Nouvelles prestations
(9902fra)
Version 5.2 (Marz 1996)
1. P621(4). FACTEUR DIVISEUR DES SIGNAUX DES VOLANTS ÉLECTRONIQUES
Le paramètre P621(4) s'utilise en même temps avec les paramètres P602(4) et P621(5) qui indiquent le facteur multiplicateur des signaux du volant électronique du 1 er et 2 ème axe respectivement.
Le paramètre P621(4) indique si sont divisés ou non les signaux de tous les volants électroniques.
P621(4)=0
P621(4)=1
Ne sont pas divisés.
Les signaux de tous les volants sont divisés par 2.
Exemples dans l'axe X pour que la CNC assume 100 impulsions/tour avec codeurs à 25, 50 et 100 impulsions/tour, il faut:
Volant Fagor à 25 impulsions/tour:
Volant Fagor à 50 impulsions/tour:
Volant Fagor à 100 impulsions/tour:
P602(4)=0 et P621(4)=0 25 x 4 / 1 = 100 impulsions/tour.
P602(4)=1 et P621(4)=0 50 x 2 / 1 = 100 impulsions/tour.
P602(4)=1 et P621(4)=1 100 x 2 / 2 = 100 impulsions/tour.
Version 5.6 (Juin 1996)
1. DÉPLACEMENT AVEC VOLANT PRINCIPAL
Cette prestation permet, une fois la trajectoire définie, de gouverner les déplacements de la machine au moyen du Volant
Principal.
Conditions requises:
Le contrôle du "Déplacement avec Volant Principal" se fait avec le Deuxième Volant, la machine devant donc être munie de deux volants et ne peut être munie de manivelles.
Personnalisation:
Le paramètre machine "P622(6)" indique si l’on dispose de la prestation "Déplacement avec Volant Principal"
P622(6) = 0
P622(6) = 1
On ne dispose pas de cette prestation
On dispose de la prestation "Déplacement avec Volant Principal"
Le contrôle du "Déplacement avec Volant Principal" se fait avec le Deuxième Volant, la machine devant donc être munie du
Premier Volant et ne peut être munie de manivelles, c’est-à-dire, que:
P621(7)=1
P622(3)=0
P609(1)=0
La machine n’est pas munie de manivelles
On dispose de 2 volants
Le premier volant électronique n’est pas le FAGOR 100P
Le raccordement du "Volant Principal" se fait à travers le connecteur A4. Il admet un signal sinusoïdal et un signal carré différentiel, les paramètres machine suivants devant être personnalisés:
P621(6)
P621(3)
P621(1,2)
P621(5)
Sens de comptage du "Volant Principal"
Unités de mesure du "Volant Principal"
Résolution de comptage du "Volant Principal"
Facteur de multiplication des signaux du "Volant Principal"
Sélection:
a) Modèles CNC-800TI et CNC-800TGI. À partir du PLCI.
Une fois tous les paramètres machine personnalisés, il faut utiliser la sortie O39 du PLCI pour activer ou désactiver la prestation
"Déplacement avec Volant Principal".
Paramètre P622(6) Sortie PLCI O39 Prestation "Déplacement avec Volant Principal"
P622(6) = 0
P622(6) =1
P622(6) =1
-----
O39 = 0
O39 =1
La prestation n'est pas disponible
Prestation inactivée
Prestation activée
- 2 -
b) Modèles CNC-800T et CNC-800TG. En utilisant le terminal 11 du connecteur I/O 1.
Une fois tous les paramètres machine personnalisés, il faut utiliser l’entrée "Déplacement avec Volant Principal", terminal 11 du connecteur I/O 1 pour activer ou désactiver la prestation "Déplacement avec Volant Principal".
Paramètre P622(6)
P622(6) = 0
P622(6) =1
P622(6) =1
Pin 11 I/O1
-----
Pin 11 = 0Vdc
Pin 11 = 24Vdc
Prestation "Déplacement avec Volant Principal"
La prestation n'est pas disponible
Prestation inactivée
Prestation activée
Fonctionnement de base. (P622(6)=1, O39=1)
a) La machine étant à l’arrêt.
Le premier volant est le seul à être activé, le deuxième volant (Volant Principal) ne marche pas.
On ne peut donc déplacer que l’axe X au moyen des volants.
b) La machine étant en route (CNC en cours d’exécution).
Les axes ne commencent à se déplacer qu’au moment où on fait tourner le Volant Principal.
La vitesse d’avance des axes dépend de la vitesse de rotation du Volant Principal.
