[valeurRésolution,...] nomAxe' DÉTECTION CAUSE SOLUTION 8342 Pendant l’édition et l’exécution. La syntaxe de l'instruction n'est pas correcte. Vérifier dans le manuel de programmation la syntaxe de l'instruction. '#AXIS[axe, ...]' DÉTECTION CAUSE SOLUTION 8341 Pendant l’édition et l’exécution. La syntaxe de l'instruction n'est pas correcte. Vérifier dans le manuel de programmation la syntaxe de l'instruction. '#TOOL AX[axe +/-]' DÉTECTION CAUSE SOLUTION 8340 Pendant l’édition et l’exécution. La syntaxe de l'instruction n'est pas correcte. Vérifier dans le manuel de programmation la syntaxe de l'instruction. '#SET AX [axe, ...] <option>' DÉTECTION CAUSE SOLUTION 8339 Pendant l’édition et l’exécution. La syntaxe de l'instruction n'est pas correcte. Vérifier dans le manuel de programmation la syntaxe de l'instruction. '#CALL AX [axe, <position,> ...] <option>' DÉTECTION CAUSE SOLUTION 8338 Pendant l’édition et l’exécution. La syntaxe de l'instruction n'est pas correcte. Vérifier dans le manuel de programmation la syntaxe de l'instruction. '#TANGFEED RMIN[rayon]' DÉTECTION CAUSE SOLUTION 8337 Pendant l’édition et l’exécution. La syntaxe de l'instruction n'est pas correcte. Vérifier dans le manuel de programmation la syntaxe de l'instruction. Pendant l’édition et l’exécution. La syntaxe de l'instruction n'est pas correcte. Vérifier dans le manuel de programmation la syntaxe de l'instruction. CNC 8070 '#LINK[maître, esclave <,erreur>]...[...]' DÉTECTION CAUSE SOLUTION Pendant l’édition et l’exécution. La syntaxe de l'instruction n'est pas correcte. Vérifier dans le manuel de programmation la syntaxe de l'instruction. (REF: 1901) ·197· S o l ut i o n s d ’ e r r e ur s . 8346 '#ROUNDPAR[param, …]: erreur de syntaxe' DÉTECTION CAUSE SOLUTION 8347 '#ASPLINE MODE [<initial> <, final>]: erreur de syntaxe' DÉTECTION CAUSE SOLUTION 8348 CNC 8070 (REF: 1901) ·198· Au cours de l'exécution. La syntaxe de l'instruction n'est pas correcte. Vérifier dans le manuel de programmation la syntaxe de l'instruction. '#FACE [abscisse, ordonnée<,longitudinal, axe, axe>]<[cinématique]>: erreur de syntaxe' DÉTECTION CAUSE SOLUTION 8358 Au cours de l'exécution. La syntaxe de l'instruction n'est pas correcte. Vérifier dans le manuel de programmation la syntaxe de l'instruction. '#CAX <[broche, nom]>: erreur de syntaxe' DÉTECTION CAUSE SOLUTION 8357 Au cours de l'exécution. La syntaxe de l'instruction n'est pas correcte. Vérifier dans le manuel de programmation la syntaxe de l'instruction. '#CS/ACS DEF ACT[n]: erreur de syntaxe' DÉTECTION CAUSE SOLUTION 8356 Au cours de l'exécution. La syntaxe de l'instruction n'est pas correcte. Vérifier dans le manuel de programmation la syntaxe de l'instruction. '#CS/ACS ON/NEW <[n]> <[MODE m, V1, V2, V3, j1, j2, j3, 0/1]>: erreur de syntaxe' DÉTECTION CAUSE SOLUTION 8354 Au cours de l'exécution. La syntaxe de l'instruction n'est pas correcte. Vérifier dans le manuel de programmation la syntaxe de l'instruction. '#CS/ACS DEF <[n]> [MODE m, V1, V2, V3, j1, j2, j3, 0/1]: erreur de syntaxe' DÉTECTION CAUSE SOLUTION 8353 Au cours de l'exécution. La syntaxe de l'instruction n'est pas correcte. Vérifier dans le manuel de programmation la syntaxe de l'instruction. '#KIN ID <[cinématique]>: erreur de syntaxe' DÉTECTION CAUSE SOLUTION 8352 Au cours de l'exécution. La syntaxe de l'instruction n'est pas correcte. Vérifier dans le manuel de programmation la syntaxe de l'instruction. '#TLC ON[n]’: erreur de syntaxe' DÉTECTION CAUSE SOLUTION 8351 Au cours de l'exécution. La syntaxe de l'instruction n'est pas correcte. Vérifier dans le manuel de programmation la syntaxe de l'instruction. '#SLOPE[type <,jerk> <,accél> <,déplac>]: erreur de syntaxe' DÉTECTION CAUSE SOLUTION 8350 Au cours de l'exécution. La syntaxe de l'instruction n'est pas correcte. Vérifier dans le manuel de programmation la syntaxe de l'instruction. '#ASPLINE STARTTANG/ENDTANG axes: erreur de syntaxe' DÉTECTION CAUSE SOLUTION 8349 Au cours de l'exécution. La syntaxe de l'instruction n'est pas correcte. Vérifier dans le manuel de programmation la syntaxe de l'instruction. Au cours de l'exécution. La syntaxe de l'instruction n'est pas correcte. Vérifier dans le manuel de programmation la syntaxe de l'instruction. '#CYL [abscisse, ordonnée, longitudinal rayon] <[cinématique]>: erreur de syntaxe' DÉTECTION CAUSE SOLUTION Au cours de l'exécution. La syntaxe de l'instruction n'est pas correcte. Vérifier dans le manuel de programmation la syntaxe de l'instruction. S o l ut i o n s d ’ e r r e ur s . 8359 '#HSC ON <[CONTERROR/FAST valeur, CORNER valeur]>: erreur de syntaxe' DÉTECTION CAUSE SOLUTION 8360 '#DGWZ[Axe1min, Axe1max, Axe2min, Axe2max <, Axe3min, Axe3max>]' DÉTECTION CAUSE SOLUTION 8361 Pendant l’édition et l’exécution. La syntaxe de l'instruction n'est pas correcte. Vérifier dans le manuel de programmation la syntaxe de l'instruction. #EXEC["path" <,channel>] DÉTECTION CAUSE SOLUTION 8370 Pendant l’édition et l’exécution. La syntaxe de l'instruction n'est pas correcte. Vérifier dans le manuel de programmation la syntaxe de l'instruction. #SELECT PROBE[probe_number] DÉTECTION CAUSE SOLUTION 8369 Pendant l’édition et l’exécution. La syntaxe de l'instruction n'est pas correcte. Vérifier dans le manuel de programmation la syntaxe de l'instruction. #RENAME AX[previous_axis_name, new_axis_name][...] DÉTECTION CAUSE SOLUTION 8368 Pendant l’édition et l’exécution. La syntaxe de l'instruction n'est pas correcte. Vérifier dans le manuel de programmation la syntaxe de l'instruction. '#RPT[Ni, Nf <,répétitions>]' DÉTECTION CAUSE SOLUTION 8367 Pendant l’édition et l’exécution. La syntaxe de l'instruction n'est pas correcte. Vérifier dans le manuel de programmation la syntaxe de l'instruction. '#SCALE[valeur]' DÉTECTION CAUSE SOLUTION 8366 Au cours de l'exécution. La syntaxe de l'instruction n'est pas correcte. Vérifier dans le manuel de programmation la syntaxe de l'instruction. '#PROBE num liste_paramètres' DÉTECTION CAUSE SOLUTION 8365 Pendant l’édition et l’exécution. La syntaxe de l'instruction n'est pas correcte. Vérifier dans le manuel de programmation la syntaxe de l'instruction. '#POLY[axe[a,b,c,d,e] ... SP EP R]: erreur de syntaxe' DÉTECTION CAUSE SOLUTION 8364 Pendant l’édition et l’exécution. La syntaxe de l'instruction n'est pas correcte. Vérifier dans le manuel de programmation la syntaxe de l'instruction. '#PATH["path"]' DÉTECTION CAUSE SOLUTION 8363 Pendant l’édition et l’exécution. La syntaxe de l'instruction n'est pas correcte. Vérifier dans le manuel de programmation la syntaxe de l'instruction. '#CD ON <[horizon]>' DÉTECTION CAUSE SOLUTION 8362 Au cours de l'exécution. La syntaxe de l'instruction n'est pas correcte. Vérifier dans le manuel de programmation la syntaxe de l'instruction. Pendant l’édition et l’exécution. La syntaxe de l'instruction n'est pas correcte. Vérifier dans le manuel de programmation la syntaxe de l'instruction. CNC 8070 #WAIT/#MEET [marque, channel...] DÉTECTION CAUSE SOLUTION Pendant l’édition et l’exécution. La syntaxe de l'instruction n'est pas correcte. Vérifier dans le manuel de programmation la syntaxe de l'instruction. (REF: 1901) ·199· S o l ut i o n s d ’ e r r e ur s . 8371 #SIGNAL[marque...] DÉTECTION CAUSE SOLUTION 8372 #TIME <[>time<]> DÉTECTION CAUSE SOLUTION 8373 CNC 8070 (REF: 1901) ·200· Au cours de l'exécution. La syntaxe de l'instruction n'est pas correcte. Vérifier dans le manuel de programmation la syntaxe de l'instruction. '#TOOL ORI: erreur de syntaxe' DÉTECTION CAUSE SOLUTION 8382 Au cours de l'exécution. La syntaxe de l'instruction n'est pas correcte. Vérifier dans le manuel de programmation la syntaxe de l'instruction. '#TLC OFF: erreur de syntaxe' DÉTECTION CAUSE SOLUTION 8381 Au cours de l'exécution. La syntaxe de l'instruction n'est pas correcte. Vérifier dans le manuel de programmation la syntaxe de l'instruction. '#RTCP ON/OFF: erreur de syntaxe' DÉTECTION CAUSE SOLUTION 8380 Pendant l’édition et l’exécution. La syntaxe de l'instruction n'est pas correcte. Vérifier dans le manuel de programmation la syntaxe de l'instruction. '#SPLINE ON/OFF: erreur de syntaxe' DÉTECTION CAUSE SOLUTION 8379 Pendant l’édition et l’exécution. La syntaxe de l'instruction n'est pas correcte. Vérifier dans le manuel de programmation la syntaxe de l'instruction. #UNLINK DÉTECTION CAUSE SOLUTION 8378 Pendant l’édition et l’exécution. La syntaxe de l'instruction n'est pas correcte. Vérifier dans le manuel de programmation la syntaxe de l'instruction. #SYNC POS DÉTECTION CAUSE SOLUTION 8377 Pendant l’édition et l’exécution. La syntaxe de l'instruction n'est pas correcte. Vérifier dans le manuel de programmation la syntaxe de l'instruction. #COMMENT BEGIN/END DÉTECTION CAUSE SOLUTION 8376 Pendant l’édition et l’exécution. La syntaxe de l'instruction n'est pas correcte. Vérifier dans le manuel de programmation la syntaxe de l'instruction. #FLUSH DÉTECTION CAUSE SOLUTION 8375 Pendant l’édition et l’exécution. La syntaxe de l'instruction n'est pas correcte. Vérifier dans le manuel de programmation la syntaxe de l'instruction. #FREE AX ALL DÉTECTION CAUSE SOLUTION 8374 Pendant l’édition et l’exécution. La syntaxe de l'instruction n'est pas correcte. Vérifier dans le manuel de programmation la syntaxe de l'instruction. Au cours de l'exécution. La syntaxe de l'instruction n'est pas correcte. Vérifier dans le manuel de programmation la syntaxe de l'instruction. '#CS/ACS OFF <ALL>: erreur de syntaxe' DÉTECTION CAUSE SOLUTION Au cours de l'exécution. La syntaxe de l'instruction n'est pas correcte. Vérifier dans le manuel de programmation la syntaxe de l'instruction. S o l ut i o n s d ’ e r r e ur s . 8383 '#ECS ON/OFF: erreur de syntaxe' DÉTECTION CAUSE SOLUTION 8384 '#MCS <ON/OFF>: erreur de syntaxe' DÉTECTION CAUSE SOLUTION 8385 Pendant l’édition et l’exécution. La syntaxe de l'instruction n'est pas correcte. Vérifier dans le manuel de programmation la syntaxe de l'instruction. '#PARK/UNPARK axe' DÉTECTION CAUSE SOLUTION 8394 Pendant l’édition et l’exécution. La syntaxe de l'instruction n'est pas correcte. Vérifier dans le manuel de programmation la syntaxe de l'instruction. '#VAR/ENDVAR/DELETE' DÉTECTION CAUSE SOLUTION 8393 Pendant l’édition et l’exécution. La syntaxe de l'instruction n'est pas correcte. Vérifier dans le manuel de programmation la syntaxe de l'instruction. '#CYCLE BEGIN/END' DÉTECTION CAUSE SOLUTION 8392 Pendant l’édition et l’exécution. La syntaxe de l'instruction n'est pas correcte. Vérifier dans le manuel de programmation la syntaxe de l'instruction. '#RET' DÉTECTION CAUSE SOLUTION 8391 Pendant l’édition et l’exécution. La syntaxe de l'instruction n'est pas correcte. Vérifier dans le manuel de programmation la syntaxe de l'instruction. '#EFHOLD/DFHOLD' DÉTECTION CAUSE SOLUTION 8390 Au cours de l'exécution. La syntaxe de l'instruction n'est pas correcte. Vérifier dans le manuel de programmation la syntaxe de l'instruction. '#ESTOP/DSTOP' DÉTECTION CAUSE SOLUTION 8389 Pendant l’édition et l’exécution. La syntaxe de l'instruction n'est pas correcte. Vérifier dans le manuel de programmation la syntaxe de l'instruction. '#CAX/FACE/CYL OFF: erreur de syntaxe' DÉTECTION CAUSE SOLUTION 8388 Pendant l’édition et l’exécution. La syntaxe de l'instruction n'est pas correcte. Vérifier dans le manuel de programmation la syntaxe de l'instruction. '#ESBLK/DSBLK' DÉTECTION CAUSE SOLUTION 8387 Au cours de l'exécution. La syntaxe de l'instruction n'est pas correcte. Vérifier dans le manuel de programmation la syntaxe de l'instruction. '#INIT MACROTAB' DÉTECTION CAUSE SOLUTION 8386 Au cours de l'exécution. La syntaxe de l'instruction n'est pas correcte. Vérifier dans le manuel de programmation la syntaxe de l'instruction. Pendant l’édition et l’exécution. La syntaxe de l'instruction n'est pas correcte. Vérifier dans le manuel de programmation la syntaxe de l'instruction. CNC 8070 '#CALL nom_sous-routine' DÉTECTION CAUSE SOLUTION Pendant l’édition et l’exécution. La syntaxe de l'instruction n'est pas correcte. Vérifier dans le manuel de programmation la syntaxe de l'instruction. (REF: 1901) ·201· S o l ut i o n s d ’ e r r e ur s . 8395 '#PCALL nom_sous-routine <param>' DÉTECTION CAUSE SOLUTION 8396 '#MCALL nom_sous-routine <param>' DÉTECTION CAUSE SOLUTION 8397 CNC 8070 (REF: 1901) ·202· Au cours de l'édition et exécution dans MDI. La syntaxe de l'instruction n'est pas correcte. Vérifier dans le manuel de programmation la syntaxe de l'instruction. '#MOVE INF[axe+/- <,avance> <,PRESENT/NEXT/NULL/WAITINPOS>]' DÉTECTION CAUSE SOLUTION 8406 Au cours de l'édition et exécution dans MDI. La syntaxe de l'instruction n'est pas correcte. Vérifier dans le manuel de programmation la syntaxe de l'instruction. '#MOVE ADD[axe_cote <,avance> <,PRESENT/NEXT/NULL/WAITINPOS>]' DÉTECTION CAUSE SOLUTION 8405 Au cours de l'édition. Le numéro de magasin défini dans la variable n’est pas valide. Le numéro de magasin doit être une valeur entre 1 et 4. Si le numéro de magasin n'est pas indiqué, c'est le premier qui est pris. '#MOVE<ABS>[axe_cote<,avance><,PRESENT/NEXT/NULL/WAITINPOS>]' DÉTECTION CAUSE SOLUTION 8404 Pendant l’édition et l’exécution. La syntaxe de l'instruction n'est pas correcte. Vérifier dans le manuel de programmation la syntaxe de l'instruction. 