Manuel de Programmation. Fagor 800T CNC 800T
FAGOR 800T CNC
MANUEL DE PROGRAMMATION
Ref. 9701 (fr)
UTILISATION DES INFORMATIONS DE CE MANUEL
Ce manuel est utilisé lorsque l'on réalise un programme en ISO.
La CNC peut stocker deux programmes en codes ISO:
P99994 Programme spécial de sous programmes utilisateur en codes ISO.
P99996 Programme pièce utilisateur en codes ISO.
Ces deux programmes peuvent être élaborées sur un ordinateur et être envoyés ensuite dans la
CNC. L'aparté Péripheriques du Manuel d'Opération explique comment s'effectue cette transmission entre ordinateur et CNC.
Depuis la CNC il sera possible d'éditer ou modifier le programme P99996 mais on ne pourra pas accéder au programme P99994. Le programme P99994 doit être élaboré sur un ordinateur ou un périphérique.
Ce manuel donne toutes les informations sur les codes ISO utilisés par la CNC 800T.
Notes: L'information de ce manuel peut subir des variations suite à des modifications techniques.
FAGOR AUTOMATION, S.Coop. Ltda. se réserve le droit de modifier le contenu de ce manuel sans obligation de notification.
INDEX
Section Page
Table de comparaison des modèles CNC FAGOR 800T ................................................. ix
Chapitre 1 CONSTRUCTION D'UN PROGRAMME
Chapitre 2 PROGRAMMATION DES COTES
Chapitre 3 SYSTEMES DE REFERENCE
Section Page
Chapitre 4 FONCTIONS COMPLEMENTAIRES
Avance "F" en mm/min ou dixièmes de pouces/min (G94) ............................................. 2
Vitesse de Coupe Constant "S" en m/min ou pieds/min (G96) ....................................... 4
Chapitre 5 CONTROL DE TRAJECTOIRE
Interpolation circulaire avec programmation du centre de l'arc en cotes absolues ......... 6
Chapitre 6 FONCTIONS PREPARATOIRES ADDITIONNELLES
Traitement de bloc unique. Activation (G47), Annulation (G48) ................................... 9
Chapitre 7 COMPENSATION D'OUTIL
Section Page
Chapitre 8 CYCLES FIXES D'USINAGE
Chapitre 9 SOUS-PROGRAMMES (SOUSROUTINES)
Programme spécial de sous-programmes d'utilisateur P99994 ........................................ 1
Chapitre 10 PROGRAMMATION PARAMETRIQUE
TABLE COMPARATIVE
DES MODELES
FAGOR CNC 800T
MODELES CNC 800T DISPONIBLES
Modèle CNC 800T Compact avec écran 8" Jaune
Modèle CNC 800T Modulaire avec écran 9" Jaune
Composé de l'Unité Centrale, Moniteur et Clavier.
Modèle CNC 800T Modulaire avec écran 14" Couleur
Composé de l'Unité Centrale, Moniteur et Clavier.
DESCRIPTION TECHNIQUE
Contrôle des axes X, Z
Contrôle de Broche
Broche en tours par minute
(RPM)
Vitesse de Coupe Constante
de la broche (VCC)
Arrêt orienté de la broche
Outils
Compensation d'outil
Outil motorisé
Manivelles électroniques
Communication via RS 232C
Automate intégré (PLCI)
Edition d'un programme ISO
(Programme 99996)
Exécution d'un programme
ISO (Programme 99996)
Représentation Graphique
CNC
800-T
l l l l l l l
32 l l
2 l l l
32 l l
2 l l
CNC
800-TI
l l l
CNC
800-TG
l l
CNC
800-TGI
l l l l l l l l l l
32 l l
2 l l l l l l
32 l l
2 l l l
NOUVELLES PRESTATIONS
ET
MODIFICATIONS
Date: Avril 1993
PRESTATION
Avance rapide en fonction de la position du commutateur “Feed Rate”
Outil pour la passe de finition
Déplacement avec les manivelles elect.
limité à la F autorisée
Contrôle des limites de courses lors du déplacement avec manivelles electr
Format d’affichage de la S
Possibilité après interruption du programme d’activer/désactiver les sorties O1, O2, O3
Opération automatique “Arrondi de profil”
Profils
Version Software: 2.1 et suivantes
MANUEL ET SECTION MODIFIEES
Manuel d’Opération Section 2.3.1
Manuel d’Installation
Manuel d’Opération
Manuel d’Opération
Section 3.5
Section 3.5
Section 2.3.1
Manuel d’Installation
Manuel d’Opération
Manuel d’Opération
Section 6
Section 5.5.3
Chapitre 6
Date: Octobre 1993
PRESTATION
Accélération/ décélération broche
Limitation des T/mn en VCC
Arrêt orienté de la broche
Outil Motorisé
Opération automatique “Perçage simple”
Opération automatique “Perçage multiple”
Version Software: 3.1 et suivantes
MANUEL ET SECTION MODIFIEES
Manuel d’Opération
Manuel d’Opération
Chapitre 6
Section 4.3.1
Manuel d’Installation
Manuel d’Opération
Manuel d’Installation
Manuel d’Opération
Manuel d’Opération
Manuel d’Opération
Section 6.4.1
Section 4.8
Section 5.9
Section 2.3
Section 5.8
Section 5.9
Date: Decembre 1993
PRESTATION
Assignation d’un numéro de 5 chiffres aux programmes pièce
Sauvegarde des programmes pièce sur un périphérique
Opération “Clavette” automatique
Temporisation avant d’ouvrir la boucle
Code d’accès seul pour les Modes Spéciaux
Manivelle inactive si le commutateur est hors des positions manivelle
Version Software: 3.2 et suivantes
MANUEL ET SECTION MODIFIEES
Manuel d’Opération Chapitre 7
Manuel d’Opération Section 7.7
Manuel d’Opération
Manuel d’Installation
Manuel d’Installation
Manuel d’Installation
Section 5.10
Section 4.3.2
Section 3.7
Section 4.3.2
Date: Juillet 1994
PRESTATION
Accélération/décélération de la broche linéaire et en forme de cloche
Profil avec et sans arrondis
Opération de filetage admet la sortie de filet
Avance rapide à 200% en fonction de la position du commutateur “Feed Rate”
Inspection d’outil
Exécution du programme 99996
Version Software: 4.1 et suivantes
MANUEL ET SECTION MODIFIE
Manuel d’Installation Section 5.8
Manuel d’Opération
Manuel d’Opération
Manuel d’Installation
Manuel d’Opération
Manuel d’Installation
Manuel d’Opération
Manuel d’Opération
Manuel d’Installation
Manuel d’Opération
Section 6.2
Section 5.6.2
Section 4.3.3
Section 2.3.1
Section 3.4.3
Section 3.4.3
Section 5.1.3
Section 3.1.1
Section 3.1.0
Date: Janvier 1995
PRESTATION
Version Software: 5.1 et suivantes
MANUEL ET SECTION MODIFIEES
Confirmation de M3/M4 en détectant l’inversion par comptage.
Manuel d’Installation Section 6.3
Déplacements en manuel en mm/tour
Manivelle gérée depuis l’automate PLCI.
Inhibition do la broche depuis le PLCI
Manuel d’Installation
Manuel PLCI
Section 4.3.2
Manuel d’Installation
Manuel d’Opération
Section 3.10
Section 3.9 et 7.9
Effacer le contenu de tous les paramètres arithmétiques en leur donnant la valeur zéro.
Opération automatique d’arrondi, en cycle, avec un angle différent de 90°.
Opération automatique de rainurage (gorges) frontal et passe de finition.
Opération automatique d’arrondi de profil par suivi de profil ou ébauche.
Manuel d’Opération
Manuel d'Opération
Manuel d’Opération
Section, 5 5.2.
Section 5.7
Section 5.5.3
Point d’approche dans l’opération arrondi de profil (modification)
Exécution du profil, en cycle, par suivi de profil ou ébauche.
Point d’approche dans l’exécution du profil, en cycle (modification).
Opération automatique de taraudage
M20 amis à la fin d’une pièce
Manuel d’Opération
Manuel d’Opération
Manuel d’Opération
Manuel d’Opération
Manuel d’Installation
Section 5.5.3
Section 6.2
Section 6.2
Section 5.8
Section 3.8.3.1
Représentation graphique (Simulation)
Exécution / Simulation du programme 99996
(programme utilisateur en lSO)
Exécution automatique en bloc à bloc du programme 99996
Edition du programme 99996
Manuel d’Opération
Manuel d’Installation
Manuel d’Opération
Manuel d’Installation
Manuel d’Opération
Section 5.1.3
Section 3.1 1
Section 3 10
Section 3. 10
Section 3. 10
Manuel d’Installation
Manuel d’Opération
Manuel de Programmation
Section 3.12
Section 3.11
Manuel de Programmation Chapitre 9
Programme utilisateur 99994 en lSO pour stocker les sous programmes
Sous-programme associé à l’exécution d’un outil Manuel d’Installation
(seulement en exécution du programme 99996) Manuel de Programmation
Section 4.3.4
Codes ISO du CNC 800T Manuel de Programmation
Date:
Mars 1995
PRESTATION
Version Software: 5.2 et suivantes
MANUEL ET SECTION MODIFIEES
Edition du programme 99996 sur tous les modèles
Lorsque l’on arrêt l’exécution les touches de la broche, arrosage, 01, 02, 03 et TOOL sont habilitées.
Programmation lSO. Nouvelle fonction: G86
(cycle fixe de filetage longitudinal)
Demande depuis le PLCl du nombre de tours de la broche.
Manuel d’Installation
Manuel d’Opérations
Manuel d’Opérations
Manuel d’Opérations
Manuel PLCI
Section 3.11
Section 3.10
Section 5.1.4
Section 7.5
Les déplacements en JOG (manuel) incrémental Manuel d’installation tiennent compte du rayon/diamètre
Programmation ISO. Nouvelles fonctions:
G47, G48 (traitement bloc unique).
Section 4.3.3
Manuel de Programmation Section 6.7
Manuel de Programmation Section 8.17
Date:
Novembre 1995
PRESTATION
Modification de correcteur d’usure durant l'exécution
Déplacement avec une seule manivelle
électronique
Lecture de la S réelle depuis le PLCI
Version Softtware: 5.5 et suivantes
MANUEL ET SECTION MODIFIES
Manuel d’Opération
Manuel d’Installation
Manuel d’Installation
Manuel PLCI
Section 3 .4.4
Section 4.3.2
Section 7.5
INTRODUCTION
Introduction - 1
CONDITIONS DE SÉCURITÉ
Lisez les mesures de sécurité qui suivent, à l’objet d’éviter des lésions aux personnes et à prévenir des dommages à ce produit et aux produits qui y sont raccordés.
L’appareil en pourra être réparé que par le personnel autorisé par Fagor Automation.
Fagor Automation ne pourra en aucun cas être responsable de tout dommage physique ou matériel qui découlerait du non-respect de ces normes de bases de sécurité
Précautions vis à vis de dommages à des personnes
Avant d’allumer l’appareil, vérifiez que vous l’avez mis à la terre.
En vue d’éviter des décharges électriques, vérifiez que vous avez procédé à la prise de terre.
Ne pas travailler dans des ambiances humides.
Pour éviter des décharges électriques, travaillez toujours dans des ambiances à humidité relative inférieure à 90% sans condensation à 45º C.
Ne pas travailler dans des ambiances explosives
Afin d’éviter des risques, des lésions ou des dommages, ne pas travailler dans des ambiances explosives.
Précautions pour éviter l’endommagement du produit
Ambiance de travail
Cet appareil est préparé pour être utilisé dans des Ambiances Industrielles et respecte les directives et les normes en vigueur dans l’Union Européenne.
Fagor Automation ne se responsabilise pas des dommages qu’il pourrait provoquer s’il est monté sous d’autres conditions (ambiances résidentielles ou domestiques).
Installer l’appareil à l’endroit adéquat
Il est recommandé d’installer la Commande Numérique, autant que possible, éloignée de liquides de refroidissement, de produits chimiques, de coups, etc., qui pourraient l’endommager.
L’appareil respecte les directives européennes en ce qui concerne la compatibilité
électromagnétique. Il est néanmoins conseillé de le tenir éloigné des sources de perturbation électromagnétique, telles que :
- Les charges puissantes branchées au secteur sur lequel est raccordé l’équipement.
- Les émetteurs-récepteurs portatifs proches (radiotéléphones, émetteurs radioamateurs),
- Émetteurs-récepteurs de radio/télévision proches,
- Appareils de soudure à l’arc proches,
- Lignes de haute tensions proches,
- Etc.
Conditions de l’environnement
La température ambiante qui doit exister au régime de fonctionnement doit être comprise entre +5ºC et +45ºC.
La température ambiante qui doit exister au régime de non fonctionnement doit être comprise entre -25ºC et 70ºC.
Introduction - 3
Protections de l’appareil
Unité Centrale
Il incorpore 2 fusibles extérieurs rapides (F) de 3,15 Amp./ 250 V., pour la protection de l‘entrée de secteur.
Toutes les entrées-sorties digitales sont protégées par 1 fusible extérieurs rapides (F) de
3,15 Amp./ 250 V contre l’éventuelle surtension de la source extérieure (plus de 33 Vcc.) et contre le branchement inversé de la source d’alimentation.
Moniteur
Le type de fusible de protection dépend du type de moniteur. Voir l’étiquette d’identification du propre appareil.
Précautions à prendre durant les réparations
Ne pas manipuler l’intérieur de l’appareil
Seul le personnel autorisé par Fagor Automation peut manipuler l’intérieur de l’appareil.
Ne pas manipuler les connecteurs lorsque l’appareil est branché au secteur
Avant de manipuler les connecteurs (entrées/sorties, mesure, etc.), vérifiez que l’appareil est débranché du secteur.
Symboles de sécurité
Symboles pouvant apparaître sur le manuel
Symbole ATTENTION.
Il a un texte associé qui indique les actions ou les opérations pouvant provoquer des dommages aux personnes ou aux appareils.
Symboles que peut présenter le produit
Symbole ATTENTION.
Il a un texte associé qui indique les actions ou les opérations pouvant provoquer des dommages aux personnes ou aux appareils.
Symbole D’ÉLECTROCUTION.
Il indique que le point en question peut être sous tension électrique.
Symbole PROTECTION DE MASSES.
Il indique que le point en question doit être branché au point central de mise
à la terre de la machine afin de protéger les personnes et les appareils
Introduction - 4
CONDITIONS DE RENVOI
Si vous allez envoyer le CNC, emballez-les dans sa caisse en carton originale avec leur matériel d’emballage original. Si vous ne disposez pas du matériel d’emballage original, emballez-le de la façon suivante :
1.Obtenez une caisse en carton dont les 3 dimensions internes auront au moins 15 cm (6 pouces) de plus que celles de l’appareil, Le carton utilisé pour la caisse doit avoir une résistance de 170 Kg (375 livres).
2.Si vous avez l’intention de l’expédier à un bureau de Fagor Automation pour qu’il soit réparé, veuillez joindre une étiquette à l’appareil en indiquant le nom du propriétaire de l’appareil,, son adresse, le nom de la personne à contacter, le type d’appareil, le numéro de série, le symptôme et une description succincte de la panne.
3.Enveloppez l’appareil avec un film de polyéthylène ou d’un matériau semblable afin de le protéger.
Si vous allez expédier le moniteur, protégez tout particulièrement le verre de l’écran.
4.Capitonnez l’appareil dans la caisse en carton, en la remplissant de mousse de polyuréthane de tous côtés.
5.Scellez la caisse en carton avec du ruban d’emballage ou avec des agrafes industrielles.
Introduction - 5
DOCUMENTATION FAGOR
POUR LA CNC 800T
Manuel CNC 800T OEM
Il s’adresse au constructeur de la machine ou à la personne chargée de réaliser l’installation et la mise au point de la Commande Numérique.
Le manuel d’installation se trouve à l’intérieur.
Elle peut contenir occasionnellement un manuel ayant trait aux “Nouvelles
Prestations” de logiciel récemment introduites.
Manuel CNC 800T USER.
Il s’adresse à l’usager final, c’est-à-dire, à la personne qui va travailler avec la Commande Numérique.
Manuel DNC 25/30
Manuel Protocole DNC
Manuel PLCI
Elle contient 2 manuels à l’intérieur :
Le Manuel d’Utilisation qui décrit comment travailler avec la CNC.
Le Manuel de Programmation, qui décrit comment élaborer un programme en code ISO.
Elle peut contenir occasionnellement un manuel ayant trait aux “Nouvelles
Prestations” de logiciel récemment introduites.
Il s’adresse aux personnes qui vont utiliser l’option de logiciel de communication DNC.
Il s’adresse aux personne qui désirent réaliser leur propre communication de
DNC, sans utiliser l’option de logiciel de communication DNC 25/30.
Il doit être utilisé lorsque la CNC est munie d’Automate Intégré.
Manuel DNC-PLC
Manuel Floppy Disk
Il s’adresse au constructeur de la machine ou à la personne qui se charge de réaliser l’installation et la mise au point de l’Automate Intégré.
Il s’adresse aux personnes qui vont utiliser l’option de logiciel de communication DNC-PLC.
Il s’adresse aux personnes qui utilisent le lecteur à disquettes de Fagor. Ce manuel indique comment ledit lecteur à disquettes doit être utilisé.
Introduction - 6
CONTENU DU PRÉSENT MANUEL
Le Manuel de Programmation se compose des parties suivantes :
Index
Tableau comparatif des modèles Fagor CNC 800T.
Nouvelles Prestations et modifications.
Introduction
Chapitre 1
Résumé des conditions de sécurité.
Conditions de Renvoi.
Liste de Documents Fagor pour la CNC 800T.
Contenu du présent Manuel.
Construction d’un programme.
Il indique la structure que doit avoir le programme pièce et tous les blocs qui le forment.
Il montre toutes les fonctions préparatoires G qui sont disponibles.
Chapitre 2
Chapitre 3
Chapitre 4
Programmation de cotes (coordonnées)
Il montre la manière de sélectionner les unités de travail, le type de programmation (absolu / incrémental).
Il explique les systèmes de coordonnées pour la programmation de cotes
(cartésiennes, polaires, au moyen de deux angles, au moyen d’angle et de coordonnée cartésienne).
Systèmes de référence.
Il indique comment programmer la recherche de référence machine, la présélection de cotes, les transferts d’origine et la présélection de zéro polaire.
Il indique comment garder et comment récupérer l’origine des coordonnées.
Fonctions complémentaires.
Il montre la manière de programmer les fonctions préparatoires d’avance et de vitesse.
Il indique la manière de programmer la vitesse de rotation de la broche (tr/ min., coupe constante).
Il expose la façon de programmer l’arrêt orienté de la broche.
Il montre comment il faut programmer l’outil et comment modifier les valeurs de la table depuis le programme d’usager.
Il indique comment programmer les fonctions auxiliaires “M”.
Chapitre 5
Chapitre 6
Contrôle de trajectoire.
Il indique comment programmer le travail en arête vive et en arête arrondie.
Il montre comment programmer le positionnement rapide, l’interpolation linéaire et l’interpolation circulaire.
Il indique comment programmer les entrées et les sorties tangentielles et l’arrondissement et le chanfreinage des arêtes.
Il expose comment programmer le filetage électronique et le mouvement jusqu’à la butée.
Fonctions préparatoires supplémentaires.
Il montre comment programmer une temporisation.
Il indique comment afficher le code d’erreur.
Il expose comment travailler avec des sauts et des appels inconditionnels
Il montre comment programmer un filetage électronique.
Il indique comment appliquer un facteur d’échelle.
Il expose comment travailler avec un palpeur.
Il expose comment programmer le traitement de bloc unique.
Introduction - 7
Chapitre 7
Chapitre 8
Chapitre 9
Chapitre 10
Compensation d’outils.
Il montre comment programmer la compensation de rayon et de longueur d’outil.
Cycles fixes d’usinage.
Il affiche comment programmer les différents cycles fixes d’usinage.
Sous-routines.
Programme spécifique de sous-routines d’usager P99994
Il indique comment identifier une sous-routine standard ou paramétrique.
Il indique comment programmer un appel à une sous-routine standard ou paramétrique
Il affiche les niveaux d’emboîtement des sous-routines.
Programmation paramétrique
Il montre comment il faut faire la programmation paramétrique (assignations, opérateurs, fonctions de saut, etc.).
Exemple de programmation
Codes d’erreur.
Introduction - 8
1.
CONSTRUCTION D’UN PROGRAMME
Un programme de commande numérique est formé par un ensemble de blocs et instructions.
Ces blocs ou instructions sont constitués de mots formés des lettres majuscules et de nombres.
Le format numérique dont dispose la CNC :
- les signes
. + -
- les chiffres
0 1 2 3 4 5 6 7 8 9
La programmation admet de ne pas programmer le format numérique si celui-ci a valeur zéro, ou le signe s’il est positif.
Le format numérique d’un mot peut être remplacé par un paramètre arithmétique. Durant l’exécution, la commande remplacera le paramètre par sa valeur. Exemple:
Si l’on a programmé XP3, la CNC substituera durant l’exécution P3 par sa valeur numérique, obtenant des résultats tels que X20, X20.567, X-0.003, etc.
1.1 STRUCTURE D’UN PROGRAMME
Tous les blocs qui composent le programme auront la structure suivante :
Numéro de bloc + Bloc de programme
Chapitre: 1
CONSTRUCTION D'UN PROGRAMME
Section: Page
1
1.2 NUMERO DE BLOC
Le numéro de bloc sert pour identifier chaque bloc constituant un programme.
Il est représenté par la lettre N suivie de jusqu’à 4 chiffres (0-9999).
Les blocs de programme doivent être ordonnés numériquement. Il est recommandé de laisser un intervalle entre les numéros de blocs afin de pouvoir y insérer si nécessaire de nouveaux blocs.
Attention:
Tout au long de ce manuel le format “N4” désignera le numéro de bloc, indiquant qu’il doit se définir avec la lettre N suivie de 4 chiffres (il n’est pas admis de décimales).
1.2.1 BLOCS CONDITIONNELS
Il existe deux types de blocs conditionnels:
a) BLOC CONDITIONNEL NORMAL N4.
Si après le numéro de bloc N4 on met un point décimal (.), le bloc devient bloc conditionnel normal. La CNC l’exécutera uniquement si le signal extérieur correspondant est activé (entrée de blocs conditionnels).
Durant l’exécution de n’importe quel programme, la CNC lit 4 blocs avant celui en exécution.
Pour que le bloc soit exécuté, le signal extérieur doit être actif avant l’exécution des 4 blocs antérieurs au bloc conditionnel.
b) BLOC CONDITIONNEL SPECIAL N4..
Si à la suite du numéro de bloc N4 (0-9999) on met deux points décimaux (..), le bloc reste personnalisé comme bloc conditionnel spécial. C’est à dire, la CNC l’exécutera seulement si le signal extérieur correspondant (entrée de blocs conditionnels), est activée.
Dans ce cas il suffit d’activer le signal extérieur (entrée de blocs conditionnels), durant l’exécution du bloc antérieur au bloc conditionnel spécial.
Le bloc conditionnel spécial N4.., annule la compensation de rayon de l' outil G41 ou
G42
Page
2
Chapitre: 1
CONSTRUCTION D'UN PROGRAMME
Section:
NUMERO DE BLOC
1.3 BLOC DE PROGRAMME
Sera écrit avec des commandes en langage ISO, spécialement prévues pour contrôler le mouvement des axes, car elles donnent l’information des conditions de déplacement et la valeur de l’avance.
Chaque bloc de programmation peut disposer des fonctions suivantes:
G
Fonctions préparatoires
X, Z
Cotes des axes
F
Vitesse d’avance
S
T
M
Vitesse de rotation de la broche
Numéro de l’outil
Fonctions auxiliaires
Dans chaque bloc il faut maintenir cet ordre, même s’il n’est pas nécessaire que chaque bloc contienne toutes les informations.
Suivant les unités de travail sélectionnées (mm ou pouces) on doit utiliser le format suivant de programmation:
Format en millimètres:
Format en pouces:
N4 G2 X+/-4.3 Z+/-4.3 F4 S4 T2.2 M2
N4 G2 X+/-3.4 Z+/-3.4 F4 S4 T2.2 M2
Tout au long du présent manuel on utilisera les formats:
“N4” Pour se référer au numéro de bloc, indiquant qu’il doit être défini avec la lettre N suivie de jusqu’à 4 chiffres (N0 a N9999).
“G2” Pour se référer à une fonction préparatoire, indiquant qu’elle doit être définie avec la lettre G suivie de jusqu’à 2 chiffres (G00 a G99).
+/- 4.3
Signifie qu’après la lettre qu’il accompagne (X ou Z) on peut écrire un nombre positif ou négatif avec jusqu’à 4 chiffres devant le point décimal et jusqu’à 3 après.
+/- 3.4
Signifie qu’après la lettre qu’il accompagne (X ou Z) on peut écrire un nombre positif ou négatif avec jusqu’à 3 chiffres devant le point décimal et jusqu’à 4 après.
“F4” Pour se référer à l’avance des axes, indiquant qu’elle doit être définie avec la lettre F suivie de jusqu’à 4 chiffres (F0 a F9999) lorsque l’on travaille en mm/min ou pouces/min.
Si on travaille en mm/tour on utilisera le format F3.4 et en pouces/tour
F2.4
“S4”
T2.2
Pour se référer à la vitesse de broche, indiquant qu’elle doit être définie avec la lettre S suivie de jusqu’à 4 chiffres (S0 a S9999).