Si le volant s’arrête, la machine s’arrête elle aussi.
Si l’on inverse le sens de rotation du Volant Principal, la CNC inverse le sens du déplacement (Fonction Retour d’un seul bloc).
c) La prestation "Déplacement avec Volant Principal" peut être utilisée avec n’importe quel type d’exécution, qu’il s’agisse d’un cycle, d’un programme ISO, d’un Chanfrein, etc ...
Normalement, la CNC étant en cours d’exécution, le premier volant ne marche pas, sauf durant l’exécution en mode demiautomatique des opérations automatiques "Chariotage Conique" et "Arrondi".
Dans ces deux opérations semi-automatiques, le Volant Principal contrôle l’avance de la trajectoire et le Premier Volant déplacera l’axe X.
Prestation "Déplacement avec Volant Principal" désactivée (P622(6)=1, O39=0)
Lorsque la prestation "Déplacement avec Volant Principal" est désactivée, sortie O39 du PLC =0, les volants agissent comme jusqu’à présent.
2. REPRÉSENTATION GRAPHIQUE DURANT L’EXÉCUTION
Jusqu’à présent, la CNC 800T permettait de réaliser une vérification graphique (simulation graphique) avant l’exécution.
À partir de maintenant, il est aussi possible d’afficher graphiquement la trajectoire d’usinage au cours de la phase d’exécution.
Conditions requises
Pour pouvoir utiliser cette application, il faut disposer du modèle CNC-800TG ou CNC-800TGI, car il s’agit de la présentation graphique.
Fonctionnement
Lors de l’exécution d’une Opération Automatique, d’un Programme Pièce, du Programme ISO en mode Automatique ou Bloc
à Bloc, il est possible d’afficher sur l’écran la trajectoire d’usinage durant la phase d’exécution.
Pour ce faire, une fois l’exécution commencée, on peut taper sur les touches suivantes:
Touche «4» La CNC affiche l’écran de représentation graphique.
Touche «3» La CNC affiche les Coordonnées Commande, Actuel, Reste et sur la partie supérieure, les valeurs des paramètres Arithmétiques.
Touche «2» La CNC affiche l’Erreur de Poursuite en gros caractères.
Touche «1» La CNC affiche la Position Actuelle en gros caractères.
Touche «0» La CNC retourne à l’écran standard.
- 3 -
3. ZONE DE TRAVAIL / ZONE D’EXCLUSION
Cette prestation permet, une fois la zone définie, de la sélectionner à partir du PLCI comme zone de travail ou comme zone d’exclusion.
Conditions requises:
Pour pouvoir utiliser cette prestation, il faut disposer du modèle CNC-800TI ou CNC-800TGI, car les sorties O46 et O47 du
PLCI sont utilisées pour sélectionner la zone comme zone de travail ou bien comme zone d’exclusion.
Personnalisation:
Le paramètre machine "P622(5)" indique si la CNC permet de sélectionner une zone comme zone de travail ou comme zone d’exclusion.
P622(5) = 0On ne dispose pas de cette prestation
P622(5) = 1On dispose de cette prestation.
Lorsque l’on dispose de cette prestation "P622(5)=1", il faut utiliser les paramètres machine suivants pour définir ce qui va être la zone de travail ou la zone d’exclusion.
P902 Coordonnée X plus positive
P903 Coordonnée X moins positive
P904 Coordonnée Z plus positive
P905 Coordonnée Z moins positive
Pour que la CNC puisse assimiler les valeurs assignées à ces paramètres, il faut éteindre et rallumer la CNC.
Sélection:
Une fois tous les paramètres machine personnalisés, il faut utiliser les sorties O46 et O47 du PLCI pour sélectionner la zone comme zone de travail ou comme zone d’exclusion.
Sortie PLCI
046
O46 = 0
O46 = 0
Sortie PLCI
047
O47 = 0
O47 = 1
O46 = 1 O47 = 0
O46 = 1 O47 = 1
Fonctionnement de base. "P622(5)=1"
Prestation "Zone de Travail / Zone d’Exclusion"
Prestation inactivée
Zone activée comme Zone de Travail
(il n’est pas possible d’en sortir)
Zone activée comme Zone d’Exclusion
(il n’est pas possible d’y entrer)
Prestation inactivée
La CNC, lors de l’allumage, assimile comme zone sélectionnée celle qui est définie au moyen des paramètres machine "P902,
P903, P904 et P905".