'Numéro de magasin d'outils non valide' DÉTECTION CAUSE SOLUTION 8403 Pendant l’édition et l’exécution. La syntaxe de l'instruction n'est pas correcte. Vérifier dans le manuel de programmation la syntaxe de l'instruction. '#EXBLK[bloc <,canal>]' DÉTECTION CAUSE SOLUTION 8402 Pendant l’édition et l’exécution. La syntaxe de l'instruction n'est pas correcte. Vérifier dans le manuel de programmation la syntaxe de l'instruction. '#FREE SP ALL' DÉTECTION CAUSE SOLUTION 8401 Pendant l’édition et l’exécution. La syntaxe de l'instruction n'est pas correcte. Vérifier dans le manuel de programmation la syntaxe de l'instruction. '#RENAME SP[nom_broche_antérieure, nom_broche_nouvelle][...][...]' DÉTECTION CAUSE SOLUTION 8400 Pendant l’édition et l’exécution. La syntaxe de l'instruction n'est pas correcte. Vérifier dans le manuel de programmation la syntaxe de l'instruction. '#FREE SP/#CALL SP/#SET SP[nom_broche, ...]' DÉTECTION CAUSE SOLUTION 8399 Pendant l’édition et l’exécution. La syntaxe de l'instruction n'est pas correcte. Vérifier dans le manuel de programmation la syntaxe de l'instruction. '#MASTER nom_broche' DÉTECTION CAUSE SOLUTION 8398 Pendant l’édition et l’exécution. La syntaxe de l'instruction n'est pas correcte. Vérifier dans le manuel de programmation la syntaxe de l'instruction. Au cours de l'édition et exécution dans MDI. La syntaxe de l'instruction n'est pas correcte. Vérifier dans le manuel de programmation la syntaxe de l'instruction. '#<T>CAM ON[l, maître, esclave, n, m, o, p <,ONCE/CONT>]' DÉTECTION CAUSE SOLUTION Au cours de l'édition et exécution dans MDI. La syntaxe de l'instruction n'est pas correcte. Vérifier dans le manuel de programmation la syntaxe de l'instruction. S o l ut i o n s d ’ e r r e ur s . 8407 '#<T>CAM OFF[esclave]' DÉTECTION CAUSE SOLUTION 8408 '#<T>FOLLOW ON[maître, esclave <, Nm, Dn, VEL/POS>]' DÉTECTION CAUSE SOLUTION 8409 SOLUTION SOLUTION Au cours de l'édition. Dans les instructions #FOLLOW ON et #SYNC, le paramètre D est programmé avant le paramètre N. Programmer le paramètre N avant le paramètre D. '#ANGAX OFF/SUSP <[expression1, expression2, expression3, ...]>' DÉTECTION CAUSE SOLUTION 8419 Au cours de l'édition. Dans les instructions #FOLLOW ON et #SYNC il faut programmer l’un des paramètres D ou N. Programmer les deux paramètres D et N ou aucun, on ne peut pas en programmer un seul. 'Programmer le numérateur avant le dénominateur' DÉTECTION CAUSE 8418 Pendant l’édition et l’exécution. La syntaxe de l'instruction n'est pas correcte. Vérifier dans le manuel de programmation la syntaxe de l'instruction. Numérateur/dénominateur: programmer tous les deux ou aucun' DÉTECTION CAUSE 8416 Pendant l’édition et l’exécution. La syntaxe de l'instruction n'est pas correcte. Vérifier dans le manuel de programmation la syntaxe de l'instruction. '#UNSYNC[broche_esclave <, broche_esclave...>]' DÉTECTION CAUSE SOLUTION 8415 Pendant l’édition et l’exécution. La syntaxe de l'instruction n'est pas correcte. Vérifier dans le manuel de programmation la syntaxe de l'instruction. '#<T>SYNC[broche_master, broche_esclave <,Nx, Dx, Ox>] <[...] ...>' DÉTECTION CAUSE SOLUTION 8414 Au cours de l'exécution. La syntaxe de l'instruction n'est pas correcte. Vérifier dans le manuel de programmation la syntaxe de l'instruction. '#LATHECY/MILLCY ON/OFF' DÉTECTION CAUSE SOLUTION 8413 Au cours de l'exécution. La syntaxe de l'instruction n'est pas correcte. Vérifier dans le manuel de programmation la syntaxe de l'instruction. '#BSPLINEND' DÉTECTION CAUSE SOLUTION 8412 Au cours de l'édition et exécution dans MDI. La syntaxe de l'instruction n'est pas correcte. Vérifier dans le manuel de programmation la syntaxe de l'instruction. '#BSPLINE[axe]' DÉTECTION CAUSE SOLUTION 8411 Au cours de l'édition et exécution dans MDI. La syntaxe de l'instruction n'est pas correcte. Vérifier dans le manuel de programmation la syntaxe de l'instruction. '#<T>FOLLOW OFF[esclave]' DÉTECTION CAUSE SOLUTION 8410 Au cours de l'édition et exécution dans MDI. La syntaxe de l'instruction n'est pas correcte. Vérifier dans le manuel de programmation la syntaxe de l'instruction. Au cours de l'exécution. La syntaxe de l'instruction n'est pas correcte. Vérifier dans le manuel de programmation la syntaxe de l'instruction. '#ANGAX ON [expression1, expression2, expression3, ...]' DÉTECTION CAUSE SOLUTION CNC 8070 Au cours de l'exécution. La syntaxe de l'instruction n'est pas correcte. Vérifier dans le manuel de programmation la syntaxe de l'instruction. (REF: 1901) ·203· S o l ut i o n s d ’ e r r e ur s . 8420 '#SERVO ON/OFF [axe/broche]' DÉTECTION CAUSE SOLUTION 8421 '#MDOFF' DÉTECTION CAUSE SOLUTION 8422 SOLUTION SOLUTION SOLUTION 8430 ·204· Au cours de l'édition. Erreur au cours de la programmation du langage de la CNC 8055. L'instruction n'est pas programmée. Consulter dans le manuel de la CNC 8055 la syntaxe correcte. '(DGWZ expression1, expression6>)' DÉTECTION CAUSE (REF: 1901) Au cours de l'édition. Erreur au cours de la programmation du langage de la CNC 8055. L'instruction n'est pas programmée. Consulter dans le manuel de la CNC 8055 la syntaxe correcte. '(MSG "texte")' DÉTECTION CAUSE CNC 8070 Au cours de l'édition. Dans les instructions #CS et #ACS, les commandes FIRST et SECOND ne peuvent pas être programmées dans le MODE 6. Vérifier dans le manuel de programmation la syntaxe des instructions. '(ERREUR <nombre entier> <,"texte">) DÉTECTION CAUSE 8429 Au cours de l'exécution. La syntaxe de l'instruction n'est pas correcte. Vérifier dans le manuel de programmation la syntaxe de l'instruction. Le paramètre FIRST/SECOND est interdit dans ce MODE' DÉTECTION CAUSE 8428 Au cours de l'exécution. La syntaxe de l'instruction n'est pas correcte. Vérifier dans le manuel de programmation la syntaxe de l'instruction. '#DEF "macro1" = "text1" "macro2" = "text2" ...' DÉTECTION CAUSE SOLUTION 8427 Au cours de l'exécution. La syntaxe de l'instruction n'est pas correcte. Vérifier dans le manuel de programmation la syntaxe de l'instruction. '#HSC OFF' DÉTECTION CAUSE SOLUTION 8426 Au cours de l'exécution. La syntaxe de l'instruction n'est pas correcte. Vérifier dans le manuel de programmation la syntaxe de l'instruction. '#CLEAR<[marque, ...]>' DÉTECTION CAUSE SOLUTION 8425 Au cours de l'exécution. La syntaxe de l'instruction n'est pas correcte. Vérifier dans le manuel de programmation la syntaxe de l'instruction. '#OSC axe1 axe2 ...' DÉTECTION CAUSE SOLUTION 8424 Au cours de l'exécution. La syntaxe de l'instruction n'est pas correcte. Vérifier dans le manuel de programmation la syntaxe de l'instruction. '#CD OFF' DÉTECTION CAUSE SOLUTION 8423 Au cours de l'exécution. La syntaxe de l'instruction n'est pas correcte. Vérifier dans le manuel de programmation la syntaxe de l'instruction. SOLUTION expression2, expression3, expression4 <,expression5, Au cours de l'édition. Erreur au cours de la programmation du langage de la CNC 8055. L'instruction n'est pas programmée. Consulter dans le manuel de la CNC 8055 la syntaxe correcte. S o l ut i o n s d ’ e r r e ur s . 8431 '(ESBLK/DSBLK)' DÉTECTION CAUSE SOLUTION 8432 '(ESTOP/DSTOP)' DÉTECTION CAUSE SOLUTION 8433 SOLUTION SOLUTION SOLUTION SOLUTION SOLUTION Au cours de l'édition. Erreur au cours de la programmation du langage de la CNC 8055. L'instruction n'est pas programmée. Consulter dans le manuel de la CNC 8055 la syntaxe correcte. '(RET)' DÉTECTION CAUSE SOLUTION 8439 Au cours de l'édition. Erreur au cours de la programmation du langage de la CNC 8055. L'instruction n'est pas programmée. Consulter dans le manuel de la CNC 8055 la syntaxe correcte. '(SUB nombre entier)' DÉTECTION CAUSE 8438 Au cours de l'édition. Erreur au cours de la programmation du langage de la CNC 8055. L'instruction n'est pas programmée. Consulter dans le manuel de la CNC 8055 la syntaxe correcte. '(IF condition action1 <ELSE action2>)' DÉTECTION CAUSE 8437 Au cours de l'édition. Erreur au cours de la programmation du langage de la CNC 8055. L'instruction n'est pas programmée. Consulter dans le manuel de la CNC 8055 la syntaxe correcte. '(RPT N(expression), N(expression))' DÉTECTION CAUSE 8436 Au cours de l'édition. Erreur au cours de la programmation du langage de la CNC 8055. Les instructions EFHOLD/DFHOLD ne sont pas seules dans le bloc ou bien il faut en programmer une des deux. Consulter dans le manuel de la CNC 8055 la syntaxe correcte. Les deux instructions doivent être seules dans le bloc et être programmées. '(GOTO N(expression))' DÉTECTION CAUSE 8435 Au cours de l'édition. Erreur au cours de la programmation du langage de la CNC 8055. Les instructions ESTOP/DSTOP ne sont pas seules dans le bloc ou bien il faut en programmer une des deux. Consulter dans le manuel de la CNC 8055 la syntaxe correcte. Les deux instructions doivent être seules dans le bloc et être programmées. '(EFHOLD/DFHOLD)' DÉTECTION CAUSE 8434 Au cours de l'édition. Erreur au cours de la programmation du langage de la CNC 8055. Les instructions EFHOLD/DFHOLD ne sont pas seules dans le bloc ou bien il faut en programmer une des deux. Consulter dans le manuel de la CNC 8055 la syntaxe correcte. Les deux instructions doivent être seules dans le bloc et être programmées. Au cours de l'édition. Erreur au cours de la programmation du langage de la CNC 8055. L'instruction n’est pas seule dans le bloc ou elle n'a pas été programmée. Consulter dans le manuel de la CNC 8055 la syntaxe correcte. L'instruction doit être seule dans le bloc. CNC 8070 '(CALL expression)' DÉTECTION CAUSE SOLUTION Au cours de l'édition. Erreur au cours de la programmation du langage de la CNC 8055. L'instruction n'est pas programmée. Consulter dans le manuel de la CNC 8055 la syntaxe correcte. (REF: 1901) ·205· S o l ut i o n s d ’ e r r e ur s . 8440 '(PCALL/MCALL/PROBE expression <,param>)' DÉTECTION CAUSE SOLUTION 8441 '(MDOFF)' DÉTECTION CAUSE SOLUTION 8442 SOLUTION SOLUTION SOLUTION SOLUTION SOLUTION SOLUTION SOLUTION 8455 ·206· Au cours de l'édition. Erreur en programmant en langage de la CNC 8055. Valeur incorrecte du paramètre E dans la fonction G49. Consulter dans le manuel de la CNC 8055 la syntaxe correcte. 'Valeur du paramètre S incorrecte' DÉTECTION CAUSE (REF: 1901) Au cours de l'édition. Erreur en programmant en langage de la CNC 8055. Programmation incorrecte de la fonction G33/G34. Consulter dans le manuel de la CNC 8055 la syntaxe correcte. 'Valeur du paramètre E incorrecte' DÉTECTION CAUSE CNC 8070 Au cours de l'édition. Erreur en programmant en langage de la CNC 8055. La fonction G9 exige de programmer le point intermédiaire (paramètres I, J, K). Consulter dans le manuel de la CNC 8055 la syntaxe correcte. 'Programmation incorrecte du filet' DÉTECTION CAUSE 8454 Au cours de l'édition. Erreur en programmant en langage de la CNC 8055. Le bloc G2/G3 programmé n'admet pas les paramètres I, J, K pour définir le centre de l'interpolation. Consulter dans le manuel de la CNC 8055 la syntaxe correcte. 'La fonction programmée exige les paramètres I, J, K' DÉTECTION CAUSE 8452 Au cours de l'édition. Erreur en programmant en langage de la CNC 8055. Le nombre d'axes programmés pour la fonction G n'est pas correct. Consulter dans le manuel de la CNC 8055 la syntaxe correcte. 'Le bloc G2/G3 programmé n’admet pas des paramètres I, J, K' DÉTECTION CAUSE 8447 Au cours de l'édition. Erreur en programmant en langage de la CNC 8055. Les actions programmées dans l'instruction IF ne sont pas valides; les actions ne peuvent pas être IF ni SUB. Consulter dans le manuel de la CNC 8055 la syntaxe correcte. 'Le nombre d'axes programmé est incorrect' DÉTECTION CAUSE 8446 Au cours de l'édition. Erreur au cours de la programmation du langage de la CNC 8055. L'instruction n'est pas programmée. Consulter dans le manuel de la CNC 8055 la syntaxe correcte. 'Action interdite dans l'instruction IF' DÉTECTION CAUSE 8445 Au cours de l'édition. Erreur au cours de la programmation du langage de la CNC 8055. L'instruction n’est pas seule dans le bloc ou elle n'a pas été programmée. Consulter dans le manuel de la CNC 8055 la syntaxe correcte. L'instruction doit être seule dans le bloc. '(EXEC P(expression) <,répertoire>' DÉTECTION CAUSE 8443 Au cours de l'édition. Erreur au cours de la programmation du langage de la CNC 8055. L'instruction n'est pas programmée. Consulter dans le manuel de la CNC 8055 la syntaxe correcte. SOLUTION Au cours de l'édition. Erreur en programmant en langage de la CNC 8055. Valeur incorrecte du paramètre S dans la fonction G. Consulter dans le manuel de la CNC 8055 la syntaxe correcte. S o l ut i o n s d ’ e r r e ur s . 8456 'Valeur du paramètre L incorrecte' DÉTECTION CAUSE SOLUTION 8457 'Ordre incorrect des axes' DÉTECTION CAUSE SOLUTION 8458 SOLUTION SOLUTION SOLUTION SOLUTION SOLUTION Au cours de l'édition. Erreur au cours de la programmation du langage de la CNC 8055. L'instruction n'est pas programmée. Consulter dans le manuel de la CNC 8055 la syntaxe correcte. '(WRITE bloc)' DÉTECTION CAUSE SOLUTION 8465 Au cours de l'édition. Erreur au cours de la programmation du langage de la CNC 8055. L'instruction n'est pas programmée. Consulter dans le manuel de la CNC 8055 la syntaxe correcte. '(OPEN P(expression) <,répertoire><,A/D><,commentaire>)' DÉTECTION CAUSE 8464 Au cours de l'édition. Erreur au cours de la programmation du langage de la CNC 8055. L'instruction n’est pas seule dans le bloc ou elle n'a pas été programmée. Consulter dans le manuel de la CNC 8055 la syntaxe correcte. L'instruction doit être seule dans le bloc. '(DIGIT/TRACE expression<,param>)' DÉTECTION CAUSE 8463 Au cours de l'édition. Erreur en programmant en langage de la CNC 8055. Le cycle PROBE n'existe pas. Consulter dans le manuel de la CNC 8055 les cycles disponibles. '(INIPAR)' DÉTECTION CAUSE 8462 Au cours de l'édition. Erreur en programmant en langage de la CNC 8055. La fonction programmée n’existe que sur la fraiseuse et le programme est d’un tour (fichier pit). Changer le nom du fichier ou utiliser le logiciel correct. 'Cycle PROBE inexistant dans le tour' DÉTECTION CAUSE SOLUTION 8461 Au cours de l'édition. Erreur en programmant en langage de la CNC 8055. La fonction programmée n’existe que sur le tour et le programme est d’une fraiseuse (fichier pim). Changer le nom du fichier ou utiliser le logiciel correct. 'Fonction ou variable inexistante dans le tour' DÉTECTION CAUSE 8460 Au cours de l'édition. Erreur en programmant en langage de la CNC 8055. L'ordre des axes dans le bloc n'est pas correct. Consulter dans le manuel de la CNC 8055 la syntaxe correcte. 