Pour se référer à l’outil de travail, indiquant qu’il doit être défini avec la lettre T et qu’il peut disposer jusqu’à 2 chiffres devant le point décimal et jusqu’à 2 chiffres après.
“M2” Pour se référer aux fonctions auxiliaires, indiquant qu’elles doit être définies avec la lettre M suivie de jusqu’à 2 chiffres (M0 a M99).
Chapitre: 1
CONSTRUCTION D'UN PROGRAMME
Section:
BLOC DE PROGRAMME
Page
3
1.4 FONCTIONS PREPARATOIRES (G)
Les fonctions préparatoires se programment par la lettre G suivie de deux chiffres (G2).
Elles se programment toujours au début du bloc et servent à déterminer la géométrie de la pièce et les conditions de travail de CNC
1.4.1 TABLE DES FONCTIONS "G" EMPLOYÉES DANS LA CNC
G31
G32
G33
G36
G37
G38
G39
G40
G41
G42
G47
G48
G49
G50
G06
G07
G08
G09
G20
G21
G22
G23
G24
G25
G26
G27
G28
G29
G30
Fonction M D
G00
G01
G02
G03
G04
G05
*
*
* Positionnement rapide
* * Interpolation lineaire
*
Description
Interpolation circulaire dans le sens horaire
Interpolation circulaire dans le sens anti-horaire
Temporisation
Arête arrondie
*
Interpolation circulaire avec coordonnées absolues
Arête vive
Arc tangent à la trajectoire antérieure
Arc defini par trois points
Appel à un sousroutine standard
Appel à un sousroutine paramétrique
Identification d'un sousroutine standard
Identification d'un sousroutine paramétrique
Fin de sousroutine
Saut/appel inconditionnel
Saut/appel si égal à 0
Saut/appel si non égal à 0
Saut/appel si plus petit que
Saut/appel si égal à ou plus grand que
Afficher code d'erreur
*
Garder origine de coordonnées
Récupérer l'origine de coordonnées gardé avant avec G31
Filetage
Arrondi contrôlé d'arêtes
Entrée tangentielle
Sortie tangentielle
Chanfrein
* * Annulation de la compensation de rayon d'outil
* Compensation de rayon d'outil à gauche
*
*
Compensation de rayon d'outil à droite
Activer le traitement de bloc unique
* * Annuler le traitement de bloc unique
* Programmation de % d'avance
Chargement des dimensions d'outil
9.2
9.4
9.1
9.3
9.
5.5
5.2
5.6
5.7
6.3
10.6
10.6
10.6
10.6
6.2
Section
5.3
5.4
5.5
5.5
6.1
5.1
3.5
3.5
6.4
5.10
5.8
5.9
5.11
7.4
7.1
7.1
6.7
6.7
4.1
4.3
Page
4
Chapitre: 1
CONSTRUCTION D'UN PROGRAMME
Section:
FONCTIONS
PREPARATOIRES (G)
Fonction M D
G51
G53/G59 *
G66
G67 N0
G67 N1
G67 N2
G67 N3
G67 N4
G67 N5
G67 N6
G67 N7
G67 N8
G68
G69
G70
G71
G72
G74
G75
G81
G82
G84
G85
G86
G90
G91
G92
G93
G94
G95
Description
Correction des dimensions des outils
Translations d'origine
Suivi de profil
Cycle fixe de cylindrage
Cycle fixe de dressage
Cycle fixe de cylindrage conique
Cycle fixe de filetage
Cycle fixe de arrondi
Cycle fixe de rainurage
Cycle fixe de perçage simple
Cycle fixe de perçage multiple
Cycle fixe de clavettes
Cycle fixe d'ébauche sur X
Cycle fixe d'ébauche sur Z
Programmation en pouces
Programmation en millimètres
*
*
* Facteur échelle
Référence machine
Travail avec palpeur
Cycle fixe de chariotage de segments droits
Cycle fixe de dressage de segments droits
Cycle fixe de chariotage de segments courbes
Cycle fixe de dressage de segments courbes
Cycle fixe de filetage longitudinal
* * Programmation en coordonnées absolues
* Programmation en coordonnées incrémentales
Présélection de cotes
Limitation de la vitesse maximale de la broche "S"
Présélection de l'origine polaire
* Vitesse d'avance "F" de l'axe en mm/min. (0.1 pouce/tour)
* * Vitesse d'avance "F" de l'axe en mm/tour. (0.1 pouce/tour)
G96
G97
* Vitesse "S" en m/min. (pieds/min.) (Vitesse de Coupe Constant)
* * Vitesse "S" en tours/min.
4.2
4.2
La “M” signifie MODAL, c’est à dire, qu’une fois programmée, la fonction G est active tant que l’on ne programme pas une autre G incompatible ou que l’on exécute M02, M30,
ARRÊT D’URGENCE, RESET ou que l’on éteigne et mette en marche la CNC.
Section
4.3
3.4
8.10
8.1
8.2
8.8
8.9
8.11
8.12
2.1
2.1
8.3
8.4
8.5
8.6
8.7
6.5
3.1
6.6
8.13
8.14
8.15
8.16
8.17
2.2
2.2
3.2
4.2
3.3
4.1
4.1
La lettre “D” signifie PAR DEFAUT, c’est à dire qu’elles seront assumées par la CNC au moment de la mise en marche, après l’exécution de M02, M30, après un ARRÊT
D’URGENCE ou RESET.
Dans un même bloc on peut programmer toutes les fonctions G que l’on désire, et dans un ordre quelconque sauf G20, G21, G22, G23, G24, G25, G26, G27, G28, G29, G30, G31,
G32, G50, G51, G53/G59, G72, G74 et G92 qui doivent être seules dans un bloc, car spéciales. Si dans un même bloc on programme des fonctions G incompatibles, la CNC assume la dernière programmée.
Chapitre: 1
CONSTRUCTION D'UN PROGRAMME
Section:
FONCTIONS
PREPARATOIRES (G)
Page
5
2.
PROGRAMMATION DES COTES
2.1 UNITES DE MESURE. MILLIMETRES (G71) OU POUCES (G70)
La CNC dispose du paramètre machine “P13” pour définir les unités de mesure de la CNC.
Par conséquent ces unités de mesure peuvent être altérées tout au long du programme, disposant pour cela des fonctions:
G70 Programmation en pouces
G71 Programmation en millimètres
Selon que l’on a programmé G70 ou G71, la CNC assume ce système d’unités pour tous les blocs programmés à la suite.
Les fonctions G70/G71 sont modales et incompatibles entre elles.
Au moment de la mise en marche, après M02, M30, RESET ou ARRET D’URGENCE, la CNC assume le système d’unités défini par le paramètre machine P13.
Chapitre: 2
PROGRAMMATION DE COTES
Section:
MILLIMETRES (G71)
POUCES (G70)
Page
1
2.2 PROGRAMMATION ABSOLUE (G90) OU INCREMENTALE (G91)
La programmation des coordonnées d’un point, peut être réalisée, soit en coordonnées absolues G90 ou bien en coordonnées incrémentales G91.
Lorsque l’on travaille en G90, les coordonnées du point programmé sont référées au point d’origine des coordonnées.
Lorsque l’on travaille en G91, les coordonnées du point programmé sont référées au point antérieur de la trajectoire, c’est à dire, les valeurs programmées indiquent le déplacement à réaliser sur l’axe correspondant.
Après la mise en marche, après avoir exécuté M02, M30, ARRET D’URGENCE ou
RESET, la CNC assume la fonction G90.
Les fonctions G90 et G91 sont incompatibles entre elles.
Exemples en supposant que la programmation de l’axe X est au diamètre.
Point initial (P0)
X20 Z50.
Programmation absolue G90
N100 G90 G01 X40 Z30
N110 X60 Z20
Programmation incrémentale G91
P0 —> P1
P1 —> P2
N100 G91 G01 X20 Z-20
N110 X20 Z-10
P0 —> P1
P1 —> P2
Point initial (P0)
X40 Z40
Programmation absolue G90
N100 G90 G02 X100 Z10 I40 K10
Ou bien
N100 G90 G02 X100 Z10 R41.231
Programmation incrémentale G91
N100 G91 G02 X60 Z-30 I40 K10
Ou bien
N100 G91 G02 X60 Z-30 R41.231
Page
2
Chapitre: 2
PROGRAMMATION DE COTES
Section:
ABSOLUE (G90)
INCREMENTALE (G91)
2.3 PROGRAMMATION DE COTES
La CNC permet de programmer les coordonnées des axes dans les formats suivants:
- Coordonnées cartésiennes
- Coordonnées polaires
- Programmation par deux angles
- Programmation par un angle et une coordonnée cartésienne
2.3.1 COORDONNEES CARTESIENNES
Le format des cotes des axes est:
En mm: X±4.3 Z±4.3
En pouces: X±3.4 Z±3.4
Les valeurs des cotes programmées seront absolues ou incrémentales, selon que l’on a programmé G90/G91.
Dans le cas de cotes positives, il n’est pas nécessaire d’écrire le signe +. Les zéros de début et fin de cote peuvent être omis.
Exemple: Programmation de l’axe X au diamètre le point initial (X60 Z70).
Cotes absolues:
N100 G90 X70 Z30
N110 X100 Z10
Cotes incrémentales:
N100 G91 X10 Z-40
N110 X30 Z-20
Chapitre: 2
PROGRAMMATION DE COTES
Section:
COORDONNEES
CARTESIENNES
Page
3
2.3.2 COORDONNEES POLAIRES
Le format pour définir un point est:
En mm: R±4.3 A±3.3
En pouces: R±3.4 A±3.3
R étant la valeur du rayon et A celle de l’angle par rapport à l’origine polaire. (L’angle toujours en degrés). Au moment de la mise en marche, après M02, M30, ARRET
D’URGENCE ou RESET, la CNC assume comme origine polaire le point X0 Z0.
L’origine polaire peut être changée par la fonction G93.
Les valeurs de R et A seront absolues ou incrémentales selon que l'on travaille en G90 ou
G91.
En cas de valeurs positives, il n’est pas nécessaire d’écrire le signe. Les zéros de début et de fin peuvent être omis.
Lorsque l’on programme des mouvements en rapide (G00) ou en interpolation linéaire
(G01), il est nécessaire de programmer R et A.
Lorsqu’il s’agit d’interpolations circulaires (G02 ou G03), on programme l’angle A±3.3
du point final de l’arc et les cotes du centre de l’arc référées au point initial.
En cas d’interpolation circulaire (G02 ou G03) travaillant en coordonnées polaires, le centre de la circonférence se définit par I,K, comme dans le cas de coordonnées cartésiennes.
Lorsque l’on programme une interpolation circulaire avec G02,G03, la CNC assume le centre de l’arc comme nouvelle origine polaire.
Page
4
Chapitre: 2
PROGRAMMATION DE COTES
Section:
COORDONNES POLAIRES
Exemples de programmation en millimètres, en supposant que la programmation de l’axe
X est au diamètre
Exemple 1
En coordonnées absolues (G90)
N100 G93 I80 K50 ........................ (Présélection d’origine polaire)
N110 G01 G90 R30 A270 ............. P0
N120 R28.284 A225 ...................... P1
N130 R40 A180 ............................. P2
En coordonnées incrémentales (G91)
N100 G93 I80 K50 ........................ (Présélection de l’origine polaire)
N110 G01 G90 R30 A270 ............. P0
N120 G91 R-1.716 A-45 ............... P1
N130 R11.716 A-45 ...................... P2
Exemple 2, en supposant que le point initial est le P0 (X40 Z50)
En coordonnées absolues (G90)
N100 G90 G02 A198.435 I30 K-10
Ou bien N100 G93 I100 K40
N110 G90 G02 A198.435
En coordonnées incrémentales (G91)
N100 G91 G02 A-90 I30 K-10
Ou bien N100 G93 I100 K40
N110 G91 G02 A-90
Chapitre: 2
PROGRAMMATION DE COTES
Section:
COORDONNES POLAIRES
Page
5
2.3.3 PROGRAMMATION PAR DEUX ANGLES (A1, A2)
Un point intermédiaire d’une trajectoire, peut aussi être défini par:
A1 A2 (X, Z). Où:
A1 est l’angle de sortie, depuis le point de début de la trajectoire (P0).
A2 est l’angle de sortie du point intermédiaire (P1).
(X, Z) sont les coordonnées du point final P2.
La CNC calcule automatiquement les coordonnées de P1.
Exemple de programmation, P0 étant le point initial (X40 Z50) et l’axe X programmé au diamètre.
N100 A135 A153.435
N110 X100 Z10
Page
6
Chapitre: 2
PROGRAMMATION DE COTES
Section:
PAR DEUX ANGLES (A1, A2)
2.3.4 ANGLE ET UNE COORDONNEE CARTESIENNE
On peut également définir un point par l’angle de sortie de la trajectoire du point antérieur et une coordonnée cartésienne du point que l’on veut définir.
Exemple de programmation, P0 étant le point initial (X20 Z80) et l’axe X programmé au diamètre.
En cotes absolues
N100 G90
N110 A116.565 X60
N120 A180 Z60
N130 A135 X80
N140 A180 Z40
N150 A153.435 X100
N160 A135 Z10
En cotes incrémentales
N100 G91
N110 A116.565 X40
N120 A180 Z-10
N130 A135 X20
N140 A180 Z-10
N150 A153.435 X20
N160 A135 Z-10
Dans la définition des points par deux angles ou un angle et une coordonnée, il est possible d’intercaler des arrondis, chanfreins, entrées et sorties tangentielles.
Point initial P0 (X20 Z80)
N100 G01 G36 R10 A116 A180
N110 G39 R5 X60 Z40
N120 G36 R10 A90 X100
N130 A180 Z10
Chapitre: 2
PROGRAMMATION DE COTES
Section:
UN ANGLE ET UNE
COORDONNEE CARTESIENNE
Page
7
3.
SYSTEMES DE REFERENCE
3.1 RECHERCHE DE REFERENCE MACHINE (G74)
Lorsque l’on programme dans un bloc G74, la CNC déplace les axes jusqu’au point de référence machine.
Il peut exister deux cas:
a) Recherche sur les deux axes.
Si dans le bloc on programme G74 seul, la CNC déplace en premier l’axe X et ensuite l’axe Z.
b) Recherche sur un seul axe ou sur les deux axes dans un ordre déterminé.
Si on désire effectuer la recherche du zéro machine sur un seul axe, se doit indiquer après la fonction G74 l’axe désiré.
Si on désire effectuer la recherche du zéro machine dans un ordre différent à l’antérieur, on programme G74 et ensuite les axes dans l’ordre désiré.
Dans un bloc où l’on a programmé G74, on ne peut programmer aucune autre fonction.
Lorsque l’axe qui s’est déplacé atteint le point de référence machine, à l’écran apparaît la distance de ce point au dernier zéro pièce programmé, moins la longueur de l’outil sur cet axe (X ou Z).
Chapitre: 3
SYSTEMES DE REFERENCE
Section:
RECHERCHE DE REFERENCE
MACHINE (G74)
Page
1
3.2 PRESELECTION DE COTES (G92)
Par l’intermédiaire de la fonction G92 on peut présélectionner n’importe qu’elle valeur pour les axes de la CNC; ceci suppose pouvoir réaliser des translations d’origine de coordonnées.
Lorsque l’on programme la fonction G92, il ne s’effectue aucun mouvement des axes et la
CNC accepte les valeurs programmées à la suite de G92 comme nouvelles cotes de ces axes
Format de programmation: N4 G92 X Z .
Exemple: Programmation de l’axe X au diamètre, le point initial étant P0 (X20 Z80)
Sans utiliser la fonction G92.
N100 G01 G90 X40 Z50
N110 Z10
Si on utilise la fonction G92, la programmation sera:
N90 G92 X20 Z0
N100 G90 X40 Z-30
N110 Z-70
(Le point P0 devient le point X20 Z0)
Dans le bloc où l’on programme G92, on ne peut programmer aucune autre fonction.
La présélection de cote par G92 se réfère toujours à la position théorique à laquelle se trouvent les axes.
Page
2
Chapitre: 3
SYSTEMES DE REFERENCE
Section:
PRESELECTION DE COTES
(G92)
3.3 PRESELECTION D’ORIGINE POLAIRE (G93)
Par l’intermédiaire de la fonction G93, on peut présélectionner n’importe quel point comme origine de coordonnées polaires.
Il existe deux façons de présélectionner une origine de coordonnées polaires: a) En définissant les cotes de l’origine polaire.
Format N4 G93 I±4.3 K±4.3 en mm
N4 G93 I±3.4 K±3.4 en pouces
N Numéro de bloc
I
G93 Code de présélection d’origine polaire
Valeur de l’abscisse de l’origine des coordonnées polaires; c’est à dire, la
K valeur de X (Toujours, en valeur absolue).
Valeur de l'ordonnée de l’origine de coordonnées polaires, c’est à dire, la valeur de Z (Toujours, en valeur absolue).
Si l’on programme de cette manière la présélection d’origine polaire, la CNC n’admet pas d’autre information dans le même bloc.
b) En assumant le point actuel comme nouvelle origine polaire.
Si dans un bloc quelconque on programme en plus un G93, celui-ci impliquera qu’avant d’effectuer le mouvement que le bloc comporte, l’origine polaire sera le point où se trouve la machine à cet instant.
Attention:
Lorsque l’on programme une interpolation circulaire avec G02,G03, la CNC assume le centre de l’arc comme nouvelle origine polaire.
A la mise sous tension ou après M02, M30, ARRET D’URGENCE ou
RESET, la CNC assume comme origine polaire le point (X0,Z0).
Chapitre: 3
SYSTEMES DE REFERENCE
Section:
PRESELECTION D'ORIGINE
POLAIRE (G93)
Page
3
3.4 TRANSLATIONS D’ORIGINE (G53...G59)
Par les fonctions G53, G54, G55, G56, G57, G58 et G59, on peut travailler avec 7 translations d’origine différentes. Les valeurs de ces translations d’origine sont stockées dans la mémoire de la CNC et sont référées au zéro machine.
Pour accéder à la table de translations d’origine G53-G59 on doit taper la séquence de touches suivante
Une fois dans la table on peut effacer toutes les translations d’origine. Pour cela on doit taper la séquence de touches
Les fonctions G53-G59 doivent être utilisées pour charger un transfert d’origine dans la table ou pour appliquer un transfert d’origine de la table au programme en cours.
Charger un transfert d’origine dans la table.
Chargement valeurs absolues. Permet de charger à l’adresse de la table indiquée (G53-
G59) les valeurs définies par X, Z.
Format: N4 G53-G59 X±4.3 Z±4.3 en mm,
N4 G53-G59 X±3.4 Z±3.4 en pouces.
N Numéro de bloc
G Code de transfert d’origine (G53 a G59)
X Valeur du transfert d’origine référé au zéro machine de l’axe X
Z Valeur du transfert d’origine référé au zéro machine de l’axe Z
Chargement de valeurs incrémentales. Permet d’incrémenter les valeurs existantes de l’adresse indiquée de la table (G53/G59), avec les quantités définies par I, K.
Format: N4 G53-G59 I±4.3 K±4.3 en mm,
N4 G53-G59 I±3.4 K±3.4 en pouces.
N Numéro de bloc
G Code du transfert d’origine (G53 a G59)
I Quantité qui s’ajoute à la valeur de l’axe X stockée précédemment
K Quantité qui s’ajoute à la valeur de l’axe Z stockée précédemment
Appliquer un transfert d’origine, qui se trouve dans la table, au programme en cours.
Format: N4 G53-G59
Réalise un transfert des origines de coordonnées du programme en cours, en accord avec les valeurs stockées à l’adresse indiquée de la table (G53-G59).
Page
4
Chapitre: 3
SYSTEMES DE REFERENCE
Section:
TRANSLATIONS D'ORIGINE
(G53...G59)
Exemple:
En supposant que l’outil se trouve au point X200 Z530, que l’axe X se programme au rayon et que le point zéro-machine est X0 Z0, la programmation de la trajectoire théorique sera:
N10
N20
N30
G53 X0 Z340
G54 X0 Z170
G55 X0 Z0
N40 G90 G01 F250
N50 G53
N60 X140 Z170
N70 Z150
N80 X160 Z130
N90 G03 X160 Z90 I0 K-20
N100 G08 X160 Z50
N110 G01 X180 Z30
N120 Z0
N130 X140
N140 G54
N150 G25 N60.130.1
N160 G55
N170 G25 N60.120.1
N180 G00 X200 Z530
N190 M30
Charge le transfert d’origine dans la table
Charge le transfert d’origine dans la table
Charge le transfert d’origine dans la table
Applique le transfert d’origine G53
Applique le transfert d’origine G54
Applique le transfert d’origine G55
Chapitre: 3
SYSTEMES DE REFERENCE
Section:
TRANSLATIONS D'ORIGINE
(G53...G59)
Page
5
3.5 GARDER ET RECUPERER LES ORIGINES DE COORDONNEES
(G31, G32)
G31 : Garder les origines de coordonnées actuelles
G32 : Récupérer les origines de coordonnées gardées avec G31.
Par l’intermédiaire de la fonction G31, on peut à n’importe quel moment garder l’origine de coordonnées avec lesquelles on travaille et plus loin on peut récupérer cette origine par l’intermédiaire de la fonction G32.
Cette prestation est utile dans le cas où il est nécessaire d’utiliser plus d’une origine de coordonnées (origine pièce) dans le même programme. Elle permet de coter une partie du programme par rapport à une origine, de garder cette origine avec G31, de faire un transfert d’origine avec G92 ou G53-G59, de coter la suite du programme par rapport à une nouvelle origine, et finalement récupérer l’origine primitive par l’intermédiaire de G32. Les fonctions
G31 et G32 doivent être programmées seules dans un bloc, le format est:
N4 G31
N4 G32
Où:
N4 Numéro de bloc
G31 Garder l’origine des coordonnées actuelle
G32 Récupérer l’origine des coordonnées gardée par G31
Exemple:
Page
6
Programmation de l’axe X au diamètre. Point initial X120 Z120.
N110 X60 Z100
N120 G31
N130 G92 X0 Z0
N140 G01 X0 Z-10
N150 G02 X0 Z-20 R5
N160 G25 N130.150.3
N170 G32
N180 G00 X120 Z120
(Approche de la pièce)
(Garder l’origine des coordonnées)
(Transfert de l’origine)
(Usinage)
(Usinage)
(Usinage)
(Récupérer l’origine initiale)
(Retour au point de départ)
Chapitre: 3
SYSTEMES DE REFERENCE
Section:
GARDER ET RECUPERER LES
ORIGINES (G31, G32)
4.
FONCTIONS COMPLEMENTAIRES
4.1 PROGRAMMATION DE L’AVANCE (F)
La signification de F (vitesse d’avance programmable) diffère selon que l’on est en G94 ou
G95 et selon le système de mesure employé, en millimètres ou en pouces. Dans le tableau suivant on indique les différences.
Format Unités de programmation
G94
F4
G95
F3.4
F1
F1
(1mm/min) F1
Millimètres
Valeurs minimales Valeurs maximales
(1mm/min) F9999 (9999mm/min)
(1mm/tour) F0.0001
(0.0001mm/tour) F500 (500mm/tour)
G94
Format Unités de programmation
F4 F1 (0.1pouce/min) F1
Pouces
Valeurs minimales Valeurs maximales
(0.1pouce/min) F3937 (393.7 pouce/min)
G95
F2.4
F1 (1pouce/tour) F0.0001
(0.0001pouce/tr.)
F19.68
(19.685 pouce/tr.)
L’avance maximale réelle de la machine peut être limitée à une valeur minimale inférieure
(voir livre d’instructions de la machine).
L’avance de travail maximale de la machine peut être programmée directement, en utilisant le code F0.
Exemple: Sur une machine, dont l’avance de travail maximale (programmable) est
10.000 mm/min., on peut programmer F10000 ou F0.
L’avance F programmée est effective, lorsque l’on travaille en interpolation linéaire G01 ou circulaire G02/G03.
En supposant que l’on ne programme pas la fonction F, la CNC assumera l’avance F0.
Si on travaille en positionnement G00, la machine se déplacera en rapide, indépendamment de la F programmée.
La vitesse rapide est fixée pour chacun des axes à la mise au point de la machine, la valeur maximale possible étant de 65,535 mts/min. (voir livre d’instructions de la machine).
L’avance programmée peut varier entre 0% et 120% ou bien, entre 0% et 100% selon le paramètre P600(3), par le commutateur qui se trouve sur le panneau de commande de la
CNC, si cette dernière n’est pas en train d’exécuter un filetage à l’aide des fonctions G33,
G86, G87 ou bien un palpage (G57).
Chapitre: 4
FONCTIONS COMPLEMENTAIRES
Section:
PROGRAMMATION DE
L'AVANCE (F)
Page
1
4.1.1 AVANCE F EN mm/min ou dixièmes de pouces/min (G94)
Dès que l’on programme le code G94 la commande entend que les avances programmées par F4 sont en mm/min, ou en dixièmes de pouces/min.
La fonction G94 est modale, c’est à dire, une fois programmée elle se maintient active jusqu’à que l’on programme G95.
4.1.2 AVANCE F EN mm/tour ou pouces/tour (G95)
Dés la programmation du code G95 la CNC entend que les avances programmées par F3.4
sont en mm/tour ou en pouces/tour.
La valeur maximale programmable est F500 qui équivaut à 500 mm/tour. En pouces le format est F2.4 et la valeur maximale programmable est 19.685 qui équivaut à 19,685 pouces/tour.
La fonction G95 est modale, c’est à dire, une fois programmée se maintient active jusqu’à que l’on programme G94.