Il est néanmoins possible de modifier les valeurs en question à partir du programme, en assignant les nouvelles dimensions aux paramètres arithmétiques:
P206
P207
P208
P209
Coordonnée X plus positive
Coordonnée X moins positive
Coordonnée Z plus positive
Coordonnée Z moins positive
La CNC assimile ces nouvelles valeurs mais ne modifie pas les paramètres machine "P902, P903, P904 et P905".
Il faut en outre tenir compte du fait que lors de l’allumage, la CNC assimilera de nouveau les valeurs définies par les paramètres machine.
La zone sélectionnée pourra être activée comme zone de travail ou comme zone d’exclusion à partir du PLCI, en utilisant les sorties O46 et O47, tel qu’il a été dit plus haut.
Lorsqu’elle est sélectionnée comme Zone de Travail, la CNC agit de la manière suivante:
.
Durant les déplacements avec JOG ou Volant, elle ne permet pas de sortir de cette zone.
.
Si l’on essaie d’en sortir en cours d’exécution, elle affiche une erreur 67 "Erreur limites X, Z"
Lorsqu’elle est sélectionnée comme Zone d’Exclusion, la CNC agit de la manière suivante:
.
Durant les déplacements avec JOG ou Volant, elle ne permet pas d’entrer dans cette zone.
.
Si l’on essaie d’y entrer en cours d’exécution, elle affiche une erreur 67 "Erreur limites X, Z"
- 4 -
4. CHANGEURS DE GAMME MANUELS
Fonctionnement jusqu’à cette version
Si on désire faire le changement de gamme manuellement, il faut personnaliser le paramètre machine "P601(1)" avec la valeur
"0".
Lorsque la nouvelle vitesse de broche "S" sélectionnée implique un changement de gamme, la CNC affichera un message indiquant la gamme à sélectionner.
L’Utilisateur doit mener les opérations suivantes:
1 Arrêter la broche.
2 Changer manuellement de gamme
3 Restaurer la rotation de la broche
4 Taper sur la touche [ENTER]
La CNC poursuit l’exécution.
Fonctionnement à partir de cette version
Si on désire faire le changement de gamme manuellement, il faut personnaliser le paramètre machine "P601(1)" avec la valeur
"0".
Lorsque la nouvelle vitesse de broche "S" sélectionnée implique un changement de gamme, la CNC arrête la broche et indique la gamme à sélectionner.
L’Utilisateur doit mener les opérations suivantes:
1. Changer manuellement de gamme
2. Taper sur la touche [ENTER]
La CNC restaure la rotation de la broche et poursuit l’exécution.
5. COMPENSATION DU JEU DE VIS VARIABLE
Jusqu’à présent, la CNC 800T ne tenait compte que d’un seul jeu de vis.
À partir de maintenant, il est aussi possible de corriger des mesures lorsque le jeu d’inversion de vis est variable selon la zone où se trouve la machine.
Conditions requises
Les tables de compensation des jeux de vis se transforment. Elles sont à présent utilisées pour compenser l’erreur des jeux de vis et l’erreur variable des jeux de vis (les deux à la fois).
Personnalisation
Les paramètres machine "P622(7)" et "P622(8)" indiquent si on dispose de cette prestation.
P622(7) = 0
P622(7) = 1
P622(8) = 0
P622(8) = 1
On ne dispose pas de cette prestation sur l’axe Z.
On dispose de cette prestation sur l’axe Z.
On ne dispose pas de cette prestation sur l’axe X.
On dispose de cette prestation sur l’axe X.
Chaque fois que l’on travaille avec la prestation "Jeu de Vis Variable", il faut sélectionner la compensation d’erreur de jeux de vis de l’axe correspondant.
P605(2) = 0
P605(1) = 0
Compensation d’erreur de jeu de vis de l’axe X (0=Non, 1=Oui)
Compensation d’erreur de jeu de vis de l’axe Z (0=Non, 1=Oui)
- 5 -
Définition de la table
Les 15 premiers points de la table sont utilisés pour le sens positif et les 15 autres pour le sens négatif.
Lorsque l’on désire corriger l’erreur de vis, le jeu de vis est la différence existant entre les deux courbes.
Jeu
Sens positif
Coordonnée
Sens négatif
Lorsque l’on ne désire pas corriger l’erreur de vis, une des tables aura la valeur 0 et l’autre courbe sera le jeu de vis.
Jeu
Sens positif
Coordonnée
Sens négatif
Notes:
Les deux parcours doivent respecter toutes les conditions requises des tables de compensation de jeu de vis.