'Fonction ou variable inexistante dans la fraiseuse' DÉTECTION CAUSE 8459 Au cours de l'édition. Erreur en programmant en langage de la CNC 8055. Valeur incorrecte du paramètre L dans la fonction G33/G34. Consulter dans le manuel de la CNC 8055 la syntaxe correcte. Au cours de l'édition. Erreur au cours de la programmation du langage de la CNC 8055. L'instruction n'est pas programmée. Consulter dans le manuel de la CNC 8055 la syntaxe correcte. '(REPOS axe1, axe2, ...)' DÉTECTION CAUSE SOLUTION Au cours de l'édition. Erreur au cours de la programmation du langage de la CNC 8055. L'instruction n'est pas programmée. Consulter dans le manuel de la CNC 8055 la syntaxe correcte. CNC 8070 (REF: 1901) ·207· S o l ut i o n s d ’ e r r e ur s . 8466 '(PAGE expression)' DÉTECTION CAUSE SOLUTION 8467 '(SYMBOL/ODW expression1, expression2, expression3)' DÉTECTION CAUSE SOLUTION 8468 SOLUTION SOLUTION SOLUTION SOLUTION SOLUTION SOLUTION SOLUTION 8475 Au cours de l'édition ou traduction d'un programme. Erreur au cours de la programmation du langage de la CNC 8055. La fonction programmée n’existe que sur les fraiseuses et le programme est de tour (fichier pit). Changer le nom du fichier ou utiliser le logiciel correct. 'Cycle TRACE inexistant dans le tour' DÉTECTION CAUSE (REF: 1901) SOLUTION ·208· Au cours de l'édition. Erreur au cours de la programmation du langage de la CNC 8055. L'instruction n’est pas seule dans le bloc ou elle n'a pas été programmée. Consulter dans le manuel de la CNC 8055 la syntaxe correcte. L'instruction doit être seule dans le bloc. 'Cycle DIGIT inexistant dans le tour' DÉTECTION CAUSE CNC 8070 Au cours de l'édition. Erreur au cours de la programmation du langage de la CNC 8055. L'instruction n'est pas programmée. Consulter dans le manuel de la CNC 8055 la syntaxe correcte. '(SYSTEM)' DÉTECTION CAUSE 8474 Au cours de l'édition. Erreur au cours de la programmation du langage de la CNC 8055. L'instruction n’est pas seule dans le bloc ou elle n'a pas été programmée. Consulter dans le manuel de la CNC 8055 la syntaxe correcte. L'instruction doit être seule dans le bloc. '(WBUF <"texte", expression>)' DÉTECTION CAUSE 8473 Au cours de l'édition. Erreur au cours de la programmation du langage de la CNC 8055. L'instruction n'est pas programmée. Consulter dans le manuel de la CNC 8055 la syntaxe correcte. '(WKEY)' DÉTECTION CAUSE 8472 Au cours de l'édition. Erreur au cours de la programmation du langage de la CNC 8055. L'instruction n'est pas programmée. Consulter dans le manuel de la CNC 8055 la syntaxe correcte. 'SK expression1 = "texte1" <expression2 = "texte2"><...>)' DÉTECTION CAUSE 8471 Au cours de l'édition. Erreur au cours de la programmation du langage de la CNC 8055. L'instruction n'est pas programmée. Consulter dans le manuel de la CNC 8055 la syntaxe correcte. '(DW expression1 = expression2 <expression3 = expression4><...>)' DÉTECTION CAUSE 8470 Au cours de l'édition. Erreur au cours de la programmation du langage de la CNC 8055. L'instruction n'est pas programmée. Consulter dans le manuel de la CNC 8055 la syntaxe correcte. '(IB expression = INPUT"texte" <,format>)' DÉTECTION CAUSE 8469 Au cours de l'édition. Erreur au cours de la programmation du langage de la CNC 8055. L'instruction n'est pas programmée. Consulter dans le manuel de la CNC 8055 la syntaxe correcte. Au cours de l'édition ou traduction d'un programme. Erreur au cours de la programmation du langage de la CNC 8055. La fonction programmée n’existe que sur les fraiseuses et le programme est de tour (fichier pit). Changer le nom du fichier ou utiliser le logiciel correct. S o l ut i o n s d ’ e r r e ur s . 8476 'Fonction sans traduction' DÉTECTION CAUSE SOLUTION 8477 'Minuscules interdites dans la CNC 8055' DÉTECTION CAUSE SOLUTION 8478 SOLUTION SOLUTION SOLUTION Au cours de l'exécution. La syntaxe de l'instruction n'est pas correcte. Vérifier dans le manuel de programmation la syntaxe de l'instruction. 'Programmation non valide dans la fraiseuse' DÉTECTION CAUSE SOLUTION 8487 Au cours de l'édition. Erreur en programmant en langage de la CNC 8055. L'ordre des données dans le bloc n'est pas correct. Consulter dans le manuel de la CNC 8055 la syntaxe correcte. '#DGSPDL nom_broche' DÉTECTION CAUSE SOLUTION 8486 Au cours de l'édition. Erreur en programmant en langage de la CNC 8055. La valeur programmée pour le numéro de bloc ou le nombre de répétitions n'est pas valide. Consulter dans le manuel de la CNC 8055 la syntaxe correcte. 'Ordre des données incorrect' DÉTECTION CAUSE 8485 Au cours de l'édition. Erreur en programmant en langage de la CNC 8055. Le bloc programmé n'est pas valide (bloc vide, bloc type N10, etc.) Consulter dans le manuel de la CNC 8055 la syntaxe correcte. 'Valeur hors de rang' DÉTECTION CAUSE 8484 Au cours de l'exécution. La syntaxe de l'instruction n'est pas correcte. Vérifier dans le manuel de programmation la syntaxe de l'instruction. 'Il manque de l'information dans le bloc' DÉTECTION CAUSE 8483 Au cours de l'exécution. La syntaxe de l'instruction n'est pas correcte. Vérifier dans le manuel de programmation la syntaxe de l'instruction. '#TANGCTRL OFF/SUSP <[axe1, axe2, ...]' DÉTECTION CAUSE SOLUTION 8482 Pendant l’édition et l’exécution. La syntaxe de l'instruction n'est pas correcte. Vérifier dans le manuel de programmation la syntaxe de l'instruction. '#TANGCTRL ON [<axe1 angle1, axe2 angle2, ...><, avance>]' DÉTECTION CAUSE SOLUTION 8480 Au cours de l'édition. Erreur en programmant en langage de la CNC 8055. Le langage de la CNC 8055 ne permet pas l'utilisation de minuscules. Programmer les mots réservés en majuscules. G45 <eje1 angulo1 eje2 angulo2 ...> DÉTECTION CAUSE SOLUTION 8479 Au cours de la traduction d’un programme. La fonction programmée n'a pas équivalent dans la CNC 8055. La CNC ne peut pas traduire la fonction. Consulter les fonctions disponibles dans le manuel de la CNC 8055. Au cours de l'édition. Erreur en programmant en langage de la CNC 8055. Programmation incorrecte de la fonction G15 dans la fraiseuse. Consulter dans le manuel de la CNC 8055 la syntaxe correcte. CNC 8070 'Programmation non valide dans le tour' DÉTECTION CAUSE SOLUTION Au cours de l'édition. Erreur en programmant en langage de la CNC 8055. Programmation incorrecte de la fonction G15 dans le tour. Consulter dans le manuel de la CNC 8055 la syntaxe correcte. (REF: 1901) ·209· S o l ut i o n s d ’ e r r e ur s . 8488 'Le nombre de répétitions n'est pas admis' DÉTECTION CAUSE SOLUTION 8489 '$FOR i = initial, final, incrément' DÉTECTION CAUSE SOLUTION 8490 SOLUTION 8498 8499 Au cours de l'édition. Erreur en programmant en langage de la CNC 8055. Dans la fonction G24/G27 il y a un paramètre en plus. Consulter dans le manuel de la CNC 8055 la syntaxe correcte. 'Paramètres incorrects en fonction' DÉTECTION CAUSE SOLUTION ·210· Au cours de l'édition. Erreur en programmant en langage de la CNC 8055. Valeur incorrecte du paramètre K pour la fonction G. Consulter dans le manuel de la CNC 8055 la syntaxe correcte. 'Il y a un paramètre de plus' DÉTECTION CAUSE SOLUTION (REF: 1901) Au cours de l'exécution. La syntaxe de l'instruction n'est pas correcte. Vérifier dans le manuel de programmation la syntaxe de l'instruction. 'Valeur du paramètre K incorrecte' DÉTECTION CAUSE CNC 8070 Pendant l’édition et l’exécution. La syntaxe de l'instruction n'est pas correcte. Vérifier dans le manuel de programmation la syntaxe de l'instruction. '$WHILE condition' DÉTECTION CAUSE SOLUTION 8497 Au cours de l'exécution. La syntaxe de l'instruction n'est pas correcte. Vérifier dans le manuel de programmation la syntaxe de l'instruction. $WHILE condition DÉTECTION CAUSE SOLUTION 8496 Au cours de l'exécution. La syntaxe de l'instruction n'est pas correcte. Vérifier dans le manuel de programmation la syntaxe de l'instruction. '$CASE expression' DÉTECTION CAUSE SOLUTION 8495 Au cours de l'exécution. La syntaxe de l'instruction n'est pas correcte. Vérifier dans le manuel de programmation la syntaxe de l'instruction. '$SWITCH expression' DÉTECTION CAUSE SOLUTION 8494 Au cours de l'exécution. La syntaxe de l'instruction n'est pas correcte. Vérifier dans le manuel de programmation la syntaxe de l'instruction. '$ELSEIF condition' DÉTECTION CAUSE SOLUTION 8493 Au cours de l'exécution. La syntaxe de l'instruction n'est pas correcte. Vérifier dans le manuel de programmation la syntaxe de l'instruction. '$IF condition' DÉTECTION CAUSE SOLUTION 8492 Au cours de l'exécution. La syntaxe de l'instruction n'est pas correcte. Vérifier dans le manuel de programmation la syntaxe de l'instruction. '$GOTO Nexpression/$GOTO [expression]' DÉTECTION CAUSE SOLUTION 8491 Au cours de l'édition. Erreur en programmant en langage de la CNC 8055. On ne peut programmer que le nombre de répétitions dans un bloc de déplacement. Consulter dans le manuel de la CNC 8055 la syntaxe correcte. Au cours de l'édition. Erreur en programmant en langage de la CNC 8055. Il y a des paramètres invalides dans la fonction G programmée. Consulter dans le manuel de la CNC 8055 la syntaxe correcte. S o l ut i o n s d ’ e r r e ur s . 8502 'L'interpolation circulaire en polaires n'admet pas le rayon' DÉTECTION CAUSE SOLUTION 8503 'Il faut programmer la cote finale du déplacement' DÉTECTION CAUSE SOLUTION 8504 SOLUTION SOLUTION SOLUTION Pendant l’édition et l’exécution. Le nom de la sous-routine n'accepte pas d'espaces vides. Modifier le nom de la sous-routine. #DINDIST ON[0/1, channelNumber <,channelNumber ,channelNumber>]. DÉTECTION CAUSE SOLUTION 8514 Pendant l’édition et l’exécution. La syntaxe de l'instruction n'est pas correcte. Vérifier dans le manuel de programmation la syntaxe de l'instruction. Espace dans le nom de la sous-routine non autorisé. DÉTECTION CAUSE SOLUTION 8513 Pendant l’édition et l’exécution. La syntaxe de l'instruction n'est pas correcte. Vérifier dans le manuel de programmation la syntaxe de l'instruction. #WARNINGSTOP["Text <%d>" <,value>] /[integer]. DÉTECTION CAUSE SOLUTION 8512 Au cours de l'édition. Le numéro programmé dans le caractère générique "?n" est négatif ou supérieur au nombre d’axes du canal. Le numéro programmé dans le caractère générique "?n" doit être un numéro d'axe valide. #ABORT [expresión]/[\"file_name\"]/Nexpresión/OFF DÉTECTION CAUSE SOLUTION 8511 Au cours de l'édition. Le caractère générique "?n" est programmé plus d’une fois dans le bloc. Programmer le caractère générique une seule fois dans le bloc. 'Numéro de caractère générique non valide' DÉTECTION CAUSE 8510 Au cours de l'édition. Erreur en programmant en langage de la CNC 8055. Si dans la fonction G49 on programme le paramètre E, la fonction ne permet plus de paramètres. Consulter dans le manuel de la CNC 8055 la syntaxe correcte. 'Double programmation caractère générique' DÉTECTION CAUSE SOLUTION 8509 Au cours de l'édition. Erreur en programmant en langage de la CNC 8055. Valeur incorrecte du nombre de blocs dans la fonction G41/G42. Consulter dans le manuel de la CNC 8055 la syntaxe correcte. 'Programmer uniquement le paramètre E' DÉTECTION CAUSE 8507 Au cours de l'édition. Erreur en programmant en langage de la CNC 8055. Il manque la cote finale du déplacement sur G8, G9 ou G33. Consulter dans le manuel de la CNC 8055 la syntaxe correcte. 'Valeur incorrecte du nombre des blocs (0-50)' DÉTECTION CAUSE 8506 Au cours de l'édition. Erreur en programmant en langage de la CNC 8055. L'interpolation circulaire en polaires n'admet pas la programmation du rayon; elle n'admet que le paramètre Q. Consulter dans le manuel de la CNC 8055 la syntaxe correcte. Pendant l’édition et l’exécution. La syntaxe de l'instruction n'est pas correcte. Vérifier dans le manuel de programmation la syntaxe de l'instruction. CNC 8070 #DINDIST OFF. DÉTECTION CAUSE SOLUTION Pendant l’édition et l’exécution. La syntaxe de l'instruction n'est pas correcte. Vérifier dans le manuel de programmation la syntaxe de l'instruction. (REF: 1901) ·211· S o l ut i o n s d ’ e r r e ur s . 8515 Le premier paramètre #DINDIST doit être 0 ou 1. DÉTECTION CAUSE SOLUTION 8516 #DINDIST_EXEC_CYCLE[channelNumber]. DÉTECTION CAUSE SOLUTION 8517 SOLUTION 8525 (REF: 1901) ·212· Pendant l’édition et l’exécution. La syntaxe de l'instruction n'est pas correcte. Vérifier dans le manuel de programmation la syntaxe de l'instruction. '#CAM SELECT[<came,>"path\fichier"]' DÉTECTION CAUSE SOLUTION 8526 Pendant l’édition et l’exécution. La syntaxe de l'instruction n'est pas correcte. Vérifier dans le manuel de programmation la syntaxe de l'instruction. #POCKET3D BEGIN/END. DÉTECTION CAUSE SOLUTION CNC 8070 Pendant l’édition et l’exécution. La syntaxe de l'instruction n'est pas correcte. Vérifier dans le manuel de programmation la syntaxe de l'instruction. #POCKET2D BEGIN/END. DÉTECTION CAUSE SOLUTION 8524 Pendant l’édition et l’exécution. La syntaxe de l'instruction n'est pas correcte. Vérifier dans le manuel de programmation la syntaxe de l'instruction. #ROTATEMZ1-4 Pi/+i/-i. DÉTECTION CAUSE SOLUTION 8523 Pendant l’édition et l’exécution. La syntaxe de l'instruction n'est pas correcte. Vérifier dans le manuel de programmation la syntaxe de l'instruction. G174 permet uniquement de programmer un axe. DÉTECTION CAUSE SOLUTION 8522 Pendant l’édition et l’exécution. La variable est uniquement de lecture ou la CNC a bloqué provisoirement la variable pendant qu'elle exécute une opération sur cette dernière. Si la variable est uniquement de lecture, elle peut pas s'écrire. Si la CNC a bloqué la variable, patienter jusqu'à la fin des opérations. #DELETE UserVariableName <, UserVariableName, ...