4.1.3 FEED-RATE PROGRAMMABLE (G49)
Avec la fonction G49, il est possible d’indiquer par programme le % de la vitesse d’avance
F programmée avec lequel on désire travailler.
La fonction G49 étant activée, le commutateur de M.F.O. est sans effet. Le format de programmation est: G49 K (1/120)
A la suite de G49 K on programme le % de l'avance F désiré, on peut programmer une valeur entière entre 1 et 120.
La fonction G49 est modale, c’est à dire, une fois programmée un %, celui-ci se maintient jusqu’à que l’on en programme un autre, ou bien, jusqu’à ce que l’on annule la fonction.
Pour annuler la fonction G49 K ( ), on doit programmer: G49 K, ou bien G49 seul.
La fonction G49 est également annulée, lorsque l’on exécute M02, M30, RESET ou
ARRET D’URGENCE.
La fonction G49 K, doit se programmer seule dans le bloc.
Page
2
Chapitre: 4
FONCTIONS COMPLEMENTAIRES
Section:
PROGRAMMATION DE
L'AVANCE (F)
4.2 VITESSE DE ROTATION DE LA BROCHE ET ARRET ORIENTE (S)
Le code S a deux significations:
a) Vitesse de rotation de la broche
La vitesse de rotation de la broche se programme directement en tours/min. ou m/min.
(pieds/min.), par le code S4. La programmation en m/min. (pieds/min.), s’utilise lorsque l’on travaille en vitesse de coupe constante.
On peut programmer une valeur comprise entre S0 et S9999 qui correspondra a 0 tour/ min. et 9999 tours/min. Cette valeur maximale est limitée par le maximum permis dans chaque cas concret de machine et il est défini par paramètre-machine.
Pour chaque cas concret il est nécessaire de consulter le livre d’instructions de la machine.
La vitesse de broche programmée peut être modifiée entre 50% et 120%, par les commandes que se trouvent sur la face avant de la CNC, si cette dernière n’est pas en train d’exécuter un filetage à l’aide des fonctions G33, G86, G87 ou bien un palpage
(G57).
Si on travaille en G96, vitesse de coupe constante, les valeurs possibles de S sont:
S0-S3047 (0 m/min., 3047 m/min.).
S0-S9999 (0 pieds/min., 9999 pies/min.).
b) Arrêt orienté de la broche
Si à la suite de la fonction M19 on programme S4.3, le code S4.3 indique la position d’arrêt de la broche en degrés, à partir de l’impulsion zéro machine venant du codeur.
La CNC enverra une sortie S analogique définie par les paramètres machine P606(2) et P702 jusqu’à ce que la broche se positionne au point défini par S4.3
4.2.1 VITESSE S EN tour./min (G97)
A partir du moment où l’on programme le code G97, la CNC entend que les vitesses de broche programmées par S4 sont en tour/min.
Si dans le bloc où l’on programme G97 on ne programme pas la vitesse de broche S4, la
CNC assume comme vitesse programmée, la vitesse à laquelle tourne la broche à cet instant.
La fonction G97 est modale; c’est à dire, une fois programmée, se maintient active jusqu’à ce que l’on programme G96.
La CNC, à la mise en marche assume la fonction G97.
Chapitre: 4
FONCTIONS COMPLEMENTAIRES
Section:
VITESSE DE LA BROCHE /
ARRET ORIENTE (S)
Page
3
4.2.2 VITESSE DE COUPE CONSTANTE. S EN mts/min ou pieds/min (G96)
A partir du moment où l’on programme le code G96, la CNC entend que les vitesses de broche programmées par S4 sont en mts./min. (pies/min.) et le tour commence à travailler en mode “vitesse de coupe constante”.
La CNC assume comme gamme de travail la gamme de la broche qui est sélectionnée. Si aucune gamme n’est sélectionnée on doit programmer la gamme de broche désirée dans le même bloc (M41, M42, M43, M44).
S’il n’y a pas de gamme sélectionnée et qu’aucune n’est programmée dans le bloc qui contient la fonction G96 la CNC affichera l’erreur 10. La CNC n’affichera pas cette erreur lorsque la machine dispose d’une seule gamme de broche, dans ce cas elle exécute la fonction M41 pour la sélectionner.
Il est recommandé de programmer dans un même bloc G96 et la vitesse de la broche (S4).
Si on programme seule la fonction G96, la CNC assume comme vitesse de broche dans le mode “vitesse de coupe constante”, la dernière avec laquelle on a travaillé la dernière fois dans ce mode. S’il n’y a aucune antériorité la CNC affichera l’erreur 10.
Si le premier mouvement à la suite de G96, se réalise en rapide (G00), la CNC, pour calculer les tours de la broche, assume comme diamètre de la pièce celui de la fin du dit mouvement.
Si le premier mouvement à la suite de G96 se réalise en G01, G02 ou G03, la CNC assume comme diamètre, la valeur au moment d’exécuter G96.
La fonction G96 est modale, c’est à dire, une fois programmée, se maintient active jusqu’à ce que l’on programme G97.
4.2.3 LIMITATION DE S EN VITESSE DE COUPE CONSTANTE (G92)
Par l’intermédiaire de la fonction G92 on peut limiter la vitesse maximale de la broche lorsque l’on travaille en G96 (vitesse de coupe constante).
Avec le bloc N4 G92 S4 on limite la vitesse de broche à la valeur fixée par S4 (en tour/min)
La CNC calcule à tout moment la vitesse de rotation, en t/mn, à laquelle doit tourner la broche pour obtenir la vitesse de coupe constante programmée, m/min ou pieds/min.
Si la vitesse de rotation calculée est supérieure à celle maximale fixée par la fonction G92
S4, la CNC la limite, faisant tourner la broche à la vitesse maximale fixée.
Page
4
Chapitre: 4
FONCTIONS COMPLEMENTAIRES
Section:
VITESSE DE LA BROCHE /
ARRET ORIENTE (S)
4.3 PROGRAMMATION DE L'OUTIL (T)
L’outil à utiliser se programme avec le code T2.2
Les deux chiffres à gauche du point décimal indiquent le numéro d’outil que l’on désire sélectionner.
Les deux chiffres à droite du point décimal indiquent le numéro de correcteur d’outil que l’on désire utiliser.
On peut disposer de jusqu’à 32 outils T1 à T32 et 32 correcteurs Txx.1 a Txx.32.
La fonction T peut se programmer dans les formes suivantes:
T2.2
La CNC sélectionne l’outil indiqué et tient compte des valeurs indiquées par le correcteur sélectionné.
T2 La CNC sélectionne l’outil indiqué et prend les valeurs indiquées par le correcteur de même numéro. On peut programmer T3 ou T3.3
T.2
La CNC ne change pas d’outil et tient compte des valeurs indiquées par le nouveau correcteur sélectionné.
La CNC applique toujours les valeurs de longueur (X,Z,I,K) stockées dans la table de correcteurs.
Lorsque l’on programme G41 ou G42, la CNC applique comme valeur de compensation de rayon, la valeur R stockée dans la table de correcteurs.
Si aucun T n’est programmé, la CNC applique le code T00 qui correspond à un outil de dimensions nulles.
Dans chaque adresse de la table de correcteurs d’outils (01-32), se stockent les valeurs suivantes.
X Longueur de l’outil selon l’axe X ............. ±8388.607mm (±330.2599")
Z Longueur de l’outil selon l’axe Z .............. ±8388.607mm (±330.2599")
F Code de forme de l’outil .......................................... F0-F9 (Voir figure)
R Rayon de l’outil ................................................. 1000.00mm (39.3700")
I Correction de longueur (usure), selon l’axe X.
Cette valeur s’introduit toujours au diamètre ........... ±32.766 (±1.2900")
K Correction de longueur d’outil
(usure) selon l’axe Z ............................................... ±32.766 (±1.2900")
Attention:
Si le fabriquant de la machine a associé un sous programme à la fonction T, il ne faut rien programmer après la fonction T, sinon la CNC affichera l'erreur correspondante.
Si le changement d'outil ne comporte aucun sous programme associé la CNC envoie le code du nouvel outil, affiche le message "TOOL CHANGE" et arrête l'exécution du programme.
Chapitre: 4
FONCTIONS COMPLEMENTAIRES
Section:
PROGRAMMATION
DE L'OUTIL (T)
Page
5
CODES DE FORME
Code "0" et "9"
Code "1"
Code "2"
Code "3"
Code "7"
Code "6"
Code "5"
P: pointe de l’outil
C: Centre de l’outil
Page
6
Chapitre: 4
FONCTIONS COMPLEMENTAIRES
Section:
PROGRAMMATION
DE L'OUTIL (T)
Code "4"
Code "4"
Code "5"
Code "6"
Code "7"
Code "8"
Code "3"
Code "2"
Code "1"
Code "8"
P: Pointe de l’outil
C: Centre de l’outil
Chapitre: 4
FONCTIONS COMPLEMENTAIRES
Section:
PROGRAMMATION
DE L'OUTIL (T)
Page
7
4.3.1 CHARGER LES DIMENSIONS DE L’OUTIL DANS LA TABLE (G50)
Avec la fonction G50, on peut introduire ou modifier les dimensions des différents outils de la table de correcteurs.
Il existe différentes manières de programmer la fonction G50:
a) Chargement de toutes les dimensions d’un outil
Avec le bloc N4 G50 T2 X±4.3 Z±4.3 F1 R4.3 I±2.3 K±2.3
On charge à l’adresse de la table indiquée par T2, les valeurs définies par X, Z, F, R,
I, K.
N4 Numéro de bloc
G50 Code de chargement des dimensions
T
X
Adresse de la table d’outils (T01-T32)
Longueur de l’outil selon l’axe X
Z
F1
R
Longueur de l’outil selon l’axe Z
Code de forme de l’outil (F0-F9)
Rayon de l’outil
I
K
Correction pour l’usure de l’outil selon l’axe X (toujours au diamètre).
Correction pour l’usure de outil selon l’axe Z
Les valeurs de X, Z, F, R, I, K se substituent à celles existantes à la position T2.
b) Se l'on désire changer quelques valeurs de la table.
Si l'on ne désire changer que quelques valeurs, il suffit de programmer ces valeurs à la suite de G50 T2, le reste des valeurs de la table ne sont pas altérées.
Si l'on programme de cette manière, il faut tenir compte des particularités suivantes:
* Si on programme X ou Z, ou les deux, et on ne programme pas I, K, les longueurs
(X,Z) sont substituées dans la table par les nouvelles valeurs et les valeurs de correction pour usures correspondantes, I ou K ou les deux se mettent à zéro
* Si après G50 T2 on programme I±2.3 ou bien I±2.3 K±2.3, ces valeurs s’ajoutent ou se retranchent à celles précédemment stockées.
Attention:
Dans les blocs où est programmé G50, il n’est pas permis de programmer aucune autre information.
Page
8
Chapitre: 4
FONCTIONS COMPLEMENTAIRES
Section:
PROGRAMMATION
DE L'OUTIL (T)
4.3.2 CORRIGER LES DIMENSIONS DE L’OUTIL (G51)
Avec la fonction G51, on peut modifier les valeurs I,K de l’outil en utilisation, sans que se modifient les valeurs stockées dans la table d’outils.
Format: N4 G51 I±4.3 K±4.3 en mm
N4 G51 I±3.4 K±3.4 en pouces
I
N4 Numéro de bloc
G51 Code de modification
Valeur qui s’ajoute ou se retranche à la valeur de I qu’utilise la CNC à ce moment, pour compenser la longueur de l’outil en cours.
K Valeur qui s’ajoute ou se retranche à la valeur de K qu’utilise la CNC à ce moment, pour compenser la longueur de l’outil en cours.
Ces valeurs ne modifient pas la table des outils, c’est à dire, la fois suivante que l’on utilisera ce même outil, la CNC assumera les valeurs I,K de la table, sans tenir compte de la modification antérieurement introduite par G51.
Dans un bloc où l’on programme G51, il n’est pas permis de programmer aucune autre information.
Chapitre: 4
FONCTIONS COMPLEMENTAIRES
Section:
PROGRAMMATION
DE L'OUTIL (T)
Page
9
4.4 FONCTIONS AUXILIAIRES (M)
Les fonctions auxiliaires se programment avec le code M2.
On peut programmer 96 fonctions auxiliaires différentes (M00-M99). Les fonctions M41,
M42, M43, M44 sont implicites avec la S, si le paramètre P601 (1) est à 1. Si le paramètre est à 0, M41, M42, M43, M44 doivent être programmées. Les fonctions auxiliaires, sortent
à l’extérieur (armoire électrique) en code BCD.
La CNC dispose également de 15 sorties décodées pour fonctions auxiliaires. Ces sorties seront assignées aux fonctions désirées à la mise au point de la CNC en machine.
Les fonctions auxiliaires auxquelles on n'a assigné aucune sortie décodée, s’exécutent toujours au début du bloc où elles sont programmées.
Lorsque l’on assigne une sortie décodée à une fonction auxiliaire on décide également, si cette fonction doit s’exécuter au début ou à la fin du bloc où elle est programmée. En un bloc on peut programmer jusqu’à un maximum de 7 fonctions auxiliaires.
Lorsque dans un bloc on a programmé plus d’une fonction auxiliaire, la CNC les exécute dans l’ordre où elles ont été programmées.
Quelques fonctions auxiliaires ont une signification interne dans la CNC.
M00. ARRET DE PROGRAMME
Lorsque la CNC lit dans un bloc le code M00 elle interrompt le programme. Pour annuler
M00 il faut donner à nouveau l’ordre MARCHE.
Il est recommandé de personnaliser cette fonction dans la table des fonctions M décodées, de manière qu’elle s’exécute à la fin du bloc où elle est programmée (voir
Manuel d’Installation et Mise en Marche).
M01. ARRET CONDITIONNEL DU PROGRAMME
Identique à M00, sauf que la CNC en tient compte l’entrée Arrêt conditionnel est activée.
M02. FIN DE PROGRAMME
Ce code indique fin de programme et réalise une fonction de Reset général de la CNC
(Mise en conditions initiales). Egalement exécute la fonction M05.
Même chose que pour M00, il est recommandé de la personnaliser pour qu’elle s’exécute
à la fin du bloc où elle est programmée.
M30. FIN DE PROGRAMME AVEC RETOUR AU DEBUT
Identique à M02, sauf que la CNC retourne au premier bloc du programme. Egalement exécute la fonction M05.
M03. MISE EN MARCHE DE LA BROCHE A DROITE (sens horaire)
Il est recommandé de personnaliser cette fonction, de manière qu’elle s’exécute au début du bloc où elle est programmée.
Page
10
Chapitre: 4
FONCTIONS COMPLEMENTAIRES
Section:
FONCTIONS AUXILIAIRES (M)
M04. MISE EN MARCHE DE LA BROCHE A GAUCHE (sens anti-horaire)
Il est recommandé de personnaliser cette fonction, de manière qu’elle s’exécute au début du bloc où elle est programmée.
M05. ARRET DE BROCHE
Il est recommandé de personnaliser cette fonction, de manière qu’elle s’exécute à la fin du bloc où elle est programmée.
M10, M11. ASSOCIEES AU DISPOSITIF EXTERNE O1
M12, M13. ASSOCIEES AU DISPOSITIF EXTERNE O2
M14, M15. ASSOCIEES AU DISPOSITIF EXTERNE O3
Codes associés aux touches correspondant aux dispositifs externes “O1”, “O2” et “O3”.
Les codes M10, M12 et M14 indiquent l’activation et les codes M11, M13 et M15 la désactivation du dispositif externe correspondant.
M19 ARRET ORIENTE DE BROCHE
Lorsque l’on programme M19 S4.3 la broche tourne à une vitesse et un sens définis par les paramètres machine P606(2) et P706 jusqu’à la valeur de S4.3 en degrés. Les degrés seront référés au point référence du codeur de broche.
Lorsque la broche est dans la bande d’arrêt (P707), le signal de blocage de la broche est
émis (M15 décodée) et maintient la broche en boucle fermée, appliquant les paramètres
P708 (gain) et P709 (consigne minimale de la broche).
Si on programme dans un bloc M19 S4.3, il n’est pas admis plus d’informations dans ce bloc.
M20 FIN D’EXECUTION D’UNE PIECE
Ce code indique que l’on a terminé l’exécution d’une pièce. Par exemple, sur une machine qui dispose d’un embarreur le PLC peut contrôler, avec cette fonction, l’usinage de pièces en série.
M41, M42, M43, M44 SELECTION DES GAMMES DE VITESSE DE BROCHE
Si le paramètre-machine P601(1) a la valeur 1, ces codes sont générés automatiquement par la CNC en programmant les fonctions S. Si ce paramètre a la valeur 0, il est nécessaire de les programmer.
Même si le paramètre P601(1) a la valeur 1, si on travaille en vitesse de coupe constante
(G96) il est obligatoire de programmer M41, M42, M43, M44.
M45. VITESSE DE ROTATION DE L’OUTIL MOTORISE
Format de programmation: N4 M45 S±4
S±4 définit le sens et la vitesse en tours par minute de l’outil motorisé.
Le signe (±) définit le sens de rotation. Avec S+4 on tournera dans un sens et avec
S-4 on tournera en sens contraire.
On peut programmer une valeur comprise entre S0 et S±9999 qui correspond à 0 t/mn.
et 9999 t/mn. respectivement.
Chapitre: 4
FONCTIONS COMPLEMENTAIRES
Section:
FONCTIONS AUXILIAIRES (M)
Page
11
5.
CONTROLE DE TRAJECTOIRE
5.1 ARETE ARRONDIE (G05)
Lorsque l’on travaille en G05, la CNC commence l’exécution du bloc suivant du programme, en même temps que débute la décélération des axes programmés dans le bloc antérieur.
C’est à dire, les mouvements programmés dans le bloc suivant, s’exécutent avant que la machine ait atteint la position exacte programmée dans le bloc antérieur.
Exemple:
Programmation de X au diamètre.
Le point initial étant X40 Z50.
N100 G90 G01 G05 X80
N110 Z20
Comme on le voit dans l’exemple, les chants seront arrondis.
La différence entre le profil théorique et réel est fonction de la valeur de l’avance.
Plus l’avance sera grande, plus la différence entre le profil théorique et le réel sera grande.
La fonction G05 est modale et incompatible avec G07. La fonction G05 peut se programmer
G5.
5.2 ARETE VIVE (G07)
Lorsque l’on travaille en G07, la CNC n’exécute pas le bloc suivant de programme, jusqu’à ce que l’on ait atteint la position exacte programmée dans le bloc antérieur.
Exemple:
Programmation de X au diamètre.
Le point initial étant X40 Z50.
N100 G90 G01 G07 X80
N110 Z20
Le profil théorique et le réel coïncident.
La fonction G07 est modale et incompatible avec G05. La fonction G07 peut se programmer
G7.
Chapitre: 5
CONTROL DE TRAJECTOIRE
Section:
ARETE ARRONDIE (G05)
ARETE VIVE (G07)
Page
1
5.3 POSITIONNEMENT RAPIDE (G00)
Les déplacements programmés à la suite de G00, s’exécutent en avance rapide fixée, à la mise au point de la machine, par les paramètres machine.
Lorsque les deux axes se déplacent en même temps, la trajectoire résultante est une ligne droite entre le point initial et le point final. L’avance sera déterminée par l’axe le plus lent.
Si l’on programme G00 la dernière F programmée n’est pas annulée; c’est à dire, lorsque l’on programme G01, G02 ou G03, on récupère cette F.
Par le paramètre machine P4 on peut fixer si le commutateur % d’avance, lorsque l’on travaille en G00, varie de 0% à 100% ou reste fixe à 100%.
Le code G00 annule la compensation de rayon d’outil (G41, G42). C’est à dire, lorsque l’on travaille avec G41 ou G42 et on programme G00, la compensation de rayon est sans effet jusqu’à ce que l’on programme de nouveau G01, G02 ou G03.
Le code G00 est modal et incompatible avec G01, G02, G03 et G33.
La fonction G00 peut se programmer G ou G0.
Page
2
Chapitre: 5
CONTROL DE TRAJECTOIRE
Section:
POSITIONNEMENT RAPIDE
(G00)
5.4 INTERPOLATION LINEAIRE (G01)
Les déplacements programmés après G01 s’exécutent selon une ligne droite, à l’avance F programmée.
Lorsque les deux axes se déplacent en même temps, la trajectoire résultante est une ligne droite entre le point initial et le point final. La machine se déplace selon cette trajectoire à l’avance F programmée.
La CNC calcule les avances de chaque axe pour que l’avance de la trajectoire résultante soit la F programmée.
Exemple:
Programmation de l’axe X au diamètre.
Point initial X40 Z50
N100 G90 G01 X60 Z10 F300
Par le commutateur du panneau frontal de la CNC, l’avance F programmée peut varier entre
0% et 120%, ou bien entre 0% et 100% suivant la valeur du paramètre P600(3).
Lorsque l’on presse la touche d’avance rapide et que l’on exécute un mouvement en G01, le pourcentage de la vitesse d’avance sera de 200% de la vitesse d’avance programmée, si le paramètre machine P600(3) a la valeur zéro.
La fonction G01 est modale et incompatible avec G00, G02, G03 et G33.
La fonction G01 peut être programmée G1.
Lorsque l’on met en marche la CNC, après l’exécution de M02/M30, un ARRET
D’URGENCE ou après un RESET, la CNC assume le code G01.
Chapitre: 5
CONTROL DE TRAJECTOIRE
Section:
INTERPOLATION LINEAIRE
(G01)
Page
3
5.5 INTERPOLATION CIRCULAIRE (G02, G03)
G02: Interpolation circulaire à droite (sens horaire).
G03: Interpolation circulaire à gauche (sens anti-horaire).
Les mouvements programmés à la suite de G02/G03, s’exécutent en forme de trajectoire circulaire à l’avance F programmée.
Les définitions de sens horaire (G02) et sens anti-horaire (G03), sont fixées par les normes suivantes : a) Paramètre P600(1)= 0 b) Paramètre P600(1) = 1
Les fonctions G02/G03 sont modales et incompatibles entre elles, et également avec G00,
G01 et G33.
Les fonctions G74, G75, ou n’importe quel cycle fixe annulent G02, G03.
Les fonctions G02/G03 peuvent se programmer G2/G3.
Le format d’un bloc pour programmer une interpolation circulaire en coordonnées cartésiennes est le suivant:
N4 G02 (G03) X±4.3 Z±4.3 I±4.3 K±4.3
N4 : Numéro de bloc
G02 (G03) : Code qui définit l’interpolation
X±4.3
: Cote X du point final de l’arc
Z±4.3
I±4.3
K±4.3
: Cote Z du point final de l’arc
: Distance du point de départ au centre de l’arc, selon l’axe X.
: Distance du point de départ au centre de l’arc, selon l’axe Z.
Les valeurs de I, K se programment avec signe. Il est nécessaire de toujours les programmer, même s’ils ont la valeur zéro.
Page
4
Chapitre: 5
CONTROL DE TRAJECTOIRE
Section:
INTERPOLATION CIRCULAIRE
(G02, G03)
Le format d’un bloc pour programmer une interpolation circulaire en coordonnées polaires est le suivant:
N4 G02 (G03) A±3.3 I±4.3 K±4.3
N4 : Numéro de bloc
G02 (G03) : Code qui définit l’interpolation
A±3.3
: Angle entre l’axe des abscisses, et le segment pôle/point final de l’arc.
I±4.3
K±4.3
: Distance du point de départ au centre de l’arc, selon l’axe X.
: Distance du point de départ au centre de l’arc, selon l’axe Z.
Lorsque l’on programme une interpolation circulaire avec G02 ou G03, la CNC assume le centre de l’arc comme nouveau centre polaire. Dans ce cas, même si la programmation de l’axe X est au diamètre, la programmation de I est toujours au rayon.
Lorsque l’on presse la touche d’avance rapide et que l’on exécute un mouvement en G01, le pourcentage de la vitesse d’avance sera de 200% de la vitesse d’avance programmée, si le paramètre machine P600(3) a la valeur zéro.
5.5.1 INTERPOLATION CIRCULAIRE AVEC PROGRAMMATION
DU RAYON DE L’ARC
Format en mm: en pouces:
G02 (G03) X±4.3 Z±4.3 R±4.3
G02 (G03) X±3.4 Z±3.4 R±3.4
Où: G02(G03) fonction qui définit le sens de l’interpolation circulaire
X
Z
R cote X du point final de l’arc cote Z du point final de l’arc rayon de l’arc
Ceci signifie, que l’on peut programmer l’interpolation circulaire par le point final et le rayon
à la place des coordonnées (I, K) du centre.
Si l’arc de la circonférence est inférieur à 180º, le rayon se programmera avec signe positif, et s’il est inférieur à 180º, le rayon sera négatif.
P0 étant le point initial de l’arc et P1 le point final, avec une même valeur de rayon, il existe quatre arcs passant par les deux points.
Suivant le sens de l’interpolation circulaire G02 ou G03, et du signe du rayon on définit l’arc désiré. De cette manière le format de programmation des arcs de la figure sera le suivant:
Arc 1 G02 X Z R -
Arc 2 G02 X Z R +
Arc 3 G03 X Z R +
Arc 4 G03 X Z R -
Attention:
Si l’on programme un cercle complet avec la programmation du rayon, la CNC affichera l’erreur 47, puisqu’il existe une infinité de solutions.