Une des conditions établit que le point de référence machine doit toujours avoir la valeur 0.
Si la vis a du jeu sur le point de référence machine, il faut assigner la valeur en question au paramètre machine P109 ou
P309 (Jeu de vis sur l’axe X ou Z) et décaler de cette quantité tous les points de la table.
Exemple:
Jeu
Sens positif
Coordonnée
Sens négatif
Jeu
Coordonnée
Fonctionnement:
Lorsque l’on dispose de la prestation "Compensation de Jeu de Vis Variable". La CNC travaille comme avec la compensation d’erreur de jeu de vis, c’est-à-dire, qu’elle applique à tout moment le jeu de vis défini sur la table pour le point en question et pour le sens d’usinage.
Lorsque l’axe inverse, la CNC commute de courbe et récupère ou applique le jeu correspondant aux point et sens en question.
Version 5.7 (Juillet 1996)
1. DÉTECTION DE ZONE DE TRAVAIL / ZONE D’EXCLUSION
Lorsque l’on travaille avec la prestation "Zone de travail / Zone d’exclusion", la CNC ne permet pas d’accéder ou de sortir de la zone en question pendant les déplacements de la machine au moyen des touches de JOG ou du volant.
Pour éviter que l’utilisateur ne songe à un fonctionnement incorrect de la machine, car aucun texte n’est affiché, à partir de cette version la CNC agit de la manière suivante pendant les déplacements de la machine au moyen des touches de JOG ou du volant:
* Lorsqu’elle est sélectionnée comme Zone de Travail, la CNC met l’entrée I46 du PLCI à niveau logique haut lorsque l’on essaie de sortir de la zone sélectionnée.
* Lorsqu’elle est sélectionnée comme Zone d’Exclusion, la CNC met l’entrée I46 du PLCI à niveau logique haut lorsque l’on essaie d’entrer dans la zone sélectionnée.
- 6 -
2. RÉINITIALISATION DE L’EXÉCUTION À MOITIÉ DE LA PIÈCE
Si au cours de l’usinage d’une pièce, l’exécution est interrompue (coupe de secteur, etc.), il est possible de réexécuter la pièce à partir de l’opération à laquelle l’usinage a été interrompu. On évite de cette façon d’avoir à répéter toute la pièce, avec la perte de temps que cela implique.
Pour réinitialiser l’exécution de la pièce, il faut suivre la démarche suivante:
1. Sélectionner le mode de travail Visualisateur, celui qui apparaît lors de l’allumage de la CNC, après la page "Test Général
Passé ".
Aucun cycle n’est sélectionné dans ce mode de travail.
2. Taper sur la touche [RECALL] pour ouvrir la fenêtre des programmes pièce.
3. Sélectionner le programme pièce que l’on avait sélectionné. Se mettre en position, au moyen des touches [fléchée haut] et
[fléchée bas] sur le programme pièce désiré et taper sur la touche [RECALL].
4. Sélectionner au moyen des touches [fléchée haut] et [fléchée bas], l’opération au cours de laquelle l’usinage de la pièce s’est interrompu et taper sur la touche
La CNC exécutera l’opération sélectionnée et poursuivra l’exécution du programme pièce jusqu’à la fin.
Version 6.1 (Janvier 1997)
1. NOUVELLES LANGUES (Chinois (Taiwan) et Portugais)
Paramètre machine P99 P99 = 5 Portugais P99 = 6 Chinois (Taiwan)
2. MODIFICATIONS DANS LE TRAVAIL AVEC VOLANT PRINCIPAL
Le travail avec Volant Principal est devenu:
a) Avec machine à l'arrêt.
Seulement est habilitée le premier volant, le deuxième volant (Volant Principal) ne fonctionne pas.
Donc avec les volants on ne pourra déplacer que l'axe X.
b) Avec machine en marche (CNC en Exécution).
Seulement est habilité le Volant Principal, la premier volant ne fonctionne pas.
Les axes commencent à se déplacer quand on tourne le Volant Principal
La vitesse d'avance des axes dépend de la vitesse de rotation du Volant Principal.
Si le volant s'arrête, la machine s'arrête.
Si le sens de rotation du Volant Principal est inverti, la CNC change le sens du mouvement (Fonction Retour d'un seul bloc).
c) Opération d'Arrondi Semi-automatique
L'opération d'Arrondi Semi-automatique commence en tournant le Volant Principal.
Si la rotation du Volant Principal est arrêtée, l'exécution s'arrête.