>. DÉTECTION CAUSE SOLUTION 8521 Pendant l’édition et l’exécution. La syntaxe de l'instruction n'est pas correcte. Vérifier dans le manuel de programmation la syntaxe de l'instruction. Variable externe sans permission d'écriture. DÉTECTION CAUSE 8520 Pendant l’édition et l’exécution. La syntaxe de l'instruction n'est pas correcte. Vérifier dans le manuel de programmation la syntaxe de l'instruction. #FEEDND ON/OFF. DÉTECTION CAUSE SOLUTION 8519 Pendant l’édition et l’exécution. La syntaxe de l'instruction n'est pas correcte. Vérifier dans le manuel de programmation la syntaxe de l'instruction. #PATHND ON/OFF. DÉTECTION CAUSE SOLUTION 8518 Pendant l’édition et l’exécution. La syntaxe de l'instruction n'est pas correcte. Vérifier dans le manuel de programmation la syntaxe de l'instruction. Au cours de l'édition et exécution dans MDI. La syntaxe de l'instruction n'est pas correcte. Vérifier dans le manuel de programmation la syntaxe de l'instruction. '#CAM DESELECT[came]' DÉTECTION CAUSE SOLUTION Au cours de l'édition et exécution dans MDI. La syntaxe de l'instruction n'est pas correcte. Vérifier dans le manuel de programmation la syntaxe de l'instruction. S o l ut i o n s d ’ e r r e ur s . 8527 '#REPOS <INT/INI> nomAxe/nomBroche …' DÉTECTION CAUSE SOLUTION 8528 #VOLCOMP ON/OFF DÉTECTION CAUSE SOLUTION 8529 Pendant l’édition et l’exécution. La syntaxe de l'instruction n'est pas correcte. Vérifier dans le manuel de programmation la syntaxe de l'instruction. #DEFROT[ERROR/WARNING/NONE, critère, Q valeurAngle] DÉTECTION CAUSE SOLUTION 8539 Pendant l’édition et l’exécution. La syntaxe de l'instruction n'est pas correcte. Vérifier dans le manuel de programmation la syntaxe de l'instruction. #CSROT<ON><[ROTATE]>/OFF DÉTECTION CAUSE SOLUTION 8537 Pendant l’édition et l’exécution. La syntaxe de l'instruction n'est pas correcte. Vérifier dans le manuel de programmation la syntaxe de l'instruction. #VIRTAX <ON> <[coteAxe]> DÉTECTION CAUSE SOLUTION 8536 Pendant l’édition et l’exécution. La syntaxe de l'instruction n'est pas correcte. Vérifier dans le manuel de programmation la syntaxe de l'instruction. #VIRTAX OFF DÉTECTION CAUSE SOLUTION 8535 Pendant l’édition et l’exécution. La syntaxe de l'instruction n'est pas correcte. Vérifier dans le manuel de programmation la syntaxe de l'instruction. #PWMOUT ON<[FREQ/F valeur, DUTY/D valeur]>/OFF DÉTECTION CAUSE SOLUTION 8534 Pendant l’édition et l’exécution. La syntaxe de l'instruction n'est pas correcte. Vérifier dans le manuel de programmation la syntaxe de l'instruction. #HSC ON[FAST <, E valeur, CORNER valeurAngle>] DÉTECTION CAUSE SOLUTION 8533 Pendant l’édition et l’exécution. La syntaxe de l'instruction n'est pas correcte. Vérifier dans le manuel de programmation la syntaxe de l'instruction. #SWTOUT ON[TON = valeur,TOF = valeur,PON = valeur,POF = valeur]/OFF DÉTECTION CAUSE SOLUTION 8532 Pendant l’édition et l’exécution. La syntaxe de l'instruction n'est pas correcte. Vérifier dans le manuel de programmation la syntaxe de l'instruction. #RENAME SP OFF [nomBroche,...] DÉTECTION CAUSE SOLUTION 8531 Pendant l’édition et l’exécution. La syntaxe de l'instruction n'est pas correcte. Vérifier dans le manuel de programmation la syntaxe de l'instruction. #RENAME AX OFF [nomAxe,...] DÉTECTION CAUSE SOLUTION 8530 Au cours de l'édition. La syntaxe de l'instruction n'est pas correcte. Vérifier dans le manuel de programmation la syntaxe de l'instruction. Après #REPOS, programmer une séquence d’axes et/ou de broches du canal. Pendant l’édition et l’exécution. La syntaxe de l'instruction n'est pas correcte. Vérifier dans le manuel de programmation la syntaxe de l'instruction. CNC 8070 #DEFGRAPH["path\fichier"] DÉTECTION CAUSE SOLUTION Pendant l’édition et l’exécution. La syntaxe de l'instruction n'est pas correcte. Vérifier dans le manuel de programmation la syntaxe de l'instruction. (REF: 1901) ·213· S o l ut i o n s d ’ e r r e ur s . 8540 #RETDSBLK DÉTECTION CAUSE SOLUTION 8541 #COMP3D OFF DÉTECTION CAUSE SOLUTION 8542 SOLUTION SOLUTION 8560 8561 Pendant l’édition et l’exécution. Sur la pièce circulaire définie avec l'instruction #DGWZ, le rayon ou le diamètre interne est supérieur à l'externe. Programmer un rayon ou un diamètre interne est supérieur à l'externe. Au cours de l'édition. Fonction G4 mal programmée. La fonction G4 peut être programmée comme G4 <time> ou G4 K<time>, où <time> est le temps d'attente. Au cours de l'édition et exécution dans MDI. Un déplacement incrémental (commande I) est programmé dans une fonction qui ne le permet pas. Réviser la programmation. Pendant l’édition et l’exécution. La syntaxe de l'instruction n'est pas correcte. Vérifier dans le manuel de programmation la syntaxe de l'instruction. #ISO OFF DÉTECTION CAUSE SOLUTION ·214· Pendant l’édition et l’exécution. La syntaxe de l'instruction n'est pas correcte. Vérifier dans le manuel de programmation la syntaxe de l'instruction. #ISO <ON><[NAME=\"fileName\"]> DÉTECTION CAUSE SOLUTION (REF: 1901) rayon/diamExterne] 'Programmation incrémentale interdite' DÉTECTION CAUSE CNC 8070 rayon/diamInterne, On attendait K expression après G04. DÉTECTION CAUSE SOLUTION 8558 limSupAxe1, Le rayon ou diamètre interne doit être inférieur à l'externe. DÉTECTION CAUSE 8555 Au cours de l'exécution. La programmation du paramètre D dans le bloc n'est pas autorisé. Corriger la programmation. #DGWZ<CYL>[limInfAxe1, <Pi,Ci,...> DÉTECTION CAUSE SOLUTION 8554 Pendant l’édition et l’exécution. La syntaxe de l'instruction n'est pas correcte. Vérifier dans le manuel de programmation la syntaxe de l'instruction. Paramètre D non autorisé dans le bloc. DÉTECTION CAUSE SOLUTION 8553 Pendant l’édition et l’exécution. La syntaxe de l'instruction n'est pas correcte. Vérifier dans le manuel de programmation la syntaxe de l'instruction. #KINORG DÉTECTION CAUSE SOLUTION 8552 Pendant l’édition et l’exécution. La syntaxe de l'instruction n'est pas correcte. Vérifier dans le manuel de programmation la syntaxe de l'instruction. #SELECT ORI[HEAD1-2/TABLE1-2, HEAD1-2/TABLE1-2] DÉTECTION CAUSE SOLUTION 8551 Pendant l’édition et l’exécution. La syntaxe de l'instruction n'est pas correcte. Vérifier dans le manuel de programmation la syntaxe de l'instruction. #COMP3D <ON> <[PARAX/NORMAL]> DÉTECTION CAUSE SOLUTION 8550 Pendant l’édition et l’exécution. La syntaxe de l'instruction n'est pas correcte. Vérifier dans le manuel de programmation la syntaxe de l'instruction. Pendant l’édition et l’exécution. La syntaxe de l'instruction n'est pas correcte. Vérifier dans le manuel de programmation la syntaxe de l'instruction. S o l ut i o n s d ’ e r r e ur s . 8562 #HSC ON[SURFACE <, E valeur, CORNER valeurAngle>] DÉTECTION CAUSE SOLUTION 8563 #GAPCTRL ON/OFF [<axisName posValue> <,GAP value>] DÉTECTION CAUSE SOLUTION 8564 Pendant l’édition et l’exécution. La syntaxe de l'instruction n'est pas correcte. Vérifier dans le manuel de programmation la syntaxe de l'instruction. #CUTTING ON/OFF <[param]> DÉTECTION CAUSE SOLUTION 8573 Pendant l’édition et l’exécution. La syntaxe de l'instruction n'est pas correcte. Vérifier dans le manuel de programmation la syntaxe de l'instruction. #WRITE[<FhandleFichier,> "Texte <%d>"/nºentier <,valeur>] DÉTECTION CAUSE SOLUTION 8572 Pendant l’édition et l’exécution. La syntaxe de l'instruction n'est pas correcte. Vérifier dans le manuel de programmation la syntaxe de l'instruction. #CLOSE<[FhandleFichier]> DÉTECTION CAUSE SOLUTION 8571 Pendant l’édition et l’exécution. La commande NR n'admet pas les valeurs 0 et 1. Programmer la commande NR avec une valeur égale ou supérieure à 2. #OPEN["fichier" <, A/D> <, KEEPLINE> <, FhandleFichier>] DÉTECTION CAUSE SOLUTION 8570 Pendant l’édition et l’exécution. Le cycle n'admet pas la programmation de la commande NR. Éliminer la commande NR du bloc. Pour répéter le bloc, utiliser l'instruction #RPT. Valeur incorrecte de NR (0-1). DÉTECTION CAUSE SOLUTION 8569 Pendant l’édition et l’exécution. La syntaxe de l'instruction n'est pas correcte. Vérifier dans le manuel de programmation la syntaxe de l'instruction. Programmation de NR non autorisée dans le cycle. DÉTECTION CAUSE SOLUTION 8568 Pendant l’édition et l’exécution. La syntaxe de l'instruction n'est pas correcte. Vérifier dans le manuel de programmation la syntaxe de l'instruction. #MATERIAL[fileName] DÉTECTION CAUSE SOLUTION 8567 Pendant l’édition et l’exécution. La syntaxe de l'instruction n'est pas correcte. Vérifier dans le manuel de programmation la syntaxe de l'instruction. #LEAPEND DÉTECTION CAUSE SOLUTION 8566 Pendant l’édition et l’exécution. La syntaxe de l'instruction n'est pas correcte. Vérifier dans le manuel de programmation la syntaxe de l'instruction. #LEAPBEGIN[<DOWN> <,G90/G91> <,POS posValue> <,POSLIMIT value>] DÉTECTION CAUSE SOLUTION 8565 Pendant l’édition et l’exécution. La syntaxe de l'instruction n'est pas correcte. Vérifier dans le manuel de programmation la syntaxe de l'instruction. Pendant l’édition et l’exécution. La syntaxe de l'instruction n'est pas correcte. Vérifier dans le manuel de programmation la syntaxe de l'instruction. CNC 8070 #GAPPOS[<nomAxe coteAxe> <nomAxe coteAxe> <nomAxecoteAxe>] DÉTECTION CAUSE SOLUTION Pendant l’édition et l’exécution. La syntaxe de l'instruction n'est pas correcte. Vérifier dans le manuel de programmation la syntaxe de l'instruction. (REF: 1901) ·215· S o l ut i o n s d ’ e r r e ur s . 8701 'Il manque la ressource ou numéro après le symbole' DÉTECTION CAUSE SOLUTION 8702 'Ressource avant symbole' DÉTECTION CAUSE SOLUTION 8703 CNC 8070 (REF: 1901) ·216· Au cours de l'édition. Il manque la seconde consultation de la commande OR. Programmer "consultation OR consultation" 'Il manque la première opérande de la consultation AND' DÉTECTION CAUSE SOLUTION 8712 Au cours de l'édition. Il manque la première consultation de la commande OR. Programmer "consultation OR consultation" 'Il manque la deuxième opérande de la consultation OR' DÉTECTION CAUSE SOLUTION 8711 Au cours de l'édition. Il faut programmer la période du module périodique PE. Programmer "PE période". 'Il manque la première opérande de la consultation OR' DÉTECTION CAUSE SOLUTION 8710 Au cours de l'édition. Commande DEF ou PDEF. Il faut programmer le symbole, la ressource ou le numéro. Programmer "DEF/PDEF symbole ressource" ou "DEF/PDEF symbole numéro". 'Il manque période de module périodique' DÉTECTION CAUSE SOLUTION 8709 Au cours de l'édition. Commande DEF ou PDEF. I y a deux numéros programmés. Programmer "DEF/PDEF symbole ressource" ou "DEF/PDEF symbole numéro". 'Il manque symbole suivi de ressource ou numéro' DÉTECTION CAUSE SOLUTION 8708 Au cours de l'édition. Commande DEF ou PDEF. I y a deux ressources programmées. Programmer "DEF/PDEF symbole ressource" ou "DEF/PDEF symbole numéro". 'On ne peut pas redéfinir les numéros' DÉTECTION CAUSE SOLUTION 8707 Au cours de l'édition. Commande DEF ou PDEF. Il y a deux symboles programmés. Programmer "DEF/PDEF symbole ressource" ou "DEF/PDEF symbole numéro". 'On ne peut pas redéfinir les ressources' DÉTECTION CAUSE SOLUTION 8706 Au cours de l'édition. Commande DEF ou PDEF. Le numéro est programmé avant le symbole. Programmer "DEF/PDEF symbole numéro". 'On attendait ressource ou nombre au lieu de symbole' DÉTECTION CAUSE SOLUTION 8705 Au cours de l'édition. Commande DEF ou PDEF. La ressource est programmée avant le symbole. Programmer "DEF/PDEF symbole ressource". 'Numéro avant symbole' DÉTECTION CAUSE SOLUTION 8704 Au cours de l'édition. Il manque la ressource après DFU, DFD, ERA ou après le symbole de DEF/PDEF. Programmer "DEF/PDEF symbole ressource" ou "DFU/DFD/ERA ressource" Au cours de l'édition. Il manque la première consultation de la commande AND. Programmer "consultation AND consultation" 'Il manque la deuxième opérande de la consultation AND' DÉTECTION CAUSE SOLUTION Au cours de l'édition. Il manque la seconde consultation de la commande AND. Programmer "consultation AND consultation" S o l ut i o n s d ’ e r r e ur s . 8713 'Il manque la première opérande de la consultation XOR' DÉTECTION CAUSE SOLUTION 8714 'Il manque la deuxième opérande de la consultation XOR' DÉTECTION CAUSE SOLUTION 8715 SOLUTION Au cours de l'édition. Il manque l'instruction après "=". Programmer "condition = instruction". 'Il manque la deuxième opérande du CPS' DÉTECTION CAUSE SOLUTION 8723 Au cours de l'édition. Il manque la ressource après la commande DFD. Programmer "DFD ressource". 'On attendait instruction d'action après "="' DÉTECTION CAUSE SOLUTION 8722 Au cours de l'édition. Il manque la ressource après la commande DFU. Programmer "DFU ressource". 'Il manque la ressource DFD' DÉTECTION CAUSE SOLUTION 8721 Au cours de l'édition. Le nombre de parenthèses d’ouverture ne coïncide pas avec le nombre de parenthèses de fermeture. Vérifier que chaque parenthèse d’ouverture a sa parenthèse de fermeture correspondante. 'Il manque la ressource DFU' DÉTECTION CAUSE SOLUTION 8720 Au cours de l'édition. Il y a une parenthèse de fermeture mais il manque la parenthèse d’ouverture. Programmer "(consultation)" 'Parenthèse dépareillée' DÉTECTION CAUSE 8719 Au cours de l'édition. Il y a une parenthèse d’ouverture mais il manque la parenthèse de fermeture. Programmer "(consultation)" 'Il manque parenthèse d'ouverture' DÉTECTION CAUSE SOLUTION 8718 Au cours de l'édition. Il manque la consultation de la commande NOT. Programmer "NOT consultation" 'Il manque parenthèse de fermeture' DÉTECTION CAUSE SOLUTION 8717 Au cours de l'édition. Il manque la seconde consultation de la commande XOR. Programmer "consultation XOR consultation" 'Il manque l'opérande de la consultation NOT' DÉTECTION CAUSE SOLUTION 8716 Au cours de l'édition. Il manque la première consultation de la commande XOR. Programmer "consultation XOR consultation" Au cours de l'édition. Il manque la deuxième ressource de la commande CPS. Programmer "CPS ressource opération ressource". Les ressources pourront être un registre, un symbole ou un numéro. L’opération pourra être une des commandes GT, GE, EQ, NE, LE, LT. CNC 8070 'Il manque l'opérateur du CPS' DÉTECTION CAUSE SOLUTION Au cours de l'édition. Il manque l'opération de la commande CPS. Programmer "CPS ressource opération ressource". Les ressources pourront être un registre, un symbole ou un numéro. L’opération pourra être une des commandes GT, GE, EQ, NE, LE, LT. (REF: 1901) ·217· S o l ut i o n s d ’ e r r e ur s . 