Chapitre: 5
CONTROL DE TRAJECTOIRE
Section:
INTERPOLATION CIRCULAIRE
(G02, G03)
Page
5
5.5.2 INTERPOLATION CIRCULAIRE AVEC PROGRAMMATION
DU CENTRE DE L’ARC EN COORDONNEES ABSOLUES
(G06)
En ajoutant la fonction G06 dans un bloc d’interpolation circulaire, on peut programmer les cotes du centre de l’arc (I, K), en coordonnées absolues, c’est à dire, par rapport au zéro d’origine et non par rapport au début de l’arc.
La fonction G06, N’EST PAS MODALE, par conséquent, il faudra la programmer chaque fois que l’on voudra les cotes du centre de l’arc en coordonnées absolues.
En programmant de cette manière, la valeur de I devra être au rayon ou au diamètre en fonction du paramètre machine P11.
5.5.3 EXEMPLES DE PROGRAMMATION
En supposant que la programmation est en cotes absolues (G90) et celle de l’axe X au diamètre.
Point initial P0 (X40 Z40)
Coordonnées cartésiennes
N4 G02 X100 Z10 I40 K10
Coordonnées polaires
N4 G02 A194.036 I40 K10
Programmation de rayon
N4 G02 X100 Z10 R41.231
Programmation avec G06
N4 G02 G06 X100 Z10 I120 K50
Point initial P0 (X60 Z60)
Coordonnées cartésiennes
N4 G03 X140 Z20 I-10 K-50
Coordonnées polaires
N4 G03 A78.69 I-10 K-50
Programmation de rayon
N4 G03 X140 Z20 R50.99
Programmation avec G06
N4 G03 G06 X140 Z20 I40 K10
Page
6
Chapitre: 5
CONTROL DE TRAJECTOIRE
Section:
INTERPOLATION CIRCULAIRE
(G02, G03)
5.6 TRAJECTOIRE CIRCULAIRE TANGENTE A LA TRAJECTOIRE
ANTERIEURE (G08)
Par la fonction G08 on peut programmer une trajectoire circulaire tangente à la trajectoire antérieure sans nécessité de programmer les cotes (I, K) du centre.
Le format du bloc en coordonnées cartésiennes est le suivant:
N4 G08 X±4.3 Z±4.3 en mm
N4 G08 X±3.4 Z±3.4 en pouces
N4 Numéro de bloc
G08 Code d’interpolation circulaire tangente à la trajectoire antérieure.
X
Z
Cote X du point final de l’arc.
Cote Z du point final de l’arc.
Le format du bloc en coordonnées polaires est le suivant:
N4 G08 R±4.3 A±4.3 en mm
N4 G08 R±3.4 A±4.3 en pouces
N4 Numéro de bloc
G08 Code d’interpolation circulaire tangente à la trajectoire antérieure.
R Rayon (par rapport à l’origine polaire) du point final de l’arc.
A Angle (par rapport à l’origine polaire) du point final de l’arc.
Exemple:
La programmation de l’axe X est au diamètre.
En supposant que le point initial est P0 (X40 Z70), on désire programmer une droite ensuite un arc tangent à cette dernière et ensuite un arc tangent à celui antérieur.
N110 G90 G01 Z50
N120 G08 X80 Z30
N130 G08 X110 Z15
Si les arcs sont tangents il n’est pas nécessaire de programmer les coordonnées des centres (I, K).
Si on n’utilise pas G08 la programmation sera:
N110 G90 G01 Z50
N120 G02 X80 Z30 I20 K0
N130 G03 X110 Z15 I0 K-15
La fonction G08 n’est pas modale, elle se substitue seulement à G02 et G03 dans le bloc où elle se trouve. Peut s’employer lorsque l’on désire exécuter un arc tangent à la trajectoire antérieure. La trajectoire antérieure peut être une droite ou un arc.
Attention:
En utilisant la fonction G08, il n’est pas possible d’exécuter un cercle complet, puisqu’il existe une infinité de solutions. La CNC affichera le code d’erreur 47.
Chapitre: 5
CONTROL DE TRAJECTOIRE
Section:
ARC TANGENT A LA TRAJEC-
TOIRE. ANTERIEURE (G08)
Page
7
5.7 TRAJECTOIRE CIRCULAIRE DEFINIE PAR 3 POINTS (G09)
Par la fonction G09 on peut définir une trajectoire circulaire (arc), programmant le point final et un point intermédiaire (le point initial de l’arc est le point de départ du mouvement).
C’est à dire au lieu de programmer les coordonnées du centre, on programme un point intermédiaire quelconque.
Le format du bloc en coordonnées cartésiennes est le suivant:
N4 G09 X±4.3 Z±4.3 I±4.3 K±4.3
Z
I
K
N4 Numéro de bloc.
G09 Code de trajectoire circulaire par trois points.
X Cote X du point final de l’arc.
Cote Z du point final de l’arc.
Cote X du point intermédiaire de l’arc.
Cote Z du point intermédiaire de l’arc.
Le format du bloc en coordonnées polaires est le suivant:
N4 G09 R±4.3 A±4.3 I±4.3 K±4.3
N4 Numéro de bloc.
G09 Code de trajectoire circulaire par trois points.
R
A
Rayon (par rapport à l’origine polaire) du point final de l’arc.
Angle (par rapport à l’origine polaire) du point final de l’arc.
I
K
Cote X du point intermédiaire de l’arc.
Cote Z du point intermédiaire de l’arc.
Comme on le voit le point intermédiaire doit toujours être programmé en coordonnées cartésiennes.
Exemple:
La programmation de l’axe X est au diamètre.
En supposant que le point initial est P0 (X60
Z70) et le point final de l’arc (X120 Z20), le bloc de programme pour définir cet arc sera:
N4 G09 X120 Z20 I60 K50
Il n’est pas nécessaire de programmer le sens de déplacement G02, G03 en programmant G09.
La fonction G09 n’est pas modale, elle se substitue seulement à G02 et G03 dans le bloc où elle se trouve.
Attention:
En utilisant la fonction G09, il n’est pas possible d’exécuter un cercle complet, car pour définir un arc avec cette fonction il faut programmer 3 points distincts.
La CNC affichera le code d’erreur 40.
Page
8
Chapitre: 5
CONTROL DE TRAJECTOIRE
Section:
TRAJECTOIRE CIRCULAIRE
DEFINI PAR 3 POINTS (G09)
5.8 ENTREE TANGENTIELLE (G37)
Par la fonction préparatoire G37, on peut raccorder tangentiellement deux trajectoires sans nécessité de calculer les points d’intersection.
La fonction G37 n’est pas modale, c’est à dire, devra être programmée chaque fois que l’on désire raccorder tangentiellement deux trajectoires. Ces trajectoires pourront être, droitedroite ou bien droite-courbe. A la suite de G37 il faudra programmer le rayon, R4.3 en mm ou R3.4 en pouces, de l’arc d’entrée.
La valeur du rayon devra être toujours positive.
Cette programmation devra être dans le bloc qui comporte le mouvement dont on désire modifier la trajectoire. Le mouvement devra être rectiligne (G00 ou G01).
Si on programme G37 R4.3, dans un bloc avec un mouvement circulaire (G02 ou G03), la
CNC affichera l’erreur de type 41.
Exemple: Programmation de l’axe X au rayon
Point initial X20 Z60
N100 G90 G01 X20 Z30
N110 G03 X40 Z10 R20
Dans ce même exemple, si on désire réaliser une entrée tangentielle, décrivant un arc de 5 mm de rayon, on programmera:
N100 G90 G01 G37 R5 X20 Z30
N110 G03 X40 Z10 R20
Chapitre: 5
CONTROL DE TRAJECTOIRE
Section:
ENTREE TANGENTIELLE (G37)
Page
9
5.9 SORTIE TANGENTIELLE (G38)
Par la fonction préparatoire G38 on peut raccorder tangentiellement deux trajectoires, sans nécessité de calculer les points d’intersection.
La fonction G38 n’est pas modale, c’est à dire, devra être programmée chaque fois que l’on désire raccorder tangentiellement deux trajectoires. Ces trajectoires pourront être droitedroite ou bien courbe-droite.
A la suite de G38 on devra programmer le rayon, R4.3 en mm ou bien R3.4 en pouces, de l’arc de sortie. La valeur du rayon devra être toujours positive.
Pour pouvoir programmer G38 dans un bloc, il est nécessaire que la trajectoire du bloc suivant soit rectiligne (G00 ou G01).
Si la trajectoire suivante, est circulaire (G02 ou G03), la CNC affichera une erreur de type
42.
Exemple: Programmation de l’axe X en rayon
Point initial X10 Z50
N100 G90 G02 X30 Z30 R20
N110 G01 X30 Z10
Dans ce même exemple, si on désire réaliser une sortie tangentielle décrivant un arc de 5 mm de rayon on programmera:
N100 G90 G38 R5 G02 X30 Z30 R20
N110 G01 X30 Z10
Page
10
Chapitre: 5
CONTROL DE TRAJECTOIRE
Section:
SORTIE TANGENTIELLE
(G38)
5.10 ARRONDI CONTROLE D’ARETES (G36)
Dans les travaux de tournage il est possible, par la fonction G36, d’arrondir une arête avec un rayon déterminé sans nécessité de calculer le centre ni le point initial et final de l’arc.
La fonction G36 n’est pas modale, c’est à dire, elle doit être programmée chaque fois que l’on désire l’arrondi d’une arête. Cette fonction doit être programmée dans le bloc où l’on désire placer l’arrondi à la fin du déplacement.
Le rayon de l’arrondi se programme par R4.3 en mm, ou R3.4 en pouces, et toujours positif.
Exemples: La programmation de l’axe X est au diamètre
1º Arrondi entre droite-droite
Point initial X20 Z60
N100 G90 G01 G36 R10 X80
N110 Z10
2º Arrondi entre droite-arc
Point initial X20 Z60
N100 G90 G01 G36 R10 X80
N110 G02 X60 Z10 I20 K-30
Chapitre: 5
CONTROL DE TRAJECTOIRE
Section:
ARRONDI CONTROLE
D'ARETES (G36)
Page
11
3º Arrondi entre arc-arc
Point initial X60 Z90
N100 G90 G02 G36 R10 X60 Z50 R28
N110 X60 Z10 R28
Page
12
Chapitre: 5
CONTROL DE TRAJECTOIRE
Section:
ARRONDI CONTROLE
D'ARETES (G36)
5.11 CHANFREINAGE (G39)
Dans les travaux d’usinage il est possible, par la fonction G39, de chanfreiner les arêtes entre deux droites, sans nécessité de calculer les points d’intersection.
La fonction G39 n’est pas modale, c’est à dire, doit être programmée chaque fois que l’on désire chanfreiner une arête. Cette fonction doit être programmée dans le bloc à la fin duquel le chanfrein doit être effectué.
Par le code R4.3 en mm, R3.4 en pouces, toujours positif, on programme la distance depuis la fin du déplacement programmé jusqu’au point où l’on veut réaliser le chanfrein.
Exemple: Programmation de l’axe X au diamètre
Point initial X20 Z80
N100 G90 G01 G39 R10 X80 Z60
N110 X100 Z10
Chapitre: 5
CONTROL DE TRAJECTOIRE
Section:
CHANFREINAGE (G39)
Page
13
6.
FONCTIONS PREPARATOIRES
ADDITIONNELLES
6.1 TEMPORISATION (G04)
Par la fonction G04, on peut programmer une temporisation.
La valeur de la temporisation se programme par la lettre K.
Exemple: G04 K0.05 Temporisation de 0,05 sec.
G04 K2.5 Temporisation de 2,5 sec.
Si la valeur de K se programme avec un nombre, celui-ci pourra avoir une valeur comprise entre 0,00 et 99,99, si on le programme avec un paramètre (K P3), celui-ci pourra avoir une valeur comprise entre 0,00 et 655,35 secondes.
La temporisation s’exécute au début du bloc où elle est programmée. La fonction G04 peut se programmer G4
6.2 AFFICHER UN CODE D’ERREUR (G30)
Dès que la CNC lit un bloc avec le code G30, elle arrête le programme en cours et affiche le numéro de erreur indiqué.
Format de programmation: N4 G30 K2
N4
G30
Numéro de bloc
Code qui indique la programmation d’une erreur
K2(0-99) Code d’erreur programmé
On peut également programmer le numéro d’erreur par un paramètre arithmétique, valeur comprise entre P0 et P255. Par exemple: N4 G30 KP123
Ce code associé avec les codes G26, G27, G28 et G29 permet d’arrêter le programme et détecter de possibles erreurs de mesure, etc.
Dans un bloc où l’on programme G30, on ne peut programmer d’autre information.
Attention:
Si on désire que n’apparaisse pas affiché le commentaire propre des codes d’erreur de la CNC, le numéro du code après G30 devra être supérieur à ceux employés par la CNC.
Se rappeler, que l’utilisateur peut écrire des commentaires dans le programme qui seront affichés à l’exécution du bloc correspondant.
Chapitre: 6
FONCTIONS PREPARATOIRES ADDITIONNELLES
Section:
TEMPORISATION (G04)
Page
1
6.3 SAUTS ET APPELS INCONDITIONNELS (G25)
La fonction G25 peut s’utiliser pour sauter d’un bloc à un autre dans le même programme.
Dans le même bloc où l’on programme la fonction G25, on ne peut programmer d’autre information. Il existe deux formats de programmation:
Format a) N4 G25 N4
N4 Numéro de bloc
G25 Code de saut inconditionnel
N4 Numéro du bloc auquel on saute
Lorsque la CNC lit ce bloc, elle saute au bloc indiqué et le programme continue normalement, à partir de ce dernier bloc.
Exemple:
N5 Z50
N10 G25 N50
N15 X50
N20 Z70
N50 G01 X20
N0 G00 X100
Au bloc 10, la CNC saute au bloc 50, pour continuer depuis celui-ci jusqu’à la fin du programme.
Format b) N4 G25 N4.4.2
N4
G25
N4.4.2
Numéro de bloc
Code de saut inconditionnel
Numéro de répétitions
Numéro du dernier bloc à exécuter
Numéro du bloc où doit se faire le saut
Lorsque la CNC lit un bloc de ce type, elle saute au bloc défini entre le N et le premier point décimal.
Exécute ensuite la section du programme comprise entre ce bloc et celui défini entre les deux points décimaux autant de fois qu’indiqué par le dernier nombre.
Ce dernier nombre, peut avoir une valeur comprise entre 0 et 99, par contre si on le programme avec un paramètre, celui-ci peut avoir une valeur comprise entre 0 et 255.
Si l’on écrit seulement N4.4 la CNC assumera N4.4.1
L’exécution de cette section terminée, la CNC revient au bloc suivant celui où est programmé G25 N4.4.2
Page
2
Chapitre: 6
FONCTIONS PREPARATOIRES ADDITIONNELLES
Section:
SAUTS ET APPELS
INCONDITIONNELS (G25)
Exemple: N0 G00 X10
N5 Z20
N10 G01 X50 M3
N15 G00 Z0
N20 X0
N25 G25 N0.20.8
N30 M30
Au bloc N25, la CNC sautera au bloc 0 et exécutera 8 fois la section N0-N20. Ceci terminé, elle retournera au bloc 30.
Les fonctions préparatoires G26, G27, G28, G29 et G30 correspondant à des sauts/appels conditionnels, seront vues dans l’aparté correspondant de ce manuel: PROGRAMMATION
PARAMETRIQUE, OPERATIONS AVEC PARAMETRES.
Chapitre: 6
FONCTIONS PREPARATOIRES ADDITIONNELLES
Section:
SAUTS ET APPELS
INCONDITIONNELS (G25)
Page
3
6.4 FILETAGE ELECTRONIQUE (G33)
Par la fonction G33, on peut programmer et réaliser des filetages longitudinaux, frontaux et coniques. Pour pouvoir appliquer cette fonction il est nécessaire que la machine dispose d’un capteur rotatif sur la broche. La fonction G33 est modale, c’est à dire, une fois programmée elle est active, jusqu’à ce qu’elle soit annulée par G00, G01, G02, G03, M02,
M30, ARRET D’URGENCE ou RESET.
Filetage longitudinal
Se programme par le bloc N4 G33 Z±4.3 K3.4, où:
N4
G33
Z
K
Numéro de bloc
Code qui définit le filetage
Cote finale du filetage selon l’axe Z
Pas du filetage selon l’axe Z
La cote Z sera absolue ou incrémentale, selon que l’on travaille en G90 ou G91. Tant que la fonction G33 est active, on ne peut varier la vitesse d’avance F par le commutateur FEED-RATE, cette valeur restera fixe à 100%, on ne pourra pas non plus faire varier la vitesse de broche par les touches du clavier.
Filetage frontal (Spirale) Se programme par le bloc N4 G33 X±4.3 I3.4, où:
N4
G33
I
X
Numéro de bloc
Code qui définit le filetage
Cote finale du filetage selon l’axe X
Pas du filetage selon l’axe X
La cote X sera absolue ou incrémental, selon que l’on travaille en G90 ou G91.
Filetage conique Se programme par le bloc N4 G33 X±4.3 Z±4.3 I3.4 K3.4, où:
N4
G33
X
I
Z
K
Numéro de bloc
Code que définit le filetage
Cote finale du filetage selon l’axe X
Cote finale du filetage selon l’axe Z
Pas du filetage selon l’axe X
Pas du filetage selon l’axe Z
Les cotes X et Z seront absolues ou incrémentales, selon que l'on travaille en G90 ou
G91.
Pour les filetages coniques, il suffit de programmer le pas du filetage selon un axe, puisque que le contrôle calcule le pas de l’autre axe. C’est à dire, on peut programmer:
N4 G33 X±4.3 Z±4.3 I3.4 ou bien, N4 G33 X±4.3 Z±4.3 K3.4
Malgré tout, on peut programmer les deux pas (I, K) pour forcer le contrôle à réaliser des filetages coniques avec un pas différent à celui que le contrôle aurait calculé.
Attention:
Il est nécessaire que le début du filetage s’effectue avec l’outil hors de la pièce afin d’éviter les problèmes qui pourraient se produire au moment du démarrage des axes.
Page
4
Chapitre: 6
FONCTIONS PREPARATOIRES ADDITIONNELLES
Section:
FILETAGE ELECTRONIQUE
(G33)
6.4.1 EXEMPLES
a) Filetage longitudinal
Il faut réaliser un filetage cylindrique de 5 mm de pas et d’une profondeur de 2 mm.
Supposons que l’outil est au point X60 Z60 (X se programme au rayon).
Cotes absolues
N0 G00 G90 X18 Z53
N5 G33 Z7 K5
N10 G00 X60
N15 Z60
Cotes incrémentales
N0 G00 G91 X-42 Z-7
N5 G33 Z-46 K5
N10 G00 X42
N15 Z53
b) Filetage conique
Il faut réaliser un filetage conique de pas 5 mm, selon l’axe Z et une profondeur de 2 mm.
Supposons que l’outil est au point X60 Z60 (X se programme au rayon).
Chapitre: 6
FONCTIONS PREPARATOIRES ADDITIONNELLES
Section:
FILETAGE ELECTRONIQUE
(G33)
Page
5
Cotes absolues
N0 G00 G90 X12.75 Z52
N5 G33 X18.25 Z8 K5
N10 G00 X60
N15 Z60
Cotes incrémentales
N0 G00 G91 X-47.25 Z-8
N5 G33 X5.5 Z-44 K5
N10 G00 X41.75
N15 Z52
c) Raccordement de filetages
Si on travaille en arête arrondie (G05), on peut raccorder différents filetages de manière continue sur une même pièce.
Il faut raccorder un filetage longitudinal et un conique de pas 5 mm selon l’axe Z et une profondeur de 2 mm.
Supposons que l’outil est au point X60 Z60 (X se programme au rayon).
Cotes absolues
N0 G00 G90 X8 Z57
N5 G33 G05 Z35 K5
N10 X18.8 Z8 K5
N15 G00 X60
N20 Z60
Page
6
Chapitre: 6
FONCTIONS PREPARATOIRES ADDITIONNELLES
Section:
FILETAGE ELECTRONIQUE
(G33)
6.5 FACTEUR D' ECHELLE (G72)
Par la fonction G72 on peut augmenter ou réduire des pièces programmées.
De cette manière on peut réaliser des familles de pièces de formes similaires mais de dimensions différentes avec un seul programme. La fonction G72 doit se programmer seule en un bloc.
Le format de programmation est: N4 G72 K2.4
N Numéro de bloc
G72 Code qui définit le facteur d’échelle
K Valeur du facteur d’échelle
Valeur minimale K0.0001
(Multiplication par 0,0001).
Valeur maximale K99.9999 (Multiplication par 99,9999).
A la suite de G72 toutes les coordonnées programmées se multiplient par la valeur de K jusqu’à que soit lue une nouvelle définition du facteur d’échelle G72 ou que l’on annule celui-ci.
Pour annuler le facteur d’échelle il suffit de définir un autre facteur d’échelle de valeur K1 ou également en introduisant M02, M30 ou en exécutant un RESET ou un ARRET
D’URGENCE.
Chapitre: 6
FONCTIONS PREPARATOIRES ADDITIONNELLES
Section:
FACTEUR D'ECHELLE (G72)
Page
7
6.6 TRAVAIL AVEC PALPEUR (G75)
Avec cette fonction on peut employer un palpeur de mesure, connecté à la CNC.
Le format de programmation est le suivant:
N4 G75 X±4.3 Z±4.3 en millimètres.
N4 G75 X±3.4 Z±3.4 en pouces.
La machine se déplacera jusqu’à recevoir le signal extérieur du palpeur. Une fois reçu ce signal terminera le bloc, acceptant comme position théorique des axes, les positions réelles qu’ils avaient lorsqu’a été reçu le signal. Durant le mouvement de palpage on ne pourra varier la vitesse d’avance par le commutateur de FEED-RATE, qui restera fixe à 100%.
Si les axes arrivent à la position programmée avant de recevoir le signal extérieur du palpeur, la CNC affichera l’erreur 65.
Une fois ce bloc exécuté on peut assigner les valeurs des axes aux paramètres arithmétiques que l’on désire. Ceci combiné avec la possibilité de réaliser des opérations mathématiques avec les paramètres arithmétiques, permet de réaliser des programmes spéciaux de mesure et de vérification d’outils et pièces.
La fonction G75 implique les fonctions G01 et G40; c’est à dire, à partir d’un bloc avec G75, la CNC assume la fonction G01 et G40.
Page
8
Chapitre: 6
FONCTIONS PREPARATOIRES ADDITIONNELLES
Section:
TRAVAIL AVEC PALPEUR (G75)
6.7 TRAITEMENT DE BLOC UNIQUE.
ACTIVATION (G47) ET ANNULATION (G48)
La CNC considère comme “Bloc Unique” le groupe de blocs qui se trouve entre les fonctions G47 et G48.
Après l’exécution la fonction G47 la CNC exécute tous les blocs qui viennent à la suite jusqu’à exécuter un bloc qui contienne la fonction G48.
Si on tape la touche durant l’exécution d’un “Bloc unique”, en mode Automatique ou Bloc à Bloc, la CNC continue l’exécution jusqu’à exécuter la fonction G48, qui arrête l’exécution.
La fonction G47 étant active, le commutateur M.F.O. et les touches de variation de la vitesse de rotation de broche, seront inhabilités, le programme s’exécutant à 100% de la F et de la
S programmées.
Les fonctions G47 et G48 sont modales et incompatibles entre elles.
Lorsque l’on met en marche la CNC, après l’exécution M02/M30, après un ARRET
D’URGENCE ou après un RESET, la CNC assume le code G48.
Chapitre: 6
FONCTIONS PREPARATOIRES ADDITIONNELLES
Section:
TRAITEMENT DE
BLOC UNIQUE (G47, G48)
Page
9
7.
COMPENSATION D’OUTIL
Dans les opérations habituelles d’usinage, il est nécessaire calculer et définir la trajectoire de l’outil en tenant compte des dimensions de celui-ci (longueur et rayon), de manière à obtenir les dimensions de la pièce désirées.
La compensation, de longueur et de rayon d’outil, permet de programmer directement le contour de la pièce sans tenir compte des dimensions de l’outil. La CNC calcule automatiquement, à partir du contour de la pièce et des dimensions de l’outil stockées dans la table d’outils, la trajectoire que doit suivre l’outil.
Chaque fois que l’on sélectionne un outil (T2), la CNC applique automatiquement la compensation de longueur stockée dans la table (X, Z, I, K), sans nécessité de programmer aucun code G.
Pour la compensation de rayon existent trois fonctions préparatoires:
G40 Annulation de la compensation de rayon d’outil
G41 Compensation de rayon d’outil a gauche
G42 Compensation de rayon d’outil a droite
Avec le paramètre P600(1) = 0 et axes ou P600(1) = 1 et axes
G41:
L’outil reste à gauche de la pièce selon le sens de l’ usinage.
G42:
L’outil reste à droite de la pièce selon le sens de l’ usinage.
Avec P600(1) = 0 et axes
G42 et inversement.
ou P600(1) = 1 et axes G41 agit comme
La CNC dispose d’une table de jusqu’à 32 outils pour compensation de longueur (X, Z, I,
K) et rayon (R) d’outil; Dans cette table sont stockés les codes de forme (F) de l’outil.
Chapitre: 7
COMPENSATION D'OUTIL
Section:
Page
1
Pour fixer les valeurs de compensation de rayon et longueur de chacun des outils on doit utiliser l’option “Table d’outils” dans les “Fonctions auxiliaires”.
Egalement on peut définir la table d’outils depuis le programme pièce, en utilisant la fonction
G50.