Si on continue à tourner le Volant Principal, l'exécution continue. Il n'admet pas de rotation en sens contraire.
Quand l'opération finalise la CNC ne prend pas en compte la rotation du Volant Principal pendant 1,4 de seconde. En évitant ainsi le début d'une nouvelle opération.
Ce temps écoulé, si on tourne le Volant Principal la CNC commence l'exécution d'une nouvelle opération dans le sens indiqué.
d) Opération de Tournage Conique Semi-automatique
L'opération de Tournage Conique Semi-automatique commence en tournant le Volant Principal.
Si on arrête la rotation du Volant Principal, l'exécution s'arrête.
Si on continue à tourner le Volant Principal, l'exécution continue.
Si on tourne le Volant Principal dans le sens contraire, l'opération finalise. Une nouvelle rotation du Volant Principal, dans n'importe quel sens, implique l'exécution d'une nouvelle opération dans le sens indiqué.
- 7 -
3. VERSION DE SOFTWARE DANS LA CNC
À partir de cette version, quand on accède à l'écran qu'affiche le cheksum de chacune des Eproms,
[Modes Auxiliaires] [Modes Spéciaux] [8]
La CNC affichera, le cheksum de chacune des Eprom et la Version de Software dont dispose la CNC. Par exemple: Version 6.1
Version 6.4 (Mai 1997)
1. INDICATIF DE CHANGEMENT D'OUTIL AU PLC (I97)
Sur les machines avec changeur manuel d'outils, quand la CNC détecte qu'il faut mettre un nouvel outil, elle arrête l'exécution et affiche à l'utilisateur un message pour qu'il effectue le changement.
Parfois, pendant le changement d'outil il faut prendre certaines précautions. Ces conditions doivent être traitées dans le PLC.
Par cela, à partir de cette version, la CNC affiche le message de changement d'outil, elle active l'entrée I97 du PLC, et la désactive quand se le message disparaît.
Version 6.6 (Novembre 1997)
1. GESTION DE SYSTÈMES DE MESURE AVEC IO CODÉS
Paramètres machine
P608(5), P608(8) Type de signal Io dont dispose le système de mesure. Axe X, Z. (0 = Io normal, 1 = Io codé)
P608(3), P608(6) Période signal Io codé. Axe X, Z. (0 = Période de signal Io de 20 mm, 1 = Période de signal Io de 100 mm)
P608(4), P608(7) Séquence de Io croissant avec comptage positif ou négatif. Axe X, Z.
(0 = Io croissant avec comptage positif, 1 = Io croissant avec comptage négatif)
P908, P909
Règle
COS
COC
COX
COVS
COVC
COVX
P608 (5)
1
1
1
1
1
1
P608 (3)
0
0
0
0
0
0
P608 (4)
1
0
0
0
0
1
Offset de la règle ou position qu'occupe le Zéro Machine
(M) par rapport au Zéro de la Règle. Axe X, Z
Règle
MOVS
MOVC
MOVX
FOT
FOS
FOC
Les transducteurs linéaires avec Io codé disposent d'une
échelle graduée avec son propre Zéro de Règle, il ne suffit alors que d'effectuer un déplacement de 20 mm ou 100 mm pour connaître la position, par rapport au Zéro de Règle.
P608 (5)
1
1
1
1
1
1
P608 (3)
0
0
1
1
0
1
P608 (4)
0
0
0
0
0
0
Point de référence.
Quand le système de mesure dispose de Io codé, ce point s'utilise uniquement quand l'axe dispose de compensation d'erreur de vis. L'erreur de vis dans le point de référence machine doit être 0.
Ajustage de l'offset de la règle
L'ajustage de l'offset de la règle doit être réalisé axe par axe, il est conseillé d'utiliser le processus suivant:
* Indiquer dans le paramètre "P600(7) et P600(6)" le flanc de l'impulsion de Io du système de mesure qui sera utilisé.
* Indiquer dans le paramètre "P618(8) et P618(7)" le sens dans lequel se déplacera l'axe pendant la recherche du Zéro Machine.
* Personnaliser les paramètres "P807 et P808" avec la vitesse de l'axe dans la recherche du Zéro Machine.
* Assigner la valeur 0 au paramètre " P908 et P909" (offset de la règle).
- 8 -
* Positionner l'axe dans la position adéquate, et exécuter la commande de recherche de Zéro Machine de cet axe.