8724 'Il manque l'opérateur et la deuxième opérande du CPS' DÉTECTION CAUSE SOLUTION 8725 'Il manque la première opérande du CPS' DÉTECTION CAUSE SOLUTION 8726 CNC 8070 (REF: 1901) ·218· Au cours de l'édition. Il manque le temporisateur et la valeur de présélection dans la commande TG. Programmer "TG temporisateur présélection". La valeur de présélection pourra être un registre, un symbole ou un numéro. 'Ordre des opérandes inversées dans TG' DÉTECTION CAUSE SOLUTION 8733 Au cours de l'édition. Il manque la valeur de présélection dans la commande TG. Programmer "TG temporisateur présélection". La valeur de présélection pourra être un registre, un symbole ou un numéro. 'Il manque l’indice du temporisateur et présélection dans TG' DÉTECTION CAUSE SOLUTION 8732 Au cours de l'édition. Il manque le temporisateur dans la commande TRS. Programmer "TRS temporisateur". 'Il manque présélection dans TG' DÉTECTION CAUSE SOLUTION 8731 Au cours de l'édition. Il manque le temporisateur dans la commande TEN. Programmer "TEN temporisateur". 'Il manque l’indice du temporisateur dans TRS' DÉTECTION CAUSE SOLUTION 8730 Au cours de l'édition. L’opération programmée dans la commande CPS n’est pas valide. Programmer "CPS ressource opération ressource". Les ressources pourront être un registre, un symbole ou un numéro. L’opération pourra être une des commandes GT, GE, EQ, NE, LE, LT. 'Il manque l’indice du temporisateur dans TEN' DÉTECTION CAUSE SOLUTION 8729 Au cours de l'édition. Il manque l’opérateur et les deux ressources de la commande CPS. Programmer "CPS ressource opération ressource". Les ressources pourront être un registre, un symbole ou un numéro. L’opération pourra être une des commandes GT, GE, EQ, NE, LE, LT. 'Opérateur de comparaison non valide' DÉTECTION CAUSE SOLUTION 8728 Au cours de l'édition. Il manque la première ressource de la commande CPS. Programmer "CPS ressource opération ressource". Les ressources pourront être un registre, un symbole ou un numéro. L’opération pourra être une des commandes GT, GE, EQ, NE, LE, LT. 'Il manque la première opérande, l’opérateur et la seconde opérande du CPS' DÉTECTION CAUSE SOLUTION 8727 Au cours de l'édition. Il manque l’opérateur et la deuxième ressource de la commande CPS. Programmer "CPS ressource opération ressource". Les ressources pourront être un registre, un symbole ou un numéro. L’opération pourra être une des commandes GT, GE, EQ, NE, LE, LT. Au cours de l'édition. Programmation incorrecte de la commande TG. Programmer "TG temporisateur présélection". La valeur de présélection pourra être un registre, un symbole ou un numéro. 'On attendait instruction d'action après NOT' DÉTECTION CAUSE SOLUTION Au cours de l'édition. Il manque l'instruction après NOT. Programmer "NOT instruction". S o l ut i o n s d ’ e r r e ur s . 8734 'Il manque l’indice de compteur dans CUP' DÉTECTION CAUSE SOLUTION 8735 'Il manque l’indice de compteur dans CDW' DÉTECTION CAUSE SOLUTION 8736 Au cours de l'édition. Il manque la ressource dans la commande CPL. Programmer "CPL ressource". 'Instruction antérieure incorrecte' DÉTECTION CAUSE SOLUTION 8895 Au cours de l'édition. Il manque la ressource dans la commande RES. Programmer "RES ressource". 'Il manque opérande dans CPL' DÉTECTION CAUSE SOLUTION 8894 Au cours de l'édition. Il manque la ressource dans la commande SET. Programmer "SET ressource". 'Il manque opérande dans RES' DÉTECTION CAUSE SOLUTION 8742 Au cours de l'édition. Programmation incorrecte de la commande CPR. Programmer "CPR compteur présélection". La valeur de présélection pourra être un registre, un symbole ou un numéro. 'Il manque opérande dans SET' DÉTECTION CAUSE SOLUTION 8741 Au cours de l'édition. Il manque le compteur et la valeur de présélection dans la commande CPR. Programmer "CPR compteur présélection". La valeur de présélection pourra être un registre, un symbole ou un numéro. 'Ordre des opérandes inversées dans CPR' DÉTECTION CAUSE SOLUTION 8740 Au cours de l'édition. Il manque la valeur de présélection dans la commande CPR. Programmer "CPR compteur présélection". La valeur de présélection pourra être un registre, un symbole ou un numéro. 'Il manque l’indice du compteur et présélection dans CPR' DÉTECTION CAUSE SOLUTION 8739 Au cours de l'édition. Il manque le compteur dans la commande CEN. Programmer "CEN compteur" 'Il manque présélection dans CPR' DÉTECTION CAUSE SOLUTION 8738 Au cours de l'édition. Il manque le compteur dans la commande CDW. Programmer "CDW compteur". 'Il manque l’indice de compteur dans CEN' DÉTECTION CAUSE SOLUTION 8737 Au cours de l'édition. Il manque le compteur dans la commande CUP. Programmer "CUP compteur". En compilant le programme PLC. L’analyse du programme de PLC que réalise le compilateur, avant sa conversion à C, a détecté une instruction incorrecte. La sortie d’erreurs indique l’instruction suivant l’incorrecte. Corriger, supprimer ou commenter l’instruction incorrecte. CNC 8070 'Instruction incorrecte' DÉTECTION CAUSE SOLUTION En compilant le programme PLC. L’analyse du programme de PLC que réalise le compilateur, avant sa conversion à C, a détecté une instruction incorrecte. La sortie d’erreurs indique l’instruction incorrecte. Corriger, supprimer ou commenter l’instruction incorrecte. (REF: 1901) ·219· S o l ut i o n s d ’ e r r e ur s . 8896 'Le module vide n'est permis que sur CY1' DÉTECTION CAUSE SOLUTION CNC 8070 (REF: 1901) ·220· En compilant le programme PLC. Un module PRG, PE ou SUB vide est programmé dans le programme PLC. En cas de module vide, on peut le supprimer ou bien mettre une seule instruction qui soit “;”. S o l ut i o n s d ’ e r r e ur s . 9000-9999 9301 'Les axes maître et esclave doivent avoir le même REFFEED1 et REFFEED2' DÉTECTION CAUSE SOLUTION 9302 'Pour assumer la nouvelle valeur il est nécessaire de redémarrer windows' DÉTECTION CAUSE SOLUTION 9303 SOLUTION SOLUTION SOLUTION SOLUTION Pendant la validation des paramètres machine. La CNC ne peut pas activer le filtre automatique du mode HSC FAST parce qu’il y a trois filtres de fréquence actifs sur l’axe. Supprimer un filtre de fréquence de l’axe ou supprimer le filtre du mode HSC FAST. 'Avec l'option de Software Motion Control le type de canal "CHTYPE" doit être de PLC' DÉTECTION CAUSE SOLUTION 9308 Pendant la validation des paramètres machine. Un des filtres passe-bas de l’axe a un numéro d’ordre trop élevé pour la fréquence définie, ce qui pourrait produire un dépassement. Vérifier les paramètres machine. Réduire l’ordre du filtre ou augmenter la fréquence. 'Filtre FAST incompatible avec le 3ème filtre d'axe' DÉTECTION CAUSE 9307 Pendant la validation des paramètres machine. Il y a un couple gantry ou tandem dont les axes maître et esclave ont différent paramètre OPMODEP. Vérifier les paramètres machine. Les deux axes doivent avoir le même paramètre OPMODEP. 'Il est conseillé de réduire l'ordre du filtre' DÉTECTION CAUSE 9306 Pendant la validation des paramètres machine. Le paramètre PRBDI1 ou PRBDI2 fait référence à une entrée numérique non valide. Seules sont valides les entrées numériques qui appartiennent à des modules Fagor ou les entrées logiques si on ne veut que simuler le palpeur. Affecter aux paramètres PRBDI1 et PRBDI2 une entrée numérique d’un module Fagor ou une entrée logique. 'Axes gantry: Les deux axes SERCOS doivent avoir le même OPMODEP' DÉTECTION CAUSE 9305 Pendant la validation des paramètres machine. Une modification des paramètres machine exige le redémarrage de Windows pour prendre effet. Redémarrer windows. 'Le palpeur doit être associé à l'entrée numérique du nœud Fagor' DÉTECTION CAUSE 9304 Pendant la validation des paramètres machine. Il y a un couple gantry ou tandem dont les axes maître et esclave ont une vitesse de recherche de zéro différente sur un set (paramètres REFFEED1 et REFFEED2). Vérifier les paramètres machine. La vitesse rapide et lente de recherche de référence machine (paramètres REFFEED1 et REFFEED2) devra être la même sur les deux axes. Pendant la validation des paramètres machine. C’est un modèle MC et un canal n’est pas défini comme canal de PLC. Vérifier les paramètres machine. Sur le modèle MC, tous les canaux doivent être de PLC (paramètre CHTYPE). CNC 8070 'Les positions de compensation hors de rang ne sont pas admises' DÉTECTION CAUSE SOLUTION Pendant la validation des paramètres machine. La table de compensation de vis ou de compensation croisée de l’axe a des positions définies hors des limites du module. Définir toutes les positions dans les limites de module. (REF: 1901) ·221· S o l ut i o n s d ’ e r r e ur s . 9309 'Si le nombre de magasins est 0, il faut permettre l’outil de terre' DÉTECTION CAUSE SOLUTION 9310 'On ne peut pas changer l’override de broche pendant le filetage si feedforward < 90%' DÉTECTION CAUSE SOLUTION 9311 SOLUTION SOLUTION SOLUTION CNC 8070 ·222· Pendant la validation des paramètres machine ou le démarrage de la CNC. Les axes d’un groupe multi-axe ont le paramètre OPMODEP différent. Vérifier les paramètres machine. Tous les axes d'un groupe multi-axe doivent avoir le paramètre OPMODEP égal. 'Groupe d'axes avec différentes mesures: tous les axes SERCOS doivent être vitesse' DÉTECTION CAUSE SOLUTION (REF: 1901) Pendant la validation des paramètres machine ou le démarrage de la CNC. L'asservissement admet 8 gammes et le nombre total de sets de paramètres définis dans un groupe MULTIAXIS dépasse cette valeur. Réduire le nombre d’axes du groupe MULTIAXIS ou réduire le nombre de jeux de paramètres des axes du groupe. 'Les axes du groupe n'ont pas le même OPMODEP: tous vitesse ou tous position' DÉTECTION CAUSE SOLUTION 9317 Pendant la validation des paramètres machine ou le démarrage de la CNC. Les axes d’un groupe MULTIAXIS ne sont pas tous associés au même asservissement (paramètre DRIVEID). Tous les axes Sercos d’un groupe MULTIAXIS doivent être associés au même asservissement et donc avoir le même paramètre DRIVEID. 'Le nombre de Sets du groupe dépasse le nombre de Sets de l'asservissement' DÉTECTION CAUSE 9316 Pendant la validation des paramètres machine ou le démarrage de la CNC. Il n’y a aucun axe dans le système ayant le même DRIVEID que celui indiqué en définissant un groupe MULTIAXIS. Affecter un DRIVEID dans les groupes MULTIAXIS qui soit associé à des axes du système. 'L'axe SERCOS du groupe multi-axe a un DRIVEID différent' DÉTECTION CAUSE 9315 Pendant la validation des paramètres machine ou le démarrage de la CNC. Un des axes fait partie d’un couple gantry et d’un groupe MULTIAXIS. Corriger la table d'axes gantry et multi-axe. Un axe ne peut être que dans l’une des deux configurations. 'DRIVEID de l'axe du groupe MULTIAXIS non valide dans le système' DÉTECTION CAUSE 9314 Pendant la validation des paramètres machine ou le démarrage de la CNC. Un des axes fait partie d’un couple tandem et d’un groupe MULTIAXIS. Corriger la table d'axes tandem et multi-axe. Un axe ne peut être que dans l’une des deux configurations. 'Un axe GANTRY ne peut pas être dans un groupe MULTIAXIS' DÉTECTION CAUSE SOLUTION 9313 Pendant la validation des paramètres machine ou l’exécution d’un filetage G33. On ne peut pas modifier l’override de la broche pendant le filetage si le feedforward est inférieur à 90%, pour éviter d’endommager le filet. Augmenter le feedforward de la broche. 'Un axe TANDEM ne peut pas être dans un groupe MULTIAXIS' DÉTECTION CAUSE SOLUTION 9312 Pendant la validation des paramètres machine. La machine n’a aucun magasin et n’admet pas d’outils de terre. Pour pouvoir changer d’outil sur une machine sans magasins, la machine doit admettre des outils de terre (paramètre GROUND). Pendant la validation des paramètres machine. Les axes d’un groupe multi-axe ont le paramètre COUNTERID différent et ne sont pas Sercos vitesse. Vérifier les paramètres machine. Tous les axes d'un groupe multi-axe doivent avoir le paramètre COUNTERID égal, si le paramètre n'est pas égal, les axes doivent être des axes Sercos vitesse. S o l ut i o n s d ’ e r r e ur s . 9318 'Deux axes en différents groupes multi-axes avec le même COUNTERID dans l'un des SETs' DÉTECTION CAUSE SOLUTION 9319 'Deux axes en différents groupes multi-axes avec le même ANAOUTID dans l'un des SETs' DÉTECTION CAUSE SOLUTION 9320 SOLUTION Pendant la validation des paramètres machine ou le démarrage de la CNC. Il y a un asservissement Mechatrolink qui fait partie d’un groupe MULTIAXIS. Un asservissement Mechatrolink ne peut pas faire partie d’un groupe MULTIAXIS. Supprimer l’axe Mechatrolink du groupe ou utiliser MULTIAXIS ou utiliser des asservissements Sercos. 'Axes Mechatrolink: Les inverters doivent être des broches' DÉTECTION CAUSE SOLUTION 9326 Pendant la validation des paramètres machine ou le démarrage de la CNC. Il y a un asservissement Mechatrolink qui fait partie d’un couple tandem. Un asservissement Mechatrolink ne peut pas faire partie d’un axe tandem. Supprimer l’axe Mechatrolink du couple tandem ou utiliser des asservissements Sercos. 'Avec les axes Mechatrolink les groupes MULTIAXIS ne sont pas admis' DÉTECTION CAUSE SOLUTION 9325 Pendant la validation des paramètres machine ou le démarrage de la CNC. On ne dispose pas du hardware nécessaire pour travailler avec des axes Mechatrolink. Contacter Fagor Automation. 'Avec les axes Mechatrolink les axes Tandem ne sont pas admis' DÉTECTION CAUSE SOLUTION 9324 Pendant la validation des paramètres machine ou le démarrage de la CNC. Les axes d’un groupe MULTIAXIS ont le paramètre DRIVETYPE différent. Vérifier les paramètres machine. Tous les axes d’un groupe MULTIAXIS doivent avoir le même paramètre DRIVETYPE ; tous les axes doivent être analogiques ou Sercos. 'Il n'y a pas de Hardware pour les axes Mechatrolink' DÉTECTION CAUSE 9323 Pendant la validation des paramètres machine. Les axes d’un groupe MULTIAXIS ont le paramètre ABSFEEDBACK différent. Vérifier les paramètres machine. Tous les axes d'un groupe MULTIAXIS doivent avoir le paramètre ABSFEEDBACK égal. 