Les valeurs maximales de chaque champ de la table d’outils sont:
X, Z (longueur outil) +/-8388.607 mm (+/-330.2599 pouces)
I, K
(correction longueur outil) +/-32.766 mm (+/-1.2900 pouces)
R
(Rayon) 1000.000 mm (39.3700 pouces)
F
(Code de forme) Il est nécessaire de le définir pour la compensation de rayon. Les codes possibles sont : F0-F9 (Voir figure).
La compensation de rayon est effective par G41 ou G42, en prenant la valeur sélectionnée par la fonction T de la table (T01 T32). Si la fonction T n’est pas programmée, la CNC assume la valeur T00 qui correspond à un outil de dimensions égales à zéro.
Les fonctions G41, G42 sont modales (maintenues) et sont annulées par G40, M02, M30 ainsi que par ARRET D’URGENCE ou un RESET général.
Attention:
Les valeurs de I employées pour corriger les usures d’outil doivent être programmées au diamètre.
Page
2
Chapitre: 7
COMPENSATION D'OUTIL
Section:
Code "1"
Code "2"
Code "3"
CODES DE FORME
Code "0" et "9"
Code "7"
Code "6"
Code "5"
P: Pointe de l’outil
C: Centre de l’outil
Chapitre: 7
COMPENSATION D'OUTIL
Section:
Page
3
Code "4"
Code "4"
Code "5"
Code "6"
Code "7"
Code "8"
Code "3"
Code "2"
Code "1"
Code "8"
P: Pointe de l’outil
C: Centre de l’outil
Page
4
Chapitre: 7
COMPENSATION D'OUTIL
Section:
7.1
SELECTION ET DEBUT DE LA COMPENSATION DE RAYON
(G41, G42)
On doit utiliser les codes G41 ou G42 pour le début de la compensation
Dans le même bloc où l’on programme G41/G42 ou dans un bloc antérieur, on doit avoir programmé la fonction T (T01 T32) pour sélectionner dans la table d’outils la valeur de correction à appliquer. Si aucun outil n’est sélectionné, la CNC assume la valeur T00 (outil de valeurs = 0).
Attention:
La sélection de la compensation de rayon d’outil (G41/G42) peut se réaliser seulement lorsque sont actifs G00 ou G01 (déplacements rectilignes).
Si le premier appel de la compensation se réalise avec G02 ou G03 actifs, la
CNC affichera le code d’erreur 48.
Dans les pages suivantes sont détaillés les différents cas de début de compensation de rayon d’outil.
Trajectoire compensée (T.C)
Trajectoire programmée (T.P)
Chapitre: 7
COMPENSATION D'OUTIL
Section:
COMPENSATION DE
RAYON D'OUTIL (G41, G42)
Page
5
Page
6
Chapitre: 7
COMPENSATION D'OUTIL
Section:
COMPENSATION DE
RAYON D'OUTIL (G41, G42)
7.2 FONCTIONNEMENT AVEC COMPENSATION DE RAYON
Ci après, des figures où l’on peut voir les diverses trajectoires suivies par un outil contrôlé par une CNC programmée avec compensation de rayon.
Trajectoire compensée (T.C)
Trajectoire programmée (T.P)
Chapitre: 7
COMPENSATION D'OUTIL
Section:
FONCTIONNEMENT AVEC
COMPENSATION DE RAYON
Page
7
Page
8
Trajectoire compensée (T.C)
Trajectoire programmée (T.P)
Chapitre: 7
COMPENSATION D'OUTIL
Section:
FONCTIONNEMENT AVEC
COMPENSATION DE RAYON
7.3 ANNULATION TEMPORAIRE DE LA COMPENSATION AVEC
G00
Lorsque l’on détecte un passage de G01, G02, G03 à G00, l’outil reste tangent à la perpendiculaire, à l’extrémité du déplacement programmé en le bloc de G01, G02 ou G03.
Ce même traitement s’applique lorsque l’on programme un bloc avec G40, mais sans information de mouvement. Les déplacements suivants en G00 s’effectuent sans compensation de rayon.
Lorsque l’on détecte le passage de G00 à G01, G02, G03 le traitement correspond à celui du premier point compensé, la compensation radiale s’applique normalement.
Cas spécial:
Si le contrôle n’a pas suffisamment d’informations pour compenser, mais le mouvement est en G00, l’exécution se fera sans compensation radiale.
Chapitre: 7
COMPENSATION D'OUTIL
Section:
ANNULATION TEMPORAIRE
AVEC G00
Page
9
7.4 ANNULATION DE LA COMPENSATION DE RAYON (G40)
L’annulation de la compensation de rayon s’effectue par la fonction G40.
Il faut tenir compte que l’arrêt de la compensation de rayon (G40), peut s’effectuer seulement dans un bloc où est programmé un mouvement rectiligne (G00, G01).
Si on programme G40 dans un bloc avec G02 ou G03 la CNC affichera le code d’erreur
48.
A la suite, des figures avec les différents cas d’annulation.
Trajectoire compensée (T.C)
Trajectoire programmée (T.P)
Page
10
Chapitre: 7
COMPENSATION D'OUTIL
Section:
ANNULATION DE LA COM-
PENSATION DE RAYON (G40)
Trajectoire compensée (T.C)
Trajectoire programmée (T.P)
Chapitre: 7
COMPENSATION D'OUTIL
Section:
ANNULATION DE LA COM-
PENSATION DE RAYON (G40)
Page
11
8.
CYCLES FIXES D’USINAGE
La CNC dispose des cycles fixes d’usinage suivants.
G67 N0 Cycle fixe de cylindrage.
G67 N1 Cycle fixe de dressage
G67 N2 Cycle fixe de cylindrage conique
G67 N3 Cycle fixe de filetage
G67 N4 Cycle fixe de arrondi
G67 N5 Cycle fixe de gorges (rainurage)
G67 N6 Cycle fixe de perçage multiple
G67 N7 Cycle fixe de perçage simple / Cycle fixe taraudage
G67 N8 Cycle fixe de clavette en X ou Z
G66 Cycle fixe de suivi de profil (non accessible depuis le clavier)
G68
G69
G81
G82
G84
G85
Cycle fixe d’ébauche sur l’axe X (non accessible depuis le clavier)
Cycle fixe d’ébauche sur l’axe Z (non accessible depuis le clavier)
Cycle fixe de tournage de segments droits (non accessible depuis le clavier)
Cycle fixe de dressage de segments droits (non accessible depuis le clavier)
Cycle fixe de tournage de segments courbes (non accessible depuis le clavier)
Cycle fixe de dressage de segments courbes (non accessible depuis le clavier)
G86 Cycle fixe de filetage longitudinal (non accessible depuis le clavier)
Paramètres relatifs aux cycles fixes:
Les cycles fixes peuvent altérer le contenu des paramètres P0 a P99.
Ainsi, la CNC actualise, à la mise en marche, après un Reset et chaque fois que l’on abandonne le mode exécution du programme P99996, les paramètres arithmétiques suivants:
P190 Cote X du point de changement d’outil fixé par le fabricant
P191 Cote Z du point de changement d’outil fixé par le fabricant
P201 Unités de travail (0=mm, 1=pouces)
P24 Unités de travail (0=Rayons, 1=Diamètres)
Lorsque l’on programme les cycles fixes, si la valeur d’un paramètre est une constante, il est nécessaire de taper la touche K après le symbole =. Par exemple: N4 G66 P0 = K25
......
Chapitre: 8
CYCLES FIXES D'USINAGE
Section:
Page
1
8.1 CYCLE FIXE DE CYLINDRAGE (G67 N0)
Paramètres de base de définition du cycle:
P100 Cote X du point “BEGIN” en unités de travail (rayons/diamètres)
P101 Cote Z du point “BEGIN”
P102 Cote X du point “END” en unités de travail (rayons/diamètres)
P103 Cote Z du point “END”
P4
Définit le pas de cylindrage
∆
. Se programmera par une valeur positive exprimée au rayon.
Si on programme avec valeur 0, la CNC tiendra compte du paramètre P5 (nombre de passes de cylindrage). Si l’on définit P4=0 et P5=0, la CNC affichera le message d’erreur correspondant.
P6
Indique le diamètre final (
φ
) que l’on désire obtenir dans l’opération de cylindrage.
P19
Définit la distance de sécurité en X (se programme au rayon)
P20
Définit la distance de sécurité en Z
Paramètres relatifs à la passe de finition:
Si on ne désire pas de passe de finition définir: P22=K0 et P23=K0.
P22
Pourcentage (%) de la passe d’ébauche programmée, qui sera utilisé comme passe de finition
P23
Pourcentage (%) de l’avance d’ébauche programmée, qui sera utilisé comme avance de finition
Paramètres relatifs à l’outil de finition:
Si on désire utiliser un outil pour l’ébauche et un autre pour la finition on doit définir les paramètres ci-dessous.
Si on ne désire pas changer d’outil définir P26=K0.
Page
2
Chapitre: 8
CYCLES FIXES D'USINAGE
Section:
CYLINDRAGE
(G67 N0)
P26
Définit le numéro d’outil que l’on désire utiliser pour la passe de finition.
Si le fabricant a défini un point de changement d’outil, la machine se déplacera
à ce point, paramètres arithmétiques P190 et P191, pour effectuer le changement d’outil.
S’il n’y a pas de point de changement d’outil il faut définir les paramètres arithmétiques P134 et P135 pour définir le point de changement d’outil.
P134 Cote X du point où se déplacera la machine pour effectuer le changement d’outil.
Se définit en unités de travail (rayons/diamètres)
P135 Cote Z du point où se déplacera la machine pour effectuer le changement d’outil
La CNC prend en compte les paramètres P134 et P135 si le fabricant n’a pas défini un point de changement d’outil.
Concepts généraux:
1.
Les conditions d’usinage (vitesse d’avance, vitesse de rotation de la broche, sens de rotation de la broche, etc.) doivent se programmer avant l’appel du cycle.
2.- Les paramètres doivent se programmer dans un bloc antérieur à celui de l’appel du cycle.
N2 F10 S1000 M03
N4 P100=K P101=K P102=K P103=K P4=K P6=K P19=K P20=K .....
N6 G67 N0
3.- Le cycle fixe n’altère pas les paramètres d’appel P22, P23 et P26, qui peuvent être utilisés pour des cycles postérieurs. Par contre il altère le contenu des “Paramètres de base de définition du cycle”.
4.- Le fonctionnement de base du cycle est expliqué dans le manuel d’Opération.
5.- Les conditions de sortie sont G00 et G90.
Chapitre: 8
CYCLES FIXES D'USINAGE
Section:
CYLINDRAGE
(G67 N0)
Page
3
8.2 CYCLE FIXE DE DRESSAGE (G67 N1)
Paramètres de base de définition du cycle:
P100 Cote X du point “BEGIN” en unités de travail (rayons/diamètres)
P101 Cote Z du point “BEGIN”
P102 Cote X du point “END” en unités de travail (rayons/diamètres)
P103 Cote Z du point “END”
P4
Définit le pas de dressage
∆
. Se programmera par une valeur positive.
Si on le programme avec valeur 0, la CNC tiendra compte du paramètre P5
(nombre de passes de dressage). Si on définit P4=0 et P5=0, la CNC affichera le message d’erreur correspondant.
P6
Indique le diamètre final (
φ
) que l’on désire obtenir dans l’opération de cylindrage.
P19
Définit la distance de sécurité en X (se définit au rayon)
P20
Définit la distance de sécurité en Z
Paramètres relatifs à la passe de finition:
Si on ne désire pas de passe de finition définir: P22=K0 et P23=K0.
P22
Pourcentage (%) de la passe d'ébauche programmée, que l’on utilisée comme passe de finition
P23
Pourcentage (%) de l' avance d’ébauche programmé, que l’on utilise comme avance de finition
Paramètres relatifs à l’outil de finition:
Si l’on désire utiliser un outil pour l’ébauche et un autre pour la passe de finition on doit définir les paramètres ci-dessous.
Si l’on ne désire pas changer d’outil définir P26=K0.
Page
4
Chapitre: 8
CYCLES FIXES D'USINAGE
Section:
DRESSAGE
(G67 N1)
P26
Définit le numéro d’outil que l’on désire utiliser pour la passe de finition.
Si le fabricant a défini un point de changement d’outil, la machine se déplacera à ce point, paramètres arithmétiques P190 et P191, pour effectuer le changement d’outil.
S’il n’y a pas de point de changement d’outil il faut définir les paramètres arithmétiques P134 et P135 pour définir le point de changement d’outil.
P134 Cote X du point où se déplacera la machine pour effectuer le changement d’outil.
Se définit en unités de travail (rayons/diamètres)
P135 Cote Z du point où se déplacera la machine pour effectuer le changement d’outil
La CNC prend en compte les paramètres P134 et P135 si le fabricant n’a pas défini un point de changement d’outil.
Concepts généraux:
1.
Les conditions d’usinage (vitesse d’avance, vitesse de rotation de la broche, sens de rotation de la broche, etc.) doivent se programmer avant l’appel du cycle.
2.- Les paramètres doivent se programmer dans un bloc antérieur à celui de l’appel du cycle.
N2 F10 S1000 M03
N4 P100=K P101=K P102=K P103=K P4=K P6=K P19=K P20=K .....
N6 G67 N1
3.- Le cycle fixe n’altère pas les paramètres d’appel P22, P23 et P26, qui peuvent être utilisés pour des cycles postérieurs. Par contre il altère le contenu des “Paramètres de base de définition du cycle”.
4.- Le fonctionnement de base du cycle est expliqué dans le manuel d’Opération.
5.- Les conditions de sortie sont G00 et G90.
Chapitre: 8
CYCLES FIXES D'USINAGE
Section:
DRESSAGE
(G67 N1)
Page
5
8.3 CYCLE FIXE DE CYLINDRAGE CONIQUE (G67 N2)
Paramètres de base de définition du cycle:
P100 Cote X du point “BEGIN” en unités de travail (rayons/diamètres)
P101 Cote Z du point “BEGIN”
P4
Définit le pas de cylindrage
∆
. Se programmera par un valeur positive exprimée au rayon.
Si on le programme avec valeur 0, la CNC tiendra compte du paramètre P5
(nombre de passes de dressage). Si on définit P4=0 et P5=0, la CNC affichera le message d’erreur correspondant.
P6
Indique le diamètre final (
φ
) que l’on désire obtenir dans l’opération de cylindrage.
P7
définit la pente (%) du chanfrein ou plan incliné que l’on désire effectuer.
P7 = 100 x (10/40) = 25
P7 = 100 x tg 14,036 =25
P10
Indique le quadrant que l’on désire usiner. Avec P18 définit le type d’angle que l’on désire effectuer.
P18
Indique le type de géométrie de l’angle. Avec P10 définit le type d’angle que l’on désire effectuer.
Page
6
P19
Définit la distance de sécurité en X (se définit au rayon).
P20
Définit la distance de sécurité en Z.
Chapitre: 8
CYCLES FIXES D'USINAGE
Section:
CYLINDRAGE CONIQUE
(G67 N2)
Paramètres relatifs à la passe de finition:
Si l’on ne désire pas de passe de finition définir: P22=K0 et P23=K0.
P22
Pourcentage (%) de la passe d’ébauche programmée, que l’on utilise comme passe de finition
P23
Pourcentage (%) de l’avance d’ébauche programmée, que l’on utilise comme avance de finition
Paramètres relatifs à l’outil de finition:
Si l’on désire utiliser un outil pour l’ébauche et un autre pour la passe de finition on doit définir les paramètres ci-dessous.
Si l’on ne désire pas changer d’outil définir P26=K0.
P26
Définit le numéro d’outil que l’on désire utiliser pour la passe de finition.
Si le fabricant a défini un point de changement d’outil, la machine se déplacera
à ce point, paramètres arithmétiques P190 et P191, pour effectuer le changement d’outil.
S’il n’y a pas de point de changement d’outil il faut définir les paramètres arithmétiques P134 et P135 pour définir le point de changement d’outil.
P134 Cote X du point où se déplacera la machine pour effectuer le changement d’outil.
Se définit en unités de travail (rayons/diamètres)
P135 Cote Z du point où se déplacera la machine pour effectuer le changement d’outil
La CNC prend en compte les paramètres P134 et P135 si le fabricant n’a pas défini un point de changement d’outil.
Concepts généraux:
1.
Les conditions d’usinage (vitesse d’avance, vitesse de rotation de la broche, sens de rotation de la broche, etc.) doivent se programmer avant l’appel du cycle.
2.- Les paramètres doivent se programmer dans un bloc antérieur à celui de l’appel du cycle.
N2 F10 S1000 M03
N4 P100=K P101=K P102=K P103=K P4=K P6=K P19=K P20=K .....
N6 G67 N1
3.- Le cycle fixe n’altère pas les paramètres d’appel P22, P23 et P26, qui peuvent être utilisés pour des cycles postérieurs. Par contre il altère le contenu des “Paramètres de base de définition du cycle”.
4.- Le fonctionnement de base du cycle est expliqué dans le manuel d’Opération.
5.- Les conditions de sortie sont G00 et G90.
Chapitre: 8
CYCLES FIXES D'USINAGE
Section:
CYLINDRAGE CONIQUE
(G67 N2)
Page
7
8.4 CYCLE FIXE DE FILETAGE (G67 N3)
Paramètres de base de définition du cycle:
P100 Cote X du point “BEGIN” en unités de travail (rayons/diamètres)
P101 Cote Z du point “BEGIN”
P102 Cote X du point “END” en unités de travail (rayons/diamètres)
P103 Cote Z du point “END”
P4
Définit le pas de filetage
∆
. Se programmera par une valeur positive exprimée au rayon. Si l’on définit P4=0 la CNC affichera l’erreur correspondante.
Se programmera au rayon et la profondeur de chaque passe sera fonction du nombre de passe correspondant(
∆ n), comme le montre la figure suivante.
Page
8
P8
Définit le pas du filet “P”. Les filetages à droite ou à gauche s’effectueront en sélectionnant de manière adéquate le sens de rotation de la broche.
P11
Indique le type de filetage. Si filetage extérieur P11=0. Si filetage intérieur
P11=1.
P14
Définit la profondeur du filet “H”. Se programmera au rayon et avec valeur positive. S’il est programmé avec valeur 0, la CNC affichera l’erreur correspondante.
Chapitre: 8
CYCLES FIXES D'USINAGE
Section:
FILETAGE
(G67 N3)
P16
Définit l’angle de pénétration de l’outil. Est référé à l’axe X
S’il est programmé avec valeur 0, le filet se réalisera avec pénétration radiale. Si on lui assigne une valeur égale à la moitié de l’angle de l’outil, la pénétration se réalise le long du flanc du filet.
P19
Définit la distance de sécurité en X (se définit au rayon)
P20
Définit la distance de sécurité en Z
P128 Distance fin de filetage. Définit à quelle distance de la fin du filetage commence la sortie de filet, effectuant un filet conique dont le pas en Z est toujours P10.
Si P128=K0 il n’y a pas de sortie de filet. Si P128 négatif, l’erreur 3 est générée.
Concepts généraux:
1.
Les conditions d’usinage (vitesse d’avance, vitesse de rotation de la broche, sens de rotation de la broche, etc.) doivent se programmer avant l’appel du cycle.
2.- Les paramètres doivent se programmer dans un bloc antérieur à celui de l’appel du cycle.
N2 F10 S1000 M03
N4 P100=K P101=K P102=K P103=K P4=K P8=K P11=K P14=K P16=K .....
N6 G67 N3
3.- Le cycle fixe n’altère pas les paramètres d’appel P22, P23 et P26, qui peuvent être utilisés pour des cycles postérieurs. Par contre il altère le contenu des “Paramètres de base de définition du cycle”.
4.- Le fonctionnement de base du cycle est expliqué dans le manuel d’Opération.
5.- Les conditions de sortie sont G00 et G90.
Chapitre: 8
CYCLES FIXES D'USINAGE
Section:
FILETAGE
(G67 N3)
Page
9
8.5 CYCLE FIXE D’ARRONDI (G67 N4)
Paramètres de base de définition du cycle:
P16
Type de cycle
P100 Cote X du point “BEGIN” en unités de travail (rayons/diamètres)
P101 Cote Z du point “BEGIN”
P102 Cote X du point “END” en unités de travail (rayons/diamètres)
P103 Cote Z du point “END”
P4
Définit la passe d’arrondi
∆
. Se programmera par une valeur positive exprimée au rayon.
S’il est programmé avec valeur 0, la CNC tiendra compte du paramètre P5
(nombre de passes d’arrondi). Si l’on définit P4=0 et P5=0, la CNC affichera le message d’erreur correspondant.
P9
Définit le rayon d’arrondi R
P10
Indique le quadrant que l’on désire usiner.
P15
Type d’arrondi. Si arrondi convexe P15=0. Si arrondi concave P15=1.
P18
Indique le type de géométrie de l’angle.
Page
10
Chapitre: 8
CYCLES FIXES D'USINAGE
Section:
ARRONDI
(G67 N4)
P19
Définit la distance de sécurité en X (se définit au rayon)
P20
Définit la distance de sécurité en Z
Paramètres relatifs à la passe de finition:
Si l’on ne désire pas de passe de finition définir: P22=K0 et P23=K0.
P22
Pourcentage (%) de la passe d’ébauche que l’on utilise comme passe de finition
P23
Pourcentage (%) d’avance d’ébauche que l’on utilise comme avance de finition
Paramètres relatifs à l’outil de finition:
Si l’on désire utiliser un outil pour l’ébauche et un autre pour la finition on doit définir les paramètres ci-dessous.
Si l’on ne désire pas changer d’outil définir P26=K0.
P26
Définit le numéro d’outil que l’on désire utiliser pour la passe de finition.
Si le fabricant a défini un point de changement d’outil, la machine se déplacera
à ce point, paramètres arithmétiques P190 et P191, pour effectuer le changement d’outil.
S’il n’y a pas de point de changement d’outil il faut définir les paramètres arithmétiques P134 et P135 pour définir le point de changement d’outil.
P134 Cote X du point où se déplacera la machine pour effectuer le changement d’outil.
Se définit en unités de travail (rayons/diamètres)
P135 Cote Z du point où se déplacera la machine pour effectuer le changement d’outil
La CNC prend en compte les paramètres P134 et P135 si le fabricant n’a pas défini un point de changement d’outil.
Concepts généraux:
1.
Les conditions d’usinage (vitesse d’avance, vitesse de rotation de la broche, sens de rotation de la broche, etc.) doivent se programmer avant l’appel du cycle.
2.- Les paramètres doivent se programmer dans un bloc antérieur à celui de l’appel du cycle.
N2 F10 S1000 M03
N4 P16=K P100=K P101=K P102=K P103=K P4=K P9=K P10=K P15=K .....
N6 G67 N4
3.- Le cycle fixe n’altère pas les paramètres d’appel P22, P23 et P26, qui peuvent être utilisés pour des cycles postérieurs. Par contre il altère le contenu des “Paramètres de base de définition du cycle”.
4.- Le fonctionnement de base du cycle est expliqué dans le manuel d’Opération.
5.- Les conditions de sortie sont G00 et G90.
Chapitre: 8
CYCLES FIXES D'USINAGE
Section:
ARRONDI
(G67 N4)
Page
11
8.6 CYCLE FIXE DE RAINURAGE (GORGE) (G67 N5)
Paramètres de base de définition du cycle:
P100 Cote X du point “BEGIN” en unités de travail (rayons/diamètres)
P101 Cote Z du point “BEGIN”
P102 Cote X du point “END” en unités de travail (rayons/diamètres)
P103 Cote Z du point “END”
P4
Définit le pas de rainurage (gorge)
∆
. Se programmera par une valeur positive exprimée au rayon.
S’il est programmé avec valeur 0, la CNC tiendra compte du paramètre P5
(nombre de passes de rainurage (gorge). Si l’on définit P4=0 et P5=0, la CNC affichera le message d’erreur correspondant.
P6
Indique le diamètre final (
φ
) que l’on désire obtenir pour l’opération de rainurage
(gorge).
P12
Indique la largeur de l’outil (TW).
P13
Définit le temps que restera, à chaque passe de rainurage (gorge), l’outil au fond de la rainure. Se définit en secondes, ainsi, P13=K1.5 signifie une temporisation de 1.5 secondes.
P19
Définit la distance de sécurité en X (se définit au rayon)
P20
Définit la distance de sécurité en Z
Page
12
Chapitre: 8
CYCLES FIXES D'USINAGE
Section:
RAINURAGE
(G67 N5)
Paramètres relatifs à la passe de finition:
Si l’on ne désire pas de passe de finition définir: P22=K0 et P23=K0.
P22
Pourcentage (%) de la passe d’ébauche programmée, que l’on utilise comme passe de finition
P23
Pourcentage (%) d’avance d’ébauche programmé, que l’on utilise comme avance de finition
Concepts généraux:
1.
Les conditions d’usinage (vitesse d’avance, vitesse de rotation de la broche, sens de rotation de la broche, etc.) doivent se programmer avant l’appel du cycle.
2.- Les paramètres doivent se programmer dans un bloc antérieur à celui de l’appel du cycle.
N2 F10 S1000 M03
N4 P100=K P101=K P102=K P103=K P4=K P6=K P12=K P13=K P19=K .....
N6 G67 N5
3.- Le cycle fixe n’altère pas les paramètres d’appel P22, P23 et P26, qui peuvent être utilisés pour des cycles postérieurs. Par contre il altère le contenu des “Paramètres de base de définition du cycle”.
4.- Le fonctionnement de base du cycle est expliqué dans le manuel d’Opération.
5.- Les conditions de sortie sont G00 et G90.