Touche [X] ou [Z], touche [flèche en haut] et touche
À la fin de la recherche la CNC affichera la valeur de coordonnée de l'axe se rapportant au Zéro de la Règle.
* Ensuite déplacer l'axe jusqu'au point zéro machine, ou jusqu'à un point aux dimensions connues par rapport au zéro machine, on observera la lecture que la CNC réalise de ce point.
La valeur qu'il faut assigner au paramètre machine qui définit l'offset de la règle doit être calculée avec la formule suivante.
Valeur = Lecture de la CNC à ce point - Valeur de coordonnée machine du point.
Exemple pour l'axe X: Si le point aux dimensions connues se trouve a 230 mm du zéro machine et la CNC affiche la valeur de coordonnée 423.5 mm, l'offset de la règle sera:
Paramètre machine P908 = 423,5 - 230 = 193.5 mm.
* Ensuite assigner cette nouvelle valeur au paramètre machine, taper sur la touche RESET pour que cette valeur soit assumée par la CNC.
* Il est nécessaire de réaliser une nouvelle recherche du Zéro Machine pour que cet axe prenne les valeurs correctes.
2. FILETAGE AVEC PASSES DE PÉNÉTRATION CONSTANTES
À partir de cette version, la pénétration de chaque passe sera en fonction du signe assigné au paramètre
∆∆
Avec
Avec
∆∆ positif, la pénétration de chaque passe est en fonction de la passe correspondante
(
∆∆
√
n )
∆∆ négatif, les pénétrations se maintiennent constants, avec la valeur absolue du paramètre
∆∆
3. GÉNÉRATION D'UN PROGRAMME EN CODE ISO
La CNC permet de générer, à partir d'une opération ou programme pièce, un programme en code ISO à bas niveau.
Quand on veut disposer de cette prestation il faut personnaliser le paramètre machine "P623(2)=1".
Le programme en code ISO généré par la CNC est toujours appelé 99996 et pourra être emmagasiné dans la CNC elle-même ou dans un ordinateur.
Le programme 99996 est un programme spécial d'usager en code ISO, qui peut être:
Généré à partir d'une opération ou programme pièce.
Édité dans la CNC elle-même, avec l'option "Modes auxiliaires - Édition programme 99996"
Être transmis à la CNC après avoir été élaboré dans un ordinateur.
Génération du programme ISO en mémoire de la CNC (99996).
Le CN800T dispose de 7 K de mémoire pour emmagasiner le programme 99996. Si le programme généré dépasse cette taille, la CNC affichera l'erreur correspondante.
Pour générer le programme 99996 il faut suivre les pas suivants:
* S'il s'agit d'une opération. Sélectionner ou définir l'opération désirée.
* S'il s'agit d'un programme pièce. Sélectionner dans le dossier de programmes pièce le programme pièce et positionner le curseur sur la tête de celle-ci ("PIÈCE 01435". On devra voir la liste des opérations qui la composent).
* Taper sur la séquence de touches [AUX].[7]. La CNC affichera la page de simulation graphique.
* Taper sur la touche . La CNC commence la simulation et la génération du programme 99996.
* Une fois finalisée la simulation, le programme 99996 emmagasiné en mémoire contiendra en code ISO tous les blocs qui ont été simulés.
Génération du programme ISO (99996) dans un ordinateur
Normalement, le programme 99996 généré à partir d'un programme pièce est supérieur à la mémoire disponible dans la CNC.
Grâce à l'utilisation du DNC30 il est possible de générer ce programme (99996) dans la mémoire de l'ordinateur.
Pour générer le programme 99996 dans un ordinateur il faut suivre les pas suivants:
* Activer la communication DNC et exécuter le programme DNC30 dans l'ordinateur.
* Sélectionner dans l'ordinateur l'option "Gestion de Programmes - Réception Digitalisée".
- 9 -
* Dans la CNC sélectionner l'opération ou se positionner sur la tête du programme pièce ("PIÈCE 01435". On devra voir la liste des opérations qui la composent).
* Taper sur la séquence de touches [AUX][8]. La CNC affichera la page de simulation graphique.
* Taper sur la touche . La CNC commence la simulation et la génération du programme 99996.
* Une fois finalisée la simulation, le programme 99996 qui a été généré dans l'ordinateur contiendra en code ISO tous les blocs qui ont été simulés dans la CNC.
Ce programme peut être exécuté dans la CNC grâce à l'option "Exécution programme infini" du DNC30.
4. RÉGLEMENTATION DE SÉCURITÉ EN MACHINES
La CNC dispose des prestations suivantes pour respecter la réglementation de sécurité sur machines.
Habilitation de la touche DEPART depuis le PLC
Cette prestation est disponible quand le paramètre "P619(7)=1" a été personnalisé.
La sortie O25 du PLC indique si la touche DEPART est habilitée (=1) ou non (=0)
Déplacements des axes affectés par l'Arrêt des Avances. (était déjà disponible)
L'entrée d'Arrêt des Avances, pin 15 du connecteur I/O 1, doit se trouver normalement au niveau logique haut.
Si pendant le déplacement des axes, l'entrée d'Arrêt des Avances se met au niveau logique bas, la CNC maintient la rotation de la broche et arrête l'avance des axes, en fournissant des signaux de valeur 0V et en maintenant les embrayages activés.
Quand ce signal retourne au niveau logique haut, la CNC continuera avec le déplacement des axes.
Avance des axes en mode manuel limitée depuis le PLC.
Cette prestation est disponible quand le paramètre "P619(7)=1" a été personnalisé
Chaque fois que la sortie O26 du PLC est activée, la CNC assume l'avance fixée dans le paramètre machine "P812"
Volant géré depuis le PLC.
Le paramètre "P623(3)" indique si le déplacement des axes avec volants est affecté par l'Arrêt des Avances (=1) ou non (=0)
Le paramètre machine "P622(1)" indique si est appliqué le facteur correspondant à la position du commutateur (=0) ou si est appliqué le facteur indiqué par les sorties O44 et O45 du PLC (=1) (Il était déjà disponible)
Contrôle de la broche depuis le PLC.
Cette prestation est disponible quand le paramètre "P619(7)=1" a été personnalisé.
La sortie O27 indique à la CNC qu'elle doit (O27=1) appliquer à la broche le signal fixé depuis le PLC. La valeur du signal est fixée dans le registre R156 et avec la marque M1956 est envoyée à la CNC.
R156= 0000 1111 1111 1111 => + 10V.
R156= 0000 0111 1111 1111 => + 5V.
R156= 0000 0011 1111 1111 => + 2,5V.
R156= 0000 0000 0000 0000 => + 0V.
R156= 0001 1111 1111 1111 => - 10V.
R156= 0001 0111 1111 1111 => 5V.
R156= 0001 0011 1111 1111 => - 2,5V.
R156= 0001 0000 0000 0000 => 0V.
De même, la sortie O43 du PLC, permet de contrôler la rotation de la broche. (Elle était déjà disponible)
Normalement elle doit se trouver au niveau logique bas.
Si elle est mise au niveau logique haut, la CNC arrête la rotation de la broche.
Quand cette sortie retourne au niveau logique bas, la CNC récupère la rotation de la broche.
Information au PLC de l'état de la recherche de référence machine
I88 Recherche de référence machine en processus
I100 Recherche de référence machine finalisée sur l'axe X
I101 Recherche de référence machine finalisée sur l'axe Z
- 10 -
Information additionnelle de la CNC au PLC
R120 La partie basse de ce registre indique le code de la touche tapée.
Cette valeur se maintient pendant 200 millièmes de seconde, sauf si on tape une autre touche avant.
Ce registre peut être annulé depuis le PLC, après avoir été géré.
R121 bit 1 bit 2 bit 3 bit 4
Indique que l'opération de Cylindrage est sélectionnée (=1)
Indique que l'opération de Dressage est sélectionnée (=1)
Indique que l'opération de Cylindrage Conique est sélectionnée (=1)
Indique que l'opération d'Arrondi est sélectionnée (=1) bit 5 bit 6 bit 7 bit 8
Indique que l'opération de Filetage est sélectionnée (=1)
Indique que l'opération de Rainurage est sélectionnée (=1)
Indique que l'opération de Profil est sélectionnée (=1)
Indique que l'option Modes Auxiliaires est sélectionnée (=1) bit 9 Indique que l'option Mesure d'outil est sélectionnée (=1) bit 10 Indique que l'opération de Perçage multiple est sélectionnée (=1) bit 11 Indique que l'opération de Perçage simple / Taraudage est sélectionnée (=1) bit 12 Indique que l'opération de Clavettes est sélectionnée (=1) bit 13 Indique que le mode d'Inspection d'Outil est sélectionné (=1) bit 14 Indique que le mode de Simulation graphique est sélectionné (=1) bit 16 Indique que le mode correspondant aux paramètres "Passe de finition, Avance de finition, Outil de finition et Distances de sécurité sur X et sur Z des cycles" est sélectionné (=1)
Version 6.8 (Mars 1998)
1. NOUVELLES LANGUES (SUÉDOIS ET NORVÉGIEN)
Les langues pouvant être sélectionnées avec le paramètre machine P99 sont:
Espagnol...(P99=0) Allemand.....(P99=1) Anglais....(P99=2)
Portugais...(P99=5) Taiwanais.....(P99=6) Suédois....(P99=7)
Français......(P99=3) Italien....(P99=4)
Norvégien...(P99=8)
2. CODEUR À 1000 IMPULSIONS COMME CODEUR À 1250
Cette performance permet à la CNC d'adapter la mesure du codeur à 1000 impulsions pour la traiter comme mesure à 1250 impulsions.