'Les axes du groupe multi-axis doivent avoir le même DRIVETYPE' DÉTECTION CAUSE SOLUTION 9322 Pendant la validation des paramètres machine ou le démarrage de la CNC. Il y a des axes dans différents groupes MULTIAXIS partageant la même sortie analogique. Changer le paramètre ANAOUTID des axes impliqués pour qu’ils ne partagent pas la même sortie analogique. 'Les axes maître et esclave doivent avoir le même ABSFEEDBACK' DÉTECTION CAUSE SOLUTION 9321 Pendant la validation des paramètres machine ou le démarrage de la CNC. Il y a des axes dans différents groupes MULTIAXIS partageant la même entrée de mesure. Changer le paramètre CONTERID des axes impliqués pour qu’ils ne partagent pas la même entrée de mesure. Pendant la validation des paramètres machine ou le démarrage de la CNC. Dans une configuration Mechatrolink, les inverters doivent toujours être des broches. Vérifier les paramètres machine. 'Mechatrolink I: Looptime 2 ms' DÉTECTION CAUSE SOLUTION Pendant la validation des paramètres machine ou le démarrage de la CNC. Le mode MlinkI-I Mechatrolink n’’admet qu’un temps de cycle de 2 ms. Pour le mode Mlink-I assigner un temps de cycle de 2 ms (paramètre LOOPTIME) ou utiliser le mode Mlink II (paramètre MLINK). CNC 8070 (REF: 1901) ·223· S o l ut i o n s d ’ e r r e ur s . 9327 'Mechatrolink: Nombre maximum d’axes et de broches dépassé' DÉTECTION CAUSE SOLUTION 9328 'MECHATROLINK II: Maximum 2 variables DRV par axe' DÉTECTION CAUSE SOLUTION 9329 SOLUTION SOLUTION SOLUTION CNC 8070 SOLUTION (REF: 1901) Pendant la validation des paramètres machine ou le démarrage de la CNC. Le hardware de l’unité centrale est pour le bus Sercos et les asservissements sont Mechatrolink. Utiliser des asservissements Sercos. Vérifier le type d'asservissement défini dans les paramètres machine (paramètre DRIVETYPE). 'Hardware Mechatrolink n'est pas compatible avec les axes Sercos' DÉTECTION CAUSE SOLUTION ·224· Pendant la validation des paramètres machine ou le démarrage de la CNC. Dans les axes analogiques avec mesure à distance (paramètre COUNTERTYPE), le paramètre COUNTERID ne peut pas avoir une valeur 0 (zéro). Vérifier les paramètres machine. Vérifier le type de mesure affecté à l’axe (paramètre COUNTERTYPE). Dans les axes analogiques avec mesure à distance, le paramètre COUNTERID indique la direction logique de l'asservissement, qui ne peut pas être zéro. 'Hardware Sercos n'est pas compatible avec les axes Mechatrolink' DÉTECTION CAUSE 9334 Pendant la validation des paramètres machine ou le démarrage de la CNC. On ne peut envoyer que les sous-commandes qui résolvent les variables et les paramètres sur Mechatrolink II à 32 octets. Pour pouvoir accéder aux variables et aux paramètres de l'asservissement (DRV), il faut configurer le bus comme Mechatrolink II à 32 octets (paramètres MLINK et DATASIZE). 'COUNTERTYPE à distance et COUNTERID 0 incompatibles' DÉTECTION CAUSE 9333 Pendant la validation des paramètres machine ou le démarrage de la CNC. Les bus numériques Sercos et Mechatrolink sont incompatibles. Vérifier les paramètres machine. • Avec le bus Sercos, définir sur tous les axes le paramètre MLINK = Non et de plus DRIVETYPE ne peut pas valoir "Mlink". • Avec le bus Mechatrolink, définir sur tous les axes le paramètre MLINK différent de "non" et de plus, DRIVETYPE ne peut pas valoir "Sercos". 'On n'admet pas des variables ou paramètres DRV avec Mechatrolink I ou Mechatrolink II à 17 bytes' DÉTECTION CAUSE 9332 Pendant la validation des paramètres machine ou le démarrage de la CNC. Dans la table de variables de l'asservissement (DRV) des paramètres OEM, des paramètres et des variables sont assignés à un même axe. La définition de paramètres et de variables pour un même axe est exclusive ou des paramètres ou des variables sont définis. 'Avec les axes Mechatrolink les axes Sercos ne sont pas admis' DÉTECTION CAUSE SOLUTION 9331 Pendant la validation des paramètres machine ou le démarrage de la CNC. Dans la table de paramètres OEM, plus de deux variables DRV sont affectées à un même axe. Affecter un maximum de deux variables DRV à chaque axe. 'MECHATROLINK II: Des variables et des paramètres DRV ne sont pas permis sur le même axe' DÉTECTION CAUSE 9330 Pendant la validation des paramètres machine ou le démarrage de la CNC. La configuration Mechatrolink dépasse le nombre maximum permis d’axes et de broches (servos et inverters). Le mode Mlink-I admet un maximum de 14 éléments et le mode Mlink-II 30 éléments. L’utilisation d’un intervalle de temps (Slot Time) de 90 microsecondes au lieu de 60, réduit aussi le nombre maximum d'asservissements. Réduire le nombre d'asservissements ou utiliser le mode Mlink-II avec un slot time de 60 microsecondes. Pendant la validation des paramètres machine ou le démarrage de la CNC. Le hardware de l’unité centrale est pour le bus Mechatrolink et les asservissements sont Sercos. Utiliser des asservissements Mechatrolink. Vérifier le type d'asservissement défini dans les paramètres machine (paramètre DRIVETYPE). S o l ut i o n s d ’ e r r e ur s . 9336 'Paramètres machine incompatibles' DÉTECTION CAUSE SOLUTION 9337 Sercos position ne fonctionne pas avec LOOPTIME supérieur à 8 ms. DÉTECTION CAUSE SOLUTION 9340 SOLUTION SOLUTION Au cours du démarrage de la CNC ou la validation des paramètres machine. Le set actif sur plusieurs axes utilise la même sortie analogique d’un module RCS-S (paramètre COUNTERID). Deux sets actifs ne peuvent pas partager la même sortie analogique. Activer un set différent sur un axe ou configurer une sortie analogique différente dans le set. 'Offset de la cinématique, hors de la gamme permise par la valeur maximale' DÉTECTION. CAUSE SOLUTION 9347 Au cours du démarrage de la CNC ou la validation des paramètres machine. Plusieurs sets qui avec la même entrée de mesure d’un module RCS.S (paramètre COUNTERID), n’ont pas la même valeur dans un des paramètres suivants: FEEDBACKTYPE, SSITYPE, SSI, I0TYPE, ABSOFF, EXTMULT, REFPULSE, I0CODDI1, I0CODDI2, NPULSES et FBACKAL. Dans les sets avec un même COUNTERID, définir les paramètres indiqués avec la même valeur. 'Compteur Sercos: Set actif à plusieurs axes ne peut pas avoir le même paramètre ANAOUTID' DÉTECTION CAUSE 9342 Pendant la validation des paramètres machine ou le démarrage de la CNC. Les régulateurs Sercos position disposent d'une temps de cycle limité à 8 ms. Attribuer au paramètre machine LOOPTIME une valeur égale ou inférieure à 8 ms ou utiliser les régulateurs dans vitesse (OPMODE = Vitesse). 'Compteur Sercos: sets con igual COUNTERID deben tener igual el\los parámetro(s) FEEDBACKTYPE, SSITYPE, SSI, I0TYPE, ABSOFF, EXTMULT, REFPULSE, I0CODDI1, I0CODDI2, NPULSES et FBACKAL' DÉTECTION CAUSE 9341 Pendant la validation des paramètres machine ou le démarrage de la CNC. Deux performances incompatibles entre elles sont actives. Les paramètres machine en rapport figurent dans le message d’erreur (par exemple, les paramètres HBLS et MODBUSSVRRS ne sont pas compatibles car les deux utilisent la liaison série). Annuler un des deux paramètres mentionnés dans le message d'erreur. Au cours de la validation de paramètres machine ou de l'écriture d'une variable. L'offset défini par la cinématique est hors de la gamme permise par le paramètre machine. Assigner à la variable V.MPK.OFTDATAkin[nb] de la cinématique une valeur comprise entre "- MAX OFFSET" et "+ MAX OFFSET" (gamme définie par le paramètre machine de la cinématique correspondante). 'Axe répété dans VOLCOMP' DÉTECTION CAUSE SOLUTION Pendant la validation des paramètres machine ou le démarrage de la CNC. Dans les paramètres VMOVAXIS ou VCOMPAXIS de la compensation volumétrique le même axe est défini deux fois. Corriger les paramètres machine. CNC 8070 (REF: 1901) ·225· S o l ut i o n s d ’ e r r e ur s . 23000-23999 23038 Erreur dans le fichier de compensation volumétrique: Valeur maximale dépassée. DÉTECTION CAUSE SOLUTION 23039 Erreur dans le fichier de compensation volumétrique: Valeur de la plage non valable. DÉTECTION CAUSE SOLUTION 23101 SOLUTION SOLUTION SOLUTION CNC 8070 ·226· Au cours de l'exécution. Le PLC a essayé d’activer une compensation volumétrique non définie correctement et par conséquent la compensation de la machine n’est pas possible. Définir une compensation volumétrique adéquate dans les paramètres machine (paramètres VOLCOMP). 'La marque VOLCOMP ne peut pas être activée avec une autre table active sur des axes communs' DÉTECTION CAUSE SOLUTION (REF: 1901) Au cours de l'exécution. La CNC a détecté une erreur interne dans le calcul de la compensation volumétrique et a annulé les valeurs de la compensation. Contacter Fagor Automation. 'La marque VOLCOMP ne peut pas être activée sans une table validée' DÉTECTION CAUSE 23104 Pendant la validation des paramètres machine ou le démarrage de la CNC. Le fichier de définition de la compensation volumétrique ne contient pas les données adéquates. Compensation volumétrique de base. • Le fichier n'est pas de type csv. • Le format du fichier défini dans VCOMPFILE n'est pas valable. • Tous les points du fichier défini dans VCOMPFILE ne sont pas définis. Le nombre de points est défini par l'expression: NPOINTSAX1 × NPOINTSAX2 × NPOINTSAX3 Compensation volumétrique moyenne et grande: • Le format du fichier défini dans VCOMPFILE n'est pas valable. Sélectionner un fichier adéquat. Dans la compensation volumétrique de base, le fichier doit être du type csv et tous ses points doivent être définis. 'Erreur du système de compensation volumétrique: compensation désactivée' DÉTECTION CAUSE 23103 Pendant la validation des paramètres machine ou le démarrage de la CNC. Le fichier de définition de la compensation volumétrique ne contient pas les données adéquates. Changer la valeur de la plage par la différence entre les valeurs maximale et minimale. 'Erreur dans l'analyse du fichier de définition de la compensation volumétrique' DÉTECTION CAUSE 23102 Pendant la validation des paramètres machine ou le démarrage de la CNC. Le fichier de définition de la compensation volumétrique ne contient pas les données adéquates. Mettre comme valeur maximale dans le fichier, la valeur maximale de la table. Au cours de l'exécution. Le PLC a essayé d’activer une compensation volumétrique avec une autre active et un des axes utilisés est commun dans les deux compensations. Il ne peut pas y avoir deux compensations volumétriques actives avec un axe en commun. Avant d’activer une compensation, annuler l’active avec la marque de PLC correspondante. S o l ut i o n s d ’ e r r e ur s . 24000-24999 24001 EtherCAT: Datalink non présent. DÉTECTION CAUSE SOLUTION 24002 EtherCAT: Paquet perdu. DÉTECTION CAUSE SOLUTION 24003 SOLUTION SOLUTION Pendant la validation des paramètres machine ou le démarrage de la CNC. Le fichier pour accéder aux ressources du bus EtherCAT à partir du système CNCPLC Fagor n'existe pas. Générer un fichier de chargement (cartographie) avec l'application Fagor EtherCAT Mapper et le copier dans Mtb/Data. Le fichier doit s'appeler resourceRouterConf.xml. EtherCAT: Format de fichier de chargement incorrect. DÉTECTION CAUSE SOLUTION 24022 Pendant la validation des paramètres machine ou le démarrage de la CNC. Le fichier ENI de configuration du réseau EtherCAT a un format illisible pour la CNC. Le configurateur qui a généré le fichier ENI peut ne pas être compatible avec la CNC. Le fichier peut être incomplet ou corrompu. Vérifier le fichier. EtherCAT: Le fichier de chargement n'existe pas. DÉTECTION CAUSE 24021 Pendant la validation des paramètres machine ou le démarrage de la CNC. Le fichier ENI de configuration du réseau EtherCAT n'existe pas. Copier dans Mtb/Data le fichier ENI de configuration du réseau EtherCAT. Le fichier doit s'appeler fagor_ethercatConfFile.xml. EtherCAT: Format de fichier ENI de configuration incorrect. DÉTECTION CAUSE 24020 Au cours du fonctionnement de la CNC. Fonctionnement incorrect de l'un des esclaves d'EtherCAT. Vérifier les connexions et l'état des esclaves. EtherCAT: Le fichier ENI de configuration n'existe pas. DÉTECTION CAUSE SOLUTION 24011 Au cours du fonctionnement de la CNC. Le câble EtherCAT est débranché ou il y a des interférences dans le bus. Vérifier les connexions et l'état des esclaves. EtherCAT: Working Counter error. DÉTECTION CAUSE SOLUTION 24010 Au cours du fonctionnement de la CNC. Le câble EtherCAT est débranché ou un esclave ne fonctionne pas correctement. Vérifier les connexions et l'état des esclaves. EtherCAT: CRC incorrect. DÉTECTION CAUSE SOLUTION 24004 Pendant la validation des paramètres machine ou le démarrage de la CNC. Le câble EtherCAT est débranché. Brancher le câble d'EtherCAT. Pendant la validation des paramètres machine ou le démarrage de la CNC. Le fichier de chargement (cartographie) des ressources EtherCAT a un format illisible pour la CNC. Le fichier peut être incomplet ou corrompu. Vérifier le fichier. CNC 8070 EtherCAT: Erreur au cours du processus de chargement des ressources. DÉTECTION CAUSE SOLUTION Pendant la validation des paramètres machine ou le démarrage de la CNC. Les possibles causes sont les suivantes: • Le format du fichier est incorrect. • La version de l'application Fagor EtherCAT Mapping est incompatible avec la version de la CNC. • La version ne supporte pas l'une des ressources cartographiées. Contacter Fagor Automation. (REF: 1901) ·227· S o l ut i o n s d ’ e r r e ur s . 