Chapitre: 8
CYCLES FIXES D'USINAGE
Section:
RAINURAGE
(G67 N5)
Page
13
8.7 CYCLE FIXE DE PERÇAGE MULTIPLE (G67 N6)
Movement à F
Movement rapide
Paramètres de base de définition du cycle:
P100 Cote X du point “BEGIN” en unités de travail (rayons/diamètres)
P101 Cote Z du point “BEGIN”
P102 Cote X du point “END” en unités de travail (rayons/diamètres)
P103 Cote Z du point “END”
P4
Définit l’incrément angulaire
∆
entre perçages. Se programmera par une valeur positive exprimée en degrés.
P5
Définit le nombre de perçages (N) que l’on désire effectuer.
P8
Indique le pas ou la pénétration maximale (P) à chaque perçage (prise de matériel.
Lorsqu’il se réfère à l’axe X on doit le définir au rayon.
P13
Définit le temps que restera, à chaque perçage, le foret au fond du trou. Se définit en secondes, ainsi, P13=K1.5 signifie une temporisation de 1.5 secondes.
P16
Indique la position angulaire (
α
) du premier trou.
P19
Définit la distance de sécurité en X (se définit au rayon).
P20
Définit la distance de sécurité en Z.
Page
14
Chapitre: 8
CYCLES FIXES D'USINAGE
Section:
PERÇAGE MULTIPLE
(G67 N6)
Concepts généraux:
1.
Les conditions d’usinage (vitesse d’avance, vitesse de rotation de la broche, sens de rotation de la broche, etc.) doivent se programmer avant l’appel du cycle.
2.- Les paramètres doivent se programmer dans un bloc antérieur à celui de l’appel du cycle.
N2 F10 S1000 M03
N4 P100=K P101=K P102=K P103=K P4=K P5=K P8=K P13=K P16=K .....
N6 G67 N6
3.- Le cycle fixe n’altère pas les paramètres d’appel P22, P23 et P26, qui peuvent être utilisés pour des cycles postérieurs. Par contre il altère le contenu des “Paramètres de base de définition du cycle”.
4.- Le fonctionnement de base du cycle est expliqué dans le manuel d’Opération.
5.- Les conditions de sortie sont G00 et G90.
Chapitre: 8
CYCLES FIXES D'USINAGE
Section:
PERÇAGE MULTIPLE
(G67 N6)
Page
15
8.8 CYCLE FIXE DE PERÇAGE SIMPLE (G67 N7)
CYCLE FIXE DE TARAUDAGE (G67 N7)
Ces deux cycles se définissent de manière similaire, seul diffère le paramètre “P8”, pas ou pénétration maximale (P). Dans le cycle de taraudage il faut le définir avec la valeur P8=0, et dans le cycle de perçage simple il faut le définir avec une valeur distincte de 0.
Movement rapide
Movement à F
Paramètres de base de définition du cycle:
P101 Cote Z du point “BEGIN”
P103 Cote Z du point “END”
P8
Indique le pas ou la pénétration maximale (P) à chaque perçage (prise de matière).
Lorsque l’on désire définir le cycle de taraudage il faut le définir avec la valeur
P8=0, et lorsque l’on désire définir le cycle de perçage simple il faut le définir avec une valeur distincte de 0.
P13
Définit le temps que restera la foret au fond du trou. Se définit en secondes, ainsi,
P13=K1.5 signifie une temporisation de 1.5 secondes.
P19
Définit la distance de sécurité en X (se définit au rayon)
P20
Définit la distance de sécurité en Z
Page
16
Chapitre: 8
CYCLES FIXES D'USINAGE
Section:
PERÇAGE SIMPLE
(G67 N7)
Concepts généraux:
1.
Les conditions d’usinage (vitesse d’avance, vitesse de rotation de la broche, sens de rotation de la broche, etc.) doivent se programmer avant l’appel du cycle.
2.- Les paramètres doivent se programmer dans un bloc antérieur à celui de l’appel du cycle.
N2 F10 S1000 M03
N4 P101=K P103=K P8=K P13=K P19=K P20=K
N6 G67 N7
3.- Le cycle fixe n’altère pas les paramètres d’appel P22, P23 et P26, qui peuvent être utilisés pour des cycles postérieurs. Par contre il altère le contenu des “Paramètres de base de définition du cycle”.
4.- Le fonctionnement de base du cycle est expliqué dans le manuel d’Opération.
5.- Les conditions de sortie sont G00 et G90.
Chapitre: 8
CYCLES FIXES D'USINAGE
Section:
PERÇAGE SIMPLE
(G67 N7)
Page
17
8.9 CYCLE FIXE DE CLAVETTES (G67 N8)
Paramètres de base de définition du cycle:
P100 Cote X du point “BEGIN” en unités de travail (rayons/diamètres)
P101 Cote Z du point “BEGIN”
P102 Cote X du point “END” en unités de travail (rayons/diamètres)
P103 Cote Z du point “END”
P4
Définit l’incrément angulaire
∆
entre clavettes. Se programmera par une valeur positive exprimée en degrés.
P5
Définit le nombre de clavettes (N) que l’on désire effectuer.
P16
Indique la position angulaire (
α
) de la première clavette.
P19
Définit la distance de sécurité en X (se définit au rayon)
P20
Définit la distance de sécurité en Z
Page
18
Chapitre: 8
CYCLES FIXES D'USINAGE
Section:
CLAVETTES
(G67 N8)
Concepts généraux:
1.
Les conditions d’usinage (vitesse d’avance, vitesse de rotation de la broche, sens de rotation de la broche, etc.) doivent se programmer avant l’appel du cycle.
2.- Les paramètres doivent se programmer dans un bloc antérieur à celui de l’appel du cycle.
N2 F10 S1000 M03
N4 P100=K P101=K P102=K P103=K P4=K P5=K P16=K P19=K P20=K
N6 G67 N8
3.- Le cycle fixe n’altère pas les paramètres d’appel P22, P23 et P26, qui peuvent être utilisés pour des cycles postérieurs. Par contre il altère le contenu des “Paramètres de base de définition du cycle”.
4.- Le fonctionnement de base du cycle est expliqué dans le manuel d’Opération.
5.- Les conditions de sortie sont G00 et G90.
Chapitre: 8
CYCLES FIXES D'USINAGE
Section:
CLAVETTES
(G67 N8)
Page
19
8.10 CYCLE FIXE DE SUIVI DE PROFIL (G66)
Format:
N4 G66 P0=K P1=K P4=K P5=K P7=K P8=K P9=K P12=K P13=K P14=K
Signification des paramètres:
P0
Cote X du point initial (A) du profil (au rayon ou diamètre).
P1
Cote Z du point initial (A) du profil.
P4
Surépaisseur de matière, c’est à dire, la quantité (selon unités de mesure) à éliminer de la pièce d’origine.
Doit être supérieure ou égale à zéro et supérieure ou égale à la surépaisseur pour la finition; en cas contraire, l’erreur 3 est générée. Selon la valeur de P12, sera interprété comme surépaisseur en X ou en Z.
P5
Pas maximal. Doit être supérieur à zéro; en cas contraire, l’erreur 3 est générée.
Selon la valeur de P12, sera interprété comme pas en X ou en Z. le pas réel calculé par le contrôle, sera inférieur ou égal au pas maximal.
P7
Surépaisseur pour la finition sur l’axe X. Doit être supérieure ou égale à zéro; en cas contraire, l’erreur 3 est générée.
P8
Surépaisseur pour la finition sur l’axe Z. Doit être supérieure ou égale à zéro; en cas contraire, l’erreur 3 est générée.
P9
Vitesse d’avance, de la passe de finition. Si elle est zéro, il n’y a pas de passe de finition. S’il est négatif, l’erreur 3 est générée.
Page
20
Chapitre: 8
CYCLES FIXES D'USINAGE
Section:
SUIVI DE PROFIL
(G66)
P12 Angle de l’outil. Doit être supérieur ou égal à zéro et inférieur ou égal à 90°; sinon, l’erreur 3 est générée.
S’il est inférieur ou égal à 45º, P4 sera pris comme surépaisseur en X et P5 comme pas maximal en X.
S’il est supérieur à 45º, P4 sera pris comme surépaisseur en Z et P5 comme pas maximal en Z.
P13 Numéro du premier bloc de définition du profil.
P14 Numéro du dernier bloc de définition du profil.
Chapitre: 8
CYCLES FIXES D'USINAGE
Section:
SUIVI DE PROFIL
(G66)
Page
21
Au moment de programmer ce cycle fixe, il faut tenir compte des indications suivantes:
1º Pour la définition du profil, il ne faut pas programmer le point initial A qui est déjà défini par les paramètres P0 et P1.
2º Les conditions d’usinage (vitesse d’avance, rotation de la broche, etc.) doivent
être programmées avant l’appel du cycle.
3º Les paramètres peuvent être programmés dans le bloc d’appel du cycle ou dans des blocs antérieurs.
Ce cycle fixe n’altère pas les paramètres d’appel, qui peuvent être utilisés pour des cycles postérieurs. Par contre il altère le contenu des paramètres P70 a P99.
4º Les conditions de sortie du cycle sont G00 et G90.
5º Le profil peut être formé de droites, arcs, arrondis, entrées tangentielles, sorties tangentielles et chanfreins.
6º La programmation peut être en absolu ou en incrémental.
7º Dans la définition du profil aucune fonction T n’est possible.
8º Les mouvements d’approche et de sortie se font en rapide et les autres à la vitesse programmée.
9º Le cycle termine au point où était positionné l’outil initialement.
10º On peut travailler avec compensation de rayon d’outil (G41, G42).
11º La coordonnée X du point d’appel du cycle fixe, doit être différente de P0, sinon la
CNC générera le code d’erreur 4.
La coordonnée Z du point d’appel du cycle fixe, doit être différente de P1, sinon la
CNC générera le code d’erreur 4.
12º Les mouvements d’usinage s’effectuent à la vitesse d’avance programmée.
Page
22
Chapitre: 8
CYCLES FIXES D'USINAGE
Section:
SUIVI DE PROFIL
(G66)
Exemple G66. Programmation de l’axe X au diamètre
N100 —
N110 G90 G00 G42 X150 Z115
N120 G66 P0=K0 P1=K85 P4=K20 P5=K5 P7=K1 P8=K1
P9=K100 P12=K40 P13=K200 P14=K290
N130 G40 X160 Z135
N140 M30
N200 G36 R5 X50 Z85 ................................................................. ;Définition de profil
N210 X50 Z70
N220 X40 Z60
N230 G36 R2 X40 Z50
N240 G39 R2 X60 Z50
N250 X60 Z40
N260 G36 R2 X80 Z30
N270 G36 R10 X80 Z10
N280 G36 R2 X120 Z10
N290 X120 Z0
Chapitre: 8
CYCLES FIXES D'USINAGE
Section:
SUIVI DE PROFIL
(G66)
Page
23
8.11 CYCLE FIXE D' EBAUCHE SUR L’AXE X (G68)
Format:
N4 G68 P0=K P1=K P5=K P7=K P8=K P9=K P13=K P14=K
Signification des paramètres:
P0
Cote absolue X du point initial (A) du profil (au rayon ou diamètre).
P1
Cote absolue Z du point initial du profil (A).
P5
Pas maximal (au rayon). Doit être supérieur à zéro; en cas contraire, il se produit l’erreur 3.
Le pas réel calculé par le contrôle sera inférieur ou égal au pas maximal.
P7
Surépaisseur pour la finition sur l’axe X (au rayon). Doit être supérieur ou égal à zéro; en cas contraire, il se produit l’erreur 3.
P8
Surépaisseur pour la finition sur l’axe Z. Doit être supérieur ou égal à zéro; en cas contraire, il se produit l’erreur 3.
P9
Vitesse d’avance de la passe de finition.
Si à ce paramètre on lui assigne la valeur P9=0 il n’y a pas de passe de finition mais réalise une passe finale d’ébauche conservant les surépaisseurs indiquées par P7 et
P8.
Si on lui assigne une valeur négative la passe de finition ne s’effectue pas, ni la passe finale d’ébauche.
Page
24
Chapitre: 8
CYCLES FIXES D'USINAGE
Section:
EBAUCHE SUR X
(G68)
P10 Il faut assigner à ce paramètre une valeur distincte de zéro lorsque l’on désire que la
CNC effectue une passe finale d’ébauche avant d’effectuer la passe de finition.
P13 Numéro du premier bloc de définition du profil.
P14 Numéro du dernier bloc de définition du profil. Doit être supérieur à P13; sinon l’erreur 13 est générée.
Chapitre: 8
CYCLES FIXES D'USINAGE
Section:
EBAUCHE SUR X
(G68)
Page
25
Au moment de programmer ce cycle fixe, il faut tenir compte de ce qui suit:
1.
La distance entre le point de départ 0 et le point final (B), selon l’axe X, doit être égale ou supérieure à P7.
Pour éviter l’erreur 31 lorsque l'on travaille avec compensation de rayon, il est recommandé de donner à cette distance, une valeur égale à P7, plus un nombre entier de fois P5 (pas).
2.
La distance entre le point de départ 0 et le point initial (A), selon l’axe Z, doit être supérieure à P8.
3.
Pour la définition du profil, il ne faut pas programmer le point initial (A) car il est déjà défini par les paramètres P0 et P1.
4.
Les conditions d’usinage (avance, rotation de la broche, etc.) doivent être programmées avant l’appel du cycle.
Les paramètres peuvent être programmées dans le bloc d’appel du cycle ou dans des blocs antérieurs.
Ce cycle fixe n’altère pas les paramètres d’appel, qui peuvent être utilisés pour des cycles postérieurs. Par contre il altère le contenu des paramètres P70 a P99.
Les déplacements du cycle de travail élémentaire (voir figure) s’effectuent de la manière suivante: : Du point 1 au 2 et du 2 au 3 ils s’effectuent à la vitesse d’avance programmée, tandis que du 0 au 1 et du 3 au 0 ils s’effectuent en avance rapide.
Les conditions de sortie sont G00 et G90.
5.
Le profil peut être formé par des segments droits et des segments courbes.
Tous les blocs de définition du profil se programmeront en coordonnées cartésiennes.
Il faut toujours programmer les 2 axes et de plus en absolu sinon la commande générera l’erreur 21.
Si le profil dispose de segments courbes, ceux-ci se programmeront avec les coordonnées
I, K du centre, référées au point initial de l’arc et avec le signe correspondant.
Si pour la définition du profil on programme des fonctions F, S, T ou M, elles seront ignorées sauf pour la passe de finition.
6.
Le cycle termine au point où était positionné l’outil initialement (0).
7.
On pourra travailler avec compensation de rayon d’outil (G41, G42) chaque fois que le dernier mouvement avant l’appel du cycle fixe aura été en G00. Sinon, la CNC générera l’erreur 35.
Page
26
Chapitre: 8
CYCLES FIXES D'USINAGE
Section:
EBAUCHE SUR X
(G68)
Exemple G68.
N100 —
N110 G42 G00 X120 Z0
N120 G68 P0=K0 P1=K-10 P5=K2 P7=K0.8 P8=K0.8
P9=K100 P13=K200 P14=K250
N130 G40 X130 Z10
N140 M30
N200 G03 X40 Z-30 I-6 K-26 .................................................. ;Définition du profil
N210 G01 X40 Z-40
N220 G02 X80 Z-60 I25 K5
N230 G01 X80 Z-70
N240 X100 Z-80
N250 X100 Z-90
Chapitre: 8
CYCLES FIXES D'USINAGE
Section:
EBAUCHE SUR X
(G68)
Page
27
8.12 CYCLE FIXE D' EBAUCHE SUR L’AXE Z (G69)
Format:
N4 G69 P0=K P1=K P5=K P7=K P8=K P9=K P13=K P14=K
Signification des paramètres:
P0
Cote X du point initial (A) du profil (au rayon ou diamètre)
P1
Cote Z du point initial du profil (A).
P5
Pas maximal. Doit être supérieur à zéro; en cas contraire, l’erreur 3 est générée. Le pas réel calculé par le contrôle sera inférieur ou égal au pas maximal.
P7
Surépaisseur pour la finition sur l’axe X. Doit être supérieure ou égale à zéro; en cas contraire, l’erreur 3 est générée.
P8
Surépaisseur pour la finition sur l’axe Z. Doit être supérieure ou égale à zéro; en cas contraire, l’erreur 3 est générée.
P9
Vitesse d’avance de la passe de finition.
Si à ce paramètre on lui assigne la valeur P9=0 la passe de finition ne s’effectue pas mais réalise une passe finale d’ébauche conservant les surépaisseurs indiquées en P7 et P8.
Si on lui assigne une valeur négative la passe de finition n’est pas effectuée ni la passe finale d’ébauche.
Page
28
Chapitre: 8
CYCLES FIXES D'USINAGE
Section:
EBAUCHE SUR Z
(G69)
P10 On doit assigner à ce paramètre une valeur distincte de zéro lorsque l’on désire que la CNC effectue une passe finale d’ébauche avant d’effectuer la passe de finition.
P13 Numéro du premier bloc de définition du profil.
P14 Numéro du dernier bloc de définition du profil. Doit être supérieur à P13; en cas contraire, se produit l’erreur 13.
Chapitre: 8
CYCLES FIXES D'USINAGE
Section:
EBAUCHE SUR Z
(G69)
Page
29
Au moment de programmer ce cycle fixe il faut tenir compte de ce qui suit:
1.
La distance entre le point de départ 0 et le point (B) selon l’axe Z, doit être égale ou supérieure à P8.
Pour éviter que l’erreur 31 se produise lorsque l’on travaille avec compensation de rayon, il est recommandé de donner à cette distance une valeur égale à P8 plus un nombre entier de fois P5 (pas).
2.
La distance entre le point de départ 0 et le point initial (A) selon l’axe X, doit être supérieure à P7.
3.
Pour la définition du profil il ne faut pas programmer le point initial (A), puisqu’il est déjà défini par les paramètres P0 et P1.
4.
Les conditions d’usinage (avance, rotation de la broche, etc.) doivent être programmées avant l’appel du cycle.
Les paramètres peuvent être programmés dans le bloc d’appel du cycle ou dans des blocs antérieurs.
Ce cycle fixe n’altère pas les paramètres d’appel, qui peuvent être utilisés pour des cycles postérieurs. Par contre il altère le contenu des paramètres P70 a P99.
Les déplacements du cycle de travail élémentaire (voir figure) s’effectuent de la manière suivante: Du point 1 au 2 et du 2 au 3 s’effectuent a la vitesse d’avance programmée, tandis que du 0 au 1 et du 3 au 0 s’effectuent en avance rapide.
Les conditions de sortie sont G00 et G90.
5.
Le profil peut être formé par des segments droits et des segments courbes.
Tous les blocs de définition du profil se programmeront en coordonnées cartésiennes.
Il faut toujours programmer les 2 axes et de plus en absolu sinon la commande générera l’erreur 21.
Si le profil dispose de segments courbes, ceux-ci se programmeront avec les coordonnées
I, K du centre, référées au point initial de l’arc et avec le signe correspondant.
Si pour la définition du profil on programme des fonctions F, S, T ou M, elles seront ignorées sauf pour la passe de finition.
6.
Le cycle termine au point où était positionné l’outil initialement (0).
7.
On peut travailler avec compensation de rayon d’outil (G41, G42) chaque fois que le dernier mouvement avant l’appel du cycle fixe aura été en G00. Si ce n’est pas ainsi, la CNC générera erreur 35.
Page
30
Chapitre: 8
CYCLES FIXES D'USINAGE
Section:
EBAUCHE SUR Z
(G69)
Exemple G69.
N190 —
N200 G41 G0 X90 Z-5
N210 G69 P0=K80 P1=K-80 P5=K2 P7=K0.8 P8=K0.8 P9=K100
P13=K300 P14=K340
N220 G40 X100 Z0
N230 M30
N300 G01 X80 Z-60................................................................. ;Définition du profil
N310 G03 X60 Z-50 I5 K15
N320 G01 X40 Z-40
N330 G03 X10 Z-25 I5 K20
N340 G01 X10 Z-10
Chapitre: 8
CYCLES FIXES D'USINAGE
Section:
EBAUCHE SUR Z
(G69)
Page
31
8.13 CYCLE FIXE DE CHARIOTAGE DE SEGMENTS DROITS (G81)
Format:
N4 G81 P0=K P1=K P2=K P3=K P5=K P7=K P8=K P9=K
Signification des paramètres:
P0
Cote X du point A (au rayon ou diamètres)
P1
Cote Z du point A
P2
Cote X du point B (au rayon ou diamètres)
P3
Cote Z du point B
P5
Pas maximal. Doit être supérieur à zéro; en cas contraire, il se produit l’erreur 3. Le pas réel calculé par le contrôle sera inférieur ou égal au pas maximal.
P7
Surépaisseur pour la finition sur l’axe X. Doit être supérieure ou égale à zéro; en cas contraire, se produit l’erreur 3.
P8
Surépaisseur pour la finition sur l’axe Z. Doit être supérieure ou égale à zéro; en cas contraire, se produit l’erreur 3.
P9
Vitesse d’avance de la passe de finition. Si elle est nulle, il n’y a pas de passe de finition. Si elle est négative, il se produit l’erreur 3.
Exemple de programmation au diamètre. Le point de départ étant 0 (X134 Z47), et les points du profil A (X0 Z0) et B (X90 Z-45)
N90 G00 X134 Z47 .............. (Positionnement de l’outil au point 0).
N100 G81 P0=K0 P1=K0 P2=K90 P3=K-45 P5=K5 P7=K3 P8=K4 P9=K100
Page
32
Chapitre: 8
CYCLES FIXES D'USINAGE
Section:
CHARIOTAGE DE SEGMENTS
DROITS (G81)
Au moment de programmer ce cycle fixe, il faut tenir compte de ce qui suit:
1.
La distance entre le point de départ (0) et le point (B), selon l’axe X, doit que être égale ou supérieure à P7.
Pour éviter des passes trop petites ou l’erreur 31, lorsque l’on travaille avec compensation de rayon, il est recommandé de donner à cette distance une valeur égale à P7 plus un nombre entier de fois P5 (pas).
2.
La distance entre le point de départ (0) et le point (A), selon l’axe Z, doit être supérieure
à P8.
3.
Les conditions d’usinage (vitesse d’avance, vitesse de rotation de la broche, etc.) doivent être programmées avant l’appel du cycle.
Les paramètres peuvent être programmés dans le bloc d’appel du cycle ou dans des blocs antérieurs.
Ce cycle fixe n’altère pas les paramètres d’appel, qui peuvent être utilisés pour des cycles postérieurs. Par contre il altère le contenu des paramètres P70 à P99.
Les déplacements du cycle de travail élémentaire (voir figure) s’effectuent de la manière suivante: Du point 1 au 2 et du 2 au 3 s’effectuent à la vitesse d’avance programmée, tandis que du 0 au 1 et du 3 au 0 s’effectuent en avance rapide.
Les conditions de sortie sont G00 et G90.
4.
Si la position de l’outil n’est pas correcte pour exécuter le cycle, il se produit l’erreur 4.
Si elle est correcte, il sera réalisé auparavant un tournage horizontal, si nécessaire.
5.
S’il faut une passe de finition, le cycle termine au point où était positionné l’outil initialement (0). S’il n’y a pas de passe de finition, le cycle termine au point F.
6.
On peut travailler avec compensation de rayon d’outil (G41, G42) chaque fois que le dernier mouvement avant l’appel du cycle fixe aura été en G00. S'il n’en est pas ainsi, la CNC générera l’erreur 35.
Chapitre: 8
CYCLES FIXES D'USINAGE
Section:
CHARIOTAGE DE SEGMENTS
DROITS (G81)
Page
33
8.14 CYCLE FIXE DE DRESSAGE DE SEGMENTS DROITS (G82)
Format:
N4 G82 P0=K P1=K P2=K P3=K P5=K P7=K P8=K P9=K
Signification des paramètres:
P0
Cote X du point A (au rayon ou diamètres)
P1
Cote Z du point A
P2
Cote X du point B (au rayon ou diamètres)
P3
Cote Z du point B
P5
Pas maximal. Doit être supérieure à zéro; en cas contraire, se produit l’erreur 3. Le pas réel calculé par le contrôle, sera inférieur ou égal au pas maximal.
P7
Surépaisseur pour la finition sur l’axe X. Doit être supérieure ou égale à zéro; en cas contraire, il se produit l’erreur 3.
P8
Surépaisseur pour la finition sur l’axe Z. Doit être supérieure ou égale à zéro; en cas contraire, il se produit l’erreur 3.
P9
Vitesse d’avance de la passe de finition. Si elle est nulle, il n’y a pas de passe de finition. si elle est négative, il se produit l’erreur 3.
Exemple de programmation au diamètre. Le point de départ étant 0 (X136 Z39), et les points du profil A (X90 Z-45) et B (X0 Z0)
N90 G00 X136 Z39 .............. (Positionnement de l’outil au point 0)
N100 G82 P0=K90 P1=K-45 P2=K0 P3=K0 P5=K5 P7=K3 P8=K4 P9=K100
Page
34
Chapitre: 8
CYCLES FIXES D'USINAGE
Section:
DRESSAGE DE SEGMENTS
DROITS (G82)
Au moment de programmer ce cycle fixe, il faut tenir compte de ce qui suit:
1.
La distance entre le point de départ 0 et le point (B), selon l’axe Z, doit être égale ou supérieure à P8.
Pour éviter des passes trop petites ou l’erreur 31, lorsque l’on travaille avec compensation de rayon, il est recommandé de donner à cette distance une valeur égale à P8 plus un nombre entier de fois P5 (pas).
2.
La distance entre le point de départ 0 et le point (A), selon l’axe X, doit être supérieure
à P7.
3.
Les conditions d’usinage (vitesse d’avance, vitesse de rotation de la broche, etc.) doivent être programmées avant l’appel du cycle.
Les paramètres peuvent être programmés dans le bloc d’appel du cycle ou dans des blocs antérieurs.
Ce cycle fixe n’altère pas les paramètres d’appel, qui peuvent être utilisés pour des cycles postérieurs. Par contre il altère le contenu des paramètres P70 a P99.
Les déplacements du cycle de travail élémentaire (voir figure) s’effectuent de la manière suivante: Du point 1 au 2 et du 2 au 3 s’effectuent à la vitesse d’avance programmée, tandis que du 0 au 1 et du 3 au 0 s’effectuent en avance rapide.
Les conditions de sortie sont G00 et G90.
4.
Si la position de l’outil n’est pas correcte pour exécuter le cycle, il se produit l’erreur 4.
Si elle est correcte, il sera réalisé auparavant un dressage vertical, si nécessaire.
5.
S’il faut une passe de finition, le cycle termine au point où était positionné l’outil initialement (0). S’il n’y a pas de passe de finition, le cycle termine au point F.
6.
On peut travailler avec compensation de rayon d’outil (G41, G42) chaque fois que le dernier mouvement avant l’appel du cycle fixe aura été en G00. S’il n’en est pas ainsi, la CNC générera l’erreur 35.
Chapitre: 8
CYCLES FIXES D'USINAGE
Section:
DRESSAGE DE SEGMENTS
DROITS (G82)
Page
35
8.15 CYCLE FIXE. CHARIOTAGE DE SEGMENTS COURBES (G84)
Format:
N4 G84 P0=K P1=K P2=K P3=K P5=K P7=K P8=K P9=K P18=K P19=K
Signification des paramètres:
P0
Cote X du point A (au rayon ou diamètres)
P1
Cote Z du point A
P2
Cote X du point B (au rayon ou diamètres)
P3
Cote Z du point B
P5
Pas maximal. Doit être supérieur à zéro; en cas contraire, il se produit l’erreur 3. Le pas réel calculé par le contrôle sera inférieur ou égal au pas maximal.
P7
Surépaisseur pour la finition sur l’axe X. Doit être supérieure ou égale à zéro; en cas contraire, il se produit l’erreur 3.
P8
Surépaisseur pour la finition sur l’axe Z. Doit être supérieure ou égale à zéro; en cas contraire, il se produit l’erreur 3.
P9
Vitesse d’avance de la passe de finition. Si elle est nulle, il n’y a pas de passe de finition. Si elle est négative, il se produit l’erreur 3.
P18 (I). Distance du point A au centre du l’arc selon l’axe X. Même si les valeurs de l’axe
X se programment au diamètre, les valeurs de I se programment au rayon.
P19 (K). Distance du point A au centre de l’arc selon l’axe Z.
Page
36
Chapitre: 8
CYCLES FIXES D'USINAGE
Section:
CHARIOTAGE DE SEGMENTS
COURBES (G84)
Exemple de programmation au diamètre. Le point de départ étant 0 (X149 Z86), le centre de l’arc C (X160 Z91) et les points du profil A (X0 Z71) B (X120 Z11).
N90 G00 X149 Z86 ............... Positionnement de l’outil au point 0
N100 G84 P0=K0 P1=K71 P2=K120 P3=K11 P5=K5 P7=K4 P8=K4 P9=K100
P18=K80 P19=K20
Au moment de programmer ce cycle fixe, il faut tenir compte de ce qui suit:
1.
La distance entre le point de départ 0 et le point (B), selon l’axe X, doit être égale ou supérieure à P7.
Pour éviter des passes trop petites ou l’erreur 31, lorsque l’on travaille avec compensation de rayon, il est recommandé de donner à cette distance une valeur égale à P7 plus un nombre entier de fois P5 (pas).
2.
La distance entre le point de départ 0 et le point (A), selon l’axe Z, doit être supérieure
à P8.
3.
Les conditions d’usinage (vitesse d’avance, vitesse de rotation de la broche, etc.) doivent être programmées avant l’appel du cycle.
Les paramètres peuvent être programmés dans le bloc d’appel du cycle ou dans des blocs antérieurs.
Ce cycle fixe n’altère pas les paramètres d’appel, qui peuvent être utilisés pour des cycles postérieurs. Par contre il altère le contenu des paramètres P70 a P99.
Les déplacements du cycle de travail élémentaire (voir figure) s’effectuent de la manière suivante: Du point 1 au 2 et du 2 au 3 s’effectuent à la vitesse d’avance programmée, tandis que du 0 au 1 et du 3 au 0 s’effectuent en avance rapide.
Les conditions de sortie sont G00 et G90.
4.
Si la position de l’outil n’est pas correcte pour exécuter le cycle, il se produit l’erreur 4.
Il sera réalisé auparavant un tournage horizontal, si nécessaire.
5.
S’il faut une passe de finition, le cycle termine au point où était positionné l’outil initialement (0). S’il ne faut pas de passe de finition, le cycle termine au point F.
6.
On peut travailler avec compensation de rayon d’outil (G41, G42) chaque fois que le dernier mouvement avant l’appel du cycle fixe aura été en G00. S’il n’en est pas ainsi, la CNC générera l’erreur 35.
Chapitre: 8
CYCLES FIXES D'USINAGE
Section:
CHARIOTAGE DE SEGMENTS
COURBES (G84)
Page
37
8.16 CYCLE FIXE DE DRESSAGE DE SEGMENTS COURBES (G85)
Format:
N4 G85 P0=K P1=K P2=K P3=K P5=K P7=K P8=K P9=K P18=K P19=K
Signification des paramètres:
P0
Cote X du point A (au rayon ou diamètres)
P1
Cote Z du point A
P2
Cote X du point B (au rayon ou diamètres)
P3
Cote Z du point B
P5
Pas maximal. Doit être supérieur à zéro; en cas contraire, il se produit erreur 3. Le pas réel calculé par le contrôle, sera inférieur ou égal au pas maximal.
P7
Surépaisseur pour la finition sur l’axe X. Doit être supérieure ou égale à zéro; en cas contraire, il se produit l’erreur 3
P8
Surépaisseur pour la finition sur l’axe Z. Doit être supérieure ou égale à zéro; en cas contraire, il se produit l’erreur 3.
P9
Vitesse d’avance de la passe de finition. Si elle est nulle, il n’y a pas de passe de finition. Si elle est négative, il se produit l’erreur 3.
P18 (I). Distance du point A au centre de l’arc selon l’axe X. Même si les valeurs de l’axe
X se programment au diamètre, les valeurs de I se programment au rayon.
P19 (K). Distance du point A au centre de l’arc selon l’axe Z.
Page
38
Chapitre: 8
CYCLES FIXES D'USINAGE
Section:
DRESSAGE DE SEGMENTS
COURBES (G85)
Exemple de programmation au diamètre. Le point de départ étant 0 (X150 Z8), le centre de l’arc C (X160 Z91) et les points du profil A (X118 Z11) B (X0 Z70).
N90 G00 X150 Z85 .............. Positionnement de l’outil au point 0.
N100 G85 P0=K118 P1=K11 P2=K0 P3=K70 P5=K5 P7=K4 P8=K4 P9=K100
P18=K21 P19=K80
Au moment de programmer ce cycle fixe, il faut tenir compte de ce qui suit:
1.
La distance entre le point de départ 0 et le point (B), selon l’axe Z, doit que être égale ou supérieure à P8.
Pour éviter des passes trop petites ou l’erreur 31, lorsque l’on travaille avec compensation de rayon, il est recommandé de donner à cette distance une valeur égale à P8 plus un nombre entier de fois P5 (pas).
2.
La distance entre le point de départ 0 et le point (A), selon l’axe X, doit que être supérieure à P7.
3.
Les conditions d’usinage (vitesse d’avance, vitesse de rotation de la broche, etc.) doivent être programmées avant l’appel du cycle.
Les paramètres peuvent être programmés dans le bloc d’appel du cycle ou dans des blocs antérieurs.
Ce cycle fixe n’altère pas les paramètres d’appel, qui peuvent être utilisés pour des cycles postérieurs. Par contre il altère le contenu des paramètres P70 a P99.
Les déplacements du cycle de travail élémentaire (voir figure) s’effectuent de la manière suivante: Du point 1 au 2 et du 2 au 3 s’effectuent à la vitesse d’avance programmée, tandis que du 0 au 1 et du 3 au 0 s’effectuent en avance rapide.
Les conditions de sortie sont G00 et G90.
4.
Si la position de l’outil n’est pas correcte pour exécuter le cycle, il se produit l’erreur 4.
Il sera réalisé auparavant un dressage vertical, si nécessaire.
5.
S’il faut une passe de finition, le cycle termine au point où était positionné l’outil initialement (0). S’il n’y a pas de passe de finition, le cycle termine au point F.
6.
On peut travailler avec compensation de rayon d’outil (G41, G42) chaque fois que le dernier mouvement avant l’appel du cycle fixe aura été en G00. S’il n’en n’est pas ainsi, la CNC générera l’erreur 35.
Chapitre: 8
CYCLES FIXES D'USINAGE
Section:
DRESSAGE DE SEGMENTS
COURBES (G85)
Page
39
8.17 CYCLE FIXE DE FILETAGE LONGITUDINAL (G86)
Format:
N4 G86 P0=K P1=K P2=K P3=K P4=K P5=K P6=K P7=K P10=K P11=K P12=K
Signification des paramètres:
P0
Cote X absolue du point initial (A) du filetage (au rayon ou diamètre).
P1
Cote Z absolue du point initial (A) du filetage
P2
Cote X absolue du point final (B) du filetage (au rayon ou diamètre)
P3
Cote Z absolue du point final (B) du filetage
P4
Profondeur du filet (au rayon). Aura une valeur positive pour les filetages extérieurs et négative pour les intérieurs. S’il est égal à zéro, il se produit l’erreur 3.
P5
Passe initiale (au rayon). Définit la profondeur de la première passe de filetage.
Les passes successives dépendront du signe donné à ce paramètre:
- Si le signe est positif, la profondeur de la seconde passe sera P5 2 et celle de la nième P5 n, jusqu’à atteindre la profondeur de finition.
- Si le signe est négatif, l’incrément de la passe se maintiendra constant et à une valeur égale à la valeur absolue du paramètre.
- Si la valeur est égale à zéro, il se produit l’erreur 3.
Page
40
Chapitre: 8
CYCLES FIXES D'USINAGE
Section:
FILETAGE LONGITUDINAL
(G86)
P6
Distance de sécurité (au rayon). Indique à quelle distance de la superficie du filet se produit le retour en rapide au point A’.
- Si la valeur est négative, ce mouvement se réalisera en G07 (arête vive).
- Si la valeur est 0 ou positive, ce mouvement se réalisera en G05 (arête arrondie).
P7
Valeur de la passe de finition (au rayon):
- Si elle est nulle, la passe antérieure est répétée
- Si la valeur est positive, la passe de finition se réalise en maintenant l’angle
P12/2 avec l’axe X
- Si la valeur est négative, la passe de finition se réalise avec entrée radiale
P10 Pas du filetage en Z
P11 Sortie de filet. Définit à quelle distance de la fin du filetage commence la sortie. S’il est négatif, il se produit l’erreur 3. S’il est différent de zéro, le segment CB’ est un filetage conique dont le pas en Z est toujours P10. Si elle est nulle, le segment CB’ se réalise en G00.
P12 Angle de la pointe de l’outil. Il opère de manière à ce que les points de début des passes successives forment un angle P12/2 avec l’axe X.
Au moment de programmer ce cycle fixe, il faut tenir compte de ce qui suit:
1.
Les conditions d’usinage (vitesse d’avance, vitesse de rotation de la broche, etc.) doivent être programmées avant l’appel du cycle.
2.
Les paramètres peuvent être programmés dans le bloc d’appel du cycle ou dans des blocs antérieurs.
3.
Ce cycle fixe n’altère pas les paramètres d’appel, qui peuvent être utilisés pour des cycles postérieurs. Par contre il altère le contenu des paramètres P70 a P99.
4.
Les conditions de sortie sont G00,G07,G40,G90 et G97.
5.
Le cycle commence avec une approche en G00 au point A’ et termine aussi en A’.
Durant l’exécution du cycle il n’est pas possible de faire varier la vitesse d’avance F, par le commutateur FEED-RATE, dont la valeur se maintiendra fixe au 100%.
Chapitre: 8
CYCLES FIXES D'USINAGE
Section:
FILETAGE LONGITUDINAL
(G86)
Page
41
9.
SOUS-PROGRAMMES (SOUSROUTINES)
On appelle sous-programme (sousroutine) une partie de programme qui, convenablement identifiée, peut être appelée depuis un endroit quelconque d’un programme pour son exécution.
Un sous-programme (sousroutine) peut être appelé plusieurs fois depuis différents endroits d’un programme ou depuis différents programmes.
Avec un seul appel on peut répéter l’exécution d’un sous-programme (sousroutine) jusqu’à
255 fois.
Un sous-programme (sousroutine) peut être inclus dans le programme de l’utilisateur
P99996 ou bien être stocké dans le programme spécial de sous-programmes (sousroutines) de l’utilisateur P99994.
Les sous-programmes (sousroutines) paramétriques et standards sont semblables, la seule différence entre les deux est que dans le bloc d’appel dans le cas de sous-programmes
(sousroutines) paramétriques (G21 N2.2) on peut définir jusqu’à 15 paramètres.
Dans le cas de sous-programme (sousroutine) standard la définition des paramètres ne peut se faire dans le bloc d’appel.
Le nombre maximal de paramètres d’un sous-programme (sousroutine) standard ou paramétrique est 255 (P0, P254).
9.1 PROGRAMME SPECIAL DE SOUS-PROGRAMMES
(SOUSROUTINES) D’UTILISATEUR P99994
Le programme P99994 doit être élaboré dans un ordinateur et envoyé à la CNC. Il ne peut pas être modifier depuis la CNC.
Ce doit être un programme qui contienne seulement les sous-programmes d’utilisateur
élaborés en code ISO.
Si dans l’exécution du programme P99996 on effectue un appel à un sous-programme
(sousroutine), la CNC cherchera ce sous-programme (sousroutine) dans le programme
P99996 et dans le programme spécial de sous-programmes (sousroutines) P99994.
Son utilisation est conseillée lorsque l’on travaille avec plusieurs programmes d’utilisateur
P99996. De cette manière, si le programme P99994 est constitué avec tous les sousprogrammes utilisés habituellement, il ne sera pas nécessaire de les répéter dans chaque programme P99996.
Lorsque l’on dispose de sous-programme (sousroutine) associé à l’outil, paramètre machine
“P730”, il est conseillé de le stocker dans le programme P99994.
Chapitre: 9
SOUS-PROGRAMMES (SOUSROUTINES)
Section: Page
1
9.2 IDENTIFICATION D’UN SOUS-PROGRAMME STANDARD (G22)
Un sous-programme (sousroutine) standard (non paramétrique), commence toujours avec un bloc contenant la fonction G22. La structure du bloc de début de sous-programme
(sousroutine) est:
N4 G22 N2
N4 Numéro de bloc
G22 Définit le début de un sous-programme (sousroutine)
N2 Identifie le sous-programme (nombre compris entre N0 et N99).
Ce bloc ne peut pas contenir d’autre information.
A la suite du bloc de début de sous-programme, on programme les blocs que l’on désire.
Parmi les blocs programmés dans un sous-programme standard il peut y avoir des blocs paramétriques.
Un sous-programme doit toujours terminer avec un bloc de la forme: N4 G24. La fonction
G24 indique fin de sous-programme. Dans ce bloc on ne se peut programmer aucune autre information.
Exemple de programmation: N0 G22 N25
N10 X20
N15 P0=P0 F1 P1
N20 G24
Attention:
Les sous-programmes N91 a N99 ne peuvent pas être définis car la CNC les utilise.
Dans la mémoire de la CNC ne peuvent exister deux sous-programmes
(sousroutines) standards avec le même numéro d’identification, malgré qu’ils appartiennent à des programmes différents. Par contre il est possible d’identifier avec le même numéro un sous-programme (sousroutine) standard et un autre paramétrique.
9.3 APPEL A UN SOUS-PROGRAMME (SOUSROUTINE) STANDARD
(G20)
On peut appeler un sous-programme (sousroutine) standard depuis n’importe quel programme ou autre sous-programme (sousroutine) (standard ou paramétrique). L’appel à un sousprogramme (sousroutine) standard se réalise par la fonction G20. La structure d’un bloc d’appel est:
N4 G20 N2.2 N4 Numéro de bloc
G20 Appel à sous-programme (sousroutine)
N2.2 Les deux chiffres à gauche du point, identifient le numéro de sousprogramme que l’on appelle (00-99).
Les deux chiffres à droite du point, indiquent le nombre de fois que l’on va répéter le sous-programme (sousroutine) (00-99).
On peut également programmer le nombre de fois par un paramètre arithmétique, valeur comprise entre P0 et P255. Par exemple: N4 G20 N10.P123
Si on ne programme pas le nombre de fois que l’on désire répéter le sous-programme, la
CNC l’exécute une seule fois.
Dans le bloc d’appel d’un sous-programme standard, on ne peut programmer aucune autre information.
Page
2
Chapitre: 9
SOUS-PROGRAMMES (SOUSROUTINES)
Section:
SOUSROUTINE STANDARD
(G20, G22)
9.4 IDENTIFICATION D’UN SOUS-PROGRAMME PARAMETRIQUE(G23)
Un sous-programme paramétrique commence toujours par la fonction G23.
La structure du premier bloc d’un sous-programme paramétrique est:
N4 G23 N2
N4 Numéro de bloc
G23 Définit le début d’un sous-programme (sousroutine) paramétrique
N2 Identifie sous-programme (sousroutine) (nombre compris entre
N0 et N99).
Ce bloc ne peut contenir d’autre information.
A la suite du bloc de début de sous-programme, on programme les blocs que l’on désire.
Parmi les blocs programmés dans un sous-programme paramétrique il peut y avoir des blocs paramétriques.
Un sous-programme doit terminer toujours avec un bloc de la forme: N4 G24. La fonction
G24 indique fin de sous-programme. Dans ce bloc on ne peut programmer aucune autre information.
Attention:
Les sous-programmes N91 à N99 ne peuvent être définis car la CNC les utilise.
Dans la mémoire de la CNC ne peuvent exister deux sous-programmes paramétriques avec le même numéro d’identification, malgré qu’ils appartiennent
à des programmes différents. Par contre il est possible d’identifier avec le même numéro un sous-programme (sousroutine) standard et un autre paramétrique.
9.5 APPEL A UN SOUS-PROGRAMME PARAMETRIQUE (G21)
On peut appeler un sous-programme (sousroutine) paramétrique depuis n’importe quel programme ou autre sous-programme (standard ou paramétrique). L’appel à un sousprogramme paramétrique se réalise par la fonction G21. La structure d’un bloc d’appel est:
N4 G21 N2.2 P3=K±5.5 P3=K±5.5
N4 Numéro de bloc
G21 Appel à sous-programme (sousroutine)
N2.2 Les deux chiffres à gauche du point, identifient le numéro de sous-programme
(sousroutine) paramétrique que l’on appelle (00-99).
Les deux chiffres à droite du point, indiquent le nombre de fois que l’on va répéter le sous-programme paramétrique (00-99).
On peut également programmer le nombre de fois par un paramètre arithmétique, valeur comprise entre P0 et P255. Par exemple: N4 G21 N10.P123
Si on ne programme pas le nombre de fois que l’on désire répéter le sous-programme paramétrique, la CNC l’exécute une seule fois.
P3 Numéro du paramètre arithmétique (P00-P254).
K Valeur assignée au paramètre arithmétique.
Attention:
A la fin de l’exécution du sous-programme paramétrique (G24), on récupère les valeurs des paramètres assignées dans le bloc d’appel, même si tout au long du sous-programme on leur a assigné des valeurs différentes.
Chapitre: 9
SOUS-PROGRAMMES (SOUSROUTINES)
Section:
SOUSROUTINE PARAMETRIQUE
(G21,G23)
Page
3
9.6 NIVEAUX D’IMBRICATION
D’un programme principal, ou d’un sous-programme (standard ou paramétrique), on peut appeler un sous-programme, de celui-ci un second, du second un troisième, etc. ..., jusqu’à un maximum de 15 niveaux d’imbrication. Chaque niveau peut être répété 255 fois.
Diagramme d’enchaînement de sous-programmes (sousroutines)
Page
4
Chapitre: 9
SOUS-PROGRAMMES (SOUSROUTINES)
Section:
NIVEAUX D'IMBRICATIONS
10.
PROGRAMMATION PARAMETRIQUE
La CNC dispose de 255 paramètres (P0-P254) avec lesquels on peut programmer des blocs paramétriques et réaliser différents types d’opérations et sauts dans un programme. Les blocs paramétriques peuvent s’écrire à n’importe quel endroit du programme.
Les opérations que l’on peut réaliser entre paramètres sont:
F1 Somme
F2 Soustraction
F3 Multiplication
F4 Division
F5 Racine carrée
F6 Racine carrée de la somme des carrés
F7 Sinus
F8 Cosinus
F9 Tangente
F10 Arc tangente
F11 Comparaison
F12 Partie entière
F13 Partie entière plus un
F14 Partie entière moins un
F15 Valeur absolue
F16 Complément
F17 Adresse mémoire du bloc indiqué
F18 Cote X du bloc dont l’adresse est indiquée
F19 Cote Z du bloc dont l’adresse est indiquée
F20 Adresse mémoire du bloc antérieur à celui indiqué
F21 Cote I du bloc dont l’adresse est indiquée
F22 Cote K du bloc dont l’adresse est indiquée
F23 Numéro de correcteur d’outil sélectionné
F24 Valeur X de l’outil indiqué
F25 Valeur Z de l’outil indiqué
F26 Valeur F de l’outil indiqué
F27 Valeur R de l’outil indiqué
F28 Valeur I de l’outil indiqué
F29 Valeur K de l’outil indiqué
F30 Fonction logique AND
F31 Fonction logique OR
F32 Fonction logique XOR
F33 Fonction logique NOR
F34 Sans fonction
F35 Sans fonction
F36 Numéro d’outil sélectionné
Chapitre: 10
PROGRAMMATION PARAMETRIQUE
Section:
Page
1
10.1 ASSIGNATIONS
On peut assigner n’importe quelle valeur à tous les paramètres.
a) N4 P1 = P2
P1 prend la valeur de P2, tandis que P2 maintient la valeur qu’il avait.
b) N4 P1 = K1,5
P1 prend la valeur 1,5
La lettre K indique qu’il s’agit d’une constante. Les constantes admettent un rang de valeurs entre +/-99999,99999.
c) N4 P1= H (Valeur en HEXADECIMAL)
P1 prend la valeur en HEXADECIMAL indiquée après H.
Valeurs possibles de H: 0/FFFFFFFF.
d) N4 P1 = X
P1 prend la valeur de la cote théorique de l’axe X, qui se trouve à ce moment dans la
CNC.
e) N4 P1 = Z
P1 prend la valeur de la cote théorique de l’axe Z, qui se trouve à ce moment dans la
CNC.
h) N4 P1 = R
P1 prend la valeur 1 si le paramètre machine P11 (rayon / diamètre) est au rayon et la valeur 2 si est au diamètre.
i) N4 P1 = T
La CNC dispose d’une horloge interne qui mesure le temps d’exécution.
Cette fonction assigne au paramètre P1 la valeur de cette horloge à ce moment. La valeur est exprimée en centièmes de secondes.
Pour connaître le temps d' exécution de pièces ou opérations, on doit inclure des blocs de ce type au début et à la fin de la zone que l’on désire mesurer et ensuite effectuer une soustraction des valeurs obtenues.
j) N4 P1= 0X
P1 prend la valeur de la cote théorique de l’axe X, référée au zéro machine, qui se trouve dans la CNC.
l) N4 P1= 0Z
P1 prend la valeur de la cote théorique de l’axe Z, référée au zéro machine, qui se trouve dans la CNC.
Page
2
Chapitre: 10
PROGRAMMATION PARAMETRIQUE
Section:
ASSIGNATIONS
10.2 OPERATEURS “F1” à “F16”
F1 Somme
Exemple: N4 P1 = P2 F1 P3
P1 prend la valeur de la somme des paramètres P2 et P3, c’est à dire, P1 = P2 + P3.
Egalement on peut programmer, N4 P1 = P2 F1 K2 , c’est à dire, P1 prend la valeur de P2 + 2. La lettre K indique qu’il s’agit d’une constante.
Lorsque le même paramètre est additionné et donné en résultat, c’est à dire, N4 P1 =
P1 F1 K2 ceci indique qu’à partir de ce moment, P1 = P1 + 2.
F2 soustraction
N4 P10 = P2 F2 P3 ............... P10 = P2 - P3
N4 P10 = P2 F2 K3 .............. P10 = P2 - 3
N4 P10 = P10 F2 K1 ............ P10 = P10 - 1
F3 Multiplication
N4 P17 = P2 F3 P30 ............. P17 = P2 x P30
N4 P17 = P2 F3 K4 .............. P17 = P2 x 4
N4 P17 = P17 F3 K8 ............ P17 = P17x 8
F4 Division
N4 P8 = P7 F4 P35 ............... P8 = P7 : P35
N4 P8 = P2 F4 K5 ................ P8 = P2 : 5
N4 P8 = P8 F4 K2 ................ P8 = P8 : 2
F5 Racine carrée
N4 P15 = F5 P23 .................. P15 = P23
N4 P14 = F5 K9 ................... P14 = 9
N4 P18 = F5 P18 .................. P18 = P18
F6 Racine carrée de la somme des carrés
N4 P60 = P2 F6 P3 .............. P60 = P2² + P3²
N4 P50 = P40 F6 K5 ............ P50 = P40² + 5
2
N4 P1 = P1 F6 K4 ............... P1 = P1² + 4²
F7 Sinus
N4 P1 = F7 K5 ..................... P1 = Sin 5 degrés
N4 P1 = F7 P2 ...................... P1 = Sin P2
L’angle doit être en degrés, c’est à dire, P2 peut se programmer en degrés.
F8 Cosinus
N4 P1 = F8 P2 ...................... P1 = Cosinus P2
N4 P1 = F8 K75 ................... P1 = Cosinus 75 degrés
Chapitre: 10
PROGRAMMATION PARAMETRIQUE
Section:
OPERATEURS
"F1" à "F16"
Page
3
F9 Tangente
N4 P1 = F9 P2 .................... P1 = tg P2
N5 P1 = F9 K30 ................. P1 = tg 30 degrés
F10 Arc tangente
N4 P1 = F10 P2 .................. P1 = arc. tg P2 (résultat en degrés).
N4 P1 = F10 K0,5 .............. P1 = arc. tg 0,5
F11 Comparaison
Compare un paramètre avec autre ou avec une constante, et active les indicateurs de sauts conditionnels (son utilité sera expliquée dans l’aparté de sauts conditionnels, G26,
G27, G28, G29).
N4 P1 = F11 P2
Si P1 = P2, active l’indicateur de saut si zéro.
Si P1 est égal ou supérieur à P2, active l’indicateur de saut si supérieur ou égal.
Si P1 est inférieur à P2, active l’indicateur de saut si inférieur.
Egalement on peut programmer N4 P1 = F11 K6
F12 Partie entière
N4 P1=F12 P2 .................... P1 prend la valeur de la partie entière de P2.
N4 P1=F12 K5,4 ................ P1 = 5
F13 Partie entière plus un
N4 P1 = F13 P2 .................. P1 prend la valeur de la partie entière de P2 plus 1.
N4 P1 = F13 K5,4 .............. P1 = 5 + 1 = 6
F14 Partie entière moins un
N4 P1 = F14 P27 ................ P1 prend la valeur de la partie entière de P27 moins un
N4 P5 = F14 K5,4 .............. P5 = 5 - 1 = 4
F15 Valeur absolue
N4 P1 = F15 P2 .................. P1 prend la valeur absolue de P2
N4 P1 = F15 K-8 ................ P1 = 8
F16 Complémentation
N4 P7 = F16 P20........P7 prend la valeur de P20 complémenté, c’est à dire, P7 = -P20
N4 P7 = F16 K10 ............... P7 = -10
Page
4
Chapitre: 10
PROGRAMMATION PARAMETRIQUE
Section:
OPERATEURS
"F1" à "F16"
10.3 OPERATEURS “F17” à “F29”
Ces fonctions n’affectent pas les indicateurs de saut.
F17
N4 P1 = F17 P2
P1 prend la valeur de l’adresse mémoire du bloc dont le numéro est P2.
Exemple N4 P1 = F17 K12 P1 prend la valeur de l’adresse mémoire où se trouve le bloc N12.
F18
N4 P1=F18 P2
P1 prend la valeur de la cote X qui apparaît dans le bloc dont l’adresse est P2.
F18 n’accepte pas d’opérande constant. Exemple : P1 = F18 K2 N’est pas valide.
F19
N4 P1=F19 P2
P1 prend la valeur de la cote Z qui apparaît dans le bloc dont l’adresse est P2.
F19 n’accepte pas d’opérande constant. Exemple : P1 = F19 K2 N’est pas valide.
F20
N4 P1 = F20 P2
P1 prend la valeur de l’adresse mémoire du bloc antérieur à celui défini par l’adresse
P2.
F20 n’accepte pas d’opérande constant. Exemple : P1 = F20 K2 N’est pas valide.
F21
N4 P1=F21 P2
P1 prend la valeur de la cote I qui apparaît dans le bloc dont l’adresse est P2.
F21 n’accepte pas d’opérande constant. Exemple : P1 = F21 K2 N’est pas valide.
F22
N4 P1=F22 P2
P1 prend la valeur de la cote I qui apparaît dans le bloc dont l’adresse est P2.
F22 n’accepte pas d’opérande constant. Exemple : P1 = F22 K2 N’est pas valide.
F23
N4 P1 = F23
Le paramètre P1 prend le numéro de l’outil avec lequel on opère à cet instant.
F24
Cette fonction peut se programmer de deux manières distinctes:
N4 P9=F24 K2 Le paramètre P9 prend la valeur de X que se trouve, dans la table d’outils, à la position 2.
N4 P8=F24 P12 Le paramètre P8 prend la valeur de X que se trouve, dans la table d’outils, à la position indiquée par la valeur du paramètre P12.
Chapitre: 10
PROGRAMMATION PARAMETRIQUE
Section:
OPERATEURS
"F17" à "F29"
Page
5
F25
Cette fonction peut se programmer de deux manières distinctes:
N4 P15=F25 K16 Le paramètre P15 prend la valeur de Z qui se trouve, dans de la table d’outils, à la position 16.
N4 P13=F25 P34 Le paramètre P13 prend la valeur de Z qui se trouve, dans la table d’outils, à la position indiquée par la valeur du paramètre P34.
F26
Cette fonction peut se programmer de deux manières distinctes:
N4 P6=F26 K32 Le paramètre P6 prend la valeur de F qui se trouve, dans la table d’outils, à la position 32.
N4 P14=F26 P15 Le paramètre P14 prend la valeur de F qui se trouve, dans la table d’outils, à la position indiquée par la valeur du paramètre P15.
F27
Cette fonction se peut programmer de deux manières distinctes:
N4 P90=F27 K13 Le paramètre P90 prend la valeur de R qui se trouve, dans la table d’outils, à la position 13.
N4 P28=F27 P5 Le paramètre P28 prend la valeur de R qui se trouve, dans la table d’outils, à la position indiquée par la valeur du paramètre P5.
F28
Cette fonction peut se programmer de deux manière distinctes:
N4 P17=F28 K10 Le paramètre P17 prend la valeur de I qui se trouve, dans la table d’outils, à la position 10.
N4 P19=F28 P63 Le paramètre P19 prend la valeur de I qui se trouve, dans la table d’outils, à la position indiquée par la valeur du paramètre P63.
F29
Cette fonction peut se programmer de deux manières distinctes:
N4 P15=F29 K27 Le paramètre P15 prend la valeur de K qui se trouve, dans la table d’outils, à la position 27.
N4 P13=F29 P25 Le paramètre P13 prend la valeur de K qui se trouve, dans la table d’outils, à la position indiquée par la valeur du paramètre P25.
Dans un même bloc, on peut introduire toutes les assignations et opérations que l’on désire, tant que l’on ne modifie pas un nombre de paramètres supérieur à 15.
Page
6
Chapitre: 10
PROGRAMMATION PARAMETRIQUE
Section:
OPERATEURS
"F17" à "F29"
10.4 OPERATEURS BINAIRES “F30” A “F33”
Les opérations binaires dont on dispose sont:
F30
F31
F32
F33
Fonction logique AND
Fonction logique OR
Fonction logique XOR
Fonction logique NOR
Ces opérations BINAIRES, activent également les indicateurs internes (FLAGS), suivant la valeur du résultat, pour leur utilisation postérieure dans la programmation des SAUTS/
APPELS CONDITIONNELS (G26, G27, G28, G29).
Les opérations binaires peuvent se réaliser entre:
Paramètres
Paramètres et constantes
Constantes
P1 = P2 F30 P3
P11 = P25 F31 H(8)
P19 = K2 F32 K5
La valeur de la constante H doit être en code hexadécimal, entiere, positive et de 8 caractères maximaux, c’est à dire, peut être comprise entre 0 et FFFFFFFF et ne peut faire partie du premier opérande.
F30 Fonction logique AND
Exemple: N4 P1= P2 F30 P3 Valeur de P2 Valeur de P3 Valeur de P1
A5C631F C883D C001D
F31 Fonction logique OR
Exemple: N4 P11= P25 F31 H35AF9D01
Valeur de P25 Valeur de H Valeur de P11
48BE6 35AF9D01 35AF9FE7
F32 Fonction logique XOR
Exemple: N4 P19= P72 F32 H91C6EF
Valeur de P72 Valeur de H Valeur de P19
AB456 91C6EF 9B72B9
F33 Fonction logique NOT
Exemple: N4 P154= F33 P88 P154 prend la valeur de P88 en complément à 1.
Valeur de P88 Valeur de P154
4A52D63F B5AD29C0
10.5 OPERATEUR “F36”
Cette fonction n’affecte pas les indicateurs de saut.
F36
N4 P1 = F36
Le paramètre P1 prend le numéro de l’outil en cours.
Chapitre: 10
PROGRAMMATION PARAMETRIQUE
Section:
OPERATEURS
"F30" à"F33" et "F36"
Page
7
10.6 FONCTIONS DE SAUT CONDITIONNELS (G26, G27, G28, G29)
Sont similaires à la fonction G25 (saut inconditionnel) qui est détaillée au chapitre
“Fonctions Préparatoires Additionnelles” de ce même manuel.
Les fonctions G26, G27, G28 et G29, avant d’effectuer le saut de bloc ou exécuter la partie de programme indiquée, vérifient que la condition requise s’est produite.
G26 Saut si zéro.
G27 Saut si différent zéro.
Requiert la condition de “Zéro” soit vraie.
Requiert la condition de “Zéro” ne soit pas vraie.
G28 Saut si inférieur que zéro.
Requiert que soit vraie la condition de “Inférieur”
G29 Saut si supérieur ou égal a zéro. Requiert que ne soit pas vraie la condition de
“Inférieur”.
La condition de “Zéro”, aussi appelée égalité, est activée dans les cas suivants.
* Lorsque le résultat d’une opération est égal à zéro.
Exemple: N001 P1 = P3 F2 K5 La condition zéro est remplie si P3 = 5
* Si dans une comparaison les deux termes sont égaux.
Exemple: N002 P1 F11 K8 La condition zéro est remplie si P1 = 8
La condition de “Inférieur”, aussi appelée négative, elle s’active dans les cas suivants:
* Lorsque le résultat d’une opération est inférieur à zéro (négatif).
Exemple: N001 P1 = P3 F2 K5 La condition zéro est remplie si P3 est inférieur
à 5
* Si dans une comparaison, le premier opérande est inférieur au second.
Exemple: N002 P1 F11 K8 La condition est remplie si P1 est inférieur à 8
Attention:
Les assignations et les fonctions non paramétriques n’altèrent pas l’état des indicateurs de condition.
Exemple de programmation: N060 P2 F11 K22
N065 G01 X10
N070 Y20
N071 G26 N100
N072 G28 N200
N073 G29 N300
Dans le bloc N060 s’effectue une comparaison.
Les blocs N65 et N70 n’altèrent l’état des indicateurs de condition.
Ainsi, si P2 vaut 22, le programme continuera au bloc N100
Si P2 vaut moins que 22, le programme continuera au bloc N200
Si P2 vaut plus que 22, le programme continuera au bloc N300
Il faut faire attention au moment de la programmation des fonctions G26 et G29. Si dans l’exemple antérieur on avait programmé: N071 G28 N200
N072 G29 N300
N073 G26 N100
Le programme n’exécuterait pas le bloc N073. Avec P2 inférieur à 22 le programme continue en N200 et avec P2 supérieur ou égal à 22 il continue en N300.
Page
8
Chapitre: 10
PROGRAMMATION PARAMETRIQUE
Section:
FONCTIONS DE SAUT
(G26, G27, G28, G29)
Exemple de programmation paramétrique pour le calcul des coordonnées des points qui composent une parabole. La programmation de l’axe X est au diamètre.
La formule qui définit une parabole est:
Z = - K X
2
Avec:
P0 = K
P4 = X
P5 = Z
Les paramètres d’appel sont:
P0 = K
P1 = Cote X initial
P2 = Cote X final
P3 = Incrément en X.
Programme:
N0080 G21 N56.1 P0=K0,01 P1=K00 P2=K100 P3=K1.........Appel à sous programme
N0090 M30 ............................................................................ Fin de programme
N0110 G23 N56 .......................................Définition de sous programme
N0120 P4=P1 ...........................................X=X initial
N0130 P4=P4 F1 P3 P4=F11 P2 .............Compare la nouvelle cote X avec X final
N0140 G28 N160 .....................................Si inférieur, continue en N160
N0150 P4=P2 ...........................................Si supérieur, nouvelle cote X = X final
N0160 P5=P4 F3 P4 P5=P5 F3 P0
P5=F16 P5 .................................................Calcule la nouvelle cote Z
N0170 G01 XP4 ZP5 ...............................Déplacement à la nouvelle cote (X, Z)
N0180 P4=F11 P2 ....................................Compare nouvelle cote X avec X final
N0190 G27 N130...................................Si inférieur calcule un autre point, va à N130
N0200 G24 ...............................................Fin de sous programme
Chapitre: 10
PROGRAMMATION PARAMETRIQUE
Section:
FONCTIONS DE SAUT
(G26, G27, G28, G29)
Page
9
EXEMPLE
N00 G95 F10 S1000 M03
N05 G0 X80 Z50
N06 T1.1
N10 P22=K0 P23=K0 P26=0
;Conditions d’usinage
;Va au point de changement
;Sélectionne outil 1
;Il n’y a pas de passe de finition
N20 P100=K44 P101=K-135 P4=K1 P6=K38 P7=K15 P10=K4 P18=K3 P19=K1 P20=K136
N25 G67 N2 ;Cylindrage conique
N30 P16=K0 P100=K38 P101=K-125 P4=K1 P9=K3 P10=K4 P15=K0 P18=K3 P19=K1 P20=K126
N35 G67 N4 ;Arrondi
N40 P16=K0 P100=K32 P101=K-124 P4=K1 P9=K1 P10=K4 P15=K1 P18=K3 P19=K1 P20=K126
N45 G67 N4 ;Arrondi
N40 P100=K30 P101=K-98 P4=K1 P6=K28 P7=K100 P10=K4 P18=K3 P19=K1 P20=K99
N45 G67 N2 ;Cylindrage conique
N50 P100=K28 P101=K-70 P4=K1 P6=K24 P7=K100 P10=K4 P18=K3 P19=K1 P20=K71
N55 G67 N2 ;Cylindrage conique
N60 P100=K24 P101=K-27 P4=K1 P6=K19 P7=K6.41 P10=K4 P18=K3 P19=K1 P20=K28
N65 G67 N2 ;Cylindrage conique
N70 P100=K19 P101=K0 P102=K19 P103=K-27 P4=K1 P6=K17 P19=K1 P20=K1
N75 G67 N0 ;Cylindrage
N80 P100=K17 P101=K0 P102=K17 P103=K-17 P4=K1 P6=K16 P19=K1 P20=K1
N85 G67 N0 ;Cylindrage
N90 P100=K16 P101=K0 P4=K1 P6=K14 P7=K100 P10=K4 P18=K2 P19=K13 P20=K1
N95 G67 N2 ;Cylindrage conique
N100 G0 X80 Z50
N101 T2.2
N105 P12=K2 P13=K0.5
;Va au point de changement
;Sélectionne outil 2
;Largeur et temporisation
N110 P100=K28 P101=K-85 P102=K28 P103=K-87 P4=K1.7 P6=K26.5 P19=K8 P20=K0
N115 G67 N5 ;Rainurage
N120 P100=K16 P101=K-15 P102=K17 P103=K-17 P6=K14 P19=K0.5 P20=K0.5
N125 G67 N5 ;Rainurage
N130 G0 X80 Z50
N131 T3.3
;Va au point de changement
;Sélectionne outil 3
N140 P4=K0.7 P11=K0 P16=K0 P128=K0 ;Pas, filetage extérieur, angle
N141 P100=K28 P101=K-70 P102=K28 P103=K-86 P8=K1.5 P14=K0.919 P19=K8 P20=K1
N145 G67 N3 ;Filetage
N150 P4=K0.7 P11=K0 P16=K0 P128=K0 ;Passe, filetage extérieur, angle
N151 P100=K16 P101=K0 P102=K16 P103=K-16 P8=K1 P14=K0.613 P19=K15 P20=K1
N155 G67 N3 ;Filetage
N160 G0 X80 Z50
N170 M30
;Va au point de retrait
Fin de programme
CODES
D'ERREUR
022
023
025
026
013
014
015
016
017
018
019
005
006
007
008
001
002
003
004
009
010*
011
012
020
021
Cette erreur se produit si le premier caractère d'un bloc n'est pas "N"
Trop de digits pour définir une fonction
On a donné une valeur incorrecte à un paramètre de cycle fixe.
Définition d'un cycle fixe alors que une des fonctions G02, G03 ou G33 est active.
Bloc paramétrique mal programmé.
Plus de dix paramètres affectés à un même bloc
Division par zéro.
Racine carrée d'un nombre négatif.
On a assigné une valeur trop grande à un paramètre.
La gamme ou la vitesse de coupe constante n'ont pas été programmées
Plus de dix fonctions M dans un bloc.
Cette erreur se produit dans les cas suivants:
> Fonction G50 mal programmée
> Dépassement des valeurs de dimensions d'outil
> Dépassement des valeurs des transferts d'origine G53/G59
Profil d'un cycle mal défini
On a programmé un bloc incorrect soit incompatible avec le déroulement du programme à ce moment
Les fonctions G20,G21........G32, G50, G53........G59, G72, G74, G92 et G93 doivent être seules dans un bloc.
Il n'existe pas le bloc ou la sous routine appelés ou le bloc appelé par la fonction F17 n'existe pas.
Pas de filetage négatif ou trop élevé.
Erreur dans un bloc où les points sont définis par angle-angle ou angle-coordonnée.
Cette erreur se produit dans les cas suivants:
> Après avoir défini G20, G21, G22 ou G23 le numéro de la sous routine n'est pas indiqué.
> Le caractère "N" n'est pas programmé après G25, G26, G27, G28 ou G29.
> Trop de niveaux d'imbrication.
On a défini plus d'une gamme de broche dans un même bloc.
Cette erreur se produit dans les cas suivants:
> Il n'existe pas de bloc à l'adresse définie par le paramètre assigné à F18, F19, F20, F21, F22.
> On n'a pas défini l'axe correspondant dans le bloc adressé.
En programmant les axes en G74 l'un d'eux est répété.
K n'a pas été programmé après G04.
Erreur dans un bloc de définition ou d'appel à sous routine, ou de saut conditionnels.
Cette erreur se produit dans les cas suivants:
> Dépassement de capacité mémoire.
> Capacité de bande libre ou de mémoire de CNC inférieure à la taille du programme que l’on essaie
d’introduire.
027
028
029
030
031
I ou K n'ont pas été définis dans une interpolation circulaire ou un filetage.
On a essayé de sélectionner un correcteur supérieur à 32 dans la table d’outils ou un outil externe inexistant (le nombre d’outils se défini par paramètre-machine).
.
On a assigné une valeur trop grande à une fonction.
Cette erreur se produit avec une grande fréquence si on programme une valeur de F en mm. / min. et ensuite on passe en mm./ tours. sans changer la valeur de F.
On a programmé une fonction G inexistante
Valeur du rayon d’outil trop grande.
032 Valeur du rayon d’outil trop grande.
033
.
034
035
036
037
038
039
040
On a programmé un déplacement supérieur à 8388 mm ou 330,26 pouces.
Exemple: Si l'axe Z se trouve à Z -5000 et ou veut aller à z 5000 la CNC affichera l'erreur 33 si on programme le bloc N10 Z 5000, car le déplacement est de 10000 mm.
Par contre si l'on programme en deux fois l'erreur 33 ne sera pas affichée car chaque déplacement sera inférieur à 8388 mm
N10 Z0 ;Déplacement de 5000 mm
N20 Z 500 ;Déplacement de 5000 mm
On a défini S ou F avec une valeur supérieure à celle permise.
Informations insuffisantes pour compenser, pour arrondir des arêtes ou chanfreiner.
Sous routine répétée.
M19 mal programmé
G72 mal programmé.
Il faut tenir compte que si l'on applique la fonction G72 sur un seul axe celui-ci doit être à l'origine pièce( valeur zéro) au moment d'appliquer le facteur échelle.
Cette erreur se produit dans les cas suivants:
> Plus de 15 niveaux d'imbrication dans l'appel des sous routines.
> On a programmé un bloc qui contient un saut sur lui-même ex: N120 G25 N120
L'arc programmé ne passe pas par le point final défini (tolérance 0.01) ou il n'existe pas d'arc passant par les points définis à l'aide de G08, G09.
041 Cette erreur se produit lorsque l'on a programmé une entrée tangentielle. Deux cas possibles:
> Il n'existe pas assez d'espace pour réaliser l'entrée tangentielle. Un espace supérieur ou équivalent
à 2 fois le rayon d'arrondi programmé.
042
> La partie où a été définie l'entrée tangentielle est une courbe G02, G03. Cette partie doit être une droite G01.
Cette erreur se produit lorsque l'on a programmé une sortie tangentielle; Deux cas possibles:
> Il n'existe pas assez d'espace pour réaliser la sortie tangentielle. Un espace supérieur ou équivalent
à 2 fois le rayon d'arrondi programmé.
047
048
049
050
043
044
045
046
054
055
057
058
059
060
061
> La partie où a été définie l'entrée tangentielle est une courbe G02, G03. Cette partie doit être une droite G01.
Origine des coordonnées polaires mal définie (G93).
M45 S mal programmée (vitesse de rotation de l'outil motorisé)
G36, G37, G38 ou G39 mal programmées.
Coordonnées polaires mal définies.
On a programmé un déplacement zéro durant une compensation de rayon ou d’arrondi.
Début ou annulation de compensation de rayon avec G02/G03.
Chanfrein mal programmé.
On a sélectionné la vitesse de coupe constante quand la machine dispose de sortie de consigne de broche en format BCD.
Il n’y pas de disquette ou pas de bande dans le lecteur utilisé.
Erreur de parité en écriture ou en lecture de disquette
Disquette protégée en écriture
Difficultés de rotation de la disquette
Cette erreur se produit dans les cas suivants:
> Erreur de dialogue entre la C.N.C. et le lecteur de disquettes FAGOR
> Erreur de dialogue entre la C.N.C. et le lecteur de bandes FAGOR
Défaillance du circuit interne de la CNC. Consulter le service d’Assistance Technique.
Défaillance de batterie.
Au moment où se produit cette erreur, les informations contenues en mémoire seront conservées durant
10 jours de plus, la CNC éteinte. Il faudra changer le module batterie situé à la partie postérieure de l’appareil. Consulter le Service d’Assistance Technique.
Attention:
Etant donné le risque d’explosion ne pas essayer de recharger la pile ne pas l’exposer à des températures supérieures à 100 ºC et ne pas court-circuiter les bornes.
064*
065*
066*
068*
L’entrée arrêt d’urgence externe (terminal 14 du connecteur I/O 1) est activée.
Cette erreur se produit si, lorsque l'on travaille avec le palpeur (G75), on atteint la position programmée sans avoir reçu le signal du palpeur
Limite de course axe X dépassée.
L’erreur est générée, soit que la machine est hors des limites ou bien que l’on veut effectuer un déplacement qui obligerait la machine à sortir des limites.
Limite de course axe Z dépassée.
L’erreur est générée, soit que la machine est hors des limites ou bien que l’on veut effectuer un déplacement qui obligerait la machine à sortir des limites
070** Erreur de poursuite sur l’axe X
072** Erreur de poursuite sur l’axe Z.
074** Valeur de S (vitesse de broche) trop élevée.
075** Erreur de mesure sur l’axe X. Connecteur A1.
076** Erreur de mesure connecteur A2.
077** Erreur de mesure sur l’axe Z. Connecteur A3.
078** Erreur de mesure connecteur A4.
079** Erreur de mesure de broche. Connecteur A5.
087** Défaillance du circuit interne de la CNC. Consulter le service d’Assistance Technique
088** Défaillance du circuit interne de la CNC. Consulter le service d’Assistance Technique.
089 * La recherche des points de référence machine n’a pas été effectuée sur tous les axes.
Cette erreur se produit quand il est obligatoire de faire la recherche des points de référence après allumage de la CNC. Elle est rendue obligatoire par un paramètre machine.
090** Défaillance du circuit interne de la CNC. Consulter le service d’Assistance Technique.
091** Défaillance du circuit interne de la CNC. Consulter le service d’Assistance Technique.
092** Défaillance du circuit interne de la CNC. Consulter le service d’Assistance Technique.
093** Défaillance du circuit interne de la CNC. Consulter le service d’Assistance Technique.
094 Erreur de parité de la table des outils ou la table des origines (G53-G59).
095** Erreur de parité de paramètres généraux.
096** Erreur de parité des paramètres de l’axe Z.
098** Erreur de parité des paramètres de l’axe X.
099** Erreur de parité de la table des M décodées.
100** Défaillance du circuit interne de la CNC. Consulter le service d’Assistance Technique.
101** Défaillance du circuit interne de la CNC. Consulter le service d’Assistance Technique.
105 Cette erreur se produit dans les cas suivants:
> Plus de 43 caractères de commentaire.
> Plus de 5 caractères pour définir un numéro de programme
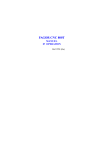
Link pubblico aggiornato
Il link pubblico alla tua chat è stato aggiornato.