P623(7)
P623(8)
Adapte la mesure du codeur de l'axe X (0=Non, 1=Oui)
Adapte la mesure du codeur de l'axe Z (0=Non, 1=Oui)
Un cas typique: On dispose de moteurs avec codeur à 1000 impulsions et vis avec pas de 5 millimètres.
Les calculs nécessaires pour définir la résolution de l'axe s'effectueront avec le nombre d'impulsions sélectionnées (1000 ou 1250)
3. COMPENSATION CROISÉE
La compensation croisée permet de compenser l'erreur de mesure que subit l'axe X en déplaçant l'axe Z.
P623(6) À l'axe X on applique la Compensation croisée (0=Non, 1=Oui)
Quand on utilise la compensation croisée la CNC permet d'appliquer la compensation de vis uniquement à l'axe Z. Il n'est pas permis d'appliquer la compensation de vis à l'axe X parce que la table correspondante à cet axe s'utilise pour la compensation croisée avec les valeurs suivantes:
P00 = X: ?????.???
P01 = DX: ????.???
Pour appliquer correctement la compensation croisée définir P605(2)=1 et P623(6)=1.
Note: La table de compensation croisée doit remplir les mêmes conditions que la table de compensation d'erreur de vis. Voir sectiont 3.8.4 du manuel d'Installation.
4. PLCI. ENTRÉE I104
Quand le commutateur du panneau de commandes est sur une des positions du volant (x1, x10, x100), l'entrée I104 est à "1"
- 11 -
Version 6.9 (Février 1999)
1. NOUVEAU PARAMÈTRE MACHINE ASSOCIÉ AUX FONCTIONS M
Le paramètre machine «P620(8)», indique quand il faut sortir les fonctions M3, M4, M5 pendant l’accélération et la décélération de la broche.
2. ANNULER LE CORRECTEUR PENDANT LE CHANGEMENT D’OUTIL
À partir de cette version il est possible d’exécuter, dans la routine associée à l’outil, un bloc du type «T.0» pour annuler le correcteur de l’outil. Cela permet d’effectuer des déplacements à une cote déterminée sans avoir à effectuer des calculs compliqués.
Il est permis uniquement d’annuler (T.0) ou de modifier (T.xx) le correcteur. Il n’est pas permis de changer d’outil (Txx.xx) dans la routine associée à l’outil.
3. FACTEUR DIVISEUR DES SIGNAUX DE MESURE
Les paramètres P620(5) et P620(6) s’utilisent avec les paramètres P602(6) et P602(5) qui indiquent le facteur multiplicateur des signaux de mesure des axes X, Z respectivement.
Ils indiquent si les signaux de mesure sont divisés (=1) ou non (=0).
P620(5)=0 et P620(6)=0
P620(5)=1 et P620(6)=1
Ils ne se divisent pas
Ils se divisent par 2.
Exemple:on veut obtenir une résolution de 0,01 mm au moyen d’un codeur de signaux carrés placé sur l’axe X avec un pas de vis de 5 mm.
Nombre d’impulsions = pas de vis / (Facteur multiplication x Résolution)
Avec P602(6)=0 et P620(5)=0 Facteur de multiplication x4
Avec P602(6)=1 et P620(5)=0 Facteur de multiplication x2
Avec P602(6)=0 et P620(5)=1 Facteur de multiplication x2
Avec P602(6)=1 et P620(5)=1 Facteur de multiplication x1
Nombre d’impulsions = 125
Nombre d’impulsions = 250
Nombre d’impulsions = 250
Nombre d’impulsions = 500
- 12 -
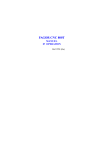
公開リンクが更新されました
あなたのチャットの公開リンクが更新されました。