24023 EtherCAT: Nœuds EtherCAT non Fagor. Option de logiciel non autorisée. DÉTECTION CAUSE SOLUTION 24255 EtherCAT: Erreur inconnue. DÉTECTION CAUSE SOLUTION 24499 (REF: 1901) ·228· Au cours du fonctionnement de la CNC. Erreur de cause inconnue dans le bus EtherCAT. Contacter Fagor Automation. EtherCAT: Erreur dans le nœud. Plus d'informations sur le diagnostic. DÉTECTION CAUSE SOLUTION CNC 8070 Au cours de démarrage de la CNC ou après une RAZ. L'initialisation d'EtherCAT a détecté un nœud non Fagor et l'option de logiciel n'est pas active pour connecter des nœuds de tiers. Supprimer les nœuds non Fagor du bus EtherCAT ou convenir l'option de logiciel pour des nœuds de tiers. Au cours du fonctionnement de la CNC. Erreur dans un nœud. Consulter le mode diagnostic pour obtenir plus d'informations. S o l ut i o n s d ’ e r r e ur s . MODULE RCS-S. E034 Erreur dans l’identification de la carte CPU. Contacter Fagor Automation. E038 Erreur de checksum du code. Le checksum du code du programme chargé n'est pas correct. Recharger le logiciel. Si le problème persiste, il se peut que les mémoires RAM, FLASH ou le code chargé soient défectueux. Contacter Fagor Automation. E039 Erreur dans la carte Sercos ®. Contacter Fagor Automation. E040 Panne du clock dans la carte du SerCon®. Contacter Fagor Automation. E041 Mémoire du SerCon détériorée. Contacter Fagor Automation. E044 Système des fichiers dans le flash détérioré. Contacter Fagor Automation. E045 Erreur de lecture de l'offset d'analogiques. Contacter Fagor Automation. E046 Erreur dans l’identification de la carte d'axes. Contacter Fagor Automation. E047 Identification inconnue de la carte d'axes. Contacter Fagor Automation. E048 Erreur dans le code de la FPGA. Le code de FPGA semble détérioré o bien il n'est pas présent. Recharger la version de logiciel de nouveau. Si le problème persiste, il se peut que les mémoires RAM, FLASH ou le code chargé soient défectueux. Contacter Fagor Automation. E083 On n'a pas pu charger la FPGA. Réinitialiser l'Unité de Comptage. Si le problème persiste, contacter Fagor Automation. E084 RAZ par Watchdog. Le système a redémarré car la surveillance par watchdog est sautée. Si le problème est répétitif et/ou persiste, contacter Fagor Automation. E085 Erreur dans l'alimentation des sorties analogiques. Contacter Fagor Automation. E133 Câble cassé, signal A du système de mesure E21A. E233 Câble cassé, signal A du système de mesure E21B. E333 Câble cassé, signal A du système de mesure E21C. E433 Câble cassé, signal A du système de mesure E21D. Pour le cas du système de mesure TTL différentiel. Le câble du signal A et/ou /A peut être cassé ou débranché. Vérifier les connexions. Vérifier le niveau des signaux fournis par le capteur. E134 Câble cassé, signal B du système de mesure E21A. E234 Câble cassé, signal B du système de mesure E21B. E334 Câble cassé, signal B du système de mesure E21C. E434 Câble cassé, signal B du système de mesure E21D. Pour le cas du système de mesure TTL différentiel. Le câble du signal B et/ou /B peut être cassé ou débranché. Vérifier les connexions. Vérifier le niveau des signaux fournis par le capteur. E135 E235 E335 CNC 8070 (REF: 1901) Câble cassé, signal I0 du système de mesure E21A. Câble cassé, signal I0 du système de mesure E21B. Câble cassé, signal I0 du système de mesure E21C. ·229· S o l ut i o n s d ’ e r r e ur s . E435 Câble cassé, signal I0 du système de mesure E21D. Pour le cas du système de mesure TTL différentiel. Le câble du signal I0 et/ou /I0 peut être cassé ou débranché. Vérifier les connexions. Vérifier le niveau des signaux fournis par le capteur. E136 Câble cassé, signal AL du système de mesure E21A. E236 Câble cassé, signal AL du système de mesure E21B. E336 Câble cassé, signal AL du système de mesure E21C. E436 Câble cassé, signal AL du système de mesure E21D. Pour le cas du système de mesure TTL différentiel. Le câble du signal AL et/ou /AL peut être cassé ou débranché. Vérifier les connexions. Vérifier le niveau des signaux fournis par le capteur. E137 Le signal d'alarme dans le système de mesure E21A a été reçu. E237 Le signal d'alarme dans le système de mesure E21B a été reçu. E337 Le signal d'alarme dans le système de mesure E21C a été reçu. E437 Le signal d'alarme dans le système de mesure E21D a été reçu. Le codeur a généré un signal d'alarme par un mauvais fonctionnement. Vérifier la documentation du codeur pour déterminer l'origine de l'alarme. Il peut aussi s'agir d'un faux positif dû à une mauvaise connexion. E138 Alarme d'amplitude dans le système de mesure E21A. E238 Alarme d'amplitude dans le système de mesure E21B. E338 Alarme d'amplitude dans le système de mesure E21C. E438 Alarme d'amplitude dans le système de mesure E21D. Atténuation excessive ou saturation des signaux A et/ou B. Le câblage, le capteur ou le système de mesure de l'Unité de Comptage Sercos peuvent avoir un problème. Si le problème persiste, contacter Fagor Automation. E140 Fréquence excessive de comptage dans le système de mesure E21A. E240 Fréquence excessive de comptage dans le système de mesure E21B. E340 Fréquence excessive de comptage dans le système de mesure E21C. E440 Fréquence excessive de comptage dans le système de mesure E21D. La vitesse du déplacement de l’axe dépasse la capacité d’échantillonnage du hardware de l'Unité de Comptage Sercos pour ce type de signal du codeur. Diminuer la vitesse maximum du déplacement de l'axe. E141 Distance incorrecte entre I0 dans le système de mesure E21A. E241 Distance incorrecte entre I0 dans le système de mesure E21B. E341 Distance incorrecte entre I0 dans le système de mesure E21C. E441 Distance incorrecte entre I0 dans le système de mesure E21D. Erreur indiquant non-répétitivité du signal d’I0 à chaque tour du codeur. Il est en train de se produire une perte d’impulsions et/ou la mesure indiquée par le capteur est erronée. Erreur RAZ. Vérifier que la connexion et le câblage sont corrects. Vérifier que le nombre d’impulsions permises comme marge d’erreur n’est pas rigoureusement bas. Vérifier que la valeur du paramètre REFPULSE de la CNC est correcte. Pour cela contacter Fagor Automation. Si l’erreur persiste, il est possible que le capteur soit défaillant. E142 Surcharge de courant ou court-circuit dans le système de mesure E21A. E242 Surcharge de courant ou court-circuit dans le système de mesure E21B. E342 Surcharge de courant ou court-circuit dans le système de mesure E21C. E442 Surcharge de courant ou court-circuit dans le système de mesure E21D. Il s’est produit un court-circuit ou le détecteur est suralimenté. Vérifier les câbles et connexions. E143 Erreur de communication dans le système de mesure E21A. CRC incorrect. E243 Erreur de communication dans le système de mesure E21B. CRC incorrect. E343 Erreur de communication dans le système de mesure E21C. CRC incorrect. E443 Erreur de communication dans le système de mesure E21D. CRC incorrect. Erreur dans la lecture de la cote absolue; CRC incorrect. Vérifier le câble et le branchement avec la règle ou avec le codeur. Vérifier le paramétrage correct du capteur. Si le problème persiste, contacter Fagor Automation. CNC 8070 (REF: 1901) E144 Erreur de communication dans le système de mesure E21A. On n'a pas reçu d'acknowledge. E244 Erreur de communication dans le système de mesure E21B. On n'a pas reçu d'acknowledge. E344 Erreur de communication dans le système de mesure E21C. On n'a pas reçu d'acknowledge. E444 Erreur de communication dans le système de mesure E21D. On n'a pas reçu d'acknowledge. Erreur dans la lecture de la cote absolue; on n'a pas reçu d'acknowledge. Vérifier le câble et le branchement avec le capteur. L’erreur est probablement due à un problème du capteur. Si le problème persiste, contacter Fagor Automation. E145 E245 E345 ·230· ABSIND: Erreur de synchronisation dans le système de mesure E21A. ABSIND: Erreur de synchronisation dans le système de mesure E21B. ABSIND: Erreur de synchronisation dans le système de mesure E21C. S o l ut i o n s d ’ e r r e ur s . E445 ABSIND: Erreur de synchronisation dans le système de mesure E21D. La synchronisation entre l'Unité de Comptage Sercos et le module ABSIND s'est perdue, ce qui a pu produire une mauvaise lecture de la cote. L’erreur est probablement due à un mauvais fonctionnement du module ABSIND ou à un problème de connexion entre le module ABSIND et l'Unité de Comptage Sercos, associée à cette mesure. Si le problème persiste, contacter Fagor Automation. E146 ABSIND: Erreur lecture d'information dans le système de mesure E21A. E246 ABSIND: Erreur lecture d'information dans le système de mesure E21B. E346 ABSIND: Erreur lecture d'information dans le système de mesure E21C. E446 ABSIND: Erreur lecture d'information dans le système de mesure E21D. L’information d’identification du module ABSIND n’a pas pu être lue au démarrage du système. L’erreur est probablement due à un mauvais fonctionnement du module ABSIND ou à un problème de connexion entre le module ABSIND et l'Unité de Comptage Sercos, associée à cette mesure. Si le problème persiste, contacter Fagor Automation. E183 INDUCTOSYN: INC signal too-low dans le système de mesure E21A. E283 INDUCTOSYN: INC signal too-low dans le système de mesure E21B. E383 INDUCTOSYN: INC signal too-low dans le système de mesure E21C. E483 INDUCTOSYN: INC signal too-low dans le système de mesure E21D. Niveau du signal incrémental du transducteur inductosyn/resolver trop bas. Vérifier les valeurs du gain et de la phase du module ABSIND avec le logiciel de réglage. Vérifier le câble et la connexion entre le module ABSIND et le transducteur inductosyn/resolver. Si l’erreur persiste et ne peut pas être éliminée avec les actions précédentes, essayer de remplacer le module ABSIND et/ou le câble associé à cette mesure. Si l'erreur persiste, contacter Fagor Automation. E184 INDUCTOSYN: INC signal too-high dans le système de mesure E21A. E284 INDUCTOSYN: INC signal too-high dans le système de mesure E21B. E384 INDUCTOSYN: INC signal too-high dans le système de mesure E21C. E484 INDUCTOSYN: INC signal too-high dans le système de mesure E21D. Niveau du signal incrémental du transducteur inductosyn/resolver trop haut. Vérifier les valeurs du gain et de la phase du module ABSIND avec le logiciel de réglage. Vérifier le câble et la connexion entre le module ABSIND et le transducteur inductosyn/resolver. Si l’erreur persiste et ne peut pas être éliminée avec les actions précédentes, essayer de remplacer le module ABSIND et/ou le câble associé à cette mesure. Si l'erreur persiste, contacter Fagor Automation. E185 INDUCTOSYN: GRAY signal absent dans le système de mesure E21A. E285 INDUCTOSYN: GRAY signal absent dans le système de mesure E21B. E385 INDUCTOSYN: GRAY signal absent dans le système de mesure E21C. E485 INDUCTOSYN: GRAY signal absent dans le système de mesure E21D. Le niveau du signal GRAY du transducteur inductosyn/resolver est omis. Vérifier les valeurs du gain et de la phase du module ABSIND avec le logiciel de réglage. Vérifier le câble et la connexion entre le module ABSIND et le transducteur inductosyn/resolver. Si l’erreur persiste et ne peut pas être éliminée avec les actions précédentes, essayer de remplacer le module ABSIND et/ou le câble associé à cette mesure. Si l'erreur persiste, contacter Fagor Automation. E186 INDUCTOSYN: Le transducteur n'est pas stable sur Power-ON dans le système de mesure E21A. E286 INDUCTOSYN: Le transducteur n'est pas stable sur Power-ON dans le système de mesure E21B. E386 INDUCTOSYN: Le transducteur n'est pas stable sur Power-ON dans le système de mesure E21C. E486 INDUCTOSYN: Le transducteur n'est pas stable sur Power-ON dans le système de mesure E21D. La position lue pendant l'initialisation du module ABSIND n'est pas stable. Vérifier que l'axe ne se déplace pas pendant le démarrage ou l'initialisation. Vérifier le câble et la connexion entre le module ABSIND et le transducteur inductosyn/resolver. Vérifier les connexions de terre sur l’armoire (bruit électrique sur les signaux). Si l’erreur persiste et ne peut pas être éliminée avec les actions précédentes, essayer de remplacer le module ABSIND et/ou le câble associé à cette mesure. Si l'erreur persiste, contacter Fagor Automation. E187 INDUCTOSYN: Checksum EEPROM incorrect dans le système de mesure E21A. E287 INDUCTOSYN: Checksum EEPROM incorrect dans le système de mesure E21B. E387 INDUCTOSYN: Checksum EEPROM incorrect dans le système de mesure E21C. E487 INDUCTOSYN: Checksum EEPROM incorrect dans le système de mesure E21D. Vérifier le réglage du gain et de la phase du module ABSIND avec le logiciel de réglage. Si l’erreur persiste et ne peut pas être éliminée avec les actions précédentes, essayer de remplacer le module ABSIND associé à cette mesure. Si l'erreur persiste, contacter Fagor Automation. E188 INDUCTOSYN: Erreur inconnue dans le système de mesure E21A. E288 INDUCTOSYN: Erreur inconnue dans le système de mesure E21B. E388 INDUCTOSYN: Erreur inconnue dans le système de mesure E21C. E488 INDUCTOSYN: Erreur inconnue dans le système de mesure E21D. Le module ABSIND a généré une erreur inconnue. L’erreur est probablement due à un mauvais fonctionnement de celuici. Si l’erreur est répétitive et persiste, essayer de remplacer le module ABSIND associé à cette mesure. Si l'erreur persiste, contacter Fagor Automation S. Coop. CNC 8070 (REF: 1901) E189 INDUCTOSYN: Inconsistance paramètre SSITYPE avec le type de capteur branché au système de mesure E21A. ·231· S o l ut i o n s d ’ e r r e ur s . E289 INDUCTOSYN: Inconsistance paramètre SSITYPE avec le type de capteur branché au système de mesure E21B. E389 INDUCTOSYN: Inconsistance paramètre SSITYPE avec le type de capteur branché au système de mesure E21C. E489 INDUCTOSYN: Inconsistance paramètre SSITYPE avec le type de capteur branché au système de mesure E21D. Vérifier l'état du dipswitch S50 du module ABSIND. La valeur sélectionnée doit être cohérente avec le paramètre machine SSITYPE de la CNC et avec le type de capteur (inductosyn/resolver) connecté au module ABSIND. E192 Paramètre REFPULSE incorrect dans le système de mesure E21A. E292 Paramètre REFPULSE incorrect dans le système de mesure E21B. E392 Paramètre REFPULSE incorrect dans le système de mesure E21C. E492 Paramètre REFPULSE incorrect dans le système de mesure E21D. La valeur du paramètre machine REFPULSE est incohérente avec le type de capteur connecté. Essayer de modifier la valeur. Si le problème persiste, contacter Fagor Automation. E193 Système de mesure numérique Fagor. Erreur dans la piste absolue E21A. E293 Système de mesure numérique Fagor. Erreur dans la piste absolue E21B. E393 Système de mesure numérique Fagor. Erreur dans la piste absolue E21C. E493 Système de mesure numérique Fagor. Erreur dans la piste absolue E21D. On ne peut pas calculer la position absolue. Perte de comptage. Le signal analogique < 0,20 Vpp. Vérifier que le codeur ou la règle travaillent à une vitesse appropriée. Vérifier les tolérances du montage. Nettoyer le verre ou le ruban d'acier de la règle. Si aucune des solutions précédentes ne parvient pas à résoudre l'erreur, remplacer le codeur ou la tête de la règle. E194 Système de mesure numérique Fagor. Erreur dans la CPU. Système de mesure E21A. E294 Système de mesure numérique Fagor. Erreur dans la CPU. Système de mesure E21B. E394 Système de mesure numérique Fagor. Erreur dans la CPU. Système de mesure E21C. E494 Système de mesure numérique Fagor. Erreur dans la CPU. Système de mesure E21D. Codeur ou tête de la règle endommagés. Remplacer le codeur ou la tête de la règle. E195 Système de mesure numérique Fagor. Erreur dans les potentiomètres de réglage. Système de mesure E21A. E295 Système de mesure numérique Fagor. Erreur dans les potentiomètres de réglage. Système de mesure E21B. E395 Système de mesure numérique Fagor. Erreur dans les potentiomètres de réglage. Système de mesure E21C. E495 Système de mesure numérique Fagor. Erreur dans les potentiomètres de réglage. Système de mesure E21D. Codeur ou tête de la règle endommagés. Remplacer le codeur ou la tête de la règle. E196 Système de mesure numérique Fagor. Erreur dans le capteur d'image (CCD). Système de mesure E21A. E296 Système de mesure numérique Fagor. Erreur dans le capteur d'image (CCD). Système de mesure E21B. E396 Système de mesure numérique Fagor. Erreur dans le capteur d'image (CCD). Système de mesure E21C. E496 Système de mesure numérique Fagor. Erreur dans le capteur d'image (CCD). Système de mesure E21D. Vérifier les tolérances du montage. Nettoyer le verre ou le ruban d'acier de la règle. Codeur de tête de la règle endommagés; le CCD (Charge-Coupled Device) ou le LED (Light-Emitting Diode). Remplacer le codeur ou la tête de la règle. E197 Système de mesure numérique Fagor. Tension d'alimentation hors du rang. Système de mesure E21A. E297 Système de mesure numérique Fagor. Tension d'alimentation hors du rang. Système de mesure E21B. E397 Système de mesure numérique Fagor. Tension d'alimentation hors du rang. Système de mesure E21C. E497 Système de mesure numérique Fagor. Tension d'alimentation hors du rang. Système de mesure E21D. La tension d’alimentation doit être entre 5,3 V et 4,1 V. Vérifier que le câble d’alimentation du codeur ou de la règle n’est pas détérioré. Vérifier aussi que la longueur du câble est adéquate et que la connexion du câblage est satisfaisante. CNC 8070 (REF: 1901) E198 Système de mesure numérique Fagor. Erreur de paramètres. E298 Système de mesure numérique Fagor. Erreur de paramètres. E398 Système de mesure numérique Fagor. Erreur de paramètres. E498 Système de mesure numérique Fagor. Erreur de paramètres. Perte de la configuration du codeur ou de la tête de la règle. Remplacer le codeur ou la tête de la règle. E403 Panne dans MST. Problèmes de communication à travers de l'anneau à fibre optique. Vérifier les connexions dans l'anneau et l'identification de chaque module. E404 Panne dans MDT. Problèmes de communication à travers de l'anneau à fibre optique. Vérifier les connexions dans l'anneau et l'identification de chaque module. ·232· S o l ut i o n s d ’ e r r e ur s . E405 Phase non valide (>4). Problèmes de communication à travers de l'anneau à fibre optique. Vérifier les connexions dans l'anneau et l'identification de chaque module. E406 Montée erronée de phase. Problèmes de communication à travers de l'anneau à fibre optique. Vérifier les connexions dans l'anneau et l'identification de chaque module. E407 Abaissement erroné de phase. Problèmes de communication à travers de l'anneau à fibre optique. Vérifier les connexions dans l'anneau et l'identification de chaque module. E410 Bruit RAZ Sercon. Des bruits rentrent par le flexible de connexion du bus interne et remettent le SerCon à zéro mais pas le VeCon2. E411 Erreur de réception de télégrammes. Problèmes de communication à travers de l'anneau à fibre optique. Vérifier les connexions dans l'anneau et l'identification de chaque module. E412 Message synchronisme retardé. Problèmes de communication à travers de l'anneau à fibre optique. Vérifier les connexions dans l'anneau et l'identification de chaque module. E413 Erreur de handshake dans l'Unité de Comptage Sercos. L’élément maître (la CNC) envoie un message de synchronisme à chaque cycle (4 ms, normalement) qui fait que les asservissements se synchronisent. Si à un moment donné ils ne peuvent pas se synchroniser ou s’ils perdent la synchronisation, cette erreur aura lieu. La CNC n’a pas certainement envoyé ce message ou elle l'a fait au mauvais moment. Vérifier le câble de transmission ou vérifier qu’il n’y a pas de bruit dans la transmission. CNC 8070 (REF: 1901) ·233· S o l ut i o n s d ’ e r r e ur s . TABLE D'OUTILS ET DE MAGASIN. 'On ne peut pas charger l’outil sur la position %1' DÉTECTION. CAUSE SOLUTION Pendant le chargement manuel d’un outil depuis une fenêtre de dialogue ou depuis la liste du magasin. Chargement de la table du magasin en cours. L’outil ne rentre pas dans cette position de magasin, est déjà dans le magasin ou n’est pas défini dans la table d’outils. Choisir une position de magasin avec assez d’espace. Vérifier que l’outil est défini dans la table. 'Il est impossible de décharger l'outil %1' DÉTECTION. CAUSE SOLUTION Pendant le déchargement manuel d’un outil depuis une fenêtre de dialogue ou la liste du magasin. Chargement de la table d’outils ou de magasin en cours. L'outil n'est pas dans le magasin. Sélectionner un outil qui soit dans le magasin. 'On ne peut pas exécuter la manœuvre. Vérifier que la broche est vide' DÉTECTION. CAUSE SOLUTION En exécutant un bloc de chargement ou de déchargement d’un outil de terre. La broche n’est pas vide ou un canal est à l’état d’erreur. Décharger l'outil de la broche. Vérifier que l’état de tous les canaux est "READY". 'Type de table sélectionnée incorrecte' DÉTECTION. CAUSE SOLUTION Au cours du chargement de la table d’outils ou de magasin. Le fichier avec les données ne correspond pas à la table à charger ou a été modifié extérieurement. Choisir le fichier correspondant à la table à charger. 'L’outil n’existe pas ou il est déjà chargé dans le magasin' DÉTECTION. CAUSE SOLUTION Pendant le chargement d’un outil dans le magasin, avec ou sans manœuvre. L’outil n’existe pas ou est déjà dans le magasin, sur la broche ou les bras échangeurs (s’ils existent). Définir l'outil. S’il est sur la broche ou sur les bras échangeurs, le charger dans le magasin. 'L'outil %1 ne peut pas être éliminé' DÉTECTION. CAUSE SOLUTION En supprimant un outil ou en chargeant la table d’outils. La CNC ne trouve pas l'outil. L’outil n’existe pas et par conséquent il ne peut pas être supprimé. Si cela se produit en chargeant la table, initialiser la table avec la touche logiciel et la recharger. 'L’outil %1 n’existe pas ou il n'est pas chargé dans le magasin' DÉTECTION. CAUSE SOLUTION CNC 8070 'Erreur en renommant l’outil' DÉTECTION. CAUSE (REF: 1901) ·234· En déchargeant un outil du magasin, en forçant la position d’un outil ou en chargeant la table de magasin. L’outil n’existe pas ou n’est pas dans le magasin. Définir l'outil et le charger dans le magasin. SOLUTION En essayant de changer le nom d’un outil. On ne peut pas créer l'outil dans la base de données (bd8070.mdb). La base de données peut être utilisée par une autre application ou ne pas avoir de permission d’écriture. La base de données doit avoir la permission d’écriture. Si la base de données des outils est utilisée par une autre application, attendre à ce qu’elle soit libérée. S o l ut i o n s d ’ e r r e ur s . 'On ne peut pas renommer un outil de broche, de magasin ou de bras' DÉTECTION. CAUSE SOLUTION En essayant de changer le nom d’un outil. La CNC a essayé de changer le nom d’un outil alors qu’un outil existe déjà sous ce nom sur la broche, dans le magasin ou sur le bras échangeurs (s’ils existent). Choisir un autre numéro ou décharger l’outil à la terre. 'On ne peut pas mettre un outil sur la broche s’il y en a un sur le bras 2' DÉTECTION. CAUSE SOLUTION En forçant un outil comme un outil de broche. Il y a un outil sur le bras échangeur 2. Enlever l’outil du bras échangeur 2. 'On ne peut pas mettre l’outil du bras échangeur sur la broche' DÉTECTION. CAUSE SOLUTION En forçant un outil comme un outil de broche. L’outil est sur le bras échangeur 1. Enlever l’outil du bras échangeur 1. 'La position n'existe pas' DÉTECTION. CAUSE SOLUTION Pendant le chargement ou le déchargement d’un outil du magasin, avec ou sans manœuvre. La position du magasin n'existe pas. Choisir une position existante du magasin. 'Path %1 non trouvé' DÉTECTION. CAUSE SOLUTION Lors du chargement, enregistrement ou impression de la table d’outils ou magasin. Le path sélectionné n'existe pas. Définir le chemin correctement ou créer le dossier de destination. 'Fichier %1 non trouvé' DÉTECTION. CAUSE SOLUTION Au cours du chargement de la table d’outils ou de magasin. Le fichier avec les données n'existe pas. Choisir des fichiers qui existent et indiquer correctement le path. 'Erreurs au cours de la sauvegarde des données dans %1' DÉTECTION. CAUSE SOLUTION Au cours de l'enregistrant de la table d’outils ou magasin. Le fichier avec les données n’a pas pu être créé, existe déjà, n’a pas de permission d’écriture, est utilisé actuellement par une autre application ou il n’y a pas assez d’espace dans le disque. Choisir un autre répertoire pour enregistrer les tables, leur donner la permission d’écriture, fermer l’application qui est en train de les utiliser ou libérer de l’espace dans le disque. 'Erreur en ouvrant le fichier %1' DÉTECTION. CAUSE SOLUTION Lors du chargement, enregistrement ou impression de la table d’outils ou magasin. Les possibles causes sont les suivantes: • Au cours du chargement d'une table. Le fichier avec les données n’existe pas, n’a pas de permission de lecture ou est utilisé actuellement par une autre application. • En enregistrant une table ou en imprimant une table à un fichier. Le fichier avec les données n’a pas pu être créé, existe déjà, n’a pas de permission d’écriture, est utilisé actuellement par une autre application ou il n’y a pas assez d’espace dans le disque. • En imprimant une table sur une imprimante, celle-ci n’existe pas ou est mal configurée. Les possibles solutions sont les suivantes: • Au cours du chargement d'une table. Choisir des fichiers qui existent, indiquer correctement leur chemin, leur donner la permission de lecture ou fermer l’application qui est en train de les utiliser. • En enregistrant une table ou en imprimant une table à un fichier. Choisir un autre répertoire pour enregistrer les tables, leur donner la permission d’écriture, fermer l’application qui est en train de les utiliser ou libérer de l’espace dans le disque. • Pour imprimer une table sur papier, choisir une imprimante existante et bien configurée. CNC 8070 (REF: 1901) ·235· S o l ut i o n s d ’ e r r e ur s . ÉDITEUR DE PROFILS 'Profil sans résoudre' CAUSE SOLUTION Le profil à sauvegarder n’est pas résolu complètement. Résoudre le profil à enregistrer. La CNC ne laisse sauvegarder que des profils résolus. 'Mémoire insuffisante' CAUSE SOLUTION Il n’y a pas de mémoire de système pour suivre avec l’éditeur de profils. Contacter Fagor. 'Erreur de géométrie' CAUSE SOLUTION Le profil sélectionné a une géométrie non valide. Le profil sélectionné a une donnée erronée dans la définition des trajectoires. Corriger le profil. Toutes les trajectoires qui définissent le profil doivent être correctement définies. 'Erreur dans les données de l’élément' CAUSE SOLUTION Les données saisies sur un élément sont incorrectes. Corriger les données de l'élément. 'Erreur dans les données du profil' CAUSE SOLUTION Données non valides dans l’édition d’un profil "cercle" ou "rectangle". Corriger les données de l'élément. 'L’arc ne passe pas par la coordonnée initiale' CAUSE SOLUTION Dans un élément arc les données du centre, du rayon et du point initial ne sont pas cohérentes. Corriger les données de l'élément. 'L’arc ne passe pas par la coordonnée finale' CAUSE SOLUTION Dans un élément arc les données du centre, du rayon et du point final ne sont pas cohérentes. Corriger les données de l'élément. 'Il n’existe pas un arc lequel exécute toutes les données' CAUSE SOLUTION L’éditeur ne peut pas trouver un élément arc cohérent avec toutes les données connues. Corriger les données de l'élément. 'L’élément n’est pas tangent au précédent' CAUSE SOLUTION La tangence d’un élément n’est pas cohérente avec l’élément précédent. Corriger les données de l'élément. 'Valeur non valable' CAUSE CNC 8070 SOLUTION La valeur saisie pour modifier une arête (arrondissement, chanfrein, entrée tangentielle ou sortie tangentielle) n’est pas valide. Corriger les données de l'élément. La valeur de l’arête doit être inférieure aux trajectoires entre lesquelles elle est définie. 'Erreur dans l'axe du plan' CAUSE (REF: 1901) ·236· SOLUTION Un axe du plan n'est pas valide. Les deux axes du plan sont le même ou un des axes du profil sélectionné n’est pas défini dans la CNC. Le plan doit être formé par deux axes différents. Les deux axes doivent être dans la CNC. S o l ut i o n s d ’ e r r e ur s . Notes d'utilisateur: CNC 8070 (REF: 1901) ·237· S o l ut i o n s d ’ e r r e ur s . Notes d'utilisateur: CNC 8070 (REF: 1901) ·238· S o l ut i o n s d ’ e r r e ur s . Notes d'utilisateur: CNC 8070 (REF: 1901) ·239· Fagor Automation S. Coop. Bº San Andrés, 19 - Apdo. 144 E-20500 Arrasate-Mondragón, Spain Tel: +34 943 719 200 +34 943 039 800 Fax: +34 943 791 712 E-mail: info@fagorautomation.es www.fagorautomation.com ">
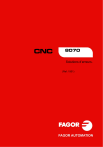
Lien public mis à jour
Le lien public vers votre chat a